
Global 3D Printed Heat Exchanger Market Growth 2025-2031
Description
The global 3D Printed Heat Exchanger market size is predicted to grow from US$ 56.6 million in 2025 to US$ 187 million in 2031; it is expected to grow at a CAGR of 22.0% from 2025 to 2031.
3D printed heat exchanger is a heat exchange device manufactured using 3D printing technology, which is used to transfer heat from hot fluid to cold fluid to meet specified process requirements.
3D printed heat exchanger has many advantages over traditional heat exchangers. First, 3D printing technology allows the design of more complex and optimized heat exchanger structures, such as special shapes, structural integration, thin walls, thin fins, microchannels, etc., which are difficult to achieve or too expensive under traditional manufacturing methods. Through 3D printing, heat exchangers with optimal channel geometry can be manufactured to improve heat transfer efficiency. In addition, 3D printing technology can significantly reduce the need for welding, reduce manufacturing costs, and shorten production cycles. Integrated molding technology allows the parts of the heat exchanger to be molded in one go without complex assembly processes. And 3D printed heat exchangers can achieve higher heat transfer performance and lower pressure drop, thereby improving the operating efficiency and energy utilization of the equipment. By optimizing the fin structure and channel design, the performance of the heat exchanger can be further improved.
3D printed heat exchanger has a wide range of applications in many fields. In the field of aerospace, heat exchangers are widely used in systems such as engine cooling and fuel management. 3D printing technology can produce heat exchangers with complex geometries and high performance to meet the needs of these systems. In the field of automobile manufacturing, heat exchangers are used in cooling systems, air conditioning systems and other parts. 3D printing technology can produce lightweight and efficient heat exchangers to improve the fuel economy and comfort of automobiles. In electronic equipment, heat exchangers are used in heat dissipation systems to ensure the stable operation of the equipment. 3D printing technology can produce heat exchangers with tiny channels and high heat dissipation efficiency to meet the heat dissipation needs of electronic equipment.
With the continuous development of 3D printing technology, more innovative technologies will be applied to the manufacture of heat exchangers. For example, new printing technologies such as powder extrusion 3D printing technology will further improve the performance and manufacturing efficiency of heat exchangers. In the future, more high-performance materials will be used in the manufacture of 3D printed heat exchangers. Intelligent manufacturing will also become an important trend in the development of 3D printed heat exchangers. By integrating advanced sensors, control systems and data analysis technologies, intelligent manufacturing and monitoring of heat exchangers can be realized to improve their performance and reliability.
Material innovation is driving the evolution of the 3D printed heat exchanger industry, enabling the use of materials beyond traditional metals. While metal remains the dominant material due to its excellent thermal conductivity and durability, advancements in non-metallic materials such as polymers, ceramics, and graphene composites are expanding the possibilities for 3D printed heat exchangers. These materials, when paired with 3D printing’s ability to enhance surface area and optimize heat transfer, can match or even exceed the performance of conventional materials in certain applications. For example, polymer-based heat exchangers with graphene additives are emerging as lightweight and cost-effective alternatives for applications that do not demand extreme thermal resistance. The ongoing development of advanced materials not only lowers production costs but also broadens the scope of industries and applications that can benefit from 3D printed heat exchangers.
The need for lightweight and compact heat exchangers is a significant trend across multiple industries, including aerospace, automotive, and electronics. 3D printing allows manufacturers to create intricate and highly efficient designs that traditional manufacturing methods cannot achieve. In aerospace, for example, weight reduction directly correlates with improved fuel efficiency, making lightweight 3D printed heat exchangers an attractive choice. Similarly, in the automotive industry, compact designs enable better integration into electric vehicles and hybrid systems, where space is often limited. The ability to customize designs for specific thermal management needs ensures that 3D printed heat exchangers can deliver high performance without compromising size or weight constraints. This trend is further driven by the demand for miniaturized components in electronics, where efficient cooling solutions are critical for maintaining performance in increasingly smaller devices.
A notable trend in the 3D printed heat exchanger industry is the rising adoption of these technologies in aerospace and defense applications. These industries demand lightweight, high-performance thermal management solutions that can withstand extreme environmental conditions and operate under strict performance standards. 3D printed heat exchangers are uniquely suited for these applications due to their ability to achieve complex geometries, enhancing heat transfer efficiency while reducing overall weight. In aerospace, these heat exchangers contribute to improved fuel efficiency and reduced emissions, addressing the industry's growing focus on sustainability. Additionally, the customization capabilities of 3D printing allow for designs tailored to specific aircraft systems, such as avionics cooling or engine thermal management. In defense, the durability and adaptability of 3D printed heat exchangers make them ideal for rugged environments and mission-critical systems, such as military vehicles and defense electronics. As the aerospace and defense sectors continue to prioritize advanced technologies, the demand for 3D printed heat exchangers is expected to grow significantly.
LP Information, Inc. (LPI) ' newest research report, the “3D Printed Heat Exchanger Industry Forecast” looks at past sales and reviews total world 3D Printed Heat Exchanger sales in 2024, providing a comprehensive analysis by region and market sector of projected 3D Printed Heat Exchanger sales for 2025 through 2031. With 3D Printed Heat Exchanger sales broken down by region, market sector and sub-sector, this report provides a detailed analysis in US$ millions of the world 3D Printed Heat Exchanger industry.
This Insight Report provides a comprehensive analysis of the global 3D Printed Heat Exchanger landscape and highlights key trends related to product segmentation, company formation, revenue, and market share, latest development, and M&A activity. This report also analyzes the strategies of leading global companies with a focus on 3D Printed Heat Exchanger portfolios and capabilities, market entry strategies, market positions, and geographic footprints, to better understand these firms’ unique position in an accelerating global 3D Printed Heat Exchanger market.
This Insight Report evaluates the key market trends, drivers, and affecting factors shaping the global outlook for 3D Printed Heat Exchanger and breaks down the forecast by Type, by Application, geography, and market size to highlight emerging pockets of opportunity. With a transparent methodology based on hundreds of bottom-up qualitative and quantitative market inputs, this study forecast offers a highly nuanced view of the current state and future trajectory in the global 3D Printed Heat Exchanger.
This report presents a comprehensive overview, market shares, and growth opportunities of 3D Printed Heat Exchanger market by product type, application, key manufacturers and key regions and countries.
Segmentation by Type:
Plate Heat Exchanger
Tube Heat Exchanger
Segmentation by Application:
Aerospace and Defense
Automotive
Energy
Others
This report also splits the market by region:
Americas
United States
Canada
Mexico
Brazil
APAC
China
Japan
Korea
Southeast Asia
India
Australia
Europe
Germany
France
UK
Italy
Russia
Middle East & Africa
Egypt
South Africa
Israel
Turkey
GCC Countries
The below companies that are profiled have been selected based on inputs gathered from primary experts and analysing the company's coverage, product portfolio, its market penetration.
Sintavia
Conflux Technology
Unison Industries (GE)
Prima Additive
Mott Corporation (IDEX)
Exergetica
PrintSky (AddUp)
Infinity Turbine LLC
Renishaw
Key Questions Addressed in this Report
What is the 10-year outlook for the global 3D Printed Heat Exchanger market?
What factors are driving 3D Printed Heat Exchanger market growth, globally and by region?
Which technologies are poised for the fastest growth by market and region?
How do 3D Printed Heat Exchanger market opportunities vary by end market size?
How does 3D Printed Heat Exchanger break out by Type, by Application?
Please note: The report will take approximately 2 business days to prepare and deliver.
3D printed heat exchanger is a heat exchange device manufactured using 3D printing technology, which is used to transfer heat from hot fluid to cold fluid to meet specified process requirements.
3D printed heat exchanger has many advantages over traditional heat exchangers. First, 3D printing technology allows the design of more complex and optimized heat exchanger structures, such as special shapes, structural integration, thin walls, thin fins, microchannels, etc., which are difficult to achieve or too expensive under traditional manufacturing methods. Through 3D printing, heat exchangers with optimal channel geometry can be manufactured to improve heat transfer efficiency. In addition, 3D printing technology can significantly reduce the need for welding, reduce manufacturing costs, and shorten production cycles. Integrated molding technology allows the parts of the heat exchanger to be molded in one go without complex assembly processes. And 3D printed heat exchangers can achieve higher heat transfer performance and lower pressure drop, thereby improving the operating efficiency and energy utilization of the equipment. By optimizing the fin structure and channel design, the performance of the heat exchanger can be further improved.
3D printed heat exchanger has a wide range of applications in many fields. In the field of aerospace, heat exchangers are widely used in systems such as engine cooling and fuel management. 3D printing technology can produce heat exchangers with complex geometries and high performance to meet the needs of these systems. In the field of automobile manufacturing, heat exchangers are used in cooling systems, air conditioning systems and other parts. 3D printing technology can produce lightweight and efficient heat exchangers to improve the fuel economy and comfort of automobiles. In electronic equipment, heat exchangers are used in heat dissipation systems to ensure the stable operation of the equipment. 3D printing technology can produce heat exchangers with tiny channels and high heat dissipation efficiency to meet the heat dissipation needs of electronic equipment.
With the continuous development of 3D printing technology, more innovative technologies will be applied to the manufacture of heat exchangers. For example, new printing technologies such as powder extrusion 3D printing technology will further improve the performance and manufacturing efficiency of heat exchangers. In the future, more high-performance materials will be used in the manufacture of 3D printed heat exchangers. Intelligent manufacturing will also become an important trend in the development of 3D printed heat exchangers. By integrating advanced sensors, control systems and data analysis technologies, intelligent manufacturing and monitoring of heat exchangers can be realized to improve their performance and reliability.
Material innovation is driving the evolution of the 3D printed heat exchanger industry, enabling the use of materials beyond traditional metals. While metal remains the dominant material due to its excellent thermal conductivity and durability, advancements in non-metallic materials such as polymers, ceramics, and graphene composites are expanding the possibilities for 3D printed heat exchangers. These materials, when paired with 3D printing’s ability to enhance surface area and optimize heat transfer, can match or even exceed the performance of conventional materials in certain applications. For example, polymer-based heat exchangers with graphene additives are emerging as lightweight and cost-effective alternatives for applications that do not demand extreme thermal resistance. The ongoing development of advanced materials not only lowers production costs but also broadens the scope of industries and applications that can benefit from 3D printed heat exchangers.
The need for lightweight and compact heat exchangers is a significant trend across multiple industries, including aerospace, automotive, and electronics. 3D printing allows manufacturers to create intricate and highly efficient designs that traditional manufacturing methods cannot achieve. In aerospace, for example, weight reduction directly correlates with improved fuel efficiency, making lightweight 3D printed heat exchangers an attractive choice. Similarly, in the automotive industry, compact designs enable better integration into electric vehicles and hybrid systems, where space is often limited. The ability to customize designs for specific thermal management needs ensures that 3D printed heat exchangers can deliver high performance without compromising size or weight constraints. This trend is further driven by the demand for miniaturized components in electronics, where efficient cooling solutions are critical for maintaining performance in increasingly smaller devices.
A notable trend in the 3D printed heat exchanger industry is the rising adoption of these technologies in aerospace and defense applications. These industries demand lightweight, high-performance thermal management solutions that can withstand extreme environmental conditions and operate under strict performance standards. 3D printed heat exchangers are uniquely suited for these applications due to their ability to achieve complex geometries, enhancing heat transfer efficiency while reducing overall weight. In aerospace, these heat exchangers contribute to improved fuel efficiency and reduced emissions, addressing the industry's growing focus on sustainability. Additionally, the customization capabilities of 3D printing allow for designs tailored to specific aircraft systems, such as avionics cooling or engine thermal management. In defense, the durability and adaptability of 3D printed heat exchangers make them ideal for rugged environments and mission-critical systems, such as military vehicles and defense electronics. As the aerospace and defense sectors continue to prioritize advanced technologies, the demand for 3D printed heat exchangers is expected to grow significantly.
LP Information, Inc. (LPI) ' newest research report, the “3D Printed Heat Exchanger Industry Forecast” looks at past sales and reviews total world 3D Printed Heat Exchanger sales in 2024, providing a comprehensive analysis by region and market sector of projected 3D Printed Heat Exchanger sales for 2025 through 2031. With 3D Printed Heat Exchanger sales broken down by region, market sector and sub-sector, this report provides a detailed analysis in US$ millions of the world 3D Printed Heat Exchanger industry.
This Insight Report provides a comprehensive analysis of the global 3D Printed Heat Exchanger landscape and highlights key trends related to product segmentation, company formation, revenue, and market share, latest development, and M&A activity. This report also analyzes the strategies of leading global companies with a focus on 3D Printed Heat Exchanger portfolios and capabilities, market entry strategies, market positions, and geographic footprints, to better understand these firms’ unique position in an accelerating global 3D Printed Heat Exchanger market.
This Insight Report evaluates the key market trends, drivers, and affecting factors shaping the global outlook for 3D Printed Heat Exchanger and breaks down the forecast by Type, by Application, geography, and market size to highlight emerging pockets of opportunity. With a transparent methodology based on hundreds of bottom-up qualitative and quantitative market inputs, this study forecast offers a highly nuanced view of the current state and future trajectory in the global 3D Printed Heat Exchanger.
This report presents a comprehensive overview, market shares, and growth opportunities of 3D Printed Heat Exchanger market by product type, application, key manufacturers and key regions and countries.
Segmentation by Type:
Plate Heat Exchanger
Tube Heat Exchanger
Segmentation by Application:
Aerospace and Defense
Automotive
Energy
Others
This report also splits the market by region:
Americas
United States
Canada
Mexico
Brazil
APAC
China
Japan
Korea
Southeast Asia
India
Australia
Europe
Germany
France
UK
Italy
Russia
Middle East & Africa
Egypt
South Africa
Israel
Turkey
GCC Countries
The below companies that are profiled have been selected based on inputs gathered from primary experts and analysing the company's coverage, product portfolio, its market penetration.
Sintavia
Conflux Technology
Unison Industries (GE)
Prima Additive
Mott Corporation (IDEX)
Exergetica
PrintSky (AddUp)
Infinity Turbine LLC
Renishaw
Key Questions Addressed in this Report
What is the 10-year outlook for the global 3D Printed Heat Exchanger market?
What factors are driving 3D Printed Heat Exchanger market growth, globally and by region?
Which technologies are poised for the fastest growth by market and region?
How do 3D Printed Heat Exchanger market opportunities vary by end market size?
How does 3D Printed Heat Exchanger break out by Type, by Application?
Please note: The report will take approximately 2 business days to prepare and deliver.
Table of Contents
87 Pages
- *This is a tentative TOC and the final deliverable is subject to change.*
- 2 Executive Summary
- 3 Global by Company
- 4 World Historic Review for 3D Printed Heat Exchanger by Geographic Region
- 5 Americas
- 6 APAC
- 7 Europe
- 8 Middle East & Africa
- 9 Market Drivers, Challenges and Trends
- 10 Manufacturing Cost Structure Analysis
- 11 Marketing, Distributors and Customer
- 12 World Forecast Review for 3D Printed Heat Exchanger by Geographic Region
- 13 Key Players Analysis
- 14 Research Findings and Conclusion
Pricing
Currency Rates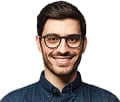
Questions or Comments?
Our team has the ability to search within reports to verify it suits your needs. We can also help maximize your budget by finding sections of reports you can purchase.