
Polypropylene Random Copolymer and High-Density Polyethylene
Description
Global Polypropylene Random Copolymer and High-Density Polyethylene Market to Reach US$109.0 Billion by 2030
The global market for Polypropylene Random Copolymer and High-Density Polyethylene estimated at US$83.5 Billion in the year 2024, is expected to reach US$109.0 Billion by 2030, growing at a CAGR of 4.6% over the analysis period 2024-2030. High-Density Polyethylene, one of the segments analyzed in the report, is expected to record a 3.7% CAGR and reach US$64.5 Billion by the end of the analysis period. Growth in the Polypropylene Random Copolymer segment is estimated at 5.9% CAGR over the analysis period.
The U.S. Market is Estimated at US$22.7 Billion While China is Forecast to Grow at 7.1% CAGR
The Polypropylene Random Copolymer and High-Density Polyethylene market in the U.S. is estimated at US$22.7 Billion in the year 2024. China, the world`s second largest economy, is forecast to reach a projected market size of US$21.2 Billion by the year 2030 trailing a CAGR of 7.1% over the analysis period 2024-2030. Among the other noteworthy geographic markets are Japan and Canada, each forecast to grow at a CAGR of 2.2% and 4.5% respectively over the analysis period. Within Europe, Germany is forecast to grow at approximately 2.9% CAGR.
Global Polypropylene Random Copolymer and High-Density Polyethylene Market - Key Trends & Drivers Summarized
Synergizing Rigidity and Resilience: How Polyolefins Are Structuring the Future of Lightweight and Durable Material Applications
What Distinguishes Polypropylene Random Copolymer and HDPE in the Competitive Polymer Landscape?
Polypropylene Random Copolymer (PPR-C) and High-Density Polyethylene (HDPE) represent two widely adopted polyolefins used across packaging, piping, medical, automotive, and industrial component applications. While both materials are derived from hydrocarbon polymerization, their distinct molecular architectures deliver divergent performance characteristics. PPR-C is synthesized by random incorporation of ethylene into a polypropylene chain, resulting in improved impact strength, optical clarity, and weldability. This makes it highly suitable for hot and cold fluid transport, medical containers, and blow-molded consumer goods. HDPE, on the other hand, features a highly linear polymer chain with minimal branching. Its crystalline structure imparts high tensile strength, rigidity, and chemical resistance, making it ideal for heavy-duty piping, structural containers, fuel tanks, geomembranes, and protective casing. Unlike flexible low-density polyethylene (LDPE), HDPE exhibits superior environmental stress cracking resistance (ESCR), long-term durability, and stiffness under mechanical loads. While each resin type finds use in separate applications, they often complement each other within integrated systems. For example, PPR-C is used for internal piping while HDPE is employed for outer structural or insulation layers. Their recyclability, availability in food- and medical-grade formulations, and processing compatibility with extrusion, blow molding, and injection molding platforms make them indispensable across value chains.
Where Are These Polyolefins Creating the Most Value Across Industry Use Cases?
The PPR-C segment finds extensive usage in hot and cold water piping systems, particularly in commercial and residential construction. Its low thermal conductivity, excellent weldability via heat fusion, and resistance to scaling and corrosion make it ideal for central heating networks, clean water supply lines, and chemical fluid systems. In medical packaging, PPR-C is used in IV bottles, specimen containers, and injection systems due to its clarity, sterility retention, and compatibility with gamma sterilization. In consumer product manufacturing, PPR-C’s transparency and stress crack resistance allow it to replace polystyrene or polycarbonate in transparent food containers, cosmetic jars, and beverage caps. The material`s low odor and taste interaction make it preferred for dairy and baby food packaging. PPR-C’s soft feel and enhanced impact behavior are leveraged in toys, lightweight luggage, and durable packaging.
HDPE dominates the landscape for applications requiring long-term performance under stress and exposure. Its use in municipal water mains, gas distribution lines, and underground sewer networks is well-established due to its chemical inertness and resistance to ground movement. In packaging, HDPE is the material of choice for detergent bottles, milk jugs, drums, and crates where dimensional stability, stackability, and drop resistance are critical. HDPE’s lightweight and high-rigidity characteristics make it suitable for automotive parts like fuel tanks, fender liners, and battery enclosures. It is also widely used in agriculture-for irrigation pipes, silage films, and pesticide containers-as well as in electronics for cable jacketing and insulation layers. Its UV resistance and barrier properties have also positioned it favorably in geomembrane and outdoor furniture markets.
How Are Manufacturers Enhancing Performance and Sustainability Across These Polymer Segments?
Material innovation in both PPR-C and HDPE is focused on enhancing application specificity while meeting evolving regulatory and performance expectations. For PPR-C, copolymer ratio optimization is enabling tailored flexibility, transparency, and weld strength. Crosslinking additives and UV stabilizers are being introduced for better outdoor stability and higher service temperatures, extending use into solar piping and green roofing membranes. High-flow variants of PPR-C are being developed for faster cycle times in thin-wall molding applications. Nucleating agents are added to control crystallinity and improve dimensional precision in large-scale pipe production. Medical-grade PPR-C is undergoing enhancements for biocompatibility, low extractables, and sterilization compatibility, particularly for prefilled syringe components and diagnostic systems.
HDPE is witnessing notable improvements in barrier performance, rigidity, and processability. Bimodal HDPE grades with broad molecular weight distribution are improving resistance to slow crack growth and pressure fatigue in large-diameter pipes. Multilayer co-extrusion technologies are being used to develop HDPE-based packaging with oxygen or moisture barriers by combining EVOH or tie layers. Carbon black and UV absorber additives are being used to protect outdoor HDPE applications from degradation. Recyclability is a major focus area. Manufacturers are integrating post-consumer recycled (PCR) content into HDPE and PPR-C packaging formats without compromising strength or food contact compliance. Chain extenders, compatibilizers, and purification additives are being used to restore molecular integrity in recycled blends. Moreover, closed-loop recycling programs for industrial containers and PE pipe scrap are helping downstream industries align with circular economy targets.
What Market Forces Are Driving the Global Expansion of PPR-C and HDPE Applications?
The growth in the polypropylene random copolymer and high-density polyethylene market is driven by several converging trends related to urbanization, sustainability mandates, packaging diversification, and cost-performance optimization. A key driver is the expanding infrastructure investment in developing regions where both PPR-C and HDPE pipes are being deployed for water transmission, gas distribution, and wastewater management. PPR-C’s cost-effectiveness, chemical inertness, and long lifecycle are supporting water safety initiatives, while HDPE’s robust fatigue resistance is being harnessed for underground and pressurized pipelines. The global demand for lightweight, durable, and chemically safe packaging is accelerating usage of both polyolefins. HDPE’s stiffness and moisture barrier properties are critical for homecare, industrial, and pharmaceutical packaging. Meanwhile, PPR-C is increasingly being used in premium product lines seeking clear or translucent packaging with enhanced performance attributes.
In automotive and transport sectors, the electrification trend is pushing designers to adopt lightweight, corrosion-resistant polymers like HDPE for battery encasements and electronic housings. The regulatory shift toward Extended Producer Responsibility (EPR) and material recyclability in North America and Europe is fostering preference for mono-material solutions made from HDPE or PPR-C, which offer excellent recyclability profiles and process consistency. Medical packaging and diagnostic device sectors are also turning to PPR-C for sterility retention, drug compatibility, and sustainability. Growth in home diagnostics, vaccine storage, and IV delivery systems are creating high-value demand for gamma-stable, high-purity PPR-C resins.
On the industrial side, HDPE is increasingly used in geomembranes, agricultural films, and container linings where durability, UV resistance, and low permeability are essential. Sustainability-focused building projects are incorporating both materials in HVAC ducting, insulated piping, and weather-resistant building panels. Strategic expansions by resin producers, investment in compounding infrastructure, and growing participation from recycling firms are reinforcing the supply landscape. As industries continue to prioritize materials that balance durability, lightweight performance, and environmental compliance, both PPR-C and HDPE are positioned for sustained growth across global markets.
SCOPE OF STUDY:The report analyzes the Polypropylene Random Copolymer and High-Density Polyethylene market in terms of units by the following Segments, and Geographic Regions/Countries:
Segments:
Type (High-Density Polyethylene, Polypropylene Random Copolymer); Application (Packaging Application, Healthcare Application, Construction Application, Other Applications)
Geographic Regions/Countries:
World; United States; Canada; Japan; China; Europe (France; Germany; Italy; United Kingdom; Spain; Russia; and Rest of Europe); Asia-Pacific (Australia; India; South Korea; and Rest of Asia-Pacific); Latin America (Argentina; Brazil; Mexico; and Rest of Latin America); Middle East (Iran; Israel; Saudi Arabia; United Arab Emirates; and Rest of Middle East); and Africa.
Select Competitors (Total 34 Featured) -
- AGRU Kunststofftechnik
- Aliaxis Group S.A.
- Aquatherm GmbH
- Borealis AG
- Braskem S.A.
- Chevron Phillips Chemical Company LLC
- China Lesso Group Holdings Ltd.
- ExxonMobil Corporation
- Formosa Plastics Corporation
- GEORG FISCHER (GF Piping Systems)
- INEOS Group Holdings S.A.
- Lotte Chemical Titan Holding Sdn Bhd
- LyondellBasell Industries N.V.
- Mitsui Chemicals, Inc.
- PetroChina Company Limited
- Pipelife International GmbH
- Reliance Industries Limited
- SABIC (Saudi Basic Industries Corporation)
- Sinopec (China Petrochemical Corporation)
- TotalEnergies SE
- Westlake Chemical Corporation
We`re transforming market and competitive intelligence with validated expert content and AI tools.
Instead of following the general norm of querying LLMs and Industry-specific SLMs, we built repositories of content curated from domain experts worldwide including video transcripts, blogs, search engines research, and massive amounts of enterprise, product/service, and market data.
TARIFF IMPACT FACTOR
Our new release incorporates impact of tariffs on geographical markets as we predict a shift in competitiveness of companies based on HQ country, manufacturing base, exports and imports (finished goods and OEM). This intricate and multifaceted market reality will impact competitors by increasing the Cost of Goods Sold (COGS), reducing profitability, reconfiguring supply chains, amongst other micro and macro market dynamics.
Please note: Reports are sold as single-site single-user licenses. Electronic versions require 24-48 hours as each copy is customized to the client with digital controls and custom watermarks. The Publisher uses digital controls protecting against copying and printing is restricted to one full copy to be used at the same location.
The latest version of Adobe Acrobat Reader is required to view the report. Upon ordering an electronic version, the Publisher will provide a link to download the purchased report.
Prior to fulfillment of an order, the client will be required to sign a document detailing the purchase terms for a publication from this publisher.
Table of Contents
- I. METHODOLOGY
- II. EXECUTIVE SUMMARY
- 1. MARKET OVERVIEW
- Influencer Market Insights
- World Market Trajectories
- Tariff Impact on Global Supply Chain Patterns
- Polypropylene Random Copolymer and High-Density Polyethylene – Global Key Competitors Percentage Market Share in 2025 (E)
- Competitive Market Presence - Strong/Active/Niche/Trivial for Players Worldwide in 2025 (E)
- 2. FOCUS ON SELECT PLAYERS
- 3. MARKET TRENDS & DRIVERS
- Rising Demand for Multi-Utility Plumbing Systems Expands Scope for Dual Material Use
- Superior Chemical Resistance and Mechanical Properties Propel Adoption in Industrial Applications
- Advancements in Copolymer Blending Technology Strengthen Business Case for Hybrid Piping Systems
- Rapid Urbanization and Industrialization Drive Growth in Infrastructure-Based Piping
- Energy-Efficient Manufacturing Processes Throw the Spotlight on Low-Emission Polyolefin Products
- Growth in Potable Water Distribution and Wastewater Management Systems Promotes Material Diversification
- Regulatory Compliance for Food-Grade and Contact-Safe Materials Sustains Product Usage in Water Supply
- Increased Focus on Lightweight and Durable Materials Encourages Substitution of Metal Piping
- Market Preference for High Flow Rates and Pressure Ratings Drives Shift Toward HDPE
- Push for Cost-Efficient Pipeline Installation in Remote Regions Promotes Polyolefin-Based Systems
- Technological Innovation in Heat Fusion and Welding Enhances Field Performance and Reliability
- Increased Adoption in Gas Transmission and Irrigation Expands Application Spectrum
- Integration of Antibacterial and UV-Stabilized Layers Adds Value in Harsh Environments
- Government Incentives for Rural Infrastructure and Sanitation Spur Regional Demand
- Growth in Process Cooling and District Heating Networks Supports Material Compatibility
- Investment in Advanced Manufacturing and Automation Drives Consistency in Product Quality
- Sustainability Goals Among Developers Favor Recyclable, Long-Life Thermoplastics
- Cross-Compatibility With Smart Meters and IoT-Enabled Valves Enables Smart Infrastructure Integration
- Rising Cost of Traditional Piping Materials Drives Competitive Substitution by HDPE and PPR-C
- Collaborations Between Resin Manufacturers and Pipe Extruders Fuel Product Innovation and Customization
- 4. GLOBAL MARKET PERSPECTIVE
- TABLE 1: World Polypropylene Random Copolymer and High-Density Polyethylene Market Analysis of Annual Sales in US$ Million for Years 2014 through 2030
- TABLE 2: World Recent Past, Current & Future Analysis for Polypropylene Random Copolymer and High-Density Polyethylene by Geographic Region - USA, Canada, Japan, China, Europe, Asia-Pacific, Latin America, Middle East and Africa Markets - Independent Analysis of Annual Sales in US$ Million for Years 2024 through 2030 and % CAGR
- TABLE 3: World Historic Review for Polypropylene Random Copolymer and High-Density Polyethylene by Geographic Region - USA, Canada, Japan, China, Europe, Asia-Pacific, Latin America, Middle East and Africa Markets - Independent Analysis of Annual Sales in US$ Million for Years 2014 through 2023 and % CAGR
- TABLE 4: World 16-Year Perspective for Polypropylene Random Copolymer and High-Density Polyethylene by Geographic Region - Percentage Breakdown of Value Sales for USA, Canada, Japan, China, Europe, Asia-Pacific, Latin America, Middle East and Africa Markets for Years 2014, 2025 & 2030
- TABLE 5: World Recent Past, Current & Future Analysis for High-Density Polyethylene by Geographic Region - USA, Canada, Japan, China, Europe, Asia-Pacific, Latin America, Middle East and Africa Markets - Independent Analysis of Annual Sales in US$ Million for Years 2024 through 2030 and % CAGR
- TABLE 6: World Historic Review for High-Density Polyethylene by Geographic Region - USA, Canada, Japan, China, Europe, Asia-Pacific, Latin America, Middle East and Africa Markets - Independent Analysis of Annual Sales in US$ Million for Years 2014 through 2023 and % CAGR
- TABLE 7: World 16-Year Perspective for High-Density Polyethylene by Geographic Region - Percentage Breakdown of Value Sales for USA, Canada, Japan, China, Europe, Asia-Pacific, Latin America, Middle East and Africa for Years 2014, 2025 & 2030
- TABLE 8: World Recent Past, Current & Future Analysis for Polypropylene Random Copolymer by Geographic Region - USA, Canada, Japan, China, Europe, Asia-Pacific, Latin America, Middle East and Africa Markets - Independent Analysis of Annual Sales in US$ Million for Years 2024 through 2030 and % CAGR
- TABLE 9: World Historic Review for Polypropylene Random Copolymer by Geographic Region - USA, Canada, Japan, China, Europe, Asia-Pacific, Latin America, Middle East and Africa Markets - Independent Analysis of Annual Sales in US$ Million for Years 2014 through 2023 and % CAGR
- TABLE 10: World 16-Year Perspective for Polypropylene Random Copolymer by Geographic Region - Percentage Breakdown of Value Sales for USA, Canada, Japan, China, Europe, Asia-Pacific, Latin America, Middle East and Africa for Years 2014, 2025 & 2030
- TABLE 11: World Recent Past, Current & Future Analysis for Packaging Application by Geographic Region - USA, Canada, Japan, China, Europe, Asia-Pacific, Latin America, Middle East and Africa Markets - Independent Analysis of Annual Sales in US$ Million for Years 2024 through 2030 and % CAGR
- TABLE 12: World Historic Review for Packaging Application by Geographic Region - USA, Canada, Japan, China, Europe, Asia-Pacific, Latin America, Middle East and Africa Markets - Independent Analysis of Annual Sales in US$ Million for Years 2014 through 2023 and % CAGR
- TABLE 13: World 16-Year Perspective for Packaging Application by Geographic Region - Percentage Breakdown of Value Sales for USA, Canada, Japan, China, Europe, Asia-Pacific, Latin America, Middle East and Africa for Years 2014, 2025 & 2030
- TABLE 14: World Recent Past, Current & Future Analysis for Healthcare Application by Geographic Region - USA, Canada, Japan, China, Europe, Asia-Pacific, Latin America, Middle East and Africa Markets - Independent Analysis of Annual Sales in US$ Million for Years 2024 through 2030 and % CAGR
- TABLE 15: World Historic Review for Healthcare Application by Geographic Region - USA, Canada, Japan, China, Europe, Asia-Pacific, Latin America, Middle East and Africa Markets - Independent Analysis of Annual Sales in US$ Million for Years 2014 through 2023 and % CAGR
- TABLE 16: World 16-Year Perspective for Healthcare Application by Geographic Region - Percentage Breakdown of Value Sales for USA, Canada, Japan, China, Europe, Asia-Pacific, Latin America, Middle East and Africa for Years 2014, 2025 & 2030
- TABLE 17: World Recent Past, Current & Future Analysis for Construction Application by Geographic Region - USA, Canada, Japan, China, Europe, Asia-Pacific, Latin America, Middle East and Africa Markets - Independent Analysis of Annual Sales in US$ Million for Years 2024 through 2030 and % CAGR
- TABLE 18: World Historic Review for Construction Application by Geographic Region - USA, Canada, Japan, China, Europe, Asia-Pacific, Latin America, Middle East and Africa Markets - Independent Analysis of Annual Sales in US$ Million for Years 2014 through 2023 and % CAGR
- TABLE 19: World 16-Year Perspective for Construction Application by Geographic Region - Percentage Breakdown of Value Sales for USA, Canada, Japan, China, Europe, Asia-Pacific, Latin America, Middle East and Africa for Years 2014, 2025 & 2030
- TABLE 20: World Recent Past, Current & Future Analysis for Other Applications by Geographic Region - USA, Canada, Japan, China, Europe, Asia-Pacific, Latin America, Middle East and Africa Markets - Independent Analysis of Annual Sales in US$ Million for Years 2024 through 2030 and % CAGR
- TABLE 21: World Historic Review for Other Applications by Geographic Region - USA, Canada, Japan, China, Europe, Asia-Pacific, Latin America, Middle East and Africa Markets - Independent Analysis of Annual Sales in US$ Million for Years 2014 through 2023 and % CAGR
- TABLE 22: World 16-Year Perspective for Other Applications by Geographic Region - Percentage Breakdown of Value Sales for USA, Canada, Japan, China, Europe, Asia-Pacific, Latin America, Middle East and Africa for Years 2014, 2025 & 2030
- III. MARKET ANALYSIS
- UNITED STATES
- Polypropylene Random Copolymer and High-Density Polyethylene Market Presence - Strong/Active/Niche/Trivial - Key Competitors in the United States for 2025 (E)
- TABLE 23: USA Recent Past, Current & Future Analysis for Polypropylene Random Copolymer and High-Density Polyethylene by Type - High-Density Polyethylene and Polypropylene Random Copolymer - Independent Analysis of Annual Sales in US$ Million for the Years 2024 through 2030 and % CAGR
- TABLE 24: USA Historic Review for Polypropylene Random Copolymer and High-Density Polyethylene by Type - High-Density Polyethylene and Polypropylene Random Copolymer Markets - Independent Analysis of Annual Sales in US$ Million for Years 2014 through 2023 and % CAGR
- TABLE 25: USA 16-Year Perspective for Polypropylene Random Copolymer and High-Density Polyethylene by Type - Percentage Breakdown of Value Sales for High-Density Polyethylene and Polypropylene Random Copolymer for the Years 2014, 2025 & 2030
- TABLE 26: USA Recent Past, Current & Future Analysis for Polypropylene Random Copolymer and High-Density Polyethylene by Application - Packaging Application, Healthcare Application, Construction Application and Other Applications - Independent Analysis of Annual Sales in US$ Million for the Years 2024 through 2030 and % CAGR
- TABLE 27: USA Historic Review for Polypropylene Random Copolymer and High-Density Polyethylene by Application - Packaging Application, Healthcare Application, Construction Application and Other Applications Markets - Independent Analysis of Annual Sales in US$ Million for Years 2014 through 2023 and % CAGR
- TABLE 28: USA 16-Year Perspective for Polypropylene Random Copolymer and High-Density Polyethylene by Application - Percentage Breakdown of Value Sales for Packaging Application, Healthcare Application, Construction Application and Other Applications for the Years 2014, 2025 & 2030
- CANADA
- TABLE 29: Canada Recent Past, Current & Future Analysis for Polypropylene Random Copolymer and High-Density Polyethylene by Type - High-Density Polyethylene and Polypropylene Random Copolymer - Independent Analysis of Annual Sales in US$ Million for the Years 2024 through 2030 and % CAGR
- TABLE 30: Canada Historic Review for Polypropylene Random Copolymer and High-Density Polyethylene by Type - High-Density Polyethylene and Polypropylene Random Copolymer Markets - Independent Analysis of Annual Sales in US$ Million for Years 2014 through 2023 and % CAGR
- TABLE 31: Canada 16-Year Perspective for Polypropylene Random Copolymer and High-Density Polyethylene by Type - Percentage Breakdown of Value Sales for High-Density Polyethylene and Polypropylene Random Copolymer for the Years 2014, 2025 & 2030
- TABLE 32: Canada Recent Past, Current & Future Analysis for Polypropylene Random Copolymer and High-Density Polyethylene by Application - Packaging Application, Healthcare Application, Construction Application and Other Applications - Independent Analysis of Annual Sales in US$ Million for the Years 2024 through 2030 and % CAGR
- TABLE 33: Canada Historic Review for Polypropylene Random Copolymer and High-Density Polyethylene by Application - Packaging Application, Healthcare Application, Construction Application and Other Applications Markets - Independent Analysis of Annual Sales in US$ Million for Years 2014 through 2023 and % CAGR
- TABLE 34: Canada 16-Year Perspective for Polypropylene Random Copolymer and High-Density Polyethylene by Application - Percentage Breakdown of Value Sales for Packaging Application, Healthcare Application, Construction Application and Other Applications for the Years 2014, 2025 & 2030
- JAPAN
- Polypropylene Random Copolymer and High-Density Polyethylene Market Presence - Strong/Active/Niche/Trivial - Key Competitors in Japan for 2025 (E)
- TABLE 35: Japan Recent Past, Current & Future Analysis for Polypropylene Random Copolymer and High-Density Polyethylene by Type - High-Density Polyethylene and Polypropylene Random Copolymer - Independent Analysis of Annual Sales in US$ Million for the Years 2024 through 2030 and % CAGR
- TABLE 36: Japan Historic Review for Polypropylene Random Copolymer and High-Density Polyethylene by Type - High-Density Polyethylene and Polypropylene Random Copolymer Markets - Independent Analysis of Annual Sales in US$ Million for Years 2014 through 2023 and % CAGR
- TABLE 37: Japan 16-Year Perspective for Polypropylene Random Copolymer and High-Density Polyethylene by Type - Percentage Breakdown of Value Sales for High-Density Polyethylene and Polypropylene Random Copolymer for the Years 2014, 2025 & 2030
- TABLE 38: Japan Recent Past, Current & Future Analysis for Polypropylene Random Copolymer and High-Density Polyethylene by Application - Packaging Application, Healthcare Application, Construction Application and Other Applications - Independent Analysis of Annual Sales in US$ Million for the Years 2024 through 2030 and % CAGR
- TABLE 39: Japan Historic Review for Polypropylene Random Copolymer and High-Density Polyethylene by Application - Packaging Application, Healthcare Application, Construction Application and Other Applications Markets - Independent Analysis of Annual Sales in US$ Million for Years 2014 through 2023 and % CAGR
- TABLE 40: Japan 16-Year Perspective for Polypropylene Random Copolymer and High-Density Polyethylene by Application - Percentage Breakdown of Value Sales for Packaging Application, Healthcare Application, Construction Application and Other Applications for the Years 2014, 2025 & 2030
- CHINA
- Polypropylene Random Copolymer and High-Density Polyethylene Market Presence - Strong/Active/Niche/Trivial - Key Competitors in China for 2025 (E)
- TABLE 41: China Recent Past, Current & Future Analysis for Polypropylene Random Copolymer and High-Density Polyethylene by Type - High-Density Polyethylene and Polypropylene Random Copolymer - Independent Analysis of Annual Sales in US$ Million for the Years 2024 through 2030 and % CAGR
- TABLE 42: China Historic Review for Polypropylene Random Copolymer and High-Density Polyethylene by Type - High-Density Polyethylene and Polypropylene Random Copolymer Markets - Independent Analysis of Annual Sales in US$ Million for Years 2014 through 2023 and % CAGR
- TABLE 43: China 16-Year Perspective for Polypropylene Random Copolymer and High-Density Polyethylene by Type - Percentage Breakdown of Value Sales for High-Density Polyethylene and Polypropylene Random Copolymer for the Years 2014, 2025 & 2030
- TABLE 44: China Recent Past, Current & Future Analysis for Polypropylene Random Copolymer and High-Density Polyethylene by Application - Packaging Application, Healthcare Application, Construction Application and Other Applications - Independent Analysis of Annual Sales in US$ Million for the Years 2024 through 2030 and % CAGR
- TABLE 45: China Historic Review for Polypropylene Random Copolymer and High-Density Polyethylene by Application - Packaging Application, Healthcare Application, Construction Application and Other Applications Markets - Independent Analysis of Annual Sales in US$ Million for Years 2014 through 2023 and % CAGR
- TABLE 46: China 16-Year Perspective for Polypropylene Random Copolymer and High-Density Polyethylene by Application - Percentage Breakdown of Value Sales for Packaging Application, Healthcare Application, Construction Application and Other Applications for the Years 2014, 2025 & 2030
- EUROPE
- Polypropylene Random Copolymer and High-Density Polyethylene Market Presence - Strong/Active/Niche/Trivial - Key Competitors in Europe for 2025 (E)
- TABLE 47: Europe Recent Past, Current & Future Analysis for Polypropylene Random Copolymer and High-Density Polyethylene by Geographic Region - France, Germany, Italy, UK, Spain, Russia and Rest of Europe Markets - Independent Analysis of Annual Sales in US$ Million for Years 2024 through 2030 and % CAGR
- TABLE 48: Europe Historic Review for Polypropylene Random Copolymer and High-Density Polyethylene by Geographic Region - France, Germany, Italy, UK, Spain, Russia and Rest of Europe Markets - Independent Analysis of Annual Sales in US$ Million for Years 2014 through 2023 and % CAGR
- TABLE 49: Europe 16-Year Perspective for Polypropylene Random Copolymer and High-Density Polyethylene by Geographic Region - Percentage Breakdown of Value Sales for France, Germany, Italy, UK, Spain, Russia and Rest of Europe Markets for Years 2014, 2025 & 2030
- TABLE 50: Europe Recent Past, Current & Future Analysis for Polypropylene Random Copolymer and High-Density Polyethylene by Type - High-Density Polyethylene and Polypropylene Random Copolymer - Independent Analysis of Annual Sales in US$ Million for the Years 2024 through 2030 and % CAGR
- TABLE 51: Europe Historic Review for Polypropylene Random Copolymer and High-Density Polyethylene by Type - High-Density Polyethylene and Polypropylene Random Copolymer Markets - Independent Analysis of Annual Sales in US$ Million for Years 2014 through 2023 and % CAGR
- TABLE 52: Europe 16-Year Perspective for Polypropylene Random Copolymer and High-Density Polyethylene by Type - Percentage Breakdown of Value Sales for High-Density Polyethylene and Polypropylene Random Copolymer for the Years 2014, 2025 & 2030
- TABLE 53: Europe Recent Past, Current & Future Analysis for Polypropylene Random Copolymer and High-Density Polyethylene by Application - Packaging Application, Healthcare Application, Construction Application and Other Applications - Independent Analysis of Annual Sales in US$ Million for the Years 2024 through 2030 and % CAGR
- TABLE 54: Europe Historic Review for Polypropylene Random Copolymer and High-Density Polyethylene by Application - Packaging Application, Healthcare Application, Construction Application and Other Applications Markets - Independent Analysis of Annual Sales in US$ Million for Years 2014 through 2023 and % CAGR
- TABLE 55: Europe 16-Year Perspective for Polypropylene Random Copolymer and High-Density Polyethylene by Application - Percentage Breakdown of Value Sales for Packaging Application, Healthcare Application, Construction Application and Other Applications for the Years 2014, 2025 & 2030
- FRANCE
- Polypropylene Random Copolymer and High-Density Polyethylene Market Presence - Strong/Active/Niche/Trivial - Key Competitors in France for 2025 (E)
- TABLE 56: France Recent Past, Current & Future Analysis for Polypropylene Random Copolymer and High-Density Polyethylene by Type - High-Density Polyethylene and Polypropylene Random Copolymer - Independent Analysis of Annual Sales in US$ Million for the Years 2024 through 2030 and % CAGR
- TABLE 57: France Historic Review for Polypropylene Random Copolymer and High-Density Polyethylene by Type - High-Density Polyethylene and Polypropylene Random Copolymer Markets - Independent Analysis of Annual Sales in US$ Million for Years 2014 through 2023 and % CAGR
- TABLE 58: France 16-Year Perspective for Polypropylene Random Copolymer and High-Density Polyethylene by Type - Percentage Breakdown of Value Sales for High-Density Polyethylene and Polypropylene Random Copolymer for the Years 2014, 2025 & 2030
- TABLE 59: France Recent Past, Current & Future Analysis for Polypropylene Random Copolymer and High-Density Polyethylene by Application - Packaging Application, Healthcare Application, Construction Application and Other Applications - Independent Analysis of Annual Sales in US$ Million for the Years 2024 through 2030 and % CAGR
- TABLE 60: France Historic Review for Polypropylene Random Copolymer and High-Density Polyethylene by Application - Packaging Application, Healthcare Application, Construction Application and Other Applications Markets - Independent Analysis of Annual Sales in US$ Million for Years 2014 through 2023 and % CAGR
- TABLE 61: France 16-Year Perspective for Polypropylene Random Copolymer and High-Density Polyethylene by Application - Percentage Breakdown of Value Sales for Packaging Application, Healthcare Application, Construction Application and Other Applications for the Years 2014, 2025 & 2030
- GERMANY
- Polypropylene Random Copolymer and High-Density Polyethylene Market Presence - Strong/Active/Niche/Trivial - Key Competitors in Germany for 2025 (E)
- TABLE 62: Germany Recent Past, Current & Future Analysis for Polypropylene Random Copolymer and High-Density Polyethylene by Type - High-Density Polyethylene and Polypropylene Random Copolymer - Independent Analysis of Annual Sales in US$ Million for the Years 2024 through 2030 and % CAGR
- TABLE 63: Germany Historic Review for Polypropylene Random Copolymer and High-Density Polyethylene by Type - High-Density Polyethylene and Polypropylene Random Copolymer Markets - Independent Analysis of Annual Sales in US$ Million for Years 2014 through 2023 and % CAGR
- TABLE 64: Germany 16-Year Perspective for Polypropylene Random Copolymer and High-Density Polyethylene by Type - Percentage Breakdown of Value Sales for High-Density Polyethylene and Polypropylene Random Copolymer for the Years 2014, 2025 & 2030
- TABLE 65: Germany Recent Past, Current & Future Analysis for Polypropylene Random Copolymer and High-Density Polyethylene by Application - Packaging Application, Healthcare Application, Construction Application and Other Applications - Independent Analysis of Annual Sales in US$ Million for the Years 2024 through 2030 and % CAGR
- TABLE 66: Germany Historic Review for Polypropylene Random Copolymer and High-Density Polyethylene by Application - Packaging Application, Healthcare Application, Construction Application and Other Applications Markets - Independent Analysis of Annual Sales in US$ Million for Years 2014 through 2023 and % CAGR
- TABLE 67: Germany 16-Year Perspective for Polypropylene Random Copolymer and High-Density Polyethylene by Application - Percentage Breakdown of Value Sales for Packaging Application, Healthcare Application, Construction Application and Other Applications for the Years 2014, 2025 & 2030
- ITALY
- TABLE 68: Italy Recent Past, Current & Future Analysis for Polypropylene Random Copolymer and High-Density Polyethylene by Type - High-Density Polyethylene and Polypropylene Random Copolymer - Independent Analysis of Annual Sales in US$ Million for the Years 2024 through 2030 and % CAGR
- TABLE 69: Italy Historic Review for Polypropylene Random Copolymer and High-Density Polyethylene by Type - High-Density Polyethylene and Polypropylene Random Copolymer Markets - Independent Analysis of Annual Sales in US$ Million for Years 2014 through 2023 and % CAGR
- TABLE 70: Italy 16-Year Perspective for Polypropylene Random Copolymer and High-Density Polyethylene by Type - Percentage Breakdown of Value Sales for High-Density Polyethylene and Polypropylene Random Copolymer for the Years 2014, 2025 & 2030
- TABLE 71: Italy Recent Past, Current & Future Analysis for Polypropylene Random Copolymer and High-Density Polyethylene by Application - Packaging Application, Healthcare Application, Construction Application and Other Applications - Independent Analysis of Annual Sales in US$ Million for the Years 2024 through 2030 and % CAGR
- TABLE 72: Italy Historic Review for Polypropylene Random Copolymer and High-Density Polyethylene by Application - Packaging Application, Healthcare Application, Construction Application and Other Applications Markets - Independent Analysis of Annual Sales in US$ Million for Years 2014 through 2023 and % CAGR
- TABLE 73: Italy 16-Year Perspective for Polypropylene Random Copolymer and High-Density Polyethylene by Application - Percentage Breakdown of Value Sales for Packaging Application, Healthcare Application, Construction Application and Other Applications for the Years 2014, 2025 & 2030
- UNITED KINGDOM
- Polypropylene Random Copolymer and High-Density Polyethylene Market Presence - Strong/Active/Niche/Trivial - Key Competitors in the United Kingdom for 2025 (E)
- TABLE 74: UK Recent Past, Current & Future Analysis for Polypropylene Random Copolymer and High-Density Polyethylene by Type - High-Density Polyethylene and Polypropylene Random Copolymer - Independent Analysis of Annual Sales in US$ Million for the Years 2024 through 2030 and % CAGR
- TABLE 75: UK Historic Review for Polypropylene Random Copolymer and High-Density Polyethylene by Type - High-Density Polyethylene and Polypropylene Random Copolymer Markets - Independent Analysis of Annual Sales in US$ Million for Years 2014 through 2023 and % CAGR
- TABLE 76: UK 16-Year Perspective for Polypropylene Random Copolymer and High-Density Polyethylene by Type - Percentage Breakdown of Value Sales for High-Density Polyethylene and Polypropylene Random Copolymer for the Years 2014, 2025 & 2030
- TABLE 77: UK Recent Past, Current & Future Analysis for Polypropylene Random Copolymer and High-Density Polyethylene by Application - Packaging Application, Healthcare Application, Construction Application and Other Applications - Independent Analysis of Annual Sales in US$ Million for the Years 2024 through 2030 and % CAGR
- TABLE 78: UK Historic Review for Polypropylene Random Copolymer and High-Density Polyethylene by Application - Packaging Application, Healthcare Application, Construction Application and Other Applications Markets - Independent Analysis of Annual Sales in US$ Million for Years 2014 through 2023 and % CAGR
- TABLE 79: UK 16-Year Perspective for Polypropylene Random Copolymer and High-Density Polyethylene by Application - Percentage Breakdown of Value Sales for Packaging Application, Healthcare Application, Construction Application and Other Applications for the Years 2014, 2025 & 2030
- SPAIN
- TABLE 80: Spain Recent Past, Current & Future Analysis for Polypropylene Random Copolymer and High-Density Polyethylene by Type - High-Density Polyethylene and Polypropylene Random Copolymer - Independent Analysis of Annual Sales in US$ Million for the Years 2024 through 2030 and % CAGR
- TABLE 81: Spain Historic Review for Polypropylene Random Copolymer and High-Density Polyethylene by Type - High-Density Polyethylene and Polypropylene Random Copolymer Markets - Independent Analysis of Annual Sales in US$ Million for Years 2014 through 2023 and % CAGR
- TABLE 82: Spain 16-Year Perspective for Polypropylene Random Copolymer and High-Density Polyethylene by Type - Percentage Breakdown of Value Sales for High-Density Polyethylene and Polypropylene Random Copolymer for the Years 2014, 2025 & 2030
- TABLE 83: Spain Recent Past, Current & Future Analysis for Polypropylene Random Copolymer and High-Density Polyethylene by Application - Packaging Application, Healthcare Application, Construction Application and Other Applications - Independent Analysis of Annual Sales in US$ Million for the Years 2024 through 2030 and % CAGR
- TABLE 84: Spain Historic Review for Polypropylene Random Copolymer and High-Density Polyethylene by Application - Packaging Application, Healthcare Application, Construction Application and Other Applications Markets - Independent Analysis of Annual Sales in US$ Million for Years 2014 through 2023 and % CAGR
- TABLE 85: Spain 16-Year Perspective for Polypropylene Random Copolymer and High-Density Polyethylene by Application - Percentage Breakdown of Value Sales for Packaging Application, Healthcare Application, Construction Application and Other Applications for the Years 2014, 2025 & 2030
- RUSSIA
- TABLE 86: Russia Recent Past, Current & Future Analysis for Polypropylene Random Copolymer and High-Density Polyethylene by Type - High-Density Polyethylene and Polypropylene Random Copolymer - Independent Analysis of Annual Sales in US$ Million for the Years 2024 through 2030 and % CAGR
- TABLE 87: Russia Historic Review for Polypropylene Random Copolymer and High-Density Polyethylene by Type - High-Density Polyethylene and Polypropylene Random Copolymer Markets - Independent Analysis of Annual Sales in US$ Million for Years 2014 through 2023 and % CAGR
- TABLE 88: Russia 16-Year Perspective for Polypropylene Random Copolymer and High-Density Polyethylene by Type - Percentage Breakdown of Value Sales for High-Density Polyethylene and Polypropylene Random Copolymer for the Years 2014, 2025 & 2030
- TABLE 89: Russia Recent Past, Current & Future Analysis for Polypropylene Random Copolymer and High-Density Polyethylene by Application - Packaging Application, Healthcare Application, Construction Application and Other Applications - Independent Analysis of Annual Sales in US$ Million for the Years 2024 through 2030 and % CAGR
- TABLE 90: Russia Historic Review for Polypropylene Random Copolymer and High-Density Polyethylene by Application - Packaging Application, Healthcare Application, Construction Application and Other Applications Markets - Independent Analysis of Annual Sales in US$ Million for Years 2014 through 2023 and % CAGR
- TABLE 91: Russia 16-Year Perspective for Polypropylene Random Copolymer and High-Density Polyethylene by Application - Percentage Breakdown of Value Sales for Packaging Application, Healthcare Application, Construction Application and Other Applications for the Years 2014, 2025 & 2030
- REST OF EUROPE
- TABLE 92: Rest of Europe Recent Past, Current & Future Analysis for Polypropylene Random Copolymer and High-Density Polyethylene by Type - High-Density Polyethylene and Polypropylene Random Copolymer - Independent Analysis of Annual Sales in US$ Million for the Years 2024 through 2030 and % CAGR
- TABLE 93: Rest of Europe Historic Review for Polypropylene Random Copolymer and High-Density Polyethylene by Type - High-Density Polyethylene and Polypropylene Random Copolymer Markets - Independent Analysis of Annual Sales in US$ Million for Years 2014 through 2023 and % CAGR
- TABLE 94: Rest of Europe 16-Year Perspective for Polypropylene Random Copolymer and High-Density Polyethylene by Type - Percentage Breakdown of Value Sales for High-Density Polyethylene and Polypropylene Random Copolymer for the Years 2014, 2025 & 2030
- TABLE 95: Rest of Europe Recent Past, Current & Future Analysis for Polypropylene Random Copolymer and High-Density Polyethylene by Application - Packaging Application, Healthcare Application, Construction Application and Other Applications - Independent Analysis of Annual Sales in US$ Million for the Years 2024 through 2030 and % CAGR
- TABLE 96: Rest of Europe Historic Review for Polypropylene Random Copolymer and High-Density Polyethylene by Application - Packaging Application, Healthcare Application, Construction Application and Other Applications Markets - Independent Analysis of Annual Sales in US$ Million for Years 2014 through 2023 and % CAGR
- TABLE 97: Rest of Europe 16-Year Perspective for Polypropylene Random Copolymer and High-Density Polyethylene by Application - Percentage Breakdown of Value Sales for Packaging Application, Healthcare Application, Construction Application and Other Applications for the Years 2014, 2025 & 2030
- ASIA-PACIFIC
- Polypropylene Random Copolymer and High-Density Polyethylene Market Presence - Strong/Active/Niche/Trivial - Key Competitors in Asia-Pacific for 2025 (E)
- TABLE 98: Asia-Pacific Recent Past, Current & Future Analysis for Polypropylene Random Copolymer and High-Density Polyethylene by Geographic Region - Australia, India, South Korea and Rest of Asia-Pacific Markets - Independent Analysis of Annual Sales in US$ Million for Years 2024 through 2030 and % CAGR
- TABLE 99: Asia-Pacific Historic Review for Polypropylene Random Copolymer and High-Density Polyethylene by Geographic Region - Australia, India, South Korea and Rest of Asia-Pacific Markets - Independent Analysis of Annual Sales in US$ Million for Years 2014 through 2023 and % CAGR
- TABLE 100: Asia-Pacific 16-Year Perspective for Polypropylene Random Copolymer and High-Density Polyethylene by Geographic Region - Percentage Breakdown of Value Sales for Australia, India, South Korea and Rest of Asia-Pacific Markets for Years 2014, 2025 & 2030
- TABLE 101: Asia-Pacific Recent Past, Current & Future Analysis for Polypropylene Random Copolymer and High-Density Polyethylene by Type - High-Density Polyethylene and Polypropylene Random Copolymer - Independent Analysis of Annual Sales in US$ Million for the Years 2024 through 2030 and % CAGR
- TABLE 102: Asia-Pacific Historic Review for Polypropylene Random Copolymer and High-Density Polyethylene by Type - High-Density Polyethylene and Polypropylene Random Copolymer Markets - Independent Analysis of Annual Sales in US$ Million for Years 2014 through 2023 and % CAGR
- TABLE 103: Asia-Pacific 16-Year Perspective for Polypropylene Random Copolymer and High-Density Polyethylene by Type - Percentage Breakdown of Value Sales for High-Density Polyethylene and Polypropylene Random Copolymer for the Years 2014, 2025 & 2030
- TABLE 104: Asia-Pacific Recent Past, Current & Future Analysis for Polypropylene Random Copolymer and High-Density Polyethylene by Application - Packaging Application, Healthcare Application, Construction Application and Other Applications - Independent Analysis of Annual Sales in US$ Million for the Years 2024 through 2030 and % CAGR
- TABLE 105: Asia-Pacific Historic Review for Polypropylene Random Copolymer and High-Density Polyethylene by Application - Packaging Application, Healthcare Application, Construction Application and Other Applications Markets - Independent Analysis of Annual Sales in US$ Million for Years 2014 through 2023 and % CAGR
- TABLE 106: Asia-Pacific 16-Year Perspective for Polypropylene Random Copolymer and High-Density Polyethylene by Application - Percentage Breakdown of Value Sales for Packaging Application, Healthcare Application, Construction Application and Other Applications for the Years 2014, 2025 & 2030
- AUSTRALIA
- Polypropylene Random Copolymer and High-Density Polyethylene Market Presence - Strong/Active/Niche/Trivial - Key Competitors in Australia for 2025 (E)
- TABLE 107: Australia Recent Past, Current & Future Analysis for Polypropylene Random Copolymer and High-Density Polyethylene by Type - High-Density Polyethylene and Polypropylene Random Copolymer - Independent Analysis of Annual Sales in US$ Million for the Years 2024 through 2030 and % CAGR
- TABLE 108: Australia Historic Review for Polypropylene Random Copolymer and High-Density Polyethylene by Type - High-Density Polyethylene and Polypropylene Random Copolymer Markets - Independent Analysis of Annual Sales in US$ Million for Years 2014 through 2023 and % CAGR
- TABLE 109: Australia 16-Year Perspective for Polypropylene Random Copolymer and High-Density Polyethylene by Type - Percentage Breakdown of Value Sales for High-Density Polyethylene and Polypropylene Random Copolymer for the Years 2014, 2025 & 2030
- TABLE 110: Australia Recent Past, Current & Future Analysis for Polypropylene Random Copolymer and High-Density Polyethylene by Application - Packaging Application, Healthcare Application, Construction Application and Other Applications - Independent Analysis of Annual Sales in US$ Million for the Years 2024 through 2030 and % CAGR
- TABLE 111: Australia Historic Review for Polypropylene Random Copolymer and High-Density Polyethylene by Application - Packaging Application, Healthcare Application, Construction Application and Other Applications Markets - Independent Analysis of Annual Sales in US$ Million for Years 2014 through 2023 and % CAGR
- TABLE 112: Australia 16-Year Perspective for Polypropylene Random Copolymer and High-Density Polyethylene by Application - Percentage Breakdown of Value Sales for Packaging Application, Healthcare Application, Construction Application and Other Applications for the Years 2014, 2025 & 2030
- INDIA
- Polypropylene Random Copolymer and High-Density Polyethylene Market Presence - Strong/Active/Niche/Trivial - Key Competitors in India for 2025 (E)
- TABLE 113: India Recent Past, Current & Future Analysis for Polypropylene Random Copolymer and High-Density Polyethylene by Type - High-Density Polyethylene and Polypropylene Random Copolymer - Independent Analysis of Annual Sales in US$ Million for the Years 2024 through 2030 and % CAGR
- TABLE 114: India Historic Review for Polypropylene Random Copolymer and High-Density Polyethylene by Type - High-Density Polyethylene and Polypropylene Random Copolymer Markets - Independent Analysis of Annual Sales in US$ Million for Years 2014 through 2023 and % CAGR
- TABLE 115: India 16-Year Perspective for Polypropylene Random Copolymer and High-Density Polyethylene by Type - Percentage Breakdown of Value Sales for High-Density Polyethylene and Polypropylene Random Copolymer for the Years 2014, 2025 & 2030
- TABLE 116: India Recent Past, Current & Future Analysis for Polypropylene Random Copolymer and High-Density Polyethylene by Application - Packaging Application, Healthcare Application, Construction Application and Other Applications - Independent Analysis of Annual Sales in US$ Million for the Years 2024 through 2030 and % CAGR
- TABLE 117: India Historic Review for Polypropylene Random Copolymer and High-Density Polyethylene by Application - Packaging Application, Healthcare Application, Construction Application and Other Applications Markets - Independent Analysis of Annual Sales in US$ Million for Years 2014 through 2023 and % CAGR
- TABLE 118: India 16-Year Perspective for Polypropylene Random Copolymer and High-Density Polyethylene by Application - Percentage Breakdown of Value Sales for Packaging Application, Healthcare Application, Construction Application and Other Applications for the Years 2014, 2025 & 2030
- SOUTH KOREA
- TABLE 119: South Korea Recent Past, Current & Future Analysis for Polypropylene Random Copolymer and High-Density Polyethylene by Type - High-Density Polyethylene and Polypropylene Random Copolymer - Independent Analysis of Annual Sales in US$ Million for the Years 2024 through 2030 and % CAGR
- TABLE 120: South Korea Historic Review for Polypropylene Random Copolymer and High-Density Polyethylene by Type - High-Density Polyethylene and Polypropylene Random Copolymer Markets - Independent Analysis of Annual Sales in US$ Million for Years 2014 through 2023 and % CAGR
- TABLE 121: South Korea 16-Year Perspective for Polypropylene Random Copolymer and High-Density Polyethylene by Type - Percentage Breakdown of Value Sales for High-Density Polyethylene and Polypropylene Random Copolymer for the Years 2014, 2025 & 2030
- TABLE 122: South Korea Recent Past, Current & Future Analysis for Polypropylene Random Copolymer and High-Density Polyethylene by Application - Packaging Application, Healthcare Application, Construction Application and Other Applications - Independent Analysis of Annual Sales in US$ Million for the Years 2024 through 2030 and % CAGR
- TABLE 123: South Korea Historic Review for Polypropylene Random Copolymer and High-Density Polyethylene by Application - Packaging Application, Healthcare Application, Construction Application and Other Applications Markets - Independent Analysis of Annual Sales in US$ Million for Years 2014 through 2023 and % CAGR
- TABLE 124: South Korea 16-Year Perspective for Polypropylene Random Copolymer and High-Density Polyethylene by Application - Percentage Breakdown of Value Sales for Packaging Application, Healthcare Application, Construction Application and Other Applications for the Years 2014, 2025 & 2030
- REST OF ASIA-PACIFIC
- TABLE 125: Rest of Asia-Pacific Recent Past, Current & Future Analysis for Polypropylene Random Copolymer and High-Density Polyethylene by Type - High-Density Polyethylene and Polypropylene Random Copolymer - Independent Analysis of Annual Sales in US$ Million for the Years 2024 through 2030 and % CAGR
- TABLE 126: Rest of Asia-Pacific Historic Review for Polypropylene Random Copolymer and High-Density Polyethylene by Type - High-Density Polyethylene and Polypropylene Random Copolymer Markets - Independent Analysis of Annual Sales in US$ Million for Years 2014 through 2023 and % CAGR
- TABLE 127: Rest of Asia-Pacific 16-Year Perspective for Polypropylene Random Copolymer and High-Density Polyethylene by Type - Percentage Breakdown of Value Sales for High-Density Polyethylene and Polypropylene Random Copolymer for the Years 2014, 2025 & 2030
- TABLE 128: Rest of Asia-Pacific Recent Past, Current & Future Analysis for Polypropylene Random Copolymer and High-Density Polyethylene by Application - Packaging Application, Healthcare Application, Construction Application and Other Applications - Independent Analysis of Annual Sales in US$ Million for the Years 2024 through 2030 and % CAGR
- TABLE 129: Rest of Asia-Pacific Historic Review for Polypropylene Random Copolymer and High-Density Polyethylene by Application - Packaging Application, Healthcare Application, Construction Application and Other Applications Markets - Independent Analysis of Annual Sales in US$ Million for Years 2014 through 2023 and % CAGR
- TABLE 130: Rest of Asia-Pacific 16-Year Perspective for Polypropylene Random Copolymer and High-Density Polyethylene by Application - Percentage Breakdown of Value Sales for Packaging Application, Healthcare Application, Construction Application and Other Applications for the Years 2014, 2025 & 2030
- LATIN AMERICA
- Polypropylene Random Copolymer and High-Density Polyethylene Market Presence - Strong/Active/Niche/Trivial - Key Competitors in Latin America for 2025 (E)
- TABLE 131: Latin America Recent Past, Current & Future Analysis for Polypropylene Random Copolymer and High-Density Polyethylene by Geographic Region - Argentina, Brazil, Mexico and Rest of Latin America Markets - Independent Analysis of Annual Sales in US$ Million for Years 2024 through 2030 and % CAGR
- TABLE 132: Latin America Historic Review for Polypropylene Random Copolymer and High-Density Polyethylene by Geographic Region - Argentina, Brazil, Mexico and Rest of Latin America Markets - Independent Analysis of Annual Sales in US$ Million for Years 2014 through 2023 and % CAGR
- TABLE 133: Latin America 16-Year Perspective for Polypropylene Random Copolymer and High-Density Polyethylene by Geographic Region - Percentage Breakdown of Value Sales for Argentina, Brazil, Mexico and Rest of Latin America Markets for Years 2014, 2025 & 2030
- TABLE 134: Latin America Recent Past, Current & Future Analysis for Polypropylene Random Copolymer and High-Density Polyethylene by Type - High-Density Polyethylene and Polypropylene Random Copolymer - Independent Analysis of Annual Sales in US$ Million for the Years 2024 through 2030 and % CAGR
- TABLE 135: Latin America Historic Review for Polypropylene Random Copolymer and High-Density Polyethylene by Type - High-Density Polyethylene and Polypropylene Random Copolymer Markets - Independent Analysis of Annual Sales in US$ Million for Years 2014 through 2023 and % CAGR
- TABLE 136: Latin America 16-Year Perspective for Polypropylene Random Copolymer and High-Density Polyethylene by Type - Percentage Breakdown of Value Sales for High-Density Polyethylene and Polypropylene Random Copolymer for the Years 2014, 2025 & 2030
- TABLE 137: Latin America Recent Past, Current & Future Analysis for Polypropylene Random Copolymer and High-Density Polyethylene by Application - Packaging Application, Healthcare Application, Construction Application and Other Applications - Independent Analysis of Annual Sales in US$ Million for the Years 2024 through 2030 and % CAGR
- TABLE 138: Latin America Historic Review for Polypropylene Random Copolymer and High-Density Polyethylene by Application - Packaging Application, Healthcare Application, Construction Application and Other Applications Markets - Independent Analysis of Annual Sales in US$ Million for Years 2014 through 2023 and % CAGR
- TABLE 139: Latin America 16-Year Perspective for Polypropylene Random Copolymer and High-Density Polyethylene by Application - Percentage Breakdown of Value Sales for Packaging Application, Healthcare Application, Construction Application and Other Applications for the Years 2014, 2025 & 2030
- ARGENTINA
- TABLE 140: Argentina Recent Past, Current & Future Analysis for Polypropylene Random Copolymer and High-Density Polyethylene by Type - High-Density Polyethylene and Polypropylene Random Copolymer - Independent Analysis of Annual Sales in US$ Million for the Years 2024 through 2030 and % CAGR
- TABLE 141: Argentina Historic Review for Polypropylene Random Copolymer and High-Density Polyethylene by Type - High-Density Polyethylene and Polypropylene Random Copolymer Markets - Independent Analysis of Annual Sales in US$ Million for Years 2014 through 2023 and % CAGR
- TABLE 142: Argentina 16-Year Perspective for Polypropylene Random Copolymer and High-Density Polyethylene by Type - Percentage Breakdown of Value Sales for High-Density Polyethylene and Polypropylene Random Copolymer for the Years 2014, 2025 & 2030
- TABLE 143: Argentina Recent Past, Current & Future Analysis for Polypropylene Random Copolymer and High-Density Polyethylene by Application - Packaging Application, Healthcare Application, Construction Application and Other Applications - Independent Analysis of Annual Sales in US$ Million for the Years 2024 through 2030 and % CAGR
- TABLE 144: Argentina Historic Review for Polypropylene Random Copolymer and High-Density Polyethylene by Application - Packaging Application, Healthcare Application, Construction Application and Other Applications Markets - Independent Analysis of Annual Sales in US$ Million for Years 2014 through 2023 and % CAGR
- TABLE 145: Argentina 16-Year Perspective for Polypropylene Random Copolymer and High-Density Polyethylene by Application - Percentage Breakdown of Value Sales for Packaging Application, Healthcare Application, Construction Application and Other Applications for the Years 2014, 2025 & 2030
- BRAZIL
- TABLE 146: Brazil Recent Past, Current & Future Analysis for Polypropylene Random Copolymer and High-Density Polyethylene by Type - High-Density Polyethylene and Polypropylene Random Copolymer - Independent Analysis of Annual Sales in US$ Million for the Years 2024 through 2030 and % CAGR
- TABLE 147: Brazil Historic Review for Polypropylene Random Copolymer and High-Density Polyethylene by Type - High-Density Polyethylene and Polypropylene Random Copolymer Markets - Independent Analysis of Annual Sales in US$ Million for Years 2014 through 2023 and % CAGR
- TABLE 148: Brazil 16-Year Perspective for Polypropylene Random Copolymer and High-Density Polyethylene by Type - Percentage Breakdown of Value Sales for High-Density Polyethylene and Polypropylene Random Copolymer for the Years 2014, 2025 & 2030
- TABLE 149: Brazil Recent Past, Current & Future Analysis for Polypropylene Random Copolymer and High-Density Polyethylene by Application - Packaging Application, Healthcare Application, Construction Application and Other Applications - Independent Analysis of Annual Sales in US$ Million for the Years 2024 through 2030 and % CAGR
- TABLE 150: Brazil Historic Review for Polypropylene Random Copolymer and High-Density Polyethylene by Application - Packaging Application, Healthcare Application, Construction Application and Other Applications Markets - Independent Analysis of Annual Sales in US$ Million for Years 2014 through 2023 and % CAGR
- TABLE 151: Brazil 16-Year Perspective for Polypropylene Random Copolymer and High-Density Polyethylene by Application - Percentage Breakdown of Value Sales for Packaging Application, Healthcare Application, Construction Application and Other Applications for the Years 2014, 2025 & 2030
- MEXICO
- TABLE 152: Mexico Recent Past, Current & Future Analysis for Polypropylene Random Copolymer and High-Density Polyethylene by Type - High-Density Polyethylene and Polypropylene Random Copolymer - Independent Analysis of Annual Sales in US$ Million for the Years 2024 through 2030 and % CAGR
- TABLE 153: Mexico Historic Review for Polypropylene Random Copolymer and High-Density Polyethylene by Type - High-Density Polyethylene and Polypropylene Random Copolymer Markets - Independent Analysis of Annual Sales in US$ Million for Years 2014 through 2023 and % CAGR
- TABLE 154: Mexico 16-Year Perspective for Polypropylene Random Copolymer and High-Density Polyethylene by Type - Percentage Breakdown of Value Sales for High-Density Polyethylene and Polypropylene Random Copolymer for the Years 2014, 2025 & 2030
- TABLE 155: Mexico Recent Past, Current & Future Analysis for Polypropylene Random Copolymer and High-Density Polyethylene by Application - Packaging Application, Healthcare Application, Construction Application and Other Applications - Independent Analysis of Annual Sales in US$ Million for the Years 2024 through 2030 and % CAGR
- TABLE 156: Mexico Historic Review for Polypropylene Random Copolymer and High-Density Polyethylene by Application - Packaging Application, Healthcare Application, Construction Application and Other Applications Markets - Independent Analysis of Annual Sales in US$ Million for Years 2014 through 2023 and % CAGR
- TABLE 157: Mexico 16-Year Perspective for Polypropylene Random Copolymer and High-Density Polyethylene by Application - Percentage Breakdown of Value Sales for Packaging Application, Healthcare Application, Construction Application and Other Applications for the Years 2014, 2025 & 2030
- REST OF LATIN AMERICA
- TABLE 158: Rest of Latin America Recent Past, Current & Future Analysis for Polypropylene Random Copolymer and High-Density Polyethylene by Type - High-Density Polyethylene and Polypropylene Random Copolymer - Independent Analysis of Annual Sales in US$ Million for the Years 2024 through 2030 and % CAGR
- TABLE 159: Rest of Latin America Historic Review for Polypropylene Random Copolymer and High-Density Polyethylene by Type - High-Density Polyethylene and Polypropylene Random Copolymer Markets - Independent Analysis of Annual Sales in US$ Million for Years 2014 through 2023 and % CAGR
- TABLE 160: Rest of Latin America 16-Year Perspective for Polypropylene Random Copolymer and High-Density Polyethylene by Type - Percentage Breakdown of Value Sales for High-Density Polyethylene and Polypropylene Random Copolymer for the Years 2014, 2025 & 2030
- TABLE 161: Rest of Latin America Recent Past, Current & Future Analysis for Polypropylene Random Copolymer and High-Density Polyethylene by Application - Packaging Application, Healthcare Application, Construction Application and Other Applications - Independent Analysis of Annual Sales in US$ Million for the Years 2024 through 2030 and % CAGR
- TABLE 162: Rest of Latin America Historic Review for Polypropylene Random Copolymer and High-Density Polyethylene by Application - Packaging Application, Healthcare Application, Construction Application and Other Applications Markets - Independent Analysis of Annual Sales in US$ Million for Years 2014 through 2023 and % CAGR
- TABLE 163: Rest of Latin America 16-Year Perspective for Polypropylene Random Copolymer and High-Density Polyethylene by Application - Percentage Breakdown of Value Sales for Packaging Application, Healthcare Application, Construction Application and Other Applications for the Years 2014, 2025 & 2030
- MIDDLE EAST
- Polypropylene Random Copolymer and High-Density Polyethylene Market Presence - Strong/Active/Niche/Trivial - Key Competitors in Middle East for 2025 (E)
- TABLE 164: Middle East Recent Past, Current & Future Analysis for Polypropylene Random Copolymer and High-Density Polyethylene by Geographic Region - Iran, Israel, Saudi Arabia, UAE and Rest of Middle East Markets - Independent Analysis of Annual Sales in US$ Million for Years 2024 through 2030 and % CAGR
- TABLE 165: Middle East Historic Review for Polypropylene Random Copolymer and High-Density Polyethylene by Geographic Region - Iran, Israel, Saudi Arabia, UAE and Rest of Middle East Markets - Independent Analysis of Annual Sales in US$ Million for Years 2014 through 2023 and % CAGR
- TABLE 166: Middle East 16-Year Perspective for Polypropylene Random Copolymer and High-Density Polyethylene by Geographic Region - Percentage Breakdown of Value Sales for Iran, Israel, Saudi Arabia, UAE and Rest of Middle East Markets for Years 2014, 2025 & 2030
- TABLE 167: Middle East Recent Past, Current & Future Analysis for Polypropylene Random Copolymer and High-Density Polyethylene by Type - High-Density Polyethylene and Polypropylene Random Copolymer - Independent Analysis of Annual Sales in US$ Million for the Years 2024 through 2030 and % CAGR
- TABLE 168: Middle East Historic Review for Polypropylene Random Copolymer and High-Density Polyethylene by Type - High-Density Polyethylene and Polypropylene Random Copolymer Markets - Independent Analysis of Annual Sales in US$ Million for Years 2014 through 2023 and % CAGR
- TABLE 169: Middle East 16-Year Perspective for Polypropylene Random Copolymer and High-Density Polyethylene by Type - Percentage Breakdown of Value Sales for High-Density Polyethylene and Polypropylene Random Copolymer for the Years 2014, 2025 & 2030
- TABLE 170: Middle East Recent Past, Current & Future Analysis for Polypropylene Random Copolymer and High-Density Polyethylene by Application - Packaging Application, Healthcare Application, Construction Application and Other Applications - Independent Analysis of Annual Sales in US$ Million for the Years 2024 through 2030 and % CAGR
- TABLE 171: Middle East Historic Review for Polypropylene Random Copolymer and High-Density Polyethylene by Application - Packaging Application, Healthcare Application, Construction Application and Other Applications Markets - Independent Analysis of Annual Sales in US$ Million for Years 2014 through 2023 and % CAGR
- TABLE 172: Middle East 16-Year Perspective for Polypropylene Random Copolymer and High-Density Polyethylene by Application - Percentage Breakdown of Value Sales for Packaging Application, Healthcare Application, Construction Application and Other Applications for the Years 2014, 2025 & 2030
- IRAN
- TABLE 173: Iran Recent Past, Current & Future Analysis for Polypropylene Random Copolymer and High-Density Polyethylene by Type - High-Density Polyethylene and Polypropylene Random Copolymer - Independent Analysis of Annual Sales in US$ Million for the Years 2024 through 2030 and % CAGR
- TABLE 174: Iran Historic Review for Polypropylene Random Copolymer and High-Density Polyethylene by Type - High-Density Polyethylene and Polypropylene Random Copolymer Markets - Independent Analysis of Annual Sales in US$ Million for Years 2014 through 2023 and % CAGR
- TABLE 175: Iran 16-Year Perspective for Polypropylene Random Copolymer and High-Density Polyethylene by Type - Percentage Breakdown of Value Sales for High-Density Polyethylene and Polypropylene Random Copolymer for the Years 2014, 2025 & 2030
- TABLE 176: Iran Recent Past, Current & Future Analysis for Polypropylene Random Copolymer and High-Density Polyethylene by Application - Packaging Application, Healthcare Application, Construction Application and Other Applications - Independent Analysis of Annual Sales in US$ Million for the Years 2024 through 2030 and % CAGR
- TABLE 177: Iran Historic Review for Polypropylene Random Copolymer and High-Density Polyethylene by Application - Packaging Application, Healthcare Application, Construction Application and Other Applications Markets - Independent Analysis of Annual Sales in US$ Million for Years 2014 through 2023 and % CAGR
- TABLE 178: Iran 16-Year Perspective for Polypropylene Random Copolymer and High-Density Polyethylene by Application - Percentage Breakdown of Value Sales for Packaging Application, Healthcare Application, Construction Application and Other Applications for the Years 2014, 2025 & 2030
- ISRAEL
- TABLE 179: Israel Recent Past, Current & Future Analysis for Polypropylene Random Copolymer and High-Density Polyethylene by Type - High-Density Polyethylene and Polypropylene Random Copolymer - Independent Analysis of Annual Sales in US$ Million for the Years 2024 through 2030 and % CAGR
- TABLE 180: Israel Historic Review for Polypropylene Random Copolymer and High-Density Polyethylene by Type - High-Density Polyethylene and Polypropylene Random Copolymer Markets - Independent Analysis of Annual Sales in US$ Million for Years 2014 through 2023 and % CAGR
- TABLE 181: Israel 16-Year Perspective for Polypropylene Random Copolymer and High-Density Polyethylene by Type - Percentage Breakdown of Value Sales for High-Density Polyethylene and Polypropylene Random Copolymer for the Years 2014, 2025 & 2030
- TABLE 182: Israel Recent Past, Current & Future Analysis for Polypropylene Random Copolymer and High-Density Polyethylene by Application - Packaging Application, Healthcare Application, Construction Application and Other Applications - Independent Analysis of Annual Sales in US$ Million for the Years 2024 through 2030 and % CAGR
- TABLE 183: Israel Historic Review for Polypropylene Random Copolymer and High-Density Polyethylene by Application - Packaging Application, Healthcare Application, Construction Application and Other Applications Markets - Independent Analysis of Annual Sales in US$ Million for Years 2014 through 2023 and % CAGR
- TABLE 184: Israel 16-Year Perspective for Polypropylene Random Copolymer and High-Density Polyethylene by Application - Percentage Breakdown of Value Sales for Packaging Application, Healthcare Application, Construction Application and Other Applications for the Years 2014, 2025 & 2030
- SAUDI ARABIA
- TABLE 185: Saudi Arabia Recent Past, Current & Future Analysis for Polypropylene Random Copolymer and High-Density Polyethylene by Type - High-Density Polyethylene and Polypropylene Random Copolymer - Independent Analysis of Annual Sales in US$ Million for the Years 2024 through 2030 and % CAGR
- TABLE 186: Saudi Arabia Historic Review for Polypropylene Random Copolymer and High-Density Polyethylene by Type - High-Density Polyethylene and Polypropylene Random Copolymer Markets - Independent Analysis of Annual Sales in US$ Million for Years 2014 through 2023 and % CAGR
- TABLE 187: Saudi Arabia 16-Year Perspective for Polypropylene Random Copolymer and High-Density Polyethylene by Type - Percentage Breakdown of Value Sales for High-Density Polyethylene and Polypropylene Random Copolymer for the Years 2014, 2025 & 2030
- TABLE 188: Saudi Arabia Recent Past, Current & Future Analysis for Polypropylene Random Copolymer and High-Density Polyethylene by Application - Packaging Application, Healthcare Application, Construction Application and Other Applications - Independent Analysis of Annual Sales in US$ Million for the Years 2024 through 2030 and % CAGR
- TABLE 189: Saudi Arabia Historic Review for Polypropylene Random Copolymer and High-Density Polyethylene by Application - Packaging Application, Healthcare Application, Construction Application and Other Applications Markets - Independent Analysis of Annual Sales in US$ Million for Years 2014 through 2023 and % CAGR
- TABLE 190: Saudi Arabia 16-Year Perspective for Polypropylene Random Copolymer and High-Density Polyethylene by Application - Percentage Breakdown of Value Sales for Packaging Application, Healthcare Application, Construction Application and Other Applications for the Years 2014, 2025 & 2030
- UNITED ARAB EMIRATES
- TABLE 191: UAE Recent Past, Current & Future Analysis for Polypropylene Random Copolymer and High-Density Polyethylene by Type - High-Density Polyethylene and Polypropylene Random Copolymer - Independent Analysis of Annual Sales in US$ Million for the Years 2024 through 2030 and % CAGR
- TABLE 192: UAE Historic Review for Polypropylene Random Copolymer and High-Density Polyethylene by Type - High-Density Polyethylene and Polypropylene Random Copolymer Markets - Independent Analysis of Annual Sales in US$ Million for Years 2014 through 2023 and % CAGR
- TABLE 193: UAE 16-Year Perspective for Polypropylene Random Copolymer and High-Density Polyethylene by Type - Percentage Breakdown of Value Sales for High-Density Polyethylene and Polypropylene Random Copolymer for the Years 2014, 2025 & 2030
- TABLE 194: UAE Recent Past, Current & Future Analysis for Polypropylene Random Copolymer and High-Density Polyethylene by Application - Packaging Application, Healthcare Application, Construction Application and Other Applications - Independent Analysis of Annual Sales in US$ Million for the Years 2024 through 2030 and % CAGR
- TABLE 195: UAE Historic Review for Polypropylene Random Copolymer and High-Density Polyethylene by Application - Packaging Application, Healthcare Application, Construction Application and Other Applications Markets - Independent Analysis of Annual Sales in US$ Million for Years 2014 through 2023 and % CAGR
- TABLE 196: UAE 16-Year Perspective for Polypropylene Random Copolymer and High-Density Polyethylene by Application - Percentage Breakdown of Value Sales for Packaging Application, Healthcare Application, Construction Application and Other Applications for the Years 2014, 2025 & 2030
- REST OF MIDDLE EAST
- TABLE 197: Rest of Middle East Recent Past, Current & Future Analysis for Polypropylene Random Copolymer and High-Density Polyethylene by Type - High-Density Polyethylene and Polypropylene Random Copolymer - Independent Analysis of Annual Sales in US$ Million for the Years 2024 through 2030 and % CAGR
- TABLE 198: Rest of Middle East Historic Review for Polypropylene Random Copolymer and High-Density Polyethylene by Type - High-Density Polyethylene and Polypropylene Random Copolymer Markets - Independent Analysis of Annual Sales in US$ Million for Years 2014 through 2023 and % CAGR
- TABLE 199: Rest of Middle East 16-Year Perspective for Polypropylene Random Copolymer and High-Density Polyethylene by Type - Percentage Breakdown of Value Sales for High-Density Polyethylene and Polypropylene Random Copolymer for the Years 2014, 2025 & 2030
- TABLE 200: Rest of Middle East Recent Past, Current & Future Analysis for Polypropylene Random Copolymer and High-Density Polyethylene by Application - Packaging Application, Healthcare Application, Construction Application and Other Applications - Independent Analysis of Annual Sales in US$ Million for the Years 2024 through 2030 and % CAGR
- TABLE 201: Rest of Middle East Historic Review for Polypropylene Random Copolymer and High-Density Polyethylene by Application - Packaging Application, Healthcare Application, Construction Application and Other Applications Markets - Independent Analysis of Annual Sales in US$ Million for Years 2014 through 2023 and % CAGR
- TABLE 202: Rest of Middle East 16-Year Perspective for Polypropylene Random Copolymer and High-Density Polyethylene by Application - Percentage Breakdown of Value Sales for Packaging Application, Healthcare Application, Construction Application and Other Applications for the Years 2014, 2025 & 2030
- AFRICA
- Polypropylene Random Copolymer and High-Density Polyethylene Market Presence - Strong/Active/Niche/Trivial - Key Competitors in Africa for 2025 (E)
- TABLE 203: Africa Recent Past, Current & Future Analysis for Polypropylene Random Copolymer and High-Density Polyethylene by Type - High-Density Polyethylene and Polypropylene Random Copolymer - Independent Analysis of Annual Sales in US$ Million for the Years 2024 through 2030 and % CAGR
- TABLE 204: Africa Historic Review for Polypropylene Random Copolymer and High-Density Polyethylene by Type - High-Density Polyethylene and Polypropylene Random Copolymer Markets - Independent Analysis of Annual Sales in US$ Million for Years 2014 through 2023 and % CAGR
- TABLE 205: Africa 16-Year Perspective for Polypropylene Random Copolymer and High-Density Polyethylene by Type - Percentage Breakdown of Value Sales for High-Density Polyethylene and Polypropylene Random Copolymer for the Years 2014, 2025 & 2030
- TABLE 206: Africa Recent Past, Current & Future Analysis for Polypropylene Random Copolymer and High-Density Polyethylene by Application - Packaging Application, Healthcare Application, Construction Application and Other Applications - Independent Analysis of Annual Sales in US$ Million for the Years 2024 through 2030 and % CAGR
- TABLE 207: Africa Historic Review for Polypropylene Random Copolymer and High-Density Polyethylene by Application - Packaging Application, Healthcare Application, Construction Application and Other Applications Markets - Independent Analysis of Annual Sales in US$ Million for Years 2014 through 2023 and % CAGR
- TABLE 208: Africa 16-Year Perspective for Polypropylene Random Copolymer and High-Density Polyethylene by Application - Percentage Breakdown of Value Sales for Packaging Application, Healthcare Application, Construction Application and Other Applications for the Years 2014, 2025 & 2030
- IV. COMPETITION
Pricing
Currency Rates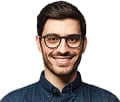