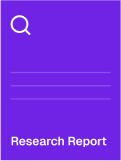
Cutting Tools and Drills for Printed Circuit Boards (PCBs) - Global Industry Market Analysis Report 2020-2031
Description
Cutting Tools and Drills for Printed Circuit Boards are precision tools used for printed circuit board (PCB) processing, including micro drills (diameter 0.05-0.3 mm), milling cutters (line width 0.03-0.1 mm), routers (for contour cutting) and engraving knives (for surface processing). The material is usually ultra-fine grain tungsten carbide (WC, particle size<0.5 μm) or diamond coating (CVD diamond, thickness 2-5 μm), and is widely used in the electronics manufacturing industry. Its high precision (tolerance<0.01 mm), high wear resistance (hardness >90 HRA), high speed (up to 200,000-300,000 RPM) and low cutting force (<0.5 N) support micro-hole drilling, line cutting and sheet forming. For example, in 5G high-density interconnect (HDI) PCBs, micro drills are used to process blind and buried vias (depth/diameter ratio>10:1, aperture<0.1 mm) to ensure high-density wiring (>1000 holes per square centimeter); in multi-layer PCB (number of layers>20 layers) production, milling cutters process micro-pitch lines (line width/line spacing<50 μm) to reduce signal interference; and in flexible circuit board (FPC) manufacturing, routers cut complex shapes (error<0.02 mm) to support foldable screen mobile phones and wearable devices. The production process uses ultra-precision grinding (surface roughness Ra<0.1 μm), laser micromachining (tool tip angle accuracy±1°) and coating technology (such as PVD or CVD coating), and the tool life can reach 5000-10000 holes (depending on the hardness of the substrate and processing parameters). The geometric accuracy and edge integrity need to be tested by scanning electron microscope (SEM) and 3D microscope. In addition, the tool needs to be matched with a high-precision CNC machine tool (speed stability ±100 RPM) and a cooling system (using compressed air or water-based cutting fluid) to reduce thermal damage and extend service life.
PCB tools and drills have performed well in the application of electronic manufacturing, but their advantages and disadvantages have triggered extensive discussions on technology, production and economy. Supporters believe that their high precision and high efficiency support the miniaturization and high performance requirements of modern electronic products. For example, in HDI board production, micro-drilling achieves high-density micro-holes through high speed and low cutting force to meet the high-speed signal transmission (>10 Gbps) of 5G devices (such as base station antennas) and smartphones; in multi-layer board processing, the micro-machining capability of the milling cutter ensures the consistency of line spacing (error<5 μm) and reduces signal loss (<0.002); in high-frequency PCBs (such as Rogers substrates, dielectric constant 3.5-4.0), diamond-coated tools have strong wear resistance (friction coefficient<0.1), reduce the frequency of tool replacement (each tool can process 500,000-1 million cm of lines), and improve production efficiency. In addition, PCB tools support a variety of substrate processing, including FR-4 (glass fiber reinforced epoxy resin), polyimide, ceramic filler substrates and metal substrates (such as aluminum substrates), adapting to the diverse needs of consumer electronics (smartphones), automotive electronics (ADAS modules) and avionics (radar systems). However, critics point out that tools and drills wear quickly, especially when processing high-hardness substrates (such as FR-4 with ceramic fillers, hardness>5 GPa) or high glass transition temperature (Tg>180°C) materials. Tool life may be shortened to 2000-3000 holes, and frequent replacement is required, increasing costs (about $1-5 per micro drill, and the tool change frequency is 1-2 times per shift). In addition, the high production cost, ultra-fine tungsten carbide powder (about $50-100 per kilogram) and diamond coating process (coating costs about $5,000 per batch) push up manufacturing costs. The price of a single tool is about $2-10, accounting for 10%-15% of the PCB processing cost. Some users also reported that micro drills may break when drilling at high speed (fracture rate is about 0.5%-1%, due to vibration or eccentricity), resulting in processing defects (such as rough hole wall or short circuit); the geometric accuracy of the tool requires high equipment (high-precision CNC machine tools are required, and the speed stability is ±100 RPM), which increases equipment investment (about 200,000-500,000 US dollars per machine tool) and maintenance costs (about 5%-10% depreciation per year).
In terms of the market, the demand for PCB tools and drills is closely related to the rapid growth of the global PCB industry, 5G communications and consumer electronics. Asia, especially China, has become the main market because of its leading PCB production in the world (estimated to account for 60% of the world in 2025, with an output value of more than 50 billion US dollars) and 5G equipment production (the number of base stations exceeds 2 million). Chinese companies (such as Shenzhen South Circuit, Pengding Technology and Shengyi Technology) use a large number of micro drills and milling cutters in the production of HDI boards, flexible boards and multilayer boards. Domestic tool manufacturers (such as Zhuzhou Diamond, Dalian Far East and Xiamen Jinlu) have reduced prices (down to US$1-3 per micro drill) through technology upgrades and large-scale production, gradually replacing imported products (such as Japan's Omron and Germany's Leitz). The North American market focuses on high-end applications. For example, the United States uses high-precision tools in avionics (such as circuit boards for Boeing 787 and Lockheed Martin F-35) and medical equipment (such as control panels for MRI and CT scanners), which must comply with IPC Class 3 standards and MIL-STD specifications. The European market focuses on high-frequency and automotive electronics. For example, Germany has growing demand for 5G antennas (produced by Siemens), autonomous driving control units (Volkswagen and BMW) and industrial automation equipment, which must comply with RoHS and REACH regulations. The growth of market demand is also driven by the trend of miniaturization and intelligence of electronic products. The demand for high-density PCBs from IoT devices (expected to exceed 30 billion in 2025), wearable devices (smart watches and fitness trackers) and new energy vehicles (production of more than 10 million vehicles) continues to increase, and the demand for cutting tools is expected to exceed 1 billion pieces in 2025. However, the market development also faces several challenges, including the supply of raw materials (such as tungsten carbide and cobalt) may be limited due to geopolitics (the main production areas are Congo and Zambia, and the cobalt production is expected to be 180,000 tons in 2025), and price fluctuations may push up costs; the processing cost increases due to tool wear (the coating technology needs to be optimized to extend the life); the rise of competitive technologies (such as laser drilling, which has higher precision but 50%-100% higher equipment costs) may divert part of the market.
In the future, the development of PCB cutting tools and drills may pay more attention to durability, intelligence and cost optimization. The development of new coating materials (e.g., nanodiamond, boron nitride, or diamond-like carbon coatings with hardness > 95 HRA) or improved tool geometry design (optimizing the helix angle and cutting edge angle, reducing cutting forces by 20%-30%) may extend tool life to 15,000-20,000 holes and reduce the frequency of replacement. The introduction of intelligent technologies, such as monitoring tool wear through sensors (real-time detection of vibration and temperature changes) or AI optimization of cutting parameters (automatic adjustment based on substrate hardness and rotation speed), may improve processing efficiency and reduce defect rates (target< 0.1%). The potential in the field of electronics manufacturing also includes supporting more advanced processes such as 6G PCB (micropores< 0.05 mm required) and flexible stretchable circuit boards (bending-resistant tools required), as well as applications in high-performance computing (HPC) and AI chip production. However, the industry still needs to face some challenges, including how to deal with the stability of the raw material supply chain (requires diversified procurement and reserves), mechanical problems of tool breakage and wear (needs to develop tougher materials), and the difficulty of finding a balance between high precision and economy (requires large-scale production to reduce costs). Overall, the demand for PCB tools and drill bits will continue to be strong due to their key role and adaptability in electronic manufacturing, but future development needs to rely on material innovation (new coatings and alloys), smart manufacturing (sensors and AI optimization) and cost control to cope with global competition and changes in market demand.
Report Scope
This report aims to deliver a thorough analysis of the global market for Cutting Tools and Drills for Printed Circuit Boards (PCBs), offering both quantitative and qualitative insights to assist readers in formulating business growth strategies, evaluating the competitive landscape, understanding their current market position, and making well-informed decisions regarding Cutting Tools and Drills for Printed Circuit Boards (PCBs).
The report is enriched with qualitative evaluations, including market drivers, challenges, Porter's Five Forces, regulatory frameworks, consumer preferences, and ESG (Environmental, Social, and Governance) factors.
The report provides detailed classification of Cutting Tools and Drills for Printed Circuit Boards (PCBs), such as type, etc.; detailed examples of Cutting Tools and Drills for Printed Circuit Boards (PCBs) applications, such as application one, etc., and provides comprehensive historical (2020-2025) and forecast (2026-2031) market size data.
The report provides detailed classification of Cutting Tools and Drills for Printed Circuit Boards (PCBs), such as PCB Drills, PCB Routers, Others, etc.; detailed examples of Cutting Tools and Drills for Printed Circuit Boards (PCBs) applications, such as Consumer Electronics, Computer, Communications, Industrial, Medical, Automotive, Military, Aerospace, Others, etc., and provides comprehensive historical (2020-2025) and forecast (2026-2031) market size data.
The report covers key global regions-North America, Europe, Asia-Pacific, Latin America, and the Middle East & Africa-providing granular, country-specific insights for major markets such as the United States, China, Germany, and Brazil.
The report deeply explores the competitive landscape of Cutting Tools and Drills for Printed Circuit Boards (PCBs) products, details the sales, revenue, and regional layout of some of the world's leading manufacturers, and provides in-depth company profiles and contact details.
The report contains a comprehensive industry chain analysis covering raw materials, downstream customers and sales channels.
Core Chapters
Chapter One: Introduces the study scope of this report, market status, market drivers, challenges, porters five forces analysis, regulatory policy, consumer preference, market attractiveness and ESG analysis.
Chapter Two: market segments by Type, covering the market size and development potential of each market segment, to help readers find the blue ocean market in different market segments.
Chapter Three: Cutting Tools and Drills for Printed Circuit Boards (PCBs) market sales and revenue in regional level and country level. It provides a quantitative analysis of the market size and development potential of each region and its main countries and introduces the market development, future development prospects, market space, and production of each country in the world.
Chapter Four: Provides the analysis of various market segments by Application, covering the market size and development potential of each market segment, to help readers find the blue ocean market in different downstream markets.
Chapter Five: Detailed analysis of Cutting Tools and Drills for Printed Circuit Boards (PCBs) manufacturers competitive landscape, price, sales, revenue, market share, footprint, merger, and acquisition information, etc.
Chapter Six: Provides profiles of leading manufacturers, introducing the basic situation of the main companies in the market in detail, including product sales, revenue, price, gross margin, product introduction.
Chapter Seven: Analysis of industrial chain, key raw materials, customers and sales channel.
Chapter Eight: Key Takeaways and Final Conclusions
Chapter Nine: Methodology and Sources.
PCB tools and drills have performed well in the application of electronic manufacturing, but their advantages and disadvantages have triggered extensive discussions on technology, production and economy. Supporters believe that their high precision and high efficiency support the miniaturization and high performance requirements of modern electronic products. For example, in HDI board production, micro-drilling achieves high-density micro-holes through high speed and low cutting force to meet the high-speed signal transmission (>10 Gbps) of 5G devices (such as base station antennas) and smartphones; in multi-layer board processing, the micro-machining capability of the milling cutter ensures the consistency of line spacing (error<5 μm) and reduces signal loss (<0.002); in high-frequency PCBs (such as Rogers substrates, dielectric constant 3.5-4.0), diamond-coated tools have strong wear resistance (friction coefficient<0.1), reduce the frequency of tool replacement (each tool can process 500,000-1 million cm of lines), and improve production efficiency. In addition, PCB tools support a variety of substrate processing, including FR-4 (glass fiber reinforced epoxy resin), polyimide, ceramic filler substrates and metal substrates (such as aluminum substrates), adapting to the diverse needs of consumer electronics (smartphones), automotive electronics (ADAS modules) and avionics (radar systems). However, critics point out that tools and drills wear quickly, especially when processing high-hardness substrates (such as FR-4 with ceramic fillers, hardness>5 GPa) or high glass transition temperature (Tg>180°C) materials. Tool life may be shortened to 2000-3000 holes, and frequent replacement is required, increasing costs (about $1-5 per micro drill, and the tool change frequency is 1-2 times per shift). In addition, the high production cost, ultra-fine tungsten carbide powder (about $50-100 per kilogram) and diamond coating process (coating costs about $5,000 per batch) push up manufacturing costs. The price of a single tool is about $2-10, accounting for 10%-15% of the PCB processing cost. Some users also reported that micro drills may break when drilling at high speed (fracture rate is about 0.5%-1%, due to vibration or eccentricity), resulting in processing defects (such as rough hole wall or short circuit); the geometric accuracy of the tool requires high equipment (high-precision CNC machine tools are required, and the speed stability is ±100 RPM), which increases equipment investment (about 200,000-500,000 US dollars per machine tool) and maintenance costs (about 5%-10% depreciation per year).
In terms of the market, the demand for PCB tools and drills is closely related to the rapid growth of the global PCB industry, 5G communications and consumer electronics. Asia, especially China, has become the main market because of its leading PCB production in the world (estimated to account for 60% of the world in 2025, with an output value of more than 50 billion US dollars) and 5G equipment production (the number of base stations exceeds 2 million). Chinese companies (such as Shenzhen South Circuit, Pengding Technology and Shengyi Technology) use a large number of micro drills and milling cutters in the production of HDI boards, flexible boards and multilayer boards. Domestic tool manufacturers (such as Zhuzhou Diamond, Dalian Far East and Xiamen Jinlu) have reduced prices (down to US$1-3 per micro drill) through technology upgrades and large-scale production, gradually replacing imported products (such as Japan's Omron and Germany's Leitz). The North American market focuses on high-end applications. For example, the United States uses high-precision tools in avionics (such as circuit boards for Boeing 787 and Lockheed Martin F-35) and medical equipment (such as control panels for MRI and CT scanners), which must comply with IPC Class 3 standards and MIL-STD specifications. The European market focuses on high-frequency and automotive electronics. For example, Germany has growing demand for 5G antennas (produced by Siemens), autonomous driving control units (Volkswagen and BMW) and industrial automation equipment, which must comply with RoHS and REACH regulations. The growth of market demand is also driven by the trend of miniaturization and intelligence of electronic products. The demand for high-density PCBs from IoT devices (expected to exceed 30 billion in 2025), wearable devices (smart watches and fitness trackers) and new energy vehicles (production of more than 10 million vehicles) continues to increase, and the demand for cutting tools is expected to exceed 1 billion pieces in 2025. However, the market development also faces several challenges, including the supply of raw materials (such as tungsten carbide and cobalt) may be limited due to geopolitics (the main production areas are Congo and Zambia, and the cobalt production is expected to be 180,000 tons in 2025), and price fluctuations may push up costs; the processing cost increases due to tool wear (the coating technology needs to be optimized to extend the life); the rise of competitive technologies (such as laser drilling, which has higher precision but 50%-100% higher equipment costs) may divert part of the market.
In the future, the development of PCB cutting tools and drills may pay more attention to durability, intelligence and cost optimization. The development of new coating materials (e.g., nanodiamond, boron nitride, or diamond-like carbon coatings with hardness > 95 HRA) or improved tool geometry design (optimizing the helix angle and cutting edge angle, reducing cutting forces by 20%-30%) may extend tool life to 15,000-20,000 holes and reduce the frequency of replacement. The introduction of intelligent technologies, such as monitoring tool wear through sensors (real-time detection of vibration and temperature changes) or AI optimization of cutting parameters (automatic adjustment based on substrate hardness and rotation speed), may improve processing efficiency and reduce defect rates (target< 0.1%). The potential in the field of electronics manufacturing also includes supporting more advanced processes such as 6G PCB (micropores< 0.05 mm required) and flexible stretchable circuit boards (bending-resistant tools required), as well as applications in high-performance computing (HPC) and AI chip production. However, the industry still needs to face some challenges, including how to deal with the stability of the raw material supply chain (requires diversified procurement and reserves), mechanical problems of tool breakage and wear (needs to develop tougher materials), and the difficulty of finding a balance between high precision and economy (requires large-scale production to reduce costs). Overall, the demand for PCB tools and drill bits will continue to be strong due to their key role and adaptability in electronic manufacturing, but future development needs to rely on material innovation (new coatings and alloys), smart manufacturing (sensors and AI optimization) and cost control to cope with global competition and changes in market demand.
Report Scope
This report aims to deliver a thorough analysis of the global market for Cutting Tools and Drills for Printed Circuit Boards (PCBs), offering both quantitative and qualitative insights to assist readers in formulating business growth strategies, evaluating the competitive landscape, understanding their current market position, and making well-informed decisions regarding Cutting Tools and Drills for Printed Circuit Boards (PCBs).
The report is enriched with qualitative evaluations, including market drivers, challenges, Porter's Five Forces, regulatory frameworks, consumer preferences, and ESG (Environmental, Social, and Governance) factors.
The report provides detailed classification of Cutting Tools and Drills for Printed Circuit Boards (PCBs), such as type, etc.; detailed examples of Cutting Tools and Drills for Printed Circuit Boards (PCBs) applications, such as application one, etc., and provides comprehensive historical (2020-2025) and forecast (2026-2031) market size data.
The report provides detailed classification of Cutting Tools and Drills for Printed Circuit Boards (PCBs), such as PCB Drills, PCB Routers, Others, etc.; detailed examples of Cutting Tools and Drills for Printed Circuit Boards (PCBs) applications, such as Consumer Electronics, Computer, Communications, Industrial, Medical, Automotive, Military, Aerospace, Others, etc., and provides comprehensive historical (2020-2025) and forecast (2026-2031) market size data.
The report covers key global regions-North America, Europe, Asia-Pacific, Latin America, and the Middle East & Africa-providing granular, country-specific insights for major markets such as the United States, China, Germany, and Brazil.
The report deeply explores the competitive landscape of Cutting Tools and Drills for Printed Circuit Boards (PCBs) products, details the sales, revenue, and regional layout of some of the world's leading manufacturers, and provides in-depth company profiles and contact details.
The report contains a comprehensive industry chain analysis covering raw materials, downstream customers and sales channels.
Core Chapters
Chapter One: Introduces the study scope of this report, market status, market drivers, challenges, porters five forces analysis, regulatory policy, consumer preference, market attractiveness and ESG analysis.
Chapter Two: market segments by Type, covering the market size and development potential of each market segment, to help readers find the blue ocean market in different market segments.
Chapter Three: Cutting Tools and Drills for Printed Circuit Boards (PCBs) market sales and revenue in regional level and country level. It provides a quantitative analysis of the market size and development potential of each region and its main countries and introduces the market development, future development prospects, market space, and production of each country in the world.
Chapter Four: Provides the analysis of various market segments by Application, covering the market size and development potential of each market segment, to help readers find the blue ocean market in different downstream markets.
Chapter Five: Detailed analysis of Cutting Tools and Drills for Printed Circuit Boards (PCBs) manufacturers competitive landscape, price, sales, revenue, market share, footprint, merger, and acquisition information, etc.
Chapter Six: Provides profiles of leading manufacturers, introducing the basic situation of the main companies in the market in detail, including product sales, revenue, price, gross margin, product introduction.
Chapter Seven: Analysis of industrial chain, key raw materials, customers and sales channel.
Chapter Eight: Key Takeaways and Final Conclusions
Chapter Nine: Methodology and Sources.
Table of Contents
128 Pages
- 1 Cutting Tools and Drills for Printed Circuit Boards (PCBs) Market Overview and Qualitative Analysis
- 1.1 Cutting Tools and Drills for Printed Circuit Boards (PCBs) Product Definition and Statistical Scope
- 1.2 Cutting Tools and Drills for Printed Circuit Boards (PCBs) Market Status and Outlook
- 1.2.1 Cutting Tools and Drills for Printed Circuit Boards (PCBs) Market Revenue Estimates and Forecasts 2020-2031
- 1.2.2 Cutting Tools and Drills for Printed Circuit Boards (PCBs) Market Sales Estimates and Forecasts 2020-2031
- 1.3 Cutting Tools and Drills for Printed Circuit Boards (PCBs) Market Driver Analysis
- 1.4 Cutting Tools and Drills for Printed Circuit Boards (PCBs) Market Challenges Analysis
- 1.5 Porter's Five Forces Analysis
- 1.5.1 Bargaining Power of Suppliers
- 1.5.2 Bargaining Power of Buyers/Consumers
- 1.5.3 Threat of New Entrants
- 1.5.4 Threat of Substitute Products
- 1.5.5 Intensity of Competitive Rivalry
- 1.6 Regulatory Policy Analysis
- 1.7 Consumer Preference Analysis
- 1.8 Market Attractiveness Analysis
- 1.9 ESG (Environmental, Social and Governance) Analysis
- 2 Cutting Tools and Drills for Printed Circuit Boards (PCBs) Market Type Estimates & Trend Analysis
- 2.1 Cutting Tools and Drills for Printed Circuit Boards (PCBs) Type Dashboard
- 2.2 Cutting Tools and Drills for Printed Circuit Boards (PCBs) Market by Type
- 2.2.1 PCB Drills
- 2.2.2 PCB Routers
- 2.2.3 Others
- 2.3 Global Cutting Tools and Drills for Printed Circuit Boards (PCBs) Market Size by Type
- 2.3.1 Historical Analysis of the Global Cutting Tools and Drills for Printed Circuit Boards (PCBs) Market Size by Type (2020-2025)
- 2.3.2 Projected Analysis of Global Cutting Tools and Drills for Printed Circuit Boards (PCBs) Market Size by Type (2026-2031)
- 3 Cutting Tools and Drills for Printed Circuit Boards (PCBs) Market Geography Estimates & Trend Analysis
- 3.1 Cutting Tools and Drills for Printed Circuit Boards (PCBs) Geography Dashboard
- 3.2 Global Cutting Tools and Drills for Printed Circuit Boards (PCBs) Historic Market Size by Region
- 3.2.1 Global Cutting Tools and Drills for Printed Circuit Boards (PCBs) Market Sales by Region (2020-2025)
- 3.2.2 Global Cutting Tools and Drills for Printed Circuit Boards (PCBs) Market Revenue by Region (2020-2025)
- 3.3 Global Cutting Tools and Drills for Printed Circuit Boards (PCBs) Forecasted Market Size by Region
- 3.3.1 Global Cutting Tools and Drills for Printed Circuit Boards (PCBs) Market Sales by Region (2026-2031)
- 3.3.2 Global Cutting Tools and Drills for Printed Circuit Boards (PCBs) Market Revenue by Region (2026-2031)
- 3.4 North America Cutting Tools and Drills for Printed Circuit Boards (PCBs) Market by Country
- 3.4.1 North America Cutting Tools and Drills for Printed Circuit Boards (PCBs) Market Sales by Country (2020-2031)
- 3.4.2 North America Cutting Tools and Drills for Printed Circuit Boards (PCBs) Market Revenue by Country (2020-2031)
- 3.4.3 United States Cutting Tools and Drills for Printed Circuit Boards (PCBs) Market Sales, Revenue and Growth Rate (2020-2031)
- 3.4.4 Canada Cutting Tools and Drills for Printed Circuit Boards (PCBs) Market Sales, Revenue and Growth Rate (2020-2031)
- 3.5 Europe Cutting Tools and Drills for Printed Circuit Boards (PCBs) Market by Country
- 3.5.1 Europe Cutting Tools and Drills for Printed Circuit Boards (PCBs) Market Sale by Country (2020-2031)
- 3.5.2 Europe Cutting Tools and Drills for Printed Circuit Boards (PCBs) Market Revenue by Country (2020-2031)
- 3.5.3 Germany Market Sales, Revenue and Growth Rate (2020-2031)
- 3.5.4 France Market Sales, Revenue and Growth Rate (2020-2031)
- 3.5.5 U.K. Market Sales, Revenue and Growth Rate (2020-2031)
- 3.5.6 Italy Market Sales, Revenue and Growth Rate (2020-2031)
- 3.5.7 Spain Market Sales, Revenue and Growth Rate (2020-2031)
- 3.6 Asia-Pacific Cutting Tools and Drills for Printed Circuit Boards (PCBs) Market by Region
- 3.6.1 Asia-Pacific Cutting Tools and Drills for Printed Circuit Boards (PCBs) Market Sales by Region (2020-2031)
- 3.6.2 Asia-Pacific Cutting Tools and Drills for Printed Circuit Boards (PCBs) Market Revenue by Region (2020-2031)
- 3.6.3 China Market Sales, Revenue and Growth Rate (2020-2031)
- 3.6.4 Japan Market Sales, Revenue and Growth Rate (2020-2031)
- 3.6.5 South Korea Market Sales, Revenue and Growth Rate (2020-2031)
- 3.6.6 India Market Sales, Revenue and Growth Rate (2020-2031)
- 3.6.7 Southeast Asia Market Sales, Revenue and Growth Rate (2020-2031)
- 3.7 Latin America Cutting Tools and Drills for Printed Circuit Boards (PCBs) Market by Country
- 3.7.1 Latin America Cutting Tools and Drills for Printed Circuit Boards (PCBs) Market Sales by Country (2020-2031)
- 3.7.2 Latin America Cutting Tools and Drills for Printed Circuit Boards (PCBs) Market Revenue by Country (2020-2031)
- 3.7.3 Mexico Market Sales, Revenue and Growth Rate (2020-2031)
- 3.7.4 Brazil Market Sales, Revenue and Growth Rate (2020-2031)
- 3.8 Middle East and Africa Cutting Tools and Drills for Printed Circuit Boards (PCBs) Market by Country
- 3.8.1 Middle East and Africa Cutting Tools and Drills for Printed Circuit Boards (PCBs) Market Sales by Country (2020-2031)
- 3.8.2 Middle East and Africa Cutting Tools and Drills for Printed Circuit Boards (PCBs) Market Revenue by Country (2020-2031)
- 3.8.3 Turkey Market Sales, Revenue and Growth Rate (2020-2031)
- 3.8.4 Saudi Arabia Market Sales, Revenue and Growth Rate (2020-2031)
- 3.8.5 South Africa Market Sales, Revenue and Growth Rate (2020-2031)
- 4 Cutting Tools and Drills for Printed Circuit Boards (PCBs) Market Application Estimates & Trend Analysis
- 4.1 Cutting Tools and Drills for Printed Circuit Boards (PCBs) Market Application Dashboard
- 4.2 Cutting Tools and Drills for Printed Circuit Boards (PCBs) Market by Application
- 4.2.1 Consumer Electronics
- 4.2.2 Computer
- 4.2.3 Communications
- 4.2.4 Industrial
- 4.2.5 Medical
- 4.2.6 Automotive
- 4.2.7 Military
- 4.2.8 Aerospace
- 4.2.9 Others
- 4.3 Global Cutting Tools and Drills for Printed Circuit Boards (PCBs) Market Size by Application
- 4.3.1 Historical Analysis of Global Cutting Tools and Drills for Printed Circuit Boards (PCBs) Market Size by Application (2020-2025)
- 4.3.2 Projected Analysis of Global Cutting Tools and Drills for Printed Circuit Boards (PCBs) Market Size by Application (2026-2031)
- 5 Cutting Tools and Drills for Printed Circuit Boards (PCBs) Market Competitive Landscape Analysis
- 5.1 Global Cutting Tools and Drills for Printed Circuit Boards (PCBs) Leading Manufacturers' Market Sales Performance and Share Analysis
- 5.2 Global Cutting Tools and Drills for Printed Circuit Boards (PCBs) Leading Manufacturers' Market Revenue Performance and Share Analysis
- 5.3 Global Cutting Tools and Drills for Printed Circuit Boards (PCBs) Leading Manufacturers' Average Sales Price (2020-2025)
- 5.4 Global Cutting Tools and Drills for Printed Circuit Boards (PCBs) Leading Manufacturers' Regional Footprint (Headquarters, Manufacturing Base and Sales Ares)
- 5.5 Mergers and Acquisition Analysis
- 6 Leading Manufacturers' Company Profiles
- 6.1 Union Tool
- 6.1.1 Union Tool Overview (Basic Corporate Information, Manufacturing Footprint, Geographic Sales Presence and Key Competitors)
- 6.1.2 Union Tool Introduction and Business Overview
- 6.1.3 Union Tool Cutting Tools and Drills for Printed Circuit Boards (PCBs) Product Portfolio
- 6.1.4 Union Tool Cutting Tools and Drills for Printed Circuit Boards (PCBs) Market Performance Analysis (Revenue, Sales, Price, Gross Margin and Market Share)
- 6.2 Guangdong Dtech Technology
- 6.2.1 Guangdong Dtech Technology Overview (Basic Corporate Information, Manufacturing Footprint, Geographic Sales Presence and Key Competitors)
- 6.2.2 Guangdong Dtech Technology Introduction and Business Overview
- 6.2.3 Guangdong Dtech Technology Cutting Tools and Drills for Printed Circuit Boards (PCBs) Product Portfolio
- 6.2.4 Guangdong Dtech Technology Cutting Tools and Drills for Printed Circuit Boards (PCBs) Market Performance Analysis (Revenue, Sales, Price, Gross Margin and Market Share)
- 6.3 Jinzhou Precision Technology
- 6.3.1 Jinzhou Precision Technology Overview (Basic Corporate Information, Manufacturing Footprint, Geographic Sales Presence and Key Competitors)
- 6.3.2 Jinzhou Precision Technology Introduction and Business Overview
- 6.3.3 Jinzhou Precision Technology Cutting Tools and Drills for Printed Circuit Boards (PCBs) Product Portfolio
- 6.3.4 Jinzhou Precision Technology Cutting Tools and Drills for Printed Circuit Boards (PCBs) Market Performance Analysis (Revenue, Sales, Price, Gross Margin and Market Share)
- 6.4 Topoint Technology
- 6.4.1 Topoint Technology Overview (Basic Corporate Information, Manufacturing Footprint, Geographic Sales Presence and Key Competitors)
- 6.4.2 Topoint Technology Introduction and Business Overview
- 6.4.3 Topoint Technology Cutting Tools and Drills for Printed Circuit Boards (PCBs) Product Portfolio
- 6.4.4 Topoint Technology Cutting Tools and Drills for Printed Circuit Boards (PCBs) Market Performance Analysis (Revenue, Sales, Price, Gross Margin and Market Share)
- 6.5 T.C.T. Group
- 6.5.1 T.C.T. Group Overview (Basic Corporate Information, Manufacturing Footprint, Geographic Sales Presence and Key Competitors)
- 6.5.2 T.C.T. Group Introduction and Business Overview
- 6.5.3 T.C.T. Group Cutting Tools and Drills for Printed Circuit Boards (PCBs) Product Portfolio
- 6.5.4 T.C.T. Group Cutting Tools and Drills for Printed Circuit Boards (PCBs) Market Performance Analysis (Revenue, Sales, Price, Gross Margin and Market Share)
- 6.6 Xinxiang Good Team Electronics
- 6.6.1 Xinxiang Good Team Electronics Overview (Basic Corporate Information, Manufacturing Footprint, Geographic Sales Presence and Key Competitors)
- 6.6.2 Xinxiang Good Team Electronics Introduction and Business Overview
- 6.6.3 Xinxiang Good Team Electronics Cutting Tools and Drills for Printed Circuit Boards (PCBs) Product Portfolio
- 6.6.4 Xinxiang Good Team Electronics Cutting Tools and Drills for Printed Circuit Boards (PCBs) Market Performance Analysis (Revenue, Sales, Price, Gross Margin and Market Share)
- 6.7 KYOCERA Precision Tools
- 6.7.1 KYOCERA Precision Tools Overview (Basic Corporate Information, Manufacturing Footprint, Geographic Sales Presence and Key Competitors)
- 6.7.2 KYOCERA Precision Tools Introduction and Business Overview
- 6.7.3 KYOCERA Precision Tools Cutting Tools and Drills for Printed Circuit Boards (PCBs) Product Portfolio
- 6.7.4 KYOCERA Precision Tools Cutting Tools and Drills for Printed Circuit Boards (PCBs) Market Performance Analysis (Revenue, Sales, Price, Gross Margin and Market Share)
- 6.8 Key Ware Electronics
- 6.8.1 Key Ware Electronics Overview (Basic Corporate Information, Manufacturing Footprint, Geographic Sales Presence and Key Competitors)
- 6.8.2 Key Ware Electronics Introduction and Business Overview
- 6.8.3 Key Ware Electronics Cutting Tools and Drills for Printed Circuit Boards (PCBs) Product Portfolio
- 6.8.4 Key Ware Electronics Cutting Tools and Drills for Printed Circuit Boards (PCBs) Market Performance Analysis (Revenue, Sales, Price, Gross Margin and Market Share)
- 6.9 Yichang Josn Seiko Technology
- 6.9.1 Yichang Josn Seiko Technology Overview (Basic Corporate Information, Manufacturing Footprint, Geographic Sales Presence and Key Competitors)
- 6.9.2 Yichang Josn Seiko Technology Introduction and Business Overview
- 6.9.3 Yichang Josn Seiko Technology Cutting Tools and Drills for Printed Circuit Boards (PCBs) Product Portfolio
- 6.9.4 Yichang Josn Seiko Technology Cutting Tools and Drills for Printed Circuit Boards (PCBs) Market Performance Analysis (Revenue, Sales, Price, Gross Margin and Market Share)
- 6.10 Xiamen Xiazhi Technology Tool
- 6.10.1 Xiamen Xiazhi Technology Tool Overview (Basic Corporate Information, Manufacturing Footprint, Geographic Sales Presence and Key Competitors)
- 6.10.2 Xiamen Xiazhi Technology Tool Introduction and Business Overview
- 6.10.3 Xiamen Xiazhi Technology Tool Cutting Tools and Drills for Printed Circuit Boards (PCBs) Product Portfolio
- 6.10.4 Xiamen Xiazhi Technology Tool Cutting Tools and Drills for Printed Circuit Boards (PCBs) Market Performance Analysis (Revenue, Sales, Price, Gross Margin and Market Share)
- 6.11 Chong Qing Kanzasin Technology
- 6.11.1 Chong Qing Kanzasin Technology Overview (Basic Corporate Information, Manufacturing Footprint, Geographic Sales Presence and Key Competitors)
- 6.11.2 Chong Qing Kanzasin Technology Introduction and Business Overview
- 6.11.3 Chong Qing Kanzasin Technology Cutting Tools and Drills for Printed Circuit Boards (PCBs) Product Portfolio
- 6.11.4 Chong Qing Kanzasin Technology Cutting Tools and Drills for Printed Circuit Boards (PCBs) Market Performance Analysis (Revenue, Sales, Price, Gross Margin and Market Share)
- 6.12 Tera Auto Corporation
- 6.12.1 Tera Auto Corporation Overview (Basic Corporate Information, Manufacturing Footprint, Geographic Sales Presence and Key Competitors)
- 6.12.2 Tera Auto Corporation Introduction and Business Overview
- 6.12.3 Tera Auto Corporation Cutting Tools and Drills for Printed Circuit Boards (PCBs) Product Portfolio
- 6.12.4 Tera Auto Corporation Cutting Tools and Drills for Printed Circuit Boards (PCBs) Market Performance Analysis (Revenue, Sales, Price, Gross Margin and Market Share)
- 6.13 Zhejiang Richvertex Precision Tools
- 6.13.1 Zhejiang Richvertex Precision Tools Overview (Basic Corporate Information, Manufacturing Footprint, Geographic Sales Presence and Key Competitors)
- 6.13.2 Zhejiang Richvertex Precision Tools Introduction and Business Overview
- 6.13.3 Zhejiang Richvertex Precision Tools Cutting Tools and Drills for Printed Circuit Boards (PCBs) Product Portfolio
- 6.13.4 Zhejiang Richvertex Precision Tools Cutting Tools and Drills for Printed Circuit Boards (PCBs) Market Performance Analysis (Revenue, Sales, Price, Gross Margin and Market Share)
- 6.14 Dong Guan Sheng Ying Electronics
- 6.14.1 Dong Guan Sheng Ying Electronics Overview (Basic Corporate Information, Manufacturing Footprint, Geographic Sales Presence and Key Competitors)
- 6.14.2 Dong Guan Sheng Ying Electronics Introduction and Business Overview
- 6.14.3 Dong Guan Sheng Ying Electronics Cutting Tools and Drills for Printed Circuit Boards (PCBs) Product Portfolio
- 6.14.4 Dong Guan Sheng Ying Electronics Cutting Tools and Drills for Printed Circuit Boards (PCBs) Market Performance Analysis (Revenue, Sales, Price, Gross Margin and Market Share)
- 6.15 HAM Precision
- 6.15.1 HAM Precision Overview (Basic Corporate Information, Manufacturing Footprint, Geographic Sales Presence and Key Competitors)
- 6.15.2 HAM Precision Introduction and Business Overview
- 6.15.3 HAM Precision Cutting Tools and Drills for Printed Circuit Boards (PCBs) Product Portfolio
- 6.15.4 HAM Precision Cutting Tools and Drills for Printed Circuit Boards (PCBs) Market Performance Analysis (Revenue, Sales, Price, Gross Margin and Market Share)
- 6.16 IND-SPHINX Precision
- 6.16.1 IND-SPHINX Precision Overview (Basic Corporate Information, Manufacturing Footprint, Geographic Sales Presence and Key Competitors)
- 6.16.2 IND-SPHINX Precision Introduction and Business Overview
- 6.16.3 IND-SPHINX Precision Cutting Tools and Drills for Printed Circuit Boards (PCBs) Product Portfolio
- 6.16.4 IND-SPHINX Precision Cutting Tools and Drills for Printed Circuit Boards (PCBs) Market Performance Analysis (Revenue, Sales, Price, Gross Margin and Market Share)
- 6.17 Tungaloy
- 6.17.1 Tungaloy Overview (Basic Corporate Information, Manufacturing Footprint, Geographic Sales Presence and Key Competitors)
- 6.17.2 Tungaloy Introduction and Business Overview
- 6.17.3 Tungaloy Cutting Tools and Drills for Printed Circuit Boards (PCBs) Product Portfolio
- 6.17.4 Tungaloy Cutting Tools and Drills for Printed Circuit Boards (PCBs) Market Performance Analysis (Revenue, Sales, Price, Gross Margin and Market Share)
- 6.18 Diamond Tech
- 6.18.1 Diamond Tech Overview (Basic Corporate Information, Manufacturing Footprint, Geographic Sales Presence and Key Competitors)
- 6.18.2 Diamond Tech Introduction and Business Overview
- 6.18.3 Diamond Tech Cutting Tools and Drills for Printed Circuit Boards (PCBs) Product Portfolio
- 6.18.4 Diamond Tech Cutting Tools and Drills for Printed Circuit Boards (PCBs) Market Performance Analysis (Revenue, Sales, Price, Gross Margin and Market Share)
- 6.19 WELL-SUN Precision Tool
- 6.19.1 WELL-SUN Precision Tool Overview (Basic Corporate Information, Manufacturing Footprint, Geographic Sales Presence and Key Competitors)
- 6.19.2 WELL-SUN Precision Tool Introduction and Business Overview
- 6.19.3 WELL-SUN Precision Tool Cutting Tools and Drills for Printed Circuit Boards (PCBs) Product Portfolio
- 6.19.4 WELL-SUN Precision Tool Cutting Tools and Drills for Printed Circuit Boards (PCBs) Market Performance Analysis (Revenue, Sales, Price, Gross Margin and Market Share)
- 6.20 AOSHITOOL
- 6.20.1 AOSHITOOL Overview (Basic Corporate Information, Manufacturing Footprint, Geographic Sales Presence and Key Competitors)
- 6.20.2 AOSHITOOL Introduction and Business Overview
- 6.20.3 AOSHITOOL Cutting Tools and Drills for Printed Circuit Boards (PCBs) Product Portfolio
- 6.20.4 AOSHITOOL Cutting Tools and Drills for Printed Circuit Boards (PCBs) Market Performance Analysis (Revenue, Sales, Price, Gross Margin and Market Share)
- 6.21 CTC
- 6.21.1 CTC Overview (Basic Corporate Information, Manufacturing Footprint, Geographic Sales Presence and Key Competitors)
- 6.21.2 CTC Introduction and Business Overview
- 6.21.3 CTC Cutting Tools and Drills for Printed Circuit Boards (PCBs) Product Portfolio
- 6.21.4 CTC Cutting Tools and Drills for Printed Circuit Boards (PCBs) Market Performance Analysis (Revenue, Sales, Price, Gross Margin and Market Share)
- 7 Industry Chain Analysis
- 7.1 Upstream Key Raw Materials
- 7.1.1 Raw Materials A Definition and Suppliers
- 7.1.2 Raw Materials B Definition and Suppliers
- 7.1.3 Raw Materials C Definition and Suppliers
- 7.2 Cutting Tools and Drills for Printed Circuit Boards (PCBs) Typical Downstream Customers
- 7.3 Cutting Tools and Drills for Printed Circuit Boards (PCBs) Sales Channel Analysis
- 8 Key Takeaways and Final Conclusions
- 9 Methodology and Sources
- 9.1 Research Methodology
- 9.2 Data Mining
- 9.2.1 Preliminary Data Sources
- 9.2.2 Secondary Sources
- 9.3 Industry Analysis Matrix
- 9.4 Disclaimer
Pricing
Currency Rates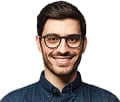
Questions or Comments?
Our team has the ability to search within reports to verify it suits your needs. We can also help maximize your budget by finding sections of reports you can purchase.