
Friction Welding
Description
Global Friction Welding Market to Reach US$825.1 Million by 2030
The global market for Friction Welding estimated at US$671.0 Million in the year 2024, is expected to reach US$825.1 Million by 2030, growing at a CAGR of 3.5% over the analysis period 2024-2030. Rotary Friction Welding (RFW), one of the segments analyzed in the report, is expected to record a 4.2% CAGR and reach US$408.0 Million by the end of the analysis period. Growth in the Friction Stir Welding (FSW) segment is estimated at 2.8% CAGR over the analysis period.
The U.S. Market is Estimated at US$181.0 Million While China is Forecast to Grow at 6.8% CAGR
The Friction Welding market in the U.S. is estimated at US$181.0 Million in the year 2024. China, the world`s second largest economy, is forecast to reach a projected market size of US$173.0 Million by the year 2030 trailing a CAGR of 6.8% over the analysis period 2024-2030. Among the other noteworthy geographic markets are Japan and Canada, each forecast to grow at a CAGR of 1.1% and 2.6% respectively over the analysis period. Within Europe, Germany is forecast to grow at approximately 1.8% CAGR.
Global Friction Welding Market - Key Trends & Drivers Summarized
Why Is Friction Welding Gaining Popularity Across Industries?
Friction welding is becoming a preferred welding technology across various industries due to its ability to join materials without requiring melting, thus producing joints with excellent strength and durability. Unlike traditional welding methods, friction welding relies on heat generated from mechanical friction, making it ideal for materials that are difficult to weld with conventional processes, such as dissimilar metals and temperature-sensitive materials. This process produces high-quality, defect-free joints that can withstand heavy loads, high temperatures, and pressure, making it valuable in industries like automotive, aerospace, defense, and construction. For example, in automotive applications, friction welding is used to produce lightweight, strong components by joining materials such as aluminum to steel, contributing to vehicle weight reduction and improved fuel efficiency. This ability to join different materials without fusion has made friction welding an indispensable technology in sectors that prioritize both durability and efficiency.
Beyond strength and durability, friction welding is appreciated for its eco-friendly profile as it requires no filler materials or shielding gases, which reduces emissions and waste. This characteristic has aligned friction welding with growing industry demands for sustainable manufacturing practices. Additionally, the process is highly energy-efficient, often completing welds in seconds, which minimizes operational costs and improves productivity. With these benefits, friction welding is increasingly viewed as a sustainable, cost-effective alternative to traditional fusion welding, supporting industries that seek both environmental responsibility and high-performance standards.
How Are Technological Advancements Enhancing Friction Welding Capabilities?
Technological advancements have significantly enhanced friction welding processes, improving precision, speed, and the range of materials that can be joined. One major development is in rotary friction welding, which allows precise control over parameters such as friction pressure, rotation speed, and forging pressure, resulting in highly consistent and reliable welds. Advancements in linear and orbital friction welding have also expanded the application of this technology, making it possible to join complex shapes and larger components used in sectors like aerospace and heavy equipment manufacturing. Furthermore, improvements in automation and robotics have streamlined friction welding, enabling continuous, repeatable welds in high-volume production environments, which is essential in industries like automotive where consistent quality and efficiency are critical. Additionally, the integration of real-time monitoring systems in friction welding machines allows operators to track parameters and make adjustments on-the-fly, reducing the risk of errors and ensuring high-quality output. These monitoring systems use sensors and data analytics to detect any anomalies in the welding process, making it possible to maintain optimal conditions and reduce material waste. Developments in hybrid friction welding techniques, such as friction stir welding (FSW), are enabling manufacturers to join materials with even greater complexity and precision, such as in high-strength alloys and complex geometries. These technological advancements are making friction welding a more versatile, reliable, and adaptive process, meeting the increasingly complex demands of modern manufacturing.
Which Industries Are Driving Demand for Friction Welding Beyond Automotive?
While automotive manufacturing remains a major driver for friction welding, demand is also growing across industries like aerospace, marine, defense, and oil & gas due to the process’s unique benefits in producing strong, defect-free joints. The aerospace industry, in particular, relies on friction welding for applications where joint integrity and weight reduction are paramount, such as in airframes, turbine components, and fuel systems. The ability to join lightweight metals like titanium and aluminum with precision makes friction welding valuable for reducing aircraft weight, leading to improved fuel efficiency and performance. In the marine industry, where components must withstand harsh environments and corrosive elements, friction welding is used for joining steel and stainless steel in propeller shafts, pipelines, and ship hulls. The oil & gas sector also finds friction welding indispensable for joining critical components in drilling equipment, pipelines, and offshore structures. These components require robust, reliable joints that can endure extreme pressures, temperatures, and corrosive environments, making friction welding a preferred choice. The defense industry uses friction welding in the production of military-grade equipment and weapon systems, as it creates joints that are resilient under extreme stress and can join dissimilar metals, a frequent requirement in advanced defense applications. This cross-industry adoption underscores the versatility of friction welding, as it adapts to the stringent quality and performance standards across diverse sectors focused on strength, durability, and efficiency.
What’s Driving Growth in the Friction Welding Market?
The growth in the friction welding market is driven by several factors, including rising demand for lightweight and durable materials, advancements in automation, and an increasing focus on sustainable manufacturing. The automotive and aerospace industries, in particular, are shifting towards lightweight materials to improve fuel efficiency and reduce emissions, which has amplified demand for friction welding to join dissimilar materials like aluminum and steel. Advancements in robotic automation and real-time monitoring have also supported market growth by enabling manufacturers to integrate friction welding into high-speed production lines with enhanced precision and consistency, which is essential for large-scale applications in sectors like automotive and electronics. Moreover, the trend toward environmentally conscious manufacturing practices has spurred interest in friction welding, as it eliminates the need for filler materials, produces minimal waste, and uses less energy compared to traditional welding methods. This aligns well with industries seeking to reduce their environmental impact and meet sustainability goals. Additionally, the demand for high-performance components in sectors such as oil & gas, defense, and marine, which require materials that can endure extreme conditions, has further driven adoption. Together, these factors highlight the robust growth trajectory of the friction welding market as industries seek cost-effective, sustainable, and high-quality solutions for joining materials in an increasingly complex manufacturing landscape.
SCOPE OF STUDY:The report analyzes the Friction Welding market in terms of units by the following Segments, and Geographic Regions/Countries:
Segments:
Welding Type (Rotary Friction Welding (RFW), Friction Stir Welding (FSW), Linear Friction Welding (LFW)); End-Use (Aerospace End-Use, Automotive End-Use, Shipbuilding End-Use, Railways End-Use, Other End-Uses)
Geographic Regions/Countries:
World; USA; Canada; Japan; China; Europe; France; Germany; Italy; UK; Spain; Russia; Rest of Europe; Asia-Pacific; Australia; India; South Korea; Rest of Asia-Pacific; Latin America; Argentina; Brazil; Mexico; Rest of Latin America; Middle East; Iran; Israel; Saudi Arabia; UAE; Rest of Middle East; Africa.
Select Competitors (Total 58 Featured) -
- Berkoa, S. Coop. Machine Tools
- Bond Technologies
- Dukane Corporation
- Fooke GmbH
- Grenzebach Maschinenbau GmbH
- Hitachi Power Solutions Co., Ltd.
- KUKA AG
- MTI Welding Technologies Ltd.
- PaR Systems LLC
- Precision Technologies Group Limited
We`re transforming market and competitive intelligence with validated expert content and AI tools.
Instead of following the general norm of querying LLMs and Industry-specific SLMs, we built repositories of content curated from domain experts worldwide including video transcripts, blogs, search engines research, and massive amounts of enterprise, product/service, and market data.
TARIFF IMPACT FACTOR
Our new release incorporates impact of tariffs on geographical markets as we predict a shift in competitiveness of companies based on HQ country, manufacturing base, exports and imports (finished goods and OEM). This intricate and multifaceted market reality will impact competitors by increasing the Cost of Goods Sold (COGS), reducing profitability, reconfiguring supply chains, amongst other micro and macro market dynamics.
Please note: Reports are sold as single-site single-user licenses. Electronic versions require 24-48 hours as each copy is customized to the client with digital controls and custom watermarks. The Publisher uses digital controls protecting against copying and printing is restricted to one full copy to be used at the same location.
The latest version of Adobe Acrobat Reader is required to view the report. Upon ordering an electronic version, the Publisher will provide a link to download the purchased report.
Prior to fulfillment of an order, the client will be required to sign a document detailing the purchase terms for a publication from this publisher.
Table of Contents
- I. METHODOLOGY
- II. EXECUTIVE SUMMARY
- 1. MARKET OVERVIEW
- Influencer Market Insights
- Tariff Impact on Global Supply Chain Patterns
- Friction Welding – Global Key Competitors Percentage Market Share in 2025 (E)
- Competitive Market Presence - Strong/Active/Niche/Trivial for Players Worldwide in 2025 (E)
- 2. FOCUS ON SELECT PLAYERS
- 3. MARKET TRENDS & DRIVERS
- Rising Demand for Lightweight Materials in Automotive Manufacturing Spurs Growth in Friction Welding
- Technological Advancements in Friction Stir Welding (FSW) Propel Innovation in Aerospace Applications
- Growing Focus on Fuel Efficiency and Emission Reduction Strengthens the Business Case for Friction Welding in Transportation
- Surge in Adoption of Friction Welding in Electric Vehicle (EV) Battery Manufacturing Expands Market Opportunities
- Increasing Use of Dissimilar Metal Joining in Industrial Applications Drives Demand for Friction Welding Solutions
- Advancements in Automated and Robotic Friction Welding Systems Propel Growth in Precision Manufacturing
- Rising Focus on Sustainable Manufacturing Processes Expands Market for Friction Welding in Green Technologies
- Growing Application of Friction Welding in High-Pressure, High-Temperature Environments Spurs Market in Oil & Gas Sector
- Technological Innovations in Linear and Rotary Friction Welding Strengthen Market for Advanced Metal Joining Solutions
- Rising Use of Friction Welding in Medical Device Manufacturing Expands Addressable Market for High-Precision Applications
- Surge in Demand for High-Strength, Corrosion-Resistant Joints Propels Growth in Marine and Shipbuilding Industries
- Increasing Adoption of Friction Welding in Defense and Military Equipment Strengthens Market for High-Reliability Bonding
- 4. GLOBAL MARKET PERSPECTIVE
- TABLE 1: World Friction Welding Market Analysis of Annual Sales in US$ Thousand for Years 2015 through 2030
- TABLE 2: World Recent Past, Current & Future Analysis for Friction Welding by Geographic Region - USA, Canada, Japan, China, Europe, Asia-Pacific, Latin America, Middle East and Africa Markets - Independent Analysis of Annual Sales in US$ Thousand for Years 2024 through 2030 and % CAGR
- TABLE 3: World Historic Review for Friction Welding by Geographic Region - USA, Canada, Japan, China, Europe, Asia-Pacific, Latin America, Middle East and Africa Markets - Independent Analysis of Annual Sales in US$ Thousand for Years 2015 through 2023 and % CAGR
- TABLE 4: World 15-Year Perspective for Friction Welding by Geographic Region - Percentage Breakdown of Value Sales for USA, Canada, Japan, China, Europe, Asia-Pacific, Latin America, Middle East and Africa Markets for Years 2015, 2025 & 2030
- TABLE 5: World Recent Past, Current & Future Analysis for Rotary Friction Welding (RFW) by Geographic Region - USA, Canada, Japan, China, Europe, Asia-Pacific, Latin America, Middle East and Africa Markets - Independent Analysis of Annual Sales in US$ Thousand for Years 2024 through 2030 and % CAGR
- TABLE 6: World Historic Review for Rotary Friction Welding (RFW) by Geographic Region - USA, Canada, Japan, China, Europe, Asia-Pacific, Latin America, Middle East and Africa Markets - Independent Analysis of Annual Sales in US$ Thousand for Years 2015 through 2023 and % CAGR
- TABLE 7: World 15-Year Perspective for Rotary Friction Welding (RFW) by Geographic Region - Percentage Breakdown of Value Sales for USA, Canada, Japan, China, Europe, Asia-Pacific, Latin America, Middle East and Africa for Years 2015, 2025 & 2030
- TABLE 8: World Recent Past, Current & Future Analysis for Friction Stir Welding (FSW) by Geographic Region - USA, Canada, Japan, China, Europe, Asia-Pacific, Latin America, Middle East and Africa Markets - Independent Analysis of Annual Sales in US$ Thousand for Years 2024 through 2030 and % CAGR
- TABLE 9: World Historic Review for Friction Stir Welding (FSW) by Geographic Region - USA, Canada, Japan, China, Europe, Asia-Pacific, Latin America, Middle East and Africa Markets - Independent Analysis of Annual Sales in US$ Thousand for Years 2015 through 2023 and % CAGR
- TABLE 10: World 15-Year Perspective for Friction Stir Welding (FSW) by Geographic Region - Percentage Breakdown of Value Sales for USA, Canada, Japan, China, Europe, Asia-Pacific, Latin America, Middle East and Africa for Years 2015, 2025 & 2030
- TABLE 11: World Recent Past, Current & Future Analysis for Linear Friction Welding (LFW) by Geographic Region - USA, Canada, Japan, China, Europe, Asia-Pacific, Latin America, Middle East and Africa Markets - Independent Analysis of Annual Sales in US$ Thousand for Years 2024 through 2030 and % CAGR
- TABLE 12: World Historic Review for Linear Friction Welding (LFW) by Geographic Region - USA, Canada, Japan, China, Europe, Asia-Pacific, Latin America, Middle East and Africa Markets - Independent Analysis of Annual Sales in US$ Thousand for Years 2015 through 2023 and % CAGR
- TABLE 13: World 15-Year Perspective for Linear Friction Welding (LFW) by Geographic Region - Percentage Breakdown of Value Sales for USA, Canada, Japan, China, Europe, Asia-Pacific, Latin America, Middle East and Africa for Years 2015, 2025 & 2030
- TABLE 14: World Recent Past, Current & Future Analysis for Aerospace End-Use by Geographic Region - USA, Canada, Japan, China, Europe, Asia-Pacific, Latin America, Middle East and Africa Markets - Independent Analysis of Annual Sales in US$ Thousand for Years 2024 through 2030 and % CAGR
- TABLE 15: World Historic Review for Aerospace End-Use by Geographic Region - USA, Canada, Japan, China, Europe, Asia-Pacific, Latin America, Middle East and Africa Markets - Independent Analysis of Annual Sales in US$ Thousand for Years 2015 through 2023 and % CAGR
- TABLE 16: World 15-Year Perspective for Aerospace End-Use by Geographic Region - Percentage Breakdown of Value Sales for USA, Canada, Japan, China, Europe, Asia-Pacific, Latin America, Middle East and Africa for Years 2015, 2025 & 2030
- TABLE 17: World Recent Past, Current & Future Analysis for Automotive End-Use by Geographic Region - USA, Canada, Japan, China, Europe, Asia-Pacific, Latin America, Middle East and Africa Markets - Independent Analysis of Annual Sales in US$ Thousand for Years 2024 through 2030 and % CAGR
- TABLE 18: World Historic Review for Automotive End-Use by Geographic Region - USA, Canada, Japan, China, Europe, Asia-Pacific, Latin America, Middle East and Africa Markets - Independent Analysis of Annual Sales in US$ Thousand for Years 2015 through 2023 and % CAGR
- TABLE 19: World 15-Year Perspective for Automotive End-Use by Geographic Region - Percentage Breakdown of Value Sales for USA, Canada, Japan, China, Europe, Asia-Pacific, Latin America, Middle East and Africa for Years 2015, 2025 & 2030
- TABLE 20: World Recent Past, Current & Future Analysis for Shipbuilding End-Use by Geographic Region - USA, Canada, Japan, China, Europe, Asia-Pacific, Latin America, Middle East and Africa Markets - Independent Analysis of Annual Sales in US$ Thousand for Years 2024 through 2030 and % CAGR
- TABLE 21: World Historic Review for Shipbuilding End-Use by Geographic Region - USA, Canada, Japan, China, Europe, Asia-Pacific, Latin America, Middle East and Africa Markets - Independent Analysis of Annual Sales in US$ Thousand for Years 2015 through 2023 and % CAGR
- TABLE 22: World 15-Year Perspective for Shipbuilding End-Use by Geographic Region - Percentage Breakdown of Value Sales for USA, Canada, Japan, China, Europe, Asia-Pacific, Latin America, Middle East and Africa for Years 2015, 2025 & 2030
- TABLE 23: World Recent Past, Current & Future Analysis for Railways End-Use by Geographic Region - USA, Canada, Japan, China, Europe, Asia-Pacific, Latin America, Middle East and Africa Markets - Independent Analysis of Annual Sales in US$ Thousand for Years 2024 through 2030 and % CAGR
- TABLE 24: World Historic Review for Railways End-Use by Geographic Region - USA, Canada, Japan, China, Europe, Asia-Pacific, Latin America, Middle East and Africa Markets - Independent Analysis of Annual Sales in US$ Thousand for Years 2015 through 2023 and % CAGR
- TABLE 25: World 15-Year Perspective for Railways End-Use by Geographic Region - Percentage Breakdown of Value Sales for USA, Canada, Japan, China, Europe, Asia-Pacific, Latin America, Middle East and Africa for Years 2015, 2025 & 2030
- TABLE 26: World Recent Past, Current & Future Analysis for Other End-Uses by Geographic Region - USA, Canada, Japan, China, Europe, Asia-Pacific, Latin America, Middle East and Africa Markets - Independent Analysis of Annual Sales in US$ Thousand for Years 2024 through 2030 and % CAGR
- TABLE 27: World Historic Review for Other End-Uses by Geographic Region - USA, Canada, Japan, China, Europe, Asia-Pacific, Latin America, Middle East and Africa Markets - Independent Analysis of Annual Sales in US$ Thousand for Years 2015 through 2023 and % CAGR
- TABLE 28: World 15-Year Perspective for Other End-Uses by Geographic Region - Percentage Breakdown of Value Sales for USA, Canada, Japan, China, Europe, Asia-Pacific, Latin America, Middle East and Africa for Years 2015, 2025 & 2030
- III. MARKET ANALYSIS
- UNITED STATES
- Friction Welding Market Presence - Strong/Active/Niche/Trivial - Key Competitors in the United States for 2025 (E)
- TABLE 29: USA Recent Past, Current & Future Analysis for Friction Welding by Welding Type - Rotary Friction Welding (RFW), Friction Stir Welding (FSW) and Linear Friction Welding (LFW) - Independent Analysis of Annual Sales in US$ Thousand for the Years 2024 through 2030 and % CAGR
- TABLE 30: USA Historic Review for Friction Welding by Welding Type - Rotary Friction Welding (RFW), Friction Stir Welding (FSW) and Linear Friction Welding (LFW) Markets - Independent Analysis of Annual Sales in US$ Thousand for Years 2015 through 2023 and % CAGR
- TABLE 31: USA 15-Year Perspective for Friction Welding by Welding Type - Percentage Breakdown of Value Sales for Rotary Friction Welding (RFW), Friction Stir Welding (FSW) and Linear Friction Welding (LFW) for the Years 2015, 2025 & 2030
- TABLE 32: USA Recent Past, Current & Future Analysis for Friction Welding by End-Use - Aerospace End-Use, Automotive End-Use, Shipbuilding End-Use, Railways End-Use and Other End-Uses - Independent Analysis of Annual Sales in US$ Thousand for the Years 2024 through 2030 and % CAGR
- TABLE 33: USA Historic Review for Friction Welding by End-Use - Aerospace End-Use, Automotive End-Use, Shipbuilding End-Use, Railways End-Use and Other End-Uses Markets - Independent Analysis of Annual Sales in US$ Thousand for Years 2015 through 2023 and % CAGR
- TABLE 34: USA 15-Year Perspective for Friction Welding by End-Use - Percentage Breakdown of Value Sales for Aerospace End-Use, Automotive End-Use, Shipbuilding End-Use, Railways End-Use and Other End-Uses for the Years 2015, 2025 & 2030
- CANADA
- TABLE 35: Canada Recent Past, Current & Future Analysis for Friction Welding by Welding Type - Rotary Friction Welding (RFW), Friction Stir Welding (FSW) and Linear Friction Welding (LFW) - Independent Analysis of Annual Sales in US$ Thousand for the Years 2024 through 2030 and % CAGR
- TABLE 36: Canada Historic Review for Friction Welding by Welding Type - Rotary Friction Welding (RFW), Friction Stir Welding (FSW) and Linear Friction Welding (LFW) Markets - Independent Analysis of Annual Sales in US$ Thousand for Years 2015 through 2023 and % CAGR
- TABLE 37: Canada 15-Year Perspective for Friction Welding by Welding Type - Percentage Breakdown of Value Sales for Rotary Friction Welding (RFW), Friction Stir Welding (FSW) and Linear Friction Welding (LFW) for the Years 2015, 2025 & 2030
- TABLE 38: Canada Recent Past, Current & Future Analysis for Friction Welding by End-Use - Aerospace End-Use, Automotive End-Use, Shipbuilding End-Use, Railways End-Use and Other End-Uses - Independent Analysis of Annual Sales in US$ Thousand for the Years 2024 through 2030 and % CAGR
- TABLE 39: Canada Historic Review for Friction Welding by End-Use - Aerospace End-Use, Automotive End-Use, Shipbuilding End-Use, Railways End-Use and Other End-Uses Markets - Independent Analysis of Annual Sales in US$ Thousand for Years 2015 through 2023 and % CAGR
- TABLE 40: Canada 15-Year Perspective for Friction Welding by End-Use - Percentage Breakdown of Value Sales for Aerospace End-Use, Automotive End-Use, Shipbuilding End-Use, Railways End-Use and Other End-Uses for the Years 2015, 2025 & 2030
- JAPAN
- Friction Welding Market Presence - Strong/Active/Niche/Trivial - Key Competitors in Japan for 2025 (E)
- TABLE 41: Japan Recent Past, Current & Future Analysis for Friction Welding by Welding Type - Rotary Friction Welding (RFW), Friction Stir Welding (FSW) and Linear Friction Welding (LFW) - Independent Analysis of Annual Sales in US$ Thousand for the Years 2024 through 2030 and % CAGR
- TABLE 42: Japan Historic Review for Friction Welding by Welding Type - Rotary Friction Welding (RFW), Friction Stir Welding (FSW) and Linear Friction Welding (LFW) Markets - Independent Analysis of Annual Sales in US$ Thousand for Years 2015 through 2023 and % CAGR
- TABLE 43: Japan 15-Year Perspective for Friction Welding by Welding Type - Percentage Breakdown of Value Sales for Rotary Friction Welding (RFW), Friction Stir Welding (FSW) and Linear Friction Welding (LFW) for the Years 2015, 2025 & 2030
- TABLE 44: Japan Recent Past, Current & Future Analysis for Friction Welding by End-Use - Aerospace End-Use, Automotive End-Use, Shipbuilding End-Use, Railways End-Use and Other End-Uses - Independent Analysis of Annual Sales in US$ Thousand for the Years 2024 through 2030 and % CAGR
- TABLE 45: Japan Historic Review for Friction Welding by End-Use - Aerospace End-Use, Automotive End-Use, Shipbuilding End-Use, Railways End-Use and Other End-Uses Markets - Independent Analysis of Annual Sales in US$ Thousand for Years 2015 through 2023 and % CAGR
- TABLE 46: Japan 15-Year Perspective for Friction Welding by End-Use - Percentage Breakdown of Value Sales for Aerospace End-Use, Automotive End-Use, Shipbuilding End-Use, Railways End-Use and Other End-Uses for the Years 2015, 2025 & 2030
- CHINA
- Friction Welding Market Presence - Strong/Active/Niche/Trivial - Key Competitors in China for 2025 (E)
- TABLE 47: China Recent Past, Current & Future Analysis for Friction Welding by Welding Type - Rotary Friction Welding (RFW), Friction Stir Welding (FSW) and Linear Friction Welding (LFW) - Independent Analysis of Annual Sales in US$ Thousand for the Years 2024 through 2030 and % CAGR
- TABLE 48: China Historic Review for Friction Welding by Welding Type - Rotary Friction Welding (RFW), Friction Stir Welding (FSW) and Linear Friction Welding (LFW) Markets - Independent Analysis of Annual Sales in US$ Thousand for Years 2015 through 2023 and % CAGR
- TABLE 49: China 15-Year Perspective for Friction Welding by Welding Type - Percentage Breakdown of Value Sales for Rotary Friction Welding (RFW), Friction Stir Welding (FSW) and Linear Friction Welding (LFW) for the Years 2015, 2025 & 2030
- TABLE 50: China Recent Past, Current & Future Analysis for Friction Welding by End-Use - Aerospace End-Use, Automotive End-Use, Shipbuilding End-Use, Railways End-Use and Other End-Uses - Independent Analysis of Annual Sales in US$ Thousand for the Years 2024 through 2030 and % CAGR
- TABLE 51: China Historic Review for Friction Welding by End-Use - Aerospace End-Use, Automotive End-Use, Shipbuilding End-Use, Railways End-Use and Other End-Uses Markets - Independent Analysis of Annual Sales in US$ Thousand for Years 2015 through 2023 and % CAGR
- TABLE 52: China 15-Year Perspective for Friction Welding by End-Use - Percentage Breakdown of Value Sales for Aerospace End-Use, Automotive End-Use, Shipbuilding End-Use, Railways End-Use and Other End-Uses for the Years 2015, 2025 & 2030
- EUROPE
- Friction Welding Market Presence - Strong/Active/Niche/Trivial - Key Competitors in Europe for 2025 (E)
- TABLE 53: Europe Recent Past, Current & Future Analysis for Friction Welding by Geographic Region - France, Germany, Italy, UK, Spain, Russia and Rest of Europe Markets - Independent Analysis of Annual Sales in US$ Thousand for Years 2024 through 2030 and % CAGR
- TABLE 54: Europe Historic Review for Friction Welding by Geographic Region - France, Germany, Italy, UK, Spain, Russia and Rest of Europe Markets - Independent Analysis of Annual Sales in US$ Thousand for Years 2015 through 2023 and % CAGR
- TABLE 55: Europe 15-Year Perspective for Friction Welding by Geographic Region - Percentage Breakdown of Value Sales for France, Germany, Italy, UK, Spain, Russia and Rest of Europe Markets for Years 2015, 2025 & 2030
- TABLE 56: Europe Recent Past, Current & Future Analysis for Friction Welding by Welding Type - Rotary Friction Welding (RFW), Friction Stir Welding (FSW) and Linear Friction Welding (LFW) - Independent Analysis of Annual Sales in US$ Thousand for the Years 2024 through 2030 and % CAGR
- TABLE 57: Europe Historic Review for Friction Welding by Welding Type - Rotary Friction Welding (RFW), Friction Stir Welding (FSW) and Linear Friction Welding (LFW) Markets - Independent Analysis of Annual Sales in US$ Thousand for Years 2015 through 2023 and % CAGR
- TABLE 58: Europe 15-Year Perspective for Friction Welding by Welding Type - Percentage Breakdown of Value Sales for Rotary Friction Welding (RFW), Friction Stir Welding (FSW) and Linear Friction Welding (LFW) for the Years 2015, 2025 & 2030
- TABLE 59: Europe Recent Past, Current & Future Analysis for Friction Welding by End-Use - Aerospace End-Use, Automotive End-Use, Shipbuilding End-Use, Railways End-Use and Other End-Uses - Independent Analysis of Annual Sales in US$ Thousand for the Years 2024 through 2030 and % CAGR
- TABLE 60: Europe Historic Review for Friction Welding by End-Use - Aerospace End-Use, Automotive End-Use, Shipbuilding End-Use, Railways End-Use and Other End-Uses Markets - Independent Analysis of Annual Sales in US$ Thousand for Years 2015 through 2023 and % CAGR
- TABLE 61: Europe 15-Year Perspective for Friction Welding by End-Use - Percentage Breakdown of Value Sales for Aerospace End-Use, Automotive End-Use, Shipbuilding End-Use, Railways End-Use and Other End-Uses for the Years 2015, 2025 & 2030
- FRANCE
- Friction Welding Market Presence - Strong/Active/Niche/Trivial - Key Competitors in France for 2025 (E)
- TABLE 62: France Recent Past, Current & Future Analysis for Friction Welding by Welding Type - Rotary Friction Welding (RFW), Friction Stir Welding (FSW) and Linear Friction Welding (LFW) - Independent Analysis of Annual Sales in US$ Thousand for the Years 2024 through 2030 and % CAGR
- TABLE 63: France Historic Review for Friction Welding by Welding Type - Rotary Friction Welding (RFW), Friction Stir Welding (FSW) and Linear Friction Welding (LFW) Markets - Independent Analysis of Annual Sales in US$ Thousand for Years 2015 through 2023 and % CAGR
- TABLE 64: France 15-Year Perspective for Friction Welding by Welding Type - Percentage Breakdown of Value Sales for Rotary Friction Welding (RFW), Friction Stir Welding (FSW) and Linear Friction Welding (LFW) for the Years 2015, 2025 & 2030
- TABLE 65: France Recent Past, Current & Future Analysis for Friction Welding by End-Use - Aerospace End-Use, Automotive End-Use, Shipbuilding End-Use, Railways End-Use and Other End-Uses - Independent Analysis of Annual Sales in US$ Thousand for the Years 2024 through 2030 and % CAGR
- TABLE 66: France Historic Review for Friction Welding by End-Use - Aerospace End-Use, Automotive End-Use, Shipbuilding End-Use, Railways End-Use and Other End-Uses Markets - Independent Analysis of Annual Sales in US$ Thousand for Years 2015 through 2023 and % CAGR
- TABLE 67: France 15-Year Perspective for Friction Welding by End-Use - Percentage Breakdown of Value Sales for Aerospace End-Use, Automotive End-Use, Shipbuilding End-Use, Railways End-Use and Other End-Uses for the Years 2015, 2025 & 2030
- GERMANY
- Friction Welding Market Presence - Strong/Active/Niche/Trivial - Key Competitors in Germany for 2025 (E)
- TABLE 68: Germany Recent Past, Current & Future Analysis for Friction Welding by Welding Type - Rotary Friction Welding (RFW), Friction Stir Welding (FSW) and Linear Friction Welding (LFW) - Independent Analysis of Annual Sales in US$ Thousand for the Years 2024 through 2030 and % CAGR
- TABLE 69: Germany Historic Review for Friction Welding by Welding Type - Rotary Friction Welding (RFW), Friction Stir Welding (FSW) and Linear Friction Welding (LFW) Markets - Independent Analysis of Annual Sales in US$ Thousand for Years 2015 through 2023 and % CAGR
- TABLE 70: Germany 15-Year Perspective for Friction Welding by Welding Type - Percentage Breakdown of Value Sales for Rotary Friction Welding (RFW), Friction Stir Welding (FSW) and Linear Friction Welding (LFW) for the Years 2015, 2025 & 2030
- TABLE 71: Germany Recent Past, Current & Future Analysis for Friction Welding by End-Use - Aerospace End-Use, Automotive End-Use, Shipbuilding End-Use, Railways End-Use and Other End-Uses - Independent Analysis of Annual Sales in US$ Thousand for the Years 2024 through 2030 and % CAGR
- TABLE 72: Germany Historic Review for Friction Welding by End-Use - Aerospace End-Use, Automotive End-Use, Shipbuilding End-Use, Railways End-Use and Other End-Uses Markets - Independent Analysis of Annual Sales in US$ Thousand for Years 2015 through 2023 and % CAGR
- TABLE 73: Germany 15-Year Perspective for Friction Welding by End-Use - Percentage Breakdown of Value Sales for Aerospace End-Use, Automotive End-Use, Shipbuilding End-Use, Railways End-Use and Other End-Uses for the Years 2015, 2025 & 2030
- ITALY
- TABLE 74: Italy Recent Past, Current & Future Analysis for Friction Welding by Welding Type - Rotary Friction Welding (RFW), Friction Stir Welding (FSW) and Linear Friction Welding (LFW) - Independent Analysis of Annual Sales in US$ Thousand for the Years 2024 through 2030 and % CAGR
- TABLE 75: Italy Historic Review for Friction Welding by Welding Type - Rotary Friction Welding (RFW), Friction Stir Welding (FSW) and Linear Friction Welding (LFW) Markets - Independent Analysis of Annual Sales in US$ Thousand for Years 2015 through 2023 and % CAGR
- TABLE 76: Italy 15-Year Perspective for Friction Welding by Welding Type - Percentage Breakdown of Value Sales for Rotary Friction Welding (RFW), Friction Stir Welding (FSW) and Linear Friction Welding (LFW) for the Years 2015, 2025 & 2030
- TABLE 77: Italy Recent Past, Current & Future Analysis for Friction Welding by End-Use - Aerospace End-Use, Automotive End-Use, Shipbuilding End-Use, Railways End-Use and Other End-Uses - Independent Analysis of Annual Sales in US$ Thousand for the Years 2024 through 2030 and % CAGR
- TABLE 78: Italy Historic Review for Friction Welding by End-Use - Aerospace End-Use, Automotive End-Use, Shipbuilding End-Use, Railways End-Use and Other End-Uses Markets - Independent Analysis of Annual Sales in US$ Thousand for Years 2015 through 2023 and % CAGR
- TABLE 79: Italy 15-Year Perspective for Friction Welding by End-Use - Percentage Breakdown of Value Sales for Aerospace End-Use, Automotive End-Use, Shipbuilding End-Use, Railways End-Use and Other End-Uses for the Years 2015, 2025 & 2030
- UNITED KINGDOM
- Friction Welding Market Presence - Strong/Active/Niche/Trivial - Key Competitors in the United Kingdom for 2025 (E)
- TABLE 80: UK Recent Past, Current & Future Analysis for Friction Welding by Welding Type - Rotary Friction Welding (RFW), Friction Stir Welding (FSW) and Linear Friction Welding (LFW) - Independent Analysis of Annual Sales in US$ Thousand for the Years 2024 through 2030 and % CAGR
- TABLE 81: UK Historic Review for Friction Welding by Welding Type - Rotary Friction Welding (RFW), Friction Stir Welding (FSW) and Linear Friction Welding (LFW) Markets - Independent Analysis of Annual Sales in US$ Thousand for Years 2015 through 2023 and % CAGR
- TABLE 82: UK 15-Year Perspective for Friction Welding by Welding Type - Percentage Breakdown of Value Sales for Rotary Friction Welding (RFW), Friction Stir Welding (FSW) and Linear Friction Welding (LFW) for the Years 2015, 2025 & 2030
- TABLE 83: UK Recent Past, Current & Future Analysis for Friction Welding by End-Use - Aerospace End-Use, Automotive End-Use, Shipbuilding End-Use, Railways End-Use and Other End-Uses - Independent Analysis of Annual Sales in US$ Thousand for the Years 2024 through 2030 and % CAGR
- TABLE 84: UK Historic Review for Friction Welding by End-Use - Aerospace End-Use, Automotive End-Use, Shipbuilding End-Use, Railways End-Use and Other End-Uses Markets - Independent Analysis of Annual Sales in US$ Thousand for Years 2015 through 2023 and % CAGR
- TABLE 85: UK 15-Year Perspective for Friction Welding by End-Use - Percentage Breakdown of Value Sales for Aerospace End-Use, Automotive End-Use, Shipbuilding End-Use, Railways End-Use and Other End-Uses for the Years 2015, 2025 & 2030
- SPAIN
- TABLE 86: Spain Recent Past, Current & Future Analysis for Friction Welding by Welding Type - Rotary Friction Welding (RFW), Friction Stir Welding (FSW) and Linear Friction Welding (LFW) - Independent Analysis of Annual Sales in US$ Thousand for the Years 2024 through 2030 and % CAGR
- TABLE 87: Spain Historic Review for Friction Welding by Welding Type - Rotary Friction Welding (RFW), Friction Stir Welding (FSW) and Linear Friction Welding (LFW) Markets - Independent Analysis of Annual Sales in US$ Thousand for Years 2015 through 2023 and % CAGR
- TABLE 88: Spain 15-Year Perspective for Friction Welding by Welding Type - Percentage Breakdown of Value Sales for Rotary Friction Welding (RFW), Friction Stir Welding (FSW) and Linear Friction Welding (LFW) for the Years 2015, 2025 & 2030
- TABLE 89: Spain Recent Past, Current & Future Analysis for Friction Welding by End-Use - Aerospace End-Use, Automotive End-Use, Shipbuilding End-Use, Railways End-Use and Other End-Uses - Independent Analysis of Annual Sales in US$ Thousand for the Years 2024 through 2030 and % CAGR
- TABLE 90: Spain Historic Review for Friction Welding by End-Use - Aerospace End-Use, Automotive End-Use, Shipbuilding End-Use, Railways End-Use and Other End-Uses Markets - Independent Analysis of Annual Sales in US$ Thousand for Years 2015 through 2023 and % CAGR
- TABLE 91: Spain 15-Year Perspective for Friction Welding by End-Use - Percentage Breakdown of Value Sales for Aerospace End-Use, Automotive End-Use, Shipbuilding End-Use, Railways End-Use and Other End-Uses for the Years 2015, 2025 & 2030
- RUSSIA
- TABLE 92: Russia Recent Past, Current & Future Analysis for Friction Welding by Welding Type - Rotary Friction Welding (RFW), Friction Stir Welding (FSW) and Linear Friction Welding (LFW) - Independent Analysis of Annual Sales in US$ Thousand for the Years 2024 through 2030 and % CAGR
- TABLE 93: Russia Historic Review for Friction Welding by Welding Type - Rotary Friction Welding (RFW), Friction Stir Welding (FSW) and Linear Friction Welding (LFW) Markets - Independent Analysis of Annual Sales in US$ Thousand for Years 2015 through 2023 and % CAGR
- TABLE 94: Russia 15-Year Perspective for Friction Welding by Welding Type - Percentage Breakdown of Value Sales for Rotary Friction Welding (RFW), Friction Stir Welding (FSW) and Linear Friction Welding (LFW) for the Years 2015, 2025 & 2030
- TABLE 95: Russia Recent Past, Current & Future Analysis for Friction Welding by End-Use - Aerospace End-Use, Automotive End-Use, Shipbuilding End-Use, Railways End-Use and Other End-Uses - Independent Analysis of Annual Sales in US$ Thousand for the Years 2024 through 2030 and % CAGR
- TABLE 96: Russia Historic Review for Friction Welding by End-Use - Aerospace End-Use, Automotive End-Use, Shipbuilding End-Use, Railways End-Use and Other End-Uses Markets - Independent Analysis of Annual Sales in US$ Thousand for Years 2015 through 2023 and % CAGR
- TABLE 97: Russia 15-Year Perspective for Friction Welding by End-Use - Percentage Breakdown of Value Sales for Aerospace End-Use, Automotive End-Use, Shipbuilding End-Use, Railways End-Use and Other End-Uses for the Years 2015, 2025 & 2030
- REST OF EUROPE
- TABLE 98: Rest of Europe Recent Past, Current & Future Analysis for Friction Welding by Welding Type - Rotary Friction Welding (RFW), Friction Stir Welding (FSW) and Linear Friction Welding (LFW) - Independent Analysis of Annual Sales in US$ Thousand for the Years 2024 through 2030 and % CAGR
- TABLE 99: Rest of Europe Historic Review for Friction Welding by Welding Type - Rotary Friction Welding (RFW), Friction Stir Welding (FSW) and Linear Friction Welding (LFW) Markets - Independent Analysis of Annual Sales in US$ Thousand for Years 2015 through 2023 and % CAGR
- TABLE 100: Rest of Europe 15-Year Perspective for Friction Welding by Welding Type - Percentage Breakdown of Value Sales for Rotary Friction Welding (RFW), Friction Stir Welding (FSW) and Linear Friction Welding (LFW) for the Years 2015, 2025 & 2030
- TABLE 101: Rest of Europe Recent Past, Current & Future Analysis for Friction Welding by End-Use - Aerospace End-Use, Automotive End-Use, Shipbuilding End-Use, Railways End-Use and Other End-Uses - Independent Analysis of Annual Sales in US$ Thousand for the Years 2024 through 2030 and % CAGR
- TABLE 102: Rest of Europe Historic Review for Friction Welding by End-Use - Aerospace End-Use, Automotive End-Use, Shipbuilding End-Use, Railways End-Use and Other End-Uses Markets - Independent Analysis of Annual Sales in US$ Thousand for Years 2015 through 2023 and % CAGR
- TABLE 103: Rest of Europe 15-Year Perspective for Friction Welding by End-Use - Percentage Breakdown of Value Sales for Aerospace End-Use, Automotive End-Use, Shipbuilding End-Use, Railways End-Use and Other End-Uses for the Years 2015, 2025 & 2030
- ASIA-PACIFIC
- Friction Welding Market Presence - Strong/Active/Niche/Trivial - Key Competitors in Asia-Pacific for 2025 (E)
- TABLE 104: Asia-Pacific Recent Past, Current & Future Analysis for Friction Welding by Geographic Region - Australia, India, South Korea and Rest of Asia-Pacific Markets - Independent Analysis of Annual Sales in US$ Thousand for Years 2024 through 2030 and % CAGR
- TABLE 105: Asia-Pacific Historic Review for Friction Welding by Geographic Region - Australia, India, South Korea and Rest of Asia-Pacific Markets - Independent Analysis of Annual Sales in US$ Thousand for Years 2015 through 2023 and % CAGR
- TABLE 106: Asia-Pacific 15-Year Perspective for Friction Welding by Geographic Region - Percentage Breakdown of Value Sales for Australia, India, South Korea and Rest of Asia-Pacific Markets for Years 2015, 2025 & 2030
- TABLE 107: Asia-Pacific Recent Past, Current & Future Analysis for Friction Welding by Welding Type - Rotary Friction Welding (RFW), Friction Stir Welding (FSW) and Linear Friction Welding (LFW) - Independent Analysis of Annual Sales in US$ Thousand for the Years 2024 through 2030 and % CAGR
- TABLE 108: Asia-Pacific Historic Review for Friction Welding by Welding Type - Rotary Friction Welding (RFW), Friction Stir Welding (FSW) and Linear Friction Welding (LFW) Markets - Independent Analysis of Annual Sales in US$ Thousand for Years 2015 through 2023 and % CAGR
- TABLE 109: Asia-Pacific 15-Year Perspective for Friction Welding by Welding Type - Percentage Breakdown of Value Sales for Rotary Friction Welding (RFW), Friction Stir Welding (FSW) and Linear Friction Welding (LFW) for the Years 2015, 2025 & 2030
- TABLE 110: Asia-Pacific Recent Past, Current & Future Analysis for Friction Welding by End-Use - Aerospace End-Use, Automotive End-Use, Shipbuilding End-Use, Railways End-Use and Other End-Uses - Independent Analysis of Annual Sales in US$ Thousand for the Years 2024 through 2030 and % CAGR
- TABLE 111: Asia-Pacific Historic Review for Friction Welding by End-Use - Aerospace End-Use, Automotive End-Use, Shipbuilding End-Use, Railways End-Use and Other End-Uses Markets - Independent Analysis of Annual Sales in US$ Thousand for Years 2015 through 2023 and % CAGR
- TABLE 112: Asia-Pacific 15-Year Perspective for Friction Welding by End-Use - Percentage Breakdown of Value Sales for Aerospace End-Use, Automotive End-Use, Shipbuilding End-Use, Railways End-Use and Other End-Uses for the Years 2015, 2025 & 2030
- AUSTRALIA
- Friction Welding Market Presence - Strong/Active/Niche/Trivial - Key Competitors in Australia for 2025 (E)
- TABLE 113: Australia Recent Past, Current & Future Analysis for Friction Welding by Welding Type - Rotary Friction Welding (RFW), Friction Stir Welding (FSW) and Linear Friction Welding (LFW) - Independent Analysis of Annual Sales in US$ Thousand for the Years 2024 through 2030 and % CAGR
- TABLE 114: Australia Historic Review for Friction Welding by Welding Type - Rotary Friction Welding (RFW), Friction Stir Welding (FSW) and Linear Friction Welding (LFW) Markets - Independent Analysis of Annual Sales in US$ Thousand for Years 2015 through 2023 and % CAGR
- TABLE 115: Australia 15-Year Perspective for Friction Welding by Welding Type - Percentage Breakdown of Value Sales for Rotary Friction Welding (RFW), Friction Stir Welding (FSW) and Linear Friction Welding (LFW) for the Years 2015, 2025 & 2030
- TABLE 116: Australia Recent Past, Current & Future Analysis for Friction Welding by End-Use - Aerospace End-Use, Automotive End-Use, Shipbuilding End-Use, Railways End-Use and Other End-Uses - Independent Analysis of Annual Sales in US$ Thousand for the Years 2024 through 2030 and % CAGR
- TABLE 117: Australia Historic Review for Friction Welding by End-Use - Aerospace End-Use, Automotive End-Use, Shipbuilding End-Use, Railways End-Use and Other End-Uses Markets - Independent Analysis of Annual Sales in US$ Thousand for Years 2015 through 2023 and % CAGR
- TABLE 118: Australia 15-Year Perspective for Friction Welding by End-Use - Percentage Breakdown of Value Sales for Aerospace End-Use, Automotive End-Use, Shipbuilding End-Use, Railways End-Use and Other End-Uses for the Years 2015, 2025 & 2030
- INDIA
- Friction Welding Market Presence - Strong/Active/Niche/Trivial - Key Competitors in India for 2025 (E)
- TABLE 119: India Recent Past, Current & Future Analysis for Friction Welding by Welding Type - Rotary Friction Welding (RFW), Friction Stir Welding (FSW) and Linear Friction Welding (LFW) - Independent Analysis of Annual Sales in US$ Thousand for the Years 2024 through 2030 and % CAGR
- TABLE 120: India Historic Review for Friction Welding by Welding Type - Rotary Friction Welding (RFW), Friction Stir Welding (FSW) and Linear Friction Welding (LFW) Markets - Independent Analysis of Annual Sales in US$ Thousand for Years 2015 through 2023 and % CAGR
- TABLE 121: India 15-Year Perspective for Friction Welding by Welding Type - Percentage Breakdown of Value Sales for Rotary Friction Welding (RFW), Friction Stir Welding (FSW) and Linear Friction Welding (LFW) for the Years 2015, 2025 & 2030
- TABLE 122: India Recent Past, Current & Future Analysis for Friction Welding by End-Use - Aerospace End-Use, Automotive End-Use, Shipbuilding End-Use, Railways End-Use and Other End-Uses - Independent Analysis of Annual Sales in US$ Thousand for the Years 2024 through 2030 and % CAGR
- TABLE 123: India Historic Review for Friction Welding by End-Use - Aerospace End-Use, Automotive End-Use, Shipbuilding End-Use, Railways End-Use and Other End-Uses Markets - Independent Analysis of Annual Sales in US$ Thousand for Years 2015 through 2023 and % CAGR
- TABLE 124: India 15-Year Perspective for Friction Welding by End-Use - Percentage Breakdown of Value Sales for Aerospace End-Use, Automotive End-Use, Shipbuilding End-Use, Railways End-Use and Other End-Uses for the Years 2015, 2025 & 2030
- SOUTH KOREA
- TABLE 125: South Korea Recent Past, Current & Future Analysis for Friction Welding by Welding Type - Rotary Friction Welding (RFW), Friction Stir Welding (FSW) and Linear Friction Welding (LFW) - Independent Analysis of Annual Sales in US$ Thousand for the Years 2024 through 2030 and % CAGR
- TABLE 126: South Korea Historic Review for Friction Welding by Welding Type - Rotary Friction Welding (RFW), Friction Stir Welding (FSW) and Linear Friction Welding (LFW) Markets - Independent Analysis of Annual Sales in US$ Thousand for Years 2015 through 2023 and % CAGR
- TABLE 127: South Korea 15-Year Perspective for Friction Welding by Welding Type - Percentage Breakdown of Value Sales for Rotary Friction Welding (RFW), Friction Stir Welding (FSW) and Linear Friction Welding (LFW) for the Years 2015, 2025 & 2030
- TABLE 128: South Korea Recent Past, Current & Future Analysis for Friction Welding by End-Use - Aerospace End-Use, Automotive End-Use, Shipbuilding End-Use, Railways End-Use and Other End-Uses - Independent Analysis of Annual Sales in US$ Thousand for the Years 2024 through 2030 and % CAGR
- TABLE 129: South Korea Historic Review for Friction Welding by End-Use - Aerospace End-Use, Automotive End-Use, Shipbuilding End-Use, Railways End-Use and Other End-Uses Markets - Independent Analysis of Annual Sales in US$ Thousand for Years 2015 through 2023 and % CAGR
- TABLE 130: South Korea 15-Year Perspective for Friction Welding by End-Use - Percentage Breakdown of Value Sales for Aerospace End-Use, Automotive End-Use, Shipbuilding End-Use, Railways End-Use and Other End-Uses for the Years 2015, 2025 & 2030
- REST OF ASIA-PACIFIC
- TABLE 131: Rest of Asia-Pacific Recent Past, Current & Future Analysis for Friction Welding by Welding Type - Rotary Friction Welding (RFW), Friction Stir Welding (FSW) and Linear Friction Welding (LFW) - Independent Analysis of Annual Sales in US$ Thousand for the Years 2024 through 2030 and % CAGR
- TABLE 132: Rest of Asia-Pacific Historic Review for Friction Welding by Welding Type - Rotary Friction Welding (RFW), Friction Stir Welding (FSW) and Linear Friction Welding (LFW) Markets - Independent Analysis of Annual Sales in US$ Thousand for Years 2015 through 2023 and % CAGR
- TABLE 133: Rest of Asia-Pacific 15-Year Perspective for Friction Welding by Welding Type - Percentage Breakdown of Value Sales for Rotary Friction Welding (RFW), Friction Stir Welding (FSW) and Linear Friction Welding (LFW) for the Years 2015, 2025 & 2030
- TABLE 134: Rest of Asia-Pacific Recent Past, Current & Future Analysis for Friction Welding by End-Use - Aerospace End-Use, Automotive End-Use, Shipbuilding End-Use, Railways End-Use and Other End-Uses - Independent Analysis of Annual Sales in US$ Thousand for the Years 2024 through 2030 and % CAGR
- TABLE 135: Rest of Asia-Pacific Historic Review for Friction Welding by End-Use - Aerospace End-Use, Automotive End-Use, Shipbuilding End-Use, Railways End-Use and Other End-Uses Markets - Independent Analysis of Annual Sales in US$ Thousand for Years 2015 through 2023 and % CAGR
- TABLE 136: Rest of Asia-Pacific 15-Year Perspective for Friction Welding by End-Use - Percentage Breakdown of Value Sales for Aerospace End-Use, Automotive End-Use, Shipbuilding End-Use, Railways End-Use and Other End-Uses for the Years 2015, 2025 & 2030
- LATIN AMERICA
- Friction Welding Market Presence - Strong/Active/Niche/Trivial - Key Competitors in Latin America for 2025 (E)
- TABLE 137: Latin America Recent Past, Current & Future Analysis for Friction Welding by Geographic Region - Argentina, Brazil, Mexico and Rest of Latin America Markets - Independent Analysis of Annual Sales in US$ Thousand for Years 2024 through 2030 and % CAGR
- TABLE 138: Latin America Historic Review for Friction Welding by Geographic Region - Argentina, Brazil, Mexico and Rest of Latin America Markets - Independent Analysis of Annual Sales in US$ Thousand for Years 2015 through 2023 and % CAGR
- TABLE 139: Latin America 15-Year Perspective for Friction Welding by Geographic Region - Percentage Breakdown of Value Sales for Argentina, Brazil, Mexico and Rest of Latin America Markets for Years 2015, 2025 & 2030
- TABLE 140: Latin America Recent Past, Current & Future Analysis for Friction Welding by Welding Type - Rotary Friction Welding (RFW), Friction Stir Welding (FSW) and Linear Friction Welding (LFW) - Independent Analysis of Annual Sales in US$ Thousand for the Years 2024 through 2030 and % CAGR
- TABLE 141: Latin America Historic Review for Friction Welding by Welding Type - Rotary Friction Welding (RFW), Friction Stir Welding (FSW) and Linear Friction Welding (LFW) Markets - Independent Analysis of Annual Sales in US$ Thousand for Years 2015 through 2023 and % CAGR
- TABLE 142: Latin America 15-Year Perspective for Friction Welding by Welding Type - Percentage Breakdown of Value Sales for Rotary Friction Welding (RFW), Friction Stir Welding (FSW) and Linear Friction Welding (LFW) for the Years 2015, 2025 & 2030
- TABLE 143: Latin America Recent Past, Current & Future Analysis for Friction Welding by End-Use - Aerospace End-Use, Automotive End-Use, Shipbuilding End-Use, Railways End-Use and Other End-Uses - Independent Analysis of Annual Sales in US$ Thousand for the Years 2024 through 2030 and % CAGR
- TABLE 144: Latin America Historic Review for Friction Welding by End-Use - Aerospace End-Use, Automotive End-Use, Shipbuilding End-Use, Railways End-Use and Other End-Uses Markets - Independent Analysis of Annual Sales in US$ Thousand for Years 2015 through 2023 and % CAGR
- TABLE 145: Latin America 15-Year Perspective for Friction Welding by End-Use - Percentage Breakdown of Value Sales for Aerospace End-Use, Automotive End-Use, Shipbuilding End-Use, Railways End-Use and Other End-Uses for the Years 2015, 2025 & 2030
- ARGENTINA
- TABLE 146: Argentina Recent Past, Current & Future Analysis for Friction Welding by Welding Type - Rotary Friction Welding (RFW), Friction Stir Welding (FSW) and Linear Friction Welding (LFW) - Independent Analysis of Annual Sales in US$ Thousand for the Years 2024 through 2030 and % CAGR
- TABLE 147: Argentina Historic Review for Friction Welding by Welding Type - Rotary Friction Welding (RFW), Friction Stir Welding (FSW) and Linear Friction Welding (LFW) Markets - Independent Analysis of Annual Sales in US$ Thousand for Years 2015 through 2023 and % CAGR
- TABLE 148: Argentina 15-Year Perspective for Friction Welding by Welding Type - Percentage Breakdown of Value Sales for Rotary Friction Welding (RFW), Friction Stir Welding (FSW) and Linear Friction Welding (LFW) for the Years 2015, 2025 & 2030
- TABLE 149: Argentina Recent Past, Current & Future Analysis for Friction Welding by End-Use - Aerospace End-Use, Automotive End-Use, Shipbuilding End-Use, Railways End-Use and Other End-Uses - Independent Analysis of Annual Sales in US$ Thousand for the Years 2024 through 2030 and % CAGR
- TABLE 150: Argentina Historic Review for Friction Welding by End-Use - Aerospace End-Use, Automotive End-Use, Shipbuilding End-Use, Railways End-Use and Other End-Uses Markets - Independent Analysis of Annual Sales in US$ Thousand for Years 2015 through 2023 and % CAGR
- TABLE 151: Argentina 15-Year Perspective for Friction Welding by End-Use - Percentage Breakdown of Value Sales for Aerospace End-Use, Automotive End-Use, Shipbuilding End-Use, Railways End-Use and Other End-Uses for the Years 2015, 2025 & 2030
- BRAZIL
- TABLE 152: Brazil Recent Past, Current & Future Analysis for Friction Welding by Welding Type - Rotary Friction Welding (RFW), Friction Stir Welding (FSW) and Linear Friction Welding (LFW) - Independent Analysis of Annual Sales in US$ Thousand for the Years 2024 through 2030 and % CAGR
- TABLE 153: Brazil Historic Review for Friction Welding by Welding Type - Rotary Friction Welding (RFW), Friction Stir Welding (FSW) and Linear Friction Welding (LFW) Markets - Independent Analysis of Annual Sales in US$ Thousand for Years 2015 through 2023 and % CAGR
- TABLE 154: Brazil 15-Year Perspective for Friction Welding by Welding Type - Percentage Breakdown of Value Sales for Rotary Friction Welding (RFW), Friction Stir Welding (FSW) and Linear Friction Welding (LFW) for the Years 2015, 2025 & 2030
- TABLE 155: Brazil Recent Past, Current & Future Analysis for Friction Welding by End-Use - Aerospace End-Use, Automotive End-Use, Shipbuilding End-Use, Railways End-Use and Other End-Uses - Independent Analysis of Annual Sales in US$ Thousand for the Years 2024 through 2030 and % CAGR
- TABLE 156: Brazil Historic Review for Friction Welding by End-Use - Aerospace End-Use, Automotive End-Use, Shipbuilding End-Use, Railways End-Use and Other End-Uses Markets - Independent Analysis of Annual Sales in US$ Thousand for Years 2015 through 2023 and % CAGR
- TABLE 157: Brazil 15-Year Perspective for Friction Welding by End-Use - Percentage Breakdown of Value Sales for Aerospace End-Use, Automotive End-Use, Shipbuilding End-Use, Railways End-Use and Other End-Uses for the Years 2015, 2025 & 2030
- MEXICO
- TABLE 158: Mexico Recent Past, Current & Future Analysis for Friction Welding by Welding Type - Rotary Friction Welding (RFW), Friction Stir Welding (FSW) and Linear Friction Welding (LFW) - Independent Analysis of Annual Sales in US$ Thousand for the Years 2024 through 2030 and % CAGR
- TABLE 159: Mexico Historic Review for Friction Welding by Welding Type - Rotary Friction Welding (RFW), Friction Stir Welding (FSW) and Linear Friction Welding (LFW) Markets - Independent Analysis of Annual Sales in US$ Thousand for Years 2015 through 2023 and % CAGR
- TABLE 160: Mexico 15-Year Perspective for Friction Welding by Welding Type - Percentage Breakdown of Value Sales for Rotary Friction Welding (RFW), Friction Stir Welding (FSW) and Linear Friction Welding (LFW) for the Years 2015, 2025 & 2030
- TABLE 161: Mexico Recent Past, Current & Future Analysis for Friction Welding by End-Use - Aerospace End-Use, Automotive End-Use, Shipbuilding End-Use, Railways End-Use and Other End-Uses - Independent Analysis of Annual Sales in US$ Thousand for the Years 2024 through 2030 and % CAGR
- TABLE 162: Mexico Historic Review for Friction Welding by End-Use - Aerospace End-Use, Automotive End-Use, Shipbuilding End-Use, Railways End-Use and Other End-Uses Markets - Independent Analysis of Annual Sales in US$ Thousand for Years 2015 through 2023 and % CAGR
- TABLE 163: Mexico 15-Year Perspective for Friction Welding by End-Use - Percentage Breakdown of Value Sales for Aerospace End-Use, Automotive End-Use, Shipbuilding End-Use, Railways End-Use and Other End-Uses for the Years 2015, 2025 & 2030
- REST OF LATIN AMERICA
- TABLE 164: Rest of Latin America Recent Past, Current & Future Analysis for Friction Welding by Welding Type - Rotary Friction Welding (RFW), Friction Stir Welding (FSW) and Linear Friction Welding (LFW) - Independent Analysis of Annual Sales in US$ Thousand for the Years 2024 through 2030 and % CAGR
- TABLE 165: Rest of Latin America Historic Review for Friction Welding by Welding Type - Rotary Friction Welding (RFW), Friction Stir Welding (FSW) and Linear Friction Welding (LFW) Markets - Independent Analysis of Annual Sales in US$ Thousand for Years 2015 through 2023 and % CAGR
- TABLE 166: Rest of Latin America 15-Year Perspective for Friction Welding by Welding Type - Percentage Breakdown of Value Sales for Rotary Friction Welding (RFW), Friction Stir Welding (FSW) and Linear Friction Welding (LFW) for the Years 2015, 2025 & 2030
- TABLE 167: Rest of Latin America Recent Past, Current & Future Analysis for Friction Welding by End-Use - Aerospace End-Use, Automotive End-Use, Shipbuilding End-Use, Railways End-Use and Other End-Uses - Independent Analysis of Annual Sales in US$ Thousand for the Years 2024 through 2030 and % CAGR
- TABLE 168: Rest of Latin America Historic Review for Friction Welding by End-Use - Aerospace End-Use, Automotive End-Use, Shipbuilding End-Use, Railways End-Use and Other End-Uses Markets - Independent Analysis of Annual Sales in US$ Thousand for Years 2015 through 2023 and % CAGR
- TABLE 169: Rest of Latin America 15-Year Perspective for Friction Welding by End-Use - Percentage Breakdown of Value Sales for Aerospace End-Use, Automotive End-Use, Shipbuilding End-Use, Railways End-Use and Other End-Uses for the Years 2015, 2025 & 2030
- MIDDLE EAST
- Friction Welding Market Presence - Strong/Active/Niche/Trivial - Key Competitors in Middle East for 2025 (E)
- TABLE 170: Middle East Recent Past, Current & Future Analysis for Friction Welding by Geographic Region - Iran, Israel, Saudi Arabia, UAE and Rest of Middle East Markets - Independent Analysis of Annual Sales in US$ Thousand for Years 2024 through 2030 and % CAGR
- TABLE 171: Middle East Historic Review for Friction Welding by Geographic Region - Iran, Israel, Saudi Arabia, UAE and Rest of Middle East Markets - Independent Analysis of Annual Sales in US$ Thousand for Years 2015 through 2023 and % CAGR
- TABLE 172: Middle East 15-Year Perspective for Friction Welding by Geographic Region - Percentage Breakdown of Value Sales for Iran, Israel, Saudi Arabia, UAE and Rest of Middle East Markets for Years 2015, 2025 & 2030
- TABLE 173: Middle East Recent Past, Current & Future Analysis for Friction Welding by Welding Type - Rotary Friction Welding (RFW), Friction Stir Welding (FSW) and Linear Friction Welding (LFW) - Independent Analysis of Annual Sales in US$ Thousand for the Years 2024 through 2030 and % CAGR
- TABLE 174: Middle East Historic Review for Friction Welding by Welding Type - Rotary Friction Welding (RFW), Friction Stir Welding (FSW) and Linear Friction Welding (LFW) Markets - Independent Analysis of Annual Sales in US$ Thousand for Years 2015 through 2023 and % CAGR
- TABLE 175: Middle East 15-Year Perspective for Friction Welding by Welding Type - Percentage Breakdown of Value Sales for Rotary Friction Welding (RFW), Friction Stir Welding (FSW) and Linear Friction Welding (LFW) for the Years 2015, 2025 & 2030
- TABLE 176: Middle East Recent Past, Current & Future Analysis for Friction Welding by End-Use - Aerospace End-Use, Automotive End-Use, Shipbuilding End-Use, Railways End-Use and Other End-Uses - Independent Analysis of Annual Sales in US$ Thousand for the Years 2024 through 2030 and % CAGR
- TABLE 177: Middle East Historic Review for Friction Welding by End-Use - Aerospace End-Use, Automotive End-Use, Shipbuilding End-Use, Railways End-Use and Other End-Uses Markets - Independent Analysis of Annual Sales in US$ Thousand for Years 2015 through 2023 and % CAGR
- TABLE 178: Middle East 15-Year Perspective for Friction Welding by End-Use - Percentage Breakdown of Value Sales for Aerospace End-Use, Automotive End-Use, Shipbuilding End-Use, Railways End-Use and Other End-Uses for the Years 2015, 2025 & 2030
- IRAN
- TABLE 179: Iran Recent Past, Current & Future Analysis for Friction Welding by Welding Type - Rotary Friction Welding (RFW), Friction Stir Welding (FSW) and Linear Friction Welding (LFW) - Independent Analysis of Annual Sales in US$ Thousand for the Years 2024 through 2030 and % CAGR
- TABLE 180: Iran Historic Review for Friction Welding by Welding Type - Rotary Friction Welding (RFW), Friction Stir Welding (FSW) and Linear Friction Welding (LFW) Markets - Independent Analysis of Annual Sales in US$ Thousand for Years 2015 through 2023 and % CAGR
- TABLE 181: Iran 15-Year Perspective for Friction Welding by Welding Type - Percentage Breakdown of Value Sales for Rotary Friction Welding (RFW), Friction Stir Welding (FSW) and Linear Friction Welding (LFW) for the Years 2015, 2025 & 2030
- TABLE 182: Iran Recent Past, Current & Future Analysis for Friction Welding by End-Use - Aerospace End-Use, Automotive End-Use, Shipbuilding End-Use, Railways End-Use and Other End-Uses - Independent Analysis of Annual Sales in US$ Thousand for the Years 2024 through 2030 and % CAGR
- TABLE 183: Iran Historic Review for Friction Welding by End-Use - Aerospace End-Use, Automotive End-Use, Shipbuilding End-Use, Railways End-Use and Other End-Uses Markets - Independent Analysis of Annual Sales in US$ Thousand for Years 2015 through 2023 and % CAGR
- TABLE 184: Iran 15-Year Perspective for Friction Welding by End-Use - Percentage Breakdown of Value Sales for Aerospace End-Use, Automotive End-Use, Shipbuilding End-Use, Railways End-Use and Other End-Uses for the Years 2015, 2025 & 2030
- ISRAEL
- TABLE 185: Israel Recent Past, Current & Future Analysis for Friction Welding by Welding Type - Rotary Friction Welding (RFW), Friction Stir Welding (FSW) and Linear Friction Welding (LFW) - Independent Analysis of Annual Sales in US$ Thousand for the Years 2024 through 2030 and % CAGR
- TABLE 186: Israel Historic Review for Friction Welding by Welding Type - Rotary Friction Welding (RFW), Friction Stir Welding (FSW) and Linear Friction Welding (LFW) Markets - Independent Analysis of Annual Sales in US$ Thousand for Years 2015 through 2023 and % CAGR
- TABLE 187: Israel 15-Year Perspective for Friction Welding by Welding Type - Percentage Breakdown of Value Sales for Rotary Friction Welding (RFW), Friction Stir Welding (FSW) and Linear Friction Welding (LFW) for the Years 2015, 2025 & 2030
- TABLE 188: Israel Recent Past, Current & Future Analysis for Friction Welding by End-Use - Aerospace End-Use, Automotive End-Use, Shipbuilding End-Use, Railways End-Use and Other End-Uses - Independent Analysis of Annual Sales in US$ Thousand for the Years 2024 through 2030 and % CAGR
- TABLE 189: Israel Historic Review for Friction Welding by End-Use - Aerospace End-Use, Automotive End-Use, Shipbuilding End-Use, Railways End-Use and Other End-Uses Markets - Independent Analysis of Annual Sales in US$ Thousand for Years 2015 through 2023 and % CAGR
- TABLE 190: Israel 15-Year Perspective for Friction Welding by End-Use - Percentage Breakdown of Value Sales for Aerospace End-Use, Automotive End-Use, Shipbuilding End-Use, Railways End-Use and Other End-Uses for the Years 2015, 2025 & 2030
- SAUDI ARABIA
- TABLE 191: Saudi Arabia Recent Past, Current & Future Analysis for Friction Welding by Welding Type - Rotary Friction Welding (RFW), Friction Stir Welding (FSW) and Linear Friction Welding (LFW) - Independent Analysis of Annual Sales in US$ Thousand for the Years 2024 through 2030 and % CAGR
- TABLE 192: Saudi Arabia Historic Review for Friction Welding by Welding Type - Rotary Friction Welding (RFW), Friction Stir Welding (FSW) and Linear Friction Welding (LFW) Markets - Independent Analysis of Annual Sales in US$ Thousand for Years 2015 through 2023 and % CAGR
- TABLE 193: Saudi Arabia 15-Year Perspective for Friction Welding by Welding Type - Percentage Breakdown of Value Sales for Rotary Friction Welding (RFW), Friction Stir Welding (FSW) and Linear Friction Welding (LFW) for the Years 2015, 2025 & 2030
- TABLE 194: Saudi Arabia Recent Past, Current & Future Analysis for Friction Welding by End-Use - Aerospace End-Use, Automotive End-Use, Shipbuilding End-Use, Railways End-Use and Other End-Uses - Independent Analysis of Annual Sales in US$ Thousand for the Years 2024 through 2030 and % CAGR
- TABLE 195: Saudi Arabia Historic Review for Friction Welding by End-Use - Aerospace End-Use, Automotive End-Use, Shipbuilding End-Use, Railways End-Use and Other End-Uses Markets - Independent Analysis of Annual Sales in US$ Thousand for Years 2015 through 2023 and % CAGR
- TABLE 196: Saudi Arabia 15-Year Perspective for Friction Welding by End-Use - Percentage Breakdown of Value Sales for Aerospace End-Use, Automotive End-Use, Shipbuilding End-Use, Railways End-Use and Other End-Uses for the Years 2015, 2025 & 2030
- UNITED ARAB EMIRATES
- TABLE 197: UAE Recent Past, Current & Future Analysis for Friction Welding by Welding Type - Rotary Friction Welding (RFW), Friction Stir Welding (FSW) and Linear Friction Welding (LFW) - Independent Analysis of Annual Sales in US$ Thousand for the Years 2024 through 2030 and % CAGR
- TABLE 198: UAE Historic Review for Friction Welding by Welding Type - Rotary Friction Welding (RFW), Friction Stir Welding (FSW) and Linear Friction Welding (LFW) Markets - Independent Analysis of Annual Sales in US$ Thousand for Years 2015 through 2023 and % CAGR
- TABLE 199: UAE 15-Year Perspective for Friction Welding by Welding Type - Percentage Breakdown of Value Sales for Rotary Friction Welding (RFW), Friction Stir Welding (FSW) and Linear Friction Welding (LFW) for the Years 2015, 2025 & 2030
- TABLE 200: UAE Recent Past, Current & Future Analysis for Friction Welding by End-Use - Aerospace End-Use, Automotive End-Use, Shipbuilding End-Use, Railways End-Use and Other End-Uses - Independent Analysis of Annual Sales in US$ Thousand for the Years 2024 through 2030 and % CAGR
- TABLE 201: UAE Historic Review for Friction Welding by End-Use - Aerospace End-Use, Automotive End-Use, Shipbuilding End-Use, Railways End-Use and Other End-Uses Markets - Independent Analysis of Annual Sales in US$ Thousand for Years 2015 through 2023 and % CAGR
- TABLE 202: UAE 15-Year Perspective for Friction Welding by End-Use - Percentage Breakdown of Value Sales for Aerospace End-Use, Automotive End-Use, Shipbuilding End-Use, Railways End-Use and Other End-Uses for the Years 2015, 2025 & 2030
- REST OF MIDDLE EAST
- TABLE 203: Rest of Middle East Recent Past, Current & Future Analysis for Friction Welding by Welding Type - Rotary Friction Welding (RFW), Friction Stir Welding (FSW) and Linear Friction Welding (LFW) - Independent Analysis of Annual Sales in US$ Thousand for the Years 2024 through 2030 and % CAGR
- TABLE 204: Rest of Middle East Historic Review for Friction Welding by Welding Type - Rotary Friction Welding (RFW), Friction Stir Welding (FSW) and Linear Friction Welding (LFW) Markets - Independent Analysis of Annual Sales in US$ Thousand for Years 2015 through 2023 and % CAGR
- TABLE 205: Rest of Middle East 15-Year Perspective for Friction Welding by Welding Type - Percentage Breakdown of Value Sales for Rotary Friction Welding (RFW), Friction Stir Welding (FSW) and Linear Friction Welding (LFW) for the Years 2015, 2025 & 2030
- TABLE 206: Rest of Middle East Recent Past, Current & Future Analysis for Friction Welding by End-Use - Aerospace End-Use, Automotive End-Use, Shipbuilding End-Use, Railways End-Use and Other End-Uses - Independent Analysis of Annual Sales in US$ Thousand for the Years 2024 through 2030 and % CAGR
- TABLE 207: Rest of Middle East Historic Review for Friction Welding by End-Use - Aerospace End-Use, Automotive End-Use, Shipbuilding End-Use, Railways End-Use and Other End-Uses Markets - Independent Analysis of Annual Sales in US$ Thousand for Years 2015 through 2023 and % CAGR
- TABLE 208: Rest of Middle East 15-Year Perspective for Friction Welding by End-Use - Percentage Breakdown of Value Sales for Aerospace End-Use, Automotive End-Use, Shipbuilding End-Use, Railways End-Use and Other End-Uses for the Years 2015, 2025 & 2030
- AFRICA
- Friction Welding Market Presence - Strong/Active/Niche/Trivial - Key Competitors in Africa for 2025 (E)
- TABLE 209: Africa Recent Past, Current & Future Analysis for Friction Welding by Welding Type - Rotary Friction Welding (RFW), Friction Stir Welding (FSW) and Linear Friction Welding (LFW) - Independent Analysis of Annual Sales in US$ Thousand for the Years 2024 through 2030 and % CAGR
- TABLE 210: Africa Historic Review for Friction Welding by Welding Type - Rotary Friction Welding (RFW), Friction Stir Welding (FSW) and Linear Friction Welding (LFW) Markets - Independent Analysis of Annual Sales in US$ Thousand for Years 2015 through 2023 and % CAGR
- TABLE 211: Africa 15-Year Perspective for Friction Welding by Welding Type - Percentage Breakdown of Value Sales for Rotary Friction Welding (RFW), Friction Stir Welding (FSW) and Linear Friction Welding (LFW) for the Years 2015, 2025 & 2030
- TABLE 212: Africa Recent Past, Current & Future Analysis for Friction Welding by End-Use - Aerospace End-Use, Automotive End-Use, Shipbuilding End-Use, Railways End-Use and Other End-Uses - Independent Analysis of Annual Sales in US$ Thousand for the Years 2024 through 2030 and % CAGR
- TABLE 213: Africa Historic Review for Friction Welding by End-Use - Aerospace End-Use, Automotive End-Use, Shipbuilding End-Use, Railways End-Use and Other End-Uses Markets - Independent Analysis of Annual Sales in US$ Thousand for Years 2015 through 2023 and % CAGR
- TABLE 214: Africa 15-Year Perspective for Friction Welding by End-Use - Percentage Breakdown of Value Sales for Aerospace End-Use, Automotive End-Use, Shipbuilding End-Use, Railways End-Use and Other End-Uses for the Years 2015, 2025 & 2030
- IV. COMPETITION
Pricing
Currency Rates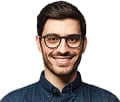