
Medical Injection Molding
Description
Global Medical Injection Molding Market to Reach US$30.4 Billion by 2030
The global market for Medical Injection Molding estimated at US$23.1 Billion in the year 2024, is expected to reach US$30.4 Billion by 2030, growing at a CAGR of 4.6% over the analysis period 2024-2030. Medical Equipment Component, one of the segments analyzed in the report, is expected to record a 6.4% CAGR and reach US$7.5 Billion by the end of the analysis period. Growth in the Consumables segment is estimated at 5.1% CAGR over the analysis period.
The U.S. Market is Estimated at US$6.3 Billion While China is Forecast to Grow at 8.7% CAGR
The Medical Injection Molding market in the U.S. is estimated at US$6.3 Billion in the year 2024. China, the world`s second largest economy, is forecast to reach a projected market size of US$6.4 Billion by the year 2030 trailing a CAGR of 8.7% over the analysis period 2024-2030. Among the other noteworthy geographic markets are Japan and Canada, each forecast to grow at a CAGR of 1.8% and 3.7% respectively over the analysis period. Within Europe, Germany is forecast to grow at approximately 2.7% CAGR.
Global Medical Injection Molding Market – Key Trends & Drivers Summarized
Is Medical Injection Molding Becoming the Backbone of High-Volume, Precision Healthcare Manufacturing?
Medical injection molding has become a fundamental process in the mass production of critical healthcare components, enabling the consistent delivery of complex, high-precision, and sterile plastic parts used across diagnostics, therapeutics, and surgical applications. Unlike general-purpose molding, medical-grade injection molding adheres to stringent regulatory, material, and process control standards. It plays an indispensable role in manufacturing components such as syringes, IV connectors, diagnostic cartridges, catheter tips, surgical instruments, dental devices, and drug delivery systems like inhalers and auto-injectors. The ability to produce millions of identical parts with micron-level accuracy, contamination-free finishes, and tight tolerances makes this process an ideal fit for healthcare. As medical devices become smaller, smarter, and more patient-centric, manufacturers are shifting towards micro-molding and multi-material molding to produce complex, multi-component devices that incorporate features such as seals, valves, embedded electronics, or flexible joints. The role of cleanroom manufacturing is also expanding, with ISO Class 7 and Class 8 environments becoming standard for high-risk applications. Medical injection molding supports lean manufacturing objectives by minimizing waste, enhancing automation, and reducing the need for secondary operations. Its scalability allows for cost-effective production across both low-volume prototyping and high-volume commercial batches. As regulatory scrutiny intensifies and OEMs demand vertically integrated partners capable of handling everything from mold design to packaging, the injection molding ecosystem is evolving into a full-service manufacturing model. This shift is not only transforming the supplier landscape but also cementing injection molding as a foundational element in the global medical device supply chain.
How Are Technological Advancements Redefining What’s Possible in Precision Medical Molding?
The medical injection molding market is undergoing a rapid transformation fueled by innovations in materials science, automation, and mold-making technologies. One of the most significant advancements is the integration of multi-shot and overmolding capabilities, which allow for the combination of multiple materials—rigid and elastomeric—in a single molding cycle. This enables the production of soft-touch components, seals, and grips that are increasingly required in wearable medical devices and ergonomic surgical instruments. Micro-injection molding is another frontier gaining traction, particularly in the production of intricate components for minimally invasive devices, microfluidic diagnostic platforms, and implantable drug delivery systems. Advanced CAD/CAM software, coupled with high-speed CNC machining, now allows for the rapid creation of complex molds with high repeatability and tighter tolerances. Meanwhile, in-mold labeling (IML), in-mold assembly, and automation-assisted mold ejection systems are reducing post-molding processing and human error. Material innovation is equally vital, with rising use of medical-grade polymers such as PEEK, polycarbonate, polypropylene, thermoplastic elastomers (TPEs), and liquid silicone rubber (LSR), which offer biocompatibility, radiation resistance, and chemical stability for various clinical environments. Furthermore, real-time monitoring and process validation technologies such as cavity pressure sensors and AI-based quality control systems are becoming indispensable for ensuring compliance with FDA, EU MDR, and ISO 13485 standards. These technical advancements are not only accelerating product development cycles but are also enabling mass customization and design freedom, ushering in a new era of precision, quality, and innovation in healthcare manufacturing.
Why Are OEMs and End-Use Segments Increasingly Relying on Injection Molding Partners?
The growing complexity of modern medical devices and the heightened expectations of healthcare providers have made injection molding a strategic priority for OEMs and end-use sectors. Device manufacturers now seek molding partners capable of managing not just fabrication but also design for manufacturability (DFM), tooling, regulatory documentation, and post-molding operations such as assembly, testing, and packaging. This full-spectrum outsourcing model is especially prevalent in the production of combination products, which merge pharmaceutical and device elements—such as prefilled syringes or inhalation systems—that require both medical-grade materials and drug-contact safe processing. The in-vitro diagnostics (IVD) segment is another major consumer, leveraging injection molding for test cartridges, reaction chambers, and disposable labware, particularly as demand surges for rapid testing platforms and point-of-care devices. Similarly, the growing popularity of home-use and wearable health monitoring devices is driving demand for lightweight, user-friendly, and high-precision plastic housings, connectors, and interfaces—all of which are manufactured through specialized injection molding techniques. Hospitals and surgical centers are also pushing for more ergonomic and single-use instruments to mitigate cross-contamination risks and reduce reprocessing costs, further expanding the market for molded disposable products. Additionally, as the medical device landscape becomes more globalized, OEMs are under pressure to localize production while maintaining consistent quality. This is giving rise to molding hubs in Asia-Pacific, Eastern Europe, and Latin America, where manufacturers are setting up ISO-certified cleanrooms to meet both regional and export demands. The shift toward integrated manufacturing and regulatory readiness is turning medical injection molding vendors into key stakeholders in the innovation and supply ecosystem of modern healthcare.
The Growth in the Medical Injection Molding Market Is Driven by Several Factors…
The growth in the medical injection molding market is driven by several factors rooted in technological progress, changing end-use requirements, and evolving procurement behaviors across healthcare systems. A primary driver is the escalating demand for miniaturized, high-precision components used in next-generation devices such as microfluidic diagnostic systems, wearable drug delivery tools, and robotic surgery accessories, all of which require advanced molding techniques like micro-injection and insert molding. From a materials perspective, the rapid development and availability of specialized medical-grade polymers that meet stringent regulatory criteria—including sterilization compatibility and drug contact safety—are significantly influencing design decisions and accelerating molding adoption. End-use sectors such as diagnostics, respiratory care, diabetes management, and minimally invasive surgery are increasingly favoring injection-molded components due to their reproducibility, low tolerances, and high-volume scalability. The shift toward point-of-care diagnostics and self-administered treatments is also creating demand for intuitive, patient-friendly devices manufactured via ergonomic and precision molding processes. On the consumer side, there is growing preference for disposable, sterile, and tamper-proof devices—especially in the wake of pandemic-era infection control protocols—which is propelling the production of single-use molded medical products. OEMs are further driving market expansion by demanding turnkey solutions from molding vendors that include mold design, simulation, regulatory documentation, and integrated post-processing. In addition, the globalization of the medical device industry and the rising participation of contract manufacturing organizations (CMOs) and private label producers are boosting production capacities and geographic reach. These factors, combined with increasing investments in cleanroom infrastructure, smart manufacturing, and automation, are positioning medical injection molding as a linchpin of scalable, compliant, and innovative healthcare product manufacturing on a global scale.
The report analyzes the Medical Injection Molding market in terms of units by the following Segments, and Geographic Regions/Countries:
Segments:
Product (Medical Equipment Component, Consumables, Patient Aids, Orthopedics Instruments, Dental Products, Others); System (Hot Runner, Cold Runner); Material (Plastics, Metals, Others)
Geographic Regions/Countries:
World; United States; Canada; Japan; China; Europe (France; Germany; Italy; United Kingdom; Spain; Russia; and Rest of Europe); Asia-Pacific (Australia; India; South Korea; and Rest of Asia-Pacific); Latin America (Argentina; Brazil; Mexico; and Rest of Latin America); Middle East (Iran; Israel; Saudi Arabia; United Arab Emirates; and Rest of Middle East); and Africa.
Select Competitors (Total 39 Featured) -
- Accumold
- Beacon MedTech Solutions
- Biomerics
- Currier Plastics
- Falcon Plastics
- Fictiv
- HTI Plastics
- Intricon Corporation
- Natech Plastics
- Nypro Healthcare
- Phillips Precision Medic
- Precision Associates
- PSN Labs
- PTI Engineered Plastics Inc.
- Sanmina Corporation
- Seaskymedical
- Spectrum Plastics Group
- TESco Associates
- Tessy Plastics
- The Rodon Group
We`re transforming market and competitive intelligence with validated expert content and AI tools.
Instead of following the general norm of querying LLMs and Industry-specific SLMs, we built repositories of content curated from domain experts worldwide including video transcripts, blogs, search engines research, and massive amounts of enterprise, product/service, and market data.
TARIFF IMPACT FACTOR
Our new release incorporates impact of tariffs on geographical markets as we predict a shift in competitiveness of companies based on HQ country, manufacturing base, exports and imports (finished goods and OEM). This intricate and multifaceted market reality will impact competitors by increasing the Cost of Goods Sold (COGS), reducing profitability, reconfiguring supply chains, amongst other micro and macro market dynamics.
Please note: Reports are sold as single-site single-user licenses. Electronic versions require 24-48 hours as each copy is customized to the client with digital controls and custom watermarks. The Publisher uses digital controls protecting against copying and printing is restricted to one full copy to be used at the same location.
The latest version of Adobe Acrobat Reader is required to view the report. Upon ordering an electronic version, the Publisher will provide a link to download the purchased report.
Prior to fulfillment of an order, the client will be required to sign a document detailing the purchase terms for a publication from this publisher.
Table of Contents
- I. METHODOLOGY
- II. EXECUTIVE SUMMARY
- 1. MARKET OVERVIEW
- Influencer Market Insights
- Tariff Impact on Global Supply Chain Patterns
- Medical Injection Molding – Global Key Competitors Percentage Market Share in 2025 (E)
- Competitive Market Presence - Strong/Active/Niche/Trivial for Players Worldwide in 2025 (E)
- 2. FOCUS ON SELECT PLAYERS
- 3. MARKET TRENDS & DRIVERS
- Rising Demand for High-Precision Medical Components Spurs Growth in Injection Molding Services
- Proliferation of Single-Use Medical Devices Expands Addressable Market for Injection Molded Products
- Increasing Preference for Miniaturized Devices Throws Spotlight on Micro-Molding Technologies
- Stringent Regulatory Requirements for Medical Plastics Strengthen Business Case for Cleanroom Molding
- Adoption of Advanced Mold Design Software Propels Innovation in Medical Component Engineering
- Expansion of Drug Delivery Devices Market Drives Demand for Molded Parts in Inhalers and Injectors
- Integration of Multi-Material Molding Techniques Accelerates Functional Product Capabilities
- Outsourcing of Manufacturing by OEMs Boosts Opportunities for Contract Injection Mold Manufacturers
- Advances in Resin Technology Expand Application Range of Molded Medical Components
- Growth in Wearable Medical Devices Spurs Use of Soft Touch and Elastomeric Injection Molding
- Rising Number of Diagnostic Consumables Drives Demand for Precision-Molded Plastics
- Focus on Sustainable Medical Manufacturing Propels Use of Recyclable and Biodegradable Resins
- Surge in Point-of-Care Testing Devices Strengthens Need for Rapid Prototyping and Low-Volume Molding
- Increased Demand for Antimicrobial and Sterile Medical Components Accelerates Specialized Molding
- Automation and Industry 4.0 Integration Enhances Productivity of Injection Molding Facilities
- Regulatory Emphasis on Traceability and Quality Assurance Drives Adoption of Smart Mold Monitoring
- Emergence of Complex Multi-Cavity Molds Supports Economies of Scale in High-Volume Production
- Innovation in Overmolding and Insert Molding Expands Functional Capabilities of Medical Products
- Medical Molding Applications in Ophthalmology and ENT Devices Drive Niche Market Growth
- Rising Demand from Asia-Pacific for Cost-Effective, Precision Molded Components Sustains Global Expansion
- 4. GLOBAL MARKET PERSPECTIVE
- TABLE 1: World Medical Injection Molding Market Analysis of Annual Sales in US$ Million for Years 2015 through 2030
- TABLE 2: World Recent Past, Current & Future Analysis for Medical Injection Molding by Geographic Region - USA, Canada, Japan, China, Europe, Asia-Pacific, Latin America, Middle East and Africa Markets - Independent Analysis of Annual Sales in US$ Million for Years 2024 through 2030 and % CAGR
- TABLE 3: World Historic Review for Medical Injection Molding by Geographic Region - USA, Canada, Japan, China, Europe, Asia-Pacific, Latin America, Middle East and Africa Markets - Independent Analysis of Annual Sales in US$ Million for Years 2015 through 2023 and % CAGR
- TABLE 4: World 15-Year Perspective for Medical Injection Molding by Geographic Region - Percentage Breakdown of Value Sales for USA, Canada, Japan, China, Europe, Asia-Pacific, Latin America, Middle East and Africa Markets for Years 2015, 2025 & 2030
- TABLE 5: World Recent Past, Current & Future Analysis for Medical Equipment Component by Geographic Region - USA, Canada, Japan, China, Europe, Asia-Pacific, Latin America, Middle East and Africa Markets - Independent Analysis of Annual Sales in US$ Million for Years 2024 through 2030 and % CAGR
- TABLE 6: World Historic Review for Medical Equipment Component by Geographic Region - USA, Canada, Japan, China, Europe, Asia-Pacific, Latin America, Middle East and Africa Markets - Independent Analysis of Annual Sales in US$ Million for Years 2015 through 2023 and % CAGR
- TABLE 7: World 15-Year Perspective for Medical Equipment Component by Geographic Region - Percentage Breakdown of Value Sales for USA, Canada, Japan, China, Europe, Asia-Pacific, Latin America, Middle East and Africa for Years 2015, 2025 & 2030
- TABLE 8: World Recent Past, Current & Future Analysis for Consumables by Geographic Region - USA, Canada, Japan, China, Europe, Asia-Pacific, Latin America, Middle East and Africa Markets - Independent Analysis of Annual Sales in US$ Million for Years 2024 through 2030 and % CAGR
- TABLE 9: World Historic Review for Consumables by Geographic Region - USA, Canada, Japan, China, Europe, Asia-Pacific, Latin America, Middle East and Africa Markets - Independent Analysis of Annual Sales in US$ Million for Years 2015 through 2023 and % CAGR
- TABLE 10: World 15-Year Perspective for Consumables by Geographic Region - Percentage Breakdown of Value Sales for USA, Canada, Japan, China, Europe, Asia-Pacific, Latin America, Middle East and Africa for Years 2015, 2025 & 2030
- TABLE 11: World Recent Past, Current & Future Analysis for Patient Aids by Geographic Region - USA, Canada, Japan, China, Europe, Asia-Pacific, Latin America, Middle East and Africa Markets - Independent Analysis of Annual Sales in US$ Million for Years 2024 through 2030 and % CAGR
- TABLE 12: World Historic Review for Patient Aids by Geographic Region - USA, Canada, Japan, China, Europe, Asia-Pacific, Latin America, Middle East and Africa Markets - Independent Analysis of Annual Sales in US$ Million for Years 2015 through 2023 and % CAGR
- TABLE 13: World 15-Year Perspective for Patient Aids by Geographic Region - Percentage Breakdown of Value Sales for USA, Canada, Japan, China, Europe, Asia-Pacific, Latin America, Middle East and Africa for Years 2015, 2025 & 2030
- TABLE 14: World Recent Past, Current & Future Analysis for Orthopedics Instruments by Geographic Region - USA, Canada, Japan, China, Europe, Asia-Pacific, Latin America, Middle East and Africa Markets - Independent Analysis of Annual Sales in US$ Million for Years 2024 through 2030 and % CAGR
- TABLE 15: World Historic Review for Orthopedics Instruments by Geographic Region - USA, Canada, Japan, China, Europe, Asia-Pacific, Latin America, Middle East and Africa Markets - Independent Analysis of Annual Sales in US$ Million for Years 2015 through 2023 and % CAGR
- TABLE 16: World 15-Year Perspective for Orthopedics Instruments by Geographic Region - Percentage Breakdown of Value Sales for USA, Canada, Japan, China, Europe, Asia-Pacific, Latin America, Middle East and Africa for Years 2015, 2025 & 2030
- TABLE 17: World Recent Past, Current & Future Analysis for Dental Products by Geographic Region - USA, Canada, Japan, China, Europe, Asia-Pacific, Latin America, Middle East and Africa Markets - Independent Analysis of Annual Sales in US$ Million for Years 2024 through 2030 and % CAGR
- TABLE 18: World Historic Review for Dental Products by Geographic Region - USA, Canada, Japan, China, Europe, Asia-Pacific, Latin America, Middle East and Africa Markets - Independent Analysis of Annual Sales in US$ Million for Years 2015 through 2023 and % CAGR
- TABLE 19: World 15-Year Perspective for Dental Products by Geographic Region - Percentage Breakdown of Value Sales for USA, Canada, Japan, China, Europe, Asia-Pacific, Latin America, Middle East and Africa for Years 2015, 2025 & 2030
- TABLE 20: World Recent Past, Current & Future Analysis for Other Products by Geographic Region - USA, Canada, Japan, China, Europe, Asia-Pacific, Latin America, Middle East and Africa Markets - Independent Analysis of Annual Sales in US$ Million for Years 2024 through 2030 and % CAGR
- TABLE 21: World Historic Review for Other Products by Geographic Region - USA, Canada, Japan, China, Europe, Asia-Pacific, Latin America, Middle East and Africa Markets - Independent Analysis of Annual Sales in US$ Million for Years 2015 through 2023 and % CAGR
- TABLE 22: World 15-Year Perspective for Other Products by Geographic Region - Percentage Breakdown of Value Sales for USA, Canada, Japan, China, Europe, Asia-Pacific, Latin America, Middle East and Africa for Years 2015, 2025 & 2030
- TABLE 23: World Recent Past, Current & Future Analysis for Metals by Geographic Region - USA, Canada, Japan, China, Europe, Asia-Pacific, Latin America, Middle East and Africa Markets - Independent Analysis of Annual Sales in US$ Million for Years 2024 through 2030 and % CAGR
- TABLE 24: World Historic Review for Metals by Geographic Region - USA, Canada, Japan, China, Europe, Asia-Pacific, Latin America, Middle East and Africa Markets - Independent Analysis of Annual Sales in US$ Million for Years 2015 through 2023 and % CAGR
- TABLE 25: World 15-Year Perspective for Metals by Geographic Region - Percentage Breakdown of Value Sales for USA, Canada, Japan, China, Europe, Asia-Pacific, Latin America, Middle East and Africa for Years 2015, 2025 & 2030
- TABLE 26: World Recent Past, Current & Future Analysis for Other Materials by Geographic Region - USA, Canada, Japan, China, Europe, Asia-Pacific, Latin America, Middle East and Africa Markets - Independent Analysis of Annual Sales in US$ Million for Years 2024 through 2030 and % CAGR
- TABLE 27: World Historic Review for Other Materials by Geographic Region - USA, Canada, Japan, China, Europe, Asia-Pacific, Latin America, Middle East and Africa Markets - Independent Analysis of Annual Sales in US$ Million for Years 2015 through 2023 and % CAGR
- TABLE 28: World 15-Year Perspective for Other Materials by Geographic Region - Percentage Breakdown of Value Sales for USA, Canada, Japan, China, Europe, Asia-Pacific, Latin America, Middle East and Africa for Years 2015, 2025 & 2030
- TABLE 29: World Recent Past, Current & Future Analysis for Plastics by Geographic Region - USA, Canada, Japan, China, Europe, Asia-Pacific, Latin America, Middle East and Africa Markets - Independent Analysis of Annual Sales in US$ Million for Years 2024 through 2030 and % CAGR
- TABLE 30: World Historic Review for Plastics by Geographic Region - USA, Canada, Japan, China, Europe, Asia-Pacific, Latin America, Middle East and Africa Markets - Independent Analysis of Annual Sales in US$ Million for Years 2015 through 2023 and % CAGR
- TABLE 31: World 15-Year Perspective for Plastics by Geographic Region - Percentage Breakdown of Value Sales for USA, Canada, Japan, China, Europe, Asia-Pacific, Latin America, Middle East and Africa for Years 2015, 2025 & 2030
- TABLE 32: World Recent Past, Current & Future Analysis for Hot Runner by Geographic Region - USA, Canada, Japan, China, Europe, Asia-Pacific, Latin America, Middle East and Africa Markets - Independent Analysis of Annual Sales in US$ Million for Years 2024 through 2030 and % CAGR
- TABLE 33: World Historic Review for Hot Runner by Geographic Region - USA, Canada, Japan, China, Europe, Asia-Pacific, Latin America, Middle East and Africa Markets - Independent Analysis of Annual Sales in US$ Million for Years 2015 through 2023 and % CAGR
- TABLE 34: World 15-Year Perspective for Hot Runner by Geographic Region - Percentage Breakdown of Value Sales for USA, Canada, Japan, China, Europe, Asia-Pacific, Latin America, Middle East and Africa for Years 2015, 2025 & 2030
- TABLE 35: World Recent Past, Current & Future Analysis for Cold Runner by Geographic Region - USA, Canada, Japan, China, Europe, Asia-Pacific, Latin America, Middle East and Africa Markets - Independent Analysis of Annual Sales in US$ Million for Years 2024 through 2030 and % CAGR
- TABLE 36: World Historic Review for Cold Runner by Geographic Region - USA, Canada, Japan, China, Europe, Asia-Pacific, Latin America, Middle East and Africa Markets - Independent Analysis of Annual Sales in US$ Million for Years 2015 through 2023 and % CAGR
- TABLE 37: World 15-Year Perspective for Cold Runner by Geographic Region - Percentage Breakdown of Value Sales for USA, Canada, Japan, China, Europe, Asia-Pacific, Latin America, Middle East and Africa for Years 2015, 2025 & 2030
- III. MARKET ANALYSIS
- UNITED STATES
- Medical Injection Molding Market Presence - Strong/Active/Niche/Trivial - Key Competitors in the United States for 2025 (E)
- TABLE 38: USA Recent Past, Current & Future Analysis for Medical Injection Molding by Product - Medical Equipment Component, Consumables, Patient Aids, Orthopedics Instruments, Dental Products and Other Products - Independent Analysis of Annual Sales in US$ Million for the Years 2024 through 2030 and % CAGR
- TABLE 39: USA Historic Review for Medical Injection Molding by Product - Medical Equipment Component, Consumables, Patient Aids, Orthopedics Instruments, Dental Products and Other Products Markets - Independent Analysis of Annual Sales in US$ Million for Years 2015 through 2023 and % CAGR
- TABLE 40: USA 15-Year Perspective for Medical Injection Molding by Product - Percentage Breakdown of Value Sales for Medical Equipment Component, Consumables, Patient Aids, Orthopedics Instruments, Dental Products and Other Products for the Years 2015, 2025 & 2030
- TABLE 41: USA Recent Past, Current & Future Analysis for Medical Injection Molding by Material - Metals, Other Materials and Plastics - Independent Analysis of Annual Sales in US$ Million for the Years 2024 through 2030 and % CAGR
- TABLE 42: USA Historic Review for Medical Injection Molding by Material - Metals, Other Materials and Plastics Markets - Independent Analysis of Annual Sales in US$ Million for Years 2015 through 2023 and % CAGR
- TABLE 43: USA 15-Year Perspective for Medical Injection Molding by Material - Percentage Breakdown of Value Sales for Metals, Other Materials and Plastics for the Years 2015, 2025 & 2030
- TABLE 44: USA Recent Past, Current & Future Analysis for Medical Injection Molding by System - Hot Runner and Cold Runner - Independent Analysis of Annual Sales in US$ Million for the Years 2024 through 2030 and % CAGR
- TABLE 45: USA Historic Review for Medical Injection Molding by System - Hot Runner and Cold Runner Markets - Independent Analysis of Annual Sales in US$ Million for Years 2015 through 2023 and % CAGR
- TABLE 46: USA 15-Year Perspective for Medical Injection Molding by System - Percentage Breakdown of Value Sales for Hot Runner and Cold Runner for the Years 2015, 2025 & 2030
- CANADA
- TABLE 47: Canada Recent Past, Current & Future Analysis for Medical Injection Molding by Product - Medical Equipment Component, Consumables, Patient Aids, Orthopedics Instruments, Dental Products and Other Products - Independent Analysis of Annual Sales in US$ Million for the Years 2024 through 2030 and % CAGR
- TABLE 48: Canada Historic Review for Medical Injection Molding by Product - Medical Equipment Component, Consumables, Patient Aids, Orthopedics Instruments, Dental Products and Other Products Markets - Independent Analysis of Annual Sales in US$ Million for Years 2015 through 2023 and % CAGR
- TABLE 49: Canada 15-Year Perspective for Medical Injection Molding by Product - Percentage Breakdown of Value Sales for Medical Equipment Component, Consumables, Patient Aids, Orthopedics Instruments, Dental Products and Other Products for the Years 2015, 2025 & 2030
- TABLE 50: Canada Recent Past, Current & Future Analysis for Medical Injection Molding by Material - Metals, Other Materials and Plastics - Independent Analysis of Annual Sales in US$ Million for the Years 2024 through 2030 and % CAGR
- TABLE 51: Canada Historic Review for Medical Injection Molding by Material - Metals, Other Materials and Plastics Markets - Independent Analysis of Annual Sales in US$ Million for Years 2015 through 2023 and % CAGR
- TABLE 52: Canada 15-Year Perspective for Medical Injection Molding by Material - Percentage Breakdown of Value Sales for Metals, Other Materials and Plastics for the Years 2015, 2025 & 2030
- TABLE 53: Canada Recent Past, Current & Future Analysis for Medical Injection Molding by System - Hot Runner and Cold Runner - Independent Analysis of Annual Sales in US$ Million for the Years 2024 through 2030 and % CAGR
- TABLE 54: Canada Historic Review for Medical Injection Molding by System - Hot Runner and Cold Runner Markets - Independent Analysis of Annual Sales in US$ Million for Years 2015 through 2023 and % CAGR
- TABLE 55: Canada 15-Year Perspective for Medical Injection Molding by System - Percentage Breakdown of Value Sales for Hot Runner and Cold Runner for the Years 2015, 2025 & 2030
- JAPAN
- Medical Injection Molding Market Presence - Strong/Active/Niche/Trivial - Key Competitors in Japan for 2025 (E)
- TABLE 56: Japan Recent Past, Current & Future Analysis for Medical Injection Molding by Product - Medical Equipment Component, Consumables, Patient Aids, Orthopedics Instruments, Dental Products and Other Products - Independent Analysis of Annual Sales in US$ Million for the Years 2024 through 2030 and % CAGR
- TABLE 57: Japan Historic Review for Medical Injection Molding by Product - Medical Equipment Component, Consumables, Patient Aids, Orthopedics Instruments, Dental Products and Other Products Markets - Independent Analysis of Annual Sales in US$ Million for Years 2015 through 2023 and % CAGR
- TABLE 58: Japan 15-Year Perspective for Medical Injection Molding by Product - Percentage Breakdown of Value Sales for Medical Equipment Component, Consumables, Patient Aids, Orthopedics Instruments, Dental Products and Other Products for the Years 2015, 2025 & 2030
- TABLE 59: Japan Recent Past, Current & Future Analysis for Medical Injection Molding by Material - Metals, Other Materials and Plastics - Independent Analysis of Annual Sales in US$ Million for the Years 2024 through 2030 and % CAGR
- TABLE 60: Japan Historic Review for Medical Injection Molding by Material - Metals, Other Materials and Plastics Markets - Independent Analysis of Annual Sales in US$ Million for Years 2015 through 2023 and % CAGR
- TABLE 61: Japan 15-Year Perspective for Medical Injection Molding by Material - Percentage Breakdown of Value Sales for Metals, Other Materials and Plastics for the Years 2015, 2025 & 2030
- TABLE 62: Japan Recent Past, Current & Future Analysis for Medical Injection Molding by System - Hot Runner and Cold Runner - Independent Analysis of Annual Sales in US$ Million for the Years 2024 through 2030 and % CAGR
- TABLE 63: Japan Historic Review for Medical Injection Molding by System - Hot Runner and Cold Runner Markets - Independent Analysis of Annual Sales in US$ Million for Years 2015 through 2023 and % CAGR
- TABLE 64: Japan 15-Year Perspective for Medical Injection Molding by System - Percentage Breakdown of Value Sales for Hot Runner and Cold Runner for the Years 2015, 2025 & 2030
- CHINA
- Medical Injection Molding Market Presence - Strong/Active/Niche/Trivial - Key Competitors in China for 2025 (E)
- TABLE 65: China Recent Past, Current & Future Analysis for Medical Injection Molding by Product - Medical Equipment Component, Consumables, Patient Aids, Orthopedics Instruments, Dental Products and Other Products - Independent Analysis of Annual Sales in US$ Million for the Years 2024 through 2030 and % CAGR
- TABLE 66: China Historic Review for Medical Injection Molding by Product - Medical Equipment Component, Consumables, Patient Aids, Orthopedics Instruments, Dental Products and Other Products Markets - Independent Analysis of Annual Sales in US$ Million for Years 2015 through 2023 and % CAGR
- TABLE 67: China 15-Year Perspective for Medical Injection Molding by Product - Percentage Breakdown of Value Sales for Medical Equipment Component, Consumables, Patient Aids, Orthopedics Instruments, Dental Products and Other Products for the Years 2015, 2025 & 2030
- TABLE 68: China Recent Past, Current & Future Analysis for Medical Injection Molding by Material - Metals, Other Materials and Plastics - Independent Analysis of Annual Sales in US$ Million for the Years 2024 through 2030 and % CAGR
- TABLE 69: China Historic Review for Medical Injection Molding by Material - Metals, Other Materials and Plastics Markets - Independent Analysis of Annual Sales in US$ Million for Years 2015 through 2023 and % CAGR
- TABLE 70: China 15-Year Perspective for Medical Injection Molding by Material - Percentage Breakdown of Value Sales for Metals, Other Materials and Plastics for the Years 2015, 2025 & 2030
- TABLE 71: China Recent Past, Current & Future Analysis for Medical Injection Molding by System - Hot Runner and Cold Runner - Independent Analysis of Annual Sales in US$ Million for the Years 2024 through 2030 and % CAGR
- TABLE 72: China Historic Review for Medical Injection Molding by System - Hot Runner and Cold Runner Markets - Independent Analysis of Annual Sales in US$ Million for Years 2015 through 2023 and % CAGR
- TABLE 73: China 15-Year Perspective for Medical Injection Molding by System - Percentage Breakdown of Value Sales for Hot Runner and Cold Runner for the Years 2015, 2025 & 2030
- EUROPE
- Medical Injection Molding Market Presence - Strong/Active/Niche/Trivial - Key Competitors in Europe for 2025 (E)
- TABLE 74: Europe Recent Past, Current & Future Analysis for Medical Injection Molding by Geographic Region - France, Germany, Italy, UK, Spain, Russia and Rest of Europe Markets - Independent Analysis of Annual Sales in US$ Million for Years 2024 through 2030 and % CAGR
- TABLE 75: Europe Historic Review for Medical Injection Molding by Geographic Region - France, Germany, Italy, UK, Spain, Russia and Rest of Europe Markets - Independent Analysis of Annual Sales in US$ Million for Years 2015 through 2023 and % CAGR
- TABLE 76: Europe 15-Year Perspective for Medical Injection Molding by Geographic Region - Percentage Breakdown of Value Sales for France, Germany, Italy, UK, Spain, Russia and Rest of Europe Markets for Years 2015, 2025 & 2030
- TABLE 77: Europe Recent Past, Current & Future Analysis for Medical Injection Molding by Product - Medical Equipment Component, Consumables, Patient Aids, Orthopedics Instruments, Dental Products and Other Products - Independent Analysis of Annual Sales in US$ Million for the Years 2024 through 2030 and % CAGR
- TABLE 78: Europe Historic Review for Medical Injection Molding by Product - Medical Equipment Component, Consumables, Patient Aids, Orthopedics Instruments, Dental Products and Other Products Markets - Independent Analysis of Annual Sales in US$ Million for Years 2015 through 2023 and % CAGR
- TABLE 79: Europe 15-Year Perspective for Medical Injection Molding by Product - Percentage Breakdown of Value Sales for Medical Equipment Component, Consumables, Patient Aids, Orthopedics Instruments, Dental Products and Other Products for the Years 2015, 2025 & 2030
- TABLE 80: Europe Recent Past, Current & Future Analysis for Medical Injection Molding by Material - Metals, Other Materials and Plastics - Independent Analysis of Annual Sales in US$ Million for the Years 2024 through 2030 and % CAGR
- TABLE 81: Europe Historic Review for Medical Injection Molding by Material - Metals, Other Materials and Plastics Markets - Independent Analysis of Annual Sales in US$ Million for Years 2015 through 2023 and % CAGR
- TABLE 82: Europe 15-Year Perspective for Medical Injection Molding by Material - Percentage Breakdown of Value Sales for Metals, Other Materials and Plastics for the Years 2015, 2025 & 2030
- TABLE 83: Europe Recent Past, Current & Future Analysis for Medical Injection Molding by System - Hot Runner and Cold Runner - Independent Analysis of Annual Sales in US$ Million for the Years 2024 through 2030 and % CAGR
- TABLE 84: Europe Historic Review for Medical Injection Molding by System - Hot Runner and Cold Runner Markets - Independent Analysis of Annual Sales in US$ Million for Years 2015 through 2023 and % CAGR
- TABLE 85: Europe 15-Year Perspective for Medical Injection Molding by System - Percentage Breakdown of Value Sales for Hot Runner and Cold Runner for the Years 2015, 2025 & 2030
- FRANCE
- Medical Injection Molding Market Presence - Strong/Active/Niche/Trivial - Key Competitors in France for 2025 (E)
- TABLE 86: France Recent Past, Current & Future Analysis for Medical Injection Molding by Product - Medical Equipment Component, Consumables, Patient Aids, Orthopedics Instruments, Dental Products and Other Products - Independent Analysis of Annual Sales in US$ Million for the Years 2024 through 2030 and % CAGR
- TABLE 87: France Historic Review for Medical Injection Molding by Product - Medical Equipment Component, Consumables, Patient Aids, Orthopedics Instruments, Dental Products and Other Products Markets - Independent Analysis of Annual Sales in US$ Million for Years 2015 through 2023 and % CAGR
- TABLE 88: France 15-Year Perspective for Medical Injection Molding by Product - Percentage Breakdown of Value Sales for Medical Equipment Component, Consumables, Patient Aids, Orthopedics Instruments, Dental Products and Other Products for the Years 2015, 2025 & 2030
- TABLE 89: France Recent Past, Current & Future Analysis for Medical Injection Molding by Material - Metals, Other Materials and Plastics - Independent Analysis of Annual Sales in US$ Million for the Years 2024 through 2030 and % CAGR
- TABLE 90: France Historic Review for Medical Injection Molding by Material - Metals, Other Materials and Plastics Markets - Independent Analysis of Annual Sales in US$ Million for Years 2015 through 2023 and % CAGR
- TABLE 91: France 15-Year Perspective for Medical Injection Molding by Material - Percentage Breakdown of Value Sales for Metals, Other Materials and Plastics for the Years 2015, 2025 & 2030
- TABLE 92: France Recent Past, Current & Future Analysis for Medical Injection Molding by System - Hot Runner and Cold Runner - Independent Analysis of Annual Sales in US$ Million for the Years 2024 through 2030 and % CAGR
- TABLE 93: France Historic Review for Medical Injection Molding by System - Hot Runner and Cold Runner Markets - Independent Analysis of Annual Sales in US$ Million for Years 2015 through 2023 and % CAGR
- TABLE 94: France 15-Year Perspective for Medical Injection Molding by System - Percentage Breakdown of Value Sales for Hot Runner and Cold Runner for the Years 2015, 2025 & 2030
- GERMANY
- Medical Injection Molding Market Presence - Strong/Active/Niche/Trivial - Key Competitors in Germany for 2025 (E)
- TABLE 95: Germany Recent Past, Current & Future Analysis for Medical Injection Molding by Product - Medical Equipment Component, Consumables, Patient Aids, Orthopedics Instruments, Dental Products and Other Products - Independent Analysis of Annual Sales in US$ Million for the Years 2024 through 2030 and % CAGR
- TABLE 96: Germany Historic Review for Medical Injection Molding by Product - Medical Equipment Component, Consumables, Patient Aids, Orthopedics Instruments, Dental Products and Other Products Markets - Independent Analysis of Annual Sales in US$ Million for Years 2015 through 2023 and % CAGR
- TABLE 97: Germany 15-Year Perspective for Medical Injection Molding by Product - Percentage Breakdown of Value Sales for Medical Equipment Component, Consumables, Patient Aids, Orthopedics Instruments, Dental Products and Other Products for the Years 2015, 2025 & 2030
- TABLE 98: Germany Recent Past, Current & Future Analysis for Medical Injection Molding by Material - Metals, Other Materials and Plastics - Independent Analysis of Annual Sales in US$ Million for the Years 2024 through 2030 and % CAGR
- TABLE 99: Germany Historic Review for Medical Injection Molding by Material - Metals, Other Materials and Plastics Markets - Independent Analysis of Annual Sales in US$ Million for Years 2015 through 2023 and % CAGR
- TABLE 100: Germany 15-Year Perspective for Medical Injection Molding by Material - Percentage Breakdown of Value Sales for Metals, Other Materials and Plastics for the Years 2015, 2025 & 2030
- TABLE 101: Germany Recent Past, Current & Future Analysis for Medical Injection Molding by System - Hot Runner and Cold Runner - Independent Analysis of Annual Sales in US$ Million for the Years 2024 through 2030 and % CAGR
- TABLE 102: Germany Historic Review for Medical Injection Molding by System - Hot Runner and Cold Runner Markets - Independent Analysis of Annual Sales in US$ Million for Years 2015 through 2023 and % CAGR
- TABLE 103: Germany 15-Year Perspective for Medical Injection Molding by System - Percentage Breakdown of Value Sales for Hot Runner and Cold Runner for the Years 2015, 2025 & 2030
- ITALY
- TABLE 104: Italy Recent Past, Current & Future Analysis for Medical Injection Molding by Product - Medical Equipment Component, Consumables, Patient Aids, Orthopedics Instruments, Dental Products and Other Products - Independent Analysis of Annual Sales in US$ Million for the Years 2024 through 2030 and % CAGR
- TABLE 105: Italy Historic Review for Medical Injection Molding by Product - Medical Equipment Component, Consumables, Patient Aids, Orthopedics Instruments, Dental Products and Other Products Markets - Independent Analysis of Annual Sales in US$ Million for Years 2015 through 2023 and % CAGR
- TABLE 106: Italy 15-Year Perspective for Medical Injection Molding by Product - Percentage Breakdown of Value Sales for Medical Equipment Component, Consumables, Patient Aids, Orthopedics Instruments, Dental Products and Other Products for the Years 2015, 2025 & 2030
- TABLE 107: Italy Recent Past, Current & Future Analysis for Medical Injection Molding by Material - Metals, Other Materials and Plastics - Independent Analysis of Annual Sales in US$ Million for the Years 2024 through 2030 and % CAGR
- TABLE 108: Italy Historic Review for Medical Injection Molding by Material - Metals, Other Materials and Plastics Markets - Independent Analysis of Annual Sales in US$ Million for Years 2015 through 2023 and % CAGR
- TABLE 109: Italy 15-Year Perspective for Medical Injection Molding by Material - Percentage Breakdown of Value Sales for Metals, Other Materials and Plastics for the Years 2015, 2025 & 2030
- TABLE 110: Italy Recent Past, Current & Future Analysis for Medical Injection Molding by System - Hot Runner and Cold Runner - Independent Analysis of Annual Sales in US$ Million for the Years 2024 through 2030 and % CAGR
- TABLE 111: Italy Historic Review for Medical Injection Molding by System - Hot Runner and Cold Runner Markets - Independent Analysis of Annual Sales in US$ Million for Years 2015 through 2023 and % CAGR
- TABLE 112: Italy 15-Year Perspective for Medical Injection Molding by System - Percentage Breakdown of Value Sales for Hot Runner and Cold Runner for the Years 2015, 2025 & 2030
- UNITED KINGDOM
- Medical Injection Molding Market Presence - Strong/Active/Niche/Trivial - Key Competitors in the United Kingdom for 2025 (E)
- TABLE 113: UK Recent Past, Current & Future Analysis for Medical Injection Molding by Product - Medical Equipment Component, Consumables, Patient Aids, Orthopedics Instruments, Dental Products and Other Products - Independent Analysis of Annual Sales in US$ Million for the Years 2024 through 2030 and % CAGR
- TABLE 114: UK Historic Review for Medical Injection Molding by Product - Medical Equipment Component, Consumables, Patient Aids, Orthopedics Instruments, Dental Products and Other Products Markets - Independent Analysis of Annual Sales in US$ Million for Years 2015 through 2023 and % CAGR
- TABLE 115: UK 15-Year Perspective for Medical Injection Molding by Product - Percentage Breakdown of Value Sales for Medical Equipment Component, Consumables, Patient Aids, Orthopedics Instruments, Dental Products and Other Products for the Years 2015, 2025 & 2030
- TABLE 116: UK Recent Past, Current & Future Analysis for Medical Injection Molding by Material - Metals, Other Materials and Plastics - Independent Analysis of Annual Sales in US$ Million for the Years 2024 through 2030 and % CAGR
- TABLE 117: UK Historic Review for Medical Injection Molding by Material - Metals, Other Materials and Plastics Markets - Independent Analysis of Annual Sales in US$ Million for Years 2015 through 2023 and % CAGR
- TABLE 118: UK 15-Year Perspective for Medical Injection Molding by Material - Percentage Breakdown of Value Sales for Metals, Other Materials and Plastics for the Years 2015, 2025 & 2030
- TABLE 119: UK Recent Past, Current & Future Analysis for Medical Injection Molding by System - Hot Runner and Cold Runner - Independent Analysis of Annual Sales in US$ Million for the Years 2024 through 2030 and % CAGR
- TABLE 120: UK Historic Review for Medical Injection Molding by System - Hot Runner and Cold Runner Markets - Independent Analysis of Annual Sales in US$ Million for Years 2015 through 2023 and % CAGR
- TABLE 121: UK 15-Year Perspective for Medical Injection Molding by System - Percentage Breakdown of Value Sales for Hot Runner and Cold Runner for the Years 2015, 2025 & 2030
- SPAIN
- TABLE 122: Spain Recent Past, Current & Future Analysis for Medical Injection Molding by Product - Medical Equipment Component, Consumables, Patient Aids, Orthopedics Instruments, Dental Products and Other Products - Independent Analysis of Annual Sales in US$ Million for the Years 2024 through 2030 and % CAGR
- TABLE 123: Spain Historic Review for Medical Injection Molding by Product - Medical Equipment Component, Consumables, Patient Aids, Orthopedics Instruments, Dental Products and Other Products Markets - Independent Analysis of Annual Sales in US$ Million for Years 2015 through 2023 and % CAGR
- TABLE 124: Spain 15-Year Perspective for Medical Injection Molding by Product - Percentage Breakdown of Value Sales for Medical Equipment Component, Consumables, Patient Aids, Orthopedics Instruments, Dental Products and Other Products for the Years 2015, 2025 & 2030
- TABLE 125: Spain Recent Past, Current & Future Analysis for Medical Injection Molding by Material - Metals, Other Materials and Plastics - Independent Analysis of Annual Sales in US$ Million for the Years 2024 through 2030 and % CAGR
- TABLE 126: Spain Historic Review for Medical Injection Molding by Material - Metals, Other Materials and Plastics Markets - Independent Analysis of Annual Sales in US$ Million for Years 2015 through 2023 and % CAGR
- TABLE 127: Spain 15-Year Perspective for Medical Injection Molding by Material - Percentage Breakdown of Value Sales for Metals, Other Materials and Plastics for the Years 2015, 2025 & 2030
- TABLE 128: Spain Recent Past, Current & Future Analysis for Medical Injection Molding by System - Hot Runner and Cold Runner - Independent Analysis of Annual Sales in US$ Million for the Years 2024 through 2030 and % CAGR
- TABLE 129: Spain Historic Review for Medical Injection Molding by System - Hot Runner and Cold Runner Markets - Independent Analysis of Annual Sales in US$ Million for Years 2015 through 2023 and % CAGR
- TABLE 130: Spain 15-Year Perspective for Medical Injection Molding by System - Percentage Breakdown of Value Sales for Hot Runner and Cold Runner for the Years 2015, 2025 & 2030
- RUSSIA
- TABLE 131: Russia Recent Past, Current & Future Analysis for Medical Injection Molding by Product - Medical Equipment Component, Consumables, Patient Aids, Orthopedics Instruments, Dental Products and Other Products - Independent Analysis of Annual Sales in US$ Million for the Years 2024 through 2030 and % CAGR
- TABLE 132: Russia Historic Review for Medical Injection Molding by Product - Medical Equipment Component, Consumables, Patient Aids, Orthopedics Instruments, Dental Products and Other Products Markets - Independent Analysis of Annual Sales in US$ Million for Years 2015 through 2023 and % CAGR
- TABLE 133: Russia 15-Year Perspective for Medical Injection Molding by Product - Percentage Breakdown of Value Sales for Medical Equipment Component, Consumables, Patient Aids, Orthopedics Instruments, Dental Products and Other Products for the Years 2015, 2025 & 2030
- TABLE 134: Russia Recent Past, Current & Future Analysis for Medical Injection Molding by Material - Metals, Other Materials and Plastics - Independent Analysis of Annual Sales in US$ Million for the Years 2024 through 2030 and % CAGR
- TABLE 135: Russia Historic Review for Medical Injection Molding by Material - Metals, Other Materials and Plastics Markets - Independent Analysis of Annual Sales in US$ Million for Years 2015 through 2023 and % CAGR
- TABLE 136: Russia 15-Year Perspective for Medical Injection Molding by Material - Percentage Breakdown of Value Sales for Metals, Other Materials and Plastics for the Years 2015, 2025 & 2030
- TABLE 137: Russia Recent Past, Current & Future Analysis for Medical Injection Molding by System - Hot Runner and Cold Runner - Independent Analysis of Annual Sales in US$ Million for the Years 2024 through 2030 and % CAGR
- TABLE 138: Russia Historic Review for Medical Injection Molding by System - Hot Runner and Cold Runner Markets - Independent Analysis of Annual Sales in US$ Million for Years 2015 through 2023 and % CAGR
- TABLE 139: Russia 15-Year Perspective for Medical Injection Molding by System - Percentage Breakdown of Value Sales for Hot Runner and Cold Runner for the Years 2015, 2025 & 2030
- REST OF EUROPE
- TABLE 140: Rest of Europe Recent Past, Current & Future Analysis for Medical Injection Molding by Product - Medical Equipment Component, Consumables, Patient Aids, Orthopedics Instruments, Dental Products and Other Products - Independent Analysis of Annual Sales in US$ Million for the Years 2024 through 2030 and % CAGR
- TABLE 141: Rest of Europe Historic Review for Medical Injection Molding by Product - Medical Equipment Component, Consumables, Patient Aids, Orthopedics Instruments, Dental Products and Other Products Markets - Independent Analysis of Annual Sales in US$ Million for Years 2015 through 2023 and % CAGR
- TABLE 142: Rest of Europe 15-Year Perspective for Medical Injection Molding by Product - Percentage Breakdown of Value Sales for Medical Equipment Component, Consumables, Patient Aids, Orthopedics Instruments, Dental Products and Other Products for the Years 2015, 2025 & 2030
- TABLE 143: Rest of Europe Recent Past, Current & Future Analysis for Medical Injection Molding by Material - Metals, Other Materials and Plastics - Independent Analysis of Annual Sales in US$ Million for the Years 2024 through 2030 and % CAGR
- TABLE 144: Rest of Europe Historic Review for Medical Injection Molding by Material - Metals, Other Materials and Plastics Markets - Independent Analysis of Annual Sales in US$ Million for Years 2015 through 2023 and % CAGR
- TABLE 145: Rest of Europe 15-Year Perspective for Medical Injection Molding by Material - Percentage Breakdown of Value Sales for Metals, Other Materials and Plastics for the Years 2015, 2025 & 2030
- TABLE 146: Rest of Europe Recent Past, Current & Future Analysis for Medical Injection Molding by System - Hot Runner and Cold Runner - Independent Analysis of Annual Sales in US$ Million for the Years 2024 through 2030 and % CAGR
- TABLE 147: Rest of Europe Historic Review for Medical Injection Molding by System - Hot Runner and Cold Runner Markets - Independent Analysis of Annual Sales in US$ Million for Years 2015 through 2023 and % CAGR
- TABLE 148: Rest of Europe 15-Year Perspective for Medical Injection Molding by System - Percentage Breakdown of Value Sales for Hot Runner and Cold Runner for the Years 2015, 2025 & 2030
- ASIA-PACIFIC
- Medical Injection Molding Market Presence - Strong/Active/Niche/Trivial - Key Competitors in Asia-Pacific for 2025 (E)
- TABLE 149: Asia-Pacific Recent Past, Current & Future Analysis for Medical Injection Molding by Geographic Region - Australia, India, South Korea and Rest of Asia-Pacific Markets - Independent Analysis of Annual Sales in US$ Million for Years 2024 through 2030 and % CAGR
- TABLE 150: Asia-Pacific Historic Review for Medical Injection Molding by Geographic Region - Australia, India, South Korea and Rest of Asia-Pacific Markets - Independent Analysis of Annual Sales in US$ Million for Years 2015 through 2023 and % CAGR
- TABLE 151: Asia-Pacific 15-Year Perspective for Medical Injection Molding by Geographic Region - Percentage Breakdown of Value Sales for Australia, India, South Korea and Rest of Asia-Pacific Markets for Years 2015, 2025 & 2030
- TABLE 152: Asia-Pacific Recent Past, Current & Future Analysis for Medical Injection Molding by Product - Medical Equipment Component, Consumables, Patient Aids, Orthopedics Instruments, Dental Products and Other Products - Independent Analysis of Annual Sales in US$ Million for the Years 2024 through 2030 and % CAGR
- TABLE 153: Asia-Pacific Historic Review for Medical Injection Molding by Product - Medical Equipment Component, Consumables, Patient Aids, Orthopedics Instruments, Dental Products and Other Products Markets - Independent Analysis of Annual Sales in US$ Million for Years 2015 through 2023 and % CAGR
- TABLE 154: Asia-Pacific 15-Year Perspective for Medical Injection Molding by Product - Percentage Breakdown of Value Sales for Medical Equipment Component, Consumables, Patient Aids, Orthopedics Instruments, Dental Products and Other Products for the Years 2015, 2025 & 2030
- TABLE 155: Asia-Pacific Recent Past, Current & Future Analysis for Medical Injection Molding by Material - Metals, Other Materials and Plastics - Independent Analysis of Annual Sales in US$ Million for the Years 2024 through 2030 and % CAGR
- TABLE 156: Asia-Pacific Historic Review for Medical Injection Molding by Material - Metals, Other Materials and Plastics Markets - Independent Analysis of Annual Sales in US$ Million for Years 2015 through 2023 and % CAGR
- TABLE 157: Asia-Pacific 15-Year Perspective for Medical Injection Molding by Material - Percentage Breakdown of Value Sales for Metals, Other Materials and Plastics for the Years 2015, 2025 & 2030
- TABLE 158: Asia-Pacific Recent Past, Current & Future Analysis for Medical Injection Molding by System - Hot Runner and Cold Runner - Independent Analysis of Annual Sales in US$ Million for the Years 2024 through 2030 and % CAGR
- TABLE 159: Asia-Pacific Historic Review for Medical Injection Molding by System - Hot Runner and Cold Runner Markets - Independent Analysis of Annual Sales in US$ Million for Years 2015 through 2023 and % CAGR
- TABLE 160: Asia-Pacific 15-Year Perspective for Medical Injection Molding by System - Percentage Breakdown of Value Sales for Hot Runner and Cold Runner for the Years 2015, 2025 & 2030
- AUSTRALIA
- Medical Injection Molding Market Presence - Strong/Active/Niche/Trivial - Key Competitors in Australia for 2025 (E)
- TABLE 161: Australia Recent Past, Current & Future Analysis for Medical Injection Molding by Product - Medical Equipment Component, Consumables, Patient Aids, Orthopedics Instruments, Dental Products and Other Products - Independent Analysis of Annual Sales in US$ Million for the Years 2024 through 2030 and % CAGR
- TABLE 162: Australia Historic Review for Medical Injection Molding by Product - Medical Equipment Component, Consumables, Patient Aids, Orthopedics Instruments, Dental Products and Other Products Markets - Independent Analysis of Annual Sales in US$ Million for Years 2015 through 2023 and % CAGR
- TABLE 163: Australia 15-Year Perspective for Medical Injection Molding by Product - Percentage Breakdown of Value Sales for Medical Equipment Component, Consumables, Patient Aids, Orthopedics Instruments, Dental Products and Other Products for the Years 2015, 2025 & 2030
- TABLE 164: Australia Recent Past, Current & Future Analysis for Medical Injection Molding by Material - Metals, Other Materials and Plastics - Independent Analysis of Annual Sales in US$ Million for the Years 2024 through 2030 and % CAGR
- TABLE 165: Australia Historic Review for Medical Injection Molding by Material - Metals, Other Materials and Plastics Markets - Independent Analysis of Annual Sales in US$ Million for Years 2015 through 2023 and % CAGR
- TABLE 166: Australia 15-Year Perspective for Medical Injection Molding by Material - Percentage Breakdown of Value Sales for Metals, Other Materials and Plastics for the Years 2015, 2025 & 2030
- TABLE 167: Australia Recent Past, Current & Future Analysis for Medical Injection Molding by System - Hot Runner and Cold Runner - Independent Analysis of Annual Sales in US$ Million for the Years 2024 through 2030 and % CAGR
- TABLE 168: Australia Historic Review for Medical Injection Molding by System - Hot Runner and Cold Runner Markets - Independent Analysis of Annual Sales in US$ Million for Years 2015 through 2023 and % CAGR
- TABLE 169: Australia 15-Year Perspective for Medical Injection Molding by System - Percentage Breakdown of Value Sales for Hot Runner and Cold Runner for the Years 2015, 2025 & 2030
- INDIA
- Medical Injection Molding Market Presence - Strong/Active/Niche/Trivial - Key Competitors in India for 2025 (E)
- TABLE 170: India Recent Past, Current & Future Analysis for Medical Injection Molding by Product - Medical Equipment Component, Consumables, Patient Aids, Orthopedics Instruments, Dental Products and Other Products - Independent Analysis of Annual Sales in US$ Million for the Years 2024 through 2030 and % CAGR
- TABLE 171: India Historic Review for Medical Injection Molding by Product - Medical Equipment Component, Consumables, Patient Aids, Orthopedics Instruments, Dental Products and Other Products Markets - Independent Analysis of Annual Sales in US$ Million for Years 2015 through 2023 and % CAGR
- TABLE 172: India 15-Year Perspective for Medical Injection Molding by Product - Percentage Breakdown of Value Sales for Medical Equipment Component, Consumables, Patient Aids, Orthopedics Instruments, Dental Products and Other Products for the Years 2015, 2025 & 2030
- TABLE 173: India Recent Past, Current & Future Analysis for Medical Injection Molding by Material - Metals, Other Materials and Plastics - Independent Analysis of Annual Sales in US$ Million for the Years 2024 through 2030 and % CAGR
- TABLE 174: India Historic Review for Medical Injection Molding by Material - Metals, Other Materials and Plastics Markets - Independent Analysis of Annual Sales in US$ Million for Years 2015 through 2023 and % CAGR
- TABLE 175: India 15-Year Perspective for Medical Injection Molding by Material - Percentage Breakdown of Value Sales for Metals, Other Materials and Plastics for the Years 2015, 2025 & 2030
- TABLE 176: India Recent Past, Current & Future Analysis for Medical Injection Molding by System - Hot Runner and Cold Runner - Independent Analysis of Annual Sales in US$ Million for the Years 2024 through 2030 and % CAGR
- TABLE 177: India Historic Review for Medical Injection Molding by System - Hot Runner and Cold Runner Markets - Independent Analysis of Annual Sales in US$ Million for Years 2015 through 2023 and % CAGR
- TABLE 178: India 15-Year Perspective for Medical Injection Molding by System - Percentage Breakdown of Value Sales for Hot Runner and Cold Runner for the Years 2015, 2025 & 2030
- SOUTH KOREA
- TABLE 179: South Korea Recent Past, Current & Future Analysis for Medical Injection Molding by Product - Medical Equipment Component, Consumables, Patient Aids, Orthopedics Instruments, Dental Products and Other Products - Independent Analysis of Annual Sales in US$ Million for the Years 2024 through 2030 and % CAGR
- TABLE 180: South Korea Historic Review for Medical Injection Molding by Product - Medical Equipment Component, Consumables, Patient Aids, Orthopedics Instruments, Dental Products and Other Products Markets - Independent Analysis of Annual Sales in US$ Million for Years 2015 through 2023 and % CAGR
- TABLE 181: South Korea 15-Year Perspective for Medical Injection Molding by Product - Percentage Breakdown of Value Sales for Medical Equipment Component, Consumables, Patient Aids, Orthopedics Instruments, Dental Products and Other Products for the Years 2015, 2025 & 2030
- TABLE 182: South Korea Recent Past, Current & Future Analysis for Medical Injection Molding by Material - Metals, Other Materials and Plastics - Independent Analysis of Annual Sales in US$ Million for the Years 2024 through 2030 and % CAGR
- TABLE 183: South Korea Historic Review for Medical Injection Molding by Material - Metals, Other Materials and Plastics Markets - Independent Analysis of Annual Sales in US$ Million for Years 2015 through 2023 and % CAGR
- TABLE 184: South Korea 15-Year Perspective for Medical Injection Molding by Material - Percentage Breakdown of Value Sales for Metals, Other Materials and Plastics for the Years 2015, 2025 & 2030
- TABLE 185: South Korea Recent Past, Current & Future Analysis for Medical Injection Molding by System - Hot Runner and Cold Runner - Independent Analysis of Annual Sales in US$ Million for the Years 2024 through 2030 and % CAGR
- TABLE 186: South Korea Historic Review for Medical Injection Molding by System - Hot Runner and Cold Runner Markets - Independent Analysis of Annual Sales in US$ Million for Years 2015 through 2023 and % CAGR
- TABLE 187: South Korea 15-Year Perspective for Medical Injection Molding by System - Percentage Breakdown of Value Sales for Hot Runner and Cold Runner for the Years 2015, 2025 & 2030
- REST OF ASIA-PACIFIC
- TABLE 188: Rest of Asia-Pacific Recent Past, Current & Future Analysis for Medical Injection Molding by Product - Medical Equipment Component, Consumables, Patient Aids, Orthopedics Instruments, Dental Products and Other Products - Independent Analysis of Annual Sales in US$ Million for the Years 2024 through 2030 and % CAGR
- TABLE 189: Rest of Asia-Pacific Historic Review for Medical Injection Molding by Product - Medical Equipment Component, Consumables, Patient Aids, Orthopedics Instruments, Dental Products and Other Products Markets - Independent Analysis of Annual Sales in US$ Million for Years 2015 through 2023 and % CAGR
- TABLE 190: Rest of Asia-Pacific 15-Year Perspective for Medical Injection Molding by Product - Percentage Breakdown of Value Sales for Medical Equipment Component, Consumables, Patient Aids, Orthopedics Instruments, Dental Products and Other Products for the Years 2015, 2025 & 2030
- TABLE 191: Rest of Asia-Pacific Recent Past, Current & Future Analysis for Medical Injection Molding by Material - Metals, Other Materials and Plastics - Independent Analysis of Annual Sales in US$ Million for the Years 2024 through 2030 and % CAGR
- TABLE 192: Rest of Asia-Pacific Historic Review for Medical Injection Molding by Material - Metals, Other Materials and Plastics Markets - Independent Analysis of Annual Sales in US$ Million for Years 2015 through 2023 and % CAGR
- TABLE 193: Rest of Asia-Pacific 15-Year Perspective for Medical Injection Molding by Material - Percentage Breakdown of Value Sales for Metals, Other Materials and Plastics for the Years 2015, 2025 & 2030
- TABLE 194: Rest of Asia-Pacific Recent Past, Current & Future Analysis for Medical Injection Molding by System - Hot Runner and Cold Runner - Independent Analysis of Annual Sales in US$ Million for the Years 2024 through 2030 and % CAGR
- TABLE 195: Rest of Asia-Pacific Historic Review for Medical Injection Molding by System - Hot Runner and Cold Runner Markets - Independent Analysis of Annual Sales in US$ Million for Years 2015 through 2023 and % CAGR
- TABLE 196: Rest of Asia-Pacific 15-Year Perspective for Medical Injection Molding by System - Percentage Breakdown of Value Sales for Hot Runner and Cold Runner for the Years 2015, 2025 & 2030
- LATIN AMERICA
- Medical Injection Molding Market Presence - Strong/Active/Niche/Trivial - Key Competitors in Latin America for 2025 (E)
- TABLE 197: Latin America Recent Past, Current & Future Analysis for Medical Injection Molding by Geographic Region - Argentina, Brazil, Mexico and Rest of Latin America Markets - Independent Analysis of Annual Sales in US$ Million for Years 2024 through 2030 and % CAGR
- TABLE 198: Latin America Historic Review for Medical Injection Molding by Geographic Region - Argentina, Brazil, Mexico and Rest of Latin America Markets - Independent Analysis of Annual Sales in US$ Million for Years 2015 through 2023 and % CAGR
- TABLE 199: Latin America 15-Year Perspective for Medical Injection Molding by Geographic Region - Percentage Breakdown of Value Sales for Argentina, Brazil, Mexico and Rest of Latin America Markets for Years 2015, 2025 & 2030
- TABLE 200: Latin America Recent Past, Current & Future Analysis for Medical Injection Molding by Product - Medical Equipment Component, Consumables, Patient Aids, Orthopedics Instruments, Dental Products and Other Products - Independent Analysis of Annual Sales in US$ Million for the Years 2024 through 2030 and % CAGR
- TABLE 201: Latin America Historic Review for Medical Injection Molding by Product - Medical Equipment Component, Consumables, Patient Aids, Orthopedics Instruments, Dental Products and Other Products Markets - Independent Analysis of Annual Sales in US$ Million for Years 2015 through 2023 and % CAGR
- TABLE 202: Latin America 15-Year Perspective for Medical Injection Molding by Product - Percentage Breakdown of Value Sales for Medical Equipment Component, Consumables, Patient Aids, Orthopedics Instruments, Dental Products and Other Products for the Years 2015, 2025 & 2030
- TABLE 203: Latin America Recent Past, Current & Future Analysis for Medical Injection Molding by Material - Metals, Other Materials and Plastics - Independent Analysis of Annual Sales in US$ Million for the Years 2024 through 2030 and % CAGR
- TABLE 204: Latin America Historic Review for Medical Injection Molding by Material - Metals, Other Materials and Plastics Markets - Independent Analysis of Annual Sales in US$ Million for Years 2015 through 2023 and % CAGR
- TABLE 205: Latin America 15-Year Perspective for Medical Injection Molding by Material - Percentage Breakdown of Value Sales for Metals, Other Materials and Plastics for the Years 2015, 2025 & 2030
- TABLE 206: Latin America Recent Past, Current & Future Analysis for Medical Injection Molding by System - Hot Runner and Cold Runner - Independent Analysis of Annual Sales in US$ Million for the Years 2024 through 2030 and % CAGR
- TABLE 207: Latin America Historic Review for Medical Injection Molding by System - Hot Runner and Cold Runner Markets - Independent Analysis of Annual Sales in US$ Million for Years 2015 through 2023 and % CAGR
- TABLE 208: Latin America 15-Year Perspective for Medical Injection Molding by System - Percentage Breakdown of Value Sales for Hot Runner and Cold Runner for the Years 2015, 2025 & 2030
- ARGENTINA
- TABLE 209: Argentina Recent Past, Current & Future Analysis for Medical Injection Molding by Product - Medical Equipment Component, Consumables, Patient Aids, Orthopedics Instruments, Dental Products and Other Products - Independent Analysis of Annual Sales in US$ Million for the Years 2024 through 2030 and % CAGR
- TABLE 210: Argentina Historic Review for Medical Injection Molding by Product - Medical Equipment Component, Consumables, Patient Aids, Orthopedics Instruments, Dental Products and Other Products Markets - Independent Analysis of Annual Sales in US$ Million for Years 2015 through 2023 and % CAGR
- TABLE 211: Argentina 15-Year Perspective for Medical Injection Molding by Product - Percentage Breakdown of Value Sales for Medical Equipment Component, Consumables, Patient Aids, Orthopedics Instruments, Dental Products and Other Products for the Years 2015, 2025 & 2030
- TABLE 212: Argentina Recent Past, Current & Future Analysis for Medical Injection Molding by Material - Metals, Other Materials and Plastics - Independent Analysis of Annual Sales in US$ Million for the Years 2024 through 2030 and % CAGR
- TABLE 213: Argentina Historic Review for Medical Injection Molding by Material - Metals, Other Materials and Plastics Markets - Independent Analysis of Annual Sales in US$ Million for Years 2015 through 2023 and % CAGR
- TABLE 214: Argentina 15-Year Perspective for Medical Injection Molding by Material - Percentage Breakdown of Value Sales for Metals, Other Materials and Plastics for the Years 2015, 2025 & 2030
- TABLE 215: Argentina Recent Past, Current & Future Analysis for Medical Injection Molding by System - Hot Runner and Cold Runner - Independent Analysis of Annual Sales in US$ Million for the Years 2024 through 2030 and % CAGR
- TABLE 216: Argentina Historic Review for Medical Injection Molding by System - Hot Runner and Cold Runner Markets - Independent Analysis of Annual Sales in US$ Million for Years 2015 through 2023 and % CAGR
- TABLE 217: Argentina 15-Year Perspective for Medical Injection Molding by System - Percentage Breakdown of Value Sales for Hot Runner and Cold Runner for the Years 2015, 2025 & 2030
- BRAZIL
- TABLE 218: Brazil Recent Past, Current & Future Analysis for Medical Injection Molding by Product - Medical Equipment Component, Consumables, Patient Aids, Orthopedics Instruments, Dental Products and Other Products - Independent Analysis of Annual Sales in US$ Million for the Years 2024 through 2030 and % CAGR
- TABLE 219: Brazil Historic Review for Medical Injection Molding by Product - Medical Equipment Component, Consumables, Patient Aids, Orthopedics Instruments, Dental Products and Other Products Markets - Independent Analysis of Annual Sales in US$ Million for Years 2015 through 2023 and % CAGR
- TABLE 220: Brazil 15-Year Perspective for Medical Injection Molding by Product - Percentage Breakdown of Value Sales for Medical Equipment Component, Consumables, Patient Aids, Orthopedics Instruments, Dental Products and Other Products for the Years 2015, 2025 & 2030
- TABLE 221: Brazil Recent Past, Current & Future Analysis for Medical Injection Molding by Material - Metals, Other Materials and Plastics - Independent Analysis of Annual Sales in US$ Million for the Years 2024 through 2030 and % CAGR
- TABLE 222: Brazil Historic Review for Medical Injection Molding by Material - Metals, Other Materials and Plastics Markets - Independent Analysis of Annual Sales in US$ Million for Years 2015 through 2023 and % CAGR
- TABLE 223: Brazil 15-Year Perspective for Medical Injection Molding by Material - Percentage Breakdown of Value Sales for Metals, Other Materials and Plastics for the Years 2015, 2025 & 2030
- TABLE 224: Brazil Recent Past, Current & Future Analysis for Medical Injection Molding by System - Hot Runner and Cold Runner - Independent Analysis of Annual Sales in US$ Million for the Years 2024 through 2030 and % CAGR
- TABLE 225: Brazil Historic Review for Medical Injection Molding by System - Hot Runner and Cold Runner Markets - Independent Analysis of Annual Sales in US$ Million for Years 2015 through 2023 and % CAGR
- TABLE 226: Brazil 15-Year Perspective for Medical Injection Molding by System - Percentage Breakdown of Value Sales for Hot Runner and Cold Runner for the Years 2015, 2025 & 2030
- MEXICO
- TABLE 227: Mexico Recent Past, Current & Future Analysis for Medical Injection Molding by Product - Medical Equipment Component, Consumables, Patient Aids, Orthopedics Instruments, Dental Products and Other Products - Independent Analysis of Annual Sales in US$ Million for the Years 2024 through 2030 and % CAGR
- TABLE 228: Mexico Historic Review for Medical Injection Molding by Product - Medical Equipment Component, Consumables, Patient Aids, Orthopedics Instruments, Dental Products and Other Products Markets - Independent Analysis of Annual Sales in US$ Million for Years 2015 through 2023 and % CAGR
- TABLE 229: Mexico 15-Year Perspective for Medical Injection Molding by Product - Percentage Breakdown of Value Sales for Medical Equipment Component, Consumables, Patient Aids, Orthopedics Instruments, Dental Products and Other Products for the Years 2015, 2025 & 2030
- TABLE 230: Mexico Recent Past, Current & Future Analysis for Medical Injection Molding by Material - Metals, Other Materials and Plastics - Independent Analysis of Annual Sales in US$ Million for the Years 2024 through 2030 and % CAGR
- TABLE 231: Mexico Historic Review for Medical Injection Molding by Material - Metals, Other Materials and Plastics Markets - Independent Analysis of Annual Sales in US$ Million for Years 2015 through 2023 and % CAGR
- TABLE 232: Mexico 15-Year Perspective for Medical Injection Molding by Material - Percentage Breakdown of Value Sales for Metals, Other Materials and Plastics for the Years 2015, 2025 & 2030
- TABLE 233: Mexico Recent Past, Current & Future Analysis for Medical Injection Molding by System - Hot Runner and Cold Runner - Independent Analysis of Annual Sales in US$ Million for the Years 2024 through 2030 and % CAGR
- TABLE 234: Mexico Historic Review for Medical Injection Molding by System - Hot Runner and Cold Runner Markets - Independent Analysis of Annual Sales in US$ Million for Years 2015 through 2023 and % CAGR
- TABLE 235: Mexico 15-Year Perspective for Medical Injection Molding by System - Percentage Breakdown of Value Sales for Hot Runner and Cold Runner for the Years 2015, 2025 & 2030
- REST OF LATIN AMERICA
- TABLE 236: Rest of Latin America Recent Past, Current & Future Analysis for Medical Injection Molding by Product - Medical Equipment Component, Consumables, Patient Aids, Orthopedics Instruments, Dental Products and Other Products - Independent Analysis of Annual Sales in US$ Million for the Years 2024 through 2030 and % CAGR
- TABLE 237: Rest of Latin America Historic Review for Medical Injection Molding by Product - Medical Equipment Component, Consumables, Patient Aids, Orthopedics Instruments, Dental Products and Other Products Markets - Independent Analysis of Annual Sales in US$ Million for Years 2015 through 2023 and % CAGR
- TABLE 238: Rest of Latin America 15-Year Perspective for Medical Injection Molding by Product - Percentage Breakdown of Value Sales for Medical Equipment Component, Consumables, Patient Aids, Orthopedics Instruments, Dental Products and Other Products for the Years 2015, 2025 & 2030
- TABLE 239: Rest of Latin America Recent Past, Current & Future Analysis for Medical Injection Molding by Material - Metals, Other Materials and Plastics - Independent Analysis of Annual Sales in US$ Million for the Years 2024 through 2030 and % CAGR
- TABLE 240: Rest of Latin America Historic Review for Medical Injection Molding by Material - Metals, Other Materials and Plastics Markets - Independent Analysis of Annual Sales in US$ Million for Years 2015 through 2023 and % CAGR
- TABLE 241: Rest of Latin America 15-Year Perspective for Medical Injection Molding by Material - Percentage Breakdown of Value Sales for Metals, Other Materials and Plastics for the Years 2015, 2025 & 2030
- TABLE 242: Rest of Latin America Recent Past, Current & Future Analysis for Medical Injection Molding by System - Hot Runner and Cold Runner - Independent Analysis of Annual Sales in US$ Million for the Years 2024 through 2030 and % CAGR
- TABLE 243: Rest of Latin America Historic Review for Medical Injection Molding by System - Hot Runner and Cold Runner Markets - Independent Analysis of Annual Sales in US$ Million for Years 2015 through 2023 and % CAGR
- TABLE 244: Rest of Latin America 15-Year Perspective for Medical Injection Molding by System - Percentage Breakdown of Value Sales for Hot Runner and Cold Runner for the Years 2015, 2025 & 2030
- MIDDLE EAST
- Medical Injection Molding Market Presence - Strong/Active/Niche/Trivial - Key Competitors in Middle East for 2025 (E)
- TABLE 245: Middle East Recent Past, Current & Future Analysis for Medical Injection Molding by Geographic Region - Iran, Israel, Saudi Arabia, UAE and Rest of Middle East Markets - Independent Analysis of Annual Sales in US$ Million for Years 2024 through 2030 and % CAGR
- TABLE 246: Middle East Historic Review for Medical Injection Molding by Geographic Region - Iran, Israel, Saudi Arabia, UAE and Rest of Middle East Markets - Independent Analysis of Annual Sales in US$ Million for Years 2015 through 2023 and % CAGR
- TABLE 247: Middle East 15-Year Perspective for Medical Injection Molding by Geographic Region - Percentage Breakdown of Value Sales for Iran, Israel, Saudi Arabia, UAE and Rest of Middle East Markets for Years 2015, 2025 & 2030
- TABLE 248: Middle East Recent Past, Current & Future Analysis for Medical Injection Molding by Product - Medical Equipment Component, Consumables, Patient Aids, Orthopedics Instruments, Dental Products and Other Products - Independent Analysis of Annual Sales in US$ Million for the Years 2024 through 2030 and % CAGR
- TABLE 249: Middle East Historic Review for Medical Injection Molding by Product - Medical Equipment Component, Consumables, Patient Aids, Orthopedics Instruments, Dental Products and Other Products Markets - Independent Analysis of Annual Sales in US$ Million for Years 2015 through 2023 and % CAGR
- TABLE 250: Middle East 15-Year Perspective for Medical Injection Molding by Product - Percentage Breakdown of Value Sales for Medical Equipment Component, Consumables, Patient Aids, Orthopedics Instruments, Dental Products and Other Products for the Years 2015, 2025 & 2030
- TABLE 251: Middle East Recent Past, Current & Future Analysis for Medical Injection Molding by Material - Metals, Other Materials and Plastics - Independent Analysis of Annual Sales in US$ Million for the Years 2024 through 2030 and % CAGR
- TABLE 252: Middle East Historic Review for Medical Injection Molding by Material - Metals, Other Materials and Plastics Markets - Independent Analysis of Annual Sales in US$ Million for Years 2015 through 2023 and % CAGR
- TABLE 253: Middle East 15-Year Perspective for Medical Injection Molding by Material - Percentage Breakdown of Value Sales for Metals, Other Materials and Plastics for the Years 2015, 2025 & 2030
- TABLE 254: Middle East Recent Past, Current & Future Analysis for Medical Injection Molding by System - Hot Runner and Cold Runner - Independent Analysis of Annual Sales in US$ Million for the Years 2024 through 2030 and % CAGR
- TABLE 255: Middle East Historic Review for Medical Injection Molding by System - Hot Runner and Cold Runner Markets - Independent Analysis of Annual Sales in US$ Million for Years 2015 through 2023 and % CAGR
- TABLE 256: Middle East 15-Year Perspective for Medical Injection Molding by System - Percentage Breakdown of Value Sales for Hot Runner and Cold Runner for the Years 2015, 2025 & 2030
- IRAN
- TABLE 257: Iran Recent Past, Current & Future Analysis for Medical Injection Molding by Product - Medical Equipment Component, Consumables, Patient Aids, Orthopedics Instruments, Dental Products and Other Products - Independent Analysis of Annual Sales in US$ Million for the Years 2024 through 2030 and % CAGR
- TABLE 258: Iran Historic Review for Medical Injection Molding by Product - Medical Equipment Component, Consumables, Patient Aids, Orthopedics Instruments, Dental Products and Other Products Markets - Independent Analysis of Annual Sales in US$ Million for Years 2015 through 2023 and % CAGR
- TABLE 259: Iran 15-Year Perspective for Medical Injection Molding by Product - Percentage Breakdown of Value Sales for Medical Equipment Component, Consumables, Patient Aids, Orthopedics Instruments, Dental Products and Other Products for the Years 2015, 2025 & 2030
- TABLE 260: Iran Recent Past, Current & Future Analysis for Medical Injection Molding by Material - Metals, Other Materials and Plastics - Independent Analysis of Annual Sales in US$ Million for the Years 2024 through 2030 and % CAGR
- TABLE 261: Iran Historic Review for Medical Injection Molding by Material - Metals, Other Materials and Plastics Markets - Independent Analysis of Annual Sales in US$ Million for Years 2015 through 2023 and % CAGR
- TABLE 262: Iran 15-Year Perspective for Medical Injection Molding by Material - Percentage Breakdown of Value Sales for Metals, Other Materials and Plastics for the Years 2015, 2025 & 2030
- TABLE 263: Iran Recent Past, Current & Future Analysis for Medical Injection Molding by System - Hot Runner and Cold Runner - Independent Analysis of Annual Sales in US$ Million for the Years 2024 through 2030 and % CAGR
- TABLE 264: Iran Historic Review for Medical Injection Molding by System - Hot Runner and Cold Runner Markets - Independent Analysis of Annual Sales in US$ Million for Years 2015 through 2023 and % CAGR
- TABLE 265: Iran 15-Year Perspective for Medical Injection Molding by System - Percentage Breakdown of Value Sales for Hot Runner and Cold Runner for the Years 2015, 2025 & 2030
- ISRAEL
- TABLE 266: Israel Recent Past, Current & Future Analysis for Medical Injection Molding by Product - Medical Equipment Component, Consumables, Patient Aids, Orthopedics Instruments, Dental Products and Other Products - Independent Analysis of Annual Sales in US$ Million for the Years 2024 through 2030 and % CAGR
- TABLE 267: Israel Historic Review for Medical Injection Molding by Product - Medical Equipment Component, Consumables, Patient Aids, Orthopedics Instruments, Dental Products and Other Products Markets - Independent Analysis of Annual Sales in US$ Million for Years 2015 through 2023 and % CAGR
- TABLE 268: Israel 15-Year Perspective for Medical Injection Molding by Product - Percentage Breakdown of Value Sales for Medical Equipment Component, Consumables, Patient Aids, Orthopedics Instruments, Dental Products and Other Products for the Years 2015, 2025 & 2030
- TABLE 269: Israel Recent Past, Current & Future Analysis for Medical Injection Molding by Material - Metals, Other Materials and Plastics - Independent Analysis of Annual Sales in US$ Million for the Years 2024 through 2030 and % CAGR
- TABLE 270: Israel Historic Review for Medical Injection Molding by Material - Metals, Other Materials and Plastics Markets - Independent Analysis of Annual Sales in US$ Million for Years 2015 through 2023 and % CAGR
- TABLE 271: Israel 15-Year Perspective for Medical Injection Molding by Material - Percentage Breakdown of Value Sales for Metals, Other Materials and Plastics for the Years 2015, 2025 & 2030
- TABLE 272: Israel Recent Past, Current & Future Analysis for Medical Injection Molding by System - Hot Runner and Cold Runner - Independent Analysis of Annual Sales in US$ Million for the Years 2024 through 2030 and % CAGR
- TABLE 273: Israel Historic Review for Medical Injection Molding by System - Hot Runner and Cold Runner Markets - Independent Analysis of Annual Sales in US$ Million for Years 2015 through 2023 and % CAGR
- TABLE 274: Israel 15-Year Perspective for Medical Injection Molding by System - Percentage Breakdown of Value Sales for Hot Runner and Cold Runner for the Years 2015, 2025 & 2030
- SAUDI ARABIA
- TABLE 275: Saudi Arabia Recent Past, Current & Future Analysis for Medical Injection Molding by Product - Medical Equipment Component, Consumables, Patient Aids, Orthopedics Instruments, Dental Products and Other Products - Independent Analysis of Annual Sales in US$ Million for the Years 2024 through 2030 and % CAGR
- TABLE 276: Saudi Arabia Historic Review for Medical Injection Molding by Product - Medical Equipment Component, Consumables, Patient Aids, Orthopedics Instruments, Dental Products and Other Products Markets - Independent Analysis of Annual Sales in US$ Million for Years 2015 through 2023 and % CAGR
- TABLE 277: Saudi Arabia 15-Year Perspective for Medical Injection Molding by Product - Percentage Breakdown of Value Sales for Medical Equipment Component, Consumables, Patient Aids, Orthopedics Instruments, Dental Products and Other Products for the Years 2015, 2025 & 2030
- TABLE 278: Saudi Arabia Recent Past, Current & Future Analysis for Medical Injection Molding by Material - Metals, Other Materials and Plastics - Independent Analysis of Annual Sales in US$ Million for the Years 2024 through 2030 and % CAGR
- TABLE 279: Saudi Arabia Historic Review for Medical Injection Molding by Material - Metals, Other Materials and Plastics Markets - Independent Analysis of Annual Sales in US$ Million for Years 2015 through 2023 and % CAGR
- TABLE 280: Saudi Arabia 15-Year Perspective for Medical Injection Molding by Material - Percentage Breakdown of Value Sales for Metals, Other Materials and Plastics for the Years 2015, 2025 & 2030
- TABLE 281: Saudi Arabia Recent Past, Current & Future Analysis for Medical Injection Molding by System - Hot Runner and Cold Runner - Independent Analysis of Annual Sales in US$ Million for the Years 2024 through 2030 and % CAGR
- TABLE 282: Saudi Arabia Historic Review for Medical Injection Molding by System - Hot Runner and Cold Runner Markets - Independent Analysis of Annual Sales in US$ Million for Years 2015 through 2023 and % CAGR
- TABLE 283: Saudi Arabia 15-Year Perspective for Medical Injection Molding by System - Percentage Breakdown of Value Sales for Hot Runner and Cold Runner for the Years 2015, 2025 & 2030
- UNITED ARAB EMIRATES
- TABLE 284: UAE Recent Past, Current & Future Analysis for Medical Injection Molding by Product - Medical Equipment Component, Consumables, Patient Aids, Orthopedics Instruments, Dental Products and Other Products - Independent Analysis of Annual Sales in US$ Million for the Years 2024 through 2030 and % CAGR
- TABLE 285: UAE Historic Review for Medical Injection Molding by Product - Medical Equipment Component, Consumables, Patient Aids, Orthopedics Instruments, Dental Products and Other Products Markets - Independent Analysis of Annual Sales in US$ Million for Years 2015 through 2023 and % CAGR
- TABLE 286: UAE 15-Year Perspective for Medical Injection Molding by Product - Percentage Breakdown of Value Sales for Medical Equipment Component, Consumables, Patient Aids, Orthopedics Instruments, Dental Products and Other Products for the Years 2015, 2025 & 2030
- TABLE 287: UAE Recent Past, Current & Future Analysis for Medical Injection Molding by Material - Metals, Other Materials and Plastics - Independent Analysis of Annual Sales in US$ Million for the Years 2024 through 2030 and % CAGR
- TABLE 288: UAE Historic Review for Medical Injection Molding by Material - Metals, Other Materials and Plastics Markets - Independent Analysis of Annual Sales in US$ Million for Years 2015 through 2023 and % CAGR
- TABLE 289: UAE 15-Year Perspective for Medical Injection Molding by Material - Percentage Breakdown of Value Sales for Metals, Other Materials and Plastics for the Years 2015, 2025 & 2030
- TABLE 290: UAE Recent Past, Current & Future Analysis for Medical Injection Molding by System - Hot Runner and Cold Runner - Independent Analysis of Annual Sales in US$ Million for the Years 2024 through 2030 and % CAGR
- TABLE 291: UAE Historic Review for Medical Injection Molding by System - Hot Runner and Cold Runner Markets - Independent Analysis of Annual Sales in US$ Million for Years 2015 through 2023 and % CAGR
- TABLE 292: UAE 15-Year Perspective for Medical Injection Molding by System - Percentage Breakdown of Value Sales for Hot Runner and Cold Runner for the Years 2015, 2025 & 2030
- REST OF MIDDLE EAST
- TABLE 293: Rest of Middle East Recent Past, Current & Future Analysis for Medical Injection Molding by Product - Medical Equipment Component, Consumables, Patient Aids, Orthopedics Instruments, Dental Products and Other Products - Independent Analysis of Annual Sales in US$ Million for the Years 2024 through 2030 and % CAGR
- TABLE 294: Rest of Middle East Historic Review for Medical Injection Molding by Product - Medical Equipment Component, Consumables, Patient Aids, Orthopedics Instruments, Dental Products and Other Products Markets - Independent Analysis of Annual Sales in US$ Million for Years 2015 through 2023 and % CAGR
- TABLE 295: Rest of Middle East 15-Year Perspective for Medical Injection Molding by Product - Percentage Breakdown of Value Sales for Medical Equipment Component, Consumables, Patient Aids, Orthopedics Instruments, Dental Products and Other Products for the Years 2015, 2025 & 2030
- TABLE 296: Rest of Middle East Recent Past, Current & Future Analysis for Medical Injection Molding by Material - Metals, Other Materials and Plastics - Independent Analysis of Annual Sales in US$ Million for the Years 2024 through 2030 and % CAGR
- TABLE 297: Rest of Middle East Historic Review for Medical Injection Molding by Material - Metals, Other Materials and Plastics Markets - Independent Analysis of Annual Sales in US$ Million for Years 2015 through 2023 and % CAGR
- TABLE 298: Rest of Middle East 15-Year Perspective for Medical Injection Molding by Material - Percentage Breakdown of Value Sales for Metals, Other Materials and Plastics for the Years 2015, 2025 & 2030
- TABLE 299: Rest of Middle East Recent Past, Current & Future Analysis for Medical Injection Molding by System - Hot Runner and Cold Runner - Independent Analysis of Annual Sales in US$ Million for the Years 2024 through 2030 and % CAGR
- TABLE 300: Rest of Middle East Historic Review for Medical Injection Molding by System - Hot Runner and Cold Runner Markets - Independent Analysis of Annual Sales in US$ Million for Years 2015 through 2023 and % CAGR
- TABLE 301: Rest of Middle East 15-Year Perspective for Medical Injection Molding by System - Percentage Breakdown of Value Sales for Hot Runner and Cold Runner for the Years 2015, 2025 & 2030
- AFRICA
- Medical Injection Molding Market Presence - Strong/Active/Niche/Trivial - Key Competitors in Africa for 2025 (E)
- TABLE 302: Africa Recent Past, Current & Future Analysis for Medical Injection Molding by Product - Medical Equipment Component, Consumables, Patient Aids, Orthopedics Instruments, Dental Products and Other Products - Independent Analysis of Annual Sales in US$ Million for the Years 2024 through 2030 and % CAGR
- TABLE 303: Africa Historic Review for Medical Injection Molding by Product - Medical Equipment Component, Consumables, Patient Aids, Orthopedics Instruments, Dental Products and Other Products Markets - Independent Analysis of Annual Sales in US$ Million for Years 2015 through 2023 and % CAGR
- TABLE 304: Africa 15-Year Perspective for Medical Injection Molding by Product - Percentage Breakdown of Value Sales for Medical Equipment Component, Consumables, Patient Aids, Orthopedics Instruments, Dental Products and Other Products for the Years 2015, 2025 & 2030
- TABLE 305: Africa Recent Past, Current & Future Analysis for Medical Injection Molding by Material - Metals, Other Materials and Plastics - Independent Analysis of Annual Sales in US$ Million for the Years 2024 through 2030 and % CAGR
- TABLE 306: Africa Historic Review for Medical Injection Molding by Material - Metals, Other Materials and Plastics Markets - Independent Analysis of Annual Sales in US$ Million for Years 2015 through 2023 and % CAGR
- TABLE 307: Africa 15-Year Perspective for Medical Injection Molding by Material - Percentage Breakdown of Value Sales for Metals, Other Materials and Plastics for the Years 2015, 2025 & 2030
- TABLE 308: Africa Recent Past, Current & Future Analysis for Medical Injection Molding by System - Hot Runner and Cold Runner - Independent Analysis of Annual Sales in US$ Million for the Years 2024 through 2030 and % CAGR
- TABLE 309: Africa Historic Review for Medical Injection Molding by System - Hot Runner and Cold Runner Markets - Independent Analysis of Annual Sales in US$ Million for Years 2015 through 2023 and % CAGR
- TABLE 310: Africa 15-Year Perspective for Medical Injection Molding by System - Percentage Breakdown of Value Sales for Hot Runner and Cold Runner for the Years 2015, 2025 & 2030
- IV. COMPETITION
Pricing
Currency Rates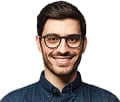