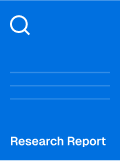
Weaving Machine Global Market Insights 2025, Analysis and Forecast to 2030, by Manufacturers, Regions, Technology, Product Type
Description
Weaving Machine Market Summary
Introduction
Weaving machines, also known as looms, are critical industrial equipment used in the textile industry to interlace warp and weft yarns into fabrics, ranging from apparel to technical textiles. These machines, categorized into air jet looms, rapier looms, water jet looms, and gripper looms, vary in speed, efficiency, and suitability for different fabric types. The industry is driven by global textile demand, technological advancements, and automation trends, with China leading as the world’s largest textile producer and exporter, achieving $141.9 billion in textile exports in 2024, a 5.7% increase year-over-year. Weaving machines incorporate advanced features like IoT integration, energy-efficient designs, and automated controls to enhance productivity and fabric quality. Key players like Lindauer DORNIER GmbH and Picanol innovate with smart looms, while companies like Qingdao Haijia, producing 20,000 shuttleless looms annually, cater to high-volume markets. Challenges include high capital costs, outdated technology in some regions, and environmental regulations, while trends like sustainable textiles, digitalization, and demand for customized fabrics shape the market’s future. Asia Pacific dominates consumption, fueled by textile production, with Europe and North America focusing on high-value technical textiles.
Market Size and Growth Forecast
The global weaving machine market is projected to reach USD 6.5–7.5 billion by 2025, with an estimated compound annual growth rate (CAGR) of 4.5%–6.5% through 2030. This growth is driven by rising demand for high-quality textiles, automation in manufacturing, and investments in modernizing textile production, particularly in emerging economies. The market benefits from technological advancements like shuttleless looms and increasing adoption in technical textile applications.
Regional Analysis
Asia Pacific leads the weaving machine market, with an estimated growth rate of 5%–7%. China, the global textile production hub, accounts for over 50% of world textile output, driven by $1 trillion in industrial investments in 2023 and supportive export policies. India’s textile sector, growing 8% annually, boosts demand for rapier and air jet looms, supported by government schemes like the Technology Upgradation Fund Scheme. Bangladesh and Vietnam, with 10% export growth, drive demand for water jet looms. North America follows with a growth rate of 4%–6%, led by the United States, where automotive and aerospace textiles, valued at $30 billion in 2023, fuel demand for advanced looms. Canada supports growth through technical textile applications. Europe, with a growth rate of 3.5%–5.5%, is driven by Germany, Italy, and the UK, where EU sustainability regulations targeting 90% emissions reduction by 2030 promote eco-friendly looms. South America, with a growth rate of 3%–5%, sees contributions from Brazil’s apparel industry. The Middle East and Africa, with growth estimated at 2.5%–4.5%, are emerging markets, with Saudi Arabia’s Vision 2030 and South Africa’s textile exports driving demand, though economic constraints limit adoption.
Type Analysis
Air Jet Loom: This segment, expected to grow at a CAGR of 5%–7%, uses compressed air for weft insertion, offering high-speed production for lightweight fabrics like apparel and home textiles. Trends include energy-efficient designs, as offered by Tsudakoma, with 30% reduced vibration.
Rapier Loom: Projected to grow at a CAGR of 4.5%–6.5%, rapier looms provide versatility for complex patterns in fashion and technical textiles. Trends focus on IoT-enabled platforms like Picanol’s PicConnect for real-time monitoring.
Water Jet Loom: Expected to grow at a CAGR of 5.5%–7.5%, water jet looms are ideal for synthetic fibers, driven by Asia’s 10% growth in synthetic fabric production. Trends include low-energy models, as developed by Toyota Industries.
Gripper Loom: Anticipated to grow at a CAGR of 4%–6%, gripper looms excel in heavy fabrics like denim and industrial textiles. Trends focus on precision grippers, as offered by Lindauer DORNIER, for technical applications.
Key Market Players
Lindauer DORNIER GmbH: A Germany-based company, Lindauer DORNIER manufactures air jet and rapier looms, focusing on high-precision solutions for technical textiles and sustainability.
Toyota Industries Corporation: A Japan-based firm, Toyota Industries produces air jet and water jet looms, known for energy-efficient and high-speed weaving solutions.
Tsudakoma: A Japan-based manufacturer, Tsudakoma supplies air jet and water jet looms, emphasizing vibration reduction and high-quality fabric production.
Picanol: A Belgium-based company, Picanol offers air jet and rapier looms with IoT platforms like PicConnect, targeting productivity and digitalization.
Itema: An Italy-based firm, Itema manufactures rapier, air jet, and projectile looms, focusing on eco-efficient and versatile weaving solutions.
Zhejiang Taitan: A China-based manufacturer, Zhejiang Taitan, with $41.3 million in 2024 sales, produces rapier and air jet looms for apparel and industrial textiles.
JINGWEI Textile Machinery: A China-based company, JINGWEI supplies air jet and rapier looms, emphasizing cost-effective solutions for large-scale production.
Rifa: A China-based firm, Rifa manufactures air jet and water jet looms, focusing on high-speed and automated textile solutions.
Kingtex: A China-based manufacturer, Kingtex produces rapier and air jet looms, targeting affordable and reliable solutions for Asia Pacific markets.
Qingdao Haijia: A China-based company, Qingdao Haijia, with 20,000 shuttleless looms produced annually, supplies water jet and air jet looms for synthetic fabrics.
ZheJiang Huahai Machinery Group: A China-based firm, Huahai manufactures rapier and water jet looms, prioritizing energy efficiency and customization.
Porter’s Five Forces Analysis
Threat of New Entrants: Low to Moderate. High capital investment for advanced manufacturing, stringent quality standards, and established brand loyalty create barriers, though regional players like Zhejiang Taitan pose a moderate threat with cost-competitive offerings.
Threat of Substitutes: Moderate. Traditional shuttle looms and non-woven technologies compete in niche applications, but shuttleless looms, used in 70% of modern textile production, limit substitution due to speed and quality.
Bargaining Power of Buyers: Moderate to High. Large textile manufacturers in Asia have leverage due to bulk purchasing, but specialized looms, like Lindauer DORNIER’s technical textile solutions, reduce switching options in premium segments.
Bargaining Power of Suppliers: Moderate. Suppliers of components like sensors and motors face price volatility (steel prices up 4% in 2023), but vertical integration by players like Toyota Industries balances this power.
Competitive Rivalry: High. Picanol, Itema, and Tsudakoma compete on innovation and digitalization, while Chinese players like Qingdao Haijia drive price competition, intensifying rivalry.
Market Opportunities and Challenges
Opportunities
Textile Export Growth: China’s $141.9 billion textile exports in 2024 and Bangladesh’s 10% export growth create opportunities for high-volume looms, as offered by Qingdao Haijia.
Automation and IoT: Smart looms with IoT, growing 15% annually, enhance productivity, as pursued by Picanol’s PicConnect platform.
Sustainable Textiles: Eco-friendly looms, aligning with 70% of manufacturers targeting sustainability by 2030, drive demand, as developed by Itema.
Technical Textiles: Automotive and aerospace textiles, valued at $30 billion in the U.S., boost demand for precision looms, as offered by Lindauer DORNIER.
Emerging Markets: India’s 8% textile growth and Africa’s rising textile exports create opportunities for affordable looms, as targeted by Kingtex.
Challenges
High Capital Costs: Advanced looms, costing 30% more than traditional models, deter SMEs in price-sensitive markets like India.
Outdated Technology: India’s 40% outdated looms hinder global competitiveness, challenging modernization efforts.
Environmental Regulations: EU emissions standards, targeting 90% compliance by 2030, increase R&D costs for eco-friendly looms.
Raw Material Volatility: Steel and electronic component price fluctuations, up 4% in 2023, raise production costs for non-integrated players like Rifa.
Skills Shortage: A 20% shortfall in skilled technicians in Asia by 2025 hinders operation of automated looms, impacting adoption rates.
Introduction
Weaving machines, also known as looms, are critical industrial equipment used in the textile industry to interlace warp and weft yarns into fabrics, ranging from apparel to technical textiles. These machines, categorized into air jet looms, rapier looms, water jet looms, and gripper looms, vary in speed, efficiency, and suitability for different fabric types. The industry is driven by global textile demand, technological advancements, and automation trends, with China leading as the world’s largest textile producer and exporter, achieving $141.9 billion in textile exports in 2024, a 5.7% increase year-over-year. Weaving machines incorporate advanced features like IoT integration, energy-efficient designs, and automated controls to enhance productivity and fabric quality. Key players like Lindauer DORNIER GmbH and Picanol innovate with smart looms, while companies like Qingdao Haijia, producing 20,000 shuttleless looms annually, cater to high-volume markets. Challenges include high capital costs, outdated technology in some regions, and environmental regulations, while trends like sustainable textiles, digitalization, and demand for customized fabrics shape the market’s future. Asia Pacific dominates consumption, fueled by textile production, with Europe and North America focusing on high-value technical textiles.
Market Size and Growth Forecast
The global weaving machine market is projected to reach USD 6.5–7.5 billion by 2025, with an estimated compound annual growth rate (CAGR) of 4.5%–6.5% through 2030. This growth is driven by rising demand for high-quality textiles, automation in manufacturing, and investments in modernizing textile production, particularly in emerging economies. The market benefits from technological advancements like shuttleless looms and increasing adoption in technical textile applications.
Regional Analysis
Asia Pacific leads the weaving machine market, with an estimated growth rate of 5%–7%. China, the global textile production hub, accounts for over 50% of world textile output, driven by $1 trillion in industrial investments in 2023 and supportive export policies. India’s textile sector, growing 8% annually, boosts demand for rapier and air jet looms, supported by government schemes like the Technology Upgradation Fund Scheme. Bangladesh and Vietnam, with 10% export growth, drive demand for water jet looms. North America follows with a growth rate of 4%–6%, led by the United States, where automotive and aerospace textiles, valued at $30 billion in 2023, fuel demand for advanced looms. Canada supports growth through technical textile applications. Europe, with a growth rate of 3.5%–5.5%, is driven by Germany, Italy, and the UK, where EU sustainability regulations targeting 90% emissions reduction by 2030 promote eco-friendly looms. South America, with a growth rate of 3%–5%, sees contributions from Brazil’s apparel industry. The Middle East and Africa, with growth estimated at 2.5%–4.5%, are emerging markets, with Saudi Arabia’s Vision 2030 and South Africa’s textile exports driving demand, though economic constraints limit adoption.
Type Analysis
Air Jet Loom: This segment, expected to grow at a CAGR of 5%–7%, uses compressed air for weft insertion, offering high-speed production for lightweight fabrics like apparel and home textiles. Trends include energy-efficient designs, as offered by Tsudakoma, with 30% reduced vibration.
Rapier Loom: Projected to grow at a CAGR of 4.5%–6.5%, rapier looms provide versatility for complex patterns in fashion and technical textiles. Trends focus on IoT-enabled platforms like Picanol’s PicConnect for real-time monitoring.
Water Jet Loom: Expected to grow at a CAGR of 5.5%–7.5%, water jet looms are ideal for synthetic fibers, driven by Asia’s 10% growth in synthetic fabric production. Trends include low-energy models, as developed by Toyota Industries.
Gripper Loom: Anticipated to grow at a CAGR of 4%–6%, gripper looms excel in heavy fabrics like denim and industrial textiles. Trends focus on precision grippers, as offered by Lindauer DORNIER, for technical applications.
Key Market Players
Lindauer DORNIER GmbH: A Germany-based company, Lindauer DORNIER manufactures air jet and rapier looms, focusing on high-precision solutions for technical textiles and sustainability.
Toyota Industries Corporation: A Japan-based firm, Toyota Industries produces air jet and water jet looms, known for energy-efficient and high-speed weaving solutions.
Tsudakoma: A Japan-based manufacturer, Tsudakoma supplies air jet and water jet looms, emphasizing vibration reduction and high-quality fabric production.
Picanol: A Belgium-based company, Picanol offers air jet and rapier looms with IoT platforms like PicConnect, targeting productivity and digitalization.
Itema: An Italy-based firm, Itema manufactures rapier, air jet, and projectile looms, focusing on eco-efficient and versatile weaving solutions.
Zhejiang Taitan: A China-based manufacturer, Zhejiang Taitan, with $41.3 million in 2024 sales, produces rapier and air jet looms for apparel and industrial textiles.
JINGWEI Textile Machinery: A China-based company, JINGWEI supplies air jet and rapier looms, emphasizing cost-effective solutions for large-scale production.
Rifa: A China-based firm, Rifa manufactures air jet and water jet looms, focusing on high-speed and automated textile solutions.
Kingtex: A China-based manufacturer, Kingtex produces rapier and air jet looms, targeting affordable and reliable solutions for Asia Pacific markets.
Qingdao Haijia: A China-based company, Qingdao Haijia, with 20,000 shuttleless looms produced annually, supplies water jet and air jet looms for synthetic fabrics.
ZheJiang Huahai Machinery Group: A China-based firm, Huahai manufactures rapier and water jet looms, prioritizing energy efficiency and customization.
Porter’s Five Forces Analysis
Threat of New Entrants: Low to Moderate. High capital investment for advanced manufacturing, stringent quality standards, and established brand loyalty create barriers, though regional players like Zhejiang Taitan pose a moderate threat with cost-competitive offerings.
Threat of Substitutes: Moderate. Traditional shuttle looms and non-woven technologies compete in niche applications, but shuttleless looms, used in 70% of modern textile production, limit substitution due to speed and quality.
Bargaining Power of Buyers: Moderate to High. Large textile manufacturers in Asia have leverage due to bulk purchasing, but specialized looms, like Lindauer DORNIER’s technical textile solutions, reduce switching options in premium segments.
Bargaining Power of Suppliers: Moderate. Suppliers of components like sensors and motors face price volatility (steel prices up 4% in 2023), but vertical integration by players like Toyota Industries balances this power.
Competitive Rivalry: High. Picanol, Itema, and Tsudakoma compete on innovation and digitalization, while Chinese players like Qingdao Haijia drive price competition, intensifying rivalry.
Market Opportunities and Challenges
Opportunities
Textile Export Growth: China’s $141.9 billion textile exports in 2024 and Bangladesh’s 10% export growth create opportunities for high-volume looms, as offered by Qingdao Haijia.
Automation and IoT: Smart looms with IoT, growing 15% annually, enhance productivity, as pursued by Picanol’s PicConnect platform.
Sustainable Textiles: Eco-friendly looms, aligning with 70% of manufacturers targeting sustainability by 2030, drive demand, as developed by Itema.
Technical Textiles: Automotive and aerospace textiles, valued at $30 billion in the U.S., boost demand for precision looms, as offered by Lindauer DORNIER.
Emerging Markets: India’s 8% textile growth and Africa’s rising textile exports create opportunities for affordable looms, as targeted by Kingtex.
Challenges
High Capital Costs: Advanced looms, costing 30% more than traditional models, deter SMEs in price-sensitive markets like India.
Outdated Technology: India’s 40% outdated looms hinder global competitiveness, challenging modernization efforts.
Environmental Regulations: EU emissions standards, targeting 90% compliance by 2030, increase R&D costs for eco-friendly looms.
Raw Material Volatility: Steel and electronic component price fluctuations, up 4% in 2023, raise production costs for non-integrated players like Rifa.
Skills Shortage: A 20% shortfall in skilled technicians in Asia by 2025 hinders operation of automated looms, impacting adoption rates.
Table of Contents
95 Pages
- Chapter 1 Executive Summary
- Chapter 2 Abbreviation and Acronyms
- Chapter 3 Preface
- 3.1 Research Scope
- 3.2 Research Sources
- 3.2.1 Data Sources
- 3.2.2 Assumptions
- 3.3 Research Method
- Chapter 4 Market Landscape
- 4.1 Market Overview
- 4.2 Classification/Types
- 4.3 Application/End Users
- Chapter 5 Market Trend Analysis
- 5.1 Introduction
- 5.2 Drivers
- 5.3 Restraints
- 5.4 Opportunities
- 5.5 Threats
- Chapter 6 Industry Chain Analysis
- 6.1 Upstream/Suppliers Analysis
- 6.2 Weaving Machine Analysis
- 6.2.1 Technology Analysis
- 6.2.2 Cost Analysis
- 6.2.3 Market Channel Analysis
- 6.3 Downstream Buyers/End Users
- Chapter 7 Latest Market Dynamics
- 7.1 Latest News
- 7.2 Merger and Acquisition
- 7.3 Planned/Future Project
- 7.4 Policy Dynamics
- Chapter 8 Trading Analysis
- 8.1 Export of Weaving Machine by Region
- 8.2 Import of Weaving Machine by Region
- 8.3 Balance of Trade
- Chapter 9 Historical and Forecast Weaving Machine Market in North America (2020-2030)
- 9.1 Weaving Machine Market Size
- 9.2 Weaving Machine Demand by End Use
- 9.3 Competition by Players/Suppliers
- 9.4 Type Segmentation and Price
- 9.5 Key Countries Analysis
- 9.5.1 United States
- 9.5.2 Canada
- 9.5.3 Mexico
- Chapter 10 Historical and Forecast Weaving Machine Market in South America (2020-2030)
- 10.1 Weaving Machine Market Size
- 10.2 Weaving Machine Demand by End Use
- 10.3 Competition by Players/Suppliers
- 10.4 Type Segmentation and Price
- 10.5 Key Countries Analysis
- 10.5.1 Brazil
- 10.5.2 Argentina
- 10.5.3 Chile
- 10.5.4 Peru
- Chapter 11 Historical and Forecast Weaving Machine Market in Asia & Pacific (2020-2030)
- 11.1 Weaving Machine Market Size
- 11.2 Weaving Machine Demand by End Use
- 11.3 Competition by Players/Suppliers
- 11.4 Type Segmentation and Price
- 11.5 Key Countries Analysis
- 11.5.1 China
- 11.5.2 India
- 11.5.3 Japan
- 11.5.4 South Korea
- 11.5.5 Southest Asia
- 11.5.6 Australia
- Chapter 12 Historical and Forecast Weaving Machine Market in Europe (2020-2030)
- 12.1 Weaving Machine Market Size
- 12.2 Weaving Machine Demand by End Use
- 12.3 Competition by Players/Suppliers
- 12.4 Type Segmentation and Price
- 12.5 Key Countries Analysis
- 12.5.1 Germany
- 12.5.2 France
- 12.5.3 United Kingdom
- 12.5.4 Italy
- 12.5.5 Spain
- 12.5.6 Belgium
- 12.5.7 Netherlands
- 12.5.8 Austria
- 12.5.9 Poland
- 12.5.10 Russia
- Chapter 13 Historical and Forecast Weaving Machine Market in MEA (2020-2030)
- 13.1 Weaving Machine Market Size
- 13.2 Weaving Machine Demand by End Use
- 13.3 Competition by Players/Suppliers
- 13.4 Type Segmentation and Price
- 13.5 Key Countries Analysis
- 13.5.1 Egypt
- 13.5.2 Israel
- 13.5.3 South Africa
- 13.5.4 Gulf Cooperation Council Countries
- 13.5.5 Turkey
- Chapter 14 Summary For Global Weaving Machine Market (2020-2025)
- 14.1 Weaving Machine Market Size
- 14.2 Weaving Machine Demand by End Use
- 14.3 Competition by Players/Suppliers
- 14.4 Type Segmentation and Price
- Chapter 15 Global Weaving Machine Market Forecast (2025-2030)
- 15.1 Weaving Machine Market Size Forecast
- 15.2 Weaving Machine Demand Forecast
- 15.3 Competition by Players/Suppliers
- 15.4 Type Segmentation and Price Forecast
- Chapter 16 Analysis of Global Key Vendors
- 16.1 Lindauer DORNIER GmbH
- 16.1.1 Company Profile
- 16.1.2 Main Business and Weaving Machine Information
- 16.1.3 SWOT Analysis of Lindauer DORNIER GmbH
- 16.1.4 Lindauer DORNIER GmbH Weaving Machine Sales, Revenue, Price and Gross Margin (2020-2025)
- 16.2 Toyota Industries Corporation
- 16.2.1 Company Profile
- 16.2.2 Main Business and Weaving Machine Information
- 16.2.3 SWOT Analysis of Toyota Industries Corporation
- 16.2.4 Toyota Industries Corporation Weaving Machine Sales, Revenue, Price and Gross Margin (2020-2025)
- 16.3 Tsudakoma
- 16.3.1 Company Profile
- 16.3.2 Main Business and Weaving Machine Information
- 16.3.3 SWOT Analysis of Tsudakoma
- 16.3.4 Tsudakoma Weaving Machine Sales, Revenue, Price and Gross Margin (2020-2025)
- 16.4 Picanol
- 16.4.1 Company Profile
- 16.4.2 Main Business and Weaving Machine Information
- 16.4.3 SWOT Analysis of Picanol
- 16.4.4 Picanol Weaving Machine Sales, Revenue, Price and Gross Margin (2020-2025)
- 16.5 Itema
- 16.5.1 Company Profile
- 16.5.2 Main Business and Weaving Machine Information
- 16.5.3 SWOT Analysis of Itema
- 16.5.4 Itema Weaving Machine Sales, Revenue, Price and Gross Margin (2020-2025)
- 16.6 Zhejiang Taitan
- 16.6.1 Company Profile
- 16.6.2 Main Business and Weaving Machine Information
- 16.6.3 SWOT Analysis of Zhejiang Taitan
- 16.6.4 Zhejiang Taitan Weaving Machine Sales, Revenue, Price and Gross Margin (2020-2025)
- 16.7 JINGWEI Textile Machinery
- 16.7.1 Company Profile
- 16.7.2 Main Business and Weaving Machine Information
- 16.7.3 SWOT Analysis of JINGWEI Textile Machinery
- 16.7.4 JINGWEI Textile Machinery Weaving Machine Sales, Revenue, Price and Gross Margin (2020-2025)
- 16.8 Rifa
- 16.8.1 Company Profile
- 16.8.2 Main Business and Weaving Machine Information
- 16.8.3 SWOT Analysis of Rifa
- 16.8.4 Rifa Weaving Machine Sales, Revenue, Price and Gross Margin (2020-2025)
- Please ask for sample pages for full companies list
- Tables and Figures
- Table Abbreviation and Acronyms List
- Table Research Scope of Weaving Machine Report
- Table Data Sources of Weaving Machine Report
- Table Major Assumptions of Weaving Machine Report
- Figure Market Size Estimated Method
- Figure Major Forecasting Factors
- Figure Weaving Machine Picture
- Table Weaving Machine Classification
- Table Weaving Machine Applications List
- Table Drivers of Weaving Machine Market
- Table Restraints of Weaving Machine Market
- Table Opportunities of Weaving Machine Market
- Table Threats of Weaving Machine Market
- Table Covid-19 Impact For Weaving Machine Market
- Table Raw Materials Suppliers List
- Table Different Production Methods of Weaving Machine
- Table Cost Structure Analysis of Weaving Machine
- Table Key End Users List
- Table Latest News of Weaving Machine Market
- Table Merger and Acquisition List
- Table Planned/Future Project of Weaving Machine Market
- Table Policy of Weaving Machine Market
- Table 2020-2030 Regional Export of Weaving Machine
- Table 2020-2030 Regional Import of Weaving Machine
- Table 2020-2030 Regional Trade Balance
- Figure 2020-2030 Regional Trade Balance
- Table 2020-2030 North America Weaving Machine Market Size and Market Volume List
- Figure 2020-2030 North America Weaving Machine Market Size and CAGR
- Figure 2020-2030 North America Weaving Machine Market Volume and CAGR
- Table 2020-2030 North America Weaving Machine Demand List by Application
- Table 2020-2025 North America Weaving Machine Key Players Sales List
- Table 2020-2025 North America Weaving Machine Key Players Market Share List
- Table 2020-2030 North America Weaving Machine Demand List by Type
- Table 2020-2025 North America Weaving Machine Price List by Type
- Table 2020-2030 United States Weaving Machine Market Size and Market Volume List
- Table 2020-2030 United States Weaving Machine Import & Export List
- Table 2020-2030 Canada Weaving Machine Market Size and Market Volume List
- Table 2020-2030 Canada Weaving Machine Import & Export List
- Table 2020-2030 Mexico Weaving Machine Market Size and Market Volume List
- Table 2020-2030 Mexico Weaving Machine Import & Export List
- Table 2020-2030 South America Weaving Machine Market Size and Market Volume List
- Figure 2020-2030 South America Weaving Machine Market Size and CAGR
- Figure 2020-2030 South America Weaving Machine Market Volume and CAGR
- Table 2020-2030 South America Weaving Machine Demand List by Application
- Table 2020-2025 South America Weaving Machine Key Players Sales List
- Table 2020-2025 South America Weaving Machine Key Players Market Share List
- Table 2020-2030 South America Weaving Machine Demand List by Type
- Table 2020-2025 South America Weaving Machine Price List by Type
- Table 2020-2030 Brazil Weaving Machine Market Size and Market Volume List
- Table 2020-2030 Brazil Weaving Machine Import & Export List
- Table 2020-2030 Argentina Weaving Machine Market Size and Market Volume List
- Table 2020-2030 Argentina Weaving Machine Import & Export List
- Table 2020-2030 Chile Weaving Machine Market Size and Market Volume List
- Table 2020-2030 Chile Weaving Machine Import & Export List
- Table 2020-2030 Peru Weaving Machine Market Size and Market Volume List
- Table 2020-2030 Peru Weaving Machine Import & Export List
- Table 2020-2030 Asia & Pacific Weaving Machine Market Size and Market Volume List
- Figure 2020-2030 Asia & Pacific Weaving Machine Market Size and CAGR
- Figure 2020-2030 Asia & Pacific Weaving Machine Market Volume and CAGR
- Table 2020-2030 Asia & Pacific Weaving Machine Demand List by Application
- Table 2020-2025 Asia & Pacific Weaving Machine Key Players Sales List
- Table 2020-2025 Asia & Pacific Weaving Machine Key Players Market Share List
- Table 2020-2030 Asia & Pacific Weaving Machine Demand List by Type
- Table 2020-2025 Asia & Pacific Weaving Machine Price List by Type
- Table 2020-2030 China Weaving Machine Market Size and Market Volume List
- Table 2020-2030 China Weaving Machine Import & Export List
- Table 2020-2030 India Weaving Machine Market Size and Market Volume List
- Table 2020-2030 India Weaving Machine Import & Export List
- Table 2020-2030 Japan Weaving Machine Market Size and Market Volume List
- Table 2020-2030 Japan Weaving Machine Import & Export List
- Table 2020-2030 South Korea Weaving Machine Market Size and Market Volume List
- Table 2020-2030 South Korea Weaving Machine Import & Export List
- Table 2020-2030 Southeast Asia Weaving Machine Market Size List
- Table 2020-2030 Southeast Asia Weaving Machine Market Volume List
- Table 2020-2030 Southeast Asia Weaving Machine Import List
- Table 2020-2030 Southeast Asia Weaving Machine Export List
- Table 2020-2030 Australia Weaving Machine Market Size and Market Volume List
- Table 2020-2030 Australia Weaving Machine Import & Export List
- Table 2020-2030 Europe Weaving Machine Market Size and Market Volume List
- Figure 2020-2030 Europe Weaving Machine Market Size and CAGR
- Figure 2020-2030 Europe Weaving Machine Market Volume and CAGR
- Table 2020-2030 Europe Weaving Machine Demand List by Application
- Table 2020-2025 Europe Weaving Machine Key Players Sales List
- Table 2020-2025 Europe Weaving Machine Key Players Market Share List
- Table 2020-2030 Europe Weaving Machine Demand List by Type
- Table 2020-2025 Europe Weaving Machine Price List by Type
- Table 2020-2030 Germany Weaving Machine Market Size and Market Volume List
- Table 2020-2030 Germany Weaving Machine Import & Export List
- Table 2020-2030 France Weaving Machine Market Size and Market Volume List
- Table 2020-2030 France Weaving Machine Import & Export List
- Table 2020-2030 United Kingdom Weaving Machine Market Size and Market Volume List
- Table 2020-2030 United Kingdom Weaving Machine Import & Export List
- Table 2020-2030 Italy Weaving Machine Market Size and Market Volume List
- Table 2020-2030 Italy Weaving Machine Import & Export List
- Table 2020-2030 Spain Weaving Machine Market Size and Market Volume List
- Table 2020-2030 Spain Weaving Machine Import & Export List
- Table 2020-2030 Belgium Weaving Machine Market Size and Market Volume List
- Table 2020-2030 Belgium Weaving Machine Import & Export List
- Table 2020-2030 Netherlands Weaving Machine Market Size and Market Volume List
- Table 2020-2030 Netherlands Weaving Machine Import & Export List
- Table 2020-2030 Austria Weaving Machine Market Size and Market Volume List
- Table 2020-2030 Austria Weaving Machine Import & Export List
- Table 2020-2030 Poland Weaving Machine Market Size and Market Volume List
- Table 2020-2030 Poland Weaving Machine Import & Export List
- Table 2020-2030 Russia Weaving Machine Market Size and Market Volume List
- Table 2020-2030 Russia Weaving Machine Import & Export List
- Table 2020-2030 MEA Weaving Machine Market Size and Market Volume List
- Figure 2020-2030 MEA Weaving Machine Market Size and CAGR
- Figure 2020-2030 MEA Weaving Machine Market Volume and CAGR
- Table 2020-2030 MEA Weaving Machine Demand List by Application
- Table 2020-2025 MEA Weaving Machine Key Players Sales List
- Table 2020-2025 MEA Weaving Machine Key Players Market Share List
- Table 2020-2030 MEA Weaving Machine Demand List by Type
- Table 2020-2025 MEA Weaving Machine Price List by Type
- Table 2020-2030 Egypt Weaving Machine Market Size and Market Volume List
- Table 2020-2030 Egypt Weaving Machine Import & Export List
- Table 2020-2030 Israel Weaving Machine Market Size and Market Volume List
- Table 2020-2030 Israel Weaving Machine Import & Export List
- Table 2020-2030 South Africa Weaving Machine Market Size and Market Volume List
- Table 2020-2030 South Africa Weaving Machine Import & Export List
- Table 2020-2030 Gulf Cooperation Council Countries Weaving Machine Market Size and Market Volume List
- Table 2020-2030 Gulf Cooperation Council Countries Weaving Machine Import & Export List
- Table 2020-2030 Turkey Weaving Machine Market Size and Market Volume List
- Table 2020-2030 Turkey Weaving Machine Import & Export List
- Table 2020-2025 Global Weaving Machine Market Size List by Region
- Table 2020-2025 Global Weaving Machine Market Size Share List by Region
- Table 2020-2025 Global Weaving Machine Market Volume List by Region
- Table 2020-2025 Global Weaving Machine Market Volume Share List by Region
- Table 2020-2025 Global Weaving Machine Demand List by Application
- Table 2020-2025 Global Weaving Machine Demand Market Share List by Application
- Table 2020-2025 Global Weaving Machine Key Vendors Sales List
- Table 2020-2025 Global Weaving Machine Key Vendors Sales Share List
- Figure 2020-2025 Global Weaving Machine Market Volume and Growth Rate
- Table 2020-2025 Global Weaving Machine Key Vendors Revenue List
- Figure 2020-2025 Global Weaving Machine Market Size and Growth Rate
- Table 2020-2025 Global Weaving Machine Key Vendors Revenue Share List
- Table 2020-2025 Global Weaving Machine Demand List by Type
- Table 2020-2025 Global Weaving Machine Demand Market Share List by Type
- Table 2020-2025 Regional Weaving Machine Price List
- Table 2025-2030 Global Weaving Machine Market Size List by Region
- Table 2025-2030 Global Weaving Machine Market Size Share List by Region
- Table 2025-2030 Global Weaving Machine Market Volume List by Region
- Table 2025-2030 Global Weaving Machine Market Volume Share List by Region
- Table 2025-2030 Global Weaving Machine Demand List by Application
- Table 2025-2030 Global Weaving Machine Demand Market Share List by Application
- Table 2025-2030 Global Weaving Machine Key Vendors Sales List
- Table 2025-2030 Global Weaving Machine Key Vendors Sales Share List
- Figure 2025-2030 Global Weaving Machine Market Volume and Growth Rate
- Table 2025-2030 Global Weaving Machine Key Vendors Revenue List
- Figure 2025-2030 Global Weaving Machine Market Size and Growth Rate
- Table 2025-2030 Global Weaving Machine Key Vendors Revenue Share List
- Table 2025-2030 Global Weaving Machine Demand List by Type
- Table 2025-2030 Global Weaving Machine Demand Market Share List by Type
- Table 2025-2030 Weaving Machine Regional Price List
- Table Lindauer DORNIER GmbH Information
- Table SWOT Analysis of Lindauer DORNIER GmbH
- Table 2020-2025 Lindauer DORNIER GmbH Weaving Machine Sale Volume Price Cost Revenue
- Figure 2020-2025 Lindauer DORNIER GmbH Weaving Machine Sale Volume and Growth Rate
- Figure 2020-2025 Lindauer DORNIER GmbH Weaving Machine Market Share
- Table Toyota Industries Corporation Information
- Table SWOT Analysis of Toyota Industries Corporation
- Table 2020-2025 Toyota Industries Corporation Weaving Machine Sale Volume Price Cost Revenue
- Figure 2020-2025 Toyota Industries Corporation Weaving Machine Sale Volume and Growth Rate
- Figure 2020-2025 Toyota Industries Corporation Weaving Machine Market Share
- Table Tsudakoma Information
- Table SWOT Analysis of Tsudakoma
- Table 2020-2025 Tsudakoma Weaving Machine Sale Volume Price Cost Revenue
- Figure 2020-2025 Tsudakoma Weaving Machine Sale Volume and Growth Rate
- Figure 2020-2025 Tsudakoma Weaving Machine Market Share
- Table Picanol Information
- Table SWOT Analysis of Picanol
- Table 2020-2025 Picanol Weaving Machine Sale Volume Price Cost Revenue
- Figure 2020-2025 Picanol Weaving Machine Sale Volume and Growth Rate
- Figure 2020-2025 Picanol Weaving Machine Market Share
- Table Itema Information
- Table SWOT Analysis of Itema
- Table 2020-2025 Itema Weaving Machine Sale Volume Price Cost Revenue
- Figure 2020-2025 Itema Weaving Machine Sale Volume and Growth Rate
- Figure 2020-2025 Itema Weaving Machine Market Share
- Table Zhejiang Taitan Information
- Table SWOT Analysis of Zhejiang Taitan
- Table 2020-2025 Zhejiang Taitan Weaving Machine Sale Volume Price Cost Revenue
- Figure 2020-2025 Zhejiang Taitan Weaving Machine Sale Volume and Growth Rate
- Figure 2020-2025 Zhejiang Taitan Weaving Machine Market Share
- Table JINGWEI Textile Machinery Information
- Table SWOT Analysis of JINGWEI Textile Machinery
- Table 2020-2025 JINGWEI Textile Machinery Weaving Machine Sale Volume Price Cost Revenue
- Figure 2020-2025 JINGWEI Textile Machinery Weaving Machine Sale Volume and Growth Rate
- Figure 2020-2025 JINGWEI Textile Machinery Weaving Machine Market Share
- Table Rifa Information
- Table SWOT Analysis of Rifa
- Table 2020-2025 Rifa Weaving Machine Sale Volume Price Cost Revenue
- Figure 2020-2025 Rifa Weaving Machine Sale Volume and Growth Rate
- Figure 2020-2025 Rifa Weaving Machine Market Share
Pricing
Currency Rates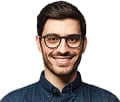
Questions or Comments?
Our team has the ability to search within reports to verify it suits your needs. We can also help maximize your budget by finding sections of reports you can purchase.