
Panelized Modular Building Systems
Description
Global Panelized Modular Building Systems Market to Reach US$198.3 Billion by 2030
The global market for Panelized Modular Building Systems estimated at US$135.3 Billion in the year 2024, is expected to reach US$198.3 Billion by 2030, growing at a CAGR of 6.6% over the analysis period 2024-2030. Wood-based Building System, one of the segments analyzed in the report, is expected to record a 7.8% CAGR and reach US$94.3 Billion by the end of the analysis period. Growth in the Metal Wood-based Building System segment is estimated at 5.1% CAGR over the analysis period.
The U.S. Market is Estimated at US$35.6 Billion While China is Forecast to Grow at 6.4% CAGR
The Panelized Modular Building Systems market in the U.S. is estimated at US$35.6 Billion in the year 2024. China, the world`s second largest economy, is forecast to reach a projected market size of US$31.8 Billion by the year 2030 trailing a CAGR of 6.4% over the analysis period 2024-2030. Among the other noteworthy geographic markets are Japan and Canada, each forecast to grow at a CAGR of 6.3% and 5.4% respectively over the analysis period. Within Europe, Germany is forecast to grow at approximately 5.1% CAGR.
Global Panelized Modular Building Systems Market - Key Trends & Drivers Summarized
Why Are Panelized Modular Systems Gaining Preference in Modern Construction?
Panelized modular building systems are increasingly used to accelerate construction timelines, reduce site labor needs, and improve project quality. These systems involve prefabricated wall, floor, or roof panels manufactured off-site and then assembled on location, offering a more controlled and efficient alternative to traditional construction methods. The approach is especially suited to residential, commercial, and institutional projects where speed, cost, and material precision are critical.
Adoption is rising due to labor shortages in construction, rising material waste concerns, and demand for faster project delivery. Panelized systems offer structural consistency, minimal on-site disruption, and reduced environmental impact by enabling better resource planning and factory-level quality control. These systems also support customization, allowing architectural flexibility while maintaining efficiency in production and assembly.
How Are Material Technologies and Design Approaches Evolving in This Segment?
Panelized systems are evolving with advances in structural insulated panels (SIPs), light-gauge steel framing, and cross-laminated timber (CLT). SIPs provide excellent thermal insulation and structural strength, making them ideal for energy-efficient buildings. CLT and other engineered wood panels are supporting the growth of sustainable mid-rise modular buildings, particularly in regions prioritizing carbon reduction.
Digital tools such as BIM (Building Information Modeling) and automated CNC machining are increasingly integrated into the design-to-fabrication workflow. These technologies enable precise panel production, clash detection, and seamless coordination among stakeholders. Pre-installed electrical conduits, plumbing channels, and window frames are also being added at the factory level to reduce site work. Flat-pack delivery and modular transport logistics are improving, making it easier to ship large volumes of panels to remote or constrained sites.
Where Is Adoption Expanding and Which Sectors Are Driving Market Growth?
Panelized modular construction is gaining traction in North America, Europe, and parts of Asia-Pacific. In the United States and Canada, panelized systems are used in single-family and multifamily housing, educational buildings, and light commercial structures. Europe, driven by energy efficiency standards and prefabrication policies, is adopting panel systems across housing and public infrastructure. In Asia, population density and rapid urbanization are pushing governments and private developers to adopt modular technologies to meet housing demand faster.
Affordable housing programs, senior living communities, and student housing are key segments driving demand due to the need for rapid, repeatable, and scalable construction methods. Disaster recovery and temporary shelter projects also benefit from panelized modular solutions, as they can be deployed and assembled quickly with minimal skilled labor. Private developers, government agencies, and construction firms are forming partnerships with modular manufacturers to meet aggressive project timelines and regulatory mandates.
Growth in the Panelized Modular Building Systems market is driven by several factors…
Growth in the panelized modular building systems market is driven by factors such as increasing demand for rapid construction methods, rising labor and material cost pressures, and growing emphasis on energy-efficient and sustainable building solutions. Advancements in prefabrication technology, including high-precision manufacturing and digital design integration, are improving scalability and reducing construction waste.
Government incentives for green buildings, coupled with rising interest in off-site construction for affordable and workforce housing, are expanding the market base. Logistics improvements and design modularity are enabling broader application across rural and urban projects. Expansion of mass timber and engineered panel technologies, combined with evolving building codes that support modular assembly, continues to reinforce global demand for panelized systems in both residential and non-residential sectors.
SCOPE OF STUDY:The report analyzes the Panelized Modular Building Systems market in terms of units by the following Segments, and Geographic Regions/Countries:
Segments:
Material (Wood-based Building System, Metal Wood-based Building System, Concrete Wood-based Building System, Composite Wood-based Building System); End-Use (Residential End-Use, Commercial End-Use, Industrial End-Use)
Geographic Regions/Countries:
World; United States; Canada; Japan; China; Europe (France; Germany; Italy; United Kingdom; and Rest of Europe); Asia-Pacific; Rest of World.
Select Competitors (Total 32 Featured) -
- Al Dabbagh Group
- Algeco Global
- ATCO Ltd
- Bechtel Corp.
- Bison Precast
- BOUYGUES
- ClarkWestern Dietrich Building Systems
- Etex Building Performance
- FullStack Modular
- Guerdon Modular Buildings (GUERDON LLC)
- Hunter Douglas Group
- Kingspan Timber Solutions (Kingspan Group)
- Laing O`Rourke
- Metek Plc
- Modulaire Group
- Palomar Modular Buildings
- Portakabin Ltd (Shepherd Building Group)
- Robertson Group Ltd
- Skanska AB
- Vantem
- Wausau Homes
We`re transforming market and competitive intelligence with validated expert content and AI tools.
Instead of following the general norm of querying LLMs and Industry-specific SLMs, we built repositories of content curated from domain experts worldwide including video transcripts, blogs, search engines research, and massive amounts of enterprise, product/service, and market data.
TARIFF IMPACT FACTOR
Our new release incorporates impact of tariffs on geographical markets as we predict a shift in competitiveness of companies based on HQ country, manufacturing base, exports and imports (finished goods and OEM). This intricate and multifaceted market reality will impact competitors by increasing the Cost of Goods Sold (COGS), reducing profitability, reconfiguring supply chains, amongst other micro and macro market dynamics.
Please note: Reports are sold as single-site single-user licenses. Electronic versions require 24-48 hours as each copy is customized to the client with digital controls and custom watermarks. The Publisher uses digital controls protecting against copying and printing is restricted to one full copy to be used at the same location.
The latest version of Adobe Acrobat Reader is required to view the report. Upon ordering an electronic version, the Publisher will provide a link to download the purchased report.
Prior to fulfillment of an order, the client will be required to sign a document detailing the purchase terms for a publication from this publisher.
Table of Contents
- I. METHODOLOGY
- II. EXECUTIVE SUMMARY
- 1. MARKET OVERVIEW
- Influencer Market Insights
- World Market Trajectories
- Tariff Impact on Global Supply Chain Patterns
- Panelized Modular Building Systems – Global Key Competitors Percentage Market Share in 2025 (E)
- Competitive Market Presence - Strong/Active/Niche/Trivial for Players Worldwide in 2025 (E)
- 2. FOCUS ON SELECT PLAYERS
- 3. MARKET TRENDS & DRIVERS
- Rising Demand for Speed and Cost Efficiency in Construction Spurs Adoption of Panelized Modular Building Systems
- Shortage of Skilled Labor in Traditional Construction Strengthens Business Case for Factory-Built Panelized Components
- Growth in Urban Housing and Infrastructure Development Throws the Spotlight on Scalable, Prefabricated Systems
- Increasing Focus on Sustainability and Waste Reduction Drives Interest in Offsite-Constructed, Energy-Efficient Panels
- Advancements in Lightweight Composite Materials Enhance Structural Performance and Transportability
- Surge in Affordable Housing Projects and Disaster Relief Shelters Fuels Demand for Quick-Assembly Modular Panels
- Government Incentives for Green Building Certifications Support Use of Insulated and Pre-Finished Panelized Systems
- Integration of Digital Design Tools and BIM Enables High-Precision Manufacturing and On-Site Installation
- Rising Adoption in Schools, Hospitals, and Retail Expansions Creates Diverse Applications for Modular Panel Systems
- Improved Logistics and Crane-Free Installation Techniques Expand Market for Remote and Compact Building Sites
- Customization Capabilities in Wall, Floor, and Roof Panels Support Design Flexibility and Aesthetic Appeal
- 4. GLOBAL MARKET PERSPECTIVE
- TABLE 1: World Panelized Modular Building Systems Market Analysis of Annual Sales in US$ Million for Years 2014 through 2030
- TABLE 2: World Recent Past, Current & Future Analysis for Panelized Modular Building Systems by Geographic Region - USA, Canada, Japan, China, Europe, Asia-Pacific and Rest of World Markets - Independent Analysis of Annual Sales in US$ Million for Years 2024 through 2030 and % CAGR
- TABLE 3: World Historic Review for Panelized Modular Building Systems by Geographic Region - USA, Canada, Japan, China, Europe, Asia-Pacific and Rest of World Markets - Independent Analysis of Annual Sales in US$ Million for Years 2014 through 2023 and % CAGR
- TABLE 4: World 16-Year Perspective for Panelized Modular Building Systems by Geographic Region - Percentage Breakdown of Value Sales for USA, Canada, Japan, China, Europe, Asia-Pacific and Rest of World Markets for Years 2014, 2025 & 2030
- TABLE 5: World Recent Past, Current & Future Analysis for Wood-based Building System by Geographic Region - USA, Canada, Japan, China, Europe, Asia-Pacific and Rest of World Markets - Independent Analysis of Annual Sales in US$ Million for Years 2024 through 2030 and % CAGR
- TABLE 6: World Historic Review for Wood-based Building System by Geographic Region - USA, Canada, Japan, China, Europe, Asia-Pacific and Rest of World Markets - Independent Analysis of Annual Sales in US$ Million for Years 2014 through 2023 and % CAGR
- TABLE 7: World 16-Year Perspective for Wood-based Building System by Geographic Region - Percentage Breakdown of Value Sales for USA, Canada, Japan, China, Europe, Asia-Pacific and Rest of World for Years 2014, 2025 & 2030
- TABLE 8: World Recent Past, Current & Future Analysis for Metal Wood-based Building System by Geographic Region - USA, Canada, Japan, China, Europe, Asia-Pacific and Rest of World Markets - Independent Analysis of Annual Sales in US$ Million for Years 2024 through 2030 and % CAGR
- TABLE 9: World Historic Review for Metal Wood-based Building System by Geographic Region - USA, Canada, Japan, China, Europe, Asia-Pacific and Rest of World Markets - Independent Analysis of Annual Sales in US$ Million for Years 2014 through 2023 and % CAGR
- TABLE 10: World 16-Year Perspective for Metal Wood-based Building System by Geographic Region - Percentage Breakdown of Value Sales for USA, Canada, Japan, China, Europe, Asia-Pacific and Rest of World for Years 2014, 2025 & 2030
- TABLE 11: World Recent Past, Current & Future Analysis for Concrete Wood-based Building System by Geographic Region - USA, Canada, Japan, China, Europe, Asia-Pacific and Rest of World Markets - Independent Analysis of Annual Sales in US$ Million for Years 2024 through 2030 and % CAGR
- TABLE 12: World Historic Review for Concrete Wood-based Building System by Geographic Region - USA, Canada, Japan, China, Europe, Asia-Pacific and Rest of World Markets - Independent Analysis of Annual Sales in US$ Million for Years 2014 through 2023 and % CAGR
- TABLE 13: World 16-Year Perspective for Concrete Wood-based Building System by Geographic Region - Percentage Breakdown of Value Sales for USA, Canada, Japan, China, Europe, Asia-Pacific and Rest of World for Years 2014, 2025 & 2030
- TABLE 14: World Recent Past, Current & Future Analysis for Composite Wood-based Building System by Geographic Region - USA, Canada, Japan, China, Europe, Asia-Pacific and Rest of World Markets - Independent Analysis of Annual Sales in US$ Million for Years 2024 through 2030 and % CAGR
- TABLE 15: World Historic Review for Composite Wood-based Building System by Geographic Region - USA, Canada, Japan, China, Europe, Asia-Pacific and Rest of World Markets - Independent Analysis of Annual Sales in US$ Million for Years 2014 through 2023 and % CAGR
- TABLE 16: World 16-Year Perspective for Composite Wood-based Building System by Geographic Region - Percentage Breakdown of Value Sales for USA, Canada, Japan, China, Europe, Asia-Pacific and Rest of World for Years 2014, 2025 & 2030
- TABLE 17: World Recent Past, Current & Future Analysis for Residential End-Use by Geographic Region - USA, Canada, Japan, China, Europe, Asia-Pacific and Rest of World Markets - Independent Analysis of Annual Sales in US$ Million for Years 2024 through 2030 and % CAGR
- TABLE 18: World Historic Review for Residential End-Use by Geographic Region - USA, Canada, Japan, China, Europe, Asia-Pacific and Rest of World Markets - Independent Analysis of Annual Sales in US$ Million for Years 2014 through 2023 and % CAGR
- TABLE 19: World 16-Year Perspective for Residential End-Use by Geographic Region - Percentage Breakdown of Value Sales for USA, Canada, Japan, China, Europe, Asia-Pacific and Rest of World for Years 2014, 2025 & 2030
- TABLE 20: World Recent Past, Current & Future Analysis for Commercial End-Use by Geographic Region - USA, Canada, Japan, China, Europe, Asia-Pacific and Rest of World Markets - Independent Analysis of Annual Sales in US$ Million for Years 2024 through 2030 and % CAGR
- TABLE 21: World Historic Review for Commercial End-Use by Geographic Region - USA, Canada, Japan, China, Europe, Asia-Pacific and Rest of World Markets - Independent Analysis of Annual Sales in US$ Million for Years 2014 through 2023 and % CAGR
- TABLE 22: World 16-Year Perspective for Commercial End-Use by Geographic Region - Percentage Breakdown of Value Sales for USA, Canada, Japan, China, Europe, Asia-Pacific and Rest of World for Years 2014, 2025 & 2030
- TABLE 23: World Recent Past, Current & Future Analysis for Industrial End-Use by Geographic Region - USA, Canada, Japan, China, Europe, Asia-Pacific and Rest of World Markets - Independent Analysis of Annual Sales in US$ Million for Years 2024 through 2030 and % CAGR
- TABLE 24: World Historic Review for Industrial End-Use by Geographic Region - USA, Canada, Japan, China, Europe, Asia-Pacific and Rest of World Markets - Independent Analysis of Annual Sales in US$ Million for Years 2014 through 2023 and % CAGR
- TABLE 25: World 16-Year Perspective for Industrial End-Use by Geographic Region - Percentage Breakdown of Value Sales for USA, Canada, Japan, China, Europe, Asia-Pacific and Rest of World for Years 2014, 2025 & 2030
- III. MARKET ANALYSIS
- UNITED STATES
- Panelized Modular Building Systems Market Presence - Strong/Active/Niche/Trivial - Key Competitors in the United States for 2025 (E)
- TABLE 26: USA Recent Past, Current & Future Analysis for Panelized Modular Building Systems by Material - Wood-based Building System, Metal Wood-based Building System, Concrete Wood-based Building System and Composite Wood-based Building System - Independent Analysis of Annual Sales in US$ Million for the Years 2024 through 2030 and % CAGR
- TABLE 27: USA Historic Review for Panelized Modular Building Systems by Material - Wood-based Building System, Metal Wood-based Building System, Concrete Wood-based Building System and Composite Wood-based Building System Markets - Independent Analysis of Annual Sales in US$ Million for Years 2014 through 2023 and % CAGR
- TABLE 28: USA 16-Year Perspective for Panelized Modular Building Systems by Material - Percentage Breakdown of Value Sales for Wood-based Building System, Metal Wood-based Building System, Concrete Wood-based Building System and Composite Wood-based Building System for the Years 2014, 2025 & 2030
- TABLE 29: USA Recent Past, Current & Future Analysis for Panelized Modular Building Systems by End-Use - Residential End-Use, Commercial End-Use and Industrial End-Use - Independent Analysis of Annual Sales in US$ Million for the Years 2024 through 2030 and % CAGR
- TABLE 30: USA Historic Review for Panelized Modular Building Systems by End-Use - Residential End-Use, Commercial End-Use and Industrial End-Use Markets - Independent Analysis of Annual Sales in US$ Million for Years 2014 through 2023 and % CAGR
- TABLE 31: USA 16-Year Perspective for Panelized Modular Building Systems by End-Use - Percentage Breakdown of Value Sales for Residential End-Use, Commercial End-Use and Industrial End-Use for the Years 2014, 2025 & 2030
- CANADA
- TABLE 32: Canada Recent Past, Current & Future Analysis for Panelized Modular Building Systems by Material - Wood-based Building System, Metal Wood-based Building System, Concrete Wood-based Building System and Composite Wood-based Building System - Independent Analysis of Annual Sales in US$ Million for the Years 2024 through 2030 and % CAGR
- TABLE 33: Canada Historic Review for Panelized Modular Building Systems by Material - Wood-based Building System, Metal Wood-based Building System, Concrete Wood-based Building System and Composite Wood-based Building System Markets - Independent Analysis of Annual Sales in US$ Million for Years 2014 through 2023 and % CAGR
- TABLE 34: Canada 16-Year Perspective for Panelized Modular Building Systems by Material - Percentage Breakdown of Value Sales for Wood-based Building System, Metal Wood-based Building System, Concrete Wood-based Building System and Composite Wood-based Building System for the Years 2014, 2025 & 2030
- TABLE 35: Canada Recent Past, Current & Future Analysis for Panelized Modular Building Systems by End-Use - Residential End-Use, Commercial End-Use and Industrial End-Use - Independent Analysis of Annual Sales in US$ Million for the Years 2024 through 2030 and % CAGR
- TABLE 36: Canada Historic Review for Panelized Modular Building Systems by End-Use - Residential End-Use, Commercial End-Use and Industrial End-Use Markets - Independent Analysis of Annual Sales in US$ Million for Years 2014 through 2023 and % CAGR
- TABLE 37: Canada 16-Year Perspective for Panelized Modular Building Systems by End-Use - Percentage Breakdown of Value Sales for Residential End-Use, Commercial End-Use and Industrial End-Use for the Years 2014, 2025 & 2030
- JAPAN
- Panelized Modular Building Systems Market Presence - Strong/Active/Niche/Trivial - Key Competitors in Japan for 2025 (E)
- TABLE 38: Japan Recent Past, Current & Future Analysis for Panelized Modular Building Systems by Material - Wood-based Building System, Metal Wood-based Building System, Concrete Wood-based Building System and Composite Wood-based Building System - Independent Analysis of Annual Sales in US$ Million for the Years 2024 through 2030 and % CAGR
- TABLE 39: Japan Historic Review for Panelized Modular Building Systems by Material - Wood-based Building System, Metal Wood-based Building System, Concrete Wood-based Building System and Composite Wood-based Building System Markets - Independent Analysis of Annual Sales in US$ Million for Years 2014 through 2023 and % CAGR
- TABLE 40: Japan 16-Year Perspective for Panelized Modular Building Systems by Material - Percentage Breakdown of Value Sales for Wood-based Building System, Metal Wood-based Building System, Concrete Wood-based Building System and Composite Wood-based Building System for the Years 2014, 2025 & 2030
- TABLE 41: Japan Recent Past, Current & Future Analysis for Panelized Modular Building Systems by End-Use - Residential End-Use, Commercial End-Use and Industrial End-Use - Independent Analysis of Annual Sales in US$ Million for the Years 2024 through 2030 and % CAGR
- TABLE 42: Japan Historic Review for Panelized Modular Building Systems by End-Use - Residential End-Use, Commercial End-Use and Industrial End-Use Markets - Independent Analysis of Annual Sales in US$ Million for Years 2014 through 2023 and % CAGR
- TABLE 43: Japan 16-Year Perspective for Panelized Modular Building Systems by End-Use - Percentage Breakdown of Value Sales for Residential End-Use, Commercial End-Use and Industrial End-Use for the Years 2014, 2025 & 2030
- CHINA
- Panelized Modular Building Systems Market Presence - Strong/Active/Niche/Trivial - Key Competitors in China for 2025 (E)
- TABLE 44: China Recent Past, Current & Future Analysis for Panelized Modular Building Systems by Material - Wood-based Building System, Metal Wood-based Building System, Concrete Wood-based Building System and Composite Wood-based Building System - Independent Analysis of Annual Sales in US$ Million for the Years 2024 through 2030 and % CAGR
- TABLE 45: China Historic Review for Panelized Modular Building Systems by Material - Wood-based Building System, Metal Wood-based Building System, Concrete Wood-based Building System and Composite Wood-based Building System Markets - Independent Analysis of Annual Sales in US$ Million for Years 2014 through 2023 and % CAGR
- TABLE 46: China 16-Year Perspective for Panelized Modular Building Systems by Material - Percentage Breakdown of Value Sales for Wood-based Building System, Metal Wood-based Building System, Concrete Wood-based Building System and Composite Wood-based Building System for the Years 2014, 2025 & 2030
- TABLE 47: China Recent Past, Current & Future Analysis for Panelized Modular Building Systems by End-Use - Residential End-Use, Commercial End-Use and Industrial End-Use - Independent Analysis of Annual Sales in US$ Million for the Years 2024 through 2030 and % CAGR
- TABLE 48: China Historic Review for Panelized Modular Building Systems by End-Use - Residential End-Use, Commercial End-Use and Industrial End-Use Markets - Independent Analysis of Annual Sales in US$ Million for Years 2014 through 2023 and % CAGR
- TABLE 49: China 16-Year Perspective for Panelized Modular Building Systems by End-Use - Percentage Breakdown of Value Sales for Residential End-Use, Commercial End-Use and Industrial End-Use for the Years 2014, 2025 & 2030
- EUROPE
- Panelized Modular Building Systems Market Presence - Strong/Active/Niche/Trivial - Key Competitors in Europe for 2025 (E)
- TABLE 50: Europe Recent Past, Current & Future Analysis for Panelized Modular Building Systems by Geographic Region - France, Germany, Italy, UK and Rest of Europe Markets - Independent Analysis of Annual Sales in US$ Million for Years 2024 through 2030 and % CAGR
- TABLE 51: Europe Historic Review for Panelized Modular Building Systems by Geographic Region - France, Germany, Italy, UK and Rest of Europe Markets - Independent Analysis of Annual Sales in US$ Million for Years 2014 through 2023 and % CAGR
- TABLE 52: Europe 16-Year Perspective for Panelized Modular Building Systems by Geographic Region - Percentage Breakdown of Value Sales for France, Germany, Italy, UK and Rest of Europe Markets for Years 2014, 2025 & 2030
- TABLE 53: Europe Recent Past, Current & Future Analysis for Panelized Modular Building Systems by Material - Wood-based Building System, Metal Wood-based Building System, Concrete Wood-based Building System and Composite Wood-based Building System - Independent Analysis of Annual Sales in US$ Million for the Years 2024 through 2030 and % CAGR
- TABLE 54: Europe Historic Review for Panelized Modular Building Systems by Material - Wood-based Building System, Metal Wood-based Building System, Concrete Wood-based Building System and Composite Wood-based Building System Markets - Independent Analysis of Annual Sales in US$ Million for Years 2014 through 2023 and % CAGR
- TABLE 55: Europe 16-Year Perspective for Panelized Modular Building Systems by Material - Percentage Breakdown of Value Sales for Wood-based Building System, Metal Wood-based Building System, Concrete Wood-based Building System and Composite Wood-based Building System for the Years 2014, 2025 & 2030
- TABLE 56: Europe Recent Past, Current & Future Analysis for Panelized Modular Building Systems by End-Use - Residential End-Use, Commercial End-Use and Industrial End-Use - Independent Analysis of Annual Sales in US$ Million for the Years 2024 through 2030 and % CAGR
- TABLE 57: Europe Historic Review for Panelized Modular Building Systems by End-Use - Residential End-Use, Commercial End-Use and Industrial End-Use Markets - Independent Analysis of Annual Sales in US$ Million for Years 2014 through 2023 and % CAGR
- TABLE 58: Europe 16-Year Perspective for Panelized Modular Building Systems by End-Use - Percentage Breakdown of Value Sales for Residential End-Use, Commercial End-Use and Industrial End-Use for the Years 2014, 2025 & 2030
- FRANCE
- Panelized Modular Building Systems Market Presence - Strong/Active/Niche/Trivial - Key Competitors in France for 2025 (E)
- TABLE 59: France Recent Past, Current & Future Analysis for Panelized Modular Building Systems by Material - Wood-based Building System, Metal Wood-based Building System, Concrete Wood-based Building System and Composite Wood-based Building System - Independent Analysis of Annual Sales in US$ Million for the Years 2024 through 2030 and % CAGR
- TABLE 60: France Historic Review for Panelized Modular Building Systems by Material - Wood-based Building System, Metal Wood-based Building System, Concrete Wood-based Building System and Composite Wood-based Building System Markets - Independent Analysis of Annual Sales in US$ Million for Years 2014 through 2023 and % CAGR
- TABLE 61: France 16-Year Perspective for Panelized Modular Building Systems by Material - Percentage Breakdown of Value Sales for Wood-based Building System, Metal Wood-based Building System, Concrete Wood-based Building System and Composite Wood-based Building System for the Years 2014, 2025 & 2030
- TABLE 62: France Recent Past, Current & Future Analysis for Panelized Modular Building Systems by End-Use - Residential End-Use, Commercial End-Use and Industrial End-Use - Independent Analysis of Annual Sales in US$ Million for the Years 2024 through 2030 and % CAGR
- TABLE 63: France Historic Review for Panelized Modular Building Systems by End-Use - Residential End-Use, Commercial End-Use and Industrial End-Use Markets - Independent Analysis of Annual Sales in US$ Million for Years 2014 through 2023 and % CAGR
- TABLE 64: France 16-Year Perspective for Panelized Modular Building Systems by End-Use - Percentage Breakdown of Value Sales for Residential End-Use, Commercial End-Use and Industrial End-Use for the Years 2014, 2025 & 2030
- GERMANY
- Panelized Modular Building Systems Market Presence - Strong/Active/Niche/Trivial - Key Competitors in Germany for 2025 (E)
- TABLE 65: Germany Recent Past, Current & Future Analysis for Panelized Modular Building Systems by Material - Wood-based Building System, Metal Wood-based Building System, Concrete Wood-based Building System and Composite Wood-based Building System - Independent Analysis of Annual Sales in US$ Million for the Years 2024 through 2030 and % CAGR
- TABLE 66: Germany Historic Review for Panelized Modular Building Systems by Material - Wood-based Building System, Metal Wood-based Building System, Concrete Wood-based Building System and Composite Wood-based Building System Markets - Independent Analysis of Annual Sales in US$ Million for Years 2014 through 2023 and % CAGR
- TABLE 67: Germany 16-Year Perspective for Panelized Modular Building Systems by Material - Percentage Breakdown of Value Sales for Wood-based Building System, Metal Wood-based Building System, Concrete Wood-based Building System and Composite Wood-based Building System for the Years 2014, 2025 & 2030
- TABLE 68: Germany Recent Past, Current & Future Analysis for Panelized Modular Building Systems by End-Use - Residential End-Use, Commercial End-Use and Industrial End-Use - Independent Analysis of Annual Sales in US$ Million for the Years 2024 through 2030 and % CAGR
- TABLE 69: Germany Historic Review for Panelized Modular Building Systems by End-Use - Residential End-Use, Commercial End-Use and Industrial End-Use Markets - Independent Analysis of Annual Sales in US$ Million for Years 2014 through 2023 and % CAGR
- TABLE 70: Germany 16-Year Perspective for Panelized Modular Building Systems by End-Use - Percentage Breakdown of Value Sales for Residential End-Use, Commercial End-Use and Industrial End-Use for the Years 2014, 2025 & 2030
- ITALY
- TABLE 71: Italy Recent Past, Current & Future Analysis for Panelized Modular Building Systems by Material - Wood-based Building System, Metal Wood-based Building System, Concrete Wood-based Building System and Composite Wood-based Building System - Independent Analysis of Annual Sales in US$ Million for the Years 2024 through 2030 and % CAGR
- TABLE 72: Italy Historic Review for Panelized Modular Building Systems by Material - Wood-based Building System, Metal Wood-based Building System, Concrete Wood-based Building System and Composite Wood-based Building System Markets - Independent Analysis of Annual Sales in US$ Million for Years 2014 through 2023 and % CAGR
- TABLE 73: Italy 16-Year Perspective for Panelized Modular Building Systems by Material - Percentage Breakdown of Value Sales for Wood-based Building System, Metal Wood-based Building System, Concrete Wood-based Building System and Composite Wood-based Building System for the Years 2014, 2025 & 2030
- TABLE 74: Italy Recent Past, Current & Future Analysis for Panelized Modular Building Systems by End-Use - Residential End-Use, Commercial End-Use and Industrial End-Use - Independent Analysis of Annual Sales in US$ Million for the Years 2024 through 2030 and % CAGR
- TABLE 75: Italy Historic Review for Panelized Modular Building Systems by End-Use - Residential End-Use, Commercial End-Use and Industrial End-Use Markets - Independent Analysis of Annual Sales in US$ Million for Years 2014 through 2023 and % CAGR
- TABLE 76: Italy 16-Year Perspective for Panelized Modular Building Systems by End-Use - Percentage Breakdown of Value Sales for Residential End-Use, Commercial End-Use and Industrial End-Use for the Years 2014, 2025 & 2030
- UNITED KINGDOM
- Panelized Modular Building Systems Market Presence - Strong/Active/Niche/Trivial - Key Competitors in the United Kingdom for 2025 (E)
- TABLE 77: UK Recent Past, Current & Future Analysis for Panelized Modular Building Systems by Material - Wood-based Building System, Metal Wood-based Building System, Concrete Wood-based Building System and Composite Wood-based Building System - Independent Analysis of Annual Sales in US$ Million for the Years 2024 through 2030 and % CAGR
- TABLE 78: UK Historic Review for Panelized Modular Building Systems by Material - Wood-based Building System, Metal Wood-based Building System, Concrete Wood-based Building System and Composite Wood-based Building System Markets - Independent Analysis of Annual Sales in US$ Million for Years 2014 through 2023 and % CAGR
- TABLE 79: UK 16-Year Perspective for Panelized Modular Building Systems by Material - Percentage Breakdown of Value Sales for Wood-based Building System, Metal Wood-based Building System, Concrete Wood-based Building System and Composite Wood-based Building System for the Years 2014, 2025 & 2030
- TABLE 80: UK Recent Past, Current & Future Analysis for Panelized Modular Building Systems by End-Use - Residential End-Use, Commercial End-Use and Industrial End-Use - Independent Analysis of Annual Sales in US$ Million for the Years 2024 through 2030 and % CAGR
- TABLE 81: UK Historic Review for Panelized Modular Building Systems by End-Use - Residential End-Use, Commercial End-Use and Industrial End-Use Markets - Independent Analysis of Annual Sales in US$ Million for Years 2014 through 2023 and % CAGR
- TABLE 82: UK 16-Year Perspective for Panelized Modular Building Systems by End-Use - Percentage Breakdown of Value Sales for Residential End-Use, Commercial End-Use and Industrial End-Use for the Years 2014, 2025 & 2030
- REST OF EUROPE
- TABLE 83: Rest of Europe Recent Past, Current & Future Analysis for Panelized Modular Building Systems by Material - Wood-based Building System, Metal Wood-based Building System, Concrete Wood-based Building System and Composite Wood-based Building System - Independent Analysis of Annual Sales in US$ Million for the Years 2024 through 2030 and % CAGR
- TABLE 84: Rest of Europe Historic Review for Panelized Modular Building Systems by Material - Wood-based Building System, Metal Wood-based Building System, Concrete Wood-based Building System and Composite Wood-based Building System Markets - Independent Analysis of Annual Sales in US$ Million for Years 2014 through 2023 and % CAGR
- TABLE 85: Rest of Europe 16-Year Perspective for Panelized Modular Building Systems by Material - Percentage Breakdown of Value Sales for Wood-based Building System, Metal Wood-based Building System, Concrete Wood-based Building System and Composite Wood-based Building System for the Years 2014, 2025 & 2030
- TABLE 86: Rest of Europe Recent Past, Current & Future Analysis for Panelized Modular Building Systems by End-Use - Residential End-Use, Commercial End-Use and Industrial End-Use - Independent Analysis of Annual Sales in US$ Million for the Years 2024 through 2030 and % CAGR
- TABLE 87: Rest of Europe Historic Review for Panelized Modular Building Systems by End-Use - Residential End-Use, Commercial End-Use and Industrial End-Use Markets - Independent Analysis of Annual Sales in US$ Million for Years 2014 through 2023 and % CAGR
- TABLE 88: Rest of Europe 16-Year Perspective for Panelized Modular Building Systems by End-Use - Percentage Breakdown of Value Sales for Residential End-Use, Commercial End-Use and Industrial End-Use for the Years 2014, 2025 & 2030
- ASIA-PACIFIC
- Panelized Modular Building Systems Market Presence - Strong/Active/Niche/Trivial - Key Competitors in Asia-Pacific for 2025 (E)
- TABLE 89: Asia-Pacific Recent Past, Current & Future Analysis for Panelized Modular Building Systems by Material - Wood-based Building System, Metal Wood-based Building System, Concrete Wood-based Building System and Composite Wood-based Building System - Independent Analysis of Annual Sales in US$ Million for the Years 2024 through 2030 and % CAGR
- TABLE 90: Asia-Pacific Historic Review for Panelized Modular Building Systems by Material - Wood-based Building System, Metal Wood-based Building System, Concrete Wood-based Building System and Composite Wood-based Building System Markets - Independent Analysis of Annual Sales in US$ Million for Years 2014 through 2023 and % CAGR
- TABLE 91: Asia-Pacific 16-Year Perspective for Panelized Modular Building Systems by Material - Percentage Breakdown of Value Sales for Wood-based Building System, Metal Wood-based Building System, Concrete Wood-based Building System and Composite Wood-based Building System for the Years 2014, 2025 & 2030
- TABLE 92: Asia-Pacific Recent Past, Current & Future Analysis for Panelized Modular Building Systems by End-Use - Residential End-Use, Commercial End-Use and Industrial End-Use - Independent Analysis of Annual Sales in US$ Million for the Years 2024 through 2030 and % CAGR
- TABLE 93: Asia-Pacific Historic Review for Panelized Modular Building Systems by End-Use - Residential End-Use, Commercial End-Use and Industrial End-Use Markets - Independent Analysis of Annual Sales in US$ Million for Years 2014 through 2023 and % CAGR
- TABLE 94: Asia-Pacific 16-Year Perspective for Panelized Modular Building Systems by End-Use - Percentage Breakdown of Value Sales for Residential End-Use, Commercial End-Use and Industrial End-Use for the Years 2014, 2025 & 2030
- REST OF WORLD
- TABLE 95: Rest of World Recent Past, Current & Future Analysis for Panelized Modular Building Systems by Material - Wood-based Building System, Metal Wood-based Building System, Concrete Wood-based Building System and Composite Wood-based Building System - Independent Analysis of Annual Sales in US$ Million for the Years 2024 through 2030 and % CAGR
- TABLE 96: Rest of World Historic Review for Panelized Modular Building Systems by Material - Wood-based Building System, Metal Wood-based Building System, Concrete Wood-based Building System and Composite Wood-based Building System Markets - Independent Analysis of Annual Sales in US$ Million for Years 2014 through 2023 and % CAGR
- TABLE 97: Rest of World 16-Year Perspective for Panelized Modular Building Systems by Material - Percentage Breakdown of Value Sales for Wood-based Building System, Metal Wood-based Building System, Concrete Wood-based Building System and Composite Wood-based Building System for the Years 2014, 2025 & 2030
- TABLE 98: Rest of World Recent Past, Current & Future Analysis for Panelized Modular Building Systems by End-Use - Residential End-Use, Commercial End-Use and Industrial End-Use - Independent Analysis of Annual Sales in US$ Million for the Years 2024 through 2030 and % CAGR
- TABLE 99: Rest of World Historic Review for Panelized Modular Building Systems by End-Use - Residential End-Use, Commercial End-Use and Industrial End-Use Markets - Independent Analysis of Annual Sales in US$ Million for Years 2014 through 2023 and % CAGR
- TABLE 100: Rest of World 16-Year Perspective for Panelized Modular Building Systems by End-Use - Percentage Breakdown of Value Sales for Residential End-Use, Commercial End-Use and Industrial End-Use for the Years 2014, 2025 & 2030
- IV. COMPETITION
Pricing
Currency Rates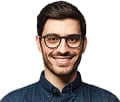