
USA Pre-Engineered Metal Building Market Outlook to 2028
Description
USA Pre- Engineered Metal Building Market Overview
The USA Pre- Engineered Metal Building Market has reached a valuation of USD 12.2 billion, driven by significant growth in sectors such as warehousing, logistics, and retail. The market's expansion is fueled by the increasing demand for durable, scalable, and cost-effective structures across industrial applications. These metal buildings cater to the need for high-efficiency construction solutions in an era of rapid urbanization. Moreover, advancements in design flexibility and energy-efficient features make these buildings appealing to companies seeking sustainable and adaptable infrastructure.
Key regions like Texas, California, and Illinois are instrumental in the market's growth due to their extensive industrial infrastructure, business-friendly policies, and continuous urban development projects. These states host major logistics hubs and manufacturing plants, contributing to higher demand for pre-engineered metal buildings. In particular, Texas and California benefit from favorable regulations, large-scale construction projects, and the increasing presence of e-commerce warehousing facilities.
Adherence to the International Building Code (IBC) and state-specific codes is mandatory for PEMBs, affecting design and construction processes. Compliance with these regulations is strictly monitored, adding an average 15% increase in project timelines for PEMBs, according to the U.S. Department of Housing and Urban Development, especially in earthquake-prone regions requiring seismic-resistant designs.
USA Pre- Engineered Metal Building Market Segmentation
By Building Type: The market is segmented by building type into Commercial, Industrial, Agricultural, and Institutional buildings. Industrial buildings hold the largest market share due to the high demand in manufacturing and warehousing sectors. The flexibility and efficiency of pre-engineered structures make them suitable for industrial use, where rapid construction and cost savings are prioritized. Industrial players in logistics and manufacturing often select these buildings for their scalability and capacity to withstand diverse environmental conditions.
By Component: The Market is also segmented by component, comprising Primary Frame, Secondary Structural Frame, Wall Panels, and Roof Panels. Primary frames dominate this segmentation, as they provide critical structural integrity to pre-engineered buildings. The demand for high-quality, durable primary frames is significant in industrial applications, where safety and longevity are key concerns. High-grade materials used in primary frames enhance building stability, making them the preferred choice for commercial and industrial setups.
USA Pre- Engineered Metal Building Market Competitive Landscape
The USA Pre- Engineered Metal Building Market is highly competitive, with established companies such as Blue Scope Buildings, Nucor Corporation, and Butler Manufacturing at the forefront. These companies maintain a strong position through technological innovation, sustainability initiatives, and extensive manufacturing capabilities. Their focus on developing cost-effective and energy-efficient buildings aligns with market demands, ensuring they remain influential in the industry.
USA Pre- Engineered Metal Building Market Analysis
Growth Drivers
Increasing Demand for Industrial Buildings: The expansion of U.S. industrial sectors, particularly in the automotive and electronics industries, is driving demand for pre-engineered metal buildings (PEMBs). With the U.S. manufacturing sector's output totaling USD 2.35 trillion in 2023, industrial companies are investing in cost-efficient building solutions that offer faster construction and adaptability. PEMBs have emerged as a solution for their speed and cost-effectiveness. According to the U.S. Bureau of Economic Analysis, the U.S. industrial production index rose to 102.1, emphasizing the sector's growth and demand for PEMBs to support expansion needs.
Rising Adoption in Retail and Commercial Sectors: Retail and commercial sectors are increasingly adopting PEMBs due to their scalability and energy efficiency. In 2023, the U.S. retail sector invested heavily in new commercial spaces, with amounts worth billions allocated for new constructions, including PEMBs, as they enable efficient structural expansion with energy savings of up to 30% compared to traditional buildings. The Bureau of Labor Statistics noted increased employment in retail trades by a million jobs, reflecting economic activity in commercial spaces driving PEMB adoption.
Energy- Efficient Building Demand: The U.S. governments focus on sustainable construction is propelling demand for energy-efficient PEMBs, which contribute significantly to meeting energy efficiency standards. According to the U.S. Energy Information Administration, buildings constructed under the Energy Star program consumed substantially less energy in 2023 than non-certified buildings, making PEMBs a favored choice for new constructions. This demand aligns with national energy goals, as the U.S. aims to reduce building energy consumption across sectors, targeting efficiency improvements notably.
Challenges
Fluctuating Raw Material Prices: The USA Pre- Engineered Metal Building Market encounters significant challenges due to rising and unpredictable prices of essential raw materials like steel. In recent years, steel costs have seen notable volatility, with global supply chain issues and increased demand further intensifying the price spikes. This fluctuation impacts the overall cost structure for manufacturers, who are forced to adjust their pricing strategies to mitigate rising expenses. As these raw material costs continue to rise, maintaining profitability while offering competitive pricing becomes an increasingly complex concern for manufacturers, directly affecting the final product price for consumers.
Complex Compliance and Zoning Regulations: Pre-engineered metal building manufacturers face ongoing challenges in navigating diverse compliance and zoning regulations that differ substantially across states. These regulations can mandate specific safety standards, zoning approvals, and design adjustments that add both time and expense to projects. For instance, states with seismic codes may require structural reinforcements, impacting the choice of materials and design. Ensuring compliance with these varying regulations while maintaining production efficiency often requires companies to invest in specialized materials or adapt their designs, leading to increased production costs and potential delays in project timelines.
USA Pre- Engineered Metal Building Market Future Outlook
The USA Pre- Engineered Metal Building Market is expected to experience steady growth through 2028, with a focus on innovation in design, sustainable construction methods, and technological advancements. As companies prioritize energy efficiency, manufacturers are likely to incorporate more eco-friendly materials and designs, positioning these structures as an attractive option in the commercial and industrial sectors. Additionally, the expansion of logistics and warehousing facilities will continue to drive demand for pre-engineered metal buildings.
Future Market Opportunities
Technological Integration in Building Design: The use of advanced digital tools, such as Building Information Modeling (BIM), is creating substantial opportunities in the pre-engineered metal building (PEMB) market. BIM technology enhances project visualization, coordination, and accuracy, reducing errors and project timelines. According to the National Institute of Standards and Technology, BIM has been shown to boost productivity remarkably in construction projects by minimizing design clashes and streamlining workflows. The majority of U.S. construction firms now utilize BIM, which supports the increasing adoption of PEMBs due to its ability to optimize design precision, ultimately lowering construction time and costs while meeting complex architectural requirements.
Growth in Urban Infrastructure Projects: Expanding urban infrastructure across U.S. metropolitan areas is driving demand for PEMBs, particularly as cities scale industrial and commercial spaces to meet growing needs. The U.S. federal infrastructure agenda has earmarked USD 1.2 trillion through 2025, primarily targeting the development of transportation and logistics hubs. PEMBs, known for their durability and efficient assembly, are ideally suited for these high-demand projects, allowing for faster setup compared to conventional buildings. As urban centers prioritize rapid construction to meet population growth and commerce needs, PEMBs are positioned to play a critical role in supporting the expansion of urban infrastructure
Please Note: It will take 5-7 business days to complete the report upon order confirmation
The USA Pre- Engineered Metal Building Market has reached a valuation of USD 12.2 billion, driven by significant growth in sectors such as warehousing, logistics, and retail. The market's expansion is fueled by the increasing demand for durable, scalable, and cost-effective structures across industrial applications. These metal buildings cater to the need for high-efficiency construction solutions in an era of rapid urbanization. Moreover, advancements in design flexibility and energy-efficient features make these buildings appealing to companies seeking sustainable and adaptable infrastructure.
Key regions like Texas, California, and Illinois are instrumental in the market's growth due to their extensive industrial infrastructure, business-friendly policies, and continuous urban development projects. These states host major logistics hubs and manufacturing plants, contributing to higher demand for pre-engineered metal buildings. In particular, Texas and California benefit from favorable regulations, large-scale construction projects, and the increasing presence of e-commerce warehousing facilities.
Adherence to the International Building Code (IBC) and state-specific codes is mandatory for PEMBs, affecting design and construction processes. Compliance with these regulations is strictly monitored, adding an average 15% increase in project timelines for PEMBs, according to the U.S. Department of Housing and Urban Development, especially in earthquake-prone regions requiring seismic-resistant designs.
USA Pre- Engineered Metal Building Market Segmentation
By Building Type: The market is segmented by building type into Commercial, Industrial, Agricultural, and Institutional buildings. Industrial buildings hold the largest market share due to the high demand in manufacturing and warehousing sectors. The flexibility and efficiency of pre-engineered structures make them suitable for industrial use, where rapid construction and cost savings are prioritized. Industrial players in logistics and manufacturing often select these buildings for their scalability and capacity to withstand diverse environmental conditions.
By Component: The Market is also segmented by component, comprising Primary Frame, Secondary Structural Frame, Wall Panels, and Roof Panels. Primary frames dominate this segmentation, as they provide critical structural integrity to pre-engineered buildings. The demand for high-quality, durable primary frames is significant in industrial applications, where safety and longevity are key concerns. High-grade materials used in primary frames enhance building stability, making them the preferred choice for commercial and industrial setups.
USA Pre- Engineered Metal Building Market Competitive Landscape
The USA Pre- Engineered Metal Building Market is highly competitive, with established companies such as Blue Scope Buildings, Nucor Corporation, and Butler Manufacturing at the forefront. These companies maintain a strong position through technological innovation, sustainability initiatives, and extensive manufacturing capabilities. Their focus on developing cost-effective and energy-efficient buildings aligns with market demands, ensuring they remain influential in the industry.
USA Pre- Engineered Metal Building Market Analysis
Growth Drivers
Increasing Demand for Industrial Buildings: The expansion of U.S. industrial sectors, particularly in the automotive and electronics industries, is driving demand for pre-engineered metal buildings (PEMBs). With the U.S. manufacturing sector's output totaling USD 2.35 trillion in 2023, industrial companies are investing in cost-efficient building solutions that offer faster construction and adaptability. PEMBs have emerged as a solution for their speed and cost-effectiveness. According to the U.S. Bureau of Economic Analysis, the U.S. industrial production index rose to 102.1, emphasizing the sector's growth and demand for PEMBs to support expansion needs.
Rising Adoption in Retail and Commercial Sectors: Retail and commercial sectors are increasingly adopting PEMBs due to their scalability and energy efficiency. In 2023, the U.S. retail sector invested heavily in new commercial spaces, with amounts worth billions allocated for new constructions, including PEMBs, as they enable efficient structural expansion with energy savings of up to 30% compared to traditional buildings. The Bureau of Labor Statistics noted increased employment in retail trades by a million jobs, reflecting economic activity in commercial spaces driving PEMB adoption.
Energy- Efficient Building Demand: The U.S. governments focus on sustainable construction is propelling demand for energy-efficient PEMBs, which contribute significantly to meeting energy efficiency standards. According to the U.S. Energy Information Administration, buildings constructed under the Energy Star program consumed substantially less energy in 2023 than non-certified buildings, making PEMBs a favored choice for new constructions. This demand aligns with national energy goals, as the U.S. aims to reduce building energy consumption across sectors, targeting efficiency improvements notably.
Challenges
Fluctuating Raw Material Prices: The USA Pre- Engineered Metal Building Market encounters significant challenges due to rising and unpredictable prices of essential raw materials like steel. In recent years, steel costs have seen notable volatility, with global supply chain issues and increased demand further intensifying the price spikes. This fluctuation impacts the overall cost structure for manufacturers, who are forced to adjust their pricing strategies to mitigate rising expenses. As these raw material costs continue to rise, maintaining profitability while offering competitive pricing becomes an increasingly complex concern for manufacturers, directly affecting the final product price for consumers.
Complex Compliance and Zoning Regulations: Pre-engineered metal building manufacturers face ongoing challenges in navigating diverse compliance and zoning regulations that differ substantially across states. These regulations can mandate specific safety standards, zoning approvals, and design adjustments that add both time and expense to projects. For instance, states with seismic codes may require structural reinforcements, impacting the choice of materials and design. Ensuring compliance with these varying regulations while maintaining production efficiency often requires companies to invest in specialized materials or adapt their designs, leading to increased production costs and potential delays in project timelines.
USA Pre- Engineered Metal Building Market Future Outlook
The USA Pre- Engineered Metal Building Market is expected to experience steady growth through 2028, with a focus on innovation in design, sustainable construction methods, and technological advancements. As companies prioritize energy efficiency, manufacturers are likely to incorporate more eco-friendly materials and designs, positioning these structures as an attractive option in the commercial and industrial sectors. Additionally, the expansion of logistics and warehousing facilities will continue to drive demand for pre-engineered metal buildings.
Future Market Opportunities
Technological Integration in Building Design: The use of advanced digital tools, such as Building Information Modeling (BIM), is creating substantial opportunities in the pre-engineered metal building (PEMB) market. BIM technology enhances project visualization, coordination, and accuracy, reducing errors and project timelines. According to the National Institute of Standards and Technology, BIM has been shown to boost productivity remarkably in construction projects by minimizing design clashes and streamlining workflows. The majority of U.S. construction firms now utilize BIM, which supports the increasing adoption of PEMBs due to its ability to optimize design precision, ultimately lowering construction time and costs while meeting complex architectural requirements.
Growth in Urban Infrastructure Projects: Expanding urban infrastructure across U.S. metropolitan areas is driving demand for PEMBs, particularly as cities scale industrial and commercial spaces to meet growing needs. The U.S. federal infrastructure agenda has earmarked USD 1.2 trillion through 2025, primarily targeting the development of transportation and logistics hubs. PEMBs, known for their durability and efficient assembly, are ideally suited for these high-demand projects, allowing for faster setup compared to conventional buildings. As urban centers prioritize rapid construction to meet population growth and commerce needs, PEMBs are positioned to play a critical role in supporting the expansion of urban infrastructure
Please Note: It will take 5-7 business days to complete the report upon order confirmation
Table of Contents
85 Pages
- 1. USA Pre-Engineered Metal Building Market Overview
- 1.1 Definition and Scope
- 1.2 Market Taxonomy
- 1.3 Market Growth Rate
- 1.4 Market Segmentation Overview
- 2. USA Pre-Engineered Metal Building Market Size (In USD Bn)
- 2.1 Historical Market Size
- 2.2 Year-On-Year Growth Analysis
- 2.3 Key Market Developments and Milestones
- 3. USA Pre-Engineered Metal Building Market Analysis
- 3.1 Growth Drivers
- 3.1.1 Industrial Expansion
- 3.1.2 Rising Adoption in Retail and Commercial Sectors
- 3.1.3 Energy-Efficient Building Demand
- 3.1.4 Federal Tax Incentives
- 3.2 Market Challenges
- 3.2.1 High Initial Cost of Installation
- 3.2.2 Limited Customization Capabilities
- 3.2.3 Regulatory and Compliance Standards
- 3.3 Opportunities
- 3.3.1 Technological Integration in Building Design
- 3.3.2 Growth in Urban Infrastructure Projects
- 3.3.3 Expansion of Industrial Manufacturing
- 3.4 Trends
- 3.4.1 Integration of Eco-Friendly Materials
- 3.4.2 Adoption of Modular Building Design
- 3.4.3 Increasing Use of Prefabrication
- 3.5 Government Regulations
- 3.5.1 Building Codes and Standards Compliance
- 3.5.2 Energy Efficiency Certification Requirements
- 3.5.3 Zoning and Land Use Regulations
- 3.6 SWOT Analysis
- 3.7 Stakeholder Ecosystem
- 3.8 Porters Five Forces
- 3.9 Competitive Landscape
- 4. USA Pre-Engineered Metal Building Market Segmentation
- 4.1 By Building Type (In Value %)
- 4.1.1 Commercial
- 4.1.2 Industrial
- 4.1.3 Agricultural
- 4.1.4 Institutional
- 4.2 By Component (In Value %)
- 4.2.1 Primary Frame
- 4.2.2 Secondary Structural Frames
- 4.2.3 Wall Panels
- 4.2.4 Roof Panels
- 4.3 By Application (In Value %)
- 4.3.1 Warehouses
- 4.3.2 Retail Buildings
- 4.3.3 Office Spaces
- 4.3.4 Manufacturing Facilities
- 4.4 By Structure Type (In Value %)
- 4.4.1 Rigid Frame
- 4.4.2 Arch Building
- 4.4.3 Single-Slope Frame
- 4.4.4 Multi-Gable
- 4.5 By Region (In Value %)
- 4.5.1 Northeast
- 4.5.2 Midwest
- 4.5.3 South
- 4.5.4 West
- 5. USA Pre-Engineered Metal Building Market Competitive Analysis
- 5.1 Detailed Profiles of Major Companies
- 5.1.1 BlueScope Buildings
- 5.1.2 Nucor Corporation
- 5.1.3 Cornerstone Building Brands
- 5.1.4 Butler Manufacturing
- 5.1.5 Varco Pruden Buildings
- 5.1.6 Kirby Building Systems
- 5.1.7 Allied Steel Buildings
- 5.1.8 Star Building Systems
- 5.1.9 Armstrong Steel
- 5.1.10 American Buildings Company
- 5.1.11 Whirlwind Steel Buildings
- 5.1.12 Mueller Inc.
- 5.1.13 Olympia Steel Buildings
- 5.1.14 SteelBuilt
- 5.1.15 Ironbuilt Steel Buildings
- 5.2 Cross Comparison Parameters (Product Offerings, Revenue, Number of Employees, Headquarters, Distribution Network, Major Clients, Manufacturing Capacity, Sustainability Practices)
- 5.3 Market Share Analysis
- 5.4 Strategic Initiatives
- 5.5 Mergers And Acquisitions
- 5.6 Investment Analysis
- 5.7 Venture Capital Funding
- 5.8 Government Incentives
- 5.9 Private Equity Investments
- 6. USA Pre-Engineered Metal Building Market Regulatory Framework
- 6.1 Structural Safety Standards
- 6.2 Environmental Compliance Requirements
- 6.3 Certification and Approval Procedures
- 7. USA Pre-Engineered Metal Building Future Market Size (In USD Bn)
- 7.1 Projected Market Size
- 7.2 Key Drivers Influencing Future Growth
- 8. USA Pre-Engineered Metal Building Future Market Segmentation
- 8.1 By Building Type
- 8.2 By Component
- 8.3 By Application
- 8.4 By Structure Type
- 8.5 By Region
- 9. USA Pre-Engineered Metal Building Market Analysts Recommendations
- 9.1 TAM/SAM/SOM Analysis
- 9.2 Industry Benchmarking
- 9.3 Customer Cohort Analysis
- 9.4 White Space Opportunity Analysis
- Disclaimer
- Contact Us
Pricing
Currency Rates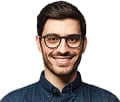
Questions or Comments?
Our team has the ability to search within reports to verify it suits your needs. We can also help maximize your budget by finding sections of reports you can purchase.