
Rubber Processing Aids and Anti-Tack Agents
Description
Global Rubber Processing Aids and Anti-Tack Agents Market to Reach US$568.7 Million by 2030
The global market for Rubber Processing Aids and Anti-Tack Agents estimated at US$458.8 Million in the year 2024, is expected to reach US$568.7 Million by 2030, growing at a CAGR of 3.6% over the analysis period 2024-2030. Fatty Acid Esters, one of the segments analyzed in the report, is expected to record a 3.1% CAGR and reach US$151.4 Million by the end of the analysis period. Growth in the Fatty Acid Amides segment is estimated at 5.0% CAGR over the analysis period.
The U.S. Market is Estimated at US$125.0 Million While China is Forecast to Grow at 6.6% CAGR
The Rubber Processing Aids and Anti-Tack Agents market in the U.S. is estimated at US$125.0 Million in the year 2024. China, the world`s second largest economy, is forecast to reach a projected market size of US$113.2 Million by the year 2030 trailing a CAGR of 6.6% over the analysis period 2024-2030. Among the other noteworthy geographic markets are Japan and Canada, each forecast to grow at a CAGR of 1.5% and 2.8% respectively over the analysis period. Within Europe, Germany is forecast to grow at approximately 2.1% CAGR.
Global Rubber Processing Aids And Anti-Tack Agents Market - Key Trends & Drivers Summarized
Why Are Processing Aids Essential in Modern Rubber Manufacturing Environments?
Rubber processing aids and anti-tack agents have become critical components in modern elastomer production as manufacturers demand enhanced processability, mixing consistency, and downstream efficiency. Processing aids are primarily used to modify the flow characteristics and plasticity of rubber during mastication, extrusion, and molding, enabling smoother blending of fillers, pigments, curatives, and reinforcements. In the absence of these additives, manufacturers face challenges like scorching, inconsistent filler dispersion, high energy consumption, and reduced throughput. A significant portion of demand stems from industries producing high-performance tires, industrial belts, hoses, gaskets, and seals-where mechanical properties and dimensional stability are closely tied to formulation consistency.
Paraffinic oils, fatty acid esters, aliphatic resins, and silicone-based processing aids dominate the market due to their compatibility with both natural and synthetic rubber systems such as SBR, BR, NBR, and EPDM. In high-volume applications like tire manufacturing, processing aids enable the incorporation of high filler loadings-especially carbon black and silica-without compromising compound viscosity or flow. Furthermore, these aids improve filler dispersion, reduce mixing time, and enhance mold flow, contributing to reduced cycle times and energy savings. Specialty processing aids that act as peptizers or coupling agents are increasingly used in formulations requiring optimized viscoelastic balance and enhanced mechanical strength.
How Are Anti-Tack Agents Improving Workflow Efficiency and Product Quality?
Anti-tack agents are essential in preventing uncured rubber compounds from adhering to each other during storage, transport, and batch staging processes. These materials are especially vital in tire manufacturing and compound preparation units where sheets, slabs, or pellets of rubber are stacked or coiled before vulcanization. Without proper anti-tack coatings, adhesion leads to scrap generation, rework, and operational delays. Typically composed of fatty acids, silica, kaolin, or proprietary blends with aqueous or solvent carriers, these agents are applied via spraying, brushing, or dipping. Innovations in water-based, non-dusting formulations are making anti-tack agents safer for workers and compliant with workplace safety regulations.
Modern anti-tack agents are also being developed to offer multifunctionality-combining anti-blocking, surface lubrication, and anti-static properties in a single solution. These products are designed to minimize interaction with curing agents, thereby ensuring that surface coatings do not interfere with vulcanization kinetics or final product performance. Moreover, eco-friendly variants that reduce VOC emissions, improve biodegradability, and eliminate heavy metal residues are gaining traction, particularly in regions with strict environmental compliance requirements. Automation-friendly anti-tack spray systems are also being integrated into smart factory setups, enabling precise dosing and real-time monitoring, thereby standardizing application quality and reducing material wastage.
Which Applications and Geographies Are Driving Market Demand Growth?
The automotive sector is the largest end-use segment for rubber processing aids and anti-tack agents, primarily due to its consumption of tires, vibration control systems, sealing profiles, and fluid handling components. Rising vehicle production volumes across Asia-Pacific and the growth of electric vehicles are directly contributing to the expanded use of high-performance elastomers, which in turn require precision compounding aided by advanced processing chemicals. The tire manufacturing segment in China, India, and Southeast Asia is particularly influential, with mid- to large-scale players upgrading formulations to improve rolling resistance, wet grip, and wear life.
Beyond automotive, industrial rubber goods such as conveyor belts, wire and cable insulation, and molded products for construction and agriculture are also driving demand. The U.S. and European markets are adopting specialized processing aids to meet REACH-compliant formulations and eliminate PAHs (polycyclic aromatic hydrocarbons). Latin America and the Middle East, meanwhile, are seeing growth due to the establishment of rubber compounding units supporting both local and export-oriented production. Additionally, the shift toward sustainability is prompting OEMs and compounders in Europe and North America to specify processing aids and anti-tack agents that support recyclability, green chemistry, and energy-efficient production.
What Are the Primary Drivers Accelerating Market Growth Worldwide?
The growth in the rubber processing aids and anti-tack agents market is driven by several factors that collectively enable scalable, efficient, and high-quality elastomer production. A key driver is the increasing demand for high-performance and specialty rubber compounds in automotive, industrial, and consumer applications. As manufacturers seek to balance cost-efficiency with product reliability, processing aids play a critical role in achieving target material properties without compromising processing speed. Simultaneously, the adoption of anti-tack agents is becoming essential in automated and high-throughput environments where workflow interruptions caused by compound sticking are not tolerable.
Rising labor costs, energy pricing, and environmental regulations are also compelling manufacturers to use advanced aids that reduce scrap rates, cycle times, and VOC emissions. Ongoing innovations in formulation chemistry and application technology are enhancing compatibility with new rubber types such as halogenated elastomers and bio-based alternatives. Sustainability initiatives-driven by regulatory bodies and corporate ESG goals-are increasing the demand for renewable, biodegradable, and low-impact processing chemicals. Finally, the digital transformation of rubber manufacturing, including the adoption of smart compounding and automated spraying systems, is reinforcing the value proposition of precision processing aids and advanced anti-tack solutions across global production hubs.
SCOPE OF STUDY:The report analyzes the Rubber Processing Aids and Anti-Tack Agents market in terms of units by the following Segments, and Geographic Regions/Countries:
Segments:
Product Type (Fatty Acid Esters, Fatty Acid Amides, Stearates, Soaps, Silicone Polymers, Other Rubber Processing Aids & Anti-Tack Agents); Application (Tires & Tubes Application, Gaskets & Seals Application, Wires & Cables Application, Molded Rubber Products Application, Medical Gloves Application, Other Applications); End-Use (Automotive & Transportation End-Use, Building & Construction End-Use, Medical End-Use, Electronics & Electricals End-Use, Footwear End-Use, Other End-Uses)
Geographic Regions/Countries:
World; United States; Canada; Japan; China; Europe (France; Germany; Italy; United Kingdom; Spain; Russia; and Rest of Europe); Asia-Pacific (Australia; India; South Korea; and Rest of Asia-Pacific); Latin America (Argentina; Brazil; Mexico; and Rest of Latin America); Middle East (Iran; Israel; Saudi Arabia; United Arab Emirates; and Rest of Middle East); and Africa.
Select Competitors (Total 34 Featured) -
- BASF SE
- Baerlocher GmbH
- Barbe Group
- Croda International
- Evonik Industries AG
- Hallstar Innovations Corp.
- H.L. Blachford Ltd.
- King Industries, Inc.
- Lehigh Technologies
- Lion Specialty Chemicals Co., Ltd.
- McGee Industries, Inc.
- McLube (Stewart-Stephenson)
- Peter Greven GmbH & Co. KG
- Polymer Solutions Group SASCO
- Sasco Chemical Group, Inc.
- Schill + Seilacher "Struktol" GmbH
- Stephenson Alkon Solutions
- Struktol (Schill + Seilacher)
We`re transforming market and competitive intelligence with validated expert content and AI tools.
Instead of following the general norm of querying LLMs and Industry-specific SLMs, we built repositories of content curated from domain experts worldwide including video transcripts, blogs, search engines research, and massive amounts of enterprise, product/service, and market data.
TARIFF IMPACT FACTOR
Our new release incorporates impact of tariffs on geographical markets as we predict a shift in competitiveness of companies based on HQ country, manufacturing base, exports and imports (finished goods and OEM). This intricate and multifaceted market reality will impact competitors by increasing the Cost of Goods Sold (COGS), reducing profitability, reconfiguring supply chains, amongst other micro and macro market dynamics.
Please note: Reports are sold as single-site single-user licenses. Electronic versions require 24-48 hours as each copy is customized to the client with digital controls and custom watermarks. The Publisher uses digital controls protecting against copying and printing is restricted to one full copy to be used at the same location.
The latest version of Adobe Acrobat Reader is required to view the report. Upon ordering an electronic version, the Publisher will provide a link to download the purchased report.
Prior to fulfillment of an order, the client will be required to sign a document detailing the purchase terms for a publication from this publisher.
Table of Contents
- I. METHODOLOGY
- II. EXECUTIVE SUMMARY
- 1. MARKET OVERVIEW
- Influencer Market Insights
- World Market Trajectories
- Tariff Impact on Global Supply Chain Patterns
- Rubber Processing Aids and Anti-Tack Agents – Global Key Competitors Percentage Market Share in 2025 (E)
- Competitive Market Presence - Strong/Active/Niche/Trivial for Players Worldwide in 2025 (E)
- 2. FOCUS ON SELECT PLAYERS
- 3. MARKET TRENDS & DRIVERS
- Surge in Global Tire Production Drives Demand for High-Performance Rubber Processing Aids
- Growth in Automotive and Industrial Rubber Goods Expands Use of Anti-Tack Agents for Compound Handling
- Technological Advancements in Silica Dispersion and Mixing Efficiency Strengthen Compound Uniformity
- Environmental Regulations on VOC Emissions Propel Use of Low-Volatility and Water-Based Agents
- Rising Demand for Improved Processing Speed and Lower Energy Consumption Fuels Additive Innovation
- Expansion of Synthetic Rubber Production in Asia-Pacific Strengthens Regional Product Utilization
- OEM Requirements for Batch Consistency and Defect Reduction Drive Adoption of Processing Aids
- Shift Toward Green and Bio-Based Rubber Additives Supports Market Sustainability Objectives
- Increased Adoption of Non-Dusting and Slurry-Based Anti-Tack Formulations Enhances Worker Safety
- Growth in Footwear, Conveyor Belts, and Rubber Hoses Expands End-Use Application Scope
- Collaborations Between Polymer Producers and Additive Suppliers Accelerate Material Compatibility
- Focus on High-Filler Compounding in Performance Tires Drives Need for Enhanced Dispersion Aids
- Regulatory Push for Phthalate-Free and Safe Processing Chemicals Promotes Product Reformulation
- Expansion of Tire Retreading and Recycling Initiatives Boosts Demand for Easy-Processing Rubber Compounds
- Automated Material Handling Systems in Rubber Plants Strengthen Use of Flow-Enhancing Agents
- Customization and Tailored Formulations Improve Compatibility With Specific Elastomer Systems
- Price Volatility of Petrochemical Feedstocks Encourages Adoption of Efficient Processing Technologies
- Growing Demand for Cold Feed Extrusion and Injection Molding Enhances Use of Softening Aids
- Increased Globalization of Automotive Supply Chains Spurs Regional Sourcing of Processing Additives
- Digitalization in Rubber Compounding Drives Formulation Optimization and Real-Time Dosing Control
- 4. GLOBAL MARKET PERSPECTIVE
- TABLE 1: World Rubber Processing Aids and Anti-Tack Agents Market Analysis of Annual Sales in US$ Thousand for Years 2014 through 2030
- TABLE 2: World Recent Past, Current & Future Analysis for Rubber Processing Aids and Anti-Tack Agents by Geographic Region - USA, Canada, Japan, China, Europe, Asia-Pacific, Latin America, Middle East and Africa Markets - Independent Analysis of Annual Sales in US$ Thousand for Years 2024 through 2030 and % CAGR
- TABLE 3: World Historic Review for Rubber Processing Aids and Anti-Tack Agents by Geographic Region - USA, Canada, Japan, China, Europe, Asia-Pacific, Latin America, Middle East and Africa Markets - Independent Analysis of Annual Sales in US$ Thousand for Years 2014 through 2023 and % CAGR
- TABLE 4: World 16-Year Perspective for Rubber Processing Aids and Anti-Tack Agents by Geographic Region - Percentage Breakdown of Value Sales for USA, Canada, Japan, China, Europe, Asia-Pacific, Latin America, Middle East and Africa Markets for Years 2014, 2025 & 2030
- TABLE 5: World Recent Past, Current & Future Analysis for Fatty Acid Esters by Geographic Region - USA, Canada, Japan, China, Europe, Asia-Pacific, Latin America, Middle East and Africa Markets - Independent Analysis of Annual Sales in US$ Thousand for Years 2024 through 2030 and % CAGR
- TABLE 6: World Historic Review for Fatty Acid Esters by Geographic Region - USA, Canada, Japan, China, Europe, Asia-Pacific, Latin America, Middle East and Africa Markets - Independent Analysis of Annual Sales in US$ Thousand for Years 2014 through 2023 and % CAGR
- TABLE 7: World 16-Year Perspective for Fatty Acid Esters by Geographic Region - Percentage Breakdown of Value Sales for USA, Canada, Japan, China, Europe, Asia-Pacific, Latin America, Middle East and Africa for Years 2014, 2025 & 2030
- TABLE 8: World Recent Past, Current & Future Analysis for Fatty Acid Amides by Geographic Region - USA, Canada, Japan, China, Europe, Asia-Pacific, Latin America, Middle East and Africa Markets - Independent Analysis of Annual Sales in US$ Thousand for Years 2024 through 2030 and % CAGR
- TABLE 9: World Historic Review for Fatty Acid Amides by Geographic Region - USA, Canada, Japan, China, Europe, Asia-Pacific, Latin America, Middle East and Africa Markets - Independent Analysis of Annual Sales in US$ Thousand for Years 2014 through 2023 and % CAGR
- TABLE 10: World 16-Year Perspective for Fatty Acid Amides by Geographic Region - Percentage Breakdown of Value Sales for USA, Canada, Japan, China, Europe, Asia-Pacific, Latin America, Middle East and Africa for Years 2014, 2025 & 2030
- TABLE 11: World Recent Past, Current & Future Analysis for Stearates by Geographic Region - USA, Canada, Japan, China, Europe, Asia-Pacific, Latin America, Middle East and Africa Markets - Independent Analysis of Annual Sales in US$ Thousand for Years 2024 through 2030 and % CAGR
- TABLE 12: World Historic Review for Stearates by Geographic Region - USA, Canada, Japan, China, Europe, Asia-Pacific, Latin America, Middle East and Africa Markets - Independent Analysis of Annual Sales in US$ Thousand for Years 2014 through 2023 and % CAGR
- TABLE 13: World 16-Year Perspective for Stearates by Geographic Region - Percentage Breakdown of Value Sales for USA, Canada, Japan, China, Europe, Asia-Pacific, Latin America, Middle East and Africa for Years 2014, 2025 & 2030
- TABLE 14: World Recent Past, Current & Future Analysis for Soaps by Geographic Region - USA, Canada, Japan, China, Europe, Asia-Pacific, Latin America, Middle East and Africa Markets - Independent Analysis of Annual Sales in US$ Thousand for Years 2024 through 2030 and % CAGR
- TABLE 15: World Historic Review for Soaps by Geographic Region - USA, Canada, Japan, China, Europe, Asia-Pacific, Latin America, Middle East and Africa Markets - Independent Analysis of Annual Sales in US$ Thousand for Years 2014 through 2023 and % CAGR
- TABLE 16: World 16-Year Perspective for Soaps by Geographic Region - Percentage Breakdown of Value Sales for USA, Canada, Japan, China, Europe, Asia-Pacific, Latin America, Middle East and Africa for Years 2014, 2025 & 2030
- TABLE 17: World Recent Past, Current & Future Analysis for Silicone Polymers by Geographic Region - USA, Canada, Japan, China, Europe, Asia-Pacific, Latin America, Middle East and Africa Markets - Independent Analysis of Annual Sales in US$ Thousand for Years 2024 through 2030 and % CAGR
- TABLE 18: World Historic Review for Silicone Polymers by Geographic Region - USA, Canada, Japan, China, Europe, Asia-Pacific, Latin America, Middle East and Africa Markets - Independent Analysis of Annual Sales in US$ Thousand for Years 2014 through 2023 and % CAGR
- TABLE 19: World 16-Year Perspective for Silicone Polymers by Geographic Region - Percentage Breakdown of Value Sales for USA, Canada, Japan, China, Europe, Asia-Pacific, Latin America, Middle East and Africa for Years 2014, 2025 & 2030
- TABLE 20: World Recent Past, Current & Future Analysis for Other Rubber Processing Aids & Anti-Tack Agents by Geographic Region - USA, Canada, Japan, China, Europe, Asia-Pacific, Latin America, Middle East and Africa Markets - Independent Analysis of Annual Sales in US$ Thousand for Years 2024 through 2030 and % CAGR
- TABLE 21: World Historic Review for Other Rubber Processing Aids & Anti-Tack Agents by Geographic Region - USA, Canada, Japan, China, Europe, Asia-Pacific, Latin America, Middle East and Africa Markets - Independent Analysis of Annual Sales in US$ Thousand for Years 2014 through 2023 and % CAGR
- TABLE 22: World 16-Year Perspective for Other Rubber Processing Aids & Anti-Tack Agents by Geographic Region - Percentage Breakdown of Value Sales for USA, Canada, Japan, China, Europe, Asia-Pacific, Latin America, Middle East and Africa for Years 2014, 2025 & 2030
- TABLE 23: World Recent Past, Current & Future Analysis for Molded Rubber Products Application by Geographic Region - USA, Canada, Japan, China, Europe, Asia-Pacific, Latin America, Middle East and Africa Markets - Independent Analysis of Annual Sales in US$ Thousand for Years 2024 through 2030 and % CAGR
- TABLE 24: World Historic Review for Molded Rubber Products Application by Geographic Region - USA, Canada, Japan, China, Europe, Asia-Pacific, Latin America, Middle East and Africa Markets - Independent Analysis of Annual Sales in US$ Thousand for Years 2014 through 2023 and % CAGR
- TABLE 25: World 16-Year Perspective for Molded Rubber Products Application by Geographic Region - Percentage Breakdown of Value Sales for USA, Canada, Japan, China, Europe, Asia-Pacific, Latin America, Middle East and Africa for Years 2014, 2025 & 2030
- TABLE 26: World Recent Past, Current & Future Analysis for Medical Gloves Application by Geographic Region - USA, Canada, Japan, China, Europe, Asia-Pacific, Latin America, Middle East and Africa Markets - Independent Analysis of Annual Sales in US$ Thousand for Years 2024 through 2030 and % CAGR
- TABLE 27: World Historic Review for Medical Gloves Application by Geographic Region - USA, Canada, Japan, China, Europe, Asia-Pacific, Latin America, Middle East and Africa Markets - Independent Analysis of Annual Sales in US$ Thousand for Years 2014 through 2023 and % CAGR
- TABLE 28: World 16-Year Perspective for Medical Gloves Application by Geographic Region - Percentage Breakdown of Value Sales for USA, Canada, Japan, China, Europe, Asia-Pacific, Latin America, Middle East and Africa for Years 2014, 2025 & 2030
- TABLE 29: World Recent Past, Current & Future Analysis for Other Applications by Geographic Region - USA, Canada, Japan, China, Europe, Asia-Pacific, Latin America, Middle East and Africa Markets - Independent Analysis of Annual Sales in US$ Thousand for Years 2024 through 2030 and % CAGR
- TABLE 30: World Historic Review for Other Applications by Geographic Region - USA, Canada, Japan, China, Europe, Asia-Pacific, Latin America, Middle East and Africa Markets - Independent Analysis of Annual Sales in US$ Thousand for Years 2014 through 2023 and % CAGR
- TABLE 31: World 16-Year Perspective for Other Applications by Geographic Region - Percentage Breakdown of Value Sales for USA, Canada, Japan, China, Europe, Asia-Pacific, Latin America, Middle East and Africa for Years 2014, 2025 & 2030
- TABLE 32: World Recent Past, Current & Future Analysis for Tires & Tubes Application by Geographic Region - USA, Canada, Japan, China, Europe, Asia-Pacific, Latin America, Middle East and Africa Markets - Independent Analysis of Annual Sales in US$ Thousand for Years 2024 through 2030 and % CAGR
- TABLE 33: World Historic Review for Tires & Tubes Application by Geographic Region - USA, Canada, Japan, China, Europe, Asia-Pacific, Latin America, Middle East and Africa Markets - Independent Analysis of Annual Sales in US$ Thousand for Years 2014 through 2023 and % CAGR
- TABLE 34: World 16-Year Perspective for Tires & Tubes Application by Geographic Region - Percentage Breakdown of Value Sales for USA, Canada, Japan, China, Europe, Asia-Pacific, Latin America, Middle East and Africa for Years 2014, 2025 & 2030
- TABLE 35: World Recent Past, Current & Future Analysis for Gaskets & Seals Application by Geographic Region - USA, Canada, Japan, China, Europe, Asia-Pacific, Latin America, Middle East and Africa Markets - Independent Analysis of Annual Sales in US$ Thousand for Years 2024 through 2030 and % CAGR
- TABLE 36: World Historic Review for Gaskets & Seals Application by Geographic Region - USA, Canada, Japan, China, Europe, Asia-Pacific, Latin America, Middle East and Africa Markets - Independent Analysis of Annual Sales in US$ Thousand for Years 2014 through 2023 and % CAGR
- TABLE 37: World 16-Year Perspective for Gaskets & Seals Application by Geographic Region - Percentage Breakdown of Value Sales for USA, Canada, Japan, China, Europe, Asia-Pacific, Latin America, Middle East and Africa for Years 2014, 2025 & 2030
- TABLE 38: World Recent Past, Current & Future Analysis for Wires & Cables Application by Geographic Region - USA, Canada, Japan, China, Europe, Asia-Pacific, Latin America, Middle East and Africa Markets - Independent Analysis of Annual Sales in US$ Thousand for Years 2024 through 2030 and % CAGR
- TABLE 39: World Historic Review for Wires & Cables Application by Geographic Region - USA, Canada, Japan, China, Europe, Asia-Pacific, Latin America, Middle East and Africa Markets - Independent Analysis of Annual Sales in US$ Thousand for Years 2014 through 2023 and % CAGR
- TABLE 40: World 16-Year Perspective for Wires & Cables Application by Geographic Region - Percentage Breakdown of Value Sales for USA, Canada, Japan, China, Europe, Asia-Pacific, Latin America, Middle East and Africa for Years 2014, 2025 & 2030
- TABLE 41: World Recent Past, Current & Future Analysis for Automotive & Transportation End-Use by Geographic Region - USA, Canada, Japan, China, Europe, Asia-Pacific, Latin America, Middle East and Africa Markets - Independent Analysis of Annual Sales in US$ Thousand for Years 2024 through 2030 and % CAGR
- TABLE 42: World Historic Review for Automotive & Transportation End-Use by Geographic Region - USA, Canada, Japan, China, Europe, Asia-Pacific, Latin America, Middle East and Africa Markets - Independent Analysis of Annual Sales in US$ Thousand for Years 2014 through 2023 and % CAGR
- TABLE 43: World 16-Year Perspective for Automotive & Transportation End-Use by Geographic Region - Percentage Breakdown of Value Sales for USA, Canada, Japan, China, Europe, Asia-Pacific, Latin America, Middle East and Africa for Years 2014, 2025 & 2030
- TABLE 44: World Recent Past, Current & Future Analysis for Building & Construction End-Use by Geographic Region - USA, Canada, Japan, China, Europe, Asia-Pacific, Latin America, Middle East and Africa Markets - Independent Analysis of Annual Sales in US$ Thousand for Years 2024 through 2030 and % CAGR
- TABLE 45: World Historic Review for Building & Construction End-Use by Geographic Region - USA, Canada, Japan, China, Europe, Asia-Pacific, Latin America, Middle East and Africa Markets - Independent Analysis of Annual Sales in US$ Thousand for Years 2014 through 2023 and % CAGR
- TABLE 46: World 16-Year Perspective for Building & Construction End-Use by Geographic Region - Percentage Breakdown of Value Sales for USA, Canada, Japan, China, Europe, Asia-Pacific, Latin America, Middle East and Africa for Years 2014, 2025 & 2030
- TABLE 47: World Recent Past, Current & Future Analysis for Medical End-Use by Geographic Region - USA, Canada, Japan, China, Europe, Asia-Pacific, Latin America, Middle East and Africa Markets - Independent Analysis of Annual Sales in US$ Thousand for Years 2024 through 2030 and % CAGR
- TABLE 48: World Historic Review for Medical End-Use by Geographic Region - USA, Canada, Japan, China, Europe, Asia-Pacific, Latin America, Middle East and Africa Markets - Independent Analysis of Annual Sales in US$ Thousand for Years 2014 through 2023 and % CAGR
- TABLE 49: World 16-Year Perspective for Medical End-Use by Geographic Region - Percentage Breakdown of Value Sales for USA, Canada, Japan, China, Europe, Asia-Pacific, Latin America, Middle East and Africa for Years 2014, 2025 & 2030
- TABLE 50: World Recent Past, Current & Future Analysis for Electronics & Electricals End-Use by Geographic Region - USA, Canada, Japan, China, Europe, Asia-Pacific, Latin America, Middle East and Africa Markets - Independent Analysis of Annual Sales in US$ Thousand for Years 2024 through 2030 and % CAGR
- TABLE 51: World Historic Review for Electronics & Electricals End-Use by Geographic Region - USA, Canada, Japan, China, Europe, Asia-Pacific, Latin America, Middle East and Africa Markets - Independent Analysis of Annual Sales in US$ Thousand for Years 2014 through 2023 and % CAGR
- TABLE 52: World 16-Year Perspective for Electronics & Electricals End-Use by Geographic Region - Percentage Breakdown of Value Sales for USA, Canada, Japan, China, Europe, Asia-Pacific, Latin America, Middle East and Africa for Years 2014, 2025 & 2030
- TABLE 53: World Recent Past, Current & Future Analysis for Footwear End-Use by Geographic Region - USA, Canada, Japan, China, Europe, Asia-Pacific, Latin America, Middle East and Africa Markets - Independent Analysis of Annual Sales in US$ Thousand for Years 2024 through 2030 and % CAGR
- TABLE 54: World Historic Review for Footwear End-Use by Geographic Region - USA, Canada, Japan, China, Europe, Asia-Pacific, Latin America, Middle East and Africa Markets - Independent Analysis of Annual Sales in US$ Thousand for Years 2014 through 2023 and % CAGR
- TABLE 55: World 16-Year Perspective for Footwear End-Use by Geographic Region - Percentage Breakdown of Value Sales for USA, Canada, Japan, China, Europe, Asia-Pacific, Latin America, Middle East and Africa for Years 2014, 2025 & 2030
- TABLE 56: World Recent Past, Current & Future Analysis for Other End-Uses by Geographic Region - USA, Canada, Japan, China, Europe, Asia-Pacific, Latin America, Middle East and Africa Markets - Independent Analysis of Annual Sales in US$ Thousand for Years 2024 through 2030 and % CAGR
- TABLE 57: World Historic Review for Other End-Uses by Geographic Region - USA, Canada, Japan, China, Europe, Asia-Pacific, Latin America, Middle East and Africa Markets - Independent Analysis of Annual Sales in US$ Thousand for Years 2014 through 2023 and % CAGR
- TABLE 58: World 16-Year Perspective for Other End-Uses by Geographic Region - Percentage Breakdown of Value Sales for USA, Canada, Japan, China, Europe, Asia-Pacific, Latin America, Middle East and Africa for Years 2014, 2025 & 2030
- III. MARKET ANALYSIS
- UNITED STATES
- Rubber Processing Aids and Anti-Tack Agents Market Presence - Strong/Active/Niche/Trivial - Key Competitors in the United States for 2025 (E)
- TABLE 59: USA Recent Past, Current & Future Analysis for Rubber Processing Aids and Anti-Tack Agents by Product Type - Fatty Acid Esters, Fatty Acid Amides, Stearates, Soaps, Silicone Polymers and Other Rubber Processing Aids & Anti-Tack Agents - Independent Analysis of Annual Sales in US$ Thousand for the Years 2024 through 2030 and % CAGR
- TABLE 60: USA Historic Review for Rubber Processing Aids and Anti-Tack Agents by Product Type - Fatty Acid Esters, Fatty Acid Amides, Stearates, Soaps, Silicone Polymers and Other Rubber Processing Aids & Anti-Tack Agents Markets - Independent Analysis of Annual Sales in US$ Thousand for Years 2014 through 2023 and % CAGR
- TABLE 61: USA 16-Year Perspective for Rubber Processing Aids and Anti-Tack Agents by Product Type - Percentage Breakdown of Value Sales for Fatty Acid Esters, Fatty Acid Amides, Stearates, Soaps, Silicone Polymers and Other Rubber Processing Aids & Anti-Tack Agents for the Years 2014, 2025 & 2030
- TABLE 62: USA Recent Past, Current & Future Analysis for Rubber Processing Aids and Anti-Tack Agents by Application - Molded Rubber Products Application, Medical Gloves Application, Other Applications, Tires & Tubes Application, Gaskets & Seals Application and Wires & Cables Application - Independent Analysis of Annual Sales in US$ Thousand for the Years 2024 through 2030 and % CAGR
- TABLE 63: USA Historic Review for Rubber Processing Aids and Anti-Tack Agents by Application - Molded Rubber Products Application, Medical Gloves Application, Other Applications, Tires & Tubes Application, Gaskets & Seals Application and Wires & Cables Application Markets - Independent Analysis of Annual Sales in US$ Thousand for Years 2014 through 2023 and % CAGR
- TABLE 64: USA 16-Year Perspective for Rubber Processing Aids and Anti-Tack Agents by Application - Percentage Breakdown of Value Sales for Molded Rubber Products Application, Medical Gloves Application, Other Applications, Tires & Tubes Application, Gaskets & Seals Application and Wires & Cables Application for the Years 2014, 2025 & 2030
- TABLE 65: USA Recent Past, Current & Future Analysis for Rubber Processing Aids and Anti-Tack Agents by End-Use - Automotive & Transportation End-Use, Building & Construction End-Use, Medical End-Use, Electronics & Electricals End-Use, Footwear End-Use and Other End-Uses - Independent Analysis of Annual Sales in US$ Thousand for the Years 2024 through 2030 and % CAGR
- TABLE 66: USA Historic Review for Rubber Processing Aids and Anti-Tack Agents by End-Use - Automotive & Transportation End-Use, Building & Construction End-Use, Medical End-Use, Electronics & Electricals End-Use, Footwear End-Use and Other End-Uses Markets - Independent Analysis of Annual Sales in US$ Thousand for Years 2014 through 2023 and % CAGR
- TABLE 67: USA 16-Year Perspective for Rubber Processing Aids and Anti-Tack Agents by End-Use - Percentage Breakdown of Value Sales for Automotive & Transportation End-Use, Building & Construction End-Use, Medical End-Use, Electronics & Electricals End-Use, Footwear End-Use and Other End-Uses for the Years 2014, 2025 & 2030
- CANADA
- TABLE 68: Canada Recent Past, Current & Future Analysis for Rubber Processing Aids and Anti-Tack Agents by Product Type - Fatty Acid Esters, Fatty Acid Amides, Stearates, Soaps, Silicone Polymers and Other Rubber Processing Aids & Anti-Tack Agents - Independent Analysis of Annual Sales in US$ Thousand for the Years 2024 through 2030 and % CAGR
- TABLE 69: Canada Historic Review for Rubber Processing Aids and Anti-Tack Agents by Product Type - Fatty Acid Esters, Fatty Acid Amides, Stearates, Soaps, Silicone Polymers and Other Rubber Processing Aids & Anti-Tack Agents Markets - Independent Analysis of Annual Sales in US$ Thousand for Years 2014 through 2023 and % CAGR
- TABLE 70: Canada 16-Year Perspective for Rubber Processing Aids and Anti-Tack Agents by Product Type - Percentage Breakdown of Value Sales for Fatty Acid Esters, Fatty Acid Amides, Stearates, Soaps, Silicone Polymers and Other Rubber Processing Aids & Anti-Tack Agents for the Years 2014, 2025 & 2030
- TABLE 71: Canada Recent Past, Current & Future Analysis for Rubber Processing Aids and Anti-Tack Agents by Application - Molded Rubber Products Application, Medical Gloves Application, Other Applications, Tires & Tubes Application, Gaskets & Seals Application and Wires & Cables Application - Independent Analysis of Annual Sales in US$ Thousand for the Years 2024 through 2030 and % CAGR
- TABLE 72: Canada Historic Review for Rubber Processing Aids and Anti-Tack Agents by Application - Molded Rubber Products Application, Medical Gloves Application, Other Applications, Tires & Tubes Application, Gaskets & Seals Application and Wires & Cables Application Markets - Independent Analysis of Annual Sales in US$ Thousand for Years 2014 through 2023 and % CAGR
- TABLE 73: Canada 16-Year Perspective for Rubber Processing Aids and Anti-Tack Agents by Application - Percentage Breakdown of Value Sales for Molded Rubber Products Application, Medical Gloves Application, Other Applications, Tires & Tubes Application, Gaskets & Seals Application and Wires & Cables Application for the Years 2014, 2025 & 2030
- TABLE 74: Canada Recent Past, Current & Future Analysis for Rubber Processing Aids and Anti-Tack Agents by End-Use - Automotive & Transportation End-Use, Building & Construction End-Use, Medical End-Use, Electronics & Electricals End-Use, Footwear End-Use and Other End-Uses - Independent Analysis of Annual Sales in US$ Thousand for the Years 2024 through 2030 and % CAGR
- TABLE 75: Canada Historic Review for Rubber Processing Aids and Anti-Tack Agents by End-Use - Automotive & Transportation End-Use, Building & Construction End-Use, Medical End-Use, Electronics & Electricals End-Use, Footwear End-Use and Other End-Uses Markets - Independent Analysis of Annual Sales in US$ Thousand for Years 2014 through 2023 and % CAGR
- TABLE 76: Canada 16-Year Perspective for Rubber Processing Aids and Anti-Tack Agents by End-Use - Percentage Breakdown of Value Sales for Automotive & Transportation End-Use, Building & Construction End-Use, Medical End-Use, Electronics & Electricals End-Use, Footwear End-Use and Other End-Uses for the Years 2014, 2025 & 2030
- JAPAN
- Rubber Processing Aids and Anti-Tack Agents Market Presence - Strong/Active/Niche/Trivial - Key Competitors in Japan for 2025 (E)
- TABLE 77: Japan Recent Past, Current & Future Analysis for Rubber Processing Aids and Anti-Tack Agents by Product Type - Fatty Acid Esters, Fatty Acid Amides, Stearates, Soaps, Silicone Polymers and Other Rubber Processing Aids & Anti-Tack Agents - Independent Analysis of Annual Sales in US$ Thousand for the Years 2024 through 2030 and % CAGR
- TABLE 78: Japan Historic Review for Rubber Processing Aids and Anti-Tack Agents by Product Type - Fatty Acid Esters, Fatty Acid Amides, Stearates, Soaps, Silicone Polymers and Other Rubber Processing Aids & Anti-Tack Agents Markets - Independent Analysis of Annual Sales in US$ Thousand for Years 2014 through 2023 and % CAGR
- TABLE 79: Japan 16-Year Perspective for Rubber Processing Aids and Anti-Tack Agents by Product Type - Percentage Breakdown of Value Sales for Fatty Acid Esters, Fatty Acid Amides, Stearates, Soaps, Silicone Polymers and Other Rubber Processing Aids & Anti-Tack Agents for the Years 2014, 2025 & 2030
- TABLE 80: Japan Recent Past, Current & Future Analysis for Rubber Processing Aids and Anti-Tack Agents by Application - Molded Rubber Products Application, Medical Gloves Application, Other Applications, Tires & Tubes Application, Gaskets & Seals Application and Wires & Cables Application - Independent Analysis of Annual Sales in US$ Thousand for the Years 2024 through 2030 and % CAGR
- TABLE 81: Japan Historic Review for Rubber Processing Aids and Anti-Tack Agents by Application - Molded Rubber Products Application, Medical Gloves Application, Other Applications, Tires & Tubes Application, Gaskets & Seals Application and Wires & Cables Application Markets - Independent Analysis of Annual Sales in US$ Thousand for Years 2014 through 2023 and % CAGR
- TABLE 82: Japan 16-Year Perspective for Rubber Processing Aids and Anti-Tack Agents by Application - Percentage Breakdown of Value Sales for Molded Rubber Products Application, Medical Gloves Application, Other Applications, Tires & Tubes Application, Gaskets & Seals Application and Wires & Cables Application for the Years 2014, 2025 & 2030
- TABLE 83: Japan Recent Past, Current & Future Analysis for Rubber Processing Aids and Anti-Tack Agents by End-Use - Automotive & Transportation End-Use, Building & Construction End-Use, Medical End-Use, Electronics & Electricals End-Use, Footwear End-Use and Other End-Uses - Independent Analysis of Annual Sales in US$ Thousand for the Years 2024 through 2030 and % CAGR
- TABLE 84: Japan Historic Review for Rubber Processing Aids and Anti-Tack Agents by End-Use - Automotive & Transportation End-Use, Building & Construction End-Use, Medical End-Use, Electronics & Electricals End-Use, Footwear End-Use and Other End-Uses Markets - Independent Analysis of Annual Sales in US$ Thousand for Years 2014 through 2023 and % CAGR
- TABLE 85: Japan 16-Year Perspective for Rubber Processing Aids and Anti-Tack Agents by End-Use - Percentage Breakdown of Value Sales for Automotive & Transportation End-Use, Building & Construction End-Use, Medical End-Use, Electronics & Electricals End-Use, Footwear End-Use and Other End-Uses for the Years 2014, 2025 & 2030
- CHINA
- Rubber Processing Aids and Anti-Tack Agents Market Presence - Strong/Active/Niche/Trivial - Key Competitors in China for 2025 (E)
- TABLE 86: China Recent Past, Current & Future Analysis for Rubber Processing Aids and Anti-Tack Agents by Product Type - Fatty Acid Esters, Fatty Acid Amides, Stearates, Soaps, Silicone Polymers and Other Rubber Processing Aids & Anti-Tack Agents - Independent Analysis of Annual Sales in US$ Thousand for the Years 2024 through 2030 and % CAGR
- TABLE 87: China Historic Review for Rubber Processing Aids and Anti-Tack Agents by Product Type - Fatty Acid Esters, Fatty Acid Amides, Stearates, Soaps, Silicone Polymers and Other Rubber Processing Aids & Anti-Tack Agents Markets - Independent Analysis of Annual Sales in US$ Thousand for Years 2014 through 2023 and % CAGR
- TABLE 88: China 16-Year Perspective for Rubber Processing Aids and Anti-Tack Agents by Product Type - Percentage Breakdown of Value Sales for Fatty Acid Esters, Fatty Acid Amides, Stearates, Soaps, Silicone Polymers and Other Rubber Processing Aids & Anti-Tack Agents for the Years 2014, 2025 & 2030
- TABLE 89: China Recent Past, Current & Future Analysis for Rubber Processing Aids and Anti-Tack Agents by Application - Molded Rubber Products Application, Medical Gloves Application, Other Applications, Tires & Tubes Application, Gaskets & Seals Application and Wires & Cables Application - Independent Analysis of Annual Sales in US$ Thousand for the Years 2024 through 2030 and % CAGR
- TABLE 90: China Historic Review for Rubber Processing Aids and Anti-Tack Agents by Application - Molded Rubber Products Application, Medical Gloves Application, Other Applications, Tires & Tubes Application, Gaskets & Seals Application and Wires & Cables Application Markets - Independent Analysis of Annual Sales in US$ Thousand for Years 2014 through 2023 and % CAGR
- TABLE 91: China 16-Year Perspective for Rubber Processing Aids and Anti-Tack Agents by Application - Percentage Breakdown of Value Sales for Molded Rubber Products Application, Medical Gloves Application, Other Applications, Tires & Tubes Application, Gaskets & Seals Application and Wires & Cables Application for the Years 2014, 2025 & 2030
- TABLE 92: China Recent Past, Current & Future Analysis for Rubber Processing Aids and Anti-Tack Agents by End-Use - Automotive & Transportation End-Use, Building & Construction End-Use, Medical End-Use, Electronics & Electricals End-Use, Footwear End-Use and Other End-Uses - Independent Analysis of Annual Sales in US$ Thousand for the Years 2024 through 2030 and % CAGR
- TABLE 93: China Historic Review for Rubber Processing Aids and Anti-Tack Agents by End-Use - Automotive & Transportation End-Use, Building & Construction End-Use, Medical End-Use, Electronics & Electricals End-Use, Footwear End-Use and Other End-Uses Markets - Independent Analysis of Annual Sales in US$ Thousand for Years 2014 through 2023 and % CAGR
- TABLE 94: China 16-Year Perspective for Rubber Processing Aids and Anti-Tack Agents by End-Use - Percentage Breakdown of Value Sales for Automotive & Transportation End-Use, Building & Construction End-Use, Medical End-Use, Electronics & Electricals End-Use, Footwear End-Use and Other End-Uses for the Years 2014, 2025 & 2030
- EUROPE
- Rubber Processing Aids and Anti-Tack Agents Market Presence - Strong/Active/Niche/Trivial - Key Competitors in Europe for 2025 (E)
- TABLE 95: Europe Recent Past, Current & Future Analysis for Rubber Processing Aids and Anti-Tack Agents by Geographic Region - France, Germany, Italy, UK, Spain, Russia and Rest of Europe Markets - Independent Analysis of Annual Sales in US$ Thousand for Years 2024 through 2030 and % CAGR
- TABLE 96: Europe Historic Review for Rubber Processing Aids and Anti-Tack Agents by Geographic Region - France, Germany, Italy, UK, Spain, Russia and Rest of Europe Markets - Independent Analysis of Annual Sales in US$ Thousand for Years 2014 through 2023 and % CAGR
- TABLE 97: Europe 16-Year Perspective for Rubber Processing Aids and Anti-Tack Agents by Geographic Region - Percentage Breakdown of Value Sales for France, Germany, Italy, UK, Spain, Russia and Rest of Europe Markets for Years 2014, 2025 & 2030
- TABLE 98: Europe Recent Past, Current & Future Analysis for Rubber Processing Aids and Anti-Tack Agents by Product Type - Fatty Acid Esters, Fatty Acid Amides, Stearates, Soaps, Silicone Polymers and Other Rubber Processing Aids & Anti-Tack Agents - Independent Analysis of Annual Sales in US$ Thousand for the Years 2024 through 2030 and % CAGR
- TABLE 99: Europe Historic Review for Rubber Processing Aids and Anti-Tack Agents by Product Type - Fatty Acid Esters, Fatty Acid Amides, Stearates, Soaps, Silicone Polymers and Other Rubber Processing Aids & Anti-Tack Agents Markets - Independent Analysis of Annual Sales in US$ Thousand for Years 2014 through 2023 and % CAGR
- TABLE 100: Europe 16-Year Perspective for Rubber Processing Aids and Anti-Tack Agents by Product Type - Percentage Breakdown of Value Sales for Fatty Acid Esters, Fatty Acid Amides, Stearates, Soaps, Silicone Polymers and Other Rubber Processing Aids & Anti-Tack Agents for the Years 2014, 2025 & 2030
- TABLE 101: Europe Recent Past, Current & Future Analysis for Rubber Processing Aids and Anti-Tack Agents by Application - Molded Rubber Products Application, Medical Gloves Application, Other Applications, Tires & Tubes Application, Gaskets & Seals Application and Wires & Cables Application - Independent Analysis of Annual Sales in US$ Thousand for the Years 2024 through 2030 and % CAGR
- TABLE 102: Europe Historic Review for Rubber Processing Aids and Anti-Tack Agents by Application - Molded Rubber Products Application, Medical Gloves Application, Other Applications, Tires & Tubes Application, Gaskets & Seals Application and Wires & Cables Application Markets - Independent Analysis of Annual Sales in US$ Thousand for Years 2014 through 2023 and % CAGR
- TABLE 103: Europe 16-Year Perspective for Rubber Processing Aids and Anti-Tack Agents by Application - Percentage Breakdown of Value Sales for Molded Rubber Products Application, Medical Gloves Application, Other Applications, Tires & Tubes Application, Gaskets & Seals Application and Wires & Cables Application for the Years 2014, 2025 & 2030
- TABLE 104: Europe Recent Past, Current & Future Analysis for Rubber Processing Aids and Anti-Tack Agents by End-Use - Automotive & Transportation End-Use, Building & Construction End-Use, Medical End-Use, Electronics & Electricals End-Use, Footwear End-Use and Other End-Uses - Independent Analysis of Annual Sales in US$ Thousand for the Years 2024 through 2030 and % CAGR
- TABLE 105: Europe Historic Review for Rubber Processing Aids and Anti-Tack Agents by End-Use - Automotive & Transportation End-Use, Building & Construction End-Use, Medical End-Use, Electronics & Electricals End-Use, Footwear End-Use and Other End-Uses Markets - Independent Analysis of Annual Sales in US$ Thousand for Years 2014 through 2023 and % CAGR
- TABLE 106: Europe 16-Year Perspective for Rubber Processing Aids and Anti-Tack Agents by End-Use - Percentage Breakdown of Value Sales for Automotive & Transportation End-Use, Building & Construction End-Use, Medical End-Use, Electronics & Electricals End-Use, Footwear End-Use and Other End-Uses for the Years 2014, 2025 & 2030
- FRANCE
- Rubber Processing Aids and Anti-Tack Agents Market Presence - Strong/Active/Niche/Trivial - Key Competitors in France for 2025 (E)
- TABLE 107: France Recent Past, Current & Future Analysis for Rubber Processing Aids and Anti-Tack Agents by Product Type - Fatty Acid Esters, Fatty Acid Amides, Stearates, Soaps, Silicone Polymers and Other Rubber Processing Aids & Anti-Tack Agents - Independent Analysis of Annual Sales in US$ Thousand for the Years 2024 through 2030 and % CAGR
- TABLE 108: France Historic Review for Rubber Processing Aids and Anti-Tack Agents by Product Type - Fatty Acid Esters, Fatty Acid Amides, Stearates, Soaps, Silicone Polymers and Other Rubber Processing Aids & Anti-Tack Agents Markets - Independent Analysis of Annual Sales in US$ Thousand for Years 2014 through 2023 and % CAGR
- TABLE 109: France 16-Year Perspective for Rubber Processing Aids and Anti-Tack Agents by Product Type - Percentage Breakdown of Value Sales for Fatty Acid Esters, Fatty Acid Amides, Stearates, Soaps, Silicone Polymers and Other Rubber Processing Aids & Anti-Tack Agents for the Years 2014, 2025 & 2030
- TABLE 110: France Recent Past, Current & Future Analysis for Rubber Processing Aids and Anti-Tack Agents by Application - Molded Rubber Products Application, Medical Gloves Application, Other Applications, Tires & Tubes Application, Gaskets & Seals Application and Wires & Cables Application - Independent Analysis of Annual Sales in US$ Thousand for the Years 2024 through 2030 and % CAGR
- TABLE 111: France Historic Review for Rubber Processing Aids and Anti-Tack Agents by Application - Molded Rubber Products Application, Medical Gloves Application, Other Applications, Tires & Tubes Application, Gaskets & Seals Application and Wires & Cables Application Markets - Independent Analysis of Annual Sales in US$ Thousand for Years 2014 through 2023 and % CAGR
- TABLE 112: France 16-Year Perspective for Rubber Processing Aids and Anti-Tack Agents by Application - Percentage Breakdown of Value Sales for Molded Rubber Products Application, Medical Gloves Application, Other Applications, Tires & Tubes Application, Gaskets & Seals Application and Wires & Cables Application for the Years 2014, 2025 & 2030
- TABLE 113: France Recent Past, Current & Future Analysis for Rubber Processing Aids and Anti-Tack Agents by End-Use - Automotive & Transportation End-Use, Building & Construction End-Use, Medical End-Use, Electronics & Electricals End-Use, Footwear End-Use and Other End-Uses - Independent Analysis of Annual Sales in US$ Thousand for the Years 2024 through 2030 and % CAGR
- TABLE 114: France Historic Review for Rubber Processing Aids and Anti-Tack Agents by End-Use - Automotive & Transportation End-Use, Building & Construction End-Use, Medical End-Use, Electronics & Electricals End-Use, Footwear End-Use and Other End-Uses Markets - Independent Analysis of Annual Sales in US$ Thousand for Years 2014 through 2023 and % CAGR
- TABLE 115: France 16-Year Perspective for Rubber Processing Aids and Anti-Tack Agents by End-Use - Percentage Breakdown of Value Sales for Automotive & Transportation End-Use, Building & Construction End-Use, Medical End-Use, Electronics & Electricals End-Use, Footwear End-Use and Other End-Uses for the Years 2014, 2025 & 2030
- GERMANY
- Rubber Processing Aids and Anti-Tack Agents Market Presence - Strong/Active/Niche/Trivial - Key Competitors in Germany for 2025 (E)
- TABLE 116: Germany Recent Past, Current & Future Analysis for Rubber Processing Aids and Anti-Tack Agents by Product Type - Fatty Acid Esters, Fatty Acid Amides, Stearates, Soaps, Silicone Polymers and Other Rubber Processing Aids & Anti-Tack Agents - Independent Analysis of Annual Sales in US$ Thousand for the Years 2024 through 2030 and % CAGR
- TABLE 117: Germany Historic Review for Rubber Processing Aids and Anti-Tack Agents by Product Type - Fatty Acid Esters, Fatty Acid Amides, Stearates, Soaps, Silicone Polymers and Other Rubber Processing Aids & Anti-Tack Agents Markets - Independent Analysis of Annual Sales in US$ Thousand for Years 2014 through 2023 and % CAGR
- TABLE 118: Germany 16-Year Perspective for Rubber Processing Aids and Anti-Tack Agents by Product Type - Percentage Breakdown of Value Sales for Fatty Acid Esters, Fatty Acid Amides, Stearates, Soaps, Silicone Polymers and Other Rubber Processing Aids & Anti-Tack Agents for the Years 2014, 2025 & 2030
- TABLE 119: Germany Recent Past, Current & Future Analysis for Rubber Processing Aids and Anti-Tack Agents by Application - Molded Rubber Products Application, Medical Gloves Application, Other Applications, Tires & Tubes Application, Gaskets & Seals Application and Wires & Cables Application - Independent Analysis of Annual Sales in US$ Thousand for the Years 2024 through 2030 and % CAGR
- TABLE 120: Germany Historic Review for Rubber Processing Aids and Anti-Tack Agents by Application - Molded Rubber Products Application, Medical Gloves Application, Other Applications, Tires & Tubes Application, Gaskets & Seals Application and Wires & Cables Application Markets - Independent Analysis of Annual Sales in US$ Thousand for Years 2014 through 2023 and % CAGR
- TABLE 121: Germany 16-Year Perspective for Rubber Processing Aids and Anti-Tack Agents by Application - Percentage Breakdown of Value Sales for Molded Rubber Products Application, Medical Gloves Application, Other Applications, Tires & Tubes Application, Gaskets & Seals Application and Wires & Cables Application for the Years 2014, 2025 & 2030
- TABLE 122: Germany Recent Past, Current & Future Analysis for Rubber Processing Aids and Anti-Tack Agents by End-Use - Automotive & Transportation End-Use, Building & Construction End-Use, Medical End-Use, Electronics & Electricals End-Use, Footwear End-Use and Other End-Uses - Independent Analysis of Annual Sales in US$ Thousand for the Years 2024 through 2030 and % CAGR
- TABLE 123: Germany Historic Review for Rubber Processing Aids and Anti-Tack Agents by End-Use - Automotive & Transportation End-Use, Building & Construction End-Use, Medical End-Use, Electronics & Electricals End-Use, Footwear End-Use and Other End-Uses Markets - Independent Analysis of Annual Sales in US$ Thousand for Years 2014 through 2023 and % CAGR
- TABLE 124: Germany 16-Year Perspective for Rubber Processing Aids and Anti-Tack Agents by End-Use - Percentage Breakdown of Value Sales for Automotive & Transportation End-Use, Building & Construction End-Use, Medical End-Use, Electronics & Electricals End-Use, Footwear End-Use and Other End-Uses for the Years 2014, 2025 & 2030
- ITALY
- TABLE 125: Italy Recent Past, Current & Future Analysis for Rubber Processing Aids and Anti-Tack Agents by Product Type - Fatty Acid Esters, Fatty Acid Amides, Stearates, Soaps, Silicone Polymers and Other Rubber Processing Aids & Anti-Tack Agents - Independent Analysis of Annual Sales in US$ Thousand for the Years 2024 through 2030 and % CAGR
- TABLE 126: Italy Historic Review for Rubber Processing Aids and Anti-Tack Agents by Product Type - Fatty Acid Esters, Fatty Acid Amides, Stearates, Soaps, Silicone Polymers and Other Rubber Processing Aids & Anti-Tack Agents Markets - Independent Analysis of Annual Sales in US$ Thousand for Years 2014 through 2023 and % CAGR
- TABLE 127: Italy 16-Year Perspective for Rubber Processing Aids and Anti-Tack Agents by Product Type - Percentage Breakdown of Value Sales for Fatty Acid Esters, Fatty Acid Amides, Stearates, Soaps, Silicone Polymers and Other Rubber Processing Aids & Anti-Tack Agents for the Years 2014, 2025 & 2030
- TABLE 128: Italy Recent Past, Current & Future Analysis for Rubber Processing Aids and Anti-Tack Agents by Application - Molded Rubber Products Application, Medical Gloves Application, Other Applications, Tires & Tubes Application, Gaskets & Seals Application and Wires & Cables Application - Independent Analysis of Annual Sales in US$ Thousand for the Years 2024 through 2030 and % CAGR
- TABLE 129: Italy Historic Review for Rubber Processing Aids and Anti-Tack Agents by Application - Molded Rubber Products Application, Medical Gloves Application, Other Applications, Tires & Tubes Application, Gaskets & Seals Application and Wires & Cables Application Markets - Independent Analysis of Annual Sales in US$ Thousand for Years 2014 through 2023 and % CAGR
- TABLE 130: Italy 16-Year Perspective for Rubber Processing Aids and Anti-Tack Agents by Application - Percentage Breakdown of Value Sales for Molded Rubber Products Application, Medical Gloves Application, Other Applications, Tires & Tubes Application, Gaskets & Seals Application and Wires & Cables Application for the Years 2014, 2025 & 2030
- TABLE 131: Italy Recent Past, Current & Future Analysis for Rubber Processing Aids and Anti-Tack Agents by End-Use - Automotive & Transportation End-Use, Building & Construction End-Use, Medical End-Use, Electronics & Electricals End-Use, Footwear End-Use and Other End-Uses - Independent Analysis of Annual Sales in US$ Thousand for the Years 2024 through 2030 and % CAGR
- TABLE 132: Italy Historic Review for Rubber Processing Aids and Anti-Tack Agents by End-Use - Automotive & Transportation End-Use, Building & Construction End-Use, Medical End-Use, Electronics & Electricals End-Use, Footwear End-Use and Other End-Uses Markets - Independent Analysis of Annual Sales in US$ Thousand for Years 2014 through 2023 and % CAGR
- TABLE 133: Italy 16-Year Perspective for Rubber Processing Aids and Anti-Tack Agents by End-Use - Percentage Breakdown of Value Sales for Automotive & Transportation End-Use, Building & Construction End-Use, Medical End-Use, Electronics & Electricals End-Use, Footwear End-Use and Other End-Uses for the Years 2014, 2025 & 2030
- UNITED KINGDOM
- Rubber Processing Aids and Anti-Tack Agents Market Presence - Strong/Active/Niche/Trivial - Key Competitors in the United Kingdom for 2025 (E)
- TABLE 134: UK Recent Past, Current & Future Analysis for Rubber Processing Aids and Anti-Tack Agents by Product Type - Fatty Acid Esters, Fatty Acid Amides, Stearates, Soaps, Silicone Polymers and Other Rubber Processing Aids & Anti-Tack Agents - Independent Analysis of Annual Sales in US$ Thousand for the Years 2024 through 2030 and % CAGR
- TABLE 135: UK Historic Review for Rubber Processing Aids and Anti-Tack Agents by Product Type - Fatty Acid Esters, Fatty Acid Amides, Stearates, Soaps, Silicone Polymers and Other Rubber Processing Aids & Anti-Tack Agents Markets - Independent Analysis of Annual Sales in US$ Thousand for Years 2014 through 2023 and % CAGR
- TABLE 136: UK 16-Year Perspective for Rubber Processing Aids and Anti-Tack Agents by Product Type - Percentage Breakdown of Value Sales for Fatty Acid Esters, Fatty Acid Amides, Stearates, Soaps, Silicone Polymers and Other Rubber Processing Aids & Anti-Tack Agents for the Years 2014, 2025 & 2030
- TABLE 137: UK Recent Past, Current & Future Analysis for Rubber Processing Aids and Anti-Tack Agents by Application - Molded Rubber Products Application, Medical Gloves Application, Other Applications, Tires & Tubes Application, Gaskets & Seals Application and Wires & Cables Application - Independent Analysis of Annual Sales in US$ Thousand for the Years 2024 through 2030 and % CAGR
- TABLE 138: UK Historic Review for Rubber Processing Aids and Anti-Tack Agents by Application - Molded Rubber Products Application, Medical Gloves Application, Other Applications, Tires & Tubes Application, Gaskets & Seals Application and Wires & Cables Application Markets - Independent Analysis of Annual Sales in US$ Thousand for Years 2014 through 2023 and % CAGR
- TABLE 139: UK 16-Year Perspective for Rubber Processing Aids and Anti-Tack Agents by Application - Percentage Breakdown of Value Sales for Molded Rubber Products Application, Medical Gloves Application, Other Applications, Tires & Tubes Application, Gaskets & Seals Application and Wires & Cables Application for the Years 2014, 2025 & 2030
- TABLE 140: UK Recent Past, Current & Future Analysis for Rubber Processing Aids and Anti-Tack Agents by End-Use - Automotive & Transportation End-Use, Building & Construction End-Use, Medical End-Use, Electronics & Electricals End-Use, Footwear End-Use and Other End-Uses - Independent Analysis of Annual Sales in US$ Thousand for the Years 2024 through 2030 and % CAGR
- TABLE 141: UK Historic Review for Rubber Processing Aids and Anti-Tack Agents by End-Use - Automotive & Transportation End-Use, Building & Construction End-Use, Medical End-Use, Electronics & Electricals End-Use, Footwear End-Use and Other End-Uses Markets - Independent Analysis of Annual Sales in US$ Thousand for Years 2014 through 2023 and % CAGR
- TABLE 142: UK 16-Year Perspective for Rubber Processing Aids and Anti-Tack Agents by End-Use - Percentage Breakdown of Value Sales for Automotive & Transportation End-Use, Building & Construction End-Use, Medical End-Use, Electronics & Electricals End-Use, Footwear End-Use and Other End-Uses for the Years 2014, 2025 & 2030
- SPAIN
- TABLE 143: Spain Recent Past, Current & Future Analysis for Rubber Processing Aids and Anti-Tack Agents by Product Type - Fatty Acid Esters, Fatty Acid Amides, Stearates, Soaps, Silicone Polymers and Other Rubber Processing Aids & Anti-Tack Agents - Independent Analysis of Annual Sales in US$ Thousand for the Years 2024 through 2030 and % CAGR
- TABLE 144: Spain Historic Review for Rubber Processing Aids and Anti-Tack Agents by Product Type - Fatty Acid Esters, Fatty Acid Amides, Stearates, Soaps, Silicone Polymers and Other Rubber Processing Aids & Anti-Tack Agents Markets - Independent Analysis of Annual Sales in US$ Thousand for Years 2014 through 2023 and % CAGR
- TABLE 145: Spain 16-Year Perspective for Rubber Processing Aids and Anti-Tack Agents by Product Type - Percentage Breakdown of Value Sales for Fatty Acid Esters, Fatty Acid Amides, Stearates, Soaps, Silicone Polymers and Other Rubber Processing Aids & Anti-Tack Agents for the Years 2014, 2025 & 2030
- TABLE 146: Spain Recent Past, Current & Future Analysis for Rubber Processing Aids and Anti-Tack Agents by Application - Molded Rubber Products Application, Medical Gloves Application, Other Applications, Tires & Tubes Application, Gaskets & Seals Application and Wires & Cables Application - Independent Analysis of Annual Sales in US$ Thousand for the Years 2024 through 2030 and % CAGR
- TABLE 147: Spain Historic Review for Rubber Processing Aids and Anti-Tack Agents by Application - Molded Rubber Products Application, Medical Gloves Application, Other Applications, Tires & Tubes Application, Gaskets & Seals Application and Wires & Cables Application Markets - Independent Analysis of Annual Sales in US$ Thousand for Years 2014 through 2023 and % CAGR
- TABLE 148: Spain 16-Year Perspective for Rubber Processing Aids and Anti-Tack Agents by Application - Percentage Breakdown of Value Sales for Molded Rubber Products Application, Medical Gloves Application, Other Applications, Tires & Tubes Application, Gaskets & Seals Application and Wires & Cables Application for the Years 2014, 2025 & 2030
- TABLE 149: Spain Recent Past, Current & Future Analysis for Rubber Processing Aids and Anti-Tack Agents by End-Use - Automotive & Transportation End-Use, Building & Construction End-Use, Medical End-Use, Electronics & Electricals End-Use, Footwear End-Use and Other End-Uses - Independent Analysis of Annual Sales in US$ Thousand for the Years 2024 through 2030 and % CAGR
- TABLE 150: Spain Historic Review for Rubber Processing Aids and Anti-Tack Agents by End-Use - Automotive & Transportation End-Use, Building & Construction End-Use, Medical End-Use, Electronics & Electricals End-Use, Footwear End-Use and Other End-Uses Markets - Independent Analysis of Annual Sales in US$ Thousand for Years 2014 through 2023 and % CAGR
- TABLE 151: Spain 16-Year Perspective for Rubber Processing Aids and Anti-Tack Agents by End-Use - Percentage Breakdown of Value Sales for Automotive & Transportation End-Use, Building & Construction End-Use, Medical End-Use, Electronics & Electricals End-Use, Footwear End-Use and Other End-Uses for the Years 2014, 2025 & 2030
- RUSSIA
- TABLE 152: Russia Recent Past, Current & Future Analysis for Rubber Processing Aids and Anti-Tack Agents by Product Type - Fatty Acid Esters, Fatty Acid Amides, Stearates, Soaps, Silicone Polymers and Other Rubber Processing Aids & Anti-Tack Agents - Independent Analysis of Annual Sales in US$ Thousand for the Years 2024 through 2030 and % CAGR
- TABLE 153: Russia Historic Review for Rubber Processing Aids and Anti-Tack Agents by Product Type - Fatty Acid Esters, Fatty Acid Amides, Stearates, Soaps, Silicone Polymers and Other Rubber Processing Aids & Anti-Tack Agents Markets - Independent Analysis of Annual Sales in US$ Thousand for Years 2014 through 2023 and % CAGR
- TABLE 154: Russia 16-Year Perspective for Rubber Processing Aids and Anti-Tack Agents by Product Type - Percentage Breakdown of Value Sales for Fatty Acid Esters, Fatty Acid Amides, Stearates, Soaps, Silicone Polymers and Other Rubber Processing Aids & Anti-Tack Agents for the Years 2014, 2025 & 2030
- TABLE 155: Russia Recent Past, Current & Future Analysis for Rubber Processing Aids and Anti-Tack Agents by Application - Molded Rubber Products Application, Medical Gloves Application, Other Applications, Tires & Tubes Application, Gaskets & Seals Application and Wires & Cables Application - Independent Analysis of Annual Sales in US$ Thousand for the Years 2024 through 2030 and % CAGR
- TABLE 156: Russia Historic Review for Rubber Processing Aids and Anti-Tack Agents by Application - Molded Rubber Products Application, Medical Gloves Application, Other Applications, Tires & Tubes Application, Gaskets & Seals Application and Wires & Cables Application Markets - Independent Analysis of Annual Sales in US$ Thousand for Years 2014 through 2023 and % CAGR
- TABLE 157: Russia 16-Year Perspective for Rubber Processing Aids and Anti-Tack Agents by Application - Percentage Breakdown of Value Sales for Molded Rubber Products Application, Medical Gloves Application, Other Applications, Tires & Tubes Application, Gaskets & Seals Application and Wires & Cables Application for the Years 2014, 2025 & 2030
- TABLE 158: Russia Recent Past, Current & Future Analysis for Rubber Processing Aids and Anti-Tack Agents by End-Use - Automotive & Transportation End-Use, Building & Construction End-Use, Medical End-Use, Electronics & Electricals End-Use, Footwear End-Use and Other End-Uses - Independent Analysis of Annual Sales in US$ Thousand for the Years 2024 through 2030 and % CAGR
- TABLE 159: Russia Historic Review for Rubber Processing Aids and Anti-Tack Agents by End-Use - Automotive & Transportation End-Use, Building & Construction End-Use, Medical End-Use, Electronics & Electricals End-Use, Footwear End-Use and Other End-Uses Markets - Independent Analysis of Annual Sales in US$ Thousand for Years 2014 through 2023 and % CAGR
- TABLE 160: Russia 16-Year Perspective for Rubber Processing Aids and Anti-Tack Agents by End-Use - Percentage Breakdown of Value Sales for Automotive & Transportation End-Use, Building & Construction End-Use, Medical End-Use, Electronics & Electricals End-Use, Footwear End-Use and Other End-Uses for the Years 2014, 2025 & 2030
- REST OF EUROPE
- TABLE 161: Rest of Europe Recent Past, Current & Future Analysis for Rubber Processing Aids and Anti-Tack Agents by Product Type - Fatty Acid Esters, Fatty Acid Amides, Stearates, Soaps, Silicone Polymers and Other Rubber Processing Aids & Anti-Tack Agents - Independent Analysis of Annual Sales in US$ Thousand for the Years 2024 through 2030 and % CAGR
- TABLE 162: Rest of Europe Historic Review for Rubber Processing Aids and Anti-Tack Agents by Product Type - Fatty Acid Esters, Fatty Acid Amides, Stearates, Soaps, Silicone Polymers and Other Rubber Processing Aids & Anti-Tack Agents Markets - Independent Analysis of Annual Sales in US$ Thousand for Years 2014 through 2023 and % CAGR
- TABLE 163: Rest of Europe 16-Year Perspective for Rubber Processing Aids and Anti-Tack Agents by Product Type - Percentage Breakdown of Value Sales for Fatty Acid Esters, Fatty Acid Amides, Stearates, Soaps, Silicone Polymers and Other Rubber Processing Aids & Anti-Tack Agents for the Years 2014, 2025 & 2030
- TABLE 164: Rest of Europe Recent Past, Current & Future Analysis for Rubber Processing Aids and Anti-Tack Agents by Application - Molded Rubber Products Application, Medical Gloves Application, Other Applications, Tires & Tubes Application, Gaskets & Seals Application and Wires & Cables Application - Independent Analysis of Annual Sales in US$ Thousand for the Years 2024 through 2030 and % CAGR
- TABLE 165: Rest of Europe Historic Review for Rubber Processing Aids and Anti-Tack Agents by Application - Molded Rubber Products Application, Medical Gloves Application, Other Applications, Tires & Tubes Application, Gaskets & Seals Application and Wires & Cables Application Markets - Independent Analysis of Annual Sales in US$ Thousand for Years 2014 through 2023 and % CAGR
- TABLE 166: Rest of Europe 16-Year Perspective for Rubber Processing Aids and Anti-Tack Agents by Application - Percentage Breakdown of Value Sales for Molded Rubber Products Application, Medical Gloves Application, Other Applications, Tires & Tubes Application, Gaskets & Seals Application and Wires & Cables Application for the Years 2014, 2025 & 2030
- TABLE 167: Rest of Europe Recent Past, Current & Future Analysis for Rubber Processing Aids and Anti-Tack Agents by End-Use - Automotive & Transportation End-Use, Building & Construction End-Use, Medical End-Use, Electronics & Electricals End-Use, Footwear End-Use and Other End-Uses - Independent Analysis of Annual Sales in US$ Thousand for the Years 2024 through 2030 and % CAGR
- TABLE 168: Rest of Europe Historic Review for Rubber Processing Aids and Anti-Tack Agents by End-Use - Automotive & Transportation End-Use, Building & Construction End-Use, Medical End-Use, Electronics & Electricals End-Use, Footwear End-Use and Other End-Uses Markets - Independent Analysis of Annual Sales in US$ Thousand for Years 2014 through 2023 and % CAGR
- TABLE 169: Rest of Europe 16-Year Perspective for Rubber Processing Aids and Anti-Tack Agents by End-Use - Percentage Breakdown of Value Sales for Automotive & Transportation End-Use, Building & Construction End-Use, Medical End-Use, Electronics & Electricals End-Use, Footwear End-Use and Other End-Uses for the Years 2014, 2025 & 2030
- ASIA-PACIFIC
- Rubber Processing Aids and Anti-Tack Agents Market Presence - Strong/Active/Niche/Trivial - Key Competitors in Asia-Pacific for 2025 (E)
- TABLE 170: Asia-Pacific Recent Past, Current & Future Analysis for Rubber Processing Aids and Anti-Tack Agents by Geographic Region - Australia, India, South Korea and Rest of Asia-Pacific Markets - Independent Analysis of Annual Sales in US$ Thousand for Years 2024 through 2030 and % CAGR
- TABLE 171: Asia-Pacific Historic Review for Rubber Processing Aids and Anti-Tack Agents by Geographic Region - Australia, India, South Korea and Rest of Asia-Pacific Markets - Independent Analysis of Annual Sales in US$ Thousand for Years 2014 through 2023 and % CAGR
- TABLE 172: Asia-Pacific 16-Year Perspective for Rubber Processing Aids and Anti-Tack Agents by Geographic Region - Percentage Breakdown of Value Sales for Australia, India, South Korea and Rest of Asia-Pacific Markets for Years 2014, 2025 & 2030
- TABLE 173: Asia-Pacific Recent Past, Current & Future Analysis for Rubber Processing Aids and Anti-Tack Agents by Product Type - Fatty Acid Esters, Fatty Acid Amides, Stearates, Soaps, Silicone Polymers and Other Rubber Processing Aids & Anti-Tack Agents - Independent Analysis of Annual Sales in US$ Thousand for the Years 2024 through 2030 and % CAGR
- TABLE 174: Asia-Pacific Historic Review for Rubber Processing Aids and Anti-Tack Agents by Product Type - Fatty Acid Esters, Fatty Acid Amides, Stearates, Soaps, Silicone Polymers and Other Rubber Processing Aids & Anti-Tack Agents Markets - Independent Analysis of Annual Sales in US$ Thousand for Years 2014 through 2023 and % CAGR
- TABLE 175: Asia-Pacific 16-Year Perspective for Rubber Processing Aids and Anti-Tack Agents by Product Type - Percentage Breakdown of Value Sales for Fatty Acid Esters, Fatty Acid Amides, Stearates, Soaps, Silicone Polymers and Other Rubber Processing Aids & Anti-Tack Agents for the Years 2014, 2025 & 2030
- TABLE 176: Asia-Pacific Recent Past, Current & Future Analysis for Rubber Processing Aids and Anti-Tack Agents by Application - Molded Rubber Products Application, Medical Gloves Application, Other Applications, Tires & Tubes Application, Gaskets & Seals Application and Wires & Cables Application - Independent Analysis of Annual Sales in US$ Thousand for the Years 2024 through 2030 and % CAGR
- TABLE 177: Asia-Pacific Historic Review for Rubber Processing Aids and Anti-Tack Agents by Application - Molded Rubber Products Application, Medical Gloves Application, Other Applications, Tires & Tubes Application, Gaskets & Seals Application and Wires & Cables Application Markets - Independent Analysis of Annual Sales in US$ Thousand for Years 2014 through 2023 and % CAGR
- TABLE 178: Asia-Pacific 16-Year Perspective for Rubber Processing Aids and Anti-Tack Agents by Application - Percentage Breakdown of Value Sales for Molded Rubber Products Application, Medical Gloves Application, Other Applications, Tires & Tubes Application, Gaskets & Seals Application and Wires & Cables Application for the Years 2014, 2025 & 2030
- TABLE 179: Asia-Pacific Recent Past, Current & Future Analysis for Rubber Processing Aids and Anti-Tack Agents by End-Use - Automotive & Transportation End-Use, Building & Construction End-Use, Medical End-Use, Electronics & Electricals End-Use, Footwear End-Use and Other End-Uses - Independent Analysis of Annual Sales in US$ Thousand for the Years 2024 through 2030 and % CAGR
- TABLE 180: Asia-Pacific Historic Review for Rubber Processing Aids and Anti-Tack Agents by End-Use - Automotive & Transportation End-Use, Building & Construction End-Use, Medical End-Use, Electronics & Electricals End-Use, Footwear End-Use and Other End-Uses Markets - Independent Analysis of Annual Sales in US$ Thousand for Years 2014 through 2023 and % CAGR
- TABLE 181: Asia-Pacific 16-Year Perspective for Rubber Processing Aids and Anti-Tack Agents by End-Use - Percentage Breakdown of Value Sales for Automotive & Transportation End-Use, Building & Construction End-Use, Medical End-Use, Electronics & Electricals End-Use, Footwear End-Use and Other End-Uses for the Years 2014, 2025 & 2030
- AUSTRALIA
- Rubber Processing Aids and Anti-Tack Agents Market Presence - Strong/Active/Niche/Trivial - Key Competitors in Australia for 2025 (E)
- TABLE 182: Australia Recent Past, Current & Future Analysis for Rubber Processing Aids and Anti-Tack Agents by Product Type - Fatty Acid Esters, Fatty Acid Amides, Stearates, Soaps, Silicone Polymers and Other Rubber Processing Aids & Anti-Tack Agents - Independent Analysis of Annual Sales in US$ Thousand for the Years 2024 through 2030 and % CAGR
- TABLE 183: Australia Historic Review for Rubber Processing Aids and Anti-Tack Agents by Product Type - Fatty Acid Esters, Fatty Acid Amides, Stearates, Soaps, Silicone Polymers and Other Rubber Processing Aids & Anti-Tack Agents Markets - Independent Analysis of Annual Sales in US$ Thousand for Years 2014 through 2023 and % CAGR
- TABLE 184: Australia 16-Year Perspective for Rubber Processing Aids and Anti-Tack Agents by Product Type - Percentage Breakdown of Value Sales for Fatty Acid Esters, Fatty Acid Amides, Stearates, Soaps, Silicone Polymers and Other Rubber Processing Aids & Anti-Tack Agents for the Years 2014, 2025 & 2030
- TABLE 185: Australia Recent Past, Current & Future Analysis for Rubber Processing Aids and Anti-Tack Agents by Application - Molded Rubber Products Application, Medical Gloves Application, Other Applications, Tires & Tubes Application, Gaskets & Seals Application and Wires & Cables Application - Independent Analysis of Annual Sales in US$ Thousand for the Years 2024 through 2030 and % CAGR
- TABLE 186: Australia Historic Review for Rubber Processing Aids and Anti-Tack Agents by Application - Molded Rubber Products Application, Medical Gloves Application, Other Applications, Tires & Tubes Application, Gaskets & Seals Application and Wires & Cables Application Markets - Independent Analysis of Annual Sales in US$ Thousand for Years 2014 through 2023 and % CAGR
- TABLE 187: Australia 16-Year Perspective for Rubber Processing Aids and Anti-Tack Agents by Application - Percentage Breakdown of Value Sales for Molded Rubber Products Application, Medical Gloves Application, Other Applications, Tires & Tubes Application, Gaskets & Seals Application and Wires & Cables Application for the Years 2014, 2025 & 2030
- TABLE 188: Australia Recent Past, Current & Future Analysis for Rubber Processing Aids and Anti-Tack Agents by End-Use - Automotive & Transportation End-Use, Building & Construction End-Use, Medical End-Use, Electronics & Electricals End-Use, Footwear End-Use and Other End-Uses - Independent Analysis of Annual Sales in US$ Thousand for the Years 2024 through 2030 and % CAGR
- TABLE 189: Australia Historic Review for Rubber Processing Aids and Anti-Tack Agents by End-Use - Automotive & Transportation End-Use, Building & Construction End-Use, Medical End-Use, Electronics & Electricals End-Use, Footwear End-Use and Other End-Uses Markets - Independent Analysis of Annual Sales in US$ Thousand for Years 2014 through 2023 and % CAGR
- TABLE 190: Australia 16-Year Perspective for Rubber Processing Aids and Anti-Tack Agents by End-Use - Percentage Breakdown of Value Sales for Automotive & Transportation End-Use, Building & Construction End-Use, Medical End-Use, Electronics & Electricals End-Use, Footwear End-Use and Other End-Uses for the Years 2014, 2025 & 2030
- INDIA
- Rubber Processing Aids and Anti-Tack Agents Market Presence - Strong/Active/Niche/Trivial - Key Competitors in India for 2025 (E)
- TABLE 191: India Recent Past, Current & Future Analysis for Rubber Processing Aids and Anti-Tack Agents by Product Type - Fatty Acid Esters, Fatty Acid Amides, Stearates, Soaps, Silicone Polymers and Other Rubber Processing Aids & Anti-Tack Agents - Independent Analysis of Annual Sales in US$ Thousand for the Years 2024 through 2030 and % CAGR
- TABLE 192: India Historic Review for Rubber Processing Aids and Anti-Tack Agents by Product Type - Fatty Acid Esters, Fatty Acid Amides, Stearates, Soaps, Silicone Polymers and Other Rubber Processing Aids & Anti-Tack Agents Markets - Independent Analysis of Annual Sales in US$ Thousand for Years 2014 through 2023 and % CAGR
- TABLE 193: India 16-Year Perspective for Rubber Processing Aids and Anti-Tack Agents by Product Type - Percentage Breakdown of Value Sales for Fatty Acid Esters, Fatty Acid Amides, Stearates, Soaps, Silicone Polymers and Other Rubber Processing Aids & Anti-Tack Agents for the Years 2014, 2025 & 2030
- TABLE 194: India Recent Past, Current & Future Analysis for Rubber Processing Aids and Anti-Tack Agents by Application - Molded Rubber Products Application, Medical Gloves Application, Other Applications, Tires & Tubes Application, Gaskets & Seals Application and Wires & Cables Application - Independent Analysis of Annual Sales in US$ Thousand for the Years 2024 through 2030 and % CAGR
- TABLE 195: India Historic Review for Rubber Processing Aids and Anti-Tack Agents by Application - Molded Rubber Products Application, Medical Gloves Application, Other Applications, Tires & Tubes Application, Gaskets & Seals Application and Wires & Cables Application Markets - Independent Analysis of Annual Sales in US$ Thousand for Years 2014 through 2023 and % CAGR
- TABLE 196: India 16-Year Perspective for Rubber Processing Aids and Anti-Tack Agents by Application - Percentage Breakdown of Value Sales for Molded Rubber Products Application, Medical Gloves Application, Other Applications, Tires & Tubes Application, Gaskets & Seals Application and Wires & Cables Application for the Years 2014, 2025 & 2030
- TABLE 197: India Recent Past, Current & Future Analysis for Rubber Processing Aids and Anti-Tack Agents by End-Use - Automotive & Transportation End-Use, Building & Construction End-Use, Medical End-Use, Electronics & Electricals End-Use, Footwear End-Use and Other End-Uses - Independent Analysis of Annual Sales in US$ Thousand for the Years 2024 through 2030 and % CAGR
- TABLE 198: India Historic Review for Rubber Processing Aids and Anti-Tack Agents by End-Use - Automotive & Transportation End-Use, Building & Construction End-Use, Medical End-Use, Electronics & Electricals End-Use, Footwear End-Use and Other End-Uses Markets - Independent Analysis of Annual Sales in US$ Thousand for Years 2014 through 2023 and % CAGR
- TABLE 199: India 16-Year Perspective for Rubber Processing Aids and Anti-Tack Agents by End-Use - Percentage Breakdown of Value Sales for Automotive & Transportation End-Use, Building & Construction End-Use, Medical End-Use, Electronics & Electricals End-Use, Footwear End-Use and Other End-Uses for the Years 2014, 2025 & 2030
- SOUTH KOREA
- TABLE 200: South Korea Recent Past, Current & Future Analysis for Rubber Processing Aids and Anti-Tack Agents by Product Type - Fatty Acid Esters, Fatty Acid Amides, Stearates, Soaps, Silicone Polymers and Other Rubber Processing Aids & Anti-Tack Agents - Independent Analysis of Annual Sales in US$ Thousand for the Years 2024 through 2030 and % CAGR
- TABLE 201: South Korea Historic Review for Rubber Processing Aids and Anti-Tack Agents by Product Type - Fatty Acid Esters, Fatty Acid Amides, Stearates, Soaps, Silicone Polymers and Other Rubber Processing Aids & Anti-Tack Agents Markets - Independent Analysis of Annual Sales in US$ Thousand for Years 2014 through 2023 and % CAGR
- TABLE 202: South Korea 16-Year Perspective for Rubber Processing Aids and Anti-Tack Agents by Product Type - Percentage Breakdown of Value Sales for Fatty Acid Esters, Fatty Acid Amides, Stearates, Soaps, Silicone Polymers and Other Rubber Processing Aids & Anti-Tack Agents for the Years 2014, 2025 & 2030
- TABLE 203: South Korea Recent Past, Current & Future Analysis for Rubber Processing Aids and Anti-Tack Agents by Application - Molded Rubber Products Application, Medical Gloves Application, Other Applications, Tires & Tubes Application, Gaskets & Seals Application and Wires & Cables Application - Independent Analysis of Annual Sales in US$ Thousand for the Years 2024 through 2030 and % CAGR
- TABLE 204: South Korea Historic Review for Rubber Processing Aids and Anti-Tack Agents by Application - Molded Rubber Products Application, Medical Gloves Application, Other Applications, Tires & Tubes Application, Gaskets & Seals Application and Wires & Cables Application Markets - Independent Analysis of Annual Sales in US$ Thousand for Years 2014 through 2023 and % CAGR
- TABLE 205: South Korea 16-Year Perspective for Rubber Processing Aids and Anti-Tack Agents by Application - Percentage Breakdown of Value Sales for Molded Rubber Products Application, Medical Gloves Application, Other Applications, Tires & Tubes Application, Gaskets & Seals Application and Wires & Cables Application for the Years 2014, 2025 & 2030
- TABLE 206: South Korea Recent Past, Current & Future Analysis for Rubber Processing Aids and Anti-Tack Agents by End-Use - Automotive & Transportation End-Use, Building & Construction End-Use, Medical End-Use, Electronics & Electricals End-Use, Footwear End-Use and Other End-Uses - Independent Analysis of Annual Sales in US$ Thousand for the Years 2024 through 2030 and % CAGR
- TABLE 207: South Korea Historic Review for Rubber Processing Aids and Anti-Tack Agents by End-Use - Automotive & Transportation End-Use, Building & Construction End-Use, Medical End-Use, Electronics & Electricals End-Use, Footwear End-Use and Other End-Uses Markets - Independent Analysis of Annual Sales in US$ Thousand for Years 2014 through 2023 and % CAGR
- TABLE 208: South Korea 16-Year Perspective for Rubber Processing Aids and Anti-Tack Agents by End-Use - Percentage Breakdown of Value Sales for Automotive & Transportation End-Use, Building & Construction End-Use, Medical End-Use, Electronics & Electricals End-Use, Footwear End-Use and Other End-Uses for the Years 2014, 2025 & 2030
- REST OF ASIA-PACIFIC
- TABLE 209: Rest of Asia-Pacific Recent Past, Current & Future Analysis for Rubber Processing Aids and Anti-Tack Agents by Product Type - Fatty Acid Esters, Fatty Acid Amides, Stearates, Soaps, Silicone Polymers and Other Rubber Processing Aids & Anti-Tack Agents - Independent Analysis of Annual Sales in US$ Thousand for the Years 2024 through 2030 and % CAGR
- TABLE 210: Rest of Asia-Pacific Historic Review for Rubber Processing Aids and Anti-Tack Agents by Product Type - Fatty Acid Esters, Fatty Acid Amides, Stearates, Soaps, Silicone Polymers and Other Rubber Processing Aids & Anti-Tack Agents Markets - Independent Analysis of Annual Sales in US$ Thousand for Years 2014 through 2023 and % CAGR
- TABLE 211: Rest of Asia-Pacific 16-Year Perspective for Rubber Processing Aids and Anti-Tack Agents by Product Type - Percentage Breakdown of Value Sales for Fatty Acid Esters, Fatty Acid Amides, Stearates, Soaps, Silicone Polymers and Other Rubber Processing Aids & Anti-Tack Agents for the Years 2014, 2025 & 2030
- TABLE 212: Rest of Asia-Pacific Recent Past, Current & Future Analysis for Rubber Processing Aids and Anti-Tack Agents by Application - Molded Rubber Products Application, Medical Gloves Application, Other Applications, Tires & Tubes Application, Gaskets & Seals Application and Wires & Cables Application - Independent Analysis of Annual Sales in US$ Thousand for the Years 2024 through 2030 and % CAGR
- TABLE 213: Rest of Asia-Pacific Historic Review for Rubber Processing Aids and Anti-Tack Agents by Application - Molded Rubber Products Application, Medical Gloves Application, Other Applications, Tires & Tubes Application, Gaskets & Seals Application and Wires & Cables Application Markets - Independent Analysis of Annual Sales in US$ Thousand for Years 2014 through 2023 and % CAGR
- TABLE 214: Rest of Asia-Pacific 16-Year Perspective for Rubber Processing Aids and Anti-Tack Agents by Application - Percentage Breakdown of Value Sales for Molded Rubber Products Application, Medical Gloves Application, Other Applications, Tires & Tubes Application, Gaskets & Seals Application and Wires & Cables Application for the Years 2014, 2025 & 2030
- TABLE 215: Rest of Asia-Pacific Recent Past, Current & Future Analysis for Rubber Processing Aids and Anti-Tack Agents by End-Use - Automotive & Transportation End-Use, Building & Construction End-Use, Medical End-Use, Electronics & Electricals End-Use, Footwear End-Use and Other End-Uses - Independent Analysis of Annual Sales in US$ Thousand for the Years 2024 through 2030 and % CAGR
- TABLE 216: Rest of Asia-Pacific Historic Review for Rubber Processing Aids and Anti-Tack Agents by End-Use - Automotive & Transportation End-Use, Building & Construction End-Use, Medical End-Use, Electronics & Electricals End-Use, Footwear End-Use and Other End-Uses Markets - Independent Analysis of Annual Sales in US$ Thousand for Years 2014 through 2023 and % CAGR
- TABLE 217: Rest of Asia-Pacific 16-Year Perspective for Rubber Processing Aids and Anti-Tack Agents by End-Use - Percentage Breakdown of Value Sales for Automotive & Transportation End-Use, Building & Construction End-Use, Medical End-Use, Electronics & Electricals End-Use, Footwear End-Use and Other End-Uses for the Years 2014, 2025 & 2030
- LATIN AMERICA
- Rubber Processing Aids and Anti-Tack Agents Market Presence - Strong/Active/Niche/Trivial - Key Competitors in Latin America for 2025 (E)
- TABLE 218: Latin America Recent Past, Current & Future Analysis for Rubber Processing Aids and Anti-Tack Agents by Geographic Region - Argentina, Brazil, Mexico and Rest of Latin America Markets - Independent Analysis of Annual Sales in US$ Thousand for Years 2024 through 2030 and % CAGR
- TABLE 219: Latin America Historic Review for Rubber Processing Aids and Anti-Tack Agents by Geographic Region - Argentina, Brazil, Mexico and Rest of Latin America Markets - Independent Analysis of Annual Sales in US$ Thousand for Years 2014 through 2023 and % CAGR
- TABLE 220: Latin America 16-Year Perspective for Rubber Processing Aids and Anti-Tack Agents by Geographic Region - Percentage Breakdown of Value Sales for Argentina, Brazil, Mexico and Rest of Latin America Markets for Years 2014, 2025 & 2030
- TABLE 221: Latin America Recent Past, Current & Future Analysis for Rubber Processing Aids and Anti-Tack Agents by Product Type - Fatty Acid Esters, Fatty Acid Amides, Stearates, Soaps, Silicone Polymers and Other Rubber Processing Aids & Anti-Tack Agents - Independent Analysis of Annual Sales in US$ Thousand for the Years 2024 through 2030 and % CAGR
- TABLE 222: Latin America Historic Review for Rubber Processing Aids and Anti-Tack Agents by Product Type - Fatty Acid Esters, Fatty Acid Amides, Stearates, Soaps, Silicone Polymers and Other Rubber Processing Aids & Anti-Tack Agents Markets - Independent Analysis of Annual Sales in US$ Thousand for Years 2014 through 2023 and % CAGR
- TABLE 223: Latin America 16-Year Perspective for Rubber Processing Aids and Anti-Tack Agents by Product Type - Percentage Breakdown of Value Sales for Fatty Acid Esters, Fatty Acid Amides, Stearates, Soaps, Silicone Polymers and Other Rubber Processing Aids & Anti-Tack Agents for the Years 2014, 2025 & 2030
- TABLE 224: Latin America Recent Past, Current & Future Analysis for Rubber Processing Aids and Anti-Tack Agents by Application - Molded Rubber Products Application, Medical Gloves Application, Other Applications, Tires & Tubes Application, Gaskets & Seals Application and Wires & Cables Application - Independent Analysis of Annual Sales in US$ Thousand for the Years 2024 through 2030 and % CAGR
- TABLE 225: Latin America Historic Review for Rubber Processing Aids and Anti-Tack Agents by Application - Molded Rubber Products Application, Medical Gloves Application, Other Applications, Tires & Tubes Application, Gaskets & Seals Application and Wires & Cables Application Markets - Independent Analysis of Annual Sales in US$ Thousand for Years 2014 through 2023 and % CAGR
- TABLE 226: Latin America 16-Year Perspective for Rubber Processing Aids and Anti-Tack Agents by Application - Percentage Breakdown of Value Sales for Molded Rubber Products Application, Medical Gloves Application, Other Applications, Tires & Tubes Application, Gaskets & Seals Application and Wires & Cables Application for the Years 2014, 2025 & 2030
- TABLE 227: Latin America Recent Past, Current & Future Analysis for Rubber Processing Aids and Anti-Tack Agents by End-Use - Automotive & Transportation End-Use, Building & Construction End-Use, Medical End-Use, Electronics & Electricals End-Use, Footwear End-Use and Other End-Uses - Independent Analysis of Annual Sales in US$ Thousand for the Years 2024 through 2030 and % CAGR
- TABLE 228: Latin America Historic Review for Rubber Processing Aids and Anti-Tack Agents by End-Use - Automotive & Transportation End-Use, Building & Construction End-Use, Medical End-Use, Electronics & Electricals End-Use, Footwear End-Use and Other End-Uses Markets - Independent Analysis of Annual Sales in US$ Thousand for Years 2014 through 2023 and % CAGR
- TABLE 229: Latin America 16-Year Perspective for Rubber Processing Aids and Anti-Tack Agents by End-Use - Percentage Breakdown of Value Sales for Automotive & Transportation End-Use, Building & Construction End-Use, Medical End-Use, Electronics & Electricals End-Use, Footwear End-Use and Other End-Uses for the Years 2014, 2025 & 2030
- ARGENTINA
- TABLE 230: Argentina Recent Past, Current & Future Analysis for Rubber Processing Aids and Anti-Tack Agents by Product Type - Fatty Acid Esters, Fatty Acid Amides, Stearates, Soaps, Silicone Polymers and Other Rubber Processing Aids & Anti-Tack Agents - Independent Analysis of Annual Sales in US$ Thousand for the Years 2024 through 2030 and % CAGR
- TABLE 231: Argentina Historic Review for Rubber Processing Aids and Anti-Tack Agents by Product Type - Fatty Acid Esters, Fatty Acid Amides, Stearates, Soaps, Silicone Polymers and Other Rubber Processing Aids & Anti-Tack Agents Markets - Independent Analysis of Annual Sales in US$ Thousand for Years 2014 through 2023 and % CAGR
- TABLE 232: Argentina 16-Year Perspective for Rubber Processing Aids and Anti-Tack Agents by Product Type - Percentage Breakdown of Value Sales for Fatty Acid Esters, Fatty Acid Amides, Stearates, Soaps, Silicone Polymers and Other Rubber Processing Aids & Anti-Tack Agents for the Years 2014, 2025 & 2030
- TABLE 233: Argentina Recent Past, Current & Future Analysis for Rubber Processing Aids and Anti-Tack Agents by Application - Molded Rubber Products Application, Medical Gloves Application, Other Applications, Tires & Tubes Application, Gaskets & Seals Application and Wires & Cables Application - Independent Analysis of Annual Sales in US$ Thousand for the Years 2024 through 2030 and % CAGR
- TABLE 234: Argentina Historic Review for Rubber Processing Aids and Anti-Tack Agents by Application - Molded Rubber Products Application, Medical Gloves Application, Other Applications, Tires & Tubes Application, Gaskets & Seals Application and Wires & Cables Application Markets - Independent Analysis of Annual Sales in US$ Thousand for Years 2014 through 2023 and % CAGR
- TABLE 235: Argentina 16-Year Perspective for Rubber Processing Aids and Anti-Tack Agents by Application - Percentage Breakdown of Value Sales for Molded Rubber Products Application, Medical Gloves Application, Other Applications, Tires & Tubes Application, Gaskets & Seals Application and Wires & Cables Application for the Years 2014, 2025 & 2030
- TABLE 236: Argentina Recent Past, Current & Future Analysis for Rubber Processing Aids and Anti-Tack Agents by End-Use - Automotive & Transportation End-Use, Building & Construction End-Use, Medical End-Use, Electronics & Electricals End-Use, Footwear End-Use and Other End-Uses - Independent Analysis of Annual Sales in US$ Thousand for the Years 2024 through 2030 and % CAGR
- TABLE 237: Argentina Historic Review for Rubber Processing Aids and Anti-Tack Agents by End-Use - Automotive & Transportation End-Use, Building & Construction End-Use, Medical End-Use, Electronics & Electricals End-Use, Footwear End-Use and Other End-Uses Markets - Independent Analysis of Annual Sales in US$ Thousand for Years 2014 through 2023 and % CAGR
- TABLE 238: Argentina 16-Year Perspective for Rubber Processing Aids and Anti-Tack Agents by End-Use - Percentage Breakdown of Value Sales for Automotive & Transportation End-Use, Building & Construction End-Use, Medical End-Use, Electronics & Electricals End-Use, Footwear End-Use and Other End-Uses for the Years 2014, 2025 & 2030
- BRAZIL
- TABLE 239: Brazil Recent Past, Current & Future Analysis for Rubber Processing Aids and Anti-Tack Agents by Product Type - Fatty Acid Esters, Fatty Acid Amides, Stearates, Soaps, Silicone Polymers and Other Rubber Processing Aids & Anti-Tack Agents - Independent Analysis of Annual Sales in US$ Thousand for the Years 2024 through 2030 and % CAGR
- TABLE 240: Brazil Historic Review for Rubber Processing Aids and Anti-Tack Agents by Product Type - Fatty Acid Esters, Fatty Acid Amides, Stearates, Soaps, Silicone Polymers and Other Rubber Processing Aids & Anti-Tack Agents Markets - Independent Analysis of Annual Sales in US$ Thousand for Years 2014 through 2023 and % CAGR
- TABLE 241: Brazil 16-Year Perspective for Rubber Processing Aids and Anti-Tack Agents by Product Type - Percentage Breakdown of Value Sales for Fatty Acid Esters, Fatty Acid Amides, Stearates, Soaps, Silicone Polymers and Other Rubber Processing Aids & Anti-Tack Agents for the Years 2014, 2025 & 2030
- TABLE 242: Brazil Recent Past, Current & Future Analysis for Rubber Processing Aids and Anti-Tack Agents by Application - Molded Rubber Products Application, Medical Gloves Application, Other Applications, Tires & Tubes Application, Gaskets & Seals Application and Wires & Cables Application - Independent Analysis of Annual Sales in US$ Thousand for the Years 2024 through 2030 and % CAGR
- TABLE 243: Brazil Historic Review for Rubber Processing Aids and Anti-Tack Agents by Application - Molded Rubber Products Application, Medical Gloves Application, Other Applications, Tires & Tubes Application, Gaskets & Seals Application and Wires & Cables Application Markets - Independent Analysis of Annual Sales in US$ Thousand for Years 2014 through 2023 and % CAGR
- TABLE 244: Brazil 16-Year Perspective for Rubber Processing Aids and Anti-Tack Agents by Application - Percentage Breakdown of Value Sales for Molded Rubber Products Application, Medical Gloves Application, Other Applications, Tires & Tubes Application, Gaskets & Seals Application and Wires & Cables Application for the Years 2014, 2025 & 2030
- TABLE 245: Brazil Recent Past, Current & Future Analysis for Rubber Processing Aids and Anti-Tack Agents by End-Use - Automotive & Transportation End-Use, Building & Construction End-Use, Medical End-Use, Electronics & Electricals End-Use, Footwear End-Use and Other End-Uses - Independent Analysis of Annual Sales in US$ Thousand for the Years 2024 through 2030 and % CAGR
- TABLE 246: Brazil Historic Review for Rubber Processing Aids and Anti-Tack Agents by End-Use - Automotive & Transportation End-Use, Building & Construction End-Use, Medical End-Use, Electronics & Electricals End-Use, Footwear End-Use and Other End-Uses Markets - Independent Analysis of Annual Sales in US$ Thousand for Years 2014 through 2023 and % CAGR
- TABLE 247: Brazil 16-Year Perspective for Rubber Processing Aids and Anti-Tack Agents by End-Use - Percentage Breakdown of Value Sales for Automotive & Transportation End-Use, Building & Construction End-Use, Medical End-Use, Electronics & Electricals End-Use, Footwear End-Use and Other End-Uses for the Years 2014, 2025 & 2030
- MEXICO
- TABLE 248: Mexico Recent Past, Current & Future Analysis for Rubber Processing Aids and Anti-Tack Agents by Product Type - Fatty Acid Esters, Fatty Acid Amides, Stearates, Soaps, Silicone Polymers and Other Rubber Processing Aids & Anti-Tack Agents - Independent Analysis of Annual Sales in US$ Thousand for the Years 2024 through 2030 and % CAGR
- TABLE 249: Mexico Historic Review for Rubber Processing Aids and Anti-Tack Agents by Product Type - Fatty Acid Esters, Fatty Acid Amides, Stearates, Soaps, Silicone Polymers and Other Rubber Processing Aids & Anti-Tack Agents Markets - Independent Analysis of Annual Sales in US$ Thousand for Years 2014 through 2023 and % CAGR
- TABLE 250: Mexico 16-Year Perspective for Rubber Processing Aids and Anti-Tack Agents by Product Type - Percentage Breakdown of Value Sales for Fatty Acid Esters, Fatty Acid Amides, Stearates, Soaps, Silicone Polymers and Other Rubber Processing Aids & Anti-Tack Agents for the Years 2014, 2025 & 2030
- TABLE 251: Mexico Recent Past, Current & Future Analysis for Rubber Processing Aids and Anti-Tack Agents by Application - Molded Rubber Products Application, Medical Gloves Application, Other Applications, Tires & Tubes Application, Gaskets & Seals Application and Wires & Cables Application - Independent Analysis of Annual Sales in US$ Thousand for the Years 2024 through 2030 and % CAGR
- TABLE 252: Mexico Historic Review for Rubber Processing Aids and Anti-Tack Agents by Application - Molded Rubber Products Application, Medical Gloves Application, Other Applications, Tires & Tubes Application, Gaskets & Seals Application and Wires & Cables Application Markets - Independent Analysis of Annual Sales in US$ Thousand for Years 2014 through 2023 and % CAGR
- TABLE 253: Mexico 16-Year Perspective for Rubber Processing Aids and Anti-Tack Agents by Application - Percentage Breakdown of Value Sales for Molded Rubber Products Application, Medical Gloves Application, Other Applications, Tires & Tubes Application, Gaskets & Seals Application and Wires & Cables Application for the Years 2014, 2025 & 2030
- TABLE 254: Mexico Recent Past, Current & Future Analysis for Rubber Processing Aids and Anti-Tack Agents by End-Use - Automotive & Transportation End-Use, Building & Construction End-Use, Medical End-Use, Electronics & Electricals End-Use, Footwear End-Use and Other End-Uses - Independent Analysis of Annual Sales in US$ Thousand for the Years 2024 through 2030 and % CAGR
- TABLE 255: Mexico Historic Review for Rubber Processing Aids and Anti-Tack Agents by End-Use - Automotive & Transportation End-Use, Building & Construction End-Use, Medical End-Use, Electronics & Electricals End-Use, Footwear End-Use and Other End-Uses Markets - Independent Analysis of Annual Sales in US$ Thousand for Years 2014 through 2023 and % CAGR
- TABLE 256: Mexico 16-Year Perspective for Rubber Processing Aids and Anti-Tack Agents by End-Use - Percentage Breakdown of Value Sales for Automotive & Transportation End-Use, Building & Construction End-Use, Medical End-Use, Electronics & Electricals End-Use, Footwear End-Use and Other End-Uses for the Years 2014, 2025 & 2030
- REST OF LATIN AMERICA
- TABLE 257: Rest of Latin America Recent Past, Current & Future Analysis for Rubber Processing Aids and Anti-Tack Agents by Product Type - Fatty Acid Esters, Fatty Acid Amides, Stearates, Soaps, Silicone Polymers and Other Rubber Processing Aids & Anti-Tack Agents - Independent Analysis of Annual Sales in US$ Thousand for the Years 2024 through 2030 and % CAGR
- TABLE 258: Rest of Latin America Historic Review for Rubber Processing Aids and Anti-Tack Agents by Product Type - Fatty Acid Esters, Fatty Acid Amides, Stearates, Soaps, Silicone Polymers and Other Rubber Processing Aids & Anti-Tack Agents Markets - Independent Analysis of Annual Sales in US$ Thousand for Years 2014 through 2023 and % CAGR
- TABLE 259: Rest of Latin America 16-Year Perspective for Rubber Processing Aids and Anti-Tack Agents by Product Type - Percentage Breakdown of Value Sales for Fatty Acid Esters, Fatty Acid Amides, Stearates, Soaps, Silicone Polymers and Other Rubber Processing Aids & Anti-Tack Agents for the Years 2014, 2025 & 2030
- TABLE 260: Rest of Latin America Recent Past, Current & Future Analysis for Rubber Processing Aids and Anti-Tack Agents by Application - Molded Rubber Products Application, Medical Gloves Application, Other Applications, Tires & Tubes Application, Gaskets & Seals Application and Wires & Cables Application - Independent Analysis of Annual Sales in US$ Thousand for the Years 2024 through 2030 and % CAGR
- TABLE 261: Rest of Latin America Historic Review for Rubber Processing Aids and Anti-Tack Agents by Application - Molded Rubber Products Application, Medical Gloves Application, Other Applications, Tires & Tubes Application, Gaskets & Seals Application and Wires & Cables Application Markets - Independent Analysis of Annual Sales in US$ Thousand for Years 2014 through 2023 and % CAGR
- TABLE 262: Rest of Latin America 16-Year Perspective for Rubber Processing Aids and Anti-Tack Agents by Application - Percentage Breakdown of Value Sales for Molded Rubber Products Application, Medical Gloves Application, Other Applications, Tires & Tubes Application, Gaskets & Seals Application and Wires & Cables Application for the Years 2014, 2025 & 2030
- TABLE 263: Rest of Latin America Recent Past, Current & Future Analysis for Rubber Processing Aids and Anti-Tack Agents by End-Use - Automotive & Transportation End-Use, Building & Construction End-Use, Medical End-Use, Electronics & Electricals End-Use, Footwear End-Use and Other End-Uses - Independent Analysis of Annual Sales in US$ Thousand for the Years 2024 through 2030 and % CAGR
- TABLE 264: Rest of Latin America Historic Review for Rubber Processing Aids and Anti-Tack Agents by End-Use - Automotive & Transportation End-Use, Building & Construction End-Use, Medical End-Use, Electronics & Electricals End-Use, Footwear End-Use and Other End-Uses Markets - Independent Analysis of Annual Sales in US$ Thousand for Years 2014 through 2023 and % CAGR
- TABLE 265: Rest of Latin America 16-Year Perspective for Rubber Processing Aids and Anti-Tack Agents by End-Use - Percentage Breakdown of Value Sales for Automotive & Transportation End-Use, Building & Construction End-Use, Medical End-Use, Electronics & Electricals End-Use, Footwear End-Use and Other End-Uses for the Years 2014, 2025 & 2030
- MIDDLE EAST
- Rubber Processing Aids and Anti-Tack Agents Market Presence - Strong/Active/Niche/Trivial - Key Competitors in Middle East for 2025 (E)
- TABLE 266: Middle East Recent Past, Current & Future Analysis for Rubber Processing Aids and Anti-Tack Agents by Geographic Region - Iran, Israel, Saudi Arabia, UAE and Rest of Middle East Markets - Independent Analysis of Annual Sales in US$ Thousand for Years 2024 through 2030 and % CAGR
- TABLE 267: Middle East Historic Review for Rubber Processing Aids and Anti-Tack Agents by Geographic Region - Iran, Israel, Saudi Arabia, UAE and Rest of Middle East Markets - Independent Analysis of Annual Sales in US$ Thousand for Years 2014 through 2023 and % CAGR
- TABLE 268: Middle East 16-Year Perspective for Rubber Processing Aids and Anti-Tack Agents by Geographic Region - Percentage Breakdown of Value Sales for Iran, Israel, Saudi Arabia, UAE and Rest of Middle East Markets for Years 2014, 2025 & 2030
- TABLE 269: Middle East Recent Past, Current & Future Analysis for Rubber Processing Aids and Anti-Tack Agents by Product Type - Fatty Acid Esters, Fatty Acid Amides, Stearates, Soaps, Silicone Polymers and Other Rubber Processing Aids & Anti-Tack Agents - Independent Analysis of Annual Sales in US$ Thousand for the Years 2024 through 2030 and % CAGR
- TABLE 270: Middle East Historic Review for Rubber Processing Aids and Anti-Tack Agents by Product Type - Fatty Acid Esters, Fatty Acid Amides, Stearates, Soaps, Silicone Polymers and Other Rubber Processing Aids & Anti-Tack Agents Markets - Independent Analysis of Annual Sales in US$ Thousand for Years 2014 through 2023 and % CAGR
- TABLE 271: Middle East 16-Year Perspective for Rubber Processing Aids and Anti-Tack Agents by Product Type - Percentage Breakdown of Value Sales for Fatty Acid Esters, Fatty Acid Amides, Stearates, Soaps, Silicone Polymers and Other Rubber Processing Aids & Anti-Tack Agents for the Years 2014, 2025 & 2030
- TABLE 272: Middle East Recent Past, Current & Future Analysis for Rubber Processing Aids and Anti-Tack Agents by Application - Molded Rubber Products Application, Medical Gloves Application, Other Applications, Tires & Tubes Application, Gaskets & Seals Application and Wires & Cables Application - Independent Analysis of Annual Sales in US$ Thousand for the Years 2024 through 2030 and % CAGR
- TABLE 273: Middle East Historic Review for Rubber Processing Aids and Anti-Tack Agents by Application - Molded Rubber Products Application, Medical Gloves Application, Other Applications, Tires & Tubes Application, Gaskets & Seals Application and Wires & Cables Application Markets - Independent Analysis of Annual Sales in US$ Thousand for Years 2014 through 2023 and % CAGR
- TABLE 274: Middle East 16-Year Perspective for Rubber Processing Aids and Anti-Tack Agents by Application - Percentage Breakdown of Value Sales for Molded Rubber Products Application, Medical Gloves Application, Other Applications, Tires & Tubes Application, Gaskets & Seals Application and Wires & Cables Application for the Years 2014, 2025 & 2030
- TABLE 275: Middle East Recent Past, Current & Future Analysis for Rubber Processing Aids and Anti-Tack Agents by End-Use - Automotive & Transportation End-Use, Building & Construction End-Use, Medical End-Use, Electronics & Electricals End-Use, Footwear End-Use and Other End-Uses - Independent Analysis of Annual Sales in US$ Thousand for the Years 2024 through 2030 and % CAGR
- TABLE 276: Middle East Historic Review for Rubber Processing Aids and Anti-Tack Agents by End-Use - Automotive & Transportation End-Use, Building & Construction End-Use, Medical End-Use, Electronics & Electricals End-Use, Footwear End-Use and Other End-Uses Markets - Independent Analysis of Annual Sales in US$ Thousand for Years 2014 through 2023 and % CAGR
- TABLE 277: Middle East 16-Year Perspective for Rubber Processing Aids and Anti-Tack Agents by End-Use - Percentage Breakdown of Value Sales for Automotive & Transportation End-Use, Building & Construction End-Use, Medical End-Use, Electronics & Electricals End-Use, Footwear End-Use and Other End-Uses for the Years 2014, 2025 & 2030
- IRAN
- TABLE 278: Iran Recent Past, Current & Future Analysis for Rubber Processing Aids and Anti-Tack Agents by Product Type - Fatty Acid Esters, Fatty Acid Amides, Stearates, Soaps, Silicone Polymers and Other Rubber Processing Aids & Anti-Tack Agents - Independent Analysis of Annual Sales in US$ Thousand for the Years 2024 through 2030 and % CAGR
- TABLE 279: Iran Historic Review for Rubber Processing Aids and Anti-Tack Agents by Product Type - Fatty Acid Esters, Fatty Acid Amides, Stearates, Soaps, Silicone Polymers and Other Rubber Processing Aids & Anti-Tack Agents Markets - Independent Analysis of Annual Sales in US$ Thousand for Years 2014 through 2023 and % CAGR
- TABLE 280: Iran 16-Year Perspective for Rubber Processing Aids and Anti-Tack Agents by Product Type - Percentage Breakdown of Value Sales for Fatty Acid Esters, Fatty Acid Amides, Stearates, Soaps, Silicone Polymers and Other Rubber Processing Aids & Anti-Tack Agents for the Years 2014, 2025 & 2030
- TABLE 281: Iran Recent Past, Current & Future Analysis for Rubber Processing Aids and Anti-Tack Agents by Application - Molded Rubber Products Application, Medical Gloves Application, Other Applications, Tires & Tubes Application, Gaskets & Seals Application and Wires & Cables Application - Independent Analysis of Annual Sales in US$ Thousand for the Years 2024 through 2030 and % CAGR
- TABLE 282: Iran Historic Review for Rubber Processing Aids and Anti-Tack Agents by Application - Molded Rubber Products Application, Medical Gloves Application, Other Applications, Tires & Tubes Application, Gaskets & Seals Application and Wires & Cables Application Markets - Independent Analysis of Annual Sales in US$ Thousand for Years 2014 through 2023 and % CAGR
- TABLE 283: Iran 16-Year Perspective for Rubber Processing Aids and Anti-Tack Agents by Application - Percentage Breakdown of Value Sales for Molded Rubber Products Application, Medical Gloves Application, Other Applications, Tires & Tubes Application, Gaskets & Seals Application and Wires & Cables Application for the Years 2014, 2025 & 2030
- TABLE 284: Iran Recent Past, Current & Future Analysis for Rubber Processing Aids and Anti-Tack Agents by End-Use - Automotive & Transportation End-Use, Building & Construction End-Use, Medical End-Use, Electronics & Electricals End-Use, Footwear End-Use and Other End-Uses - Independent Analysis of Annual Sales in US$ Thousand for the Years 2024 through 2030 and % CAGR
- TABLE 285: Iran Historic Review for Rubber Processing Aids and Anti-Tack Agents by End-Use - Automotive & Transportation End-Use, Building & Construction End-Use, Medical End-Use, Electronics & Electricals End-Use, Footwear End-Use and Other End-Uses Markets - Independent Analysis of Annual Sales in US$ Thousand for Years 2014 through 2023 and % CAGR
- TABLE 286: Iran 16-Year Perspective for Rubber Processing Aids and Anti-Tack Agents by End-Use - Percentage Breakdown of Value Sales for Automotive & Transportation End-Use, Building & Construction End-Use, Medical End-Use, Electronics & Electricals End-Use, Footwear End-Use and Other End-Uses for the Years 2014, 2025 & 2030
- ISRAEL
- TABLE 287: Israel Recent Past, Current & Future Analysis for Rubber Processing Aids and Anti-Tack Agents by Product Type - Fatty Acid Esters, Fatty Acid Amides, Stearates, Soaps, Silicone Polymers and Other Rubber Processing Aids & Anti-Tack Agents - Independent Analysis of Annual Sales in US$ Thousand for the Years 2024 through 2030 and % CAGR
- TABLE 288: Israel Historic Review for Rubber Processing Aids and Anti-Tack Agents by Product Type - Fatty Acid Esters, Fatty Acid Amides, Stearates, Soaps, Silicone Polymers and Other Rubber Processing Aids & Anti-Tack Agents Markets - Independent Analysis of Annual Sales in US$ Thousand for Years 2014 through 2023 and % CAGR
- TABLE 289: Israel 16-Year Perspective for Rubber Processing Aids and Anti-Tack Agents by Product Type - Percentage Breakdown of Value Sales for Fatty Acid Esters, Fatty Acid Amides, Stearates, Soaps, Silicone Polymers and Other Rubber Processing Aids & Anti-Tack Agents for the Years 2014, 2025 & 2030
- TABLE 290: Israel Recent Past, Current & Future Analysis for Rubber Processing Aids and Anti-Tack Agents by Application - Molded Rubber Products Application, Medical Gloves Application, Other Applications, Tires & Tubes Application, Gaskets & Seals Application and Wires & Cables Application - Independent Analysis of Annual Sales in US$ Thousand for the Years 2024 through 2030 and % CAGR
- TABLE 291: Israel Historic Review for Rubber Processing Aids and Anti-Tack Agents by Application - Molded Rubber Products Application, Medical Gloves Application, Other Applications, Tires & Tubes Application, Gaskets & Seals Application and Wires & Cables Application Markets - Independent Analysis of Annual Sales in US$ Thousand for Years 2014 through 2023 and % CAGR
- TABLE 292: Israel 16-Year Perspective for Rubber Processing Aids and Anti-Tack Agents by Application - Percentage Breakdown of Value Sales for Molded Rubber Products Application, Medical Gloves Application, Other Applications, Tires & Tubes Application, Gaskets & Seals Application and Wires & Cables Application for the Years 2014, 2025 & 2030
- TABLE 293: Israel Recent Past, Current & Future Analysis for Rubber Processing Aids and Anti-Tack Agents by End-Use - Automotive & Transportation End-Use, Building & Construction End-Use, Medical End-Use, Electronics & Electricals End-Use, Footwear End-Use and Other End-Uses - Independent Analysis of Annual Sales in US$ Thousand for the Years 2024 through 2030 and % CAGR
- TABLE 294: Israel Historic Review for Rubber Processing Aids and Anti-Tack Agents by End-Use - Automotive & Transportation End-Use, Building & Construction End-Use, Medical End-Use, Electronics & Electricals End-Use, Footwear End-Use and Other End-Uses Markets - Independent Analysis of Annual Sales in US$ Thousand for Years 2014 through 2023 and % CAGR
- TABLE 295: Israel 16-Year Perspective for Rubber Processing Aids and Anti-Tack Agents by End-Use - Percentage Breakdown of Value Sales for Automotive & Transportation End-Use, Building & Construction End-Use, Medical End-Use, Electronics & Electricals End-Use, Footwear End-Use and Other End-Uses for the Years 2014, 2025 & 2030
- SAUDI ARABIA
- TABLE 296: Saudi Arabia Recent Past, Current & Future Analysis for Rubber Processing Aids and Anti-Tack Agents by Product Type - Fatty Acid Esters, Fatty Acid Amides, Stearates, Soaps, Silicone Polymers and Other Rubber Processing Aids & Anti-Tack Agents - Independent Analysis of Annual Sales in US$ Thousand for the Years 2024 through 2030 and % CAGR
- TABLE 297: Saudi Arabia Historic Review for Rubber Processing Aids and Anti-Tack Agents by Product Type - Fatty Acid Esters, Fatty Acid Amides, Stearates, Soaps, Silicone Polymers and Other Rubber Processing Aids & Anti-Tack Agents Markets - Independent Analysis of Annual Sales in US$ Thousand for Years 2014 through 2023 and % CAGR
- TABLE 298: Saudi Arabia 16-Year Perspective for Rubber Processing Aids and Anti-Tack Agents by Product Type - Percentage Breakdown of Value Sales for Fatty Acid Esters, Fatty Acid Amides, Stearates, Soaps, Silicone Polymers and Other Rubber Processing Aids & Anti-Tack Agents for the Years 2014, 2025 & 2030
- TABLE 299: Saudi Arabia Recent Past, Current & Future Analysis for Rubber Processing Aids and Anti-Tack Agents by Application - Molded Rubber Products Application, Medical Gloves Application, Other Applications, Tires & Tubes Application, Gaskets & Seals Application and Wires & Cables Application - Independent Analysis of Annual Sales in US$ Thousand for the Years 2024 through 2030 and % CAGR
- TABLE 300: Saudi Arabia Historic Review for Rubber Processing Aids and Anti-Tack Agents by Application - Molded Rubber Products Application, Medical Gloves Application, Other Applications, Tires & Tubes Application, Gaskets & Seals Application and Wires & Cables Application Markets - Independent Analysis of Annual Sales in US$ Thousand for Years 2014 through 2023 and % CAGR
- TABLE 301: Saudi Arabia 16-Year Perspective for Rubber Processing Aids and Anti-Tack Agents by Application - Percentage Breakdown of Value Sales for Molded Rubber Products Application, Medical Gloves Application, Other Applications, Tires & Tubes Application, Gaskets & Seals Application and Wires & Cables Application for the Years 2014, 2025 & 2030
- TABLE 302: Saudi Arabia Recent Past, Current & Future Analysis for Rubber Processing Aids and Anti-Tack Agents by End-Use - Automotive & Transportation End-Use, Building & Construction End-Use, Medical End-Use, Electronics & Electricals End-Use, Footwear End-Use and Other End-Uses - Independent Analysis of Annual Sales in US$ Thousand for the Years 2024 through 2030 and % CAGR
- TABLE 303: Saudi Arabia Historic Review for Rubber Processing Aids and Anti-Tack Agents by End-Use - Automotive & Transportation End-Use, Building & Construction End-Use, Medical End-Use, Electronics & Electricals End-Use, Footwear End-Use and Other End-Uses Markets - Independent Analysis of Annual Sales in US$ Thousand for Years 2014 through 2023 and % CAGR
- TABLE 304: Saudi Arabia 16-Year Perspective for Rubber Processing Aids and Anti-Tack Agents by End-Use - Percentage Breakdown of Value Sales for Automotive & Transportation End-Use, Building & Construction End-Use, Medical End-Use, Electronics & Electricals End-Use, Footwear End-Use and Other End-Uses for the Years 2014, 2025 & 2030
- UNITED ARAB EMIRATES
- TABLE 305: UAE Recent Past, Current & Future Analysis for Rubber Processing Aids and Anti-Tack Agents by Product Type - Fatty Acid Esters, Fatty Acid Amides, Stearates, Soaps, Silicone Polymers and Other Rubber Processing Aids & Anti-Tack Agents - Independent Analysis of Annual Sales in US$ Thousand for the Years 2024 through 2030 and % CAGR
- TABLE 306: UAE Historic Review for Rubber Processing Aids and Anti-Tack Agents by Product Type - Fatty Acid Esters, Fatty Acid Amides, Stearates, Soaps, Silicone Polymers and Other Rubber Processing Aids & Anti-Tack Agents Markets - Independent Analysis of Annual Sales in US$ Thousand for Years 2014 through 2023 and % CAGR
- TABLE 307: UAE 16-Year Perspective for Rubber Processing Aids and Anti-Tack Agents by Product Type - Percentage Breakdown of Value Sales for Fatty Acid Esters, Fatty Acid Amides, Stearates, Soaps, Silicone Polymers and Other Rubber Processing Aids & Anti-Tack Agents for the Years 2014, 2025 & 2030
- TABLE 308: UAE Recent Past, Current & Future Analysis for Rubber Processing Aids and Anti-Tack Agents by Application - Molded Rubber Products Application, Medical Gloves Application, Other Applications, Tires & Tubes Application, Gaskets & Seals Application and Wires & Cables Application - Independent Analysis of Annual Sales in US$ Thousand for the Years 2024 through 2030 and % CAGR
- TABLE 309: UAE Historic Review for Rubber Processing Aids and Anti-Tack Agents by Application - Molded Rubber Products Application, Medical Gloves Application, Other Applications, Tires & Tubes Application, Gaskets & Seals Application and Wires & Cables Application Markets - Independent Analysis of Annual Sales in US$ Thousand for Years 2014 through 2023 and % CAGR
- TABLE 310: UAE 16-Year Perspective for Rubber Processing Aids and Anti-Tack Agents by Application - Percentage Breakdown of Value Sales for Molded Rubber Products Application, Medical Gloves Application, Other Applications, Tires & Tubes Application, Gaskets & Seals Application and Wires & Cables Application for the Years 2014, 2025 & 2030
- TABLE 311: UAE Recent Past, Current & Future Analysis for Rubber Processing Aids and Anti-Tack Agents by End-Use - Automotive & Transportation End-Use, Building & Construction End-Use, Medical End-Use, Electronics & Electricals End-Use, Footwear End-Use and Other End-Uses - Independent Analysis of Annual Sales in US$ Thousand for the Years 2024 through 2030 and % CAGR
- TABLE 312: UAE Historic Review for Rubber Processing Aids and Anti-Tack Agents by End-Use - Automotive & Transportation End-Use, Building & Construction End-Use, Medical End-Use, Electronics & Electricals End-Use, Footwear End-Use and Other End-Uses Markets - Independent Analysis of Annual Sales in US$ Thousand for Years 2014 through 2023 and % CAGR
- TABLE 313: UAE 16-Year Perspective for Rubber Processing Aids and Anti-Tack Agents by End-Use - Percentage Breakdown of Value Sales for Automotive & Transportation End-Use, Building & Construction End-Use, Medical End-Use, Electronics & Electricals End-Use, Footwear End-Use and Other End-Uses for the Years 2014, 2025 & 2030
- REST OF MIDDLE EAST
- TABLE 314: Rest of Middle East Recent Past, Current & Future Analysis for Rubber Processing Aids and Anti-Tack Agents by Product Type - Fatty Acid Esters, Fatty Acid Amides, Stearates, Soaps, Silicone Polymers and Other Rubber Processing Aids & Anti-Tack Agents - Independent Analysis of Annual Sales in US$ Thousand for the Years 2024 through 2030 and % CAGR
- TABLE 315: Rest of Middle East Historic Review for Rubber Processing Aids and Anti-Tack Agents by Product Type - Fatty Acid Esters, Fatty Acid Amides, Stearates, Soaps, Silicone Polymers and Other Rubber Processing Aids & Anti-Tack Agents Markets - Independent Analysis of Annual Sales in US$ Thousand for Years 2014 through 2023 and % CAGR
- TABLE 316: Rest of Middle East 16-Year Perspective for Rubber Processing Aids and Anti-Tack Agents by Product Type - Percentage Breakdown of Value Sales for Fatty Acid Esters, Fatty Acid Amides, Stearates, Soaps, Silicone Polymers and Other Rubber Processing Aids & Anti-Tack Agents for the Years 2014, 2025 & 2030
- TABLE 317: Rest of Middle East Recent Past, Current & Future Analysis for Rubber Processing Aids and Anti-Tack Agents by Application - Molded Rubber Products Application, Medical Gloves Application, Other Applications, Tires & Tubes Application, Gaskets & Seals Application and Wires & Cables Application - Independent Analysis of Annual Sales in US$ Thousand for the Years 2024 through 2030 and % CAGR
- TABLE 318: Rest of Middle East Historic Review for Rubber Processing Aids and Anti-Tack Agents by Application - Molded Rubber Products Application, Medical Gloves Application, Other Applications, Tires & Tubes Application, Gaskets & Seals Application and Wires & Cables Application Markets - Independent Analysis of Annual Sales in US$ Thousand for Years 2014 through 2023 and % CAGR
- TABLE 319: Rest of Middle East 16-Year Perspective for Rubber Processing Aids and Anti-Tack Agents by Application - Percentage Breakdown of Value Sales for Molded Rubber Products Application, Medical Gloves Application, Other Applications, Tires & Tubes Application, Gaskets & Seals Application and Wires & Cables Application for the Years 2014, 2025 & 2030
- TABLE 320: Rest of Middle East Recent Past, Current & Future Analysis for Rubber Processing Aids and Anti-Tack Agents by End-Use - Automotive & Transportation End-Use, Building & Construction End-Use, Medical End-Use, Electronics & Electricals End-Use, Footwear End-Use and Other End-Uses - Independent Analysis of Annual Sales in US$ Thousand for the Years 2024 through 2030 and % CAGR
- TABLE 321: Rest of Middle East Historic Review for Rubber Processing Aids and Anti-Tack Agents by End-Use - Automotive & Transportation End-Use, Building & Construction End-Use, Medical End-Use, Electronics & Electricals End-Use, Footwear End-Use and Other End-Uses Markets - Independent Analysis of Annual Sales in US$ Thousand for Years 2014 through 2023 and % CAGR
- TABLE 322: Rest of Middle East 16-Year Perspective for Rubber Processing Aids and Anti-Tack Agents by End-Use - Percentage Breakdown of Value Sales for Automotive & Transportation End-Use, Building & Construction End-Use, Medical End-Use, Electronics & Electricals End-Use, Footwear End-Use and Other End-Uses for the Years 2014, 2025 & 2030
- AFRICA
- Rubber Processing Aids and Anti-Tack Agents Market Presence - Strong/Active/Niche/Trivial - Key Competitors in Africa for 2025 (E)
- TABLE 323: Africa Recent Past, Current & Future Analysis for Rubber Processing Aids and Anti-Tack Agents by Product Type - Fatty Acid Esters, Fatty Acid Amides, Stearates, Soaps, Silicone Polymers and Other Rubber Processing Aids & Anti-Tack Agents - Independent Analysis of Annual Sales in US$ Thousand for the Years 2024 through 2030 and % CAGR
- TABLE 324: Africa Historic Review for Rubber Processing Aids and Anti-Tack Agents by Product Type - Fatty Acid Esters, Fatty Acid Amides, Stearates, Soaps, Silicone Polymers and Other Rubber Processing Aids & Anti-Tack Agents Markets - Independent Analysis of Annual Sales in US$ Thousand for Years 2014 through 2023 and % CAGR
- TABLE 325: Africa 16-Year Perspective for Rubber Processing Aids and Anti-Tack Agents by Product Type - Percentage Breakdown of Value Sales for Fatty Acid Esters, Fatty Acid Amides, Stearates, Soaps, Silicone Polymers and Other Rubber Processing Aids & Anti-Tack Agents for the Years 2014, 2025 & 2030
- TABLE 326: Africa Recent Past, Current & Future Analysis for Rubber Processing Aids and Anti-Tack Agents by Application - Molded Rubber Products Application, Medical Gloves Application, Other Applications, Tires & Tubes Application, Gaskets & Seals Application and Wires & Cables Application - Independent Analysis of Annual Sales in US$ Thousand for the Years 2024 through 2030 and % CAGR
- TABLE 327: Africa Historic Review for Rubber Processing Aids and Anti-Tack Agents by Application - Molded Rubber Products Application, Medical Gloves Application, Other Applications, Tires & Tubes Application, Gaskets & Seals Application and Wires & Cables Application Markets - Independent Analysis of Annual Sales in US$ Thousand for Years 2014 through 2023 and % CAGR
- TABLE 328: Africa 16-Year Perspective for Rubber Processing Aids and Anti-Tack Agents by Application - Percentage Breakdown of Value Sales for Molded Rubber Products Application, Medical Gloves Application, Other Applications, Tires & Tubes Application, Gaskets & Seals Application and Wires & Cables Application for the Years 2014, 2025 & 2030
- TABLE 329: Africa Recent Past, Current & Future Analysis for Rubber Processing Aids and Anti-Tack Agents by End-Use - Automotive & Transportation End-Use, Building & Construction End-Use, Medical End-Use, Electronics & Electricals End-Use, Footwear End-Use and Other End-Uses - Independent Analysis of Annual Sales in US$ Thousand for the Years 2024 through 2030 and % CAGR
- TABLE 330: Africa Historic Review for Rubber Processing Aids and Anti-Tack Agents by End-Use - Automotive & Transportation End-Use, Building & Construction End-Use, Medical End-Use, Electronics & Electricals End-Use, Footwear End-Use and Other End-Uses Markets - Independent Analysis of Annual Sales in US$ Thousand for Years 2014 through 2023 and % CAGR
- TABLE 331: Africa 16-Year Perspective for Rubber Processing Aids and Anti-Tack Agents by End-Use - Percentage Breakdown of Value Sales for Automotive & Transportation End-Use, Building & Construction End-Use, Medical End-Use, Electronics & Electricals End-Use, Footwear End-Use and Other End-Uses for the Years 2014, 2025 & 2030
- IV. COMPETITION
Pricing
Currency Rates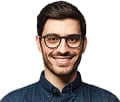