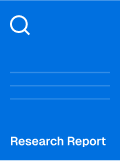
Titanium Alloy Market - Global Titanium Alloy Industry Analysis, Size, Share, Growth, Trends, and Forecast 2025-2032 - (By Alloy Type, By End-user, By Geographic Coverage and By Company)
Description
The global titanium alloy market is expected to witness notable growth, expanding from US$ 5.4 billion in 2025 to US$ 8.6 billion by 2032. This robust trajectory reflects a CAGR of 6.8% during the forecast period, with the market projected to grow by 1.6x by the end of 2032. Titanium alloys are gaining widespread adoption across multiple industries, driven by their lightweight, high-strength, and corrosion-resistant characteristics.
Market Insights
Titanium alloys are favored for their unique combination of properties—high strength-to-weight ratio, corrosion resistance, and temperature tolerance. These attributes make them ideal for use in demanding environments, particularly in aerospace, automotive, and medical applications. Alpha + Beta titanium alloys remain the most widely used category due to their excellent balance of formability, strength, and temperature performance.
Aerospace and defense applications continue to be the primary consumers of titanium alloys. These sectors rely heavily on the material for constructing airframes, engine components, and military-grade equipment where performance and durability are critical. North America, led by the U.S., holds a commanding presence in the market due to a well-established aerospace industry, while China’s rapid industrialization is creating new avenues for titanium alloy applications.
Market Drivers
The automotive sector is emerging as a powerful driver for titanium alloy demand. With the global push toward energy-efficient and electric vehicles, automakers are turning to lightweight materials to improve fuel efficiency and reduce emissions. Titanium alloys, thanks to their strength and heat resistance, are increasingly being incorporated into high-performance automotive components such as exhaust systems, engine valves, and suspension elements.
Several global automakers are actively exploring titanium integration. In 2023, Toyota partnered with Osaka Titanium Technologies to develop titanium-based solutions for future EVs. Ford has also pursued patents for titanium engine components aimed at improving vehicle longevity and performance. These developments, combined with stricter fuel economy regulations, are accelerating the use of titanium alloys in the automotive domain.
Business Opportunity
The medical sector presents a significant growth opportunity for titanium alloy manufacturers. These materials are highly biocompatible and corrosion-resistant, making them ideal for orthopedic, dental, and cardiovascular implants. In 2023, titanium dominated the medical alloy segment, supported by rising healthcare needs from an aging global population.
Innovations in 3D printing have amplified the role of titanium alloys in medicine. Additive manufacturing allows for the creation of customized implants that enhance surgical precision and patient recovery. Companies like Stryker Corporation are actively developing titanium-based dental and orthopedic implants tailored to individual patients, further expanding the market potential for titanium alloys in healthcare.
Sustainability Trends
Titanium recycling is gaining traction as a critical trend for improving sustainability and cost-efficiency in the industry. Recycled titanium can deliver up to 95% energy savings compared to virgin material production. In 2023, IperionX teamed up with Aperam to recycle titanium scrap from consumer electronics into usable, high-performance products.
Aerospace and automotive sectors are increasingly adopting recycled titanium to meet sustainability targets. For instance, Ford partnered with IperionX to procure titanium parts made from 100% recycled content. Meanwhile, the U.S. Department of Defense has awarded contracts to explore the recycling of used titanium powders. These efforts not only support environmental goals but also enhance supply chain resilience.
Regional Overview
North America maintains a strong foothold in the titanium alloy market, driven by continued investments in aerospace and defense. The U.S. leads the region, contributing over 80% of North America’s aerospace titanium revenue in 2022. Aircraft programs like the F-22 and F/A-18 incorporate significant amounts of titanium, and federal initiatives continue to fund aerospace modernization and manufacturing capabilities.
Europe is seeing stable growth, propelled by advancements in electric vehicle production and medical technology. Countries like Germany and the UK are leading adopters of titanium in the automotive sector, using the material to meet emission regulations and improve fuel efficiency. Additionally, the growing demand for medical implants in aging populations is boosting titanium use in healthcare across the continent.
Asia Pacific is emerging as the fastest-growing region, fueled by China’s expanding aerospace and automotive sectors. The country’s C919 airliner program and its massive vehicle production base—over 26 million units in 2021—are generating significant demand for titanium alloys. These factors, combined with growing technological innovation and industrial capacity, are establishing Asia Pacific as a key growth hub.
Competitive Landscape
The global titanium alloy market is led by established players such as VSMPO-AVISMA, ATI, TIMET, and Kobe Steel. These companies maintain long-standing contracts with major aerospace and automotive OEMs, allowing them to hold a dominant position in the global supply chain.
VSMPO-AVISMA operates a wide-reaching distribution network across Europe, Asia, and the Americas. ATI has diversified its product offerings to serve multiple industrial needs. Rising players like IperionX are gaining attention for their commitment to sustainable titanium production, leveraging recycling and reshoring strategies.
Recent technological advancements are shaping the competitive dynamics of the industry. The integration of artificial intelligence (AI) into production systems is improving process efficiency, while additive manufacturing and precision forging are enabling the production of complex titanium parts with minimal waste. In April 2025, Hermith GmbH optimized its Ti-6Al-4V wire for 3D printing, enhancing feedstock quality for high-demand applications. The same month, IperionX secured an $11 million loan to expand its titanium manufacturing facility in Virginia, advancing U.S.-based titanium production capabilities.
Segmentation
By Alloy Type
• Alpha & Near-Alpha Titanium Alloy
• Alpha + Beta Titanium Alloy
• Beta & Near-Beta Titanium Alloy
By End-user
• Aerospace
• Military
• Chemical
• Power Generation
• Automotive & Marine
• Medical Implants
• Consumer Goods
• Sporting Goods & Equipment
• Others (Jewellery, Construction)
By Region
• North America
• Europe
• Asia Pacific
• Latin America
• Middle East & Africa
Please note: Delivery Timelines - 5 working days.
Market Insights
Titanium alloys are favored for their unique combination of properties—high strength-to-weight ratio, corrosion resistance, and temperature tolerance. These attributes make them ideal for use in demanding environments, particularly in aerospace, automotive, and medical applications. Alpha + Beta titanium alloys remain the most widely used category due to their excellent balance of formability, strength, and temperature performance.
Aerospace and defense applications continue to be the primary consumers of titanium alloys. These sectors rely heavily on the material for constructing airframes, engine components, and military-grade equipment where performance and durability are critical. North America, led by the U.S., holds a commanding presence in the market due to a well-established aerospace industry, while China’s rapid industrialization is creating new avenues for titanium alloy applications.
Market Drivers
The automotive sector is emerging as a powerful driver for titanium alloy demand. With the global push toward energy-efficient and electric vehicles, automakers are turning to lightweight materials to improve fuel efficiency and reduce emissions. Titanium alloys, thanks to their strength and heat resistance, are increasingly being incorporated into high-performance automotive components such as exhaust systems, engine valves, and suspension elements.
Several global automakers are actively exploring titanium integration. In 2023, Toyota partnered with Osaka Titanium Technologies to develop titanium-based solutions for future EVs. Ford has also pursued patents for titanium engine components aimed at improving vehicle longevity and performance. These developments, combined with stricter fuel economy regulations, are accelerating the use of titanium alloys in the automotive domain.
Business Opportunity
The medical sector presents a significant growth opportunity for titanium alloy manufacturers. These materials are highly biocompatible and corrosion-resistant, making them ideal for orthopedic, dental, and cardiovascular implants. In 2023, titanium dominated the medical alloy segment, supported by rising healthcare needs from an aging global population.
Innovations in 3D printing have amplified the role of titanium alloys in medicine. Additive manufacturing allows for the creation of customized implants that enhance surgical precision and patient recovery. Companies like Stryker Corporation are actively developing titanium-based dental and orthopedic implants tailored to individual patients, further expanding the market potential for titanium alloys in healthcare.
Sustainability Trends
Titanium recycling is gaining traction as a critical trend for improving sustainability and cost-efficiency in the industry. Recycled titanium can deliver up to 95% energy savings compared to virgin material production. In 2023, IperionX teamed up with Aperam to recycle titanium scrap from consumer electronics into usable, high-performance products.
Aerospace and automotive sectors are increasingly adopting recycled titanium to meet sustainability targets. For instance, Ford partnered with IperionX to procure titanium parts made from 100% recycled content. Meanwhile, the U.S. Department of Defense has awarded contracts to explore the recycling of used titanium powders. These efforts not only support environmental goals but also enhance supply chain resilience.
Regional Overview
North America maintains a strong foothold in the titanium alloy market, driven by continued investments in aerospace and defense. The U.S. leads the region, contributing over 80% of North America’s aerospace titanium revenue in 2022. Aircraft programs like the F-22 and F/A-18 incorporate significant amounts of titanium, and federal initiatives continue to fund aerospace modernization and manufacturing capabilities.
Europe is seeing stable growth, propelled by advancements in electric vehicle production and medical technology. Countries like Germany and the UK are leading adopters of titanium in the automotive sector, using the material to meet emission regulations and improve fuel efficiency. Additionally, the growing demand for medical implants in aging populations is boosting titanium use in healthcare across the continent.
Asia Pacific is emerging as the fastest-growing region, fueled by China’s expanding aerospace and automotive sectors. The country’s C919 airliner program and its massive vehicle production base—over 26 million units in 2021—are generating significant demand for titanium alloys. These factors, combined with growing technological innovation and industrial capacity, are establishing Asia Pacific as a key growth hub.
Competitive Landscape
The global titanium alloy market is led by established players such as VSMPO-AVISMA, ATI, TIMET, and Kobe Steel. These companies maintain long-standing contracts with major aerospace and automotive OEMs, allowing them to hold a dominant position in the global supply chain.
VSMPO-AVISMA operates a wide-reaching distribution network across Europe, Asia, and the Americas. ATI has diversified its product offerings to serve multiple industrial needs. Rising players like IperionX are gaining attention for their commitment to sustainable titanium production, leveraging recycling and reshoring strategies.
Recent technological advancements are shaping the competitive dynamics of the industry. The integration of artificial intelligence (AI) into production systems is improving process efficiency, while additive manufacturing and precision forging are enabling the production of complex titanium parts with minimal waste. In April 2025, Hermith GmbH optimized its Ti-6Al-4V wire for 3D printing, enhancing feedstock quality for high-demand applications. The same month, IperionX secured an $11 million loan to expand its titanium manufacturing facility in Virginia, advancing U.S.-based titanium production capabilities.
Segmentation
By Alloy Type
• Alpha & Near-Alpha Titanium Alloy
• Alpha + Beta Titanium Alloy
• Beta & Near-Beta Titanium Alloy
By End-user
• Aerospace
• Military
• Chemical
• Power Generation
• Automotive & Marine
• Medical Implants
• Consumer Goods
• Sporting Goods & Equipment
• Others (Jewellery, Construction)
By Region
• North America
• Europe
• Asia Pacific
• Latin America
• Middle East & Africa
Please note: Delivery Timelines - 5 working days.
Table of Contents
220 Pages
- 1. Executive Summary
- 1.1. Global Titanium Alloy Market Snapshot
- 1.2. Future Projections
- 1.3. Key Market Trends
- 1.4. Regional Snapshot, by Value, 2025
- 1.5. Analyst Recommendations
- 2. Market Overview
- 2.1. Market Definitions and Segmentations
- 2.2. Market Dynamics
- 2.2.1. Drivers
- 2.2.2. Restraints
- 2.2.3. Market Opportunities
- 2.3. Value Chain Analysis
- 2.4. COVID-19 Impact Analysis
- 2.5. Porter's Fiver Forces Analysis
- 2.6. Impact of Russia-Ukraine Conflict
- 2.7. PESTLE Analysis
- 2.8. Regulatory Analysis
- 2.9. Price Trend Analysis
- 2.9.1. Current Prices and Future Projections, 2025-2032
- 2.9.2. Price Impact Factors
- 3. Global Titanium Alloy Market Outlook, 2019-2032
- 3.1. Global Titanium Alloy Market Outlook, by Alloy Type, Value (US$ Bn) & Volume (Tons), 2019-2032
- 3.1.1. Alpha & Near-Alpha Titanium Alloy
- 3.1.2. Alpha + Beta Titanium Alloy
- 3.1.3. Beta & Near-Beta Titanium Alloy
- 3.2. Global Titanium Alloy Market Outlook, by End-user, Value (US$ Bn) & Volume (Tons), 2019-2032
- 3.2.1. Aerospace
- 3.2.2. Military
- 3.2.3. Chemical
- 3.2.4. Power Generation
- 3.2.5. Automotive & Marine
- 3.2.6. Medical Implants
- 3.2.7. Consumer Goods
- 3.2.8. Sporting Goods & Equipment
- 3.2.9. Misc. (Jewellery, Construction, etc.)
- 3.3. Global Titanium Alloy Market Outlook, by Region, Value (US$ Bn) & Volume (Tons), 2019-2032
- 3.3.1. North America
- 3.3.2. Europe
- 3.3.3. Asia Pacific
- 3.3.4. Latin America
- 3.3.5. Middle East & Africa
- 4. North America Titanium Alloy Market Outlook, 2019-2032
- 4.1. North America Titanium Alloy Market Outlook, by Alloy Type, Value (US$ Bn) & Volume (Tons), 2019-2032
- 4.1.1. Alpha & Near-Alpha Titanium Alloy
- 4.1.2. Alpha + Beta Titanium Alloy
- 4.1.3. Beta & Near-Beta Titanium Alloy
- 4.2. North America Titanium Alloy Market Outlook, by End-user, Value (US$ Bn) & Volume (Tons), 2019-2032
- 4.2.1. Aerospace
- 4.2.2. Military
- 4.2.3. Chemical
- 4.2.4. Power Generation
- 4.2.5. Automotive & Marine
- 4.2.6. Medical Implants
- 4.2.7. Consumer Goods
- 4.2.8. Sporting Goods & Equipment
- 4.2.9. Misc. (Jewellery, Construction, etc.)
- 4.3. North America Titanium Alloy Market Outlook, by Country, Value (US$ Bn) & Volume (Tons), 2019-2032
- 4.3.1. U.S. Titanium Alloy Market Outlook, by Alloy Type, 2019-2032
- 4.3.2. U.S. Titanium Alloy Market Outlook, by End-user, 2019-2032
- 4.3.3. Canada Titanium Alloy Market Outlook, by Alloy Type, 2019-2032
- 4.3.4. Canada Titanium Alloy Market Outlook, by End-user, 2019-2032
- 4.4. BPS Analysis/Market Attractiveness Analysis
- 5. Europe Titanium Alloy Market Outlook, 2019-2032
- 5.1. Europe Titanium Alloy Market Outlook, by Alloy Type, Value (US$ Bn) & Volume (Tons), 2019-2032
- 5.1.1. Alpha & Near-Alpha Titanium Alloy
- 5.1.2. Alpha + Beta Titanium Alloy
- 5.1.3. Beta & Near-Beta Titanium Alloy
- 5.2. Europe Titanium Alloy Market Outlook, by End-user, Value (US$ Bn) & Volume (Tons), 2019-2032
- 5.2.1. Aerospace
- 5.2.2. Military
- 5.2.3. Chemical
- 5.2.4. Power Generation
- 5.2.5. Automotive & Marine
- 5.2.6. Medical Implants
- 5.2.7. Consumer Goods
- 5.2.8. Sporting Goods & Equipment
- 5.2.9. Misc. (Jewellery, Construction, etc.)
- 5.3. Europe Titanium Alloy Market Outlook, by Country, Value (US$ Bn) & Volume (Tons), 2019-2032
- 5.3.1. Germany Titanium Alloy Market Outlook, by Alloy Type, 2019-2032
- 5.3.2. Germany Titanium Alloy Market Outlook, by End-user, 2019-2032
- 5.3.3. Italy Titanium Alloy Market Outlook, by Alloy Type, 2019-2032
- 5.3.4. Italy Titanium Alloy Market Outlook, by End-user, 2019-2032
- 5.3.5. France Titanium Alloy Market Outlook, by Alloy Type, 2019-2032
- 5.3.6. France Titanium Alloy Market Outlook, by End-user, 2019-2032
- 5.3.7. U.K. Titanium Alloy Market Outlook, by Alloy Type, 2019-2032
- 5.3.8. U.K. Titanium Alloy Market Outlook, by End-user, 2019-2032
- 5.3.9. Spain Titanium Alloy Market Outlook, by Alloy Type, 2019-2032
- 5.3.10. Spain Titanium Alloy Market Outlook, by End-user, 2019-2032
- 5.3.11. Russia Titanium Alloy Market Outlook, by Alloy Type, 2019-2032
- 5.3.12. Russia Titanium Alloy Market Outlook, by End-user, 2019-2032
- 5.3.13. Rest of Europe Titanium Alloy Market Outlook, by Alloy Type, 2019-2032
- 5.3.14. Rest of Europe Titanium Alloy Market Outlook, by End-user, 2019-2032
- 5.4. BPS Analysis/Market Attractiveness Analysis
- 6. Asia Pacific Titanium Alloy Market Outlook, 2019-2032
- 6.1. Asia Pacific Titanium Alloy Market Outlook, by Alloy Type, Value (US$ Bn) & Volume (Tons), 2019-2032
- 6.1.1. Alpha & Near-Alpha Titanium Alloy
- 6.1.2. Alpha + Beta Titanium Alloy
- 6.1.3. Beta & Near-Beta Titanium Alloy
- 6.2. Asia Pacific Titanium Alloy Market Outlook, by End-user, Value (US$ Bn) & Volume (Tons), 2019-2032
- 6.2.1. Aerospace
- 6.2.2. Military
- 6.2.3. Chemical
- 6.2.4. Power Generation
- 6.2.5. Automotive & Marine
- 6.2.6. Medical Implants
- 6.2.7. Consumer Goods
- 6.2.8. Sporting Goods & Equipment
- 6.2.9. Misc. (Jewellery, Construction, etc.)
- 6.3. Asia Pacific Titanium Alloy Market Outlook, by Country, Value (US$ Bn) & Volume (Tons), 2019-2032
- 6.3.1. China Titanium Alloy Market Outlook, by Alloy Type, 2019-2032
- 6.3.2. China Titanium Alloy Market Outlook, by End-user, 2019-2032
- 6.3.3. Japan Titanium Alloy Market Outlook, by Alloy Type, 2019-2032
- 6.3.4. Japan Titanium Alloy Market Outlook, by End-user, 2019-2032
- 6.3.5. South Korea Titanium Alloy Market Outlook, by Alloy Type, 2019-2032
- 6.3.6. South Korea Titanium Alloy Market Outlook, by End-user, 2019-2032
- 6.3.7. India Titanium Alloy Market Outlook, by Alloy Type, 2019-2032
- 6.3.8. India Titanium Alloy Market Outlook, by End-user, 2019-2032
- 6.3.9. Southeast Asia Titanium Alloy Market Outlook, by Alloy Type, 2019-2032
- 6.3.10. Southeast Asia Titanium Alloy Market Outlook, by End-user, 2019-2032
- 6.3.11. Rest of SAO Titanium Alloy Market Outlook, by Alloy Type, 2019-2032
- 6.3.12. Rest of SAO Titanium Alloy Market Outlook, by End-user, 2019-2032
- 6.4. BPS Analysis/Market Attractiveness Analysis
- 7. Latin America Titanium Alloy Market Outlook, 2019-2032
- 7.1. Latin America Titanium Alloy Market Outlook, by Alloy Type, Value (US$ Bn) & Volume (Tons), 2019-2032
- 7.1.1. Alpha & Near-Alpha Titanium Alloy
- 7.1.2. Alpha + Beta Titanium Alloy
- 7.1.3. Beta & Near-Beta Titanium Alloy
- 7.2. Latin America Titanium Alloy Market Outlook, by End-user, Value (US$ Bn) & Volume (Tons), 2019-2032
- 7.2.1. Aerospace
- 7.2.2. Military
- 7.2.3. Chemical
- 7.2.4. Power Generation
- 7.2.5. Automotive & Marine
- 7.2.6. Medical Implants
- 7.2.7. Consumer Goods
- 7.2.8. Sporting Goods & Equipment
- 7.2.9. Misc. (Jewellery, Construction, etc.)
- 7.3. Latin America Titanium Alloy Market Outlook, by Country, Value (US$ Bn) & Volume (Tons), 2019-2032
- 7.3.1. Brazil Titanium Alloy Market Outlook, by Alloy Type, 2019-2032
- 7.3.2. Brazil Titanium Alloy Market Outlook, by End-user, 2019-2032
- 7.3.3. Mexico Titanium Alloy Market Outlook, by Alloy Type, 2019-2032
- 7.3.4. Mexico Titanium Alloy Market Outlook, by End-user, 2019-2032
- 7.3.5. Argentina Titanium Alloy Market Outlook, by Alloy Type, 2019-2032
- 7.3.6. Argentina Titanium Alloy Market Outlook, by End-user, 2019-2032
- 7.3.7. Rest of LATAM Titanium Alloy Market Outlook, by Alloy Type, 2019-2032
- 7.3.8. Rest of LATAM Titanium Alloy Market Outlook, by End-user, 2019-2032
- 7.4. BPS Analysis/Market Attractiveness Analysis
- 8. Middle East & Africa Titanium Alloy Market Outlook, 2019-2032
- 8.1. Middle East & Africa Titanium Alloy Market Outlook, by Alloy Type, Value (US$ Bn) & Volume (Tons), 2019-2032
- 8.1.1. Alpha & Near-Alpha Titanium Alloy
- 8.1.2. Alpha + Beta Titanium Alloy
- 8.1.3. Beta & Near-Beta Titanium Alloy
- 8.2. Middle East & Africa Titanium Alloy Market Outlook, by End-user, Value (US$ Bn) & Volume (Tons), 2019-2032
- 8.2.1. Aerospace
- 8.2.2. Military
- 8.2.3. Chemical
- 8.2.4. Power Generation
- 8.2.5. Automotive & Marine
- 8.2.6. Medical Implants
- 8.2.7. Consumer Goods
- 8.2.8. Sporting Goods & Equipment
- 8.2.9. Misc. (Jewellery, Construction, etc.)
- 8.3. Middle East & Africa Titanium Alloy Market Outlook, by Country, Value (US$ Bn) & Volume (Tons), 2019-2032
- 8.3.1. GCC Titanium Alloy Market Outlook, by Alloy Type, 2019-2032
- 8.3.2. GCC Titanium Alloy Market Outlook, by End-user, 2019-2032
- 8.3.3. South Africa Titanium Alloy Market Outlook, by Alloy Type, 2019-2032
- 8.3.4. South Africa Titanium Alloy Market Outlook, by End-user, 2019-2032
- 8.3.5. Egypt Titanium Alloy Market Outlook, by Alloy Type, 2019-2032
- 8.3.6. Egypt Titanium Alloy Market Outlook, by End-user, 2019-2032
- 8.3.7. Nigeria Titanium Alloy Market Outlook, by Alloy Type, 2019-2032
- 8.3.8. Nigeria Titanium Alloy Market Outlook, by End-user, 2019-2032
- 8.3.9. Rest of Middle East Titanium Alloy Market Outlook, by Alloy Type, 2019-2032
- 8.3.10. Rest of Middle East Titanium Alloy Market Outlook, by End-user, 2019-2032
- 8.4. BPS Analysis/Market Attractiveness Analysis
- 9. Competitive Landscape
- 9.1. Company Vs Segment Heatmap
- 9.2. Company Market Share Analysis, 2025
- 9.3. Competitive Dashboard
- 9.4. Company Profiles
- 9.4.1. Allegheny Technologies Incorporated (ATI)
- 9.4.1.1. Company Overview
- 9.4.1.2. Product Portfolio
- 9.4.1.3. Financial Overview
- 9.4.1.4. Business Strategies and Developments
- 9.4.2. Baoji Titanium Co. Ltd.
- 9.4.2.1. Company Overview
- 9.4.2.2. Product Portfolio
- 9.4.2.3. Financial Overview
- 9.4.2.4. Business Strategies and Developments
- 9.4.3. Western Superconducting Technologies Co, Ltd. (WST)
- 9.4.3.1. Company Overview
- 9.4.3.2. Product Portfolio
- 9.4.3.3. Financial Overview
- 9.4.3.4. Business Strategies and Developments
- 9.4.4. Kobe Steel, Ltd.
- 9.4.4.1. Company Overview
- 9.4.4.2. Product Portfolio
- 9.4.4.3. Financial Overview
- 9.4.4.4. Business Strategies and Developments
- 9.4.5. Western Metal Materials Co. Ltd. (WMM)
- 9.4.5.1. Company Overview
- 9.4.5.2. Product Portfolio
- 9.4.5.3. Financial Overview
- 9.4.5.4. Business Strategies and Developments
- 9.4.6. Precision Castparts Corp. (PCC)
- 9.4.6.1. Company Overview
- 9.4.6.2. Product Portfolio
- 9.4.6.3. Financial Overview
- 9.4.6.4. Business Strategies and Developments
- 9.4.7. UKTMP JSC
- 9.4.7.1. Company Overview
- 9.4.7.2. Product Portfolio
- 9.4.7.3. Financial Overview
- 9.4.7.4. Business Strategies and Developments
- 9.4.8. Toho Titanium Co., Ltd.
- 9.4.8.1. Company Overview
- 9.4.8.2. Product Portfolio
- 9.4.8.3. Financial Overview
- 9.4.8.4. Business Strategies and Developments
- 9.4.9. Hermith GmbH
- 9.4.9.1. Company Overview
- 9.4.9.2. Product Portfolio
- 9.4.9.3. Financial Overview
- 9.4.9.4. Business Strategies and Developments
- 9.4.10. Howmet Aerospace Inc.
- 9.4.10.1. Company Overview
- 9.4.10.2. Product Portfolio
- 9.4.10.3. Financial Overview
- 9.4.10.4. Business Strategies and Developments
- 9.4.11. Mishra Dhatu Nigam Limited (MIDHANI)
- 9.4.11.1. Company Overview
- 9.4.11.2. Product Portfolio
- 9.4.11.3. Financial Overview
- 9.4.11.4. Business Strategies and Developments
- 9.4.12. ERAMET Group
- 9.4.12.1. Company Overview
- 9.4.12.2. Product Portfolio
- 9.4.12.3. Financial Overview
- 9.4.12.4. Business Strategies and Developments
- 9.4.13. Xinjiang Xiangsheng New Material Technology Co., Ltd.
- 9.4.13.1. Company Overview
- 9.4.13.2. Product Portfolio
- 9.4.13.3. Financial Overview
- 9.4.13.4. Business Strategies and Developments
- 9.4.14. Oric Italiana S.r.l.
- 9.4.14.1. Company Overview
- 9.4.14.2. Product Portfolio
- 9.4.14.3. Financial Overview
- 9.4.14.4. Business Strategies and Developments
- 9.4.15. C.M.A. S.A.
- 9.4.15.1. Company Overview
- 9.4.15.2. Product Portfolio
- 9.4.15.3. Financial Overview
- 9.4.15.4. Business Strategies and Developments
- 10. Appendix
- 10.1. Research Methodology
- 10.2. Report Assumptions
- 10.3. Acronyms and Abbreviations
Pricing
Currency Rates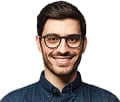
Questions or Comments?
Our team has the ability to search within reports to verify it suits your needs. We can also help maximize your budget by finding sections of reports you can purchase.