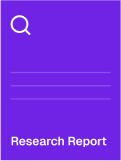
TaC Coating - Global Industry Market Analysis Report 2020-2031
Description
TaC coating (Tantalum Carbide Coating) is a hard coating with tantalum carbide (TaC) as the main component, with a hardness of 20-25 GPa (close to diamond), high temperature resistance (>3000°C), corrosion resistance (strong acid and oxidant resistance) and excellent wear resistance (friction coefficient<0.2), widely used in cutting tools, aviation components, nuclear industry and electronic equipment. It is applied by chemical vapor deposition (CVD, temperature 1000-1200°C) or physical vapor deposition (PVD, temperature 500-800°C), with a thickness of usually 5-20 μm, and a bonding layer (such as TiN or CrN) to enhance adhesion (peel strength>50 MPa). For example, on carbide tools, TaC coatings extend tool life by 2-3 times (cutting distance increased by 50%-100%) and are used to process stainless steel and titanium alloys; on aviation turbine blades, they protect the substrate against high-temperature oxidation (<0.01 mg/cm²·h, 1000°C); in nuclear reactors, they resist neutron radiation corrosion (loss rate<0.005%/year). The production process requires high-purity tantalum powder (>99.9%, priced at about $100-150/kg) and a carbon source (such as methane or propane), which is deposited in a vacuum or inert atmosphere, and the phase composition and thickness uniformity are detected by X-ray diffraction (XRD) and scanning electron microscopy (SEM).
TaC coatings have performed well in industrial applications, but their advantages and disadvantages have sparked extensive discussions on technology, cost and environment. Supporters believe that their high hardness and durability significantly improve the performance of tools and components. For example, in cutting, the cutting speed of TaC coated tools can reach 200-300 m/min (uncoated tools are only 100-150 m/min), reducing the frequency of tool replacement (increasing the life of each tool by 50%-70%) and improving production efficiency; in aircraft engines, its high temperature resistance and oxidation resistance support the blades to operate at 900-1200°C, extending the life of components to more than 20,000 hours; in the nuclear industry, radiation resistance and corrosion resistance ensure the safe operation of reactors (>30 years). In addition, the low thermal conductivity of TaC coatings (about 20 W/m·K) reduces heat diffusion and protects the substrate from thermal damage (temperature gradient<50°C). However, critics point out that the high production cost, the scarcity of tantalum resources (global reserves are about 50,000 tons, mainly produced in Congo and Australia), the price fluctuations (estimated to be $150-200/kg in 2025), plus the investment in CVD/PVD equipment (about $1 million-2 million per unit), the cost of coating a single piece of about $10-50, accounting for 20%-40% of the tool cost, limit its application in the low-end market. In addition, the coating process is energy-intensive (about 50-100 kWh per square meter), and the waste gas (such as fluorinated compounds) may pollute the environment if not properly handled (emission standard<0.1 ppm), and an exhaust gas purification system is required. Some users also reported that TaC coatings have poor uniformity on complex geometries (such as deep holes or inner surfaces) (thickness deviation >10%), and may have insufficient adhesion (peeling risk<1%), and deposition parameters need to be optimized; in addition, high-temperature deposition may cause deformation of the substrate (thermal expansion coefficient difference<10⁻⁶/°C), increasing processing difficulty.
In terms of the market, the demand for TaC coatings is closely related to the rapid development of the global cutting tools, aerospace and nuclear industries. Europe, especially Germany, has become the main market due to its leading precision manufacturing and aviation industry (Siemens turbines and Airbus A350 have an annual output value of over US$50 billion). German companies (such as Walter and Sandvik) widely use TaC coatings in high-performance tools, which must comply with DIN standards. The North American market focuses on high-end applications. For example, the United States uses TaC-coated parts in F-35 fighters and nuclear power plants (such as Vogtle Power Plant), which must comply with MIL and ASME standards. The Asian market, especially China, has huge demand potential due to its localization of aviation engines (C919 and J-20 projects) and nuclear power development (installed capacity exceeds 70 GW). Chinese companies (such as Zhuzhou Diamond and China National Nuclear Corporation) are accelerating technology research and development, and the market size is expected to reach US$500 million in 2025. The growth of market demand is also driven by industrial upgrading and national defense modernization, and the demand for durable coatings for high-precision processing and extreme environment applications continues to increase. However, the market development also faces several challenges, including the tight supply of tantalum resources (political instability in Congo affects exports), high energy consumption and exhaust emissions in the production process may be restricted by environmental regulations (such as EU ETS carbon trading), and the rise of competitive coatings (such as TiAlN or CrN, 30%-50% lower cost) may divert the market.
In the future, the development of TaC coatings may focus more on cost reduction, uniformity and versatility. Developing alternative materials (such as NbC or ZrC, 20%-30% lower price) or optimizing deposition processes (such as low-temperature PVD or plasma-enhanced CVD, reducing energy consumption by 20%) may reduce costs and environmental impact. Improving coating uniformity, such as through rotating targets or multi-source deposition technology (thickness deviation<5%), may enhance the application of complex components. Potential applications include enhancing durability and efficiency in the electronics field (such as semiconductor etching tools) or energy fields (such as high-temperature fuel cell coatings). However, the industry needs to face the scarcity of tantalum resources (recycling rate needs to be increased to more than 80%), the process challenges of high-temperature deposition (substrate deformation needs to be reduced), and the difficulty of finding a balance between high performance and economy. Overall, TaC coating will continue to maintain its position due to its excellent performance in extreme environments, but its future development needs to rely on material innovation (alternative materials and process optimization), resource management (recycling and sustainable mining) and environmental protection upgrades to cope with resource and cost pressures.
Report Scope
This report aims to deliver a thorough analysis of the global market for TaC Coating, offering both quantitative and qualitative insights to assist readers in formulating business growth strategies, evaluating the competitive landscape, understanding their current market position, and making well-informed decisions regarding TaC Coating.
The report is enriched with qualitative evaluations, including market drivers, challenges, Porter's Five Forces, regulatory frameworks, consumer preferences, and ESG (Environmental, Social, and Governance) factors.
The report provides detailed classification of TaC Coating, such as type, etc.; detailed examples of TaC Coating applications, such as application one, etc., and provides comprehensive historical (2020-2025) and forecast (2026-2031) market size data.
The report provides detailed classification of TaC Coating, such as CVD, Others, etc.; detailed examples of TaC Coating applications, such as Semiconductor, Aerospace, Others, etc., and provides comprehensive historical (2020-2025) and forecast (2026-2031) market size data.
The report covers key global regions-North America, Europe, Asia-Pacific, Latin America, and the Middle East & Africa-providing granular, country-specific insights for major markets such as the United States, China, Germany, and Brazil.
The report deeply explores the competitive landscape of TaC Coating products, details the sales, revenue, and regional layout of some of the world's leading manufacturers, and provides in-depth company profiles and contact details.
The report contains a comprehensive industry chain analysis covering raw materials, downstream customers and sales channels.
Core Chapters
Chapter One: Introduces the study scope of this report, market status, market drivers, challenges, porters five forces analysis, regulatory policy, consumer preference, market attractiveness and ESG analysis.
Chapter Two: market segments by Type, covering the market size and development potential of each market segment, to help readers find the blue ocean market in different market segments.
Chapter Three: TaC Coating market sales and revenue in regional level and country level. It provides a quantitative analysis of the market size and development potential of each region and its main countries and introduces the market development, future development prospects, market space, and production of each country in the world.
Chapter Four: Provides the analysis of various market segments by Application, covering the market size and development potential of each market segment, to help readers find the blue ocean market in different downstream markets.
Chapter Five: Detailed analysis of TaC Coating manufacturers competitive landscape, price, sales, revenue, market share, footprint, merger, and acquisition information, etc.
Chapter Six: Provides profiles of leading manufacturers, introducing the basic situation of the main companies in the market in detail, including product sales, revenue, price, gross margin, product introduction.
Chapter Seven: Analysis of industrial chain, key raw materials, customers and sales channel.
Chapter Eight: Key Takeaways and Final Conclusions
Chapter Nine: Methodology and Sources.
TaC coatings have performed well in industrial applications, but their advantages and disadvantages have sparked extensive discussions on technology, cost and environment. Supporters believe that their high hardness and durability significantly improve the performance of tools and components. For example, in cutting, the cutting speed of TaC coated tools can reach 200-300 m/min (uncoated tools are only 100-150 m/min), reducing the frequency of tool replacement (increasing the life of each tool by 50%-70%) and improving production efficiency; in aircraft engines, its high temperature resistance and oxidation resistance support the blades to operate at 900-1200°C, extending the life of components to more than 20,000 hours; in the nuclear industry, radiation resistance and corrosion resistance ensure the safe operation of reactors (>30 years). In addition, the low thermal conductivity of TaC coatings (about 20 W/m·K) reduces heat diffusion and protects the substrate from thermal damage (temperature gradient<50°C). However, critics point out that the high production cost, the scarcity of tantalum resources (global reserves are about 50,000 tons, mainly produced in Congo and Australia), the price fluctuations (estimated to be $150-200/kg in 2025), plus the investment in CVD/PVD equipment (about $1 million-2 million per unit), the cost of coating a single piece of about $10-50, accounting for 20%-40% of the tool cost, limit its application in the low-end market. In addition, the coating process is energy-intensive (about 50-100 kWh per square meter), and the waste gas (such as fluorinated compounds) may pollute the environment if not properly handled (emission standard<0.1 ppm), and an exhaust gas purification system is required. Some users also reported that TaC coatings have poor uniformity on complex geometries (such as deep holes or inner surfaces) (thickness deviation >10%), and may have insufficient adhesion (peeling risk<1%), and deposition parameters need to be optimized; in addition, high-temperature deposition may cause deformation of the substrate (thermal expansion coefficient difference<10⁻⁶/°C), increasing processing difficulty.
In terms of the market, the demand for TaC coatings is closely related to the rapid development of the global cutting tools, aerospace and nuclear industries. Europe, especially Germany, has become the main market due to its leading precision manufacturing and aviation industry (Siemens turbines and Airbus A350 have an annual output value of over US$50 billion). German companies (such as Walter and Sandvik) widely use TaC coatings in high-performance tools, which must comply with DIN standards. The North American market focuses on high-end applications. For example, the United States uses TaC-coated parts in F-35 fighters and nuclear power plants (such as Vogtle Power Plant), which must comply with MIL and ASME standards. The Asian market, especially China, has huge demand potential due to its localization of aviation engines (C919 and J-20 projects) and nuclear power development (installed capacity exceeds 70 GW). Chinese companies (such as Zhuzhou Diamond and China National Nuclear Corporation) are accelerating technology research and development, and the market size is expected to reach US$500 million in 2025. The growth of market demand is also driven by industrial upgrading and national defense modernization, and the demand for durable coatings for high-precision processing and extreme environment applications continues to increase. However, the market development also faces several challenges, including the tight supply of tantalum resources (political instability in Congo affects exports), high energy consumption and exhaust emissions in the production process may be restricted by environmental regulations (such as EU ETS carbon trading), and the rise of competitive coatings (such as TiAlN or CrN, 30%-50% lower cost) may divert the market.
In the future, the development of TaC coatings may focus more on cost reduction, uniformity and versatility. Developing alternative materials (such as NbC or ZrC, 20%-30% lower price) or optimizing deposition processes (such as low-temperature PVD or plasma-enhanced CVD, reducing energy consumption by 20%) may reduce costs and environmental impact. Improving coating uniformity, such as through rotating targets or multi-source deposition technology (thickness deviation<5%), may enhance the application of complex components. Potential applications include enhancing durability and efficiency in the electronics field (such as semiconductor etching tools) or energy fields (such as high-temperature fuel cell coatings). However, the industry needs to face the scarcity of tantalum resources (recycling rate needs to be increased to more than 80%), the process challenges of high-temperature deposition (substrate deformation needs to be reduced), and the difficulty of finding a balance between high performance and economy. Overall, TaC coating will continue to maintain its position due to its excellent performance in extreme environments, but its future development needs to rely on material innovation (alternative materials and process optimization), resource management (recycling and sustainable mining) and environmental protection upgrades to cope with resource and cost pressures.
Report Scope
This report aims to deliver a thorough analysis of the global market for TaC Coating, offering both quantitative and qualitative insights to assist readers in formulating business growth strategies, evaluating the competitive landscape, understanding their current market position, and making well-informed decisions regarding TaC Coating.
The report is enriched with qualitative evaluations, including market drivers, challenges, Porter's Five Forces, regulatory frameworks, consumer preferences, and ESG (Environmental, Social, and Governance) factors.
The report provides detailed classification of TaC Coating, such as type, etc.; detailed examples of TaC Coating applications, such as application one, etc., and provides comprehensive historical (2020-2025) and forecast (2026-2031) market size data.
The report provides detailed classification of TaC Coating, such as CVD, Others, etc.; detailed examples of TaC Coating applications, such as Semiconductor, Aerospace, Others, etc., and provides comprehensive historical (2020-2025) and forecast (2026-2031) market size data.
The report covers key global regions-North America, Europe, Asia-Pacific, Latin America, and the Middle East & Africa-providing granular, country-specific insights for major markets such as the United States, China, Germany, and Brazil.
The report deeply explores the competitive landscape of TaC Coating products, details the sales, revenue, and regional layout of some of the world's leading manufacturers, and provides in-depth company profiles and contact details.
The report contains a comprehensive industry chain analysis covering raw materials, downstream customers and sales channels.
Core Chapters
Chapter One: Introduces the study scope of this report, market status, market drivers, challenges, porters five forces analysis, regulatory policy, consumer preference, market attractiveness and ESG analysis.
Chapter Two: market segments by Type, covering the market size and development potential of each market segment, to help readers find the blue ocean market in different market segments.
Chapter Three: TaC Coating market sales and revenue in regional level and country level. It provides a quantitative analysis of the market size and development potential of each region and its main countries and introduces the market development, future development prospects, market space, and production of each country in the world.
Chapter Four: Provides the analysis of various market segments by Application, covering the market size and development potential of each market segment, to help readers find the blue ocean market in different downstream markets.
Chapter Five: Detailed analysis of TaC Coating manufacturers competitive landscape, price, sales, revenue, market share, footprint, merger, and acquisition information, etc.
Chapter Six: Provides profiles of leading manufacturers, introducing the basic situation of the main companies in the market in detail, including product sales, revenue, price, gross margin, product introduction.
Chapter Seven: Analysis of industrial chain, key raw materials, customers and sales channel.
Chapter Eight: Key Takeaways and Final Conclusions
Chapter Nine: Methodology and Sources.
Table of Contents
95 Pages
- 1 TaC Coating Market Overview and Qualitative Analysis
- 1.1 TaC Coating Product Definition and Statistical Scope
- 1.2 TaC Coating Market Status and Outlook
- 1.2.1 TaC Coating Market Revenue Estimates and Forecasts 2020-2031
- 1.2.2 TaC Coating Market Sales Estimates and Forecasts 2020-2031
- 1.3 TaC Coating Market Driver Analysis
- 1.4 TaC Coating Market Challenges Analysis
- 1.5 Porter's Five Forces Analysis
- 1.5.1 Bargaining Power of Suppliers
- 1.5.2 Bargaining Power of Buyers/Consumers
- 1.5.3 Threat of New Entrants
- 1.5.4 Threat of Substitute Products
- 1.5.5 Intensity of Competitive Rivalry
- 1.6 Regulatory Policy Analysis
- 1.7 Consumer Preference Analysis
- 1.8 Market Attractiveness Analysis
- 1.9 ESG (Environmental, Social and Governance) Analysis
- 2 TaC Coating Market Type Estimates & Trend Analysis
- 2.1 TaC Coating Type Dashboard
- 2.2 TaC Coating Market by Type
- 2.2.1 CVD
- 2.2.2 Others
- 2.3 Global TaC Coating Market Size by Type
- 2.3.1 Historical Analysis of the Global TaC Coating Market Size by Type (2020-2025)
- 2.3.2 Projected Analysis of Global TaC Coating Market Size by Type (2026-2031)
- 3 TaC Coating Market Geography Estimates & Trend Analysis
- 3.1 TaC Coating Geography Dashboard
- 3.2 Global TaC Coating Historic Market Size by Region
- 3.2.1 Global TaC Coating Market Sales by Region (2020-2025)
- 3.2.2 Global TaC Coating Market Revenue by Region (2020-2025)
- 3.3 Global TaC Coating Forecasted Market Size by Region
- 3.3.1 Global TaC Coating Market Sales by Region (2026-2031)
- 3.3.2 Global TaC Coating Market Revenue by Region (2026-2031)
- 3.4 North America TaC Coating Market by Country
- 3.4.1 North America TaC Coating Market Sales by Country (2020-2031)
- 3.4.2 North America TaC Coating Market Revenue by Country (2020-2031)
- 3.4.3 United States TaC Coating Market Sales, Revenue and Growth Rate (2020-2031)
- 3.4.4 Canada TaC Coating Market Sales, Revenue and Growth Rate (2020-2031)
- 3.5 Europe TaC Coating Market by Country
- 3.5.1 Europe TaC Coating Market Sale by Country (2020-2031)
- 3.5.2 Europe TaC Coating Market Revenue by Country (2020-2031)
- 3.5.3 Germany Market Sales, Revenue and Growth Rate (2020-2031)
- 3.5.4 France Market Sales, Revenue and Growth Rate (2020-2031)
- 3.5.5 U.K. Market Sales, Revenue and Growth Rate (2020-2031)
- 3.5.6 Italy Market Sales, Revenue and Growth Rate (2020-2031)
- 3.5.7 Spain Market Sales, Revenue and Growth Rate (2020-2031)
- 3.6 Asia-Pacific TaC Coating Market by Region
- 3.6.1 Asia-Pacific TaC Coating Market Sales by Region (2020-2031)
- 3.6.2 Asia-Pacific TaC Coating Market Revenue by Region (2020-2031)
- 3.6.3 China Market Sales, Revenue and Growth Rate (2020-2031)
- 3.6.4 Japan Market Sales, Revenue and Growth Rate (2020-2031)
- 3.6.5 South Korea Market Sales, Revenue and Growth Rate (2020-2031)
- 3.6.6 India Market Sales, Revenue and Growth Rate (2020-2031)
- 3.6.7 Southeast Asia Market Sales, Revenue and Growth Rate (2020-2031)
- 3.7 Latin America TaC Coating Market by Country
- 3.7.1 Latin America TaC Coating Market Sales by Country (2020-2031)
- 3.7.2 Latin America TaC Coating Market Revenue by Country (2020-2031)
- 3.7.3 Mexico Market Sales, Revenue and Growth Rate (2020-2031)
- 3.7.4 Brazil Market Sales, Revenue and Growth Rate (2020-2031)
- 3.8 Middle East and Africa TaC Coating Market by Country
- 3.8.1 Middle East and Africa TaC Coating Market Sales by Country (2020-2031)
- 3.8.2 Middle East and Africa TaC Coating Market Revenue by Country (2020-2031)
- 3.8.3 Turkey Market Sales, Revenue and Growth Rate (2020-2031)
- 3.8.4 Saudi Arabia Market Sales, Revenue and Growth Rate (2020-2031)
- 3.8.5 South Africa Market Sales, Revenue and Growth Rate (2020-2031)
- 4 TaC Coating Market Application Estimates & Trend Analysis
- 4.1 TaC Coating Market Application Dashboard
- 4.2 TaC Coating Market by Application
- 4.2.1 Semiconductor
- 4.2.2 Aerospace
- 4.2.3 Others
- 4.3 Global TaC Coating Market Size by Application
- 4.3.1 Historical Analysis of Global TaC Coating Market Size by Application (2020-2025)
- 4.3.2 Projected Analysis of Global TaC Coating Market Size by Application (2026-2031)
- 5 TaC Coating Market Competitive Landscape Analysis
- 5.1 Global TaC Coating Leading Manufacturers' Market Sales Performance and Share Analysis
- 5.2 Global TaC Coating Leading Manufacturers' Market Revenue Performance and Share Analysis
- 5.3 Global TaC Coating Leading Manufacturers' Average Sales Price (2020-2025)
- 5.4 Global TaC Coating Leading Manufacturers' Regional Footprint (Headquarters, Manufacturing Base and Sales Ares)
- 5.5 Mergers and Acquisition Analysis
- 6 Leading Manufacturers' Company Profiles
- 6.1 Momentive Technologies
- 6.1.1 Momentive Technologies Overview (Basic Corporate Information, Manufacturing Footprint, Geographic Sales Presence and Key Competitors)
- 6.1.2 Momentive Technologies Introduction and Business Overview
- 6.1.3 Momentive Technologies TaC Coating Product Portfolio
- 6.1.4 Momentive Technologies TaC Coating Market Performance Analysis (Revenue, Sales, Price, Gross Margin and Market Share)
- 6.2 Tokai Carbon Co., Ltd.
- 6.2.1 Tokai Carbon Co., Ltd. Overview (Basic Corporate Information, Manufacturing Footprint, Geographic Sales Presence and Key Competitors)
- 6.2.2 Tokai Carbon Co., Ltd. Introduction and Business Overview
- 6.2.3 Tokai Carbon Co., Ltd. TaC Coating Product Portfolio
- 6.2.4 Tokai Carbon Co., Ltd. TaC Coating Market Performance Analysis (Revenue, Sales, Price, Gross Margin and Market Share)
- 6.3 Toyo Tanso Co. Ltd.
- 6.3.1 Toyo Tanso Co. Ltd. Overview (Basic Corporate Information, Manufacturing Footprint, Geographic Sales Presence and Key Competitors)
- 6.3.2 Toyo Tanso Co. Ltd. Introduction and Business Overview
- 6.3.3 Toyo Tanso Co. Ltd. TaC Coating Product Portfolio
- 6.3.4 Toyo Tanso Co. Ltd. TaC Coating Market Performance Analysis (Revenue, Sales, Price, Gross Margin and Market Share)
- 6.4 Bay Carbon Inc.
- 6.4.1 Bay Carbon Inc. Overview (Basic Corporate Information, Manufacturing Footprint, Geographic Sales Presence and Key Competitors)
- 6.4.2 Bay Carbon Inc. Introduction and Business Overview
- 6.4.3 Bay Carbon Inc. TaC Coating Product Portfolio
- 6.4.4 Bay Carbon Inc. TaC Coating Market Performance Analysis (Revenue, Sales, Price, Gross Margin and Market Share)
- 6.5 ACME
- 6.5.1 ACME Overview (Basic Corporate Information, Manufacturing Footprint, Geographic Sales Presence and Key Competitors)
- 6.5.2 ACME Introduction and Business Overview
- 6.5.3 ACME TaC Coating Product Portfolio
- 6.5.4 ACME TaC Coating Market Performance Analysis (Revenue, Sales, Price, Gross Margin and Market Share)
- 7 Industry Chain Analysis
- 7.1 Upstream Key Raw Materials
- 7.1.1 Raw Materials A Definition and Suppliers
- 7.1.2 Raw Materials B Definition and Suppliers
- 7.1.3 Raw Materials C Definition and Suppliers
- 7.2 TaC Coating Typical Downstream Customers
- 7.3 TaC Coating Sales Channel Analysis
- 8 Key Takeaways and Final Conclusions
- 9 Methodology and Sources
- 9.1 Research Methodology
- 9.2 Data Mining
- 9.2.1 Preliminary Data Sources
- 9.2.2 Secondary Sources
- 9.3 Industry Analysis Matrix
- 9.4 Disclaimer
Pricing
Currency Rates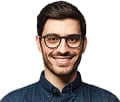
Questions or Comments?
Our team has the ability to search within reports to verify it suits your needs. We can also help maximize your budget by finding sections of reports you can purchase.