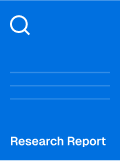
Valves and Nozzles for Plastics Processing Equipment Global Market Insights 2025, Analysis and Forecast to 2030, by Manufacturers, Regions, Technology, Application
Description
Valves and Nozzles for Plastics Processing Equipment Market Summary
Valves and nozzles for plastics processing equipment are critical components in the plastics manufacturing industry, enabling precise control of molten plastic flow in various production processes. These components ensure accurate delivery of plastic melt into molds or through extrusion systems, impacting the quality, efficiency, and consistency of plastic products. Valves regulate the flow, pressure, and direction of molten plastics, while nozzles facilitate the injection or extrusion of materials into desired shapes. These components are integral to a range of plastics processing techniques, including injection molding, blow molding, blown film extrusion, cast film extrusion, plastic sheet extrusion, plastic pipe and profile extrusion, wire and cable extrusion, and plastic recycling. The plastics processing industry is driven by growing demand for lightweight, durable, and cost-effective plastic products across sectors such as automotive, packaging, construction, and healthcare. According to industry insights, the global plastics industry supports a wide range of applications, with injection molding alone accounting for significant production volumes due to its versatility in creating complex, high-precision components. The market for valves and nozzles is characterized by high technical requirements, as these components must withstand high temperatures, pressures, and corrosive materials while maintaining precision. Emerging trends include the integration of Industry 4.0 technologies, such as automation and smart sensors, to enhance operational efficiency, alongside a shift toward sustainable materials and recycling processes. However, challenges such as high production costs, material compatibility issues, and the need for specialized engineering expertise pose constraints to market growth.
Market Size and Growth Forecast
The global market for valves and nozzles for plastics processing equipment is projected to reach USD 2.5–3.0 billion by 2025, with an estimated compound annual growth rate (CAGR) of 4%–6% through 2030. This growth is driven by the increasing adoption of plastics in industries such as automotive, packaging, and healthcare, coupled with advancements in processing technologies and rising demand for sustainable manufacturing solutions.
Regional Analysis
Asia Pacific is expected to lead the market for valves and nozzles for plastics processing equipment, with a growth rate of 5%–7% through 2030. China dominates as the largest producer and consumer of plastic products, driven by its expansive manufacturing base and growing demand for packaging, automotive components, and construction materials. India is witnessing rapid growth due to increasing industrialization and infrastructure development, boosting demand for high-performance valves and nozzles in injection molding and extrusion processes. Japan’s focus on precision engineering and advanced manufacturing technologies supports steady demand for these components in high-tech applications.
North America follows with a growth rate of 4%–5.5%, led by the United States, where the automotive and packaging industries drive demand for precision-engineered valves and nozzles. The U.S. benefits from robust research and development ecosystems and a shift toward lightweight plastic components to improve fuel efficiency in vehicles. Canada’s market is supported by growing investments in sustainable manufacturing and recycling technologies.
Europe, with a growth rate of 4%–5%, is driven by countries like Germany and Italy, which are hubs for advanced plastics processing machinery. Germany’s emphasis on eco-friendly manufacturing and stringent environmental regulations encourages the adoption of advanced valves and nozzles for recycling and biodegradable material processing. The UK and France also contribute through demand in packaging and medical device production.
South America, with a growth rate of 3.5%–5%, sees demand in Brazil and Mexico, driven by expanding automotive and construction sectors. However, limited infrastructure and economic volatility constrain broader market penetration in the region.
The Middle East and Africa, with a growth rate of 3%–4.5%, exhibit emerging potential, particularly in the UAE and South Africa. Urbanization and investments in industrial infrastructure drive demand, though economic disparities and limited technical expertise pose challenges.
Application Analysis
Injection Molding: Expected to grow at 4.5%–6.5%, this segment dominates due to its widespread use in producing precision components for automotive, healthcare, and consumer goods. Valves and nozzles in injection molding ensure accurate melt flow into molds, with trends focusing on automation and energy-efficient systems to reduce production costs.
Blow Molding: With a growth rate of 4%–6%, blow molding relies on nozzles to form hollow plastic parts like bottles and containers. The segment benefits from rising demand for packaging in food and beverage industries, with trends toward lightweight and recyclable materials.
Blown Film Extrusion: Projected to grow at 4%–5.5%, this application uses nozzles to produce thin plastic films for packaging and agricultural uses. Advancements in multilayer film production and sustainable materials are driving growth.
Cast Film Extrusion: With a growth rate of 3.5%–5%, cast film extrusion relies on precise nozzles for high-quality films used in packaging and medical applications. Trends include the adoption of high-performance materials and automation for improved consistency.
Plastic Sheet Extrusion: Expected to grow at 3.5%–5%, this segment supports construction and packaging applications. Valves and nozzles ensure uniform sheet thickness, with trends toward eco-friendly materials and energy-efficient processes.
Plastic Pipe and Profile Extrusion: With a growth rate of 4%–5.5%, this application serves construction and infrastructure needs. The demand for durable, corrosion-resistant pipes drives the need for advanced valves and nozzles, with trends focusing on automation and material efficiency.
Wire & Cable Extrusion: Projected to grow at 3%–4.5%, this segment uses nozzles to coat wires and cables with insulating plastics. Growth is driven by increasing demand for electrical infrastructure, with trends toward high-performance polymers.
Plastic Recycling: Expected to grow at 4.5%–6%, this segment is gaining traction due to global sustainability goals. Valves and nozzles designed for processing recycled plastics are critical, with trends focusing on equipment durability and compatibility with diverse materials.
Others: With a growth rate of 3%–4.5%, this category includes niche applications like 3D printing and specialty molding. Emerging trends involve precision nozzles for advanced manufacturing processes.
Key Market Players
Xaloy: A U.S.-based company specializing in high-performance components for plastics processing, Xaloy provides advanced nozzles and valves for injection molding and extrusion, focusing on durability and precision for demanding applications.
Reifenhauser: A German leader in plastics extrusion technology, Reifenhauser offers specialized valves and nozzles for blown film, cast film, and sheet extrusion, emphasizing innovation and sustainability in its solutions.
Ningbo Tan Star: A Chinese manufacturer, Ningbo Tan Star focuses on cost-effective valves and nozzles for injection molding and extrusion, catering to the growing demand in Asia Pacific’s plastics processing industry.
Zhoushan Tongda: Another Chinese firm, Zhoushan Tongda provides high-quality nozzles and valves for various plastics processing applications, with a focus on scalability and reliability for large-scale manufacturing.
Porter’s Five Forces Analysis
Threat of New Entrants: Moderate. The market has significant barriers to entry, including high capital investment for precision manufacturing and the need for specialized engineering expertise. Established players like Reifenhauser and Xaloy benefit from brand reputation, but emerging manufacturers in China, such as Ningbo Tan Star, increase competition with cost-competitive offerings.
Threat of Substitutes: Low to Moderate. Alternative flow control technologies, such as manual systems or lower-cost components, exist but are less effective in high-precision applications like injection molding. The critical role of valves and nozzles in ensuring product quality limits substitute adoption.
Bargaining Power of Buyers: Moderate to High. Large plastics processing equipment manufacturers, such as Husky and Engel, have significant negotiating power due to bulk purchasing and access to multiple suppliers, particularly in Asia Pacific. However, the specialized nature of high-performance valves and nozzles limits switching options in premium applications.
Bargaining Power of Suppliers: Moderate. Suppliers of raw materials, such as high-grade alloys and polymers, hold some leverage due to the specialized nature of inputs. However, vertical integration by major players and the availability of alternative suppliers in China balance this power.
Competitive Rivalry: High. The market is highly competitive, with key players like Xaloy, Reifenhauser, Ningbo Tan Star, and Zhoushan Tongda vying for market share through innovation, quality, and pricing. The push for automation, sustainability, and compatibility with recycled materials intensifies rivalry.
Market Opportunities and Challenges
Opportunities
Growing Plastics Demand: The rising use of plastics in automotive, packaging, and healthcare, driven by lightweighting and cost-efficiency trends, boosts demand for high-performance valves and nozzles.
Sustainability and Recycling: Global emphasis on circular economy principles creates opportunities for valves and nozzles designed for processing recycled and biodegradable plastics, particularly in Europe and North America.
Industry 4.0 Integration: The adoption of automation, IoT, and smart sensors in plastics processing equipment enhances demand for advanced valves and nozzles with real-time monitoring capabilities.
Emerging Markets Expansion: Rapid industrialization in Asia Pacific, Latin America, and Africa offers growth potential as demand for plastics processing equipment rises in these regions.
Technological Advancements: Innovations in material science and precision engineering open new applications for valves and nozzles, supporting market expansion in high-tech industries.
Challenges
High Production Costs: The complex manufacturing processes for high-performance valves and nozzles increase costs, limiting affordability in price-sensitive markets.
Material Compatibility Issues: The need for components to withstand diverse plastic materials, including corrosive or recycled polymers, poses technical challenges.
Supply Chain Constraints: Dependency on specialized raw materials and precision components exposes the market to supply chain risks, including geopolitical disruptions.
Regulatory Pressures: Stringent environmental and safety regulations, particularly in Europe, increase compliance costs and delay product development.
Skilled Workforce Shortages: The need for specialized engineering expertise to design and maintain advanced valves and nozzles is a challenge, especially in developing regions.
Valves and nozzles for plastics processing equipment are critical components in the plastics manufacturing industry, enabling precise control of molten plastic flow in various production processes. These components ensure accurate delivery of plastic melt into molds or through extrusion systems, impacting the quality, efficiency, and consistency of plastic products. Valves regulate the flow, pressure, and direction of molten plastics, while nozzles facilitate the injection or extrusion of materials into desired shapes. These components are integral to a range of plastics processing techniques, including injection molding, blow molding, blown film extrusion, cast film extrusion, plastic sheet extrusion, plastic pipe and profile extrusion, wire and cable extrusion, and plastic recycling. The plastics processing industry is driven by growing demand for lightweight, durable, and cost-effective plastic products across sectors such as automotive, packaging, construction, and healthcare. According to industry insights, the global plastics industry supports a wide range of applications, with injection molding alone accounting for significant production volumes due to its versatility in creating complex, high-precision components. The market for valves and nozzles is characterized by high technical requirements, as these components must withstand high temperatures, pressures, and corrosive materials while maintaining precision. Emerging trends include the integration of Industry 4.0 technologies, such as automation and smart sensors, to enhance operational efficiency, alongside a shift toward sustainable materials and recycling processes. However, challenges such as high production costs, material compatibility issues, and the need for specialized engineering expertise pose constraints to market growth.
Market Size and Growth Forecast
The global market for valves and nozzles for plastics processing equipment is projected to reach USD 2.5–3.0 billion by 2025, with an estimated compound annual growth rate (CAGR) of 4%–6% through 2030. This growth is driven by the increasing adoption of plastics in industries such as automotive, packaging, and healthcare, coupled with advancements in processing technologies and rising demand for sustainable manufacturing solutions.
Regional Analysis
Asia Pacific is expected to lead the market for valves and nozzles for plastics processing equipment, with a growth rate of 5%–7% through 2030. China dominates as the largest producer and consumer of plastic products, driven by its expansive manufacturing base and growing demand for packaging, automotive components, and construction materials. India is witnessing rapid growth due to increasing industrialization and infrastructure development, boosting demand for high-performance valves and nozzles in injection molding and extrusion processes. Japan’s focus on precision engineering and advanced manufacturing technologies supports steady demand for these components in high-tech applications.
North America follows with a growth rate of 4%–5.5%, led by the United States, where the automotive and packaging industries drive demand for precision-engineered valves and nozzles. The U.S. benefits from robust research and development ecosystems and a shift toward lightweight plastic components to improve fuel efficiency in vehicles. Canada’s market is supported by growing investments in sustainable manufacturing and recycling technologies.
Europe, with a growth rate of 4%–5%, is driven by countries like Germany and Italy, which are hubs for advanced plastics processing machinery. Germany’s emphasis on eco-friendly manufacturing and stringent environmental regulations encourages the adoption of advanced valves and nozzles for recycling and biodegradable material processing. The UK and France also contribute through demand in packaging and medical device production.
South America, with a growth rate of 3.5%–5%, sees demand in Brazil and Mexico, driven by expanding automotive and construction sectors. However, limited infrastructure and economic volatility constrain broader market penetration in the region.
The Middle East and Africa, with a growth rate of 3%–4.5%, exhibit emerging potential, particularly in the UAE and South Africa. Urbanization and investments in industrial infrastructure drive demand, though economic disparities and limited technical expertise pose challenges.
Application Analysis
Injection Molding: Expected to grow at 4.5%–6.5%, this segment dominates due to its widespread use in producing precision components for automotive, healthcare, and consumer goods. Valves and nozzles in injection molding ensure accurate melt flow into molds, with trends focusing on automation and energy-efficient systems to reduce production costs.
Blow Molding: With a growth rate of 4%–6%, blow molding relies on nozzles to form hollow plastic parts like bottles and containers. The segment benefits from rising demand for packaging in food and beverage industries, with trends toward lightweight and recyclable materials.
Blown Film Extrusion: Projected to grow at 4%–5.5%, this application uses nozzles to produce thin plastic films for packaging and agricultural uses. Advancements in multilayer film production and sustainable materials are driving growth.
Cast Film Extrusion: With a growth rate of 3.5%–5%, cast film extrusion relies on precise nozzles for high-quality films used in packaging and medical applications. Trends include the adoption of high-performance materials and automation for improved consistency.
Plastic Sheet Extrusion: Expected to grow at 3.5%–5%, this segment supports construction and packaging applications. Valves and nozzles ensure uniform sheet thickness, with trends toward eco-friendly materials and energy-efficient processes.
Plastic Pipe and Profile Extrusion: With a growth rate of 4%–5.5%, this application serves construction and infrastructure needs. The demand for durable, corrosion-resistant pipes drives the need for advanced valves and nozzles, with trends focusing on automation and material efficiency.
Wire & Cable Extrusion: Projected to grow at 3%–4.5%, this segment uses nozzles to coat wires and cables with insulating plastics. Growth is driven by increasing demand for electrical infrastructure, with trends toward high-performance polymers.
Plastic Recycling: Expected to grow at 4.5%–6%, this segment is gaining traction due to global sustainability goals. Valves and nozzles designed for processing recycled plastics are critical, with trends focusing on equipment durability and compatibility with diverse materials.
Others: With a growth rate of 3%–4.5%, this category includes niche applications like 3D printing and specialty molding. Emerging trends involve precision nozzles for advanced manufacturing processes.
Key Market Players
Xaloy: A U.S.-based company specializing in high-performance components for plastics processing, Xaloy provides advanced nozzles and valves for injection molding and extrusion, focusing on durability and precision for demanding applications.
Reifenhauser: A German leader in plastics extrusion technology, Reifenhauser offers specialized valves and nozzles for blown film, cast film, and sheet extrusion, emphasizing innovation and sustainability in its solutions.
Ningbo Tan Star: A Chinese manufacturer, Ningbo Tan Star focuses on cost-effective valves and nozzles for injection molding and extrusion, catering to the growing demand in Asia Pacific’s plastics processing industry.
Zhoushan Tongda: Another Chinese firm, Zhoushan Tongda provides high-quality nozzles and valves for various plastics processing applications, with a focus on scalability and reliability for large-scale manufacturing.
Porter’s Five Forces Analysis
Threat of New Entrants: Moderate. The market has significant barriers to entry, including high capital investment for precision manufacturing and the need for specialized engineering expertise. Established players like Reifenhauser and Xaloy benefit from brand reputation, but emerging manufacturers in China, such as Ningbo Tan Star, increase competition with cost-competitive offerings.
Threat of Substitutes: Low to Moderate. Alternative flow control technologies, such as manual systems or lower-cost components, exist but are less effective in high-precision applications like injection molding. The critical role of valves and nozzles in ensuring product quality limits substitute adoption.
Bargaining Power of Buyers: Moderate to High. Large plastics processing equipment manufacturers, such as Husky and Engel, have significant negotiating power due to bulk purchasing and access to multiple suppliers, particularly in Asia Pacific. However, the specialized nature of high-performance valves and nozzles limits switching options in premium applications.
Bargaining Power of Suppliers: Moderate. Suppliers of raw materials, such as high-grade alloys and polymers, hold some leverage due to the specialized nature of inputs. However, vertical integration by major players and the availability of alternative suppliers in China balance this power.
Competitive Rivalry: High. The market is highly competitive, with key players like Xaloy, Reifenhauser, Ningbo Tan Star, and Zhoushan Tongda vying for market share through innovation, quality, and pricing. The push for automation, sustainability, and compatibility with recycled materials intensifies rivalry.
Market Opportunities and Challenges
Opportunities
Growing Plastics Demand: The rising use of plastics in automotive, packaging, and healthcare, driven by lightweighting and cost-efficiency trends, boosts demand for high-performance valves and nozzles.
Sustainability and Recycling: Global emphasis on circular economy principles creates opportunities for valves and nozzles designed for processing recycled and biodegradable plastics, particularly in Europe and North America.
Industry 4.0 Integration: The adoption of automation, IoT, and smart sensors in plastics processing equipment enhances demand for advanced valves and nozzles with real-time monitoring capabilities.
Emerging Markets Expansion: Rapid industrialization in Asia Pacific, Latin America, and Africa offers growth potential as demand for plastics processing equipment rises in these regions.
Technological Advancements: Innovations in material science and precision engineering open new applications for valves and nozzles, supporting market expansion in high-tech industries.
Challenges
High Production Costs: The complex manufacturing processes for high-performance valves and nozzles increase costs, limiting affordability in price-sensitive markets.
Material Compatibility Issues: The need for components to withstand diverse plastic materials, including corrosive or recycled polymers, poses technical challenges.
Supply Chain Constraints: Dependency on specialized raw materials and precision components exposes the market to supply chain risks, including geopolitical disruptions.
Regulatory Pressures: Stringent environmental and safety regulations, particularly in Europe, increase compliance costs and delay product development.
Skilled Workforce Shortages: The need for specialized engineering expertise to design and maintain advanced valves and nozzles is a challenge, especially in developing regions.
Table of Contents
85 Pages
- Chapter 1 Executive Summary
- Chapter 2 Abbreviation and Acronyms
- Chapter 3 Preface
- 3.1 Research Scope
- 3.2 Research Sources
- 3.2.1 Data Sources
- 3.2.2 Assumptions
- 3.3 Research Method
- Chapter 4 Market Landscape
- 4.1 Market Overview
- 4.2 Classification/Types
- 4.3 Application/End Users
- Chapter 5 Market Trend Analysis
- 5.1 Introduction
- 5.2 Drivers
- 5.3 Restraints
- 5.4 Opportunities
- 5.5 Threats
- Chapter 6 Industry Chain Analysis
- 6.1 Upstream/Suppliers Analysis
- 6.2 Valves and Nozzles For Plastics Processing Equipment Analysis
- 6.2.1 Technology Analysis
- 6.2.2 Cost Analysis
- 6.2.3 Market Channel Analysis
- 6.3 Downstream Buyers/End Users
- Chapter 7 Latest Market Dynamics
- 7.1 Latest News
- 7.2 Merger and Acquisition
- 7.3 Planned/Future Project
- 7.4 Policy Dynamics
- Chapter 8 Trading Analysis
- 8.1 Export of Valves and Nozzles For Plastics Processing Equipment by Region
- 8.2 Import of Valves and Nozzles For Plastics Processing Equipment by Region
- 8.3 Balance of Trade
- Chapter 9 Historical and Forecast Valves and Nozzles For Plastics Processing Equipment Market in North America (2020-2030)
- 9.1 Valves and Nozzles For Plastics Processing Equipment Market Size
- 9.2 Valves and Nozzles For Plastics Processing Equipment Demand by End Use
- 9.3 Competition by Players/Suppliers
- 9.4 Type Segmentation and Price
- 9.5 Key Countries Analysis
- 9.5.1 United States
- 9.5.2 Canada
- 9.5.3 Mexico
- Chapter 10 Historical and Forecast Valves and Nozzles For Plastics Processing Equipment Market in South America (2020-2030)
- 10.1 Valves and Nozzles For Plastics Processing Equipment Market Size
- 10.2 Valves and Nozzles For Plastics Processing Equipment Demand by End Use
- 10.3 Competition by Players/Suppliers
- 10.4 Type Segmentation and Price
- 10.5 Key Countries Analysis
- 10.5.1 Brazil
- 10.5.2 Argentina
- 10.5.3 Chile
- 10.5.4 Peru
- Chapter 11 Historical and Forecast Valves and Nozzles For Plastics Processing Equipment Market in Asia & Pacific (2020-2030)
- 11.1 Valves and Nozzles For Plastics Processing Equipment Market Size
- 11.2 Valves and Nozzles For Plastics Processing Equipment Demand by End Use
- 11.3 Competition by Players/Suppliers
- 11.4 Type Segmentation and Price
- 11.5 Key Countries Analysis
- 11.5.1 China
- 11.5.2 India
- 11.5.3 Japan
- 11.5.4 South Korea
- 11.5.5 Southest Asia
- 11.5.6 Australia
- Chapter 12 Historical and Forecast Valves and Nozzles For Plastics Processing Equipment Market in Europe (2020-2030)
- 12.1 Valves and Nozzles For Plastics Processing Equipment Market Size
- 12.2 Valves and Nozzles For Plastics Processing Equipment Demand by End Use
- 12.3 Competition by Players/Suppliers
- 12.4 Type Segmentation and Price
- 12.5 Key Countries Analysis
- 12.5.1 Germany
- 12.5.2 France
- 12.5.3 United Kingdom
- 12.5.4 Italy
- 12.5.5 Spain
- 12.5.6 Belgium
- 12.5.7 Netherlands
- 12.5.8 Austria
- 12.5.9 Poland
- 12.5.10 Russia
- Chapter 13 Historical and Forecast Valves and Nozzles For Plastics Processing Equipment Market in MEA (2020-2030)
- 13.1 Valves and Nozzles For Plastics Processing Equipment Market Size
- 13.2 Valves and Nozzles For Plastics Processing Equipment Demand by End Use
- 13.3 Competition by Players/Suppliers
- 13.4 Type Segmentation and Price
- 13.5 Key Countries Analysis
- 13.5.1 Egypt
- 13.5.2 Israel
- 13.5.3 South Africa
- 13.5.4 Gulf Cooperation Council Countries
- 13.5.5 Turkey
- Chapter 14 Summary For Global Valves and Nozzles For Plastics Processing Equipment Market (2020-2025)
- 14.1 Valves and Nozzles For Plastics Processing Equipment Market Size
- 14.2 Valves and Nozzles For Plastics Processing Equipment Demand by End Use
- 14.3 Competition by Players/Suppliers
- 14.4 Type Segmentation and Price
- Chapter 15 Global Valves and Nozzles For Plastics Processing Equipment Market Forecast (2025-2030)
- 15.1 Valves and Nozzles For Plastics Processing Equipment Market Size Forecast
- 15.2 Valves and Nozzles For Plastics Processing Equipment Demand Forecast
- 15.3 Competition by Players/Suppliers
- 15.4 Type Segmentation and Price Forecast
- Chapter 16 Analysis of Global Key Vendors
- 16.1 Xaloy
- 16.1.1 Company Profile
- 16.1.2 Main Business and Valves and Nozzles for Plastics Processing Equipment Information
- 16.1.3 SWOT Analysis of Xaloy
- 16.1.4 Xaloy Valves and Nozzles for Plastics Processing Equipment Sales, Revenue, Price and Gross Margin (2020-2025)
- 16.2 Reifenhauser
- 16.2.1 Company Profile
- 16.2.2 Main Business and Valves and Nozzles for Plastics Processing Equipment Information
- 16.2.3 SWOT Analysis of Reifenhauser
- 16.2.4 Reifenhauser Valves and Nozzles for Plastics Processing Equipment Sales, Revenue, Price and Gross Margin (2020-2025)
- 16.3 Ningbo Tan Star
- 16.3.1 Company Profile
- 16.3.2 Main Business and Valves and Nozzles for Plastics Processing Equipment Information
- 16.3.3 SWOT Analysis of Ningbo Tan Star
- 16.3.4 Ningbo Tan Star Valves and Nozzles for Plastics Processing Equipment Sales, Revenue, Price and Gross Margin (2020-2025)
- 16.4 Zhoushan Tongda
- 16.4.1 Company Profile
- 16.4.2 Main Business and Valves and Nozzles for Plastics Processing Equipment Information
- 16.4.3 SWOT Analysis of Zhoushan Tongda
- 16.4.4 Zhoushan Tongda Valves and Nozzles for Plastics Processing Equipment Sales, Revenue, Price and Gross Margin (2020-2025)
- Please ask for sample pages for full companies list
- Tables and Figures
- Table Abbreviation and Acronyms List
- Table Research Scope of Valves and Nozzles For Plastics Processing Equipment Report
- Table Data Sources of Valves and Nozzles For Plastics Processing Equipment Report
- Table Major Assumptions of Valves and Nozzles For Plastics Processing Equipment Report
- Figure Market Size Estimated Method
- Figure Major Forecasting Factors
- Figure Valves and Nozzles For Plastics Processing Equipment Picture
- Table Valves and Nozzles For Plastics Processing Equipment Classification
- Table Valves and Nozzles For Plastics Processing Equipment Applications List
- Table Drivers of Valves and Nozzles For Plastics Processing Equipment Market
- Table Restraints of Valves and Nozzles For Plastics Processing Equipment Market
- Table Opportunities of Valves and Nozzles For Plastics Processing Equipment Market
- Table Threats of Valves and Nozzles For Plastics Processing Equipment Market
- Table Covid-19 Impact For Valves and Nozzles For Plastics Processing Equipment Market
- Table Raw Materials Suppliers List
- Table Different Production Methods of Valves and Nozzles For Plastics Processing Equipment
- Table Cost Structure Analysis of Valves and Nozzles For Plastics Processing Equipment
- Table Key End Users List
- Table Latest News of Valves and Nozzles For Plastics Processing Equipment Market
- Table Merger and Acquisition List
- Table Planned/Future Project of Valves and Nozzles For Plastics Processing Equipment Market
- Table Policy of Valves and Nozzles For Plastics Processing Equipment Market
- Table 2020-2030 Regional Export of Valves and Nozzles For Plastics Processing Equipment
- Table 2020-2030 Regional Import of Valves and Nozzles For Plastics Processing Equipment
- Table 2020-2030 Regional Trade Balance
- Figure 2020-2030 Regional Trade Balance
- Table 2020-2030 North America Valves and Nozzles For Plastics Processing Equipment Market Size and Market Volume List
- Figure 2020-2030 North America Valves and Nozzles For Plastics Processing Equipment Market Size and CAGR
- Figure 2020-2030 North America Valves and Nozzles For Plastics Processing Equipment Market Volume and CAGR
- Table 2020-2030 North America Valves and Nozzles For Plastics Processing Equipment Demand List by Application
- Table 2020-2025 North America Valves and Nozzles For Plastics Processing Equipment Key Players Sales List
- Table 2020-2025 North America Valves and Nozzles For Plastics Processing Equipment Key Players Market Share List
- Table 2020-2030 North America Valves and Nozzles For Plastics Processing Equipment Demand List by Type
- Table 2020-2025 North America Valves and Nozzles For Plastics Processing Equipment Price List by Type
- Table 2020-2030 United States Valves and Nozzles For Plastics Processing Equipment Market Size and Market Volume List
- Table 2020-2030 United States Valves and Nozzles For Plastics Processing Equipment Import & Export List
- Table 2020-2030 Canada Valves and Nozzles For Plastics Processing Equipment Market Size and Market Volume List
- Table 2020-2030 Canada Valves and Nozzles For Plastics Processing Equipment Import & Export List
- Table 2020-2030 Mexico Valves and Nozzles For Plastics Processing Equipment Market Size and Market Volume List
- Table 2020-2030 Mexico Valves and Nozzles For Plastics Processing Equipment Import & Export List
- Table 2020-2030 South America Valves and Nozzles For Plastics Processing Equipment Market Size and Market Volume List
- Figure 2020-2030 South America Valves and Nozzles For Plastics Processing Equipment Market Size and CAGR
- Figure 2020-2030 South America Valves and Nozzles For Plastics Processing Equipment Market Volume and CAGR
- Table 2020-2030 South America Valves and Nozzles For Plastics Processing Equipment Demand List by Application
- Table 2020-2025 South America Valves and Nozzles For Plastics Processing Equipment Key Players Sales List
- Table 2020-2025 South America Valves and Nozzles For Plastics Processing Equipment Key Players Market Share List
- Table 2020-2030 South America Valves and Nozzles For Plastics Processing Equipment Demand List by Type
- Table 2020-2025 South America Valves and Nozzles For Plastics Processing Equipment Price List by Type
- Table 2020-2030 Brazil Valves and Nozzles For Plastics Processing Equipment Market Size and Market Volume List
- Table 2020-2030 Brazil Valves and Nozzles For Plastics Processing Equipment Import & Export List
- Table 2020-2030 Argentina Valves and Nozzles For Plastics Processing Equipment Market Size and Market Volume List
- Table 2020-2030 Argentina Valves and Nozzles For Plastics Processing Equipment Import & Export List
- Table 2020-2030 Chile Valves and Nozzles For Plastics Processing Equipment Market Size and Market Volume List
- Table 2020-2030 Chile Valves and Nozzles For Plastics Processing Equipment Import & Export List
- Table 2020-2030 Peru Valves and Nozzles For Plastics Processing Equipment Market Size and Market Volume List
- Table 2020-2030 Peru Valves and Nozzles For Plastics Processing Equipment Import & Export List
- Table 2020-2030 Asia & Pacific Valves and Nozzles For Plastics Processing Equipment Market Size and Market Volume List
- Figure 2020-2030 Asia & Pacific Valves and Nozzles For Plastics Processing Equipment Market Size and CAGR
- Figure 2020-2030 Asia & Pacific Valves and Nozzles For Plastics Processing Equipment Market Volume and CAGR
- Table 2020-2030 Asia & Pacific Valves and Nozzles For Plastics Processing Equipment Demand List by Application
- Table 2020-2025 Asia & Pacific Valves and Nozzles For Plastics Processing Equipment Key Players Sales List
- Table 2020-2025 Asia & Pacific Valves and Nozzles For Plastics Processing Equipment Key Players Market Share List
- Table 2020-2030 Asia & Pacific Valves and Nozzles For Plastics Processing Equipment Demand List by Type
- Table 2020-2025 Asia & Pacific Valves and Nozzles For Plastics Processing Equipment Price List by Type
- Table 2020-2030 China Valves and Nozzles For Plastics Processing Equipment Market Size and Market Volume List
- Table 2020-2030 China Valves and Nozzles For Plastics Processing Equipment Import & Export List
- Table 2020-2030 India Valves and Nozzles For Plastics Processing Equipment Market Size and Market Volume List
- Table 2020-2030 India Valves and Nozzles For Plastics Processing Equipment Import & Export List
- Table 2020-2030 Japan Valves and Nozzles For Plastics Processing Equipment Market Size and Market Volume List
- Table 2020-2030 Japan Valves and Nozzles For Plastics Processing Equipment Import & Export List
- Table 2020-2030 South Korea Valves and Nozzles For Plastics Processing Equipment Market Size and Market Volume List
- Table 2020-2030 South Korea Valves and Nozzles For Plastics Processing Equipment Import & Export List
- Table 2020-2030 Southeast Asia Valves and Nozzles For Plastics Processing Equipment Market Size List
- Table 2020-2030 Southeast Asia Valves and Nozzles For Plastics Processing Equipment Market Volume List
- Table 2020-2030 Southeast Asia Valves and Nozzles For Plastics Processing Equipment Import List
- Table 2020-2030 Southeast Asia Valves and Nozzles For Plastics Processing Equipment Export List
- Table 2020-2030 Australia Valves and Nozzles For Plastics Processing Equipment Market Size and Market Volume List
- Table 2020-2030 Australia Valves and Nozzles For Plastics Processing Equipment Import & Export List
- Table 2020-2030 Europe Valves and Nozzles For Plastics Processing Equipment Market Size and Market Volume List
- Figure 2020-2030 Europe Valves and Nozzles For Plastics Processing Equipment Market Size and CAGR
- Figure 2020-2030 Europe Valves and Nozzles For Plastics Processing Equipment Market Volume and CAGR
- Table 2020-2030 Europe Valves and Nozzles For Plastics Processing Equipment Demand List by Application
- Table 2020-2025 Europe Valves and Nozzles For Plastics Processing Equipment Key Players Sales List
- Table 2020-2025 Europe Valves and Nozzles For Plastics Processing Equipment Key Players Market Share List
- Table 2020-2030 Europe Valves and Nozzles For Plastics Processing Equipment Demand List by Type
- Table 2020-2025 Europe Valves and Nozzles For Plastics Processing Equipment Price List by Type
- Table 2020-2030 Germany Valves and Nozzles For Plastics Processing Equipment Market Size and Market Volume List
- Table 2020-2030 Germany Valves and Nozzles For Plastics Processing Equipment Import & Export List
- Table 2020-2030 France Valves and Nozzles For Plastics Processing Equipment Market Size and Market Volume List
- Table 2020-2030 France Valves and Nozzles For Plastics Processing Equipment Import & Export List
- Table 2020-2030 United Kingdom Valves and Nozzles For Plastics Processing Equipment Market Size and Market Volume List
- Table 2020-2030 United Kingdom Valves and Nozzles For Plastics Processing Equipment Import & Export List
- Table 2020-2030 Italy Valves and Nozzles For Plastics Processing Equipment Market Size and Market Volume List
- Table 2020-2030 Italy Valves and Nozzles For Plastics Processing Equipment Import & Export List
- Table 2020-2030 Spain Valves and Nozzles For Plastics Processing Equipment Market Size and Market Volume List
- Table 2020-2030 Spain Valves and Nozzles For Plastics Processing Equipment Import & Export List
- Table 2020-2030 Belgium Valves and Nozzles For Plastics Processing Equipment Market Size and Market Volume List
- Table 2020-2030 Belgium Valves and Nozzles For Plastics Processing Equipment Import & Export List
- Table 2020-2030 Netherlands Valves and Nozzles For Plastics Processing Equipment Market Size and Market Volume List
- Table 2020-2030 Netherlands Valves and Nozzles For Plastics Processing Equipment Import & Export List
- Table 2020-2030 Austria Valves and Nozzles For Plastics Processing Equipment Market Size and Market Volume List
- Table 2020-2030 Austria Valves and Nozzles For Plastics Processing Equipment Import & Export List
- Table 2020-2030 Poland Valves and Nozzles For Plastics Processing Equipment Market Size and Market Volume List
- Table 2020-2030 Poland Valves and Nozzles For Plastics Processing Equipment Import & Export List
- Table 2020-2030 Russia Valves and Nozzles For Plastics Processing Equipment Market Size and Market Volume List
- Table 2020-2030 Russia Valves and Nozzles For Plastics Processing Equipment Import & Export List
- Table 2020-2030 MEA Valves and Nozzles For Plastics Processing Equipment Market Size and Market Volume List
- Figure 2020-2030 MEA Valves and Nozzles For Plastics Processing Equipment Market Size and CAGR
- Figure 2020-2030 MEA Valves and Nozzles For Plastics Processing Equipment Market Volume and CAGR
- Table 2020-2030 MEA Valves and Nozzles For Plastics Processing Equipment Demand List by Application
- Table 2020-2025 MEA Valves and Nozzles For Plastics Processing Equipment Key Players Sales List
- Table 2020-2025 MEA Valves and Nozzles For Plastics Processing Equipment Key Players Market Share List
- Table 2020-2030 MEA Valves and Nozzles For Plastics Processing Equipment Demand List by Type
- Table 2020-2025 MEA Valves and Nozzles For Plastics Processing Equipment Price List by Type
- Table 2020-2030 Egypt Valves and Nozzles For Plastics Processing Equipment Market Size and Market Volume List
- Table 2020-2030 Egypt Valves and Nozzles For Plastics Processing Equipment Import & Export List
- Table 2020-2030 Israel Valves and Nozzles For Plastics Processing Equipment Market Size and Market Volume List
- Table 2020-2030 Israel Valves and Nozzles For Plastics Processing Equipment Import & Export List
- Table 2020-2030 South Africa Valves and Nozzles For Plastics Processing Equipment Market Size and Market Volume List
- Table 2020-2030 South Africa Valves and Nozzles For Plastics Processing Equipment Import & Export List
- Table 2020-2030 Gulf Cooperation Council Countries Valves and Nozzles For Plastics Processing Equipment Market Size and Market Volume List
- Table 2020-2030 Gulf Cooperation Council Countries Valves and Nozzles For Plastics Processing Equipment Import & Export List
- Table 2020-2030 Turkey Valves and Nozzles For Plastics Processing Equipment Market Size and Market Volume List
- Table 2020-2030 Turkey Valves and Nozzles For Plastics Processing Equipment Import & Export List
- Table 2020-2025 Global Valves and Nozzles For Plastics Processing Equipment Market Size List by Region
- Table 2020-2025 Global Valves and Nozzles For Plastics Processing Equipment Market Size Share List by Region
- Table 2020-2025 Global Valves and Nozzles For Plastics Processing Equipment Market Volume List by Region
- Table 2020-2025 Global Valves and Nozzles For Plastics Processing Equipment Market Volume Share List by Region
- Table 2020-2025 Global Valves and Nozzles For Plastics Processing Equipment Demand List by Application
- Table 2020-2025 Global Valves and Nozzles For Plastics Processing Equipment Demand Market Share List by Application
- Table 2020-2025 Global Valves and Nozzles For Plastics Processing Equipment Key Vendors Sales List
- Table 2020-2025 Global Valves and Nozzles For Plastics Processing Equipment Key Vendors Sales Share List
- Figure 2020-2025 Global Valves and Nozzles For Plastics Processing Equipment Market Volume and Growth Rate
- Table 2020-2025 Global Valves and Nozzles For Plastics Processing Equipment Key Vendors Revenue List
- Figure 2020-2025 Global Valves and Nozzles For Plastics Processing Equipment Market Size and Growth Rate
- Table 2020-2025 Global Valves and Nozzles For Plastics Processing Equipment Key Vendors Revenue Share List
- Table 2020-2025 Global Valves and Nozzles For Plastics Processing Equipment Demand List by Type
- Table 2020-2025 Global Valves and Nozzles For Plastics Processing Equipment Demand Market Share List by Type
- Table 2020-2025 Regional Valves and Nozzles For Plastics Processing Equipment Price List
- Table 2025-2030 Global Valves and Nozzles For Plastics Processing Equipment Market Size List by Region
- Table 2025-2030 Global Valves and Nozzles For Plastics Processing Equipment Market Size Share List by Region
- Table 2025-2030 Global Valves and Nozzles For Plastics Processing Equipment Market Volume List by Region
- Table 2025-2030 Global Valves and Nozzles For Plastics Processing Equipment Market Volume Share List by Region
- Table 2025-2030 Global Valves and Nozzles For Plastics Processing Equipment Demand List by Application
- Table 2025-2030 Global Valves and Nozzles For Plastics Processing Equipment Demand Market Share List by Application
- Table 2025-2030 Global Valves and Nozzles For Plastics Processing Equipment Key Vendors Sales List
- Table 2025-2030 Global Valves and Nozzles For Plastics Processing Equipment Key Vendors Sales Share List
- Figure 2025-2030 Global Valves and Nozzles For Plastics Processing Equipment Market Volume and Growth Rate
- Table 2025-2030 Global Valves and Nozzles For Plastics Processing Equipment Key Vendors Revenue List
- Figure 2025-2030 Global Valves and Nozzles For Plastics Processing Equipment Market Size and Growth Rate
- Table 2025-2030 Global Valves and Nozzles For Plastics Processing Equipment Key Vendors Revenue Share List
- Table 2025-2030 Global Valves and Nozzles For Plastics Processing Equipment Demand List by Type
- Table 2025-2030 Global Valves and Nozzles For Plastics Processing Equipment Demand Market Share List by Type
- Table 2025-2030 Valves and Nozzles For Plastics Processing Equipment Regional Price List
- Table Xaloy Information
- Table SWOT Analysis of Xaloy
- Table 2020-2025 Xaloy Valves and Nozzles for Plastics Processing Equipment Sale Volume Price Cost Revenue
- Figure 2020-2025 Xaloy Valves and Nozzles for Plastics Processing Equipment Sale Volume and Growth Rate
- Figure 2020-2025 Xaloy Valves and Nozzles for Plastics Processing Equipment Market Share
- Table Reifenhauser Information
- Table SWOT Analysis of Reifenhauser
- Table 2020-2025 Reifenhauser Valves and Nozzles for Plastics Processing Equipment Sale Volume Price Cost Revenue
- Figure 2020-2025 Reifenhauser Valves and Nozzles for Plastics Processing Equipment Sale Volume and Growth Rate
- Figure 2020-2025 Reifenhauser Valves and Nozzles for Plastics Processing Equipment Market Share
- Table Ningbo Tan Star Information
- Table SWOT Analysis of Ningbo Tan Star
- Table 2020-2025 Ningbo Tan Star Valves and Nozzles for Plastics Processing Equipment Sale Volume Price Cost Revenue
- Figure 2020-2025 Ningbo Tan Star Valves and Nozzles for Plastics Processing Equipment Sale Volume and Growth Rate
- Figure 2020-2025 Ningbo Tan Star Valves and Nozzles for Plastics Processing Equipment Market Share
- Table Zhoushan Tongda Information
- Table SWOT Analysis of Zhoushan Tongda
- Table 2020-2025 Zhoushan Tongda Valves and Nozzles for Plastics Processing Equipment Sale Volume Price Cost Revenue
- Figure 2020-2025 Zhoushan Tongda Valves and Nozzles for Plastics Processing Equipment Sale Volume and Growth Rate
- Figure 2020-2025 Zhoushan Tongda Valves and Nozzles for Plastics Processing Equipment Market Share
Pricing
Currency Rates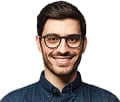
Questions or Comments?
Our team has the ability to search within reports to verify it suits your needs. We can also help maximize your budget by finding sections of reports you can purchase.