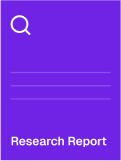
CNC Controller System - Global Industry Market Analysis Report 2020-2031
Description
A CNC controller system is a core electronic control unit used to control computer numerical control (CNC) machine tools. It achieves precise control of machining processes such as cutting, milling, turning, grinding and drilling through preset programming instructions. It is usually composed of hardware (such as processors, memory and input/output interfaces) and software (such as operating systems and machining programs). The core functions include path planning, speed control and error compensation. The CNC controller system drives the servo motor and spindle by reading G-code or M-code instructions to achieve high-precision machining of workpieces. It is widely used in metal processing, woodworking, aerospace manufacturing, mold production and automotive parts manufacturing. Its design focuses on high precision, real-time and reliability, and can adapt to a variety of needs from simple parts to complex three-dimensional surface machining.
The application of CNC controller systems has sparked widespread discussion in the manufacturing industry. Supporters believe that its high precision and automation capabilities have greatly promoted the upgrading of modern manufacturing, especially in machining scenarios that require high precision and complex shapes. For example, in the aerospace field, CNC controller systems can process complex turbine blades and fuselage components to ensure micron-level accuracy and surface finish. In addition, the flexibility of CNC controller systems enables them to adapt to the production needs of small batches and multiple varieties. The processing of different parts can be achieved by quickly changing programs, which is very suitable for customized production and rapid prototyping. Modern CNC controller systems also integrate human-machine interaction interfaces (such as touch screens) and network functions, support remote monitoring and data acquisition, and further improve production efficiency. However, critics point out that the initial cost of CNC controller systems is high, and the procurement, installation and commissioning of equipment require a large amount of capital investment, which may be a burden for small and medium-sized enterprises. In addition, the operation and programming of CNC systems require the support of professional technicians. Ordinary workers may need to receive long-term training to master them, and the shortage of technicians may become a bottleneck. Some users also reported that there are problems with the software compatibility of CNC controller systems. For example, program migration between machine tools of different brands may require additional adjustments, and the complexity of system upgrades and maintenance may also increase operating costs.
In terms of the market, the demand for CNC controller systems is closely related to the trend of intelligence and automation in the global manufacturing industry. Asia, especially China, has become the main market for CNC controller systems due to its huge manufacturing base and rapidly developing industrial automation. China's large-scale demand in automobile manufacturing, electronic product production and high-speed rail equipment manufacturing has promoted the widespread application of CNC systems. The North American and European markets pay more attention to technological innovation and high-end applications. For example, the multi-axis CNC systems used in aerospace and medical equipment manufacturing can achieve five-axis linkage processing and meet the processing requirements of complex parts. The growth of market demand is also driven by the trend of Industry 4.0 and intelligent manufacturing. More and more companies hope to achieve flexible production and digital management through CNC technology to cope with rapidly changing market demands. However, market development also faces some challenges, such as the development of core hardware (such as high-performance processors) and software technology is mainly in the hands of a few European and American companies, which may lead to supply chain dependence and price fluctuations. In addition, the energy consumption and maintenance costs of CNC controller systems are high, which may affect their promotion in areas with lower labor costs.
In the future, the development of CNC controller systems will focus on technological progress and intelligence. The integration of artificial intelligence and Internet of Things technologies may significantly improve the performance of the system, such as adaptive processing parameter adjustment through machine learning algorithms, reducing human intervention, and improving processing efficiency and consistency. In addition, the promotion of open CNC platforms may enhance the compatibility of the system, allowing users to customize functions according to their needs, thereby reducing development costs. The application potential of CNC controller systems in additive manufacturing (3D printing) and hybrid manufacturing is also worthy of attention, for example, by combining traditional subtractive processing and additive technology to achieve integrated manufacturing of complex parts. However, the industry still needs to face some challenges, such as the rise of competitive technologies (such as robotic processing systems) that may divert part of the market, and high costs and complexity may also limit its popularity in developing countries. Overall, CNC controller systems will continue to play a key role in the manufacturing industry with their high precision and high efficiency, but they need to meet future challenges through technological innovation, cost control and talent training to ensure their long-term market competitiveness.
Report Scope
This report aims to deliver a thorough analysis of the global market for CNC Controller System, offering both quantitative and qualitative insights to assist readers in formulating business growth strategies, evaluating the competitive landscape, understanding their current market position, and making well-informed decisions regarding CNC Controller System.
The report is enriched with qualitative evaluations, including market drivers, challenges, Porter's Five Forces, regulatory frameworks, consumer preferences, and ESG (Environmental, Social, and Governance) factors.
The report provides detailed classification of CNC Controller System, such as type, etc.; detailed examples of CNC Controller System applications, such as application one, etc., and provides comprehensive historical (2020-2025) and forecast (2026-2031) market size data.
The report provides detailed classification of CNC Controller System, such as Three-axis System, Four-axis System, Five-axis System, Others, etc.; detailed examples of CNC Controller System applications, such as Aerospace, Automotive, Medical Equipment, General Manufacturing, Semiconductor/Electronic Equipment, Other, etc., and provides comprehensive historical (2020-2025) and forecast (2026-2031) market size data.
The report covers key global regions-North America, Europe, Asia-Pacific, Latin America, and the Middle East & Africa-providing granular, country-specific insights for major markets such as the United States, China, Germany, and Brazil.
The report deeply explores the competitive landscape of CNC Controller System products, details the sales, revenue, and regional layout of some of the world's leading manufacturers, and provides in-depth company profiles and contact details.
The report contains a comprehensive industry chain analysis covering raw materials, downstream customers and sales channels.
Core Chapters
Chapter One: Introduces the study scope of this report, market status, market drivers, challenges, porters five forces analysis, regulatory policy, consumer preference, market attractiveness and ESG analysis.
Chapter Two: market segments by Type, covering the market size and development potential of each market segment, to help readers find the blue ocean market in different market segments.
Chapter Three: CNC Controller System market sales and revenue in regional level and country level. It provides a quantitative analysis of the market size and development potential of each region and its main countries and introduces the market development, future development prospects, market space, and production of each country in the world.
Chapter Four: Provides the analysis of various market segments by Application, covering the market size and development potential of each market segment, to help readers find the blue ocean market in different downstream markets.
Chapter Five: Detailed analysis of CNC Controller System manufacturers competitive landscape, price, sales, revenue, market share, footprint, merger, and acquisition information, etc.
Chapter Six: Provides profiles of leading manufacturers, introducing the basic situation of the main companies in the market in detail, including product sales, revenue, price, gross margin, product introduction.
Chapter Seven: Analysis of industrial chain, key raw materials, customers and sales channel.
Chapter Eight: Key Takeaways and Final Conclusions
Chapter Nine: Methodology and Sources.
The application of CNC controller systems has sparked widespread discussion in the manufacturing industry. Supporters believe that its high precision and automation capabilities have greatly promoted the upgrading of modern manufacturing, especially in machining scenarios that require high precision and complex shapes. For example, in the aerospace field, CNC controller systems can process complex turbine blades and fuselage components to ensure micron-level accuracy and surface finish. In addition, the flexibility of CNC controller systems enables them to adapt to the production needs of small batches and multiple varieties. The processing of different parts can be achieved by quickly changing programs, which is very suitable for customized production and rapid prototyping. Modern CNC controller systems also integrate human-machine interaction interfaces (such as touch screens) and network functions, support remote monitoring and data acquisition, and further improve production efficiency. However, critics point out that the initial cost of CNC controller systems is high, and the procurement, installation and commissioning of equipment require a large amount of capital investment, which may be a burden for small and medium-sized enterprises. In addition, the operation and programming of CNC systems require the support of professional technicians. Ordinary workers may need to receive long-term training to master them, and the shortage of technicians may become a bottleneck. Some users also reported that there are problems with the software compatibility of CNC controller systems. For example, program migration between machine tools of different brands may require additional adjustments, and the complexity of system upgrades and maintenance may also increase operating costs.
In terms of the market, the demand for CNC controller systems is closely related to the trend of intelligence and automation in the global manufacturing industry. Asia, especially China, has become the main market for CNC controller systems due to its huge manufacturing base and rapidly developing industrial automation. China's large-scale demand in automobile manufacturing, electronic product production and high-speed rail equipment manufacturing has promoted the widespread application of CNC systems. The North American and European markets pay more attention to technological innovation and high-end applications. For example, the multi-axis CNC systems used in aerospace and medical equipment manufacturing can achieve five-axis linkage processing and meet the processing requirements of complex parts. The growth of market demand is also driven by the trend of Industry 4.0 and intelligent manufacturing. More and more companies hope to achieve flexible production and digital management through CNC technology to cope with rapidly changing market demands. However, market development also faces some challenges, such as the development of core hardware (such as high-performance processors) and software technology is mainly in the hands of a few European and American companies, which may lead to supply chain dependence and price fluctuations. In addition, the energy consumption and maintenance costs of CNC controller systems are high, which may affect their promotion in areas with lower labor costs.
In the future, the development of CNC controller systems will focus on technological progress and intelligence. The integration of artificial intelligence and Internet of Things technologies may significantly improve the performance of the system, such as adaptive processing parameter adjustment through machine learning algorithms, reducing human intervention, and improving processing efficiency and consistency. In addition, the promotion of open CNC platforms may enhance the compatibility of the system, allowing users to customize functions according to their needs, thereby reducing development costs. The application potential of CNC controller systems in additive manufacturing (3D printing) and hybrid manufacturing is also worthy of attention, for example, by combining traditional subtractive processing and additive technology to achieve integrated manufacturing of complex parts. However, the industry still needs to face some challenges, such as the rise of competitive technologies (such as robotic processing systems) that may divert part of the market, and high costs and complexity may also limit its popularity in developing countries. Overall, CNC controller systems will continue to play a key role in the manufacturing industry with their high precision and high efficiency, but they need to meet future challenges through technological innovation, cost control and talent training to ensure their long-term market competitiveness.
Report Scope
This report aims to deliver a thorough analysis of the global market for CNC Controller System, offering both quantitative and qualitative insights to assist readers in formulating business growth strategies, evaluating the competitive landscape, understanding their current market position, and making well-informed decisions regarding CNC Controller System.
The report is enriched with qualitative evaluations, including market drivers, challenges, Porter's Five Forces, regulatory frameworks, consumer preferences, and ESG (Environmental, Social, and Governance) factors.
The report provides detailed classification of CNC Controller System, such as type, etc.; detailed examples of CNC Controller System applications, such as application one, etc., and provides comprehensive historical (2020-2025) and forecast (2026-2031) market size data.
The report provides detailed classification of CNC Controller System, such as Three-axis System, Four-axis System, Five-axis System, Others, etc.; detailed examples of CNC Controller System applications, such as Aerospace, Automotive, Medical Equipment, General Manufacturing, Semiconductor/Electronic Equipment, Other, etc., and provides comprehensive historical (2020-2025) and forecast (2026-2031) market size data.
The report covers key global regions-North America, Europe, Asia-Pacific, Latin America, and the Middle East & Africa-providing granular, country-specific insights for major markets such as the United States, China, Germany, and Brazil.
The report deeply explores the competitive landscape of CNC Controller System products, details the sales, revenue, and regional layout of some of the world's leading manufacturers, and provides in-depth company profiles and contact details.
The report contains a comprehensive industry chain analysis covering raw materials, downstream customers and sales channels.
Core Chapters
Chapter One: Introduces the study scope of this report, market status, market drivers, challenges, porters five forces analysis, regulatory policy, consumer preference, market attractiveness and ESG analysis.
Chapter Two: market segments by Type, covering the market size and development potential of each market segment, to help readers find the blue ocean market in different market segments.
Chapter Three: CNC Controller System market sales and revenue in regional level and country level. It provides a quantitative analysis of the market size and development potential of each region and its main countries and introduces the market development, future development prospects, market space, and production of each country in the world.
Chapter Four: Provides the analysis of various market segments by Application, covering the market size and development potential of each market segment, to help readers find the blue ocean market in different downstream markets.
Chapter Five: Detailed analysis of CNC Controller System manufacturers competitive landscape, price, sales, revenue, market share, footprint, merger, and acquisition information, etc.
Chapter Six: Provides profiles of leading manufacturers, introducing the basic situation of the main companies in the market in detail, including product sales, revenue, price, gross margin, product introduction.
Chapter Seven: Analysis of industrial chain, key raw materials, customers and sales channel.
Chapter Eight: Key Takeaways and Final Conclusions
Chapter Nine: Methodology and Sources.
Table of Contents
93 Pages
- 1 CNC Controller System Market Overview and Qualitative Analysis
- 1.1 CNC Controller System Product Definition and Statistical Scope
- 1.2 CNC Controller System Market Status and Outlook
- 1.2.1 CNC Controller System Market Revenue Estimates and Forecasts 2020-2031
- 1.2.2 CNC Controller System Market Sales Estimates and Forecasts 2020-2031
- 1.3 CNC Controller System Market Driver Analysis
- 1.4 CNC Controller System Market Challenges Analysis
- 1.5 Porter's Five Forces Analysis
- 1.5.1 Bargaining Power of Suppliers
- 1.5.2 Bargaining Power of Buyers/Consumers
- 1.5.3 Threat of New Entrants
- 1.5.4 Threat of Substitute Products
- 1.5.5 Intensity of Competitive Rivalry
- 1.6 Regulatory Policy Analysis
- 1.7 Consumer Preference Analysis
- 1.8 Market Attractiveness Analysis
- 1.9 ESG (Environmental, Social and Governance) Analysis
- 2 CNC Controller System Market Type Estimates & Trend Analysis
- 2.1 CNC Controller System Type Dashboard
- 2.2 CNC Controller System Market by Type
- 2.2.1 Three-axis System
- 2.2.2 Four-axis System
- 2.2.3 Five-axis System
- 2.2.4 Others
- 2.3 Global CNC Controller System Market Size by Type
- 2.3.1 Historical Analysis of the Global CNC Controller System Market Size by Type (2020-2025)
- 2.3.2 Projected Analysis of Global CNC Controller System Market Size by Type (2026-2031)
- 3 CNC Controller System Market Geography Estimates & Trend Analysis
- 3.1 CNC Controller System Geography Dashboard
- 3.2 Global CNC Controller System Historic Market Size by Region
- 3.2.1 Global CNC Controller System Market Sales by Region (2020-2025)
- 3.2.2 Global CNC Controller System Market Revenue by Region (2020-2025)
- 3.3 Global CNC Controller System Forecasted Market Size by Region
- 3.3.1 Global CNC Controller System Market Sales by Region (2026-2031)
- 3.3.2 Global CNC Controller System Market Revenue by Region (2026-2031)
- 3.4 North America CNC Controller System Market by Country
- 3.4.1 North America CNC Controller System Market Sales by Country (2020-2031)
- 3.4.2 North America CNC Controller System Market Revenue by Country (2020-2031)
- 3.4.3 United States CNC Controller System Market Sales, Revenue and Growth Rate (2020-2031)
- 3.4.4 Canada CNC Controller System Market Sales, Revenue and Growth Rate (2020-2031)
- 3.5 Europe CNC Controller System Market by Country
- 3.5.1 Europe CNC Controller System Market Sale by Country (2020-2031)
- 3.5.2 Europe CNC Controller System Market Revenue by Country (2020-2031)
- 3.5.3 Germany Market Sales, Revenue and Growth Rate (2020-2031)
- 3.5.4 France Market Sales, Revenue and Growth Rate (2020-2031)
- 3.5.5 U.K. Market Sales, Revenue and Growth Rate (2020-2031)
- 3.5.6 Italy Market Sales, Revenue and Growth Rate (2020-2031)
- 3.5.7 Spain Market Sales, Revenue and Growth Rate (2020-2031)
- 3.6 Asia-Pacific CNC Controller System Market by Region
- 3.6.1 Asia-Pacific CNC Controller System Market Sales by Region (2020-2031)
- 3.6.2 Asia-Pacific CNC Controller System Market Revenue by Region (2020-2031)
- 3.6.3 China Market Sales, Revenue and Growth Rate (2020-2031)
- 3.6.4 Japan Market Sales, Revenue and Growth Rate (2020-2031)
- 3.6.5 South Korea Market Sales, Revenue and Growth Rate (2020-2031)
- 3.6.6 India Market Sales, Revenue and Growth Rate (2020-2031)
- 3.6.7 Southeast Asia Market Sales, Revenue and Growth Rate (2020-2031)
- 3.7 Latin America CNC Controller System Market by Country
- 3.7.1 Latin America CNC Controller System Market Sales by Country (2020-2031)
- 3.7.2 Latin America CNC Controller System Market Revenue by Country (2020-2031)
- 3.7.3 Mexico Market Sales, Revenue and Growth Rate (2020-2031)
- 3.7.4 Brazil Market Sales, Revenue and Growth Rate (2020-2031)
- 3.8 Middle East and Africa CNC Controller System Market by Country
- 3.8.1 Middle East and Africa CNC Controller System Market Sales by Country (2020-2031)
- 3.8.2 Middle East and Africa CNC Controller System Market Revenue by Country (2020-2031)
- 3.8.3 Turkey Market Sales, Revenue and Growth Rate (2020-2031)
- 3.8.4 Saudi Arabia Market Sales, Revenue and Growth Rate (2020-2031)
- 3.8.5 South Africa Market Sales, Revenue and Growth Rate (2020-2031)
- 4 CNC Controller System Market Application Estimates & Trend Analysis
- 4.1 CNC Controller System Market Application Dashboard
- 4.2 CNC Controller System Market by Application
- 4.2.1 Aerospace
- 4.2.2 Automotive
- 4.2.3 Medical Equipment
- 4.2.4 General Manufacturing
- 4.2.5 Semiconductor/Electronic Equipment
- 4.2.6 Other
- 4.3 Global CNC Controller System Market Size by Application
- 4.3.1 Historical Analysis of Global CNC Controller System Market Size by Application (2020-2025)
- 4.3.2 Projected Analysis of Global CNC Controller System Market Size by Application (2026-2031)
- 5 CNC Controller System Market Competitive Landscape Analysis
- 5.1 Global CNC Controller System Leading Manufacturers' Market Sales Performance and Share Analysis
- 5.2 Global CNC Controller System Leading Manufacturers' Market Revenue Performance and Share Analysis
- 5.3 Global CNC Controller System Leading Manufacturers' Average Sales Price (2020-2025)
- 5.4 Global CNC Controller System Leading Manufacturers' Regional Footprint (Headquarters, Manufacturing Base and Sales Ares)
- 5.5 Mergers and Acquisition Analysis
- 6 Leading Manufacturers' Company Profiles
- 6.1 Fanuc Corporation
- 6.1.1 Fanuc Corporation Overview (Basic Corporate Information, Manufacturing Footprint, Geographic Sales Presence and Key Competitors)
- 6.1.2 Fanuc Corporation Introduction and Business Overview
- 6.1.3 Fanuc Corporation CNC Controller System Product Portfolio
- 6.1.4 Fanuc Corporation CNC Controller System Market Performance Analysis (Revenue, Sales, Price, Gross Margin and Market Share)
- 6.2 Mitsubishi Electric Corporation
- 6.2.1 Mitsubishi Electric Corporation Overview (Basic Corporate Information, Manufacturing Footprint, Geographic Sales Presence and Key Competitors)
- 6.2.2 Mitsubishi Electric Corporation Introduction and Business Overview
- 6.2.3 Mitsubishi Electric Corporation CNC Controller System Product Portfolio
- 6.2.4 Mitsubishi Electric Corporation CNC Controller System Market Performance Analysis (Revenue, Sales, Price, Gross Margin and Market Share)
- 6.3 Siemens
- 6.3.1 Siemens Overview (Basic Corporate Information, Manufacturing Footprint, Geographic Sales Presence and Key Competitors)
- 6.3.2 Siemens Introduction and Business Overview
- 6.3.3 Siemens CNC Controller System Product Portfolio
- 6.3.4 Siemens CNC Controller System Market Performance Analysis (Revenue, Sales, Price, Gross Margin and Market Share)
- 6.4 Heidenhain
- 6.4.1 Heidenhain Overview (Basic Corporate Information, Manufacturing Footprint, Geographic Sales Presence and Key Competitors)
- 6.4.2 Heidenhain Introduction and Business Overview
- 6.4.3 Heidenhain CNC Controller System Product Portfolio
- 6.4.4 Heidenhain CNC Controller System Market Performance Analysis (Revenue, Sales, Price, Gross Margin and Market Share)
- 6.5 Wuhan Huazhong Numerical Control Co. Ltd.
- 6.5.1 Wuhan Huazhong Numerical Control Co. Ltd. Overview (Basic Corporate Information, Manufacturing Footprint, Geographic Sales Presence and Key Competitors)
- 6.5.2 Wuhan Huazhong Numerical Control Co. Ltd. Introduction and Business Overview
- 6.5.3 Wuhan Huazhong Numerical Control Co. Ltd. CNC Controller System Product Portfolio
- 6.5.4 Wuhan Huazhong Numerical Control Co. Ltd. CNC Controller System Market Performance Analysis (Revenue, Sales, Price, Gross Margin and Market Share)
- 6.6 Fagor Automation
- 6.6.1 Fagor Automation Overview (Basic Corporate Information, Manufacturing Footprint, Geographic Sales Presence and Key Competitors)
- 6.6.2 Fagor Automation Introduction and Business Overview
- 6.6.3 Fagor Automation CNC Controller System Product Portfolio
- 6.6.4 Fagor Automation CNC Controller System Market Performance Analysis (Revenue, Sales, Price, Gross Margin and Market Share)
- 6.7 Yamazaki Mazak Corporation
- 6.7.1 Yamazaki Mazak Corporation Overview (Basic Corporate Information, Manufacturing Footprint, Geographic Sales Presence and Key Competitors)
- 6.7.2 Yamazaki Mazak Corporation Introduction and Business Overview
- 6.7.3 Yamazaki Mazak Corporation CNC Controller System Product Portfolio
- 6.7.4 Yamazaki Mazak Corporation CNC Controller System Market Performance Analysis (Revenue, Sales, Price, Gross Margin and Market Share)
- 6.8 Okuma Corporation
- 6.8.1 Okuma Corporation Overview (Basic Corporate Information, Manufacturing Footprint, Geographic Sales Presence and Key Competitors)
- 6.8.2 Okuma Corporation Introduction and Business Overview
- 6.8.3 Okuma Corporation CNC Controller System Product Portfolio
- 6.8.4 Okuma Corporation CNC Controller System Market Performance Analysis (Revenue, Sales, Price, Gross Margin and Market Share)
- 7 Industry Chain Analysis
- 7.1 Upstream Key Raw Materials
- 7.1.1 Raw Materials A Definition and Suppliers
- 7.1.2 Raw Materials B Definition and Suppliers
- 7.1.3 Raw Materials C Definition and Suppliers
- 7.2 CNC Controller System Typical Downstream Customers
- 7.3 CNC Controller System Sales Channel Analysis
- 8 Key Takeaways and Final Conclusions
- 9 Methodology and Sources
- 9.1 Research Methodology
- 9.2 Data Mining
- 9.2.1 Preliminary Data Sources
- 9.2.2 Secondary Sources
- 9.3 Industry Analysis Matrix
- 9.4 Disclaimer
Pricing
Currency Rates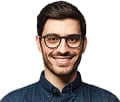
Questions or Comments?
Our team has the ability to search within reports to verify it suits your needs. We can also help maximize your budget by finding sections of reports you can purchase.