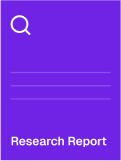
Polyphenylene Ether (PPE) - Global Industry Market Analysis Report 2020-2031
Description
Polyphenylene Ether (PPE), also known as polyphenylene ether, is a high-performance thermoplastic engineering plastic characterized by repeated benzene rings and ether bonds (-O-) structures in its main chain. It is usually prepared by the oxidative polymerization of 2,6-dimethylphenol and has excellent heat resistance, dimensional stability, electrical insulation and chemical corrosion resistance. The glass transition temperature (Tg) of PPE is as high as about 210°C, which is much higher than many common plastics, enabling it to maintain mechanical properties in high temperature environments. However, due to its high melt viscosity and poor processability in its pure state, it is usually blended and modified with polystyrene (PS) or other polymers to form PPE/PS alloys (such as Noryl resin) to improve fluidity and reduce costs. It is widely used in automobiles, electronics, home appliances and industrial parts.
The core advantage of PPE lies in its excellent thermal stability and electrical properties. It can maintain strength and rigidity at continuous use temperatures of 120-150°C, and can even withstand short-term temperatures of more than 200°C, which makes it an excellent performer in automotive engine compartment parts (such as intake manifolds) or electrical housings. In addition, PPE has a low dielectric constant (about 2.5-2.7), low dielectric loss, and is stable over a wide frequency range and high humidity, so it is often used to make cable insulators, connectors, and circuit board substrates. Its low water absorption (about 0.06-0.1%) and resistance to acids, alkalis, and non-polar solvents also make it reliable in chemical exposure environments, such as in water treatment equipment or battery housings.
The modified PPE/PS alloy further expands its application scenarios. By blending with PS, the processing performance of PPE is significantly improved, and it can be molded by injection molding, extrusion, or blow molding, while retaining high impact strength (up to 200-300 J/m after modification) and surface hardness. This alloy has a low density (about 1.06-1.10 g/cm³), making it ideal for lightweight designs. In addition, PPE is inherently flame retardant (UL94 V-1 to V-0 ratings), and can meet safety standards without the addition of halogen flame retardants, which is particularly important in electronic products and household appliances (such as TV cases and microwave oven parts). Modified PPE can also be reinforced with glass fiber or carbon fiber to further improve strength and heat resistance, making it suitable for more demanding industrial uses.
However, polystyrene ether also has some limitations. Pure PPE has low crystallinity and a high melting point (about 257°C). The processing temperature needs to reach 280-320°C, which has high equipment requirements and is easily oxidized and degraded. Therefore, the oxygen content needs to be strictly controlled during production. In addition, PPE has poor tolerance to aromatic hydrocarbons (such as benzene and toluene) and halogenated hydrocarbons. Long-term contact may cause swelling or cracking, which limits its use in certain chemical environments. At the same time, the impact toughness of unmodified PPE is low (about 50 J/m), which needs to be improved by blending or toughening agents. Nevertheless, the maturity of modification technology has effectively made up for these shortcomings, making PPE more competitive in practical applications.
From the perspective of application and development, PPE has received increasing attention in sustainable design due to its comprehensive performance. Its low density and durability support lightweight vehicles and reduce fuel consumption; its electrical insulation meets the needs of 5G equipment and new energy batteries. For example, in electric vehicle battery modules, PPE/PS alloys are used to make partitions and shells, which are both light and resistant to high temperatures. With the development of 3D printing technology, modified formulas of PPE have also begun to explore the field of additive manufacturing, using its thermal stability to produce complex parts. Overall, polystyrene ether occupies an important position in modern industry due to its high performance and modification flexibility. In the future, with environmental protection needs and technological progress, its application potential in high value-added fields will be further released.
Report Scope
This report aims to deliver a thorough analysis of the global market for Polyphenylene Ether (PPE), offering both quantitative and qualitative insights to assist readers in formulating business growth strategies, evaluating the competitive landscape, understanding their current market position, and making well-informed decisions regarding Polyphenylene Ether (PPE).
The report is enriched with qualitative evaluations, including market drivers, challenges, Porter's Five Forces, regulatory frameworks, consumer preferences, and ESG (Environmental, Social, and Governance) factors.
The report provides detailed classification of Polyphenylene Ether (PPE), such as type, etc.; detailed examples of Polyphenylene Ether (PPE) applications, such as application one, etc., and provides comprehensive historical (2020-2025) and forecast (2026-2031) market size data.
The report provides detailed classification of Polyphenylene Ether (PPE), such as PPO Resin, MPPO, etc.; detailed examples of Polyphenylene Ether (PPE) applications, such as Air Separation Membranes, Medical Instruments, Domestic Appliances, Automotive (Structural Parts), Electronic Components, Fluid Handling, Other, etc., and provides comprehensive historical (2020-2025) and forecast (2026-2031) market size data.
The report covers key global regions-North America, Europe, Asia-Pacific, Latin America, and the Middle East & Africa-providing granular, country-specific insights for major markets such as the United States, China, Germany, and Brazil.
The report deeply explores the competitive landscape of Polyphenylene Ether (PPE) products, details the sales, revenue, and regional layout of some of the world's leading manufacturers, and provides in-depth company profiles and contact details.
The report contains a comprehensive industry chain analysis covering raw materials, downstream customers and sales channels.
Core Chapters
Chapter One: Introduces the study scope of this report, market status, market drivers, challenges, porters five forces analysis, regulatory policy, consumer preference, market attractiveness and ESG analysis.
Chapter Two: market segments by Type, covering the market size and development potential of each market segment, to help readers find the blue ocean market in different market segments.
Chapter Three: Polyphenylene Ether (PPE) market sales and revenue in regional level and country level. It provides a quantitative analysis of the market size and development potential of each region and its main countries and introduces the market development, future development prospects, market space, and production of each country in the world.
Chapter Four: Provides the analysis of various market segments by Application, covering the market size and development potential of each market segment, to help readers find the blue ocean market in different downstream markets.
Chapter Five: Detailed analysis of Polyphenylene Ether (PPE) manufacturers competitive landscape, price, sales, revenue, market share, footprint, merger, and acquisition information, etc.
Chapter Six: Provides profiles of leading manufacturers, introducing the basic situation of the main companies in the market in detail, including product sales, revenue, price, gross margin, product introduction.
Chapter Seven: Analysis of industrial chain, key raw materials, customers and sales channel.
Chapter Eight: Key Takeaways and Final Conclusions
Chapter Nine: Methodology and Sources.
The core advantage of PPE lies in its excellent thermal stability and electrical properties. It can maintain strength and rigidity at continuous use temperatures of 120-150°C, and can even withstand short-term temperatures of more than 200°C, which makes it an excellent performer in automotive engine compartment parts (such as intake manifolds) or electrical housings. In addition, PPE has a low dielectric constant (about 2.5-2.7), low dielectric loss, and is stable over a wide frequency range and high humidity, so it is often used to make cable insulators, connectors, and circuit board substrates. Its low water absorption (about 0.06-0.1%) and resistance to acids, alkalis, and non-polar solvents also make it reliable in chemical exposure environments, such as in water treatment equipment or battery housings.
The modified PPE/PS alloy further expands its application scenarios. By blending with PS, the processing performance of PPE is significantly improved, and it can be molded by injection molding, extrusion, or blow molding, while retaining high impact strength (up to 200-300 J/m after modification) and surface hardness. This alloy has a low density (about 1.06-1.10 g/cm³), making it ideal for lightweight designs. In addition, PPE is inherently flame retardant (UL94 V-1 to V-0 ratings), and can meet safety standards without the addition of halogen flame retardants, which is particularly important in electronic products and household appliances (such as TV cases and microwave oven parts). Modified PPE can also be reinforced with glass fiber or carbon fiber to further improve strength and heat resistance, making it suitable for more demanding industrial uses.
However, polystyrene ether also has some limitations. Pure PPE has low crystallinity and a high melting point (about 257°C). The processing temperature needs to reach 280-320°C, which has high equipment requirements and is easily oxidized and degraded. Therefore, the oxygen content needs to be strictly controlled during production. In addition, PPE has poor tolerance to aromatic hydrocarbons (such as benzene and toluene) and halogenated hydrocarbons. Long-term contact may cause swelling or cracking, which limits its use in certain chemical environments. At the same time, the impact toughness of unmodified PPE is low (about 50 J/m), which needs to be improved by blending or toughening agents. Nevertheless, the maturity of modification technology has effectively made up for these shortcomings, making PPE more competitive in practical applications.
From the perspective of application and development, PPE has received increasing attention in sustainable design due to its comprehensive performance. Its low density and durability support lightweight vehicles and reduce fuel consumption; its electrical insulation meets the needs of 5G equipment and new energy batteries. For example, in electric vehicle battery modules, PPE/PS alloys are used to make partitions and shells, which are both light and resistant to high temperatures. With the development of 3D printing technology, modified formulas of PPE have also begun to explore the field of additive manufacturing, using its thermal stability to produce complex parts. Overall, polystyrene ether occupies an important position in modern industry due to its high performance and modification flexibility. In the future, with environmental protection needs and technological progress, its application potential in high value-added fields will be further released.
Report Scope
This report aims to deliver a thorough analysis of the global market for Polyphenylene Ether (PPE), offering both quantitative and qualitative insights to assist readers in formulating business growth strategies, evaluating the competitive landscape, understanding their current market position, and making well-informed decisions regarding Polyphenylene Ether (PPE).
The report is enriched with qualitative evaluations, including market drivers, challenges, Porter's Five Forces, regulatory frameworks, consumer preferences, and ESG (Environmental, Social, and Governance) factors.
The report provides detailed classification of Polyphenylene Ether (PPE), such as type, etc.; detailed examples of Polyphenylene Ether (PPE) applications, such as application one, etc., and provides comprehensive historical (2020-2025) and forecast (2026-2031) market size data.
The report provides detailed classification of Polyphenylene Ether (PPE), such as PPO Resin, MPPO, etc.; detailed examples of Polyphenylene Ether (PPE) applications, such as Air Separation Membranes, Medical Instruments, Domestic Appliances, Automotive (Structural Parts), Electronic Components, Fluid Handling, Other, etc., and provides comprehensive historical (2020-2025) and forecast (2026-2031) market size data.
The report covers key global regions-North America, Europe, Asia-Pacific, Latin America, and the Middle East & Africa-providing granular, country-specific insights for major markets such as the United States, China, Germany, and Brazil.
The report deeply explores the competitive landscape of Polyphenylene Ether (PPE) products, details the sales, revenue, and regional layout of some of the world's leading manufacturers, and provides in-depth company profiles and contact details.
The report contains a comprehensive industry chain analysis covering raw materials, downstream customers and sales channels.
Core Chapters
Chapter One: Introduces the study scope of this report, market status, market drivers, challenges, porters five forces analysis, regulatory policy, consumer preference, market attractiveness and ESG analysis.
Chapter Two: market segments by Type, covering the market size and development potential of each market segment, to help readers find the blue ocean market in different market segments.
Chapter Three: Polyphenylene Ether (PPE) market sales and revenue in regional level and country level. It provides a quantitative analysis of the market size and development potential of each region and its main countries and introduces the market development, future development prospects, market space, and production of each country in the world.
Chapter Four: Provides the analysis of various market segments by Application, covering the market size and development potential of each market segment, to help readers find the blue ocean market in different downstream markets.
Chapter Five: Detailed analysis of Polyphenylene Ether (PPE) manufacturers competitive landscape, price, sales, revenue, market share, footprint, merger, and acquisition information, etc.
Chapter Six: Provides profiles of leading manufacturers, introducing the basic situation of the main companies in the market in detail, including product sales, revenue, price, gross margin, product introduction.
Chapter Seven: Analysis of industrial chain, key raw materials, customers and sales channel.
Chapter Eight: Key Takeaways and Final Conclusions
Chapter Nine: Methodology and Sources.
Table of Contents
92 Pages
- 1 Polyphenylene Ether (PPE) Market Overview and Qualitative Analysis
- 1.1 Polyphenylene Ether (PPE) Product Definition and Statistical Scope
- 1.2 Polyphenylene Ether (PPE) Market Status and Outlook
- 1.2.1 Polyphenylene Ether (PPE) Market Revenue Estimates and Forecasts 2020-2031
- 1.2.2 Polyphenylene Ether (PPE) Market Sales Estimates and Forecasts 2020-2031
- 1.3 Polyphenylene Ether (PPE) Market Driver Analysis
- 1.4 Polyphenylene Ether (PPE) Market Challenges Analysis
- 1.5 Porter's Five Forces Analysis
- 1.5.1 Bargaining Power of Suppliers
- 1.5.2 Bargaining Power of Buyers/Consumers
- 1.5.3 Threat of New Entrants
- 1.5.4 Threat of Substitute Products
- 1.5.5 Intensity of Competitive Rivalry
- 1.6 Regulatory Policy Analysis
- 1.7 Consumer Preference Analysis
- 1.8 Market Attractiveness Analysis
- 1.9 ESG (Environmental, Social and Governance) Analysis
- 2 Polyphenylene Ether (PPE) Market Type Estimates & Trend Analysis
- 2.1 Polyphenylene Ether (PPE) Type Dashboard
- 2.2 Polyphenylene Ether (PPE) Market by Type
- 2.2.1 PPO Resin
- 2.2.2 MPPO
- 2.3 Global Polyphenylene Ether (PPE) Market Size by Type
- 2.3.1 Historical Analysis of the Global Polyphenylene Ether (PPE) Market Size by Type (2020-2025)
- 2.3.2 Projected Analysis of Global Polyphenylene Ether (PPE) Market Size by Type (2026-2031)
- 3 Polyphenylene Ether (PPE) Market Geography Estimates & Trend Analysis
- 3.1 Polyphenylene Ether (PPE) Geography Dashboard
- 3.2 Global Polyphenylene Ether (PPE) Historic Market Size by Region
- 3.2.1 Global Polyphenylene Ether (PPE) Market Sales by Region (2020-2025)
- 3.2.2 Global Polyphenylene Ether (PPE) Market Revenue by Region (2020-2025)
- 3.3 Global Polyphenylene Ether (PPE) Forecasted Market Size by Region
- 3.3.1 Global Polyphenylene Ether (PPE) Market Sales by Region (2026-2031)
- 3.3.2 Global Polyphenylene Ether (PPE) Market Revenue by Region (2026-2031)
- 3.4 North America Polyphenylene Ether (PPE) Market by Country
- 3.4.1 North America Polyphenylene Ether (PPE) Market Sales by Country (2020-2031)
- 3.4.2 North America Polyphenylene Ether (PPE) Market Revenue by Country (2020-2031)
- 3.4.3 United States Polyphenylene Ether (PPE) Market Sales, Revenue and Growth Rate (2020-2031)
- 3.4.4 Canada Polyphenylene Ether (PPE) Market Sales, Revenue and Growth Rate (2020-2031)
- 3.5 Europe Polyphenylene Ether (PPE) Market by Country
- 3.5.1 Europe Polyphenylene Ether (PPE) Market Sale by Country (2020-2031)
- 3.5.2 Europe Polyphenylene Ether (PPE) Market Revenue by Country (2020-2031)
- 3.5.3 Germany Market Sales, Revenue and Growth Rate (2020-2031)
- 3.5.4 France Market Sales, Revenue and Growth Rate (2020-2031)
- 3.5.5 U.K. Market Sales, Revenue and Growth Rate (2020-2031)
- 3.5.6 Italy Market Sales, Revenue and Growth Rate (2020-2031)
- 3.5.7 Spain Market Sales, Revenue and Growth Rate (2020-2031)
- 3.6 Asia-Pacific Polyphenylene Ether (PPE) Market by Region
- 3.6.1 Asia-Pacific Polyphenylene Ether (PPE) Market Sales by Region (2020-2031)
- 3.6.2 Asia-Pacific Polyphenylene Ether (PPE) Market Revenue by Region (2020-2031)
- 3.6.3 China Market Sales, Revenue and Growth Rate (2020-2031)
- 3.6.4 Japan Market Sales, Revenue and Growth Rate (2020-2031)
- 3.6.5 South Korea Market Sales, Revenue and Growth Rate (2020-2031)
- 3.6.6 India Market Sales, Revenue and Growth Rate (2020-2031)
- 3.6.7 Southeast Asia Market Sales, Revenue and Growth Rate (2020-2031)
- 3.7 Latin America Polyphenylene Ether (PPE) Market by Country
- 3.7.1 Latin America Polyphenylene Ether (PPE) Market Sales by Country (2020-2031)
- 3.7.2 Latin America Polyphenylene Ether (PPE) Market Revenue by Country (2020-2031)
- 3.7.3 Mexico Market Sales, Revenue and Growth Rate (2020-2031)
- 3.7.4 Brazil Market Sales, Revenue and Growth Rate (2020-2031)
- 3.8 Middle East and Africa Polyphenylene Ether (PPE) Market by Country
- 3.8.1 Middle East and Africa Polyphenylene Ether (PPE) Market Sales by Country (2020-2031)
- 3.8.2 Middle East and Africa Polyphenylene Ether (PPE) Market Revenue by Country (2020-2031)
- 3.8.3 Turkey Market Sales, Revenue and Growth Rate (2020-2031)
- 3.8.4 Saudi Arabia Market Sales, Revenue and Growth Rate (2020-2031)
- 3.8.5 South Africa Market Sales, Revenue and Growth Rate (2020-2031)
- 4 Polyphenylene Ether (PPE) Market Application Estimates & Trend Analysis
- 4.1 Polyphenylene Ether (PPE) Market Application Dashboard
- 4.2 Polyphenylene Ether (PPE) Market by Application
- 4.2.1 Air Separation Membranes
- 4.2.2 Medical Instruments
- 4.2.3 Domestic Appliances
- 4.2.4 Automotive (Structural Parts)
- 4.2.5 Electronic Components
- 4.2.6 Fluid Handling
- 4.2.7 Other
- 4.3 Global Polyphenylene Ether (PPE) Market Size by Application
- 4.3.1 Historical Analysis of Global Polyphenylene Ether (PPE) Market Size by Application (2020-2025)
- 4.3.2 Projected Analysis of Global Polyphenylene Ether (PPE) Market Size by Application (2026-2031)
- 5 Polyphenylene Ether (PPE) Market Competitive Landscape Analysis
- 5.1 Global Polyphenylene Ether (PPE) Leading Manufacturers' Market Sales Performance and Share Analysis
- 5.2 Global Polyphenylene Ether (PPE) Leading Manufacturers' Market Revenue Performance and Share Analysis
- 5.3 Global Polyphenylene Ether (PPE) Leading Manufacturers' Average Sales Price (2020-2025)
- 5.4 Global Polyphenylene Ether (PPE) Leading Manufacturers' Regional Footprint (Headquarters, Manufacturing Base and Sales Ares)
- 5.5 Mergers and Acquisition Analysis
- 6 Leading Manufacturers' Company Profiles
- 6.1 SABIC(GE)
- 6.1.1 SABIC(GE) Overview (Basic Corporate Information, Manufacturing Footprint, Geographic Sales Presence and Key Competitors)
- 6.1.2 SABIC(GE) Introduction and Business Overview
- 6.1.3 SABIC(GE) Polyphenylene Ether (PPE) Product Portfolio
- 6.1.4 SABIC(GE) Polyphenylene Ether (PPE) Market Performance Analysis (Revenue, Sales, Price, Gross Margin and Market Share)
- 6.2 Asahi Kasei Chemicals
- 6.2.1 Asahi Kasei Chemicals Overview (Basic Corporate Information, Manufacturing Footprint, Geographic Sales Presence and Key Competitors)
- 6.2.2 Asahi Kasei Chemicals Introduction and Business Overview
- 6.2.3 Asahi Kasei Chemicals Polyphenylene Ether (PPE) Product Portfolio
- 6.2.4 Asahi Kasei Chemicals Polyphenylene Ether (PPE) Market Performance Analysis (Revenue, Sales, Price, Gross Margin and Market Share)
- 6.3 Bluestar
- 6.3.1 Bluestar Overview (Basic Corporate Information, Manufacturing Footprint, Geographic Sales Presence and Key Competitors)
- 6.3.2 Bluestar Introduction and Business Overview
- 6.3.3 Bluestar Polyphenylene Ether (PPE) Product Portfolio
- 6.3.4 Bluestar Polyphenylene Ether (PPE) Market Performance Analysis (Revenue, Sales, Price, Gross Margin and Market Share)
- 6.4 Mitsubishi Chemicals
- 6.4.1 Mitsubishi Chemicals Overview (Basic Corporate Information, Manufacturing Footprint, Geographic Sales Presence and Key Competitors)
- 6.4.2 Mitsubishi Chemicals Introduction and Business Overview
- 6.4.3 Mitsubishi Chemicals Polyphenylene Ether (PPE) Product Portfolio
- 6.4.4 Mitsubishi Chemicals Polyphenylene Ether (PPE) Market Performance Analysis (Revenue, Sales, Price, Gross Margin and Market Share)
- 6.5 Romira(BASF)
- 6.5.1 Romira(BASF) Overview (Basic Corporate Information, Manufacturing Footprint, Geographic Sales Presence and Key Competitors)
- 6.5.2 Romira(BASF) Introduction and Business Overview
- 6.5.3 Romira(BASF) Polyphenylene Ether (PPE) Product Portfolio
- 6.5.4 Romira(BASF) Polyphenylene Ether (PPE) Market Performance Analysis (Revenue, Sales, Price, Gross Margin and Market Share)
- 6.6 Kingfa Science and Technology
- 6.6.1 Kingfa Science and Technology Overview (Basic Corporate Information, Manufacturing Footprint, Geographic Sales Presence and Key Competitors)
- 6.6.2 Kingfa Science and Technology Introduction and Business Overview
- 6.6.3 Kingfa Science and Technology Polyphenylene Ether (PPE) Product Portfolio
- 6.6.4 Kingfa Science and Technology Polyphenylene Ether (PPE) Market Performance Analysis (Revenue, Sales, Price, Gross Margin and Market Share)
- 6.7 Evonik
- 6.7.1 Evonik Overview (Basic Corporate Information, Manufacturing Footprint, Geographic Sales Presence and Key Competitors)
- 6.7.2 Evonik Introduction and Business Overview
- 6.7.3 Evonik Polyphenylene Ether (PPE) Product Portfolio
- 6.7.4 Evonik Polyphenylene Ether (PPE) Market Performance Analysis (Revenue, Sales, Price, Gross Margin and Market Share)
- 6.8 Sumitomo Chemicals
- 6.8.1 Sumitomo Chemicals Overview (Basic Corporate Information, Manufacturing Footprint, Geographic Sales Presence and Key Competitors)
- 6.8.2 Sumitomo Chemicals Introduction and Business Overview
- 6.8.3 Sumitomo Chemicals Polyphenylene Ether (PPE) Product Portfolio
- 6.8.4 Sumitomo Chemicals Polyphenylene Ether (PPE) Market Performance Analysis (Revenue, Sales, Price, Gross Margin and Market Share)
- 7 Industry Chain Analysis
- 7.1 Upstream Key Raw Materials
- 7.1.1 Raw Materials A Definition and Suppliers
- 7.1.2 Raw Materials B Definition and Suppliers
- 7.1.3 Raw Materials C Definition and Suppliers
- 7.2 Polyphenylene Ether (PPE) Typical Downstream Customers
- 7.3 Polyphenylene Ether (PPE) Sales Channel Analysis
- 8 Key Takeaways and Final Conclusions
- 9 Methodology and Sources
- 9.1 Research Methodology
- 9.2 Data Mining
- 9.2.1 Preliminary Data Sources
- 9.2.2 Secondary Sources
- 9.3 Industry Analysis Matrix
- 9.4 Disclaimer
Pricing
Currency Rates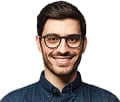
Questions or Comments?
Our team has the ability to search within reports to verify it suits your needs. We can also help maximize your budget by finding sections of reports you can purchase.