
US industry 4.0 Market Outlook to 2028
Description
US Industry 4.0 Market Overview
The US Industry 4.0 market is valued at USD 35 billion, based on a five-year historical analysis. The market has seen robust growth driven by increasing adoption of automation technologies across manufacturing, logistics, and energy sectors. Key factors contributing to this expansion include the widespread implementation of smart factory technologies, advanced robotics, and artificial intelligence (AI), which have significantly enhanced productivity and operational efficiency across various industrial verticals.
The US Industry 4.0 market is dominated by metropolitan areas such as New York, Chicago, and San Francisco due to their advanced infrastructure, high concentration of technology companies, and skilled workforce. These cities are hubs for technological innovation and industrial investment, making them critical drivers of Industry 4.0 implementation. Furthermore, federal initiatives promoting smart manufacturing have positioned these cities as leaders in this space.
The US government's Manufacturing USA initiative continues to promote advanced manufacturing through public-private partnerships. In 2024, $900 million was allocated to support these initiatives, fostering innovation in areas like robotics and AI in sectors such as aerospace and automotive. This government support has accelerated the integration of Industry 4.0 technologies by providing financial and technical assistance to manufacturers.
US Industry 4.0 Market Segmentation
By Technology: The US Industry 4.0 market is segmented by technology into Industrial Internet of Things (IIo T), Artificial Intelligence (AI), Robotics, Cloud Computing, and Edge Computing. Among these, IIo T holds a dominant share due to its role in enabling real-time monitoring and decision-making in industrial processes. With the capability to connect machines, devices, and systems, IIo T enhances operational efficiency and minimizes downtime. The integration of IIo T has revolutionized sectors such as automotive and aerospace, where the need for precision and real-time data is critical to maintaining competitiveness.
By Component: The market is further segmented by component into Hardware, Software, and Services. Hardware holds the largest share due to the high demand for sensors, controllers, and communication devices necessary to enable the interconnected systems of Industry 4.0. Additionally, continuous advancements in hardware components like Industrial Robots and smart machines have contributed to the dominance of this segment. The reliance on robust and scalable hardware infrastructure makes this component indispensable for implementing Industry 4.0 technologies.
US Industry 4.0 Market Competitive Landscape
The US Industry 4.0 market is characterized by the presence of several major global and local players who have established dominance through innovative product offerings and strategic partnerships. Companies such as General Electric and Siemens lead the market due to their extensive product portfolios and global footprint, while Rockwell Automation focuses on niche solutions in automation and control systems. The market is also witnessing increased activity from technology firms like Cisco Systems and Intel, who are advancing the Io T and AI segments through R&D and strategic collaborations with manufacturing companies.
Company Name
Establishment Year
Headquarters
Employees
Revenue (2023)
Product Portfolio
Digitalization Efforts
Partnerships
General Electric
1892
Boston, MA-----
Siemens AG
1847
Munich, Germany-----
Rockwell Automation
1903
Milwaukee, WI-----
Cisco Systems
1984
San Jose, CA-----
Intel Corporation
1968
Santa Clara, CA-----
US Industry 4.0 Market Analysis
Growth Drivers
Increasing Automation (Automation Level): The automation landscape in the US manufacturing sector has seen a significant shift in 2024. Over 2.5 million industrial robots are currently in use across manufacturing facilities in the US, according to 2024 industry reports. The deployment of automation technologies, such as automated guided vehicles (AGVs) and robotic arms, has streamlined production lines, reducing operational downtime. This expansion has been driven by the demand for higher productivity and the need to overcome labor shortages in key sectors like automotive and electronics manufacturing.
Advancements in AI and Machine Learning (Technological Integration): AI-powered systems, combined with machine learning algorithms, are being implemented to improve decision-making processes across manufacturing. In 2024, over 80,000 AI-based systems were integrated into US manufacturing plants. AI's integration into the supply chain has reduced inefficiencies by enabling real-time data analytics, optimizing production cycles, and minimizing waste. The United States Department of Commerce estimates that AI-driven processes will save over $1.2 billion annually by reducing waste and optimizing production times.
Government Policies Promoting Smart Manufacturing (Government Initiatives): The US government has implemented policies encouraging smart manufacturing, particularly through tax incentives and grants. In 2024, the government earmarked $1.5 billion to support industry-wide digital transformation, with programs targeting sectors like automotive and aerospace. Policies like the Advanced Manufacturing Partnerships (AMP) and Manufacturing USA are focused on accelerating Industry 4.0 adoption, especially in SMEs. This has fueled innovation, allowing firms to adopt cutting-edge technologies without excessive financial burdens.
Market Challenges
High Initial Investment (Cap Ex): Despite the benefits, the initial cost of implementing Industry 4.0 technologies remains a significant barrier. In 2024, the average cost of upgrading manufacturing facilities with advanced automation and AI-driven solutions was estimated at $12 million per plant. Smaller enterprises, which make up a substantial part of the US manufacturing ecosystem, often struggle with this upfront capital investment, which delays widespread adoption. This issue is particularly acute in industries such as textiles and food processing.
Integration Complexities (System Compatibility): Integrating new Industry 4.0 technologies with legacy systems has been a major challenge. As of 2024, 40% of US manufacturing firms reported difficulties in seamlessly connecting new digital solutions with existing machinery. The interoperability issues, especially in industries like aerospace and electronics, have led to operational disruptions and reduced overall efficiency during the transition phase. This complexity is causing delays in achieving full digital transformation in key manufacturing sectors.
US Industry 4.0 Market Future Outlook
Over the next five years, the US Industry 4.0 market is expected to experience significant growth driven by advancements in AI, automation, and data analytics. Continuous government support for smart manufacturing initiatives, combined with increasing demand for operational efficiency, will propel market expansion. The convergence of IT and OT (Operational Technology) systems is also anticipated to accelerate digital transformation across various industrial sectors, leading to improved decision-making capabilities, cost savings, and enhanced productivity.
Market Opportunities
Expanding Use of Robotics in Manufacturing (Robotic Process Integration): The use of robotics in US manufacturing continues to grow, with over 350,000 robots installed in 2024 alone. The automotive and electronics sectors are driving this adoption, using robots to handle complex assembly tasks and streamline production. By integrating robotics, manufacturers have reduced production costs by up to $6 billion annually and improved product quality by minimizing human error. This presents an opportunity for broader integration in other industries such as pharmaceuticals and consumer goods.
Increased Demand for Digital Twin Technology (Simulation Technology Adoption): The adoption of digital twin technology is expanding rapidly. In 2024, over 25,000 digital twins were deployed across US manufacturing sectors, allowing companies to create virtual replicas of physical processes. This technology has enabled real-time monitoring and predictive maintenance, improving equipment efficiency and reducing downtime by approximately 15%. Sectors like aerospace and defense are investing heavily in digital twins to optimize production and maintenance schedules.
Please Note: It will take 5-7 business days to complete the report upon order confirmation
The US Industry 4.0 market is valued at USD 35 billion, based on a five-year historical analysis. The market has seen robust growth driven by increasing adoption of automation technologies across manufacturing, logistics, and energy sectors. Key factors contributing to this expansion include the widespread implementation of smart factory technologies, advanced robotics, and artificial intelligence (AI), which have significantly enhanced productivity and operational efficiency across various industrial verticals.
The US Industry 4.0 market is dominated by metropolitan areas such as New York, Chicago, and San Francisco due to their advanced infrastructure, high concentration of technology companies, and skilled workforce. These cities are hubs for technological innovation and industrial investment, making them critical drivers of Industry 4.0 implementation. Furthermore, federal initiatives promoting smart manufacturing have positioned these cities as leaders in this space.
The US government's Manufacturing USA initiative continues to promote advanced manufacturing through public-private partnerships. In 2024, $900 million was allocated to support these initiatives, fostering innovation in areas like robotics and AI in sectors such as aerospace and automotive. This government support has accelerated the integration of Industry 4.0 technologies by providing financial and technical assistance to manufacturers.
US Industry 4.0 Market Segmentation
By Technology: The US Industry 4.0 market is segmented by technology into Industrial Internet of Things (IIo T), Artificial Intelligence (AI), Robotics, Cloud Computing, and Edge Computing. Among these, IIo T holds a dominant share due to its role in enabling real-time monitoring and decision-making in industrial processes. With the capability to connect machines, devices, and systems, IIo T enhances operational efficiency and minimizes downtime. The integration of IIo T has revolutionized sectors such as automotive and aerospace, where the need for precision and real-time data is critical to maintaining competitiveness.
By Component: The market is further segmented by component into Hardware, Software, and Services. Hardware holds the largest share due to the high demand for sensors, controllers, and communication devices necessary to enable the interconnected systems of Industry 4.0. Additionally, continuous advancements in hardware components like Industrial Robots and smart machines have contributed to the dominance of this segment. The reliance on robust and scalable hardware infrastructure makes this component indispensable for implementing Industry 4.0 technologies.
US Industry 4.0 Market Competitive Landscape
The US Industry 4.0 market is characterized by the presence of several major global and local players who have established dominance through innovative product offerings and strategic partnerships. Companies such as General Electric and Siemens lead the market due to their extensive product portfolios and global footprint, while Rockwell Automation focuses on niche solutions in automation and control systems. The market is also witnessing increased activity from technology firms like Cisco Systems and Intel, who are advancing the Io T and AI segments through R&D and strategic collaborations with manufacturing companies.
Company Name
Establishment Year
Headquarters
Employees
Revenue (2023)
Product Portfolio
Digitalization Efforts
Partnerships
General Electric
1892
Boston, MA-----
Siemens AG
1847
Munich, Germany-----
Rockwell Automation
1903
Milwaukee, WI-----
Cisco Systems
1984
San Jose, CA-----
Intel Corporation
1968
Santa Clara, CA-----
US Industry 4.0 Market Analysis
Growth Drivers
Increasing Automation (Automation Level): The automation landscape in the US manufacturing sector has seen a significant shift in 2024. Over 2.5 million industrial robots are currently in use across manufacturing facilities in the US, according to 2024 industry reports. The deployment of automation technologies, such as automated guided vehicles (AGVs) and robotic arms, has streamlined production lines, reducing operational downtime. This expansion has been driven by the demand for higher productivity and the need to overcome labor shortages in key sectors like automotive and electronics manufacturing.
Advancements in AI and Machine Learning (Technological Integration): AI-powered systems, combined with machine learning algorithms, are being implemented to improve decision-making processes across manufacturing. In 2024, over 80,000 AI-based systems were integrated into US manufacturing plants. AI's integration into the supply chain has reduced inefficiencies by enabling real-time data analytics, optimizing production cycles, and minimizing waste. The United States Department of Commerce estimates that AI-driven processes will save over $1.2 billion annually by reducing waste and optimizing production times.
Government Policies Promoting Smart Manufacturing (Government Initiatives): The US government has implemented policies encouraging smart manufacturing, particularly through tax incentives and grants. In 2024, the government earmarked $1.5 billion to support industry-wide digital transformation, with programs targeting sectors like automotive and aerospace. Policies like the Advanced Manufacturing Partnerships (AMP) and Manufacturing USA are focused on accelerating Industry 4.0 adoption, especially in SMEs. This has fueled innovation, allowing firms to adopt cutting-edge technologies without excessive financial burdens.
Market Challenges
High Initial Investment (Cap Ex): Despite the benefits, the initial cost of implementing Industry 4.0 technologies remains a significant barrier. In 2024, the average cost of upgrading manufacturing facilities with advanced automation and AI-driven solutions was estimated at $12 million per plant. Smaller enterprises, which make up a substantial part of the US manufacturing ecosystem, often struggle with this upfront capital investment, which delays widespread adoption. This issue is particularly acute in industries such as textiles and food processing.
Integration Complexities (System Compatibility): Integrating new Industry 4.0 technologies with legacy systems has been a major challenge. As of 2024, 40% of US manufacturing firms reported difficulties in seamlessly connecting new digital solutions with existing machinery. The interoperability issues, especially in industries like aerospace and electronics, have led to operational disruptions and reduced overall efficiency during the transition phase. This complexity is causing delays in achieving full digital transformation in key manufacturing sectors.
US Industry 4.0 Market Future Outlook
Over the next five years, the US Industry 4.0 market is expected to experience significant growth driven by advancements in AI, automation, and data analytics. Continuous government support for smart manufacturing initiatives, combined with increasing demand for operational efficiency, will propel market expansion. The convergence of IT and OT (Operational Technology) systems is also anticipated to accelerate digital transformation across various industrial sectors, leading to improved decision-making capabilities, cost savings, and enhanced productivity.
Market Opportunities
Expanding Use of Robotics in Manufacturing (Robotic Process Integration): The use of robotics in US manufacturing continues to grow, with over 350,000 robots installed in 2024 alone. The automotive and electronics sectors are driving this adoption, using robots to handle complex assembly tasks and streamline production. By integrating robotics, manufacturers have reduced production costs by up to $6 billion annually and improved product quality by minimizing human error. This presents an opportunity for broader integration in other industries such as pharmaceuticals and consumer goods.
Increased Demand for Digital Twin Technology (Simulation Technology Adoption): The adoption of digital twin technology is expanding rapidly. In 2024, over 25,000 digital twins were deployed across US manufacturing sectors, allowing companies to create virtual replicas of physical processes. This technology has enabled real-time monitoring and predictive maintenance, improving equipment efficiency and reducing downtime by approximately 15%. Sectors like aerospace and defense are investing heavily in digital twins to optimize production and maintenance schedules.
Please Note: It will take 5-7 business days to complete the report upon order confirmation
Table of Contents
81 Pages
- 1. US Industry 4.0 Market Overview
- 1.1. Definition and Scope
- 1.2. Market Taxonomy (Key Technologies, Industry Verticals)
- 1.3. Market Growth Rate
- 1.4. Market Segmentation Overview
- 2. US Industry 4.0 Market Size (In USD Bn)
- 2.1. Historical Market Size
- 2.2. Year-On-Year Growth Analysis
- 2.3. Key Market Developments and Milestones
- 3. US Industry 4.0 Market Analysis
- 3.1. Growth Drivers
- 3.1.1. Increasing Automation (Automation Level)
- 3.1.2. Advancements in AI and Machine Learning (Technological Integration)
- 3.1.3. Government Policies Promoting Smart Manufacturing (Government Initiatives)
- 3.1.4. Rising Adoption of IIoT (IoT Adoption Rate)
- 3.2. Market Challenges
- 3.2.1. High Initial Investment (CapEx)
- 3.2.2. Integration Complexities (System Compatibility)
- 3.2.3. Cybersecurity Risks (Data Security Issues)
- 3.2.4. Workforce Skill Gaps (Training and Development Needs)
- 3.3. Opportunities
- 3.3.1. Expanding Use of Robotics in Manufacturing (Robotic Process Integration)
- 3.3.2. Increased Demand for Digital Twin Technology (Simulation Technology Adoption)
- 3.3.3. Growth in Predictive Maintenance Solutions (Maintenance and Monitoring Tools)
- 3.3.4. Adoption of 5G in Industrial Applications (5G Network Penetration)
- 3.4. Trends
- 3.4.1. Integration of Edge Computing (Decentralized Data Processing)
- 3.4.2. Rise of Smart Factories (Self-Optimizing Manufacturing)
- 3.4.3. Convergence of IT and OT Systems (Systems Integration)
- 3.4.4. Utilization of Advanced Analytics (Real-time Data Insights)
- 3.5. Government Regulation
- 3.5.1. National Initiatives on Industry 4.0 (Smart Manufacturing Policy)
- 3.5.2. Compliance Standards (ISO/IEC Requirements)
- 3.5.3. Workforce Development Programs (Reskilling Initiatives)
- 3.5.4. Data Security and Privacy Regulations (GDPR, CCPA)
- 3.6. SWOT Analysis
- 3.6.1. Strengths
- 3.6.2. Weaknesses
- 3.6.3. Opportunities
- 3.6.4. Threats
- 3.7. Stakeholder Ecosystem (Vendors, Service Providers, End-Users)
- 3.8. Porters Five Forces Analysis (Bargaining Power of Buyers, Bargaining Power of Suppliers, Threat of New Entrants, Threat of Substitutes, Industry Rivalry)
- 4. US Industry 4.0 Market Segmentation
- 4.1. By Technology (In Value %)
- 4.1.1. Industrial Internet of Things (IIoT)
- 4.1.2. Artificial Intelligence (AI)
- 4.1.3. Advanced Robotics
- 4.1.4. Cloud Computing
- 4.1.5. Edge Computing
- 4.2. By Component (In Value %)
- 4.2.1. Hardware (Sensors, Actuators, Controllers)
- 4.2.2. Software (SCADA, MES, ERP)
- 4.2.3. Services (Consulting, Implementation, Support)
- 4.3. By Application (In Value %)
- 4.3.1. Predictive Maintenance
- 4.3.2. Smart Factories
- 4.3.3. Supply Chain Optimization
- 4.3.4. Human-Machine Interface (HMI)
- 4.3.5. Asset Tracking and Management
- 4.4. By Industry Vertical (In Value %)
- 4.4.1. Automotive
- 4.4.2. Aerospace & Defense
- 4.4.3. Electronics & Semiconductors
- 4.4.4. Chemicals & Materials
- 4.4.5. Healthcare & Pharmaceuticals
- 4.5. By Region (In Value %)
- 4.5.1. North-East
- 4.5.2. Midwest
- 4.5.3. South
- 4.5.4. West
- 5. US Industry 4.0 Market Competitive Analysis
- 5.1. Detailed Profiles of Major Companies
- 5.1.1. General Electric
- 5.1.2. Rockwell Automation
- 5.1.3. Siemens AG
- 5.1.4. Honeywell International
- 5.1.5. ABB Ltd.
- 5.1.6. Cisco Systems
- 5.1.7. Intel Corporation
- 5.1.8. IBM Corporation
- 5.1.9. Microsoft Corporation
- 5.1.10. Schneider Electric
- 5.1.11. SAP SE
- 5.1.12. Mitsubishi Electric Corporation
- 5.1.13. Bosch Rexroth
- 5.1.14. Emerson Electric Co.
- 5.1.15. Fanuc Corporation
- 5.2. Cross Comparison Parameters (Revenue, R&D Spending, Number of Employees, Digital Transformation Initiatives, Cloud Adoption Rate, Automation Adoption Level, AI Integration, Market Penetration by Industry Vertical)
- 5.3. Market Share Analysis
- 5.4. Strategic Initiatives (Mergers & Acquisitions, Partnerships, Joint Ventures)
- 5.5. R&D and Innovation Strategies
- 5.6. Investment Analysis
- 5.7. Venture Capital and Private Equity Investments
- 6. US Industry 4.0 Market Regulatory Framework
- 6.1. National Manufacturing Policies (Smart Manufacturing Initiatives, Industrial Strategy, Made in America Initiatives)
- 6.2. Compliance Requirements (Data Security, ISO Standards)
- 6.3. Workforce Development Programs (Reskilling, Training Initiatives)
- 6.4. Digital Infrastructure Investments
- 7. US Industry 4.0 Future Market Size (In USD Bn)
- 7.1. Future Market Size Projections
- 7.2. Key Factors Driving Future Market Growth
- 8. US Industry 4.0 Future Market Segmentation
- 8.1. By Technology (In Value %)
- 8.2. By Component (In Value %)
- 8.3. By Application (In Value %)
- 8.4. By Industry Vertical (In Value %)
- 8.5. By Region (In Value %)
- 9. US Industry 4.0 Market Analysts Recommendations
- 9.1. TAM/SAM/SOM Analysis
- 9.2. Customer Cohort Analysis
- 9.3. Go-To-Market Strategies
- 9.4. White Space Opportunity Analysis
- Disclaimer
- Contact Us
Pricing
Currency Rates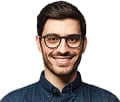
Questions or Comments?
Our team has the ability to search within reports to verify it suits your needs. We can also help maximize your budget by finding sections of reports you can purchase.