
USA Metal Forging Market Outlook to 2028
Description
USA Metal Forging Market Overview
The USA Metal Forging market is valued at USD 8.2 billion, fueled by strong demand from the automotive and aerospace industries. The market growth is supported by continuous advancements in forging technologies, enabling manufacturers to enhance precision and durability in forged components, essential in high-performance applications. Increasing investments in industrial equipment and demand for forged parts with enhanced properties further drive the market's expansion.
The primary hubs dominating the USA Metal Forging market include Michigan, Texas, and California. These regions have a strong presence of automotive and aerospace industries, both of which are the largest consumers of forged metal parts. Additionally, robust infrastructure and access to skilled labor make these areas attractive for manufacturing units focused on precision forging, contributing to their leading positions in the market.
The U.S. Environmental Protection Agency (EPA) enforces strict emission regulations in the forging industry, targeting air pollutants such as volatile organic compounds (VOCs) from forging furnaces. These standards affect operational practices, with approximately 60% of U.S. forging plants investing in emissions control systems. Compliance supports cleaner production practices but entails considerable cost implications for the industry.
USA Metal Forging Market Segmentation
By Process Type: The USA Metal Forging market is segmented by process type into open die forging, closed die forging, ring rolling, and extrusion forging. Closed die forging holds the dominant share in this segment due to its suitability for high-precision components required by the automotive and aerospace sectors. This process provides enhanced strength and uniformity in complex shapes, making it highly desirable for manufacturing gears, shafts, and other structural parts that require precision.
By Material Type: The market is segmented by material type into carbon steel, alloy steel, aluminium, stainless steel, and titanium. Carbon steel leads this segment as it provides high strength at a lower cost, making it ideal for automotive and industrial applications. Its versatility and ease of forging also contribute to its prominence, allowing for various applications across multiple industries.
USA Metal Forging Market Competitive Landscape
The USA Metal Forging market is dominated by key players leveraging advanced technology and manufacturing practices to maintain competitive advantages. This consolidation highlights the significant influence of these companies in shaping the market's landscape.
USA Metal Forging Industry Analysis
Growth Drivers
Automotive Manufacturing Demand: In 2024, the U.S. automotive industry saw a significant uptick in production, particularly in EV manufacturing, where demand for precision-forged components has become crucial. The U.S. produced 10.5 million light vehicles annually, representing a growing reliance on forged parts for durability and strength in automotive assembly. Macroeconomic indicators like the Fed's Consumer Price Index reflect a stable inflation rate for vehicle parts, making it feasible for auto manufacturers to continue investing in high-quality forged parts. Demand for forged components like transmission gears and crankshafts remains strong, driving metal forging advancements.
Aerospace and Defense Requirements: The U.S. Department of Defense's annual spending on aerospace and defense has reached $782 billion in 2024, increasing demand for durable, precision-forged metal parts in aerospace engines, structural components, and defense vehicles. Given the U.S.'s position as a leader in aircraft production, new contracts awarded to Boeing and Lockheed Martin underline the urgency for high-strength metal forged parts, essential for the durability and performance standards required in aerospace. This bolsters the need for advanced forging methods, especially in high-value metals like titanium and aluminum.
Technological Advancements in Forge Processes: Investment in forging technologies within the U.S. metal forging market saw an increase of approximately $250 million in 2023, with a focus on enhancing efficiency and precision. Improved heat treatment and automation processes, powered by machine learning, have enabled U.S. manufacturers to meet diverse forging requirements, from high-performance alloys to complex component shapes. These advancements align with the U.S. governments push towards digital transformation, as reflected in industrial policy initiatives, thus supporting increased production capabilities.
Market Restraints
Raw Material Price Volatility: Steel and aluminum prices experienced a substantial rise in 2023, with steel averaging $1,250 per ton. This volatility places pressure on the forging sector, where raw materials account for over 40% of production costs. Coupled with U.S. trade policy uncertainties and import tariffs on certain materials, the fluctuations complicate budgeting for forging companies, leading to increased operational challenges.
Skilled Labor Shortages: In 2024, the manufacturing industry faces a 10% gap in skilled labor demand, impacting the metal forging market significantly. Metal forging companies report difficulty in filling positions for highly specialized roles like forging technicians, with average wages rising to $30 per hour in response to labor shortages. The governments workforce development programs aim to address this, but the shortfall remains a bottleneck for many companies attempting to scale up production.
USA Metal Forging Market Future Outlook
Over the next five years, the USA Metal Forging market is projected to experience substantial growth, driven by technological advancements, a rise in high-precision applications, and increasing investments in infrastructure. Enhanced production capacities to meet the demand from the automotive and aerospace industries will play a key role in this growth trajectory.
Market Opportunities
Innovations in Closed-Die Forging: Closed-die forging in the U.S. has seen significant growth, driven by its application in producing high-strength parts with complex shapes. Demand has increased by 15% across the automotive and aerospace industries due to improved dimensional accuracy and material strength. As of 2024, technological advancements enable shorter lead times and lower waste, making it a lucrative area for manufacturers to explore.
Demand for Precision Forged Components: Precision forging processes have gained traction, especially within medical and defense manufacturing, due to their ability to produce high-strength, custom parts with minimal waste. The U.S. defense sectors increasing focus on advanced weaponry and machinery has led to a 12% rise in demand for precision-forged metal parts. With support from the U.S. government for advanced manufacturing projects, companies that specialize in precision forging are well-positioned for growth.
Please Note: It will take 5-7 business days to complete the report upon order confirmation
The USA Metal Forging market is valued at USD 8.2 billion, fueled by strong demand from the automotive and aerospace industries. The market growth is supported by continuous advancements in forging technologies, enabling manufacturers to enhance precision and durability in forged components, essential in high-performance applications. Increasing investments in industrial equipment and demand for forged parts with enhanced properties further drive the market's expansion.
The primary hubs dominating the USA Metal Forging market include Michigan, Texas, and California. These regions have a strong presence of automotive and aerospace industries, both of which are the largest consumers of forged metal parts. Additionally, robust infrastructure and access to skilled labor make these areas attractive for manufacturing units focused on precision forging, contributing to their leading positions in the market.
The U.S. Environmental Protection Agency (EPA) enforces strict emission regulations in the forging industry, targeting air pollutants such as volatile organic compounds (VOCs) from forging furnaces. These standards affect operational practices, with approximately 60% of U.S. forging plants investing in emissions control systems. Compliance supports cleaner production practices but entails considerable cost implications for the industry.
USA Metal Forging Market Segmentation
By Process Type: The USA Metal Forging market is segmented by process type into open die forging, closed die forging, ring rolling, and extrusion forging. Closed die forging holds the dominant share in this segment due to its suitability for high-precision components required by the automotive and aerospace sectors. This process provides enhanced strength and uniformity in complex shapes, making it highly desirable for manufacturing gears, shafts, and other structural parts that require precision.
By Material Type: The market is segmented by material type into carbon steel, alloy steel, aluminium, stainless steel, and titanium. Carbon steel leads this segment as it provides high strength at a lower cost, making it ideal for automotive and industrial applications. Its versatility and ease of forging also contribute to its prominence, allowing for various applications across multiple industries.
USA Metal Forging Market Competitive Landscape
The USA Metal Forging market is dominated by key players leveraging advanced technology and manufacturing practices to maintain competitive advantages. This consolidation highlights the significant influence of these companies in shaping the market's landscape.
USA Metal Forging Industry Analysis
Growth Drivers
Automotive Manufacturing Demand: In 2024, the U.S. automotive industry saw a significant uptick in production, particularly in EV manufacturing, where demand for precision-forged components has become crucial. The U.S. produced 10.5 million light vehicles annually, representing a growing reliance on forged parts for durability and strength in automotive assembly. Macroeconomic indicators like the Fed's Consumer Price Index reflect a stable inflation rate for vehicle parts, making it feasible for auto manufacturers to continue investing in high-quality forged parts. Demand for forged components like transmission gears and crankshafts remains strong, driving metal forging advancements.
Aerospace and Defense Requirements: The U.S. Department of Defense's annual spending on aerospace and defense has reached $782 billion in 2024, increasing demand for durable, precision-forged metal parts in aerospace engines, structural components, and defense vehicles. Given the U.S.'s position as a leader in aircraft production, new contracts awarded to Boeing and Lockheed Martin underline the urgency for high-strength metal forged parts, essential for the durability and performance standards required in aerospace. This bolsters the need for advanced forging methods, especially in high-value metals like titanium and aluminum.
Technological Advancements in Forge Processes: Investment in forging technologies within the U.S. metal forging market saw an increase of approximately $250 million in 2023, with a focus on enhancing efficiency and precision. Improved heat treatment and automation processes, powered by machine learning, have enabled U.S. manufacturers to meet diverse forging requirements, from high-performance alloys to complex component shapes. These advancements align with the U.S. governments push towards digital transformation, as reflected in industrial policy initiatives, thus supporting increased production capabilities.
Market Restraints
Raw Material Price Volatility: Steel and aluminum prices experienced a substantial rise in 2023, with steel averaging $1,250 per ton. This volatility places pressure on the forging sector, where raw materials account for over 40% of production costs. Coupled with U.S. trade policy uncertainties and import tariffs on certain materials, the fluctuations complicate budgeting for forging companies, leading to increased operational challenges.
Skilled Labor Shortages: In 2024, the manufacturing industry faces a 10% gap in skilled labor demand, impacting the metal forging market significantly. Metal forging companies report difficulty in filling positions for highly specialized roles like forging technicians, with average wages rising to $30 per hour in response to labor shortages. The governments workforce development programs aim to address this, but the shortfall remains a bottleneck for many companies attempting to scale up production.
USA Metal Forging Market Future Outlook
Over the next five years, the USA Metal Forging market is projected to experience substantial growth, driven by technological advancements, a rise in high-precision applications, and increasing investments in infrastructure. Enhanced production capacities to meet the demand from the automotive and aerospace industries will play a key role in this growth trajectory.
Market Opportunities
Innovations in Closed-Die Forging: Closed-die forging in the U.S. has seen significant growth, driven by its application in producing high-strength parts with complex shapes. Demand has increased by 15% across the automotive and aerospace industries due to improved dimensional accuracy and material strength. As of 2024, technological advancements enable shorter lead times and lower waste, making it a lucrative area for manufacturers to explore.
Demand for Precision Forged Components: Precision forging processes have gained traction, especially within medical and defense manufacturing, due to their ability to produce high-strength, custom parts with minimal waste. The U.S. defense sectors increasing focus on advanced weaponry and machinery has led to a 12% rise in demand for precision-forged metal parts. With support from the U.S. government for advanced manufacturing projects, companies that specialize in precision forging are well-positioned for growth.
Please Note: It will take 5-7 business days to complete the report upon order confirmation
Table of Contents
99 Pages
- 1. USA Metal Forging Market Overview
- 1.1 Definition and Scope
- 1.2 Market Taxonomy
- 1.3 Key Market Milestones
- 1.4 Industry Growth Rate Analysis
- 1.5 Market Segmentation Overview
- 2. USA Metal Forging Market Size (In USD Million)
- 2.1 Historical Market Size
- 2.2 Year-on-Year Market Growth Analysis
- 2.3 Milestones in Market Development and Key Investments
- 2.4 Economic Influence on Metal Forging Demand
- 3. USA Metal Forging Market Dynamics
- 3.1 Market Growth Drivers
- 3.1.1 Automotive Manufacturing Demand
- 3.1.2 Aerospace and Defense Requirements
- 3.1.3 Technological Advancements in Forge Processes
- 3.1.4 Demand for Lightweight Forged Components
- 3.2 Market Challenges
- 3.2.1 Raw Material Price Volatility
- 3.2.2 Skilled Labor Shortages
- 3.2.3 High Capital Costs for Advanced Forging Equipment
- 3.3 Opportunities in the Market
- 3.3.1 Innovations in Closed-Die Forging
- 3.3.2 Demand for Precision Forged Components
- 3.3.3 Advancements in Simulation Technologies
- 3.4 Emerging Trends in Metal Forging
- 3.4.1 Adoption of 3D Printing in Forging
- 3.4.2 Integration of Smart Manufacturing (IIoT)
- 3.4.3 Utilization of Sustainable Energy in Forge Operations
- 3.5 Regulatory Framework
- 3.5.1 OSHA Compliance Standards for Forging
- 3.5.2 Import Tariffs on Raw Materials
- 3.5.3 Environmental Protection Regulations
- 3.6 Industry Ecosystem and Supply Chain
- 3.6.1 Raw Material Suppliers
- 3.6.2 Equipment Manufacturers
- 3.6.3 Distribution Channels and End-Users
- 3.7 Porters Five Forces Analysis
- 3.8 SWOT Analysis
- 4. USA Metal Forging Market Segmentation
- 4.1 By Process Type (In Value %)
- 4.1.1 Open Die Forging
- 4.1.2 Closed Die Forging
- 4.1.3 Ring Rolling
- 4.1.4 Extrusion Forging
- 4.2 By Material Type (In Value %)
- 4.2.1 Carbon Steel
- 4.2.2 Alloy Steel
- 4.2.3 Aluminum
- 4.2.4 Stainless Steel
- 4.2.5 Titanium
- 4.3 By End-Use Industry (In Value %)
- 4.3.1 Automotive
- 4.3.2 Aerospace & Defense
- 4.3.3 Industrial Equipment
- 4.3.4 Oil & Gas
- 4.3.5 Power Generation
- 4.4 By Region (In Value %)
- 4.4.1 Northeast
- 4.4.2 Midwest
- 4.4.3 South
- 4.4.4 West
- 4.5 By Application (In Value %)
- 4.5.1 Shafts
- 4.5.2 Gears
- 4.5.3 Bearings
- 4.5.4 Valves and Flanges
- 4.5.5 Other Components
- 5. USA Metal Forging Market Competitive Landscape
- 5.1 Detailed Profiles of Major Players
- 5.1.1 Precision Castparts Corp.
- 5.1.2 Alcoa Corporation
- 5.1.3 American Axle & Manufacturing, Inc.
- 5.1.4 ATI Metals
- 5.1.5 Bharat Forge Ltd.
- 5.1.6 Ellwood Group Inc.
- 5.1.7 Scot Forge Company
- 5.1.8 Firth Rixson Limited
- 5.1.9 Wyman-Gordon Company
- 5.1.10 Schuler Group
- 5.1.11 Forgital Group
- 5.1.12 Mahindra Forgings Europe AG
- 5.1.13 Thyssenkrupp AG
- 5.1.14 Arconic Inc.
- 5.1.15 China First Heavy Industries
- 5.2 Cross Comparison Parameters (Revenue, Global Production Facilities, Employee Base, Key Clients, Innovation in Processes, Regional Presence, Raw Material Sources, Sustainable Practices)
- 5.3 Market Share Analysis (Top 5, Top 10 Players)
- 5.4 Strategic Initiatives
- 5.4.1 Capacity Expansions
- 5.4.2 Partnerships and Collaborations
- 5.4.3 Technological Advancements
- 5.5 Investment Landscape
- 5.5.1 Venture Capital Funding
- 5.5.2 Private Equity Investments
- 5.5.3 Government Grants and Incentives
- 6. USA Metal Forging Market Regulatory Framework
- 6.1 Safety Standards
- 6.2 Environmental Compliance
- 6.3 Import Tariff Regulations
- 7. USA Metal Forging Future Market Size (In USD Million)
- 7.1 Future Market Projections
- 7.2 Key Factors Driving Future Market Demand
- 8. Future Market Segmentation Analysis
- 8.1 By Process Type
- 8.2 By Material Type
- 8.3 By End-Use Industry
- 8.4 By Application
- 8.5 By Region
- 9. Market Analysts Recommendations
- 10.1 Total Addressable Market Analysis (TAM)
- 10.2 Strategic Entry Points
- 10.3 Industry Best Practices
- 10.4 White Space Opportunities
- Disclaimer
- Contact Us
Pricing
Currency Rates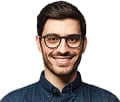
Questions or Comments?
Our team has the ability to search within reports to verify it suits your needs. We can also help maximize your budget by finding sections of reports you can purchase.