
PCB Connectors
Description
Global PCB Connectors Market to Reach US$20.5 Billion by 2030
The global market for PCB Connectors estimated at US$17.8 Billion in the year 2024, is expected to reach US$20.5 Billion by 2030, growing at a CAGR of 2.4% over the analysis period 2024-2030. Board-to-Board Connectors, one of the segments analyzed in the report, is expected to record a 2.2% CAGR and reach US$6.7 Billion by the end of the analysis period. Growth in the Wire-to-Board Connectors segment is estimated at 2.4% CAGR over the analysis period.
The U.S. Market is Estimated at US$4.8 Billion While China is Forecast to Grow at 4.6% CAGR
The PCB Connectors market in the U.S. is estimated at US$4.8 Billion in the year 2024. China, the world`s second largest economy, is forecast to reach a projected market size of US$3.9 Billion by the year 2030 trailing a CAGR of 4.6% over the analysis period 2024-2030. Among the other noteworthy geographic markets are Japan and Canada, each forecast to grow at a CAGR of 0.9% and 1.8% respectively over the analysis period. Within Europe, Germany is forecast to grow at approximately 1.3% CAGR.
Global PCB Connectors Market - Key Trends & Drivers Summarized
Why Are PCB Connectors Playing a Central Role in Emerging Electronic Architectures?
Printed Circuit Board (PCB) connectors are the essential interface components that enable electrical connectivity between boards, modules, or external systems within electronic devices. As electronic systems become more compact, modular, and functionally complex, PCB connectors have evolved into highly engineered solutions tailored for high-speed data transfer, power delivery, thermal performance, and mechanical reliability. The surge in demand for consumer electronics, industrial automation, 5G infrastructure, and electric vehicles is intensifying the need for advanced connector configurations.
Modern PCB connectors encompass a wide variety of formats-board-to-board, wire-to-board, mezzanine, backplane, edge connectors, and coaxial types-each designed for specific electrical and mechanical characteristics. Miniaturization is a dominant trend, with pitches as low as 0.25 mm now common in mobile and wearable electronics. Simultaneously, high current connectors for power electronics are being developed to manage increasing loads in applications such as EV inverters, industrial drives, and aerospace systems.
Signal integrity is a critical factor influencing connector design, particularly for high-speed data applications in networking equipment, telecom base stations, and server motherboards. To mitigate signal loss and cross-talk, connectors now feature impedance matching, differential pair configurations, and shielding enhancements. Connector manufacturers are investing in simulation and testing tools to optimize performance under various thermal, vibration, and electrical stress conditions, making them indispensable to next-generation PCB ecosystems.
What Material and Interface Innovations Are Redefining Connector Performance?
PCB connector innovation is being propelled by advances in material science, signal engineering, and interconnect standardization. High-performance thermoplastics such as LCP (liquid crystal polymer), PPS (polyphenylene sulfide), and PBT (polybutylene terephthalate) are increasingly used for connector housings due to their excellent dielectric properties, thermal stability, and resistance to moisture and chemicals. These materials enable connectors to perform in rugged environments such as automotive, medical devices, and industrial robotics.
Metal contacts are undergoing metallurgical optimization with coatings like gold-over-nickel or tin-lead alloys, ensuring low contact resistance and corrosion resistance across repeated mating cycles. Press-fit and surface-mount terminations are replacing through-hole types in high-speed applications to reduce inductance and support automated assembly. Innovations in latching mechanisms, blind-mating features, and polarized designs enhance connector reliability in high-vibration environments such as aerospace and military electronics.
The transition toward high-speed standards-such as PCIe Gen5, USB 4.0, and QSFP-DD-has created a need for connectors that can operate at 25+ Gbps while maintaining mechanical durability and EMI shielding. Co-packaged optics, fiber-to-board connectors, and hybrid power-signal modules are emerging to support bandwidth-intensive applications like AI servers, 5G radios, and optical transceivers. Connector designs now incorporate simulation-based modeling to ensure compatibility with SI/PI (signal/power integrity) requirements in dense multilayer boards.
Which End-Use Industries and Regional Markets Are Driving Connector Innovation?
The global PCB connector market spans a wide array of end-user industries, with consumer electronics, automotive, industrial automation, telecommunications, and aerospace sectors being the primary adopters. Smartphones, tablets, gaming consoles, and wearable devices rely on ultra-miniature connectors that support multiple signal and power lines within shrinking form factors. Meanwhile, automotive applications-from infotainment and ADAS to powertrain control-require vibration-resistant, heat-tolerant, and waterproof connectors certified under AEC-Q200 standards.
In industrial automation, PCB connectors are vital for PLCs, motor controllers, and HMI terminals, where reliability and signal integrity are non-negotiable. Telecommunication equipment-especially 5G base stations and edge computing devices-demands high-speed connectors with robust EMI shielding and minimal insertion loss. Aerospace and military sectors use high-reliability connectors that meet MIL-STD specifications, with applications in radar systems, flight controls, and satellite payloads.
Regionally, Asia-Pacific dominates the global market in both manufacturing and consumption. China, Taiwan, South Korea, and Japan host the world’s largest PCB and connector production ecosystems. North America and Europe are leading in high-end and application-specific connectors for automotive, aerospace, and data center markets. Growth in India and Southeast Asia is being driven by electronics manufacturing incentives, telecom infrastructure rollout, and EV assembly operations.
What Factors Are Fueling Growth in the Global PCB Connectors Market?
The growth in the global PCB connectors market is driven by rising electronics penetration across industries, increasing demand for high-speed interconnects, miniaturization of electronic devices, and the proliferation of smart technologies such as 5G, IoT, and AI. As every new product generation brings more complexity and higher performance benchmarks, the role of connectors is evolving from simple hardware interfaces to precision-engineered components that influence overall system efficiency.
The electrification of vehicles, automation of industrial processes, and expansion of global telecom infrastructure are creating sustained demand for durable, compact, and high-speed PCB connectors. Connector suppliers are responding by offering modular product families, rapid prototyping, and value-added design services to OEMs. As sustainability becomes a critical concern, lead-free solder compatibility, recyclable materials, and energy-efficient manufacturing are also influencing connector development strategies.
With electronic systems becoming more intelligent, networked, and power-dense, PCB connectors must meet increasingly stringent reliability, EMI, thermal, and signal performance standards. This market will continue to benefit from the convergence of design miniaturization, digital transformation, and cross-industry electronic integration-making it an indispensable link in the global electronics value chain.
SCOPE OF STUDY:The report analyzes the PCB Connectors market in terms of units by the following Segments, and Geographic Regions/Countries:
Segments:
Type (Board-to-Board Connectors, Wire-to-Board Connectors, Power Connectors, RF Connectors, Optical Connectors); End-User (Telecom End-User, Transportation End-User, Automotive End-User, Industrial End-User, Computer & Peripherals End-User, Other End-Users)
Geographic Regions/Countries:
World; United States; Canada; Japan; China; Europe (France; Germany; Italy; United Kingdom; Spain; Russia; and Rest of Europe); Asia-Pacific (Australia; India; South Korea; and Rest of Asia-Pacific); Latin America (Argentina; Brazil; Mexico; and Rest of Latin America); Middle East (Iran; Israel; Saudi Arabia; United Arab Emirates; and Rest of Middle East); and Africa.
Select Competitors (Total 32 Featured) -
- Amphenol
- Aptiv
- AVIC Jonhon Optronic Technology
- Belden
- FCI (Amphenol FCI / Corning)
- Foxconn (FIT)
- Hirose Electric
- JAE (Japan Aviation Electronics)
- JONHON (AVIC Jonhon)
- JST (Japan Solderless Terminals)
- LEMO
- LOTES
- Luxshare Precision
- Molex
- ODU International AG
- Phoenix Contact
- Phoenix Contact
- Radiall
- Rosenberger
- Samtec
We`re transforming market and competitive intelligence with validated expert content and AI tools.
Instead of following the general norm of querying LLMs and Industry-specific SLMs, we built repositories of content curated from domain experts worldwide including video transcripts, blogs, search engines research, and massive amounts of enterprise, product/service, and market data.
TARIFF IMPACT FACTOR
Our new release incorporates impact of tariffs on geographical markets as we predict a shift in competitiveness of companies based on HQ country, manufacturing base, exports and imports (finished goods and OEM). This intricate and multifaceted market reality will impact competitors by increasing the Cost of Goods Sold (COGS), reducing profitability, reconfiguring supply chains, amongst other micro and macro market dynamics.
Please note: Reports are sold as single-site single-user licenses. Electronic versions require 24-48 hours as each copy is customized to the client with digital controls and custom watermarks. The Publisher uses digital controls protecting against copying and printing is restricted to one full copy to be used at the same location.
The latest version of Adobe Acrobat Reader is required to view the report. Upon ordering an electronic version, the Publisher will provide a link to download the purchased report.
Prior to fulfillment of an order, the client will be required to sign a document detailing the purchase terms for a publication from this publisher.
Table of Contents
- I. METHODOLOGY
- II. EXECUTIVE SUMMARY
- 1. MARKET OVERVIEW
- Influencer Market Insights
- World Market Trajectories
- Tariff Impact on Global Supply Chain Patterns
- PCB Connectors – Global Key Competitors Percentage Market Share in 2025 (E)
- Competitive Market Presence - Strong/Active/Niche/Trivial for Players Worldwide in 2025 (E)
- 2. FOCUS ON SELECT PLAYERS
- 3. MARKET TRENDS & DRIVERS
- Growth in Consumer Electronics and IoT Devices Throws the Spotlight on High-Density PCB Connectors
- Rising Miniaturization in Device Design Drives Demand for Compact and Low-Profile Connectors
- Automotive Electronics and EV Architecture Expansion Propels Demand for High-Reliability PCB Interfaces
- 5G and Advanced Communications Infrastructure Spur Adoption of High-Frequency PCB Connector Systems
- Increased Complexity of Multi-Layer PCBs Expands Addressable Market for Precision Interconnects
- Medical Device Innovation Drives Demand for Biocompatible and Miniaturized PCB Connectors
- Integration of Embedded Systems in Industrial Automation Sustains Growth in Ruggedized Connectors
- Thermal Management Challenges Promote Development of Low-Resistance PCB Termination Solutions
- Surge in PCB Prototyping and Modular Design Trends Strengthens Business Case for Plug-and-Play Connectors
- Standardization of High-Speed Data Protocols Drives Adoption of Shielded and EMI-Protected PCB Connectors
- Proliferation of Wearables and Smart Devices Accelerates Use of Flexible and Board-to-Board Connectors
- Supply Chain Localization Efforts Propel Regional Production of High-Precision PCB Components
- Increased Focus on Signal Integrity and Noise Reduction Supports Innovation in Interposer Designs
- Renewable Energy and Smart Grid Expansion Spurs Demand for High-Current PCB Connection Systems
- Advanced Manufacturing Techniques (e.g., SMT) Drive Integration-Ready Connector Development
- Growth of Aerospace and Defense Electronics Drives Certification-Compliant Connector Designs
- Customization Demands in Edge Computing Hardware Propel Modular Connector Solutions
- Transition to Lead-Free Soldering Standards Spurs Innovation in Connector Finishing Materials
- Rise of AI Accelerators and GPUs Drives Innovation in Power Distribution and Signal Transmission Connectors
- M&A Activity Among Component Suppliers Spurs Technology Integration and Platform Expansion
- 4. GLOBAL MARKET PERSPECTIVE
- TABLE 1: World PCB Connectors Market Analysis of Annual Sales in US$ Million for Years 2014 through 2030
- TABLE 2: World Recent Past, Current & Future Analysis for PCB Connectors by Geographic Region - USA, Canada, Japan, China, Europe, Asia-Pacific, Latin America, Middle East and Africa Markets - Independent Analysis of Annual Sales in US$ Million for Years 2024 through 2030 and % CAGR
- TABLE 3: World Historic Review for PCB Connectors by Geographic Region - USA, Canada, Japan, China, Europe, Asia-Pacific, Latin America, Middle East and Africa Markets - Independent Analysis of Annual Sales in US$ Million for Years 2014 through 2023 and % CAGR
- TABLE 4: World 16-Year Perspective for PCB Connectors by Geographic Region - Percentage Breakdown of Value Sales for USA, Canada, Japan, China, Europe, Asia-Pacific, Latin America, Middle East and Africa Markets for Years 2014, 2025 & 2030
- TABLE 5: World Recent Past, Current & Future Analysis for Board-to-Board Connectors by Geographic Region - USA, Canada, Japan, China, Europe, Asia-Pacific, Latin America, Middle East and Africa Markets - Independent Analysis of Annual Sales in US$ Million for Years 2024 through 2030 and % CAGR
- TABLE 6: World Historic Review for Board-to-Board Connectors by Geographic Region - USA, Canada, Japan, China, Europe, Asia-Pacific, Latin America, Middle East and Africa Markets - Independent Analysis of Annual Sales in US$ Million for Years 2014 through 2023 and % CAGR
- TABLE 7: World 16-Year Perspective for Board-to-Board Connectors by Geographic Region - Percentage Breakdown of Value Sales for USA, Canada, Japan, China, Europe, Asia-Pacific, Latin America, Middle East and Africa for Years 2014, 2025 & 2030
- TABLE 8: World Recent Past, Current & Future Analysis for Wire-to-Board Connectors by Geographic Region - USA, Canada, Japan, China, Europe, Asia-Pacific, Latin America, Middle East and Africa Markets - Independent Analysis of Annual Sales in US$ Million for Years 2024 through 2030 and % CAGR
- TABLE 9: World Historic Review for Wire-to-Board Connectors by Geographic Region - USA, Canada, Japan, China, Europe, Asia-Pacific, Latin America, Middle East and Africa Markets - Independent Analysis of Annual Sales in US$ Million for Years 2014 through 2023 and % CAGR
- TABLE 10: World 16-Year Perspective for Wire-to-Board Connectors by Geographic Region - Percentage Breakdown of Value Sales for USA, Canada, Japan, China, Europe, Asia-Pacific, Latin America, Middle East and Africa for Years 2014, 2025 & 2030
- TABLE 11: World Recent Past, Current & Future Analysis for Power Connectors by Geographic Region - USA, Canada, Japan, China, Europe, Asia-Pacific, Latin America, Middle East and Africa Markets - Independent Analysis of Annual Sales in US$ Million for Years 2024 through 2030 and % CAGR
- TABLE 12: World Historic Review for Power Connectors by Geographic Region - USA, Canada, Japan, China, Europe, Asia-Pacific, Latin America, Middle East and Africa Markets - Independent Analysis of Annual Sales in US$ Million for Years 2014 through 2023 and % CAGR
- TABLE 13: World 16-Year Perspective for Power Connectors by Geographic Region - Percentage Breakdown of Value Sales for USA, Canada, Japan, China, Europe, Asia-Pacific, Latin America, Middle East and Africa for Years 2014, 2025 & 2030
- TABLE 14: World Recent Past, Current & Future Analysis for RF Connectors by Geographic Region - USA, Canada, Japan, China, Europe, Asia-Pacific, Latin America, Middle East and Africa Markets - Independent Analysis of Annual Sales in US$ Million for Years 2024 through 2030 and % CAGR
- TABLE 15: World Historic Review for RF Connectors by Geographic Region - USA, Canada, Japan, China, Europe, Asia-Pacific, Latin America, Middle East and Africa Markets - Independent Analysis of Annual Sales in US$ Million for Years 2014 through 2023 and % CAGR
- TABLE 16: World 16-Year Perspective for RF Connectors by Geographic Region - Percentage Breakdown of Value Sales for USA, Canada, Japan, China, Europe, Asia-Pacific, Latin America, Middle East and Africa for Years 2014, 2025 & 2030
- TABLE 17: World Recent Past, Current & Future Analysis for Optical Connectors by Geographic Region - USA, Canada, Japan, China, Europe, Asia-Pacific, Latin America, Middle East and Africa Markets - Independent Analysis of Annual Sales in US$ Million for Years 2024 through 2030 and % CAGR
- TABLE 18: World Historic Review for Optical Connectors by Geographic Region - USA, Canada, Japan, China, Europe, Asia-Pacific, Latin America, Middle East and Africa Markets - Independent Analysis of Annual Sales in US$ Million for Years 2014 through 2023 and % CAGR
- TABLE 19: World 16-Year Perspective for Optical Connectors by Geographic Region - Percentage Breakdown of Value Sales for USA, Canada, Japan, China, Europe, Asia-Pacific, Latin America, Middle East and Africa for Years 2014, 2025 & 2030
- TABLE 20: World Recent Past, Current & Future Analysis for Computer & Peripherals End-User by Geographic Region - USA, Canada, Japan, China, Europe, Asia-Pacific, Latin America, Middle East and Africa Markets - Independent Analysis of Annual Sales in US$ Million for Years 2024 through 2030 and % CAGR
- TABLE 21: World Historic Review for Computer & Peripherals End-User by Geographic Region - USA, Canada, Japan, China, Europe, Asia-Pacific, Latin America, Middle East and Africa Markets - Independent Analysis of Annual Sales in US$ Million for Years 2014 through 2023 and % CAGR
- TABLE 22: World 16-Year Perspective for Computer & Peripherals End-User by Geographic Region - Percentage Breakdown of Value Sales for USA, Canada, Japan, China, Europe, Asia-Pacific, Latin America, Middle East and Africa for Years 2014, 2025 & 2030
- TABLE 23: World Recent Past, Current & Future Analysis for Other End-Users by Geographic Region - USA, Canada, Japan, China, Europe, Asia-Pacific, Latin America, Middle East and Africa Markets - Independent Analysis of Annual Sales in US$ Million for Years 2024 through 2030 and % CAGR
- TABLE 24: World Historic Review for Other End-Users by Geographic Region - USA, Canada, Japan, China, Europe, Asia-Pacific, Latin America, Middle East and Africa Markets - Independent Analysis of Annual Sales in US$ Million for Years 2014 through 2023 and % CAGR
- TABLE 25: World 16-Year Perspective for Other End-Users by Geographic Region - Percentage Breakdown of Value Sales for USA, Canada, Japan, China, Europe, Asia-Pacific, Latin America, Middle East and Africa for Years 2014, 2025 & 2030
- TABLE 26: World Recent Past, Current & Future Analysis for Telecom End-User by Geographic Region - USA, Canada, Japan, China, Europe, Asia-Pacific, Latin America, Middle East and Africa Markets - Independent Analysis of Annual Sales in US$ Million for Years 2024 through 2030 and % CAGR
- TABLE 27: World Historic Review for Telecom End-User by Geographic Region - USA, Canada, Japan, China, Europe, Asia-Pacific, Latin America, Middle East and Africa Markets - Independent Analysis of Annual Sales in US$ Million for Years 2014 through 2023 and % CAGR
- TABLE 28: World 16-Year Perspective for Telecom End-User by Geographic Region - Percentage Breakdown of Value Sales for USA, Canada, Japan, China, Europe, Asia-Pacific, Latin America, Middle East and Africa for Years 2014, 2025 & 2030
- TABLE 29: World Recent Past, Current & Future Analysis for Transportation End-User by Geographic Region - USA, Canada, Japan, China, Europe, Asia-Pacific, Latin America, Middle East and Africa Markets - Independent Analysis of Annual Sales in US$ Million for Years 2024 through 2030 and % CAGR
- TABLE 30: World Historic Review for Transportation End-User by Geographic Region - USA, Canada, Japan, China, Europe, Asia-Pacific, Latin America, Middle East and Africa Markets - Independent Analysis of Annual Sales in US$ Million for Years 2014 through 2023 and % CAGR
- TABLE 31: World 16-Year Perspective for Transportation End-User by Geographic Region - Percentage Breakdown of Value Sales for USA, Canada, Japan, China, Europe, Asia-Pacific, Latin America, Middle East and Africa for Years 2014, 2025 & 2030
- TABLE 32: World Recent Past, Current & Future Analysis for Automotive End-User by Geographic Region - USA, Canada, Japan, China, Europe, Asia-Pacific, Latin America, Middle East and Africa Markets - Independent Analysis of Annual Sales in US$ Million for Years 2024 through 2030 and % CAGR
- TABLE 33: World Historic Review for Automotive End-User by Geographic Region - USA, Canada, Japan, China, Europe, Asia-Pacific, Latin America, Middle East and Africa Markets - Independent Analysis of Annual Sales in US$ Million for Years 2014 through 2023 and % CAGR
- TABLE 34: World 16-Year Perspective for Automotive End-User by Geographic Region - Percentage Breakdown of Value Sales for USA, Canada, Japan, China, Europe, Asia-Pacific, Latin America, Middle East and Africa for Years 2014, 2025 & 2030
- TABLE 35: World Recent Past, Current & Future Analysis for Industrial End-User by Geographic Region - USA, Canada, Japan, China, Europe, Asia-Pacific, Latin America, Middle East and Africa Markets - Independent Analysis of Annual Sales in US$ Million for Years 2024 through 2030 and % CAGR
- TABLE 36: World Historic Review for Industrial End-User by Geographic Region - USA, Canada, Japan, China, Europe, Asia-Pacific, Latin America, Middle East and Africa Markets - Independent Analysis of Annual Sales in US$ Million for Years 2014 through 2023 and % CAGR
- TABLE 37: World 16-Year Perspective for Industrial End-User by Geographic Region - Percentage Breakdown of Value Sales for USA, Canada, Japan, China, Europe, Asia-Pacific, Latin America, Middle East and Africa for Years 2014, 2025 & 2030
- III. MARKET ANALYSIS
- UNITED STATES
- PCB Connectors Market Presence - Strong/Active/Niche/Trivial - Key Competitors in the United States for 2025 (E)
- TABLE 38: USA Recent Past, Current & Future Analysis for PCB Connectors by Type - Board-to-Board Connectors, Wire-to-Board Connectors, Power Connectors, RF Connectors and Optical Connectors - Independent Analysis of Annual Sales in US$ Million for the Years 2024 through 2030 and % CAGR
- TABLE 39: USA Historic Review for PCB Connectors by Type - Board-to-Board Connectors, Wire-to-Board Connectors, Power Connectors, RF Connectors and Optical Connectors Markets - Independent Analysis of Annual Sales in US$ Million for Years 2014 through 2023 and % CAGR
- TABLE 40: USA 16-Year Perspective for PCB Connectors by Type - Percentage Breakdown of Value Sales for Board-to-Board Connectors, Wire-to-Board Connectors, Power Connectors, RF Connectors and Optical Connectors for the Years 2014, 2025 & 2030
- TABLE 41: USA Recent Past, Current & Future Analysis for PCB Connectors by End-user - Computer & Peripherals End-User, Other End-Users, Telecom End-User, Transportation End-User, Automotive End-User and Industrial End-User - Independent Analysis of Annual Sales in US$ Million for the Years 2024 through 2030 and % CAGR
- TABLE 42: USA Historic Review for PCB Connectors by End-user - Computer & Peripherals End-User, Other End-Users, Telecom End-User, Transportation End-User, Automotive End-User and Industrial End-User Markets - Independent Analysis of Annual Sales in US$ Million for Years 2014 through 2023 and % CAGR
- TABLE 43: USA 16-Year Perspective for PCB Connectors by End-user - Percentage Breakdown of Value Sales for Computer & Peripherals End-User, Other End-Users, Telecom End-User, Transportation End-User, Automotive End-User and Industrial End-User for the Years 2014, 2025 & 2030
- CANADA
- TABLE 44: Canada Recent Past, Current & Future Analysis for PCB Connectors by Type - Board-to-Board Connectors, Wire-to-Board Connectors, Power Connectors, RF Connectors and Optical Connectors - Independent Analysis of Annual Sales in US$ Million for the Years 2024 through 2030 and % CAGR
- TABLE 45: Canada Historic Review for PCB Connectors by Type - Board-to-Board Connectors, Wire-to-Board Connectors, Power Connectors, RF Connectors and Optical Connectors Markets - Independent Analysis of Annual Sales in US$ Million for Years 2014 through 2023 and % CAGR
- TABLE 46: Canada 16-Year Perspective for PCB Connectors by Type - Percentage Breakdown of Value Sales for Board-to-Board Connectors, Wire-to-Board Connectors, Power Connectors, RF Connectors and Optical Connectors for the Years 2014, 2025 & 2030
- TABLE 47: Canada Recent Past, Current & Future Analysis for PCB Connectors by End-user - Computer & Peripherals End-User, Other End-Users, Telecom End-User, Transportation End-User, Automotive End-User and Industrial End-User - Independent Analysis of Annual Sales in US$ Million for the Years 2024 through 2030 and % CAGR
- TABLE 48: Canada Historic Review for PCB Connectors by End-user - Computer & Peripherals End-User, Other End-Users, Telecom End-User, Transportation End-User, Automotive End-User and Industrial End-User Markets - Independent Analysis of Annual Sales in US$ Million for Years 2014 through 2023 and % CAGR
- TABLE 49: Canada 16-Year Perspective for PCB Connectors by End-user - Percentage Breakdown of Value Sales for Computer & Peripherals End-User, Other End-Users, Telecom End-User, Transportation End-User, Automotive End-User and Industrial End-User for the Years 2014, 2025 & 2030
- JAPAN
- PCB Connectors Market Presence - Strong/Active/Niche/Trivial - Key Competitors in Japan for 2025 (E)
- TABLE 50: Japan Recent Past, Current & Future Analysis for PCB Connectors by Type - Board-to-Board Connectors, Wire-to-Board Connectors, Power Connectors, RF Connectors and Optical Connectors - Independent Analysis of Annual Sales in US$ Million for the Years 2024 through 2030 and % CAGR
- TABLE 51: Japan Historic Review for PCB Connectors by Type - Board-to-Board Connectors, Wire-to-Board Connectors, Power Connectors, RF Connectors and Optical Connectors Markets - Independent Analysis of Annual Sales in US$ Million for Years 2014 through 2023 and % CAGR
- TABLE 52: Japan 16-Year Perspective for PCB Connectors by Type - Percentage Breakdown of Value Sales for Board-to-Board Connectors, Wire-to-Board Connectors, Power Connectors, RF Connectors and Optical Connectors for the Years 2014, 2025 & 2030
- TABLE 53: Japan Recent Past, Current & Future Analysis for PCB Connectors by End-user - Computer & Peripherals End-User, Other End-Users, Telecom End-User, Transportation End-User, Automotive End-User and Industrial End-User - Independent Analysis of Annual Sales in US$ Million for the Years 2024 through 2030 and % CAGR
- TABLE 54: Japan Historic Review for PCB Connectors by End-user - Computer & Peripherals End-User, Other End-Users, Telecom End-User, Transportation End-User, Automotive End-User and Industrial End-User Markets - Independent Analysis of Annual Sales in US$ Million for Years 2014 through 2023 and % CAGR
- TABLE 55: Japan 16-Year Perspective for PCB Connectors by End-user - Percentage Breakdown of Value Sales for Computer & Peripherals End-User, Other End-Users, Telecom End-User, Transportation End-User, Automotive End-User and Industrial End-User for the Years 2014, 2025 & 2030
- CHINA
- PCB Connectors Market Presence - Strong/Active/Niche/Trivial - Key Competitors in China for 2025 (E)
- TABLE 56: China Recent Past, Current & Future Analysis for PCB Connectors by Type - Board-to-Board Connectors, Wire-to-Board Connectors, Power Connectors, RF Connectors and Optical Connectors - Independent Analysis of Annual Sales in US$ Million for the Years 2024 through 2030 and % CAGR
- TABLE 57: China Historic Review for PCB Connectors by Type - Board-to-Board Connectors, Wire-to-Board Connectors, Power Connectors, RF Connectors and Optical Connectors Markets - Independent Analysis of Annual Sales in US$ Million for Years 2014 through 2023 and % CAGR
- TABLE 58: China 16-Year Perspective for PCB Connectors by Type - Percentage Breakdown of Value Sales for Board-to-Board Connectors, Wire-to-Board Connectors, Power Connectors, RF Connectors and Optical Connectors for the Years 2014, 2025 & 2030
- TABLE 59: China Recent Past, Current & Future Analysis for PCB Connectors by End-user - Computer & Peripherals End-User, Other End-Users, Telecom End-User, Transportation End-User, Automotive End-User and Industrial End-User - Independent Analysis of Annual Sales in US$ Million for the Years 2024 through 2030 and % CAGR
- TABLE 60: China Historic Review for PCB Connectors by End-user - Computer & Peripherals End-User, Other End-Users, Telecom End-User, Transportation End-User, Automotive End-User and Industrial End-User Markets - Independent Analysis of Annual Sales in US$ Million for Years 2014 through 2023 and % CAGR
- TABLE 61: China 16-Year Perspective for PCB Connectors by End-user - Percentage Breakdown of Value Sales for Computer & Peripherals End-User, Other End-Users, Telecom End-User, Transportation End-User, Automotive End-User and Industrial End-User for the Years 2014, 2025 & 2030
- EUROPE
- PCB Connectors Market Presence - Strong/Active/Niche/Trivial - Key Competitors in Europe for 2025 (E)
- TABLE 62: Europe Recent Past, Current & Future Analysis for PCB Connectors by Geographic Region - France, Germany, Italy, UK, Spain, Russia and Rest of Europe Markets - Independent Analysis of Annual Sales in US$ Million for Years 2024 through 2030 and % CAGR
- TABLE 63: Europe Historic Review for PCB Connectors by Geographic Region - France, Germany, Italy, UK, Spain, Russia and Rest of Europe Markets - Independent Analysis of Annual Sales in US$ Million for Years 2014 through 2023 and % CAGR
- TABLE 64: Europe 16-Year Perspective for PCB Connectors by Geographic Region - Percentage Breakdown of Value Sales for France, Germany, Italy, UK, Spain, Russia and Rest of Europe Markets for Years 2014, 2025 & 2030
- TABLE 65: Europe Recent Past, Current & Future Analysis for PCB Connectors by Type - Board-to-Board Connectors, Wire-to-Board Connectors, Power Connectors, RF Connectors and Optical Connectors - Independent Analysis of Annual Sales in US$ Million for the Years 2024 through 2030 and % CAGR
- TABLE 66: Europe Historic Review for PCB Connectors by Type - Board-to-Board Connectors, Wire-to-Board Connectors, Power Connectors, RF Connectors and Optical Connectors Markets - Independent Analysis of Annual Sales in US$ Million for Years 2014 through 2023 and % CAGR
- TABLE 67: Europe 16-Year Perspective for PCB Connectors by Type - Percentage Breakdown of Value Sales for Board-to-Board Connectors, Wire-to-Board Connectors, Power Connectors, RF Connectors and Optical Connectors for the Years 2014, 2025 & 2030
- TABLE 68: Europe Recent Past, Current & Future Analysis for PCB Connectors by End-user - Computer & Peripherals End-User, Other End-Users, Telecom End-User, Transportation End-User, Automotive End-User and Industrial End-User - Independent Analysis of Annual Sales in US$ Million for the Years 2024 through 2030 and % CAGR
- TABLE 69: Europe Historic Review for PCB Connectors by End-user - Computer & Peripherals End-User, Other End-Users, Telecom End-User, Transportation End-User, Automotive End-User and Industrial End-User Markets - Independent Analysis of Annual Sales in US$ Million for Years 2014 through 2023 and % CAGR
- TABLE 70: Europe 16-Year Perspective for PCB Connectors by End-user - Percentage Breakdown of Value Sales for Computer & Peripherals End-User, Other End-Users, Telecom End-User, Transportation End-User, Automotive End-User and Industrial End-User for the Years 2014, 2025 & 2030
- FRANCE
- PCB Connectors Market Presence - Strong/Active/Niche/Trivial - Key Competitors in France for 2025 (E)
- TABLE 71: France Recent Past, Current & Future Analysis for PCB Connectors by Type - Board-to-Board Connectors, Wire-to-Board Connectors, Power Connectors, RF Connectors and Optical Connectors - Independent Analysis of Annual Sales in US$ Million for the Years 2024 through 2030 and % CAGR
- TABLE 72: France Historic Review for PCB Connectors by Type - Board-to-Board Connectors, Wire-to-Board Connectors, Power Connectors, RF Connectors and Optical Connectors Markets - Independent Analysis of Annual Sales in US$ Million for Years 2014 through 2023 and % CAGR
- TABLE 73: France 16-Year Perspective for PCB Connectors by Type - Percentage Breakdown of Value Sales for Board-to-Board Connectors, Wire-to-Board Connectors, Power Connectors, RF Connectors and Optical Connectors for the Years 2014, 2025 & 2030
- TABLE 74: France Recent Past, Current & Future Analysis for PCB Connectors by End-user - Computer & Peripherals End-User, Other End-Users, Telecom End-User, Transportation End-User, Automotive End-User and Industrial End-User - Independent Analysis of Annual Sales in US$ Million for the Years 2024 through 2030 and % CAGR
- TABLE 75: France Historic Review for PCB Connectors by End-user - Computer & Peripherals End-User, Other End-Users, Telecom End-User, Transportation End-User, Automotive End-User and Industrial End-User Markets - Independent Analysis of Annual Sales in US$ Million for Years 2014 through 2023 and % CAGR
- TABLE 76: France 16-Year Perspective for PCB Connectors by End-user - Percentage Breakdown of Value Sales for Computer & Peripherals End-User, Other End-Users, Telecom End-User, Transportation End-User, Automotive End-User and Industrial End-User for the Years 2014, 2025 & 2030
- GERMANY
- PCB Connectors Market Presence - Strong/Active/Niche/Trivial - Key Competitors in Germany for 2025 (E)
- TABLE 77: Germany Recent Past, Current & Future Analysis for PCB Connectors by Type - Board-to-Board Connectors, Wire-to-Board Connectors, Power Connectors, RF Connectors and Optical Connectors - Independent Analysis of Annual Sales in US$ Million for the Years 2024 through 2030 and % CAGR
- TABLE 78: Germany Historic Review for PCB Connectors by Type - Board-to-Board Connectors, Wire-to-Board Connectors, Power Connectors, RF Connectors and Optical Connectors Markets - Independent Analysis of Annual Sales in US$ Million for Years 2014 through 2023 and % CAGR
- TABLE 79: Germany 16-Year Perspective for PCB Connectors by Type - Percentage Breakdown of Value Sales for Board-to-Board Connectors, Wire-to-Board Connectors, Power Connectors, RF Connectors and Optical Connectors for the Years 2014, 2025 & 2030
- TABLE 80: Germany Recent Past, Current & Future Analysis for PCB Connectors by End-user - Computer & Peripherals End-User, Other End-Users, Telecom End-User, Transportation End-User, Automotive End-User and Industrial End-User - Independent Analysis of Annual Sales in US$ Million for the Years 2024 through 2030 and % CAGR
- TABLE 81: Germany Historic Review for PCB Connectors by End-user - Computer & Peripherals End-User, Other End-Users, Telecom End-User, Transportation End-User, Automotive End-User and Industrial End-User Markets - Independent Analysis of Annual Sales in US$ Million for Years 2014 through 2023 and % CAGR
- TABLE 82: Germany 16-Year Perspective for PCB Connectors by End-user - Percentage Breakdown of Value Sales for Computer & Peripherals End-User, Other End-Users, Telecom End-User, Transportation End-User, Automotive End-User and Industrial End-User for the Years 2014, 2025 & 2030
- ITALY
- TABLE 83: Italy Recent Past, Current & Future Analysis for PCB Connectors by Type - Board-to-Board Connectors, Wire-to-Board Connectors, Power Connectors, RF Connectors and Optical Connectors - Independent Analysis of Annual Sales in US$ Million for the Years 2024 through 2030 and % CAGR
- TABLE 84: Italy Historic Review for PCB Connectors by Type - Board-to-Board Connectors, Wire-to-Board Connectors, Power Connectors, RF Connectors and Optical Connectors Markets - Independent Analysis of Annual Sales in US$ Million for Years 2014 through 2023 and % CAGR
- TABLE 85: Italy 16-Year Perspective for PCB Connectors by Type - Percentage Breakdown of Value Sales for Board-to-Board Connectors, Wire-to-Board Connectors, Power Connectors, RF Connectors and Optical Connectors for the Years 2014, 2025 & 2030
- TABLE 86: Italy Recent Past, Current & Future Analysis for PCB Connectors by End-user - Computer & Peripherals End-User, Other End-Users, Telecom End-User, Transportation End-User, Automotive End-User and Industrial End-User - Independent Analysis of Annual Sales in US$ Million for the Years 2024 through 2030 and % CAGR
- TABLE 87: Italy Historic Review for PCB Connectors by End-user - Computer & Peripherals End-User, Other End-Users, Telecom End-User, Transportation End-User, Automotive End-User and Industrial End-User Markets - Independent Analysis of Annual Sales in US$ Million for Years 2014 through 2023 and % CAGR
- TABLE 88: Italy 16-Year Perspective for PCB Connectors by End-user - Percentage Breakdown of Value Sales for Computer & Peripherals End-User, Other End-Users, Telecom End-User, Transportation End-User, Automotive End-User and Industrial End-User for the Years 2014, 2025 & 2030
- UNITED KINGDOM
- PCB Connectors Market Presence - Strong/Active/Niche/Trivial - Key Competitors in the United Kingdom for 2025 (E)
- TABLE 89: UK Recent Past, Current & Future Analysis for PCB Connectors by Type - Board-to-Board Connectors, Wire-to-Board Connectors, Power Connectors, RF Connectors and Optical Connectors - Independent Analysis of Annual Sales in US$ Million for the Years 2024 through 2030 and % CAGR
- TABLE 90: UK Historic Review for PCB Connectors by Type - Board-to-Board Connectors, Wire-to-Board Connectors, Power Connectors, RF Connectors and Optical Connectors Markets - Independent Analysis of Annual Sales in US$ Million for Years 2014 through 2023 and % CAGR
- TABLE 91: UK 16-Year Perspective for PCB Connectors by Type - Percentage Breakdown of Value Sales for Board-to-Board Connectors, Wire-to-Board Connectors, Power Connectors, RF Connectors and Optical Connectors for the Years 2014, 2025 & 2030
- TABLE 92: UK Recent Past, Current & Future Analysis for PCB Connectors by End-user - Computer & Peripherals End-User, Other End-Users, Telecom End-User, Transportation End-User, Automotive End-User and Industrial End-User - Independent Analysis of Annual Sales in US$ Million for the Years 2024 through 2030 and % CAGR
- TABLE 93: UK Historic Review for PCB Connectors by End-user - Computer & Peripherals End-User, Other End-Users, Telecom End-User, Transportation End-User, Automotive End-User and Industrial End-User Markets - Independent Analysis of Annual Sales in US$ Million for Years 2014 through 2023 and % CAGR
- TABLE 94: UK 16-Year Perspective for PCB Connectors by End-user - Percentage Breakdown of Value Sales for Computer & Peripherals End-User, Other End-Users, Telecom End-User, Transportation End-User, Automotive End-User and Industrial End-User for the Years 2014, 2025 & 2030
- SPAIN
- TABLE 95: Spain Recent Past, Current & Future Analysis for PCB Connectors by Type - Board-to-Board Connectors, Wire-to-Board Connectors, Power Connectors, RF Connectors and Optical Connectors - Independent Analysis of Annual Sales in US$ Million for the Years 2024 through 2030 and % CAGR
- TABLE 96: Spain Historic Review for PCB Connectors by Type - Board-to-Board Connectors, Wire-to-Board Connectors, Power Connectors, RF Connectors and Optical Connectors Markets - Independent Analysis of Annual Sales in US$ Million for Years 2014 through 2023 and % CAGR
- TABLE 97: Spain 16-Year Perspective for PCB Connectors by Type - Percentage Breakdown of Value Sales for Board-to-Board Connectors, Wire-to-Board Connectors, Power Connectors, RF Connectors and Optical Connectors for the Years 2014, 2025 & 2030
- TABLE 98: Spain Recent Past, Current & Future Analysis for PCB Connectors by End-user - Computer & Peripherals End-User, Other End-Users, Telecom End-User, Transportation End-User, Automotive End-User and Industrial End-User - Independent Analysis of Annual Sales in US$ Million for the Years 2024 through 2030 and % CAGR
- TABLE 99: Spain Historic Review for PCB Connectors by End-user - Computer & Peripherals End-User, Other End-Users, Telecom End-User, Transportation End-User, Automotive End-User and Industrial End-User Markets - Independent Analysis of Annual Sales in US$ Million for Years 2014 through 2023 and % CAGR
- TABLE 100: Spain 16-Year Perspective for PCB Connectors by End-user - Percentage Breakdown of Value Sales for Computer & Peripherals End-User, Other End-Users, Telecom End-User, Transportation End-User, Automotive End-User and Industrial End-User for the Years 2014, 2025 & 2030
- RUSSIA
- TABLE 101: Russia Recent Past, Current & Future Analysis for PCB Connectors by Type - Board-to-Board Connectors, Wire-to-Board Connectors, Power Connectors, RF Connectors and Optical Connectors - Independent Analysis of Annual Sales in US$ Million for the Years 2024 through 2030 and % CAGR
- TABLE 102: Russia Historic Review for PCB Connectors by Type - Board-to-Board Connectors, Wire-to-Board Connectors, Power Connectors, RF Connectors and Optical Connectors Markets - Independent Analysis of Annual Sales in US$ Million for Years 2014 through 2023 and % CAGR
- TABLE 103: Russia 16-Year Perspective for PCB Connectors by Type - Percentage Breakdown of Value Sales for Board-to-Board Connectors, Wire-to-Board Connectors, Power Connectors, RF Connectors and Optical Connectors for the Years 2014, 2025 & 2030
- TABLE 104: Russia Recent Past, Current & Future Analysis for PCB Connectors by End-user - Computer & Peripherals End-User, Other End-Users, Telecom End-User, Transportation End-User, Automotive End-User and Industrial End-User - Independent Analysis of Annual Sales in US$ Million for the Years 2024 through 2030 and % CAGR
- TABLE 105: Russia Historic Review for PCB Connectors by End-user - Computer & Peripherals End-User, Other End-Users, Telecom End-User, Transportation End-User, Automotive End-User and Industrial End-User Markets - Independent Analysis of Annual Sales in US$ Million for Years 2014 through 2023 and % CAGR
- TABLE 106: Russia 16-Year Perspective for PCB Connectors by End-user - Percentage Breakdown of Value Sales for Computer & Peripherals End-User, Other End-Users, Telecom End-User, Transportation End-User, Automotive End-User and Industrial End-User for the Years 2014, 2025 & 2030
- REST OF EUROPE
- TABLE 107: Rest of Europe Recent Past, Current & Future Analysis for PCB Connectors by Type - Board-to-Board Connectors, Wire-to-Board Connectors, Power Connectors, RF Connectors and Optical Connectors - Independent Analysis of Annual Sales in US$ Million for the Years 2024 through 2030 and % CAGR
- TABLE 108: Rest of Europe Historic Review for PCB Connectors by Type - Board-to-Board Connectors, Wire-to-Board Connectors, Power Connectors, RF Connectors and Optical Connectors Markets - Independent Analysis of Annual Sales in US$ Million for Years 2014 through 2023 and % CAGR
- TABLE 109: Rest of Europe 16-Year Perspective for PCB Connectors by Type - Percentage Breakdown of Value Sales for Board-to-Board Connectors, Wire-to-Board Connectors, Power Connectors, RF Connectors and Optical Connectors for the Years 2014, 2025 & 2030
- TABLE 110: Rest of Europe Recent Past, Current & Future Analysis for PCB Connectors by End-user - Computer & Peripherals End-User, Other End-Users, Telecom End-User, Transportation End-User, Automotive End-User and Industrial End-User - Independent Analysis of Annual Sales in US$ Million for the Years 2024 through 2030 and % CAGR
- TABLE 111: Rest of Europe Historic Review for PCB Connectors by End-user - Computer & Peripherals End-User, Other End-Users, Telecom End-User, Transportation End-User, Automotive End-User and Industrial End-User Markets - Independent Analysis of Annual Sales in US$ Million for Years 2014 through 2023 and % CAGR
- TABLE 112: Rest of Europe 16-Year Perspective for PCB Connectors by End-user - Percentage Breakdown of Value Sales for Computer & Peripherals End-User, Other End-Users, Telecom End-User, Transportation End-User, Automotive End-User and Industrial End-User for the Years 2014, 2025 & 2030
- ASIA-PACIFIC
- PCB Connectors Market Presence - Strong/Active/Niche/Trivial - Key Competitors in Asia-Pacific for 2025 (E)
- TABLE 113: Asia-Pacific Recent Past, Current & Future Analysis for PCB Connectors by Geographic Region - Australia, India, South Korea and Rest of Asia-Pacific Markets - Independent Analysis of Annual Sales in US$ Million for Years 2024 through 2030 and % CAGR
- TABLE 114: Asia-Pacific Historic Review for PCB Connectors by Geographic Region - Australia, India, South Korea and Rest of Asia-Pacific Markets - Independent Analysis of Annual Sales in US$ Million for Years 2014 through 2023 and % CAGR
- TABLE 115: Asia-Pacific 16-Year Perspective for PCB Connectors by Geographic Region - Percentage Breakdown of Value Sales for Australia, India, South Korea and Rest of Asia-Pacific Markets for Years 2014, 2025 & 2030
- TABLE 116: Asia-Pacific Recent Past, Current & Future Analysis for PCB Connectors by Type - Board-to-Board Connectors, Wire-to-Board Connectors, Power Connectors, RF Connectors and Optical Connectors - Independent Analysis of Annual Sales in US$ Million for the Years 2024 through 2030 and % CAGR
- TABLE 117: Asia-Pacific Historic Review for PCB Connectors by Type - Board-to-Board Connectors, Wire-to-Board Connectors, Power Connectors, RF Connectors and Optical Connectors Markets - Independent Analysis of Annual Sales in US$ Million for Years 2014 through 2023 and % CAGR
- TABLE 118: Asia-Pacific 16-Year Perspective for PCB Connectors by Type - Percentage Breakdown of Value Sales for Board-to-Board Connectors, Wire-to-Board Connectors, Power Connectors, RF Connectors and Optical Connectors for the Years 2014, 2025 & 2030
- TABLE 119: Asia-Pacific Recent Past, Current & Future Analysis for PCB Connectors by End-user - Computer & Peripherals End-User, Other End-Users, Telecom End-User, Transportation End-User, Automotive End-User and Industrial End-User - Independent Analysis of Annual Sales in US$ Million for the Years 2024 through 2030 and % CAGR
- TABLE 120: Asia-Pacific Historic Review for PCB Connectors by End-user - Computer & Peripherals End-User, Other End-Users, Telecom End-User, Transportation End-User, Automotive End-User and Industrial End-User Markets - Independent Analysis of Annual Sales in US$ Million for Years 2014 through 2023 and % CAGR
- TABLE 121: Asia-Pacific 16-Year Perspective for PCB Connectors by End-user - Percentage Breakdown of Value Sales for Computer & Peripherals End-User, Other End-Users, Telecom End-User, Transportation End-User, Automotive End-User and Industrial End-User for the Years 2014, 2025 & 2030
- AUSTRALIA
- PCB Connectors Market Presence - Strong/Active/Niche/Trivial - Key Competitors in Australia for 2025 (E)
- TABLE 122: Australia Recent Past, Current & Future Analysis for PCB Connectors by Type - Board-to-Board Connectors, Wire-to-Board Connectors, Power Connectors, RF Connectors and Optical Connectors - Independent Analysis of Annual Sales in US$ Million for the Years 2024 through 2030 and % CAGR
- TABLE 123: Australia Historic Review for PCB Connectors by Type - Board-to-Board Connectors, Wire-to-Board Connectors, Power Connectors, RF Connectors and Optical Connectors Markets - Independent Analysis of Annual Sales in US$ Million for Years 2014 through 2023 and % CAGR
- TABLE 124: Australia 16-Year Perspective for PCB Connectors by Type - Percentage Breakdown of Value Sales for Board-to-Board Connectors, Wire-to-Board Connectors, Power Connectors, RF Connectors and Optical Connectors for the Years 2014, 2025 & 2030
- TABLE 125: Australia Recent Past, Current & Future Analysis for PCB Connectors by End-user - Computer & Peripherals End-User, Other End-Users, Telecom End-User, Transportation End-User, Automotive End-User and Industrial End-User - Independent Analysis of Annual Sales in US$ Million for the Years 2024 through 2030 and % CAGR
- TABLE 126: Australia Historic Review for PCB Connectors by End-user - Computer & Peripherals End-User, Other End-Users, Telecom End-User, Transportation End-User, Automotive End-User and Industrial End-User Markets - Independent Analysis of Annual Sales in US$ Million for Years 2014 through 2023 and % CAGR
- TABLE 127: Australia 16-Year Perspective for PCB Connectors by End-user - Percentage Breakdown of Value Sales for Computer & Peripherals End-User, Other End-Users, Telecom End-User, Transportation End-User, Automotive End-User and Industrial End-User for the Years 2014, 2025 & 2030
- INDIA
- PCB Connectors Market Presence - Strong/Active/Niche/Trivial - Key Competitors in India for 2025 (E)
- TABLE 128: India Recent Past, Current & Future Analysis for PCB Connectors by Type - Board-to-Board Connectors, Wire-to-Board Connectors, Power Connectors, RF Connectors and Optical Connectors - Independent Analysis of Annual Sales in US$ Million for the Years 2024 through 2030 and % CAGR
- TABLE 129: India Historic Review for PCB Connectors by Type - Board-to-Board Connectors, Wire-to-Board Connectors, Power Connectors, RF Connectors and Optical Connectors Markets - Independent Analysis of Annual Sales in US$ Million for Years 2014 through 2023 and % CAGR
- TABLE 130: India 16-Year Perspective for PCB Connectors by Type - Percentage Breakdown of Value Sales for Board-to-Board Connectors, Wire-to-Board Connectors, Power Connectors, RF Connectors and Optical Connectors for the Years 2014, 2025 & 2030
- TABLE 131: India Recent Past, Current & Future Analysis for PCB Connectors by End-user - Computer & Peripherals End-User, Other End-Users, Telecom End-User, Transportation End-User, Automotive End-User and Industrial End-User - Independent Analysis of Annual Sales in US$ Million for the Years 2024 through 2030 and % CAGR
- TABLE 132: India Historic Review for PCB Connectors by End-user - Computer & Peripherals End-User, Other End-Users, Telecom End-User, Transportation End-User, Automotive End-User and Industrial End-User Markets - Independent Analysis of Annual Sales in US$ Million for Years 2014 through 2023 and % CAGR
- TABLE 133: India 16-Year Perspective for PCB Connectors by End-user - Percentage Breakdown of Value Sales for Computer & Peripherals End-User, Other End-Users, Telecom End-User, Transportation End-User, Automotive End-User and Industrial End-User for the Years 2014, 2025 & 2030
- SOUTH KOREA
- TABLE 134: South Korea Recent Past, Current & Future Analysis for PCB Connectors by Type - Board-to-Board Connectors, Wire-to-Board Connectors, Power Connectors, RF Connectors and Optical Connectors - Independent Analysis of Annual Sales in US$ Million for the Years 2024 through 2030 and % CAGR
- TABLE 135: South Korea Historic Review for PCB Connectors by Type - Board-to-Board Connectors, Wire-to-Board Connectors, Power Connectors, RF Connectors and Optical Connectors Markets - Independent Analysis of Annual Sales in US$ Million for Years 2014 through 2023 and % CAGR
- TABLE 136: South Korea 16-Year Perspective for PCB Connectors by Type - Percentage Breakdown of Value Sales for Board-to-Board Connectors, Wire-to-Board Connectors, Power Connectors, RF Connectors and Optical Connectors for the Years 2014, 2025 & 2030
- TABLE 137: South Korea Recent Past, Current & Future Analysis for PCB Connectors by End-user - Computer & Peripherals End-User, Other End-Users, Telecom End-User, Transportation End-User, Automotive End-User and Industrial End-User - Independent Analysis of Annual Sales in US$ Million for the Years 2024 through 2030 and % CAGR
- TABLE 138: South Korea Historic Review for PCB Connectors by End-user - Computer & Peripherals End-User, Other End-Users, Telecom End-User, Transportation End-User, Automotive End-User and Industrial End-User Markets - Independent Analysis of Annual Sales in US$ Million for Years 2014 through 2023 and % CAGR
- TABLE 139: South Korea 16-Year Perspective for PCB Connectors by End-user - Percentage Breakdown of Value Sales for Computer & Peripherals End-User, Other End-Users, Telecom End-User, Transportation End-User, Automotive End-User and Industrial End-User for the Years 2014, 2025 & 2030
- REST OF ASIA-PACIFIC
- TABLE 140: Rest of Asia-Pacific Recent Past, Current & Future Analysis for PCB Connectors by Type - Board-to-Board Connectors, Wire-to-Board Connectors, Power Connectors, RF Connectors and Optical Connectors - Independent Analysis of Annual Sales in US$ Million for the Years 2024 through 2030 and % CAGR
- TABLE 141: Rest of Asia-Pacific Historic Review for PCB Connectors by Type - Board-to-Board Connectors, Wire-to-Board Connectors, Power Connectors, RF Connectors and Optical Connectors Markets - Independent Analysis of Annual Sales in US$ Million for Years 2014 through 2023 and % CAGR
- TABLE 142: Rest of Asia-Pacific 16-Year Perspective for PCB Connectors by Type - Percentage Breakdown of Value Sales for Board-to-Board Connectors, Wire-to-Board Connectors, Power Connectors, RF Connectors and Optical Connectors for the Years 2014, 2025 & 2030
- TABLE 143: Rest of Asia-Pacific Recent Past, Current & Future Analysis for PCB Connectors by End-user - Computer & Peripherals End-User, Other End-Users, Telecom End-User, Transportation End-User, Automotive End-User and Industrial End-User - Independent Analysis of Annual Sales in US$ Million for the Years 2024 through 2030 and % CAGR
- TABLE 144: Rest of Asia-Pacific Historic Review for PCB Connectors by End-user - Computer & Peripherals End-User, Other End-Users, Telecom End-User, Transportation End-User, Automotive End-User and Industrial End-User Markets - Independent Analysis of Annual Sales in US$ Million for Years 2014 through 2023 and % CAGR
- TABLE 145: Rest of Asia-Pacific 16-Year Perspective for PCB Connectors by End-user - Percentage Breakdown of Value Sales for Computer & Peripherals End-User, Other End-Users, Telecom End-User, Transportation End-User, Automotive End-User and Industrial End-User for the Years 2014, 2025 & 2030
- LATIN AMERICA
- PCB Connectors Market Presence - Strong/Active/Niche/Trivial - Key Competitors in Latin America for 2025 (E)
- TABLE 146: Latin America Recent Past, Current & Future Analysis for PCB Connectors by Geographic Region - Argentina, Brazil, Mexico and Rest of Latin America Markets - Independent Analysis of Annual Sales in US$ Million for Years 2024 through 2030 and % CAGR
- TABLE 147: Latin America Historic Review for PCB Connectors by Geographic Region - Argentina, Brazil, Mexico and Rest of Latin America Markets - Independent Analysis of Annual Sales in US$ Million for Years 2014 through 2023 and % CAGR
- TABLE 148: Latin America 16-Year Perspective for PCB Connectors by Geographic Region - Percentage Breakdown of Value Sales for Argentina, Brazil, Mexico and Rest of Latin America Markets for Years 2014, 2025 & 2030
- TABLE 149: Latin America Recent Past, Current & Future Analysis for PCB Connectors by Type - Board-to-Board Connectors, Wire-to-Board Connectors, Power Connectors, RF Connectors and Optical Connectors - Independent Analysis of Annual Sales in US$ Million for the Years 2024 through 2030 and % CAGR
- TABLE 150: Latin America Historic Review for PCB Connectors by Type - Board-to-Board Connectors, Wire-to-Board Connectors, Power Connectors, RF Connectors and Optical Connectors Markets - Independent Analysis of Annual Sales in US$ Million for Years 2014 through 2023 and % CAGR
- TABLE 151: Latin America 16-Year Perspective for PCB Connectors by Type - Percentage Breakdown of Value Sales for Board-to-Board Connectors, Wire-to-Board Connectors, Power Connectors, RF Connectors and Optical Connectors for the Years 2014, 2025 & 2030
- TABLE 152: Latin America Recent Past, Current & Future Analysis for PCB Connectors by End-user - Computer & Peripherals End-User, Other End-Users, Telecom End-User, Transportation End-User, Automotive End-User and Industrial End-User - Independent Analysis of Annual Sales in US$ Million for the Years 2024 through 2030 and % CAGR
- TABLE 153: Latin America Historic Review for PCB Connectors by End-user - Computer & Peripherals End-User, Other End-Users, Telecom End-User, Transportation End-User, Automotive End-User and Industrial End-User Markets - Independent Analysis of Annual Sales in US$ Million for Years 2014 through 2023 and % CAGR
- TABLE 154: Latin America 16-Year Perspective for PCB Connectors by End-user - Percentage Breakdown of Value Sales for Computer & Peripherals End-User, Other End-Users, Telecom End-User, Transportation End-User, Automotive End-User and Industrial End-User for the Years 2014, 2025 & 2030
- ARGENTINA
- TABLE 155: Argentina Recent Past, Current & Future Analysis for PCB Connectors by Type - Board-to-Board Connectors, Wire-to-Board Connectors, Power Connectors, RF Connectors and Optical Connectors - Independent Analysis of Annual Sales in US$ Million for the Years 2024 through 2030 and % CAGR
- TABLE 156: Argentina Historic Review for PCB Connectors by Type - Board-to-Board Connectors, Wire-to-Board Connectors, Power Connectors, RF Connectors and Optical Connectors Markets - Independent Analysis of Annual Sales in US$ Million for Years 2014 through 2023 and % CAGR
- TABLE 157: Argentina 16-Year Perspective for PCB Connectors by Type - Percentage Breakdown of Value Sales for Board-to-Board Connectors, Wire-to-Board Connectors, Power Connectors, RF Connectors and Optical Connectors for the Years 2014, 2025 & 2030
- TABLE 158: Argentina Recent Past, Current & Future Analysis for PCB Connectors by End-user - Computer & Peripherals End-User, Other End-Users, Telecom End-User, Transportation End-User, Automotive End-User and Industrial End-User - Independent Analysis of Annual Sales in US$ Million for the Years 2024 through 2030 and % CAGR
- TABLE 159: Argentina Historic Review for PCB Connectors by End-user - Computer & Peripherals End-User, Other End-Users, Telecom End-User, Transportation End-User, Automotive End-User and Industrial End-User Markets - Independent Analysis of Annual Sales in US$ Million for Years 2014 through 2023 and % CAGR
- TABLE 160: Argentina 16-Year Perspective for PCB Connectors by End-user - Percentage Breakdown of Value Sales for Computer & Peripherals End-User, Other End-Users, Telecom End-User, Transportation End-User, Automotive End-User and Industrial End-User for the Years 2014, 2025 & 2030
- BRAZIL
- TABLE 161: Brazil Recent Past, Current & Future Analysis for PCB Connectors by Type - Board-to-Board Connectors, Wire-to-Board Connectors, Power Connectors, RF Connectors and Optical Connectors - Independent Analysis of Annual Sales in US$ Million for the Years 2024 through 2030 and % CAGR
- TABLE 162: Brazil Historic Review for PCB Connectors by Type - Board-to-Board Connectors, Wire-to-Board Connectors, Power Connectors, RF Connectors and Optical Connectors Markets - Independent Analysis of Annual Sales in US$ Million for Years 2014 through 2023 and % CAGR
- TABLE 163: Brazil 16-Year Perspective for PCB Connectors by Type - Percentage Breakdown of Value Sales for Board-to-Board Connectors, Wire-to-Board Connectors, Power Connectors, RF Connectors and Optical Connectors for the Years 2014, 2025 & 2030
- TABLE 164: Brazil Recent Past, Current & Future Analysis for PCB Connectors by End-user - Computer & Peripherals End-User, Other End-Users, Telecom End-User, Transportation End-User, Automotive End-User and Industrial End-User - Independent Analysis of Annual Sales in US$ Million for the Years 2024 through 2030 and % CAGR
- TABLE 165: Brazil Historic Review for PCB Connectors by End-user - Computer & Peripherals End-User, Other End-Users, Telecom End-User, Transportation End-User, Automotive End-User and Industrial End-User Markets - Independent Analysis of Annual Sales in US$ Million for Years 2014 through 2023 and % CAGR
- TABLE 166: Brazil 16-Year Perspective for PCB Connectors by End-user - Percentage Breakdown of Value Sales for Computer & Peripherals End-User, Other End-Users, Telecom End-User, Transportation End-User, Automotive End-User and Industrial End-User for the Years 2014, 2025 & 2030
- MEXICO
- TABLE 167: Mexico Recent Past, Current & Future Analysis for PCB Connectors by Type - Board-to-Board Connectors, Wire-to-Board Connectors, Power Connectors, RF Connectors and Optical Connectors - Independent Analysis of Annual Sales in US$ Million for the Years 2024 through 2030 and % CAGR
- TABLE 168: Mexico Historic Review for PCB Connectors by Type - Board-to-Board Connectors, Wire-to-Board Connectors, Power Connectors, RF Connectors and Optical Connectors Markets - Independent Analysis of Annual Sales in US$ Million for Years 2014 through 2023 and % CAGR
- TABLE 169: Mexico 16-Year Perspective for PCB Connectors by Type - Percentage Breakdown of Value Sales for Board-to-Board Connectors, Wire-to-Board Connectors, Power Connectors, RF Connectors and Optical Connectors for the Years 2014, 2025 & 2030
- TABLE 170: Mexico Recent Past, Current & Future Analysis for PCB Connectors by End-user - Computer & Peripherals End-User, Other End-Users, Telecom End-User, Transportation End-User, Automotive End-User and Industrial End-User - Independent Analysis of Annual Sales in US$ Million for the Years 2024 through 2030 and % CAGR
- TABLE 171: Mexico Historic Review for PCB Connectors by End-user - Computer & Peripherals End-User, Other End-Users, Telecom End-User, Transportation End-User, Automotive End-User and Industrial End-User Markets - Independent Analysis of Annual Sales in US$ Million for Years 2014 through 2023 and % CAGR
- TABLE 172: Mexico 16-Year Perspective for PCB Connectors by End-user - Percentage Breakdown of Value Sales for Computer & Peripherals End-User, Other End-Users, Telecom End-User, Transportation End-User, Automotive End-User and Industrial End-User for the Years 2014, 2025 & 2030
- REST OF LATIN AMERICA
- TABLE 173: Rest of Latin America Recent Past, Current & Future Analysis for PCB Connectors by Type - Board-to-Board Connectors, Wire-to-Board Connectors, Power Connectors, RF Connectors and Optical Connectors - Independent Analysis of Annual Sales in US$ Million for the Years 2024 through 2030 and % CAGR
- TABLE 174: Rest of Latin America Historic Review for PCB Connectors by Type - Board-to-Board Connectors, Wire-to-Board Connectors, Power Connectors, RF Connectors and Optical Connectors Markets - Independent Analysis of Annual Sales in US$ Million for Years 2014 through 2023 and % CAGR
- TABLE 175: Rest of Latin America 16-Year Perspective for PCB Connectors by Type - Percentage Breakdown of Value Sales for Board-to-Board Connectors, Wire-to-Board Connectors, Power Connectors, RF Connectors and Optical Connectors for the Years 2014, 2025 & 2030
- TABLE 176: Rest of Latin America Recent Past, Current & Future Analysis for PCB Connectors by End-user - Computer & Peripherals End-User, Other End-Users, Telecom End-User, Transportation End-User, Automotive End-User and Industrial End-User - Independent Analysis of Annual Sales in US$ Million for the Years 2024 through 2030 and % CAGR
- TABLE 177: Rest of Latin America Historic Review for PCB Connectors by End-user - Computer & Peripherals End-User, Other End-Users, Telecom End-User, Transportation End-User, Automotive End-User and Industrial End-User Markets - Independent Analysis of Annual Sales in US$ Million for Years 2014 through 2023 and % CAGR
- TABLE 178: Rest of Latin America 16-Year Perspective for PCB Connectors by End-user - Percentage Breakdown of Value Sales for Computer & Peripherals End-User, Other End-Users, Telecom End-User, Transportation End-User, Automotive End-User and Industrial End-User for the Years 2014, 2025 & 2030
- MIDDLE EAST
- PCB Connectors Market Presence - Strong/Active/Niche/Trivial - Key Competitors in Middle East for 2025 (E)
- TABLE 179: Middle East Recent Past, Current & Future Analysis for PCB Connectors by Geographic Region - Iran, Israel, Saudi Arabia, UAE and Rest of Middle East Markets - Independent Analysis of Annual Sales in US$ Million for Years 2024 through 2030 and % CAGR
- TABLE 180: Middle East Historic Review for PCB Connectors by Geographic Region - Iran, Israel, Saudi Arabia, UAE and Rest of Middle East Markets - Independent Analysis of Annual Sales in US$ Million for Years 2014 through 2023 and % CAGR
- TABLE 181: Middle East 16-Year Perspective for PCB Connectors by Geographic Region - Percentage Breakdown of Value Sales for Iran, Israel, Saudi Arabia, UAE and Rest of Middle East Markets for Years 2014, 2025 & 2030
- TABLE 182: Middle East Recent Past, Current & Future Analysis for PCB Connectors by Type - Board-to-Board Connectors, Wire-to-Board Connectors, Power Connectors, RF Connectors and Optical Connectors - Independent Analysis of Annual Sales in US$ Million for the Years 2024 through 2030 and % CAGR
- TABLE 183: Middle East Historic Review for PCB Connectors by Type - Board-to-Board Connectors, Wire-to-Board Connectors, Power Connectors, RF Connectors and Optical Connectors Markets - Independent Analysis of Annual Sales in US$ Million for Years 2014 through 2023 and % CAGR
- TABLE 184: Middle East 16-Year Perspective for PCB Connectors by Type - Percentage Breakdown of Value Sales for Board-to-Board Connectors, Wire-to-Board Connectors, Power Connectors, RF Connectors and Optical Connectors for the Years 2014, 2025 & 2030
- TABLE 185: Middle East Recent Past, Current & Future Analysis for PCB Connectors by End-user - Computer & Peripherals End-User, Other End-Users, Telecom End-User, Transportation End-User, Automotive End-User and Industrial End-User - Independent Analysis of Annual Sales in US$ Million for the Years 2024 through 2030 and % CAGR
- TABLE 186: Middle East Historic Review for PCB Connectors by End-user - Computer & Peripherals End-User, Other End-Users, Telecom End-User, Transportation End-User, Automotive End-User and Industrial End-User Markets - Independent Analysis of Annual Sales in US$ Million for Years 2014 through 2023 and % CAGR
- TABLE 187: Middle East 16-Year Perspective for PCB Connectors by End-user - Percentage Breakdown of Value Sales for Computer & Peripherals End-User, Other End-Users, Telecom End-User, Transportation End-User, Automotive End-User and Industrial End-User for the Years 2014, 2025 & 2030
- IRAN
- TABLE 188: Iran Recent Past, Current & Future Analysis for PCB Connectors by Type - Board-to-Board Connectors, Wire-to-Board Connectors, Power Connectors, RF Connectors and Optical Connectors - Independent Analysis of Annual Sales in US$ Million for the Years 2024 through 2030 and % CAGR
- TABLE 189: Iran Historic Review for PCB Connectors by Type - Board-to-Board Connectors, Wire-to-Board Connectors, Power Connectors, RF Connectors and Optical Connectors Markets - Independent Analysis of Annual Sales in US$ Million for Years 2014 through 2023 and % CAGR
- TABLE 190: Iran 16-Year Perspective for PCB Connectors by Type - Percentage Breakdown of Value Sales for Board-to-Board Connectors, Wire-to-Board Connectors, Power Connectors, RF Connectors and Optical Connectors for the Years 2014, 2025 & 2030
- TABLE 191: Iran Recent Past, Current & Future Analysis for PCB Connectors by End-user - Computer & Peripherals End-User, Other End-Users, Telecom End-User, Transportation End-User, Automotive End-User and Industrial End-User - Independent Analysis of Annual Sales in US$ Million for the Years 2024 through 2030 and % CAGR
- TABLE 192: Iran Historic Review for PCB Connectors by End-user - Computer & Peripherals End-User, Other End-Users, Telecom End-User, Transportation End-User, Automotive End-User and Industrial End-User Markets - Independent Analysis of Annual Sales in US$ Million for Years 2014 through 2023 and % CAGR
- TABLE 193: Iran 16-Year Perspective for PCB Connectors by End-user - Percentage Breakdown of Value Sales for Computer & Peripherals End-User, Other End-Users, Telecom End-User, Transportation End-User, Automotive End-User and Industrial End-User for the Years 2014, 2025 & 2030
- ISRAEL
- TABLE 194: Israel Recent Past, Current & Future Analysis for PCB Connectors by Type - Board-to-Board Connectors, Wire-to-Board Connectors, Power Connectors, RF Connectors and Optical Connectors - Independent Analysis of Annual Sales in US$ Million for the Years 2024 through 2030 and % CAGR
- TABLE 195: Israel Historic Review for PCB Connectors by Type - Board-to-Board Connectors, Wire-to-Board Connectors, Power Connectors, RF Connectors and Optical Connectors Markets - Independent Analysis of Annual Sales in US$ Million for Years 2014 through 2023 and % CAGR
- TABLE 196: Israel 16-Year Perspective for PCB Connectors by Type - Percentage Breakdown of Value Sales for Board-to-Board Connectors, Wire-to-Board Connectors, Power Connectors, RF Connectors and Optical Connectors for the Years 2014, 2025 & 2030
- TABLE 197: Israel Recent Past, Current & Future Analysis for PCB Connectors by End-user - Computer & Peripherals End-User, Other End-Users, Telecom End-User, Transportation End-User, Automotive End-User and Industrial End-User - Independent Analysis of Annual Sales in US$ Million for the Years 2024 through 2030 and % CAGR
- TABLE 198: Israel Historic Review for PCB Connectors by End-user - Computer & Peripherals End-User, Other End-Users, Telecom End-User, Transportation End-User, Automotive End-User and Industrial End-User Markets - Independent Analysis of Annual Sales in US$ Million for Years 2014 through 2023 and % CAGR
- TABLE 199: Israel 16-Year Perspective for PCB Connectors by End-user - Percentage Breakdown of Value Sales for Computer & Peripherals End-User, Other End-Users, Telecom End-User, Transportation End-User, Automotive End-User and Industrial End-User for the Years 2014, 2025 & 2030
- SAUDI ARABIA
- TABLE 200: Saudi Arabia Recent Past, Current & Future Analysis for PCB Connectors by Type - Board-to-Board Connectors, Wire-to-Board Connectors, Power Connectors, RF Connectors and Optical Connectors - Independent Analysis of Annual Sales in US$ Million for the Years 2024 through 2030 and % CAGR
- TABLE 201: Saudi Arabia Historic Review for PCB Connectors by Type - Board-to-Board Connectors, Wire-to-Board Connectors, Power Connectors, RF Connectors and Optical Connectors Markets - Independent Analysis of Annual Sales in US$ Million for Years 2014 through 2023 and % CAGR
- TABLE 202: Saudi Arabia 16-Year Perspective for PCB Connectors by Type - Percentage Breakdown of Value Sales for Board-to-Board Connectors, Wire-to-Board Connectors, Power Connectors, RF Connectors and Optical Connectors for the Years 2014, 2025 & 2030
- TABLE 203: Saudi Arabia Recent Past, Current & Future Analysis for PCB Connectors by End-user - Computer & Peripherals End-User, Other End-Users, Telecom End-User, Transportation End-User, Automotive End-User and Industrial End-User - Independent Analysis of Annual Sales in US$ Million for the Years 2024 through 2030 and % CAGR
- TABLE 204: Saudi Arabia Historic Review for PCB Connectors by End-user - Computer & Peripherals End-User, Other End-Users, Telecom End-User, Transportation End-User, Automotive End-User and Industrial End-User Markets - Independent Analysis of Annual Sales in US$ Million for Years 2014 through 2023 and % CAGR
- TABLE 205: Saudi Arabia 16-Year Perspective for PCB Connectors by End-user - Percentage Breakdown of Value Sales for Computer & Peripherals End-User, Other End-Users, Telecom End-User, Transportation End-User, Automotive End-User and Industrial End-User for the Years 2014, 2025 & 2030
- UNITED ARAB EMIRATES
- TABLE 206: UAE Recent Past, Current & Future Analysis for PCB Connectors by Type - Board-to-Board Connectors, Wire-to-Board Connectors, Power Connectors, RF Connectors and Optical Connectors - Independent Analysis of Annual Sales in US$ Million for the Years 2024 through 2030 and % CAGR
- TABLE 207: UAE Historic Review for PCB Connectors by Type - Board-to-Board Connectors, Wire-to-Board Connectors, Power Connectors, RF Connectors and Optical Connectors Markets - Independent Analysis of Annual Sales in US$ Million for Years 2014 through 2023 and % CAGR
- TABLE 208: UAE 16-Year Perspective for PCB Connectors by Type - Percentage Breakdown of Value Sales for Board-to-Board Connectors, Wire-to-Board Connectors, Power Connectors, RF Connectors and Optical Connectors for the Years 2014, 2025 & 2030
- TABLE 209: UAE Recent Past, Current & Future Analysis for PCB Connectors by End-user - Computer & Peripherals End-User, Other End-Users, Telecom End-User, Transportation End-User, Automotive End-User and Industrial End-User - Independent Analysis of Annual Sales in US$ Million for the Years 2024 through 2030 and % CAGR
- TABLE 210: UAE Historic Review for PCB Connectors by End-user - Computer & Peripherals End-User, Other End-Users, Telecom End-User, Transportation End-User, Automotive End-User and Industrial End-User Markets - Independent Analysis of Annual Sales in US$ Million for Years 2014 through 2023 and % CAGR
- TABLE 211: UAE 16-Year Perspective for PCB Connectors by End-user - Percentage Breakdown of Value Sales for Computer & Peripherals End-User, Other End-Users, Telecom End-User, Transportation End-User, Automotive End-User and Industrial End-User for the Years 2014, 2025 & 2030
- REST OF MIDDLE EAST
- TABLE 212: Rest of Middle East Recent Past, Current & Future Analysis for PCB Connectors by Type - Board-to-Board Connectors, Wire-to-Board Connectors, Power Connectors, RF Connectors and Optical Connectors - Independent Analysis of Annual Sales in US$ Million for the Years 2024 through 2030 and % CAGR
- TABLE 213: Rest of Middle East Historic Review for PCB Connectors by Type - Board-to-Board Connectors, Wire-to-Board Connectors, Power Connectors, RF Connectors and Optical Connectors Markets - Independent Analysis of Annual Sales in US$ Million for Years 2014 through 2023 and % CAGR
- TABLE 214: Rest of Middle East 16-Year Perspective for PCB Connectors by Type - Percentage Breakdown of Value Sales for Board-to-Board Connectors, Wire-to-Board Connectors, Power Connectors, RF Connectors and Optical Connectors for the Years 2014, 2025 & 2030
- TABLE 215: Rest of Middle East Recent Past, Current & Future Analysis for PCB Connectors by End-user - Computer & Peripherals End-User, Other End-Users, Telecom End-User, Transportation End-User, Automotive End-User and Industrial End-User - Independent Analysis of Annual Sales in US$ Million for the Years 2024 through 2030 and % CAGR
- TABLE 216: Rest of Middle East Historic Review for PCB Connectors by End-user - Computer & Peripherals End-User, Other End-Users, Telecom End-User, Transportation End-User, Automotive End-User and Industrial End-User Markets - Independent Analysis of Annual Sales in US$ Million for Years 2014 through 2023 and % CAGR
- TABLE 217: Rest of Middle East 16-Year Perspective for PCB Connectors by End-user - Percentage Breakdown of Value Sales for Computer & Peripherals End-User, Other End-Users, Telecom End-User, Transportation End-User, Automotive End-User and Industrial End-User for the Years 2014, 2025 & 2030
- AFRICA
- PCB Connectors Market Presence - Strong/Active/Niche/Trivial - Key Competitors in Africa for 2025 (E)
- TABLE 218: Africa Recent Past, Current & Future Analysis for PCB Connectors by Type - Board-to-Board Connectors, Wire-to-Board Connectors, Power Connectors, RF Connectors and Optical Connectors - Independent Analysis of Annual Sales in US$ Million for the Years 2024 through 2030 and % CAGR
- TABLE 219: Africa Historic Review for PCB Connectors by Type - Board-to-Board Connectors, Wire-to-Board Connectors, Power Connectors, RF Connectors and Optical Connectors Markets - Independent Analysis of Annual Sales in US$ Million for Years 2014 through 2023 and % CAGR
- TABLE 220: Africa 16-Year Perspective for PCB Connectors by Type - Percentage Breakdown of Value Sales for Board-to-Board Connectors, Wire-to-Board Connectors, Power Connectors, RF Connectors and Optical Connectors for the Years 2014, 2025 & 2030
- TABLE 221: Africa Recent Past, Current & Future Analysis for PCB Connectors by End-user - Computer & Peripherals End-User, Other End-Users, Telecom End-User, Transportation End-User, Automotive End-User and Industrial End-User - Independent Analysis of Annual Sales in US$ Million for the Years 2024 through 2030 and % CAGR
- TABLE 222: Africa Historic Review for PCB Connectors by End-user - Computer & Peripherals End-User, Other End-Users, Telecom End-User, Transportation End-User, Automotive End-User and Industrial End-User Markets - Independent Analysis of Annual Sales in US$ Million for Years 2014 through 2023 and % CAGR
- TABLE 223: Africa 16-Year Perspective for PCB Connectors by End-user - Percentage Breakdown of Value Sales for Computer & Peripherals End-User, Other End-Users, Telecom End-User, Transportation End-User, Automotive End-User and Industrial End-User for the Years 2014, 2025 & 2030
- IV. COMPETITION
Pricing
Currency Rates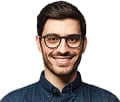