
Petroleum Refining Hydrogen Generation
Description
Global Petroleum Refining Hydrogen Generation Market to Reach US$84.9 Billion by 2030
The global market for Petroleum Refining Hydrogen Generation estimated at US$60.0 Billion in the year 2024, is expected to reach US$84.9 Billion by 2030, growing at a CAGR of 6.0% over the analysis period 2024-2030. Captive Delivery Mode, one of the segments analyzed in the report, is expected to record a 6.8% CAGR and reach US$61.5 Billion by the end of the analysis period. Growth in the Merchant Delivery Mode segment is estimated at 4.0% CAGR over the analysis period.
The U.S. Market is Estimated at US$16.3 Billion While China is Forecast to Grow at 9.5% CAGR
The Petroleum Refining Hydrogen Generation market in the U.S. is estimated at US$16.3 Billion in the year 2024. China, the world`s second largest economy, is forecast to reach a projected market size of US$17.4 Billion by the year 2030 trailing a CAGR of 9.5% over the analysis period 2024-2030. Among the other noteworthy geographic markets are Japan and Canada, each forecast to grow at a CAGR of 2.9% and 5.9% respectively over the analysis period. Within Europe, Germany is forecast to grow at approximately 3.9% CAGR.
Global Petroleum Refining Hydrogen Generation Market - Key Trends & Drivers Summarized
Why Is Hydrogen Critical to Petroleum Refining Operations?
Hydrogen plays an essential role in modern petroleum refining, serving as a key input for hydrotreating and hydrocracking processes. These units are vital for removing sulfur, nitrogen, and other contaminants from fuel streams to meet clean fuel regulations. Hydrogen is also used to improve fuel yields and quality by converting heavy hydrocarbons into lighter, more valuable fractions. As refining moves toward processing heavier and sourer crude oils, reliance on hydrogen continues to rise.
Refiners primarily produce hydrogen on-site through steam methane reforming, partial oxidation, or autothermal reforming. These technologies enable continuous, large-scale production using natural gas or refinery by-products. Integration of hydrogen generation units within refineries ensures process efficiency, operational continuity, and cost control. Facilities with high hydroprocessing capacity are typically the most significant consumers of hydrogen, particularly in regions with stringent fuel emission standards.
How Are Technology Choices and Energy Efficiency Goals Shaping Production Trends?
Steam methane reforming (SMR) remains the most widely used technology for hydrogen generation due to its reliability and scalability. However, it is also associated with high carbon dioxide emissions, prompting refiners to explore cleaner alternatives. Efforts are underway to retrofit existing SMR units with carbon capture systems to reduce emissions without disrupting operations. In parallel, interest in autothermal reforming and advanced membrane-based purification systems is growing for their potential energy savings and footprint advantages.
Refineries are increasingly focused on improving hydrogen yield, optimizing heat integration, and minimizing hydrogen losses across processing units. On-site purification systems such as pressure swing adsorption (PSA) and membrane separation are now standard in most hydrogen production trains. These systems help refiners maintain consistent hydrogen purity and pressure levels, which are crucial for catalytic performance in hydrotreaters and hydrocrackers.
Where Is Demand Rising and Which Refinery Configurations Are Driving It?
Hydrogen demand is rising across complex and deep-conversion refineries that operate multiple hydrotreating and hydrocracking units. Facilities processing heavy, high-sulfur crudes are particularly dependent on hydrogen to meet low-sulfur fuel specifications. Upgrading older refineries and adding secondary processing capacity are increasing hydrogen requirements in Asia-Pacific, Latin America, and parts of the Middle East.
Tighter environmental regulations in the US and Europe continue to support investment in hydrogen generation systems. Refineries operating under fuel sulfur limits for diesel and gasoline require stable and high-purity hydrogen supply. Integrated refinery-petrochemical complexes are also influencing demand, as hydrogen is needed for aromatics production and specialty feedstock upgrading. Regional hydrogen strategies and refinery modernization programs are further contributing to long-term demand growth.
Growth in the Petroleum Refining Hydrogen Generation market is driven by several factors…
Growth in the petroleum refining hydrogen generation market is driven by increasing hydroprocessing capacity across refineries, processing of heavier crude grades, and enforcement of ultra-low sulfur fuel regulations. Expansion of hydrotreating and hydrocracking units to meet clean fuel mandates continues to raise hydrogen requirements, particularly in high-throughput and export-oriented refineries.
Technology upgrades in SMR units, integration of carbon capture systems, and deployment of on-site purification technologies are supporting more efficient and compliant hydrogen production. Demand is further influenced by refinery-petrochemical integration, regional fuel quality mandates, and rising hydrogen purity needs in secondary processing units. Refinery investments in Asia-Pacific, Middle East, and North America are sustaining capital deployment in hydrogen production infrastructure to meet both current refining needs and future emissions reduction goals.
SCOPE OF STUDY:The report analyzes the Petroleum Refining Hydrogen Generation market in terms of units by the following Segments, and Geographic Regions/Countries:
Segments:
Delivery Mode (Captive Delivery Mode, Merchant Delivery Mode); Process (Steam Methane Reforming Process, Electrolysis Process, Partial Oxidation Process, Auto-Thermal Reforming Process, Biomass Gasification Process)
Geographic Regions/Countries:
World; United States; Canada; Japan; China; Europe (France; Germany; Italy; United Kingdom; Spain; Russia; and Rest of Europe); Asia-Pacific (Australia; India; South Korea; and Rest of Asia-Pacific); Latin America (Argentina; Brazil; Mexico; and Rest of Latin America); Middle East (Iran; Israel; Saudi Arabia; United Arab Emirates; and Rest of Middle East); and Africa.
Select Competitors (Total 37 Featured) -
- Air Liquide
- Air Products and Chemicals
- Axens
- BayoTech
- Bloom Energy
- Chevron Corporation
- China Petroleum & Chemical Corporation (Sinopec)
- Cummins Inc.
- Gazprom
- General Electric (GE)
- Haldor Topsoe
- Honeywell UOP
- Hydrogenics (Cummins Subsidiary)
- INOX Air Products
- Johnson Matthey
- Linde plc
- McPhy Energy
- Mitsubishi Power
- Shell plc
- Technip Energies
We`re transforming market and competitive intelligence with validated expert content and AI tools.
Instead of following the general norm of querying LLMs and Industry-specific SLMs, we built repositories of content curated from domain experts worldwide including video transcripts, blogs, search engines research, and massive amounts of enterprise, product/service, and market data.
TARIFF IMPACT FACTOR
Our new release incorporates impact of tariffs on geographical markets as we predict a shift in competitiveness of companies based on HQ country, manufacturing base, exports and imports (finished goods and OEM). This intricate and multifaceted market reality will impact competitors by increasing the Cost of Goods Sold (COGS), reducing profitability, reconfiguring supply chains, amongst other micro and macro market dynamics.
Please note: Reports are sold as single-site single-user licenses. Electronic versions require 24-48 hours as each copy is customized to the client with digital controls and custom watermarks. The Publisher uses digital controls protecting against copying and printing is restricted to one full copy to be used at the same location.
The latest version of Adobe Acrobat Reader is required to view the report. Upon ordering an electronic version, the Publisher will provide a link to download the purchased report.
Prior to fulfillment of an order, the client will be required to sign a document detailing the purchase terms for a publication from this publisher.
Table of Contents
- I. METHODOLOGY
- II. EXECUTIVE SUMMARY
- 1. MARKET OVERVIEW
- Influencer Market Insights
- World Market Trajectories
- Tariff Impact on Global Supply Chain Patterns
- Petroleum Refining Hydrogen Generation – Global Key Competitors Percentage Market Share in 2025 (E)
- Competitive Market Presence - Strong/Active/Niche/Trivial for Players Worldwide in 2025 (E)
- 2. FOCUS ON SELECT PLAYERS
- 3. MARKET TRENDS & DRIVERS
- Stricter Fuel Quality Standards Propel Demand for Hydrogen in Desulfurization Processes
- Global Push for Low-Emission Transportation Fuels Strengthens the Business Case for Hydrogen Utilization
- Energy Transition Initiatives Throw the Spotlight on Decarbonizing Hydrogen Production in Refineries
- Rising Demand for Cleaner Diesel and Jet Fuel Expands the Addressable Market for On-Site Hydrogen Generation
- Integration of Carbon Capture and Storage (CCS) Technologies Drives Adoption of Low-Carbon Hydrogen Pathways
- Hydrogen Demand Growth in Hydrocracking and Hydrotreating Units Sustains Capacity Expansion Projects
- Technological Advancements in SMR and ATR Efficiency Propel Refinery Hydrogen Output Optimization
- Electrolyzer Cost Declines and Renewable Integration Create Opportunities for Green Hydrogen Substitution
- Increasing Focus on Scope 1 and Scope 2 Emissions Throws the Spotlight on Internal Hydrogen Value Chains
- Global Refining Capacity Additions in Asia and Middle East Fuel New Demand for Hydrogen Infrastructure
- Co-Processing of Bio-Feedstocks Drives Need for Flexible and High-Purity Hydrogen Supply
- Refinery Energy Efficiency Programs Spur Innovation in Hydrogen Recovery and Recycling Technologies
- 4. GLOBAL MARKET PERSPECTIVE
- TABLE 1: World Petroleum Refining Hydrogen Generation Market Analysis of Annual Sales in US$ Million for Years 2014 through 2030
- TABLE 2: World Recent Past, Current & Future Analysis for Petroleum Refining Hydrogen Generation by Geographic Region - USA, Canada, Japan, China, Europe, Asia-Pacific, Latin America, Middle East and Africa Markets - Independent Analysis of Annual Sales in US$ Million for Years 2024 through 2030 and % CAGR
- TABLE 3: World Historic Review for Petroleum Refining Hydrogen Generation by Geographic Region - USA, Canada, Japan, China, Europe, Asia-Pacific, Latin America, Middle East and Africa Markets - Independent Analysis of Annual Sales in US$ Million for Years 2014 through 2023 and % CAGR
- TABLE 4: World 16-Year Perspective for Petroleum Refining Hydrogen Generation by Geographic Region - Percentage Breakdown of Value Sales for USA, Canada, Japan, China, Europe, Asia-Pacific, Latin America, Middle East and Africa Markets for Years 2014, 2025 & 2030
- TABLE 5: World Recent Past, Current & Future Analysis for Captive Delivery Mode by Geographic Region - USA, Canada, Japan, China, Europe, Asia-Pacific, Latin America, Middle East and Africa Markets - Independent Analysis of Annual Sales in US$ Million for Years 2024 through 2030 and % CAGR
- TABLE 6: World Historic Review for Captive Delivery Mode by Geographic Region - USA, Canada, Japan, China, Europe, Asia-Pacific, Latin America, Middle East and Africa Markets - Independent Analysis of Annual Sales in US$ Million for Years 2014 through 2023 and % CAGR
- TABLE 7: World 16-Year Perspective for Captive Delivery Mode by Geographic Region - Percentage Breakdown of Value Sales for USA, Canada, Japan, China, Europe, Asia-Pacific, Latin America, Middle East and Africa for Years 2014, 2025 & 2030
- TABLE 8: World Recent Past, Current & Future Analysis for Merchant Delivery Mode by Geographic Region - USA, Canada, Japan, China, Europe, Asia-Pacific, Latin America, Middle East and Africa Markets - Independent Analysis of Annual Sales in US$ Million for Years 2024 through 2030 and % CAGR
- TABLE 9: World Historic Review for Merchant Delivery Mode by Geographic Region - USA, Canada, Japan, China, Europe, Asia-Pacific, Latin America, Middle East and Africa Markets - Independent Analysis of Annual Sales in US$ Million for Years 2014 through 2023 and % CAGR
- TABLE 10: World 16-Year Perspective for Merchant Delivery Mode by Geographic Region - Percentage Breakdown of Value Sales for USA, Canada, Japan, China, Europe, Asia-Pacific, Latin America, Middle East and Africa for Years 2014, 2025 & 2030
- TABLE 11: World Recent Past, Current & Future Analysis for Steam Methane Reforming Process by Geographic Region - USA, Canada, Japan, China, Europe, Asia-Pacific, Latin America, Middle East and Africa Markets - Independent Analysis of Annual Sales in US$ Million for Years 2024 through 2030 and % CAGR
- TABLE 12: World Historic Review for Steam Methane Reforming Process by Geographic Region - USA, Canada, Japan, China, Europe, Asia-Pacific, Latin America, Middle East and Africa Markets - Independent Analysis of Annual Sales in US$ Million for Years 2014 through 2023 and % CAGR
- TABLE 13: World 16-Year Perspective for Steam Methane Reforming Process by Geographic Region - Percentage Breakdown of Value Sales for USA, Canada, Japan, China, Europe, Asia-Pacific, Latin America, Middle East and Africa for Years 2014, 2025 & 2030
- TABLE 14: World Recent Past, Current & Future Analysis for Electrolysis Process by Geographic Region - USA, Canada, Japan, China, Europe, Asia-Pacific, Latin America, Middle East and Africa Markets - Independent Analysis of Annual Sales in US$ Million for Years 2024 through 2030 and % CAGR
- TABLE 15: World Historic Review for Electrolysis Process by Geographic Region - USA, Canada, Japan, China, Europe, Asia-Pacific, Latin America, Middle East and Africa Markets - Independent Analysis of Annual Sales in US$ Million for Years 2014 through 2023 and % CAGR
- TABLE 16: World 16-Year Perspective for Electrolysis Process by Geographic Region - Percentage Breakdown of Value Sales for USA, Canada, Japan, China, Europe, Asia-Pacific, Latin America, Middle East and Africa for Years 2014, 2025 & 2030
- TABLE 17: World Recent Past, Current & Future Analysis for Partial Oxidation Process by Geographic Region - USA, Canada, Japan, China, Europe, Asia-Pacific, Latin America, Middle East and Africa Markets - Independent Analysis of Annual Sales in US$ Million for Years 2024 through 2030 and % CAGR
- TABLE 18: World Historic Review for Partial Oxidation Process by Geographic Region - USA, Canada, Japan, China, Europe, Asia-Pacific, Latin America, Middle East and Africa Markets - Independent Analysis of Annual Sales in US$ Million for Years 2014 through 2023 and % CAGR
- TABLE 19: World 16-Year Perspective for Partial Oxidation Process by Geographic Region - Percentage Breakdown of Value Sales for USA, Canada, Japan, China, Europe, Asia-Pacific, Latin America, Middle East and Africa for Years 2014, 2025 & 2030
- TABLE 20: World Recent Past, Current & Future Analysis for Auto-Thermal Reforming Process by Geographic Region - USA, Canada, Japan, China, Europe, Asia-Pacific, Latin America, Middle East and Africa Markets - Independent Analysis of Annual Sales in US$ Million for Years 2024 through 2030 and % CAGR
- TABLE 21: World Historic Review for Auto-Thermal Reforming Process by Geographic Region - USA, Canada, Japan, China, Europe, Asia-Pacific, Latin America, Middle East and Africa Markets - Independent Analysis of Annual Sales in US$ Million for Years 2014 through 2023 and % CAGR
- TABLE 22: World 16-Year Perspective for Auto-Thermal Reforming Process by Geographic Region - Percentage Breakdown of Value Sales for USA, Canada, Japan, China, Europe, Asia-Pacific, Latin America, Middle East and Africa for Years 2014, 2025 & 2030
- TABLE 23: World Recent Past, Current & Future Analysis for Biomass Gasification Process by Geographic Region - USA, Canada, Japan, China, Europe, Asia-Pacific, Latin America, Middle East and Africa Markets - Independent Analysis of Annual Sales in US$ Million for Years 2024 through 2030 and % CAGR
- TABLE 24: World Historic Review for Biomass Gasification Process by Geographic Region - USA, Canada, Japan, China, Europe, Asia-Pacific, Latin America, Middle East and Africa Markets - Independent Analysis of Annual Sales in US$ Million for Years 2014 through 2023 and % CAGR
- TABLE 25: World 16-Year Perspective for Biomass Gasification Process by Geographic Region - Percentage Breakdown of Value Sales for USA, Canada, Japan, China, Europe, Asia-Pacific, Latin America, Middle East and Africa for Years 2014, 2025 & 2030
- III. MARKET ANALYSIS
- UNITED STATES
- Petroleum Refining Hydrogen Generation Market Presence - Strong/Active/Niche/Trivial - Key Competitors in the United States for 2025 (E)
- TABLE 26: USA Recent Past, Current & Future Analysis for Petroleum Refining Hydrogen Generation by Delivery mode - Captive Delivery Mode and Merchant Delivery Mode - Independent Analysis of Annual Sales in US$ Million for the Years 2024 through 2030 and % CAGR
- TABLE 27: USA Historic Review for Petroleum Refining Hydrogen Generation by Delivery mode - Captive Delivery Mode and Merchant Delivery Mode Markets - Independent Analysis of Annual Sales in US$ Million for Years 2014 through 2023 and % CAGR
- TABLE 28: USA 16-Year Perspective for Petroleum Refining Hydrogen Generation by Delivery mode - Percentage Breakdown of Value Sales for Captive Delivery Mode and Merchant Delivery Mode for the Years 2014, 2025 & 2030
- TABLE 29: USA Recent Past, Current & Future Analysis for Petroleum Refining Hydrogen Generation by Process - Steam Methane Reforming Process, Electrolysis Process, Partial Oxidation Process, Auto-Thermal Reforming Process and Biomass Gasification Process - Independent Analysis of Annual Sales in US$ Million for the Years 2024 through 2030 and % CAGR
- TABLE 30: USA Historic Review for Petroleum Refining Hydrogen Generation by Process - Steam Methane Reforming Process, Electrolysis Process, Partial Oxidation Process, Auto-Thermal Reforming Process and Biomass Gasification Process Markets - Independent Analysis of Annual Sales in US$ Million for Years 2014 through 2023 and % CAGR
- TABLE 31: USA 16-Year Perspective for Petroleum Refining Hydrogen Generation by Process - Percentage Breakdown of Value Sales for Steam Methane Reforming Process, Electrolysis Process, Partial Oxidation Process, Auto-Thermal Reforming Process and Biomass Gasification Process for the Years 2014, 2025 & 2030
- CANADA
- TABLE 32: Canada Recent Past, Current & Future Analysis for Petroleum Refining Hydrogen Generation by Delivery mode - Captive Delivery Mode and Merchant Delivery Mode - Independent Analysis of Annual Sales in US$ Million for the Years 2024 through 2030 and % CAGR
- TABLE 33: Canada Historic Review for Petroleum Refining Hydrogen Generation by Delivery mode - Captive Delivery Mode and Merchant Delivery Mode Markets - Independent Analysis of Annual Sales in US$ Million for Years 2014 through 2023 and % CAGR
- TABLE 34: Canada 16-Year Perspective for Petroleum Refining Hydrogen Generation by Delivery mode - Percentage Breakdown of Value Sales for Captive Delivery Mode and Merchant Delivery Mode for the Years 2014, 2025 & 2030
- TABLE 35: Canada Recent Past, Current & Future Analysis for Petroleum Refining Hydrogen Generation by Process - Steam Methane Reforming Process, Electrolysis Process, Partial Oxidation Process, Auto-Thermal Reforming Process and Biomass Gasification Process - Independent Analysis of Annual Sales in US$ Million for the Years 2024 through 2030 and % CAGR
- TABLE 36: Canada Historic Review for Petroleum Refining Hydrogen Generation by Process - Steam Methane Reforming Process, Electrolysis Process, Partial Oxidation Process, Auto-Thermal Reforming Process and Biomass Gasification Process Markets - Independent Analysis of Annual Sales in US$ Million for Years 2014 through 2023 and % CAGR
- TABLE 37: Canada 16-Year Perspective for Petroleum Refining Hydrogen Generation by Process - Percentage Breakdown of Value Sales for Steam Methane Reforming Process, Electrolysis Process, Partial Oxidation Process, Auto-Thermal Reforming Process and Biomass Gasification Process for the Years 2014, 2025 & 2030
- JAPAN
- Petroleum Refining Hydrogen Generation Market Presence - Strong/Active/Niche/Trivial - Key Competitors in Japan for 2025 (E)
- TABLE 38: Japan Recent Past, Current & Future Analysis for Petroleum Refining Hydrogen Generation by Delivery mode - Captive Delivery Mode and Merchant Delivery Mode - Independent Analysis of Annual Sales in US$ Million for the Years 2024 through 2030 and % CAGR
- TABLE 39: Japan Historic Review for Petroleum Refining Hydrogen Generation by Delivery mode - Captive Delivery Mode and Merchant Delivery Mode Markets - Independent Analysis of Annual Sales in US$ Million for Years 2014 through 2023 and % CAGR
- TABLE 40: Japan 16-Year Perspective for Petroleum Refining Hydrogen Generation by Delivery mode - Percentage Breakdown of Value Sales for Captive Delivery Mode and Merchant Delivery Mode for the Years 2014, 2025 & 2030
- TABLE 41: Japan Recent Past, Current & Future Analysis for Petroleum Refining Hydrogen Generation by Process - Steam Methane Reforming Process, Electrolysis Process, Partial Oxidation Process, Auto-Thermal Reforming Process and Biomass Gasification Process - Independent Analysis of Annual Sales in US$ Million for the Years 2024 through 2030 and % CAGR
- TABLE 42: Japan Historic Review for Petroleum Refining Hydrogen Generation by Process - Steam Methane Reforming Process, Electrolysis Process, Partial Oxidation Process, Auto-Thermal Reforming Process and Biomass Gasification Process Markets - Independent Analysis of Annual Sales in US$ Million for Years 2014 through 2023 and % CAGR
- TABLE 43: Japan 16-Year Perspective for Petroleum Refining Hydrogen Generation by Process - Percentage Breakdown of Value Sales for Steam Methane Reforming Process, Electrolysis Process, Partial Oxidation Process, Auto-Thermal Reforming Process and Biomass Gasification Process for the Years 2014, 2025 & 2030
- CHINA
- Petroleum Refining Hydrogen Generation Market Presence - Strong/Active/Niche/Trivial - Key Competitors in China for 2025 (E)
- TABLE 44: China Recent Past, Current & Future Analysis for Petroleum Refining Hydrogen Generation by Delivery mode - Captive Delivery Mode and Merchant Delivery Mode - Independent Analysis of Annual Sales in US$ Million for the Years 2024 through 2030 and % CAGR
- TABLE 45: China Historic Review for Petroleum Refining Hydrogen Generation by Delivery mode - Captive Delivery Mode and Merchant Delivery Mode Markets - Independent Analysis of Annual Sales in US$ Million for Years 2014 through 2023 and % CAGR
- TABLE 46: China 16-Year Perspective for Petroleum Refining Hydrogen Generation by Delivery mode - Percentage Breakdown of Value Sales for Captive Delivery Mode and Merchant Delivery Mode for the Years 2014, 2025 & 2030
- TABLE 47: China Recent Past, Current & Future Analysis for Petroleum Refining Hydrogen Generation by Process - Steam Methane Reforming Process, Electrolysis Process, Partial Oxidation Process, Auto-Thermal Reforming Process and Biomass Gasification Process - Independent Analysis of Annual Sales in US$ Million for the Years 2024 through 2030 and % CAGR
- TABLE 48: China Historic Review for Petroleum Refining Hydrogen Generation by Process - Steam Methane Reforming Process, Electrolysis Process, Partial Oxidation Process, Auto-Thermal Reforming Process and Biomass Gasification Process Markets - Independent Analysis of Annual Sales in US$ Million for Years 2014 through 2023 and % CAGR
- TABLE 49: China 16-Year Perspective for Petroleum Refining Hydrogen Generation by Process - Percentage Breakdown of Value Sales for Steam Methane Reforming Process, Electrolysis Process, Partial Oxidation Process, Auto-Thermal Reforming Process and Biomass Gasification Process for the Years 2014, 2025 & 2030
- EUROPE
- Petroleum Refining Hydrogen Generation Market Presence - Strong/Active/Niche/Trivial - Key Competitors in Europe for 2025 (E)
- TABLE 50: Europe Recent Past, Current & Future Analysis for Petroleum Refining Hydrogen Generation by Geographic Region - France, Germany, Italy, UK, Spain, Russia and Rest of Europe Markets - Independent Analysis of Annual Sales in US$ Million for Years 2024 through 2030 and % CAGR
- TABLE 51: Europe Historic Review for Petroleum Refining Hydrogen Generation by Geographic Region - France, Germany, Italy, UK, Spain, Russia and Rest of Europe Markets - Independent Analysis of Annual Sales in US$ Million for Years 2014 through 2023 and % CAGR
- TABLE 52: Europe 16-Year Perspective for Petroleum Refining Hydrogen Generation by Geographic Region - Percentage Breakdown of Value Sales for France, Germany, Italy, UK, Spain, Russia and Rest of Europe Markets for Years 2014, 2025 & 2030
- TABLE 53: Europe Recent Past, Current & Future Analysis for Petroleum Refining Hydrogen Generation by Delivery mode - Captive Delivery Mode and Merchant Delivery Mode - Independent Analysis of Annual Sales in US$ Million for the Years 2024 through 2030 and % CAGR
- TABLE 54: Europe Historic Review for Petroleum Refining Hydrogen Generation by Delivery mode - Captive Delivery Mode and Merchant Delivery Mode Markets - Independent Analysis of Annual Sales in US$ Million for Years 2014 through 2023 and % CAGR
- TABLE 55: Europe 16-Year Perspective for Petroleum Refining Hydrogen Generation by Delivery mode - Percentage Breakdown of Value Sales for Captive Delivery Mode and Merchant Delivery Mode for the Years 2014, 2025 & 2030
- TABLE 56: Europe Recent Past, Current & Future Analysis for Petroleum Refining Hydrogen Generation by Process - Steam Methane Reforming Process, Electrolysis Process, Partial Oxidation Process, Auto-Thermal Reforming Process and Biomass Gasification Process - Independent Analysis of Annual Sales in US$ Million for the Years 2024 through 2030 and % CAGR
- TABLE 57: Europe Historic Review for Petroleum Refining Hydrogen Generation by Process - Steam Methane Reforming Process, Electrolysis Process, Partial Oxidation Process, Auto-Thermal Reforming Process and Biomass Gasification Process Markets - Independent Analysis of Annual Sales in US$ Million for Years 2014 through 2023 and % CAGR
- TABLE 58: Europe 16-Year Perspective for Petroleum Refining Hydrogen Generation by Process - Percentage Breakdown of Value Sales for Steam Methane Reforming Process, Electrolysis Process, Partial Oxidation Process, Auto-Thermal Reforming Process and Biomass Gasification Process for the Years 2014, 2025 & 2030
- FRANCE
- Petroleum Refining Hydrogen Generation Market Presence - Strong/Active/Niche/Trivial - Key Competitors in France for 2025 (E)
- TABLE 59: France Recent Past, Current & Future Analysis for Petroleum Refining Hydrogen Generation by Delivery mode - Captive Delivery Mode and Merchant Delivery Mode - Independent Analysis of Annual Sales in US$ Million for the Years 2024 through 2030 and % CAGR
- TABLE 60: France Historic Review for Petroleum Refining Hydrogen Generation by Delivery mode - Captive Delivery Mode and Merchant Delivery Mode Markets - Independent Analysis of Annual Sales in US$ Million for Years 2014 through 2023 and % CAGR
- TABLE 61: France 16-Year Perspective for Petroleum Refining Hydrogen Generation by Delivery mode - Percentage Breakdown of Value Sales for Captive Delivery Mode and Merchant Delivery Mode for the Years 2014, 2025 & 2030
- TABLE 62: France Recent Past, Current & Future Analysis for Petroleum Refining Hydrogen Generation by Process - Steam Methane Reforming Process, Electrolysis Process, Partial Oxidation Process, Auto-Thermal Reforming Process and Biomass Gasification Process - Independent Analysis of Annual Sales in US$ Million for the Years 2024 through 2030 and % CAGR
- TABLE 63: France Historic Review for Petroleum Refining Hydrogen Generation by Process - Steam Methane Reforming Process, Electrolysis Process, Partial Oxidation Process, Auto-Thermal Reforming Process and Biomass Gasification Process Markets - Independent Analysis of Annual Sales in US$ Million for Years 2014 through 2023 and % CAGR
- TABLE 64: France 16-Year Perspective for Petroleum Refining Hydrogen Generation by Process - Percentage Breakdown of Value Sales for Steam Methane Reforming Process, Electrolysis Process, Partial Oxidation Process, Auto-Thermal Reforming Process and Biomass Gasification Process for the Years 2014, 2025 & 2030
- GERMANY
- Petroleum Refining Hydrogen Generation Market Presence - Strong/Active/Niche/Trivial - Key Competitors in Germany for 2025 (E)
- TABLE 65: Germany Recent Past, Current & Future Analysis for Petroleum Refining Hydrogen Generation by Delivery mode - Captive Delivery Mode and Merchant Delivery Mode - Independent Analysis of Annual Sales in US$ Million for the Years 2024 through 2030 and % CAGR
- TABLE 66: Germany Historic Review for Petroleum Refining Hydrogen Generation by Delivery mode - Captive Delivery Mode and Merchant Delivery Mode Markets - Independent Analysis of Annual Sales in US$ Million for Years 2014 through 2023 and % CAGR
- TABLE 67: Germany 16-Year Perspective for Petroleum Refining Hydrogen Generation by Delivery mode - Percentage Breakdown of Value Sales for Captive Delivery Mode and Merchant Delivery Mode for the Years 2014, 2025 & 2030
- TABLE 68: Germany Recent Past, Current & Future Analysis for Petroleum Refining Hydrogen Generation by Process - Steam Methane Reforming Process, Electrolysis Process, Partial Oxidation Process, Auto-Thermal Reforming Process and Biomass Gasification Process - Independent Analysis of Annual Sales in US$ Million for the Years 2024 through 2030 and % CAGR
- TABLE 69: Germany Historic Review for Petroleum Refining Hydrogen Generation by Process - Steam Methane Reforming Process, Electrolysis Process, Partial Oxidation Process, Auto-Thermal Reforming Process and Biomass Gasification Process Markets - Independent Analysis of Annual Sales in US$ Million for Years 2014 through 2023 and % CAGR
- TABLE 70: Germany 16-Year Perspective for Petroleum Refining Hydrogen Generation by Process - Percentage Breakdown of Value Sales for Steam Methane Reforming Process, Electrolysis Process, Partial Oxidation Process, Auto-Thermal Reforming Process and Biomass Gasification Process for the Years 2014, 2025 & 2030
- ITALY
- TABLE 71: Italy Recent Past, Current & Future Analysis for Petroleum Refining Hydrogen Generation by Delivery mode - Captive Delivery Mode and Merchant Delivery Mode - Independent Analysis of Annual Sales in US$ Million for the Years 2024 through 2030 and % CAGR
- TABLE 72: Italy Historic Review for Petroleum Refining Hydrogen Generation by Delivery mode - Captive Delivery Mode and Merchant Delivery Mode Markets - Independent Analysis of Annual Sales in US$ Million for Years 2014 through 2023 and % CAGR
- TABLE 73: Italy 16-Year Perspective for Petroleum Refining Hydrogen Generation by Delivery mode - Percentage Breakdown of Value Sales for Captive Delivery Mode and Merchant Delivery Mode for the Years 2014, 2025 & 2030
- TABLE 74: Italy Recent Past, Current & Future Analysis for Petroleum Refining Hydrogen Generation by Process - Steam Methane Reforming Process, Electrolysis Process, Partial Oxidation Process, Auto-Thermal Reforming Process and Biomass Gasification Process - Independent Analysis of Annual Sales in US$ Million for the Years 2024 through 2030 and % CAGR
- TABLE 75: Italy Historic Review for Petroleum Refining Hydrogen Generation by Process - Steam Methane Reforming Process, Electrolysis Process, Partial Oxidation Process, Auto-Thermal Reforming Process and Biomass Gasification Process Markets - Independent Analysis of Annual Sales in US$ Million for Years 2014 through 2023 and % CAGR
- TABLE 76: Italy 16-Year Perspective for Petroleum Refining Hydrogen Generation by Process - Percentage Breakdown of Value Sales for Steam Methane Reforming Process, Electrolysis Process, Partial Oxidation Process, Auto-Thermal Reforming Process and Biomass Gasification Process for the Years 2014, 2025 & 2030
- UNITED KINGDOM
- Petroleum Refining Hydrogen Generation Market Presence - Strong/Active/Niche/Trivial - Key Competitors in the United Kingdom for 2025 (E)
- TABLE 77: UK Recent Past, Current & Future Analysis for Petroleum Refining Hydrogen Generation by Delivery mode - Captive Delivery Mode and Merchant Delivery Mode - Independent Analysis of Annual Sales in US$ Million for the Years 2024 through 2030 and % CAGR
- TABLE 78: UK Historic Review for Petroleum Refining Hydrogen Generation by Delivery mode - Captive Delivery Mode and Merchant Delivery Mode Markets - Independent Analysis of Annual Sales in US$ Million for Years 2014 through 2023 and % CAGR
- TABLE 79: UK 16-Year Perspective for Petroleum Refining Hydrogen Generation by Delivery mode - Percentage Breakdown of Value Sales for Captive Delivery Mode and Merchant Delivery Mode for the Years 2014, 2025 & 2030
- TABLE 80: UK Recent Past, Current & Future Analysis for Petroleum Refining Hydrogen Generation by Process - Steam Methane Reforming Process, Electrolysis Process, Partial Oxidation Process, Auto-Thermal Reforming Process and Biomass Gasification Process - Independent Analysis of Annual Sales in US$ Million for the Years 2024 through 2030 and % CAGR
- TABLE 81: UK Historic Review for Petroleum Refining Hydrogen Generation by Process - Steam Methane Reforming Process, Electrolysis Process, Partial Oxidation Process, Auto-Thermal Reforming Process and Biomass Gasification Process Markets - Independent Analysis of Annual Sales in US$ Million for Years 2014 through 2023 and % CAGR
- TABLE 82: UK 16-Year Perspective for Petroleum Refining Hydrogen Generation by Process - Percentage Breakdown of Value Sales for Steam Methane Reforming Process, Electrolysis Process, Partial Oxidation Process, Auto-Thermal Reforming Process and Biomass Gasification Process for the Years 2014, 2025 & 2030
- SPAIN
- TABLE 83: Spain Recent Past, Current & Future Analysis for Petroleum Refining Hydrogen Generation by Delivery mode - Captive Delivery Mode and Merchant Delivery Mode - Independent Analysis of Annual Sales in US$ Million for the Years 2024 through 2030 and % CAGR
- TABLE 84: Spain Historic Review for Petroleum Refining Hydrogen Generation by Delivery mode - Captive Delivery Mode and Merchant Delivery Mode Markets - Independent Analysis of Annual Sales in US$ Million for Years 2014 through 2023 and % CAGR
- TABLE 85: Spain 16-Year Perspective for Petroleum Refining Hydrogen Generation by Delivery mode - Percentage Breakdown of Value Sales for Captive Delivery Mode and Merchant Delivery Mode for the Years 2014, 2025 & 2030
- TABLE 86: Spain Recent Past, Current & Future Analysis for Petroleum Refining Hydrogen Generation by Process - Steam Methane Reforming Process, Electrolysis Process, Partial Oxidation Process, Auto-Thermal Reforming Process and Biomass Gasification Process - Independent Analysis of Annual Sales in US$ Million for the Years 2024 through 2030 and % CAGR
- TABLE 87: Spain Historic Review for Petroleum Refining Hydrogen Generation by Process - Steam Methane Reforming Process, Electrolysis Process, Partial Oxidation Process, Auto-Thermal Reforming Process and Biomass Gasification Process Markets - Independent Analysis of Annual Sales in US$ Million for Years 2014 through 2023 and % CAGR
- TABLE 88: Spain 16-Year Perspective for Petroleum Refining Hydrogen Generation by Process - Percentage Breakdown of Value Sales for Steam Methane Reforming Process, Electrolysis Process, Partial Oxidation Process, Auto-Thermal Reforming Process and Biomass Gasification Process for the Years 2014, 2025 & 2030
- RUSSIA
- TABLE 89: Russia Recent Past, Current & Future Analysis for Petroleum Refining Hydrogen Generation by Delivery mode - Captive Delivery Mode and Merchant Delivery Mode - Independent Analysis of Annual Sales in US$ Million for the Years 2024 through 2030 and % CAGR
- TABLE 90: Russia Historic Review for Petroleum Refining Hydrogen Generation by Delivery mode - Captive Delivery Mode and Merchant Delivery Mode Markets - Independent Analysis of Annual Sales in US$ Million for Years 2014 through 2023 and % CAGR
- TABLE 91: Russia 16-Year Perspective for Petroleum Refining Hydrogen Generation by Delivery mode - Percentage Breakdown of Value Sales for Captive Delivery Mode and Merchant Delivery Mode for the Years 2014, 2025 & 2030
- TABLE 92: Russia Recent Past, Current & Future Analysis for Petroleum Refining Hydrogen Generation by Process - Steam Methane Reforming Process, Electrolysis Process, Partial Oxidation Process, Auto-Thermal Reforming Process and Biomass Gasification Process - Independent Analysis of Annual Sales in US$ Million for the Years 2024 through 2030 and % CAGR
- TABLE 93: Russia Historic Review for Petroleum Refining Hydrogen Generation by Process - Steam Methane Reforming Process, Electrolysis Process, Partial Oxidation Process, Auto-Thermal Reforming Process and Biomass Gasification Process Markets - Independent Analysis of Annual Sales in US$ Million for Years 2014 through 2023 and % CAGR
- TABLE 94: Russia 16-Year Perspective for Petroleum Refining Hydrogen Generation by Process - Percentage Breakdown of Value Sales for Steam Methane Reforming Process, Electrolysis Process, Partial Oxidation Process, Auto-Thermal Reforming Process and Biomass Gasification Process for the Years 2014, 2025 & 2030
- REST OF EUROPE
- TABLE 95: Rest of Europe Recent Past, Current & Future Analysis for Petroleum Refining Hydrogen Generation by Delivery mode - Captive Delivery Mode and Merchant Delivery Mode - Independent Analysis of Annual Sales in US$ Million for the Years 2024 through 2030 and % CAGR
- TABLE 96: Rest of Europe Historic Review for Petroleum Refining Hydrogen Generation by Delivery mode - Captive Delivery Mode and Merchant Delivery Mode Markets - Independent Analysis of Annual Sales in US$ Million for Years 2014 through 2023 and % CAGR
- TABLE 97: Rest of Europe 16-Year Perspective for Petroleum Refining Hydrogen Generation by Delivery mode - Percentage Breakdown of Value Sales for Captive Delivery Mode and Merchant Delivery Mode for the Years 2014, 2025 & 2030
- TABLE 98: Rest of Europe Recent Past, Current & Future Analysis for Petroleum Refining Hydrogen Generation by Process - Steam Methane Reforming Process, Electrolysis Process, Partial Oxidation Process, Auto-Thermal Reforming Process and Biomass Gasification Process - Independent Analysis of Annual Sales in US$ Million for the Years 2024 through 2030 and % CAGR
- TABLE 99: Rest of Europe Historic Review for Petroleum Refining Hydrogen Generation by Process - Steam Methane Reforming Process, Electrolysis Process, Partial Oxidation Process, Auto-Thermal Reforming Process and Biomass Gasification Process Markets - Independent Analysis of Annual Sales in US$ Million for Years 2014 through 2023 and % CAGR
- TABLE 100: Rest of Europe 16-Year Perspective for Petroleum Refining Hydrogen Generation by Process - Percentage Breakdown of Value Sales for Steam Methane Reforming Process, Electrolysis Process, Partial Oxidation Process, Auto-Thermal Reforming Process and Biomass Gasification Process for the Years 2014, 2025 & 2030
- ASIA-PACIFIC
- Petroleum Refining Hydrogen Generation Market Presence - Strong/Active/Niche/Trivial - Key Competitors in Asia-Pacific for 2025 (E)
- TABLE 101: Asia-Pacific Recent Past, Current & Future Analysis for Petroleum Refining Hydrogen Generation by Geographic Region - Australia, India, South Korea and Rest of Asia-Pacific Markets - Independent Analysis of Annual Sales in US$ Million for Years 2024 through 2030 and % CAGR
- TABLE 102: Asia-Pacific Historic Review for Petroleum Refining Hydrogen Generation by Geographic Region - Australia, India, South Korea and Rest of Asia-Pacific Markets - Independent Analysis of Annual Sales in US$ Million for Years 2014 through 2023 and % CAGR
- TABLE 103: Asia-Pacific 16-Year Perspective for Petroleum Refining Hydrogen Generation by Geographic Region - Percentage Breakdown of Value Sales for Australia, India, South Korea and Rest of Asia-Pacific Markets for Years 2014, 2025 & 2030
- TABLE 104: Asia-Pacific Recent Past, Current & Future Analysis for Petroleum Refining Hydrogen Generation by Delivery mode - Captive Delivery Mode and Merchant Delivery Mode - Independent Analysis of Annual Sales in US$ Million for the Years 2024 through 2030 and % CAGR
- TABLE 105: Asia-Pacific Historic Review for Petroleum Refining Hydrogen Generation by Delivery mode - Captive Delivery Mode and Merchant Delivery Mode Markets - Independent Analysis of Annual Sales in US$ Million for Years 2014 through 2023 and % CAGR
- TABLE 106: Asia-Pacific 16-Year Perspective for Petroleum Refining Hydrogen Generation by Delivery mode - Percentage Breakdown of Value Sales for Captive Delivery Mode and Merchant Delivery Mode for the Years 2014, 2025 & 2030
- TABLE 107: Asia-Pacific Recent Past, Current & Future Analysis for Petroleum Refining Hydrogen Generation by Process - Steam Methane Reforming Process, Electrolysis Process, Partial Oxidation Process, Auto-Thermal Reforming Process and Biomass Gasification Process - Independent Analysis of Annual Sales in US$ Million for the Years 2024 through 2030 and % CAGR
- TABLE 108: Asia-Pacific Historic Review for Petroleum Refining Hydrogen Generation by Process - Steam Methane Reforming Process, Electrolysis Process, Partial Oxidation Process, Auto-Thermal Reforming Process and Biomass Gasification Process Markets - Independent Analysis of Annual Sales in US$ Million for Years 2014 through 2023 and % CAGR
- TABLE 109: Asia-Pacific 16-Year Perspective for Petroleum Refining Hydrogen Generation by Process - Percentage Breakdown of Value Sales for Steam Methane Reforming Process, Electrolysis Process, Partial Oxidation Process, Auto-Thermal Reforming Process and Biomass Gasification Process for the Years 2014, 2025 & 2030
- AUSTRALIA
- Petroleum Refining Hydrogen Generation Market Presence - Strong/Active/Niche/Trivial - Key Competitors in Australia for 2025 (E)
- TABLE 110: Australia Recent Past, Current & Future Analysis for Petroleum Refining Hydrogen Generation by Delivery mode - Captive Delivery Mode and Merchant Delivery Mode - Independent Analysis of Annual Sales in US$ Million for the Years 2024 through 2030 and % CAGR
- TABLE 111: Australia Historic Review for Petroleum Refining Hydrogen Generation by Delivery mode - Captive Delivery Mode and Merchant Delivery Mode Markets - Independent Analysis of Annual Sales in US$ Million for Years 2014 through 2023 and % CAGR
- TABLE 112: Australia 16-Year Perspective for Petroleum Refining Hydrogen Generation by Delivery mode - Percentage Breakdown of Value Sales for Captive Delivery Mode and Merchant Delivery Mode for the Years 2014, 2025 & 2030
- TABLE 113: Australia Recent Past, Current & Future Analysis for Petroleum Refining Hydrogen Generation by Process - Steam Methane Reforming Process, Electrolysis Process, Partial Oxidation Process, Auto-Thermal Reforming Process and Biomass Gasification Process - Independent Analysis of Annual Sales in US$ Million for the Years 2024 through 2030 and % CAGR
- TABLE 114: Australia Historic Review for Petroleum Refining Hydrogen Generation by Process - Steam Methane Reforming Process, Electrolysis Process, Partial Oxidation Process, Auto-Thermal Reforming Process and Biomass Gasification Process Markets - Independent Analysis of Annual Sales in US$ Million for Years 2014 through 2023 and % CAGR
- TABLE 115: Australia 16-Year Perspective for Petroleum Refining Hydrogen Generation by Process - Percentage Breakdown of Value Sales for Steam Methane Reforming Process, Electrolysis Process, Partial Oxidation Process, Auto-Thermal Reforming Process and Biomass Gasification Process for the Years 2014, 2025 & 2030
- INDIA
- Petroleum Refining Hydrogen Generation Market Presence - Strong/Active/Niche/Trivial - Key Competitors in India for 2025 (E)
- TABLE 116: India Recent Past, Current & Future Analysis for Petroleum Refining Hydrogen Generation by Delivery mode - Captive Delivery Mode and Merchant Delivery Mode - Independent Analysis of Annual Sales in US$ Million for the Years 2024 through 2030 and % CAGR
- TABLE 117: India Historic Review for Petroleum Refining Hydrogen Generation by Delivery mode - Captive Delivery Mode and Merchant Delivery Mode Markets - Independent Analysis of Annual Sales in US$ Million for Years 2014 through 2023 and % CAGR
- TABLE 118: India 16-Year Perspective for Petroleum Refining Hydrogen Generation by Delivery mode - Percentage Breakdown of Value Sales for Captive Delivery Mode and Merchant Delivery Mode for the Years 2014, 2025 & 2030
- TABLE 119: India Recent Past, Current & Future Analysis for Petroleum Refining Hydrogen Generation by Process - Steam Methane Reforming Process, Electrolysis Process, Partial Oxidation Process, Auto-Thermal Reforming Process and Biomass Gasification Process - Independent Analysis of Annual Sales in US$ Million for the Years 2024 through 2030 and % CAGR
- TABLE 120: India Historic Review for Petroleum Refining Hydrogen Generation by Process - Steam Methane Reforming Process, Electrolysis Process, Partial Oxidation Process, Auto-Thermal Reforming Process and Biomass Gasification Process Markets - Independent Analysis of Annual Sales in US$ Million for Years 2014 through 2023 and % CAGR
- TABLE 121: India 16-Year Perspective for Petroleum Refining Hydrogen Generation by Process - Percentage Breakdown of Value Sales for Steam Methane Reforming Process, Electrolysis Process, Partial Oxidation Process, Auto-Thermal Reforming Process and Biomass Gasification Process for the Years 2014, 2025 & 2030
- SOUTH KOREA
- TABLE 122: South Korea Recent Past, Current & Future Analysis for Petroleum Refining Hydrogen Generation by Delivery mode - Captive Delivery Mode and Merchant Delivery Mode - Independent Analysis of Annual Sales in US$ Million for the Years 2024 through 2030 and % CAGR
- TABLE 123: South Korea Historic Review for Petroleum Refining Hydrogen Generation by Delivery mode - Captive Delivery Mode and Merchant Delivery Mode Markets - Independent Analysis of Annual Sales in US$ Million for Years 2014 through 2023 and % CAGR
- TABLE 124: South Korea 16-Year Perspective for Petroleum Refining Hydrogen Generation by Delivery mode - Percentage Breakdown of Value Sales for Captive Delivery Mode and Merchant Delivery Mode for the Years 2014, 2025 & 2030
- TABLE 125: South Korea Recent Past, Current & Future Analysis for Petroleum Refining Hydrogen Generation by Process - Steam Methane Reforming Process, Electrolysis Process, Partial Oxidation Process, Auto-Thermal Reforming Process and Biomass Gasification Process - Independent Analysis of Annual Sales in US$ Million for the Years 2024 through 2030 and % CAGR
- TABLE 126: South Korea Historic Review for Petroleum Refining Hydrogen Generation by Process - Steam Methane Reforming Process, Electrolysis Process, Partial Oxidation Process, Auto-Thermal Reforming Process and Biomass Gasification Process Markets - Independent Analysis of Annual Sales in US$ Million for Years 2014 through 2023 and % CAGR
- TABLE 127: South Korea 16-Year Perspective for Petroleum Refining Hydrogen Generation by Process - Percentage Breakdown of Value Sales for Steam Methane Reforming Process, Electrolysis Process, Partial Oxidation Process, Auto-Thermal Reforming Process and Biomass Gasification Process for the Years 2014, 2025 & 2030
- REST OF ASIA-PACIFIC
- TABLE 128: Rest of Asia-Pacific Recent Past, Current & Future Analysis for Petroleum Refining Hydrogen Generation by Delivery mode - Captive Delivery Mode and Merchant Delivery Mode - Independent Analysis of Annual Sales in US$ Million for the Years 2024 through 2030 and % CAGR
- TABLE 129: Rest of Asia-Pacific Historic Review for Petroleum Refining Hydrogen Generation by Delivery mode - Captive Delivery Mode and Merchant Delivery Mode Markets - Independent Analysis of Annual Sales in US$ Million for Years 2014 through 2023 and % CAGR
- TABLE 130: Rest of Asia-Pacific 16-Year Perspective for Petroleum Refining Hydrogen Generation by Delivery mode - Percentage Breakdown of Value Sales for Captive Delivery Mode and Merchant Delivery Mode for the Years 2014, 2025 & 2030
- TABLE 131: Rest of Asia-Pacific Recent Past, Current & Future Analysis for Petroleum Refining Hydrogen Generation by Process - Steam Methane Reforming Process, Electrolysis Process, Partial Oxidation Process, Auto-Thermal Reforming Process and Biomass Gasification Process - Independent Analysis of Annual Sales in US$ Million for the Years 2024 through 2030 and % CAGR
- TABLE 132: Rest of Asia-Pacific Historic Review for Petroleum Refining Hydrogen Generation by Process - Steam Methane Reforming Process, Electrolysis Process, Partial Oxidation Process, Auto-Thermal Reforming Process and Biomass Gasification Process Markets - Independent Analysis of Annual Sales in US$ Million for Years 2014 through 2023 and % CAGR
- TABLE 133: Rest of Asia-Pacific 16-Year Perspective for Petroleum Refining Hydrogen Generation by Process - Percentage Breakdown of Value Sales for Steam Methane Reforming Process, Electrolysis Process, Partial Oxidation Process, Auto-Thermal Reforming Process and Biomass Gasification Process for the Years 2014, 2025 & 2030
- LATIN AMERICA
- Petroleum Refining Hydrogen Generation Market Presence - Strong/Active/Niche/Trivial - Key Competitors in Latin America for 2025 (E)
- TABLE 134: Latin America Recent Past, Current & Future Analysis for Petroleum Refining Hydrogen Generation by Geographic Region - Argentina, Brazil, Mexico and Rest of Latin America Markets - Independent Analysis of Annual Sales in US$ Million for Years 2024 through 2030 and % CAGR
- TABLE 135: Latin America Historic Review for Petroleum Refining Hydrogen Generation by Geographic Region - Argentina, Brazil, Mexico and Rest of Latin America Markets - Independent Analysis of Annual Sales in US$ Million for Years 2014 through 2023 and % CAGR
- TABLE 136: Latin America 16-Year Perspective for Petroleum Refining Hydrogen Generation by Geographic Region - Percentage Breakdown of Value Sales for Argentina, Brazil, Mexico and Rest of Latin America Markets for Years 2014, 2025 & 2030
- TABLE 137: Latin America Recent Past, Current & Future Analysis for Petroleum Refining Hydrogen Generation by Delivery mode - Captive Delivery Mode and Merchant Delivery Mode - Independent Analysis of Annual Sales in US$ Million for the Years 2024 through 2030 and % CAGR
- TABLE 138: Latin America Historic Review for Petroleum Refining Hydrogen Generation by Delivery mode - Captive Delivery Mode and Merchant Delivery Mode Markets - Independent Analysis of Annual Sales in US$ Million for Years 2014 through 2023 and % CAGR
- TABLE 139: Latin America 16-Year Perspective for Petroleum Refining Hydrogen Generation by Delivery mode - Percentage Breakdown of Value Sales for Captive Delivery Mode and Merchant Delivery Mode for the Years 2014, 2025 & 2030
- TABLE 140: Latin America Recent Past, Current & Future Analysis for Petroleum Refining Hydrogen Generation by Process - Steam Methane Reforming Process, Electrolysis Process, Partial Oxidation Process, Auto-Thermal Reforming Process and Biomass Gasification Process - Independent Analysis of Annual Sales in US$ Million for the Years 2024 through 2030 and % CAGR
- TABLE 141: Latin America Historic Review for Petroleum Refining Hydrogen Generation by Process - Steam Methane Reforming Process, Electrolysis Process, Partial Oxidation Process, Auto-Thermal Reforming Process and Biomass Gasification Process Markets - Independent Analysis of Annual Sales in US$ Million for Years 2014 through 2023 and % CAGR
- TABLE 142: Latin America 16-Year Perspective for Petroleum Refining Hydrogen Generation by Process - Percentage Breakdown of Value Sales for Steam Methane Reforming Process, Electrolysis Process, Partial Oxidation Process, Auto-Thermal Reforming Process and Biomass Gasification Process for the Years 2014, 2025 & 2030
- ARGENTINA
- TABLE 143: Argentina Recent Past, Current & Future Analysis for Petroleum Refining Hydrogen Generation by Delivery mode - Captive Delivery Mode and Merchant Delivery Mode - Independent Analysis of Annual Sales in US$ Million for the Years 2024 through 2030 and % CAGR
- TABLE 144: Argentina Historic Review for Petroleum Refining Hydrogen Generation by Delivery mode - Captive Delivery Mode and Merchant Delivery Mode Markets - Independent Analysis of Annual Sales in US$ Million for Years 2014 through 2023 and % CAGR
- TABLE 145: Argentina 16-Year Perspective for Petroleum Refining Hydrogen Generation by Delivery mode - Percentage Breakdown of Value Sales for Captive Delivery Mode and Merchant Delivery Mode for the Years 2014, 2025 & 2030
- TABLE 146: Argentina Recent Past, Current & Future Analysis for Petroleum Refining Hydrogen Generation by Process - Steam Methane Reforming Process, Electrolysis Process, Partial Oxidation Process, Auto-Thermal Reforming Process and Biomass Gasification Process - Independent Analysis of Annual Sales in US$ Million for the Years 2024 through 2030 and % CAGR
- TABLE 147: Argentina Historic Review for Petroleum Refining Hydrogen Generation by Process - Steam Methane Reforming Process, Electrolysis Process, Partial Oxidation Process, Auto-Thermal Reforming Process and Biomass Gasification Process Markets - Independent Analysis of Annual Sales in US$ Million for Years 2014 through 2023 and % CAGR
- TABLE 148: Argentina 16-Year Perspective for Petroleum Refining Hydrogen Generation by Process - Percentage Breakdown of Value Sales for Steam Methane Reforming Process, Electrolysis Process, Partial Oxidation Process, Auto-Thermal Reforming Process and Biomass Gasification Process for the Years 2014, 2025 & 2030
- BRAZIL
- TABLE 149: Brazil Recent Past, Current & Future Analysis for Petroleum Refining Hydrogen Generation by Delivery mode - Captive Delivery Mode and Merchant Delivery Mode - Independent Analysis of Annual Sales in US$ Million for the Years 2024 through 2030 and % CAGR
- TABLE 150: Brazil Historic Review for Petroleum Refining Hydrogen Generation by Delivery mode - Captive Delivery Mode and Merchant Delivery Mode Markets - Independent Analysis of Annual Sales in US$ Million for Years 2014 through 2023 and % CAGR
- TABLE 151: Brazil 16-Year Perspective for Petroleum Refining Hydrogen Generation by Delivery mode - Percentage Breakdown of Value Sales for Captive Delivery Mode and Merchant Delivery Mode for the Years 2014, 2025 & 2030
- TABLE 152: Brazil Recent Past, Current & Future Analysis for Petroleum Refining Hydrogen Generation by Process - Steam Methane Reforming Process, Electrolysis Process, Partial Oxidation Process, Auto-Thermal Reforming Process and Biomass Gasification Process - Independent Analysis of Annual Sales in US$ Million for the Years 2024 through 2030 and % CAGR
- TABLE 153: Brazil Historic Review for Petroleum Refining Hydrogen Generation by Process - Steam Methane Reforming Process, Electrolysis Process, Partial Oxidation Process, Auto-Thermal Reforming Process and Biomass Gasification Process Markets - Independent Analysis of Annual Sales in US$ Million for Years 2014 through 2023 and % CAGR
- TABLE 154: Brazil 16-Year Perspective for Petroleum Refining Hydrogen Generation by Process - Percentage Breakdown of Value Sales for Steam Methane Reforming Process, Electrolysis Process, Partial Oxidation Process, Auto-Thermal Reforming Process and Biomass Gasification Process for the Years 2014, 2025 & 2030
- MEXICO
- TABLE 155: Mexico Recent Past, Current & Future Analysis for Petroleum Refining Hydrogen Generation by Delivery mode - Captive Delivery Mode and Merchant Delivery Mode - Independent Analysis of Annual Sales in US$ Million for the Years 2024 through 2030 and % CAGR
- TABLE 156: Mexico Historic Review for Petroleum Refining Hydrogen Generation by Delivery mode - Captive Delivery Mode and Merchant Delivery Mode Markets - Independent Analysis of Annual Sales in US$ Million for Years 2014 through 2023 and % CAGR
- TABLE 157: Mexico 16-Year Perspective for Petroleum Refining Hydrogen Generation by Delivery mode - Percentage Breakdown of Value Sales for Captive Delivery Mode and Merchant Delivery Mode for the Years 2014, 2025 & 2030
- TABLE 158: Mexico Recent Past, Current & Future Analysis for Petroleum Refining Hydrogen Generation by Process - Steam Methane Reforming Process, Electrolysis Process, Partial Oxidation Process, Auto-Thermal Reforming Process and Biomass Gasification Process - Independent Analysis of Annual Sales in US$ Million for the Years 2024 through 2030 and % CAGR
- TABLE 159: Mexico Historic Review for Petroleum Refining Hydrogen Generation by Process - Steam Methane Reforming Process, Electrolysis Process, Partial Oxidation Process, Auto-Thermal Reforming Process and Biomass Gasification Process Markets - Independent Analysis of Annual Sales in US$ Million for Years 2014 through 2023 and % CAGR
- TABLE 160: Mexico 16-Year Perspective for Petroleum Refining Hydrogen Generation by Process - Percentage Breakdown of Value Sales for Steam Methane Reforming Process, Electrolysis Process, Partial Oxidation Process, Auto-Thermal Reforming Process and Biomass Gasification Process for the Years 2014, 2025 & 2030
- REST OF LATIN AMERICA
- TABLE 161: Rest of Latin America Recent Past, Current & Future Analysis for Petroleum Refining Hydrogen Generation by Delivery mode - Captive Delivery Mode and Merchant Delivery Mode - Independent Analysis of Annual Sales in US$ Million for the Years 2024 through 2030 and % CAGR
- TABLE 162: Rest of Latin America Historic Review for Petroleum Refining Hydrogen Generation by Delivery mode - Captive Delivery Mode and Merchant Delivery Mode Markets - Independent Analysis of Annual Sales in US$ Million for Years 2014 through 2023 and % CAGR
- TABLE 163: Rest of Latin America 16-Year Perspective for Petroleum Refining Hydrogen Generation by Delivery mode - Percentage Breakdown of Value Sales for Captive Delivery Mode and Merchant Delivery Mode for the Years 2014, 2025 & 2030
- TABLE 164: Rest of Latin America Recent Past, Current & Future Analysis for Petroleum Refining Hydrogen Generation by Process - Steam Methane Reforming Process, Electrolysis Process, Partial Oxidation Process, Auto-Thermal Reforming Process and Biomass Gasification Process - Independent Analysis of Annual Sales in US$ Million for the Years 2024 through 2030 and % CAGR
- TABLE 165: Rest of Latin America Historic Review for Petroleum Refining Hydrogen Generation by Process - Steam Methane Reforming Process, Electrolysis Process, Partial Oxidation Process, Auto-Thermal Reforming Process and Biomass Gasification Process Markets - Independent Analysis of Annual Sales in US$ Million for Years 2014 through 2023 and % CAGR
- TABLE 166: Rest of Latin America 16-Year Perspective for Petroleum Refining Hydrogen Generation by Process - Percentage Breakdown of Value Sales for Steam Methane Reforming Process, Electrolysis Process, Partial Oxidation Process, Auto-Thermal Reforming Process and Biomass Gasification Process for the Years 2014, 2025 & 2030
- MIDDLE EAST
- Petroleum Refining Hydrogen Generation Market Presence - Strong/Active/Niche/Trivial - Key Competitors in Middle East for 2025 (E)
- TABLE 167: Middle East Recent Past, Current & Future Analysis for Petroleum Refining Hydrogen Generation by Geographic Region - Iran, Israel, Saudi Arabia, UAE and Rest of Middle East Markets - Independent Analysis of Annual Sales in US$ Million for Years 2024 through 2030 and % CAGR
- TABLE 168: Middle East Historic Review for Petroleum Refining Hydrogen Generation by Geographic Region - Iran, Israel, Saudi Arabia, UAE and Rest of Middle East Markets - Independent Analysis of Annual Sales in US$ Million for Years 2014 through 2023 and % CAGR
- TABLE 169: Middle East 16-Year Perspective for Petroleum Refining Hydrogen Generation by Geographic Region - Percentage Breakdown of Value Sales for Iran, Israel, Saudi Arabia, UAE and Rest of Middle East Markets for Years 2014, 2025 & 2030
- TABLE 170: Middle East Recent Past, Current & Future Analysis for Petroleum Refining Hydrogen Generation by Delivery mode - Captive Delivery Mode and Merchant Delivery Mode - Independent Analysis of Annual Sales in US$ Million for the Years 2024 through 2030 and % CAGR
- TABLE 171: Middle East Historic Review for Petroleum Refining Hydrogen Generation by Delivery mode - Captive Delivery Mode and Merchant Delivery Mode Markets - Independent Analysis of Annual Sales in US$ Million for Years 2014 through 2023 and % CAGR
- TABLE 172: Middle East 16-Year Perspective for Petroleum Refining Hydrogen Generation by Delivery mode - Percentage Breakdown of Value Sales for Captive Delivery Mode and Merchant Delivery Mode for the Years 2014, 2025 & 2030
- TABLE 173: Middle East Recent Past, Current & Future Analysis for Petroleum Refining Hydrogen Generation by Process - Steam Methane Reforming Process, Electrolysis Process, Partial Oxidation Process, Auto-Thermal Reforming Process and Biomass Gasification Process - Independent Analysis of Annual Sales in US$ Million for the Years 2024 through 2030 and % CAGR
- TABLE 174: Middle East Historic Review for Petroleum Refining Hydrogen Generation by Process - Steam Methane Reforming Process, Electrolysis Process, Partial Oxidation Process, Auto-Thermal Reforming Process and Biomass Gasification Process Markets - Independent Analysis of Annual Sales in US$ Million for Years 2014 through 2023 and % CAGR
- TABLE 175: Middle East 16-Year Perspective for Petroleum Refining Hydrogen Generation by Process - Percentage Breakdown of Value Sales for Steam Methane Reforming Process, Electrolysis Process, Partial Oxidation Process, Auto-Thermal Reforming Process and Biomass Gasification Process for the Years 2014, 2025 & 2030
- IRAN
- TABLE 176: Iran Recent Past, Current & Future Analysis for Petroleum Refining Hydrogen Generation by Delivery mode - Captive Delivery Mode and Merchant Delivery Mode - Independent Analysis of Annual Sales in US$ Million for the Years 2024 through 2030 and % CAGR
- TABLE 177: Iran Historic Review for Petroleum Refining Hydrogen Generation by Delivery mode - Captive Delivery Mode and Merchant Delivery Mode Markets - Independent Analysis of Annual Sales in US$ Million for Years 2014 through 2023 and % CAGR
- TABLE 178: Iran 16-Year Perspective for Petroleum Refining Hydrogen Generation by Delivery mode - Percentage Breakdown of Value Sales for Captive Delivery Mode and Merchant Delivery Mode for the Years 2014, 2025 & 2030
- TABLE 179: Iran Recent Past, Current & Future Analysis for Petroleum Refining Hydrogen Generation by Process - Steam Methane Reforming Process, Electrolysis Process, Partial Oxidation Process, Auto-Thermal Reforming Process and Biomass Gasification Process - Independent Analysis of Annual Sales in US$ Million for the Years 2024 through 2030 and % CAGR
- TABLE 180: Iran Historic Review for Petroleum Refining Hydrogen Generation by Process - Steam Methane Reforming Process, Electrolysis Process, Partial Oxidation Process, Auto-Thermal Reforming Process and Biomass Gasification Process Markets - Independent Analysis of Annual Sales in US$ Million for Years 2014 through 2023 and % CAGR
- TABLE 181: Iran 16-Year Perspective for Petroleum Refining Hydrogen Generation by Process - Percentage Breakdown of Value Sales for Steam Methane Reforming Process, Electrolysis Process, Partial Oxidation Process, Auto-Thermal Reforming Process and Biomass Gasification Process for the Years 2014, 2025 & 2030
- ISRAEL
- TABLE 182: Israel Recent Past, Current & Future Analysis for Petroleum Refining Hydrogen Generation by Delivery mode - Captive Delivery Mode and Merchant Delivery Mode - Independent Analysis of Annual Sales in US$ Million for the Years 2024 through 2030 and % CAGR
- TABLE 183: Israel Historic Review for Petroleum Refining Hydrogen Generation by Delivery mode - Captive Delivery Mode and Merchant Delivery Mode Markets - Independent Analysis of Annual Sales in US$ Million for Years 2014 through 2023 and % CAGR
- TABLE 184: Israel 16-Year Perspective for Petroleum Refining Hydrogen Generation by Delivery mode - Percentage Breakdown of Value Sales for Captive Delivery Mode and Merchant Delivery Mode for the Years 2014, 2025 & 2030
- TABLE 185: Israel Recent Past, Current & Future Analysis for Petroleum Refining Hydrogen Generation by Process - Steam Methane Reforming Process, Electrolysis Process, Partial Oxidation Process, Auto-Thermal Reforming Process and Biomass Gasification Process - Independent Analysis of Annual Sales in US$ Million for the Years 2024 through 2030 and % CAGR
- TABLE 186: Israel Historic Review for Petroleum Refining Hydrogen Generation by Process - Steam Methane Reforming Process, Electrolysis Process, Partial Oxidation Process, Auto-Thermal Reforming Process and Biomass Gasification Process Markets - Independent Analysis of Annual Sales in US$ Million for Years 2014 through 2023 and % CAGR
- TABLE 187: Israel 16-Year Perspective for Petroleum Refining Hydrogen Generation by Process - Percentage Breakdown of Value Sales for Steam Methane Reforming Process, Electrolysis Process, Partial Oxidation Process, Auto-Thermal Reforming Process and Biomass Gasification Process for the Years 2014, 2025 & 2030
- SAUDI ARABIA
- TABLE 188: Saudi Arabia Recent Past, Current & Future Analysis for Petroleum Refining Hydrogen Generation by Delivery mode - Captive Delivery Mode and Merchant Delivery Mode - Independent Analysis of Annual Sales in US$ Million for the Years 2024 through 2030 and % CAGR
- TABLE 189: Saudi Arabia Historic Review for Petroleum Refining Hydrogen Generation by Delivery mode - Captive Delivery Mode and Merchant Delivery Mode Markets - Independent Analysis of Annual Sales in US$ Million for Years 2014 through 2023 and % CAGR
- TABLE 190: Saudi Arabia 16-Year Perspective for Petroleum Refining Hydrogen Generation by Delivery mode - Percentage Breakdown of Value Sales for Captive Delivery Mode and Merchant Delivery Mode for the Years 2014, 2025 & 2030
- TABLE 191: Saudi Arabia Recent Past, Current & Future Analysis for Petroleum Refining Hydrogen Generation by Process - Steam Methane Reforming Process, Electrolysis Process, Partial Oxidation Process, Auto-Thermal Reforming Process and Biomass Gasification Process - Independent Analysis of Annual Sales in US$ Million for the Years 2024 through 2030 and % CAGR
- TABLE 192: Saudi Arabia Historic Review for Petroleum Refining Hydrogen Generation by Process - Steam Methane Reforming Process, Electrolysis Process, Partial Oxidation Process, Auto-Thermal Reforming Process and Biomass Gasification Process Markets - Independent Analysis of Annual Sales in US$ Million for Years 2014 through 2023 and % CAGR
- TABLE 193: Saudi Arabia 16-Year Perspective for Petroleum Refining Hydrogen Generation by Process - Percentage Breakdown of Value Sales for Steam Methane Reforming Process, Electrolysis Process, Partial Oxidation Process, Auto-Thermal Reforming Process and Biomass Gasification Process for the Years 2014, 2025 & 2030
- UNITED ARAB EMIRATES
- TABLE 194: UAE Recent Past, Current & Future Analysis for Petroleum Refining Hydrogen Generation by Delivery mode - Captive Delivery Mode and Merchant Delivery Mode - Independent Analysis of Annual Sales in US$ Million for the Years 2024 through 2030 and % CAGR
- TABLE 195: UAE Historic Review for Petroleum Refining Hydrogen Generation by Delivery mode - Captive Delivery Mode and Merchant Delivery Mode Markets - Independent Analysis of Annual Sales in US$ Million for Years 2014 through 2023 and % CAGR
- TABLE 196: UAE 16-Year Perspective for Petroleum Refining Hydrogen Generation by Delivery mode - Percentage Breakdown of Value Sales for Captive Delivery Mode and Merchant Delivery Mode for the Years 2014, 2025 & 2030
- TABLE 197: UAE Recent Past, Current & Future Analysis for Petroleum Refining Hydrogen Generation by Process - Steam Methane Reforming Process, Electrolysis Process, Partial Oxidation Process, Auto-Thermal Reforming Process and Biomass Gasification Process - Independent Analysis of Annual Sales in US$ Million for the Years 2024 through 2030 and % CAGR
- TABLE 198: UAE Historic Review for Petroleum Refining Hydrogen Generation by Process - Steam Methane Reforming Process, Electrolysis Process, Partial Oxidation Process, Auto-Thermal Reforming Process and Biomass Gasification Process Markets - Independent Analysis of Annual Sales in US$ Million for Years 2014 through 2023 and % CAGR
- TABLE 199: UAE 16-Year Perspective for Petroleum Refining Hydrogen Generation by Process - Percentage Breakdown of Value Sales for Steam Methane Reforming Process, Electrolysis Process, Partial Oxidation Process, Auto-Thermal Reforming Process and Biomass Gasification Process for the Years 2014, 2025 & 2030
- REST OF MIDDLE EAST
- TABLE 200: Rest of Middle East Recent Past, Current & Future Analysis for Petroleum Refining Hydrogen Generation by Delivery mode - Captive Delivery Mode and Merchant Delivery Mode - Independent Analysis of Annual Sales in US$ Million for the Years 2024 through 2030 and % CAGR
- TABLE 201: Rest of Middle East Historic Review for Petroleum Refining Hydrogen Generation by Delivery mode - Captive Delivery Mode and Merchant Delivery Mode Markets - Independent Analysis of Annual Sales in US$ Million for Years 2014 through 2023 and % CAGR
- TABLE 202: Rest of Middle East 16-Year Perspective for Petroleum Refining Hydrogen Generation by Delivery mode - Percentage Breakdown of Value Sales for Captive Delivery Mode and Merchant Delivery Mode for the Years 2014, 2025 & 2030
- TABLE 203: Rest of Middle East Recent Past, Current & Future Analysis for Petroleum Refining Hydrogen Generation by Process - Steam Methane Reforming Process, Electrolysis Process, Partial Oxidation Process, Auto-Thermal Reforming Process and Biomass Gasification Process - Independent Analysis of Annual Sales in US$ Million for the Years 2024 through 2030 and % CAGR
- TABLE 204: Rest of Middle East Historic Review for Petroleum Refining Hydrogen Generation by Process - Steam Methane Reforming Process, Electrolysis Process, Partial Oxidation Process, Auto-Thermal Reforming Process and Biomass Gasification Process Markets - Independent Analysis of Annual Sales in US$ Million for Years 2014 through 2023 and % CAGR
- TABLE 205: Rest of Middle East 16-Year Perspective for Petroleum Refining Hydrogen Generation by Process - Percentage Breakdown of Value Sales for Steam Methane Reforming Process, Electrolysis Process, Partial Oxidation Process, Auto-Thermal Reforming Process and Biomass Gasification Process for the Years 2014, 2025 & 2030
- AFRICA
- Petroleum Refining Hydrogen Generation Market Presence - Strong/Active/Niche/Trivial - Key Competitors in Africa for 2025 (E)
- TABLE 206: Africa Recent Past, Current & Future Analysis for Petroleum Refining Hydrogen Generation by Delivery mode - Captive Delivery Mode and Merchant Delivery Mode - Independent Analysis of Annual Sales in US$ Million for the Years 2024 through 2030 and % CAGR
- TABLE 207: Africa Historic Review for Petroleum Refining Hydrogen Generation by Delivery mode - Captive Delivery Mode and Merchant Delivery Mode Markets - Independent Analysis of Annual Sales in US$ Million for Years 2014 through 2023 and % CAGR
- TABLE 208: Africa 16-Year Perspective for Petroleum Refining Hydrogen Generation by Delivery mode - Percentage Breakdown of Value Sales for Captive Delivery Mode and Merchant Delivery Mode for the Years 2014, 2025 & 2030
- TABLE 209: Africa Recent Past, Current & Future Analysis for Petroleum Refining Hydrogen Generation by Process - Steam Methane Reforming Process, Electrolysis Process, Partial Oxidation Process, Auto-Thermal Reforming Process and Biomass Gasification Process - Independent Analysis of Annual Sales in US$ Million for the Years 2024 through 2030 and % CAGR
- TABLE 210: Africa Historic Review for Petroleum Refining Hydrogen Generation by Process - Steam Methane Reforming Process, Electrolysis Process, Partial Oxidation Process, Auto-Thermal Reforming Process and Biomass Gasification Process Markets - Independent Analysis of Annual Sales in US$ Million for Years 2014 through 2023 and % CAGR
- TABLE 211: Africa 16-Year Perspective for Petroleum Refining Hydrogen Generation by Process - Percentage Breakdown of Value Sales for Steam Methane Reforming Process, Electrolysis Process, Partial Oxidation Process, Auto-Thermal Reforming Process and Biomass Gasification Process for the Years 2014, 2025 & 2030
- IV. COMPETITION
Pricing
Currency Rates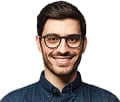