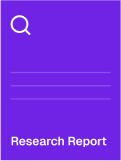
Automatic Wafer Defect Inspection System - Global Industry Market Analysis Report 2020-2031
Description
Automatic Wafer Defect Inspection System is a kind of inspection equipment used in semiconductor manufacturing. It identifies surface defects of wafers through optical imaging and AI analysis and is widely used in chip production, quality control and R&D. It usually consists of high-resolution cameras, optical systems and image processing software, and can improve inspection efficiency through automated scanning and defect classification. For example, in chip manufacturing, the automatic inspection system can identify tiny scratches and particles on wafers to ensure product quality. The automatic wafer defect inspection system is known for its high precision, automation and high efficiency, and can meet different defect detection needs through multispectral imaging and deep learning. Its application plays an important role in promoting semiconductor manufacturing and quality assurance, and is a key equipment for modern chip production.
In terms of market, The demand for automatic wafer defect detection systems is driven by the development of the semiconductor and electronics industries. With the rapid growth of the global semiconductor market, especially in the production of 5G chips and AI chips, the market demand for automatic detection systems continues to expand due to their ability to improve wafer quality and production efficiency. The rapid development of the electronics industry has also provided a broad market for detection systems. For example, in MEMS and sensor manufacturing, the system can detect micron-level defects to meet the needs of high-performance devices. In addition, with the rapid growth in the field of research and development, such as in the development of new semiconductor materials and processes, automatic detection systems can provide high-precision defect analysis to meet the market demand for high-quality detection equipment. Global attention to semiconductor technology and smart manufacturing is increasing , especially in the Asian and North American markets, the application of automatic inspection systems is expanding rapidly. However, the market also faces cost and technical challenges, such as high equipment procurement costs and difficulty in identifying complex defect types.
In the future, the development vision of automatic wafer defect inspection systems lies in the improvement of detection accuracy and intelligence. With the advancement of optical and AI technologies, future inspection systems may achieve higher resolution and faster inspection speeds, such as by developing new high-resolution cameras and multispectral imaging technologies to improve the recognition of nano-level defects and meet the needs of next-generation chips. At the same time, the industry may develop smarter inspection systems, such as by embedding deep learning and adaptive algorithms to automatically optimize defect classification and reduce errors. The automatic inspection system may also be integrated with wafer manufacturing equipment, such as optimizing production processes and reducing scrap rates by feeding back defect data in real time. In addition, with the emphasis on sustainable development, the industry may explore more energy-efficient designs, such as reducing the environmental impact of production and operation by reducing light source power consumption and using recyclable materials. In the future, automatic inspection systems may also be used in the aviation field for defect detection of high-reliability aviation chips.
In more detail, the requirements of automatic wafer defect detection systems vary in different applications. In chip production, the system requires high throughput and low false alarm rate to support high-volume manufacturing, while in R&D, flexibility and high resolution are key considerations. The manufacture of automatic inspection systems requires high-precision optical design and image processing technology, such as ensuring its imaging quality and defect recognition capabilities by accurately calibrating the camera focal length and light source angle. In addition, the use of the system needs to take into account the wafer characteristics and the inspection environment, such as improving its stability in a clean room environment by adding dust-proof design and temperature control system. In the future, as the demand for semiconductors increases, automatic wafer defect inspection systems may achieve higher accuracy and intelligence. For example, by combining with intelligent manufacturing systems, they can provide more efficient and reliable solutions for chip production and R&D, while promoting the development of inspection technology in a smarter and more environmentally friendly direction.
Report Scope
This report aims to deliver a thorough analysis of the global market for Automatic Wafer Defect Inspection System, offering both quantitative and qualitative insights to assist readers in formulating business growth strategies, evaluating the competitive landscape, understanding their current market position, and making well-informed decisions regarding Automatic Wafer Defect Inspection System.
The report is enriched with qualitative evaluations, including market drivers, challenges, Porter's Five Forces, regulatory frameworks, consumer preferences, and ESG (Environmental, Social, and Governance) factors.
The report provides detailed classification of Automatic Wafer Defect Inspection System, such as type, etc.; detailed examples of Automatic Wafer Defect Inspection System applications, such as application one, etc., and provides comprehensive historical (2020-2025) and forecast (2026-2031) market size data.
The report provides detailed classification of Automatic Wafer Defect Inspection System, such as Electron Beam Inspection System, Patterned Inspection System, Unpatterned Inspection System, etc.; detailed examples of Automatic Wafer Defect Inspection System applications, such as Electronic Semiconductor, Automotive, Others, etc., and provides comprehensive historical (2020-2025) and forecast (2026-2031) market size data.
The report covers key global regions-North America, Europe, Asia-Pacific, Latin America, and the Middle East & Africa-providing granular, country-specific insights for major markets such as the United States, China, Germany, and Brazil.
The report deeply explores the competitive landscape of Automatic Wafer Defect Inspection System products, details the sales, revenue, and regional layout of some of the world's leading manufacturers, and provides in-depth company profiles and contact details.
The report contains a comprehensive industry chain analysis covering raw materials, downstream customers and sales channels.
Core Chapters
Chapter One: Introduces the study scope of this report, market status, market drivers, challenges, porters five forces analysis, regulatory policy, consumer preference, market attractiveness and ESG analysis.
Chapter Two: market segments by Type, covering the market size and development potential of each market segment, to help readers find the blue ocean market in different market segments.
Chapter Three: Automatic Wafer Defect Inspection System market sales and revenue in regional level and country level. It provides a quantitative analysis of the market size and development potential of each region and its main countries and introduces the market development, future development prospects, market space, and production of each country in the world.
Chapter Four: Provides the analysis of various market segments by Application, covering the market size and development potential of each market segment, to help readers find the blue ocean market in different downstream markets.
Chapter Five: Detailed analysis of Automatic Wafer Defect Inspection System manufacturers competitive landscape, price, sales, revenue, market share, footprint, merger, and acquisition information, etc.
Chapter Six: Provides profiles of leading manufacturers, introducing the basic situation of the main companies in the market in detail, including product sales, revenue, price, gross margin, product introduction.
Chapter Seven: Analysis of industrial chain, key raw materials, customers and sales channel.
Chapter Eight: Key Takeaways and Final Conclusions
Chapter Nine: Methodology and Sources.
In terms of market, The demand for automatic wafer defect detection systems is driven by the development of the semiconductor and electronics industries. With the rapid growth of the global semiconductor market, especially in the production of 5G chips and AI chips, the market demand for automatic detection systems continues to expand due to their ability to improve wafer quality and production efficiency. The rapid development of the electronics industry has also provided a broad market for detection systems. For example, in MEMS and sensor manufacturing, the system can detect micron-level defects to meet the needs of high-performance devices. In addition, with the rapid growth in the field of research and development, such as in the development of new semiconductor materials and processes, automatic detection systems can provide high-precision defect analysis to meet the market demand for high-quality detection equipment. Global attention to semiconductor technology and smart manufacturing is increasing , especially in the Asian and North American markets, the application of automatic inspection systems is expanding rapidly. However, the market also faces cost and technical challenges, such as high equipment procurement costs and difficulty in identifying complex defect types.
In the future, the development vision of automatic wafer defect inspection systems lies in the improvement of detection accuracy and intelligence. With the advancement of optical and AI technologies, future inspection systems may achieve higher resolution and faster inspection speeds, such as by developing new high-resolution cameras and multispectral imaging technologies to improve the recognition of nano-level defects and meet the needs of next-generation chips. At the same time, the industry may develop smarter inspection systems, such as by embedding deep learning and adaptive algorithms to automatically optimize defect classification and reduce errors. The automatic inspection system may also be integrated with wafer manufacturing equipment, such as optimizing production processes and reducing scrap rates by feeding back defect data in real time. In addition, with the emphasis on sustainable development, the industry may explore more energy-efficient designs, such as reducing the environmental impact of production and operation by reducing light source power consumption and using recyclable materials. In the future, automatic inspection systems may also be used in the aviation field for defect detection of high-reliability aviation chips.
In more detail, the requirements of automatic wafer defect detection systems vary in different applications. In chip production, the system requires high throughput and low false alarm rate to support high-volume manufacturing, while in R&D, flexibility and high resolution are key considerations. The manufacture of automatic inspection systems requires high-precision optical design and image processing technology, such as ensuring its imaging quality and defect recognition capabilities by accurately calibrating the camera focal length and light source angle. In addition, the use of the system needs to take into account the wafer characteristics and the inspection environment, such as improving its stability in a clean room environment by adding dust-proof design and temperature control system. In the future, as the demand for semiconductors increases, automatic wafer defect inspection systems may achieve higher accuracy and intelligence. For example, by combining with intelligent manufacturing systems, they can provide more efficient and reliable solutions for chip production and R&D, while promoting the development of inspection technology in a smarter and more environmentally friendly direction.
Report Scope
This report aims to deliver a thorough analysis of the global market for Automatic Wafer Defect Inspection System, offering both quantitative and qualitative insights to assist readers in formulating business growth strategies, evaluating the competitive landscape, understanding their current market position, and making well-informed decisions regarding Automatic Wafer Defect Inspection System.
The report is enriched with qualitative evaluations, including market drivers, challenges, Porter's Five Forces, regulatory frameworks, consumer preferences, and ESG (Environmental, Social, and Governance) factors.
The report provides detailed classification of Automatic Wafer Defect Inspection System, such as type, etc.; detailed examples of Automatic Wafer Defect Inspection System applications, such as application one, etc., and provides comprehensive historical (2020-2025) and forecast (2026-2031) market size data.
The report provides detailed classification of Automatic Wafer Defect Inspection System, such as Electron Beam Inspection System, Patterned Inspection System, Unpatterned Inspection System, etc.; detailed examples of Automatic Wafer Defect Inspection System applications, such as Electronic Semiconductor, Automotive, Others, etc., and provides comprehensive historical (2020-2025) and forecast (2026-2031) market size data.
The report covers key global regions-North America, Europe, Asia-Pacific, Latin America, and the Middle East & Africa-providing granular, country-specific insights for major markets such as the United States, China, Germany, and Brazil.
The report deeply explores the competitive landscape of Automatic Wafer Defect Inspection System products, details the sales, revenue, and regional layout of some of the world's leading manufacturers, and provides in-depth company profiles and contact details.
The report contains a comprehensive industry chain analysis covering raw materials, downstream customers and sales channels.
Core Chapters
Chapter One: Introduces the study scope of this report, market status, market drivers, challenges, porters five forces analysis, regulatory policy, consumer preference, market attractiveness and ESG analysis.
Chapter Two: market segments by Type, covering the market size and development potential of each market segment, to help readers find the blue ocean market in different market segments.
Chapter Three: Automatic Wafer Defect Inspection System market sales and revenue in regional level and country level. It provides a quantitative analysis of the market size and development potential of each region and its main countries and introduces the market development, future development prospects, market space, and production of each country in the world.
Chapter Four: Provides the analysis of various market segments by Application, covering the market size and development potential of each market segment, to help readers find the blue ocean market in different downstream markets.
Chapter Five: Detailed analysis of Automatic Wafer Defect Inspection System manufacturers competitive landscape, price, sales, revenue, market share, footprint, merger, and acquisition information, etc.
Chapter Six: Provides profiles of leading manufacturers, introducing the basic situation of the main companies in the market in detail, including product sales, revenue, price, gross margin, product introduction.
Chapter Seven: Analysis of industrial chain, key raw materials, customers and sales channel.
Chapter Eight: Key Takeaways and Final Conclusions
Chapter Nine: Methodology and Sources.
Table of Contents
113 Pages
- 1 Automatic Wafer Defect Inspection System Market Overview and Qualitative Analysis
- 1.1 Automatic Wafer Defect Inspection System Product Definition and Statistical Scope
- 1.2 Automatic Wafer Defect Inspection System Market Status and Outlook
- 1.2.1 Automatic Wafer Defect Inspection System Market Revenue Estimates and Forecasts 2020-2031
- 1.2.2 Automatic Wafer Defect Inspection System Market Sales Estimates and Forecasts 2020-2031
- 1.3 Automatic Wafer Defect Inspection System Market Driver Analysis
- 1.4 Automatic Wafer Defect Inspection System Market Challenges Analysis
- 1.5 Porter's Five Forces Analysis
- 1.5.1 Bargaining Power of Suppliers
- 1.5.2 Bargaining Power of Buyers/Consumers
- 1.5.3 Threat of New Entrants
- 1.5.4 Threat of Substitute Products
- 1.5.5 Intensity of Competitive Rivalry
- 1.6 Regulatory Policy Analysis
- 1.7 Consumer Preference Analysis
- 1.8 Market Attractiveness Analysis
- 1.9 ESG (Environmental, Social and Governance) Analysis
- 2 Automatic Wafer Defect Inspection System Market Type Estimates & Trend Analysis
- 2.1 Automatic Wafer Defect Inspection System Type Dashboard
- 2.2 Automatic Wafer Defect Inspection System Market by Type
- 2.2.1 Electron Beam Inspection System
- 2.2.2 Patterned Inspection System
- 2.2.3 Unpatterned Inspection System
- 2.3 Global Automatic Wafer Defect Inspection System Market Size by Type
- 2.3.1 Historical Analysis of the Global Automatic Wafer Defect Inspection System Market Size by Type (2020-2025)
- 2.3.2 Projected Analysis of Global Automatic Wafer Defect Inspection System Market Size by Type (2026-2031)
- 3 Automatic Wafer Defect Inspection System Market Geography Estimates & Trend Analysis
- 3.1 Automatic Wafer Defect Inspection System Geography Dashboard
- 3.2 Global Automatic Wafer Defect Inspection System Historic Market Size by Region
- 3.2.1 Global Automatic Wafer Defect Inspection System Market Sales by Region (2020-2025)
- 3.2.2 Global Automatic Wafer Defect Inspection System Market Revenue by Region (2020-2025)
- 3.3 Global Automatic Wafer Defect Inspection System Forecasted Market Size by Region
- 3.3.1 Global Automatic Wafer Defect Inspection System Market Sales by Region (2026-2031)
- 3.3.2 Global Automatic Wafer Defect Inspection System Market Revenue by Region (2026-2031)
- 3.4 North America Automatic Wafer Defect Inspection System Market by Country
- 3.4.1 North America Automatic Wafer Defect Inspection System Market Sales by Country (2020-2031)
- 3.4.2 North America Automatic Wafer Defect Inspection System Market Revenue by Country (2020-2031)
- 3.4.3 United States Automatic Wafer Defect Inspection System Market Sales, Revenue and Growth Rate (2020-2031)
- 3.4.4 Canada Automatic Wafer Defect Inspection System Market Sales, Revenue and Growth Rate (2020-2031)
- 3.5 Europe Automatic Wafer Defect Inspection System Market by Country
- 3.5.1 Europe Automatic Wafer Defect Inspection System Market Sale by Country (2020-2031)
- 3.5.2 Europe Automatic Wafer Defect Inspection System Market Revenue by Country (2020-2031)
- 3.5.3 Germany Market Sales, Revenue and Growth Rate (2020-2031)
- 3.5.4 France Market Sales, Revenue and Growth Rate (2020-2031)
- 3.5.5 U.K. Market Sales, Revenue and Growth Rate (2020-2031)
- 3.5.6 Italy Market Sales, Revenue and Growth Rate (2020-2031)
- 3.5.7 Spain Market Sales, Revenue and Growth Rate (2020-2031)
- 3.6 Asia-Pacific Automatic Wafer Defect Inspection System Market by Region
- 3.6.1 Asia-Pacific Automatic Wafer Defect Inspection System Market Sales by Region (2020-2031)
- 3.6.2 Asia-Pacific Automatic Wafer Defect Inspection System Market Revenue by Region (2020-2031)
- 3.6.3 China Market Sales, Revenue and Growth Rate (2020-2031)
- 3.6.4 Japan Market Sales, Revenue and Growth Rate (2020-2031)
- 3.6.5 South Korea Market Sales, Revenue and Growth Rate (2020-2031)
- 3.6.6 India Market Sales, Revenue and Growth Rate (2020-2031)
- 3.6.7 Southeast Asia Market Sales, Revenue and Growth Rate (2020-2031)
- 3.7 Latin America Automatic Wafer Defect Inspection System Market by Country
- 3.7.1 Latin America Automatic Wafer Defect Inspection System Market Sales by Country (2020-2031)
- 3.7.2 Latin America Automatic Wafer Defect Inspection System Market Revenue by Country (2020-2031)
- 3.7.3 Mexico Market Sales, Revenue and Growth Rate (2020-2031)
- 3.7.4 Brazil Market Sales, Revenue and Growth Rate (2020-2031)
- 3.8 Middle East and Africa Automatic Wafer Defect Inspection System Market by Country
- 3.8.1 Middle East and Africa Automatic Wafer Defect Inspection System Market Sales by Country (2020-2031)
- 3.8.2 Middle East and Africa Automatic Wafer Defect Inspection System Market Revenue by Country (2020-2031)
- 3.8.3 Turkey Market Sales, Revenue and Growth Rate (2020-2031)
- 3.8.4 Saudi Arabia Market Sales, Revenue and Growth Rate (2020-2031)
- 3.8.5 South Africa Market Sales, Revenue and Growth Rate (2020-2031)
- 4 Automatic Wafer Defect Inspection System Market Application Estimates & Trend Analysis
- 4.1 Automatic Wafer Defect Inspection System Market Application Dashboard
- 4.2 Automatic Wafer Defect Inspection System Market by Application
- 4.2.1 Electronic Semiconductor
- 4.2.2 Automotive
- 4.2.3 Others
- 4.3 Global Automatic Wafer Defect Inspection System Market Size by Application
- 4.3.1 Historical Analysis of Global Automatic Wafer Defect Inspection System Market Size by Application (2020-2025)
- 4.3.2 Projected Analysis of Global Automatic Wafer Defect Inspection System Market Size by Application (2026-2031)
- 5 Automatic Wafer Defect Inspection System Market Competitive Landscape Analysis
- 5.1 Global Automatic Wafer Defect Inspection System Leading Manufacturers' Market Sales Performance and Share Analysis
- 5.2 Global Automatic Wafer Defect Inspection System Leading Manufacturers' Market Revenue Performance and Share Analysis
- 5.3 Global Automatic Wafer Defect Inspection System Leading Manufacturers' Average Sales Price (2020-2025)
- 5.4 Global Automatic Wafer Defect Inspection System Leading Manufacturers' Regional Footprint (Headquarters, Manufacturing Base and Sales Ares)
- 5.5 Mergers and Acquisition Analysis
- 6 Leading Manufacturers' Company Profiles
- 6.1 KLA Corporation
- 6.1.1 KLA Corporation Overview (Basic Corporate Information, Manufacturing Footprint, Geographic Sales Presence and Key Competitors)
- 6.1.2 KLA Corporation Introduction and Business Overview
- 6.1.3 KLA Corporation Automatic Wafer Defect Inspection System Product Portfolio
- 6.1.4 KLA Corporation Automatic Wafer Defect Inspection System Market Performance Analysis (Revenue, Sales, Price, Gross Margin and Market Share)
- 6.2 Hitachi High-Tech Corporation
- 6.2.1 Hitachi High-Tech Corporation Overview (Basic Corporate Information, Manufacturing Footprint, Geographic Sales Presence and Key Competitors)
- 6.2.2 Hitachi High-Tech Corporation Introduction and Business Overview
- 6.2.3 Hitachi High-Tech Corporation Automatic Wafer Defect Inspection System Product Portfolio
- 6.2.4 Hitachi High-Tech Corporation Automatic Wafer Defect Inspection System Market Performance Analysis (Revenue, Sales, Price, Gross Margin and Market Share)
- 6.3 SCREEN Semiconductor Solutions
- 6.3.1 SCREEN Semiconductor Solutions Overview (Basic Corporate Information, Manufacturing Footprint, Geographic Sales Presence and Key Competitors)
- 6.3.2 SCREEN Semiconductor Solutions Introduction and Business Overview
- 6.3.3 SCREEN Semiconductor Solutions Automatic Wafer Defect Inspection System Product Portfolio
- 6.3.4 SCREEN Semiconductor Solutions Automatic Wafer Defect Inspection System Market Performance Analysis (Revenue, Sales, Price, Gross Margin and Market Share)
- 6.4 Toray Engineering
- 6.4.1 Toray Engineering Overview (Basic Corporate Information, Manufacturing Footprint, Geographic Sales Presence and Key Competitors)
- 6.4.2 Toray Engineering Introduction and Business Overview
- 6.4.3 Toray Engineering Automatic Wafer Defect Inspection System Product Portfolio
- 6.4.4 Toray Engineering Automatic Wafer Defect Inspection System Market Performance Analysis (Revenue, Sales, Price, Gross Margin and Market Share)
- 6.5 Applied Materials
- 6.5.1 Applied Materials Overview (Basic Corporate Information, Manufacturing Footprint, Geographic Sales Presence and Key Competitors)
- 6.5.2 Applied Materials Introduction and Business Overview
- 6.5.3 Applied Materials Automatic Wafer Defect Inspection System Product Portfolio
- 6.5.4 Applied Materials Automatic Wafer Defect Inspection System Market Performance Analysis (Revenue, Sales, Price, Gross Margin and Market Share)
- 6.6 CE-Mat
- 6.6.1 CE-Mat Overview (Basic Corporate Information, Manufacturing Footprint, Geographic Sales Presence and Key Competitors)
- 6.6.2 CE-Mat Introduction and Business Overview
- 6.6.3 CE-Mat Automatic Wafer Defect Inspection System Product Portfolio
- 6.6.4 CE-Mat Automatic Wafer Defect Inspection System Market Performance Analysis (Revenue, Sales, Price, Gross Margin and Market Share)
- 6.7 NEXTIN
- 6.7.1 NEXTIN Overview (Basic Corporate Information, Manufacturing Footprint, Geographic Sales Presence and Key Competitors)
- 6.7.2 NEXTIN Introduction and Business Overview
- 6.7.3 NEXTIN Automatic Wafer Defect Inspection System Product Portfolio
- 6.7.4 NEXTIN Automatic Wafer Defect Inspection System Market Performance Analysis (Revenue, Sales, Price, Gross Margin and Market Share)
- 6.8 Micro Engineering
- 6.8.1 Micro Engineering Overview (Basic Corporate Information, Manufacturing Footprint, Geographic Sales Presence and Key Competitors)
- 6.8.2 Micro Engineering Introduction and Business Overview
- 6.8.3 Micro Engineering Automatic Wafer Defect Inspection System Product Portfolio
- 6.8.4 Micro Engineering Automatic Wafer Defect Inspection System Market Performance Analysis (Revenue, Sales, Price, Gross Margin and Market Share)
- 6.9 Sonix
- 6.9.1 Sonix Overview (Basic Corporate Information, Manufacturing Footprint, Geographic Sales Presence and Key Competitors)
- 6.9.2 Sonix Introduction and Business Overview
- 6.9.3 Sonix Automatic Wafer Defect Inspection System Product Portfolio
- 6.9.4 Sonix Automatic Wafer Defect Inspection System Market Performance Analysis (Revenue, Sales, Price, Gross Margin and Market Share)
- 6.10 ASML Holding
- 6.10.1 ASML Holding Overview (Basic Corporate Information, Manufacturing Footprint, Geographic Sales Presence and Key Competitors)
- 6.10.2 ASML Holding Introduction and Business Overview
- 6.10.3 ASML Holding Automatic Wafer Defect Inspection System Product Portfolio
- 6.10.4 ASML Holding Automatic Wafer Defect Inspection System Market Performance Analysis (Revenue, Sales, Price, Gross Margin and Market Share)
- 6.11 MTI Instruments
- 6.11.1 MTI Instruments Overview (Basic Corporate Information, Manufacturing Footprint, Geographic Sales Presence and Key Competitors)
- 6.11.2 MTI Instruments Introduction and Business Overview
- 6.11.3 MTI Instruments Automatic Wafer Defect Inspection System Product Portfolio
- 6.11.4 MTI Instruments Automatic Wafer Defect Inspection System Market Performance Analysis (Revenue, Sales, Price, Gross Margin and Market Share)
- 6.12 KITEC Microelectronic Technologie
- 6.12.1 KITEC Microelectronic Technologie Overview (Basic Corporate Information, Manufacturing Footprint, Geographic Sales Presence and Key Competitors)
- 6.12.2 KITEC Microelectronic Technologie Introduction and Business Overview
- 6.12.3 KITEC Microelectronic Technologie Automatic Wafer Defect Inspection System Product Portfolio
- 6.12.4 KITEC Microelectronic Technologie Automatic Wafer Defect Inspection System Market Performance Analysis (Revenue, Sales, Price, Gross Margin and Market Share)
- 7 Industry Chain Analysis
- 7.1 Upstream Key Raw Materials
- 7.1.1 Raw Materials A Definition and Suppliers
- 7.1.2 Raw Materials B Definition and Suppliers
- 7.1.3 Raw Materials C Definition and Suppliers
- 7.2 Automatic Wafer Defect Inspection System Typical Downstream Customers
- 7.3 Automatic Wafer Defect Inspection System Sales Channel Analysis
- 8 Key Takeaways and Final Conclusions
- 9 Methodology and Sources
- 9.1 Research Methodology
- 9.2 Data Mining
- 9.2.1 Preliminary Data Sources
- 9.2.2 Secondary Sources
- 9.3 Industry Analysis Matrix
- 9.4 Disclaimer
Pricing
Currency Rates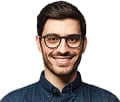
Questions or Comments?
Our team has the ability to search within reports to verify it suits your needs. We can also help maximize your budget by finding sections of reports you can purchase.