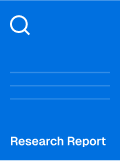
Machine Tool Spindle Global Market Insights 2025, Analysis and Forecast to 2030, by Manufacturers, Regions, Technology, Application
Description
Machine Tool Spindle Market Summary
to the Machine Tool Spindle Industry
Machine tool spindles are critical components of CNC machine tools, enabling high-speed rotation for cutting, milling, and grinding. Initially developed for internal grinding in the 1980s, electric spindles have become integral to CNC milling machines and machining centers, driven by advances in high-speed cutting technology. Spindles are one of three core high-tech components in CNC machines, alongside CNC systems and feed drives. Technical advancements focus on high power, high speed, and high rotational accuracy, with leading firms like Kessler and FISCHER setting global standards. China’s spindle industry lags behind Switzerland and Germany but is rapidly advancing. Spindles account for a significant portion of machine tool performance, supporting applications from automotive to aerospace. The industry benefits from automation and precision manufacturing trends but faces challenges from high R&D costs and technical complexity.
Market Size and Growth Forecast
The global machine tool spindle market is projected to reach USD 4.0 billion to USD 5.0 billion by 2025, with an estimated CAGR of 5% to 7% through 2030, driven by automation, high-speed machining, and industrial growth.
Regional Analysis
Asia Pacific expects a growth rate of 6% to 8%. China’s manufacturing dominance drives demand for high-speed spindles in electronics and automotive sectors. Japan focuses on precision spindles for aerospace and robotics.
North America anticipates a growth rate of 4% to 6%. The U.S. leads with aerospace and defense applications, emphasizing high-accuracy spindles. Canada’s market grows in energy and automotive sectors.
Europe projects a growth rate of 4% to 6%. Germany’s automotive and aerospace industries drive demand for advanced spindles, while the UK and France focus on precision engineering.
South America expects a growth rate of 3% to 5%. Brazil’s automotive sector supports growth, though economic constraints limit adoption.
Middle East and Africa anticipate a growth rate of 3% to 5%. The UAE’s industrial diversification drives demand, but infrastructure gaps hinder scalability.
Application Analysis
CNC Mills: Projected at 5% to 7%, CNC mills rely on high-speed spindles for automotive and electronics manufacturing. Trends include multi-axis spindles for complex geometries.
CNC Lathes: Expected at 4% to 6%, CNC lathes use spindles for precision turning, with trends toward high-torque spindles for heavy-duty applications.
CNC Plasma Cutters: Anticipated at 3% to 5%, plasma cutters require robust spindles for industrial fabrication, with steady growth.
EDM: Projected at 4% to 6%, EDM spindles support precision mold-making, with trends toward high-accuracy spindles for electronics.
CNC Water Jets: Expected at 3% to 5%, water jet spindles serve diverse materials, with moderate growth in aerospace.
Others: Anticipated at 3% to 5%, including laser cutters, with niche applications driving demand.
Key Market Players
Kessler: A German leader, Kessler develops high-RPM mill spindles.
FISCHER: A Swiss firm, FISCHER focuses on precision lathe spindles.
MCT: A German company, MCT supplies plasma cutter spindles.
IBAG: A Swiss firm, IBAG develops EDM spindles.
Novanta: A U.S. company, Novanta focuses on smart water jet spindles.
ABL: A UK firm, ABL supplies niche machining spindles.
Guangzhou Haozhi: A Chinese company, Haozhi develops high-speed spindles.
Sinomach Precision: A Chinese firm, Sinomach focuses on automotive spindles.
Wuxi Sunshine: A Chinese company, Sunshine supplies precision spindles.
Porter’s Five Forces Analysis
Threat of New Entrants: Low. High technical barriers and R&D costs deter entry, with Kessler and FISCHER dominating through innovation. Emerging players like Guangzhou Haozhi face challenges in matching precision.
Threat of Substitutes: Low. Alternative components like manual spindles lack the precision of electric spindles, giving IBAG an edge. Emerging technologies pose minimal threats.
Bargaining Power of Buyers: Moderate. Large manufacturers exert pricing pressure, but specialized spindles from MCT limit switching. Smaller buyers have less leverage.
Bargaining Power of Suppliers: High. Suppliers of bearings and motors hold leverage, impacting Sinomach Precision’s costs. Diversified sourcing by FISCHER mitigates risks.
Competitive Rivalry: High. Kessler, FISCHER, and IBAG compete on speed, accuracy, and reliability. Rapid adoption of high-speed machining intensifies rivalry.
Market Opportunities and Challenges
Opportunities
High-Speed Machining: Aerospace demand boosts Kessler’s high-accuracy spindles.
Emerging Markets: China’s manufacturing growth offers opportunities for Guangzhou Haozhi’s affordable spindles.
EV Production: Automotive shifts to EVs drive FISCHER’s precision spindles.
Digital Integration: MCT’s IoT-enabled spindles enhance productivity in electronics.
Sustainability Trends: Energy-efficient spindles from IBAG align with green manufacturing.
Aftermarket Services: Sinomach Precision’s maintenance services create revenue streams.
Technological Advancements: High-torque spindles by Kessler tap heavy-duty applications.
Challenges
High R&D Costs: Innovation pressures FISCHER’s profitability in a competitive market.
Technical Complexity: Precision requirements challenge Guangzhou Haozhi’s scalability.
Skilled Labor Shortages: Lack of expertise hinders Sinomach Precision’s growth.
Economic Volatility: Manufacturing slowdowns affect MCT’s sales in developing regions.
Component Dependency: Reliance on imported bearings impacts Kessler’s costs.
Regulatory Compliance: Stricter standards increase costs for IBAG’s high-speed spindles.
Market Fragmentation: Regional players limit FISCHER’s global share.
to the Machine Tool Spindle Industry
Machine tool spindles are critical components of CNC machine tools, enabling high-speed rotation for cutting, milling, and grinding. Initially developed for internal grinding in the 1980s, electric spindles have become integral to CNC milling machines and machining centers, driven by advances in high-speed cutting technology. Spindles are one of three core high-tech components in CNC machines, alongside CNC systems and feed drives. Technical advancements focus on high power, high speed, and high rotational accuracy, with leading firms like Kessler and FISCHER setting global standards. China’s spindle industry lags behind Switzerland and Germany but is rapidly advancing. Spindles account for a significant portion of machine tool performance, supporting applications from automotive to aerospace. The industry benefits from automation and precision manufacturing trends but faces challenges from high R&D costs and technical complexity.
Market Size and Growth Forecast
The global machine tool spindle market is projected to reach USD 4.0 billion to USD 5.0 billion by 2025, with an estimated CAGR of 5% to 7% through 2030, driven by automation, high-speed machining, and industrial growth.
Regional Analysis
Asia Pacific expects a growth rate of 6% to 8%. China’s manufacturing dominance drives demand for high-speed spindles in electronics and automotive sectors. Japan focuses on precision spindles for aerospace and robotics.
North America anticipates a growth rate of 4% to 6%. The U.S. leads with aerospace and defense applications, emphasizing high-accuracy spindles. Canada’s market grows in energy and automotive sectors.
Europe projects a growth rate of 4% to 6%. Germany’s automotive and aerospace industries drive demand for advanced spindles, while the UK and France focus on precision engineering.
South America expects a growth rate of 3% to 5%. Brazil’s automotive sector supports growth, though economic constraints limit adoption.
Middle East and Africa anticipate a growth rate of 3% to 5%. The UAE’s industrial diversification drives demand, but infrastructure gaps hinder scalability.
Application Analysis
CNC Mills: Projected at 5% to 7%, CNC mills rely on high-speed spindles for automotive and electronics manufacturing. Trends include multi-axis spindles for complex geometries.
CNC Lathes: Expected at 4% to 6%, CNC lathes use spindles for precision turning, with trends toward high-torque spindles for heavy-duty applications.
CNC Plasma Cutters: Anticipated at 3% to 5%, plasma cutters require robust spindles for industrial fabrication, with steady growth.
EDM: Projected at 4% to 6%, EDM spindles support precision mold-making, with trends toward high-accuracy spindles for electronics.
CNC Water Jets: Expected at 3% to 5%, water jet spindles serve diverse materials, with moderate growth in aerospace.
Others: Anticipated at 3% to 5%, including laser cutters, with niche applications driving demand.
Key Market Players
Kessler: A German leader, Kessler develops high-RPM mill spindles.
FISCHER: A Swiss firm, FISCHER focuses on precision lathe spindles.
MCT: A German company, MCT supplies plasma cutter spindles.
IBAG: A Swiss firm, IBAG develops EDM spindles.
Novanta: A U.S. company, Novanta focuses on smart water jet spindles.
ABL: A UK firm, ABL supplies niche machining spindles.
Guangzhou Haozhi: A Chinese company, Haozhi develops high-speed spindles.
Sinomach Precision: A Chinese firm, Sinomach focuses on automotive spindles.
Wuxi Sunshine: A Chinese company, Sunshine supplies precision spindles.
Porter’s Five Forces Analysis
Threat of New Entrants: Low. High technical barriers and R&D costs deter entry, with Kessler and FISCHER dominating through innovation. Emerging players like Guangzhou Haozhi face challenges in matching precision.
Threat of Substitutes: Low. Alternative components like manual spindles lack the precision of electric spindles, giving IBAG an edge. Emerging technologies pose minimal threats.
Bargaining Power of Buyers: Moderate. Large manufacturers exert pricing pressure, but specialized spindles from MCT limit switching. Smaller buyers have less leverage.
Bargaining Power of Suppliers: High. Suppliers of bearings and motors hold leverage, impacting Sinomach Precision’s costs. Diversified sourcing by FISCHER mitigates risks.
Competitive Rivalry: High. Kessler, FISCHER, and IBAG compete on speed, accuracy, and reliability. Rapid adoption of high-speed machining intensifies rivalry.
Market Opportunities and Challenges
Opportunities
High-Speed Machining: Aerospace demand boosts Kessler’s high-accuracy spindles.
Emerging Markets: China’s manufacturing growth offers opportunities for Guangzhou Haozhi’s affordable spindles.
EV Production: Automotive shifts to EVs drive FISCHER’s precision spindles.
Digital Integration: MCT’s IoT-enabled spindles enhance productivity in electronics.
Sustainability Trends: Energy-efficient spindles from IBAG align with green manufacturing.
Aftermarket Services: Sinomach Precision’s maintenance services create revenue streams.
Technological Advancements: High-torque spindles by Kessler tap heavy-duty applications.
Challenges
High R&D Costs: Innovation pressures FISCHER’s profitability in a competitive market.
Technical Complexity: Precision requirements challenge Guangzhou Haozhi’s scalability.
Skilled Labor Shortages: Lack of expertise hinders Sinomach Precision’s growth.
Economic Volatility: Manufacturing slowdowns affect MCT’s sales in developing regions.
Component Dependency: Reliance on imported bearings impacts Kessler’s costs.
Regulatory Compliance: Stricter standards increase costs for IBAG’s high-speed spindles.
Market Fragmentation: Regional players limit FISCHER’s global share.
Table of Contents
86 Pages
- Chapter 1 Executive Summary
- Chapter 2 Abbreviation and Acronyms
- Chapter 3 Preface
- 3.1 Research Scope
- 3.2 Research Sources
- 3.2.1 Data Sources
- 3.2.2 Assumptions
- 3.3 Research Method
- Chapter 4 Market Landscape
- 4.1 Market Overview
- 4.2 Classification/Types
- 4.3 Application/End Users
- Chapter 5 Market Trend Analysis
- 5.1 Introduction
- 5.2 Drivers
- 5.3 Restraints
- 5.4 Opportunities
- 5.5 Threats
- Chapter 6 Industry Chain Analysis
- 6.1 Upstream/Suppliers Analysis
- 6.2 Machine Tool Spindle Analysis
- 6.2.1 Technology Analysis
- 6.2.2 Cost Analysis
- 6.2.3 Market Channel Analysis
- 6.3 Downstream Buyers/End Users
- Chapter 7 Latest Market Dynamics
- 7.1 Latest News
- 7.2 Merger and Acquisition
- 7.3 Planned/Future Project
- 7.4 Policy Dynamics
- Chapter 8 Trading Analysis
- 8.1 Export of Machine Tool Spindle by Region
- 8.2 Import of Machine Tool Spindle by Region
- 8.3 Balance of Trade
- Chapter 9 Historical and Forecast Machine Tool Spindle Market in North America (2020-2030)
- 9.1 Machine Tool Spindle Market Size
- 9.2 Machine Tool Spindle Demand by End Use
- 9.3 Competition by Players/Suppliers
- 9.4 Type Segmentation and Price
- 9.5 Key Countries Analysis
- 9.5.1 United States
- 9.5.2 Canada
- 9.5.3 Mexico
- Chapter 10 Historical and Forecast Machine Tool Spindle Market in South America (2020-2030)
- 10.1 Machine Tool Spindle Market Size
- 10.2 Machine Tool Spindle Demand by End Use
- 10.3 Competition by Players/Suppliers
- 10.4 Type Segmentation and Price
- 10.5 Key Countries Analysis
- 10.5.1 Brazil
- 10.5.2 Argentina
- 10.5.3 Chile
- 10.5.4 Peru
- Chapter 11 Historical and Forecast Machine Tool Spindle Market in Asia & Pacific (2020-2030)
- 11.1 Machine Tool Spindle Market Size
- 11.2 Machine Tool Spindle Demand by End Use
- 11.3 Competition by Players/Suppliers
- 11.4 Type Segmentation and Price
- 11.5 Key Countries Analysis
- 11.5.1 China
- 11.5.2 India
- 11.5.3 Japan
- 11.5.4 South Korea
- 11.5.5 Southest Asia
- 11.5.6 Australia
- Chapter 12 Historical and Forecast Machine Tool Spindle Market in Europe (2020-2030)
- 12.1 Machine Tool Spindle Market Size
- 12.2 Machine Tool Spindle Demand by End Use
- 12.3 Competition by Players/Suppliers
- 12.4 Type Segmentation and Price
- 12.5 Key Countries Analysis
- 12.5.1 Germany
- 12.5.2 France
- 12.5.3 United Kingdom
- 12.5.4 Italy
- 12.5.5 Spain
- 12.5.6 Belgium
- 12.5.7 Netherlands
- 12.5.8 Austria
- 12.5.9 Poland
- 12.5.10 Russia
- Chapter 13 Historical and Forecast Machine Tool Spindle Market in MEA (2020-2030)
- 13.1 Machine Tool Spindle Market Size
- 13.2 Machine Tool Spindle Demand by End Use
- 13.3 Competition by Players/Suppliers
- 13.4 Type Segmentation and Price
- 13.5 Key Countries Analysis
- 13.5.1 Egypt
- 13.5.2 Israel
- 13.5.3 South Africa
- 13.5.4 Gulf Cooperation Council Countries
- 13.5.5 Turkey
- Chapter 14 Summary For Global Machine Tool Spindle Market (2020-2025)
- 14.1 Machine Tool Spindle Market Size
- 14.2 Machine Tool Spindle Demand by End Use
- 14.3 Competition by Players/Suppliers
- 14.4 Type Segmentation and Price
- Chapter 15 Global Machine Tool Spindle Market Forecast (2025-2030)
- 15.1 Machine Tool Spindle Market Size Forecast
- 15.2 Machine Tool Spindle Demand Forecast
- 15.3 Competition by Players/Suppliers
- 15.4 Type Segmentation and Price Forecast
- Chapter 16 Analysis of Global Key Vendors
- 16.1 Kessler
- 16.1.1 Company Profile
- 16.1.2 Main Business and Machine Tool Spindle Information
- 16.1.3 SWOT Analysis of Kessler
- 16.1.4 Kessler Machine Tool Spindle Sales, Revenue, Price and Gross Margin (2020-2025)
- 16.2 FISCHER
- 16.2.1 Company Profile
- 16.2.2 Main Business and Machine Tool Spindle Information
- 16.2.3 SWOT Analysis of FISCHER
- 16.2.4 FISCHER Machine Tool Spindle Sales, Revenue, Price and Gross Margin (2020-2025)
- 16.3 MCT
- 16.3.1 Company Profile
- 16.3.2 Main Business and Machine Tool Spindle Information
- 16.3.3 SWOT Analysis of MCT
- 16.3.4 MCT Machine Tool Spindle Sales, Revenue, Price and Gross Margin (2020-2025)
- 16.4 IBAG
- 16.4.1 Company Profile
- 16.4.2 Main Business and Machine Tool Spindle Information
- 16.4.3 SWOT Analysis of IBAG
- 16.4.4 IBAG Machine Tool Spindle Sales, Revenue, Price and Gross Margin (2020-2025)
- 16.5 Novanta
- 16.5.1 Company Profile
- 16.5.2 Main Business and Machine Tool Spindle Information
- 16.5.3 SWOT Analysis of Novanta
- 16.5.4 Novanta Machine Tool Spindle Sales, Revenue, Price and Gross Margin (2020-2025)
- 16.6 ABL
- 16.6.1 Company Profile
- 16.6.2 Main Business and Machine Tool Spindle Information
- 16.6.3 SWOT Analysis of ABL
- 16.6.4 ABL Machine Tool Spindle Sales, Revenue, Price and Gross Margin (2020-2025)
- Please ask for sample pages for full companies list
- Tables and Figures
- Table Abbreviation and Acronyms List
- Table Research Scope of Machine Tool Spindle Report
- Table Data Sources of Machine Tool Spindle Report
- Table Major Assumptions of Machine Tool Spindle Report
- Figure Market Size Estimated Method
- Figure Major Forecasting Factors
- Figure Machine Tool Spindle Picture
- Table Machine Tool Spindle Classification
- Table Machine Tool Spindle Applications List
- Table Drivers of Machine Tool Spindle Market
- Table Restraints of Machine Tool Spindle Market
- Table Opportunities of Machine Tool Spindle Market
- Table Threats of Machine Tool Spindle Market
- Table Covid-19 Impact For Machine Tool Spindle Market
- Table Raw Materials Suppliers List
- Table Different Production Methods of Machine Tool Spindle
- Table Cost Structure Analysis of Machine Tool Spindle
- Table Key End Users List
- Table Latest News of Machine Tool Spindle Market
- Table Merger and Acquisition List
- Table Planned/Future Project of Machine Tool Spindle Market
- Table Policy of Machine Tool Spindle Market
- Table 2020-2030 Regional Export of Machine Tool Spindle
- Table 2020-2030 Regional Import of Machine Tool Spindle
- Table 2020-2030 Regional Trade Balance
- Figure 2020-2030 Regional Trade Balance
- Table 2020-2030 North America Machine Tool Spindle Market Size and Market Volume List
- Figure 2020-2030 North America Machine Tool Spindle Market Size and CAGR
- Figure 2020-2030 North America Machine Tool Spindle Market Volume and CAGR
- Table 2020-2030 North America Machine Tool Spindle Demand List by Application
- Table 2020-2025 North America Machine Tool Spindle Key Players Sales List
- Table 2020-2025 North America Machine Tool Spindle Key Players Market Share List
- Table 2020-2030 North America Machine Tool Spindle Demand List by Type
- Table 2020-2025 North America Machine Tool Spindle Price List by Type
- Table 2020-2030 United States Machine Tool Spindle Market Size and Market Volume List
- Table 2020-2030 United States Machine Tool Spindle Import & Export List
- Table 2020-2030 Canada Machine Tool Spindle Market Size and Market Volume List
- Table 2020-2030 Canada Machine Tool Spindle Import & Export List
- Table 2020-2030 Mexico Machine Tool Spindle Market Size and Market Volume List
- Table 2020-2030 Mexico Machine Tool Spindle Import & Export List
- Table 2020-2030 South America Machine Tool Spindle Market Size and Market Volume List
- Figure 2020-2030 South America Machine Tool Spindle Market Size and CAGR
- Figure 2020-2030 South America Machine Tool Spindle Market Volume and CAGR
- Table 2020-2030 South America Machine Tool Spindle Demand List by Application
- Table 2020-2025 South America Machine Tool Spindle Key Players Sales List
- Table 2020-2025 South America Machine Tool Spindle Key Players Market Share List
- Table 2020-2030 South America Machine Tool Spindle Demand List by Type
- Table 2020-2025 South America Machine Tool Spindle Price List by Type
- Table 2020-2030 Brazil Machine Tool Spindle Market Size and Market Volume List
- Table 2020-2030 Brazil Machine Tool Spindle Import & Export List
- Table 2020-2030 Argentina Machine Tool Spindle Market Size and Market Volume List
- Table 2020-2030 Argentina Machine Tool Spindle Import & Export List
- Table 2020-2030 Chile Machine Tool Spindle Market Size and Market Volume List
- Table 2020-2030 Chile Machine Tool Spindle Import & Export List
- Table 2020-2030 Peru Machine Tool Spindle Market Size and Market Volume List
- Table 2020-2030 Peru Machine Tool Spindle Import & Export List
- Table 2020-2030 Asia & Pacific Machine Tool Spindle Market Size and Market Volume List
- Figure 2020-2030 Asia & Pacific Machine Tool Spindle Market Size and CAGR
- Figure 2020-2030 Asia & Pacific Machine Tool Spindle Market Volume and CAGR
- Table 2020-2030 Asia & Pacific Machine Tool Spindle Demand List by Application
- Table 2020-2025 Asia & Pacific Machine Tool Spindle Key Players Sales List
- Table 2020-2025 Asia & Pacific Machine Tool Spindle Key Players Market Share List
- Table 2020-2030 Asia & Pacific Machine Tool Spindle Demand List by Type
- Table 2020-2025 Asia & Pacific Machine Tool Spindle Price List by Type
- Table 2020-2030 China Machine Tool Spindle Market Size and Market Volume List
- Table 2020-2030 China Machine Tool Spindle Import & Export List
- Table 2020-2030 India Machine Tool Spindle Market Size and Market Volume List
- Table 2020-2030 India Machine Tool Spindle Import & Export List
- Table 2020-2030 Japan Machine Tool Spindle Market Size and Market Volume List
- Table 2020-2030 Japan Machine Tool Spindle Import & Export List
- Table 2020-2030 South Korea Machine Tool Spindle Market Size and Market Volume List
- Table 2020-2030 South Korea Machine Tool Spindle Import & Export List
- Table 2020-2030 Southeast Asia Machine Tool Spindle Market Size List
- Table 2020-2030 Southeast Asia Machine Tool Spindle Market Volume List
- Table 2020-2030 Southeast Asia Machine Tool Spindle Import List
- Table 2020-2030 Southeast Asia Machine Tool Spindle Export List
- Table 2020-2030 Australia Machine Tool Spindle Market Size and Market Volume List
- Table 2020-2030 Australia Machine Tool Spindle Import & Export List
- Table 2020-2030 Europe Machine Tool Spindle Market Size and Market Volume List
- Figure 2020-2030 Europe Machine Tool Spindle Market Size and CAGR
- Figure 2020-2030 Europe Machine Tool Spindle Market Volume and CAGR
- Table 2020-2030 Europe Machine Tool Spindle Demand List by Application
- Table 2020-2025 Europe Machine Tool Spindle Key Players Sales List
- Table 2020-2025 Europe Machine Tool Spindle Key Players Market Share List
- Table 2020-2030 Europe Machine Tool Spindle Demand List by Type
- Table 2020-2025 Europe Machine Tool Spindle Price List by Type
- Table 2020-2030 Germany Machine Tool Spindle Market Size and Market Volume List
- Table 2020-2030 Germany Machine Tool Spindle Import & Export List
- Table 2020-2030 France Machine Tool Spindle Market Size and Market Volume List
- Table 2020-2030 France Machine Tool Spindle Import & Export List
- Table 2020-2030 United Kingdom Machine Tool Spindle Market Size and Market Volume List
- Table 2020-2030 United Kingdom Machine Tool Spindle Import & Export List
- Table 2020-2030 Italy Machine Tool Spindle Market Size and Market Volume List
- Table 2020-2030 Italy Machine Tool Spindle Import & Export List
- Table 2020-2030 Spain Machine Tool Spindle Market Size and Market Volume List
- Table 2020-2030 Spain Machine Tool Spindle Import & Export List
- Table 2020-2030 Belgium Machine Tool Spindle Market Size and Market Volume List
- Table 2020-2030 Belgium Machine Tool Spindle Import & Export List
- Table 2020-2030 Netherlands Machine Tool Spindle Market Size and Market Volume List
- Table 2020-2030 Netherlands Machine Tool Spindle Import & Export List
- Table 2020-2030 Austria Machine Tool Spindle Market Size and Market Volume List
- Table 2020-2030 Austria Machine Tool Spindle Import & Export List
- Table 2020-2030 Poland Machine Tool Spindle Market Size and Market Volume List
- Table 2020-2030 Poland Machine Tool Spindle Import & Export List
- Table 2020-2030 Russia Machine Tool Spindle Market Size and Market Volume List
- Table 2020-2030 Russia Machine Tool Spindle Import & Export List
- Table 2020-2030 MEA Machine Tool Spindle Market Size and Market Volume List
- Figure 2020-2030 MEA Machine Tool Spindle Market Size and CAGR
- Figure 2020-2030 MEA Machine Tool Spindle Market Volume and CAGR
- Table 2020-2030 MEA Machine Tool Spindle Demand List by Application
- Table 2020-2025 MEA Machine Tool Spindle Key Players Sales List
- Table 2020-2025 MEA Machine Tool Spindle Key Players Market Share List
- Table 2020-2030 MEA Machine Tool Spindle Demand List by Type
- Table 2020-2025 MEA Machine Tool Spindle Price List by Type
- Table 2020-2030 Egypt Machine Tool Spindle Market Size and Market Volume List
- Table 2020-2030 Egypt Machine Tool Spindle Import & Export List
- Table 2020-2030 Israel Machine Tool Spindle Market Size and Market Volume List
- Table 2020-2030 Israel Machine Tool Spindle Import & Export List
- Table 2020-2030 South Africa Machine Tool Spindle Market Size and Market Volume List
- Table 2020-2030 South Africa Machine Tool Spindle Import & Export List
- Table 2020-2030 Gulf Cooperation Council Countries Machine Tool Spindle Market Size and Market Volume List
- Table 2020-2030 Gulf Cooperation Council Countries Machine Tool Spindle Import & Export List
- Table 2020-2030 Turkey Machine Tool Spindle Market Size and Market Volume List
- Table 2020-2030 Turkey Machine Tool Spindle Import & Export List
- Table 2020-2025 Global Machine Tool Spindle Market Size List by Region
- Table 2020-2025 Global Machine Tool Spindle Market Size Share List by Region
- Table 2020-2025 Global Machine Tool Spindle Market Volume List by Region
- Table 2020-2025 Global Machine Tool Spindle Market Volume Share List by Region
- Table 2020-2025 Global Machine Tool Spindle Demand List by Application
- Table 2020-2025 Global Machine Tool Spindle Demand Market Share List by Application
- Table 2020-2025 Global Machine Tool Spindle Key Vendors Sales List
- Table 2020-2025 Global Machine Tool Spindle Key Vendors Sales Share List
- Figure 2020-2025 Global Machine Tool Spindle Market Volume and Growth Rate
- Table 2020-2025 Global Machine Tool Spindle Key Vendors Revenue List
- Figure 2020-2025 Global Machine Tool Spindle Market Size and Growth Rate
- Table 2020-2025 Global Machine Tool Spindle Key Vendors Revenue Share List
- Table 2020-2025 Global Machine Tool Spindle Demand List by Type
- Table 2020-2025 Global Machine Tool Spindle Demand Market Share List by Type
- Table 2020-2025 Regional Machine Tool Spindle Price List
- Table 2025-2030 Global Machine Tool Spindle Market Size List by Region
- Table 2025-2030 Global Machine Tool Spindle Market Size Share List by Region
- Table 2025-2030 Global Machine Tool Spindle Market Volume List by Region
- Table 2025-2030 Global Machine Tool Spindle Market Volume Share List by Region
- Table 2025-2030 Global Machine Tool Spindle Demand List by Application
- Table 2025-2030 Global Machine Tool Spindle Demand Market Share List by Application
- Table 2025-2030 Global Machine Tool Spindle Key Vendors Sales List
- Table 2025-2030 Global Machine Tool Spindle Key Vendors Sales Share List
- Figure 2025-2030 Global Machine Tool Spindle Market Volume and Growth Rate
- Table 2025-2030 Global Machine Tool Spindle Key Vendors Revenue List
- Figure 2025-2030 Global Machine Tool Spindle Market Size and Growth Rate
- Table 2025-2030 Global Machine Tool Spindle Key Vendors Revenue Share List
- Table 2025-2030 Global Machine Tool Spindle Demand List by Type
- Table 2025-2030 Global Machine Tool Spindle Demand Market Share List by Type
- Table 2025-2030 Machine Tool Spindle Regional Price List
- Table Kessler Information
- Table SWOT Analysis of Kessler
- Table 2020-2025 Kessler Machine Tool Spindle Sale Volume Price Cost Revenue
- Figure 2020-2025 Kessler Machine Tool Spindle Sale Volume and Growth Rate
- Figure 2020-2025 Kessler Machine Tool Spindle Market Share
- Table FISCHER Information
- Table SWOT Analysis of FISCHER
- Table 2020-2025 FISCHER Machine Tool Spindle Sale Volume Price Cost Revenue
- Figure 2020-2025 FISCHER Machine Tool Spindle Sale Volume and Growth Rate
- Figure 2020-2025 FISCHER Machine Tool Spindle Market Share
- Table MCT Information
- Table SWOT Analysis of MCT
- Table 2020-2025 MCT Machine Tool Spindle Sale Volume Price Cost Revenue
- Figure 2020-2025 MCT Machine Tool Spindle Sale Volume and Growth Rate
- Figure 2020-2025 MCT Machine Tool Spindle Market Share
- Table IBAG Information
- Table SWOT Analysis of IBAG
- Table 2020-2025 IBAG Machine Tool Spindle Sale Volume Price Cost Revenue
- Figure 2020-2025 IBAG Machine Tool Spindle Sale Volume and Growth Rate
- Figure 2020-2025 IBAG Machine Tool Spindle Market Share
- Table Novanta Information
- Table SWOT Analysis of Novanta
- Table 2020-2025 Novanta Machine Tool Spindle Sale Volume Price Cost Revenue
- Figure 2020-2025 Novanta Machine Tool Spindle Sale Volume and Growth Rate
- Figure 2020-2025 Novanta Machine Tool Spindle Market Share
- Table ABL Information
- Table SWOT Analysis of ABL
- Table 2020-2025 ABL Machine Tool Spindle Sale Volume Price Cost Revenue
- Figure 2020-2025 ABL Machine Tool Spindle Sale Volume and Growth Rate
- Figure 2020-2025 ABL Machine Tool Spindle Market Share
Pricing
Currency Rates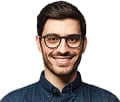
Questions or Comments?
Our team has the ability to search within reports to verify it suits your needs. We can also help maximize your budget by finding sections of reports you can purchase.