
Computer Integrated Manufacturing
Description
Global Computer Integrated Manufacturing Market to Reach US$31.7 Billion by 2030
The global market for Computer Integrated Manufacturing estimated at US$22.8 Billion in the year 2024, is expected to reach US$31.7 Billion by 2030, growing at a CAGR of 5.6% over the analysis period 2024-2030. Computer-Aided Design Manufacturing, one of the segments analyzed in the report, is expected to record a 5.0% CAGR and reach US$18.4 Billion by the end of the analysis period. Growth in the Computer-Aided Manufacturing segment is estimated at 6.4% CAGR over the analysis period.
The U.S. Market is Estimated at US$6.2 Billion While China is Forecast to Grow at 8.8% CAGR
The Computer Integrated Manufacturing market in the U.S. is estimated at US$6.2 Billion in the year 2024. China, the world`s second largest economy, is forecast to reach a projected market size of US$6.4 Billion by the year 2030 trailing a CAGR of 8.8% over the analysis period 2024-2030. Among the other noteworthy geographic markets are Japan and Canada, each forecast to grow at a CAGR of 2.8% and 5.5% respectively over the analysis period. Within Europe, Germany is forecast to grow at approximately 3.7% CAGR.
Global Computer Integrated Manufacturing Market – Key Trends & Drivers Summarized
How Is Computer Integrated Manufacturing Reshaping Modern Industrial Production?
Computer Integrated Manufacturing (CIM) is fundamentally transforming how factories and production systems are managed by integrating all aspects of the manufacturing process—from design and engineering to production, quality control, and supply chain logistics—into a unified digital environment. At its core, CIM leverages computer-aided design (CAD), computer-aided manufacturing (CAM), computer-aided engineering (CAE), enterprise resource planning (ERP), and real-time machine monitoring systems to create fully connected, automated production environments. This integration results in synchronized workflows, improved traceability, and the ability to react quickly to market and customer demands.
One of the key advantages of CIM is the elimination of data silos between departments, enabling real-time decision-making and seamless communication across the product lifecycle. In industries such as automotive, aerospace, and precision electronics, where complex assemblies require high precision and minimal error tolerance, CIM ensures that design intent is faithfully translated into final output with reduced reliance on manual intervention. The tight integration of systems enables agile manufacturing models, where product customization, batch size flexibility, and rapid time-to-market become competitive differentiators. With digital twin technologies and cloud-based analytics now integrated into CIM environments, manufacturers gain deeper insights into production efficiency and system health, enabling continuous improvement and predictive maintenance strategies.
What Role Does Automation and Interconnectivity Play in Advancing CIM Ecosystems?
The evolution of CIM is closely tied to the proliferation of industrial automation and the Industrial Internet of Things (IIoT). Today’s CIM systems are embedded with sensors, robotics, and edge computing capabilities that collect and analyze production data in real-time. This enables smart factory operations where machines not only perform tasks autonomously but also adapt to environmental and operational changes through feedback loops. Robotic systems, machine vision, and programmable logic controllers (PLCs) work in tandem to optimize production speed, reduce waste, and uphold quality consistency across high-throughput lines.
Interconnectivity across machines, systems, and software platforms is further enhanced by standardized communication protocols such as OPC-UA and MQTT, which facilitate machine-to-machine (M2M) interaction and data synchronization across the enterprise. Integration with supply chain systems allows manufacturers to align production schedules with inventory levels, customer orders, and vendor logistics, thereby improving resource utilization and reducing production lead times. Moreover, CIM platforms now incorporate cybersecurity frameworks to protect data integrity and ensure operational continuity in the face of growing cyber threats. These advanced, interconnected systems not only increase output efficiency but also provide the resilience and agility needed in today’s volatile manufacturing landscape.
How Are Industry Verticals Leveraging CIM for Competitive Advantage?
CIM adoption is accelerating across a broad spectrum of industries, each leveraging it to solve domain-specific challenges. In the automotive sector, CIM facilitates just-in-time manufacturing, lean inventory practices, and real-time coordination across global assembly plants. For aerospace manufacturers, the precision and traceability offered by CIM systems are critical for regulatory compliance, weight optimization, and part standardization across complex supply chains. Similarly, in electronics manufacturing, where time-to-market is crucial and design iterations are frequent, CIM platforms support fast prototyping, high-volume precision production, and rapid changeovers.
The food and beverage industry is utilizing CIM for batch process automation, traceability, and compliance with food safety standards, while pharmaceuticals rely on it to enable continuous manufacturing, electronic batch records, and data integrity for audits. Heavy machinery and industrial equipment producers use CIM to integrate design customization with large-scale fabrication processes, reducing rework and ensuring consistent product quality. Even the renewable energy sector is adopting CIM to streamline production of complex components such as wind turbine blades or solar modules. This cross-industry expansion underscores CIM’s versatility and growing importance in supporting high-mix, high-complexity, and digitally driven production environments.
What Are the Forces Driving the Surge in Computer Integrated Manufacturing Adoption?
The growth in the computer integrated manufacturing market is driven by several factors rooted in technological evolution, operational complexity, and industry-specific requirements. A primary driver is the increasing demand for smart factory solutions that combine automation, real-time data access, and remote operation capabilities across discrete and process manufacturing sectors. The growing use of industrial robotics, advanced machine tools, and intelligent sensors has created the need for unified platforms that can coordinate diverse production assets efficiently. Additionally, the rising emphasis on product customization and shortened lifecycle times is compelling manufacturers to adopt CIM solutions for faster product iterations and agile production workflows.
The proliferation of digital twins, AI-powered decision-making tools, and cloud-based infrastructure is further pushing the demand for integrated systems that can simulate, analyze, and optimize entire production ecosystems. In parallel, regulatory frameworks across sectors such as pharmaceuticals, food, and aerospace are requiring tighter quality control and traceability—capabilities that CIM inherently provides. The shift toward sustainable manufacturing practices, with a focus on energy efficiency and waste reduction, is also encouraging investment in CIM systems capable of tracking and optimizing resource consumption. Finally, as global supply chains become increasingly complex and digitally connected, the need for end-to-end integration—from design to delivery—is making CIM an essential enabler of next-generation industrial competitiveness.
SCOPE OF STUDY:The report analyzes the Computer Integrated Manufacturing market in terms of units by the following Segments, and Geographic Regions/Countries:
Segments:
Manufacturing Type (Computer-Aided Design Manufacturing, Computer-Aided Manufacturing, Digital Manufacturing); Organization Size (Large Enterprises, SMEs)
Geographic Regions/Countries:
World; United States; Canada; Japan; China; Europe (France; Germany; Italy; United Kingdom; Spain; Russia; and Rest of Europe); Asia-Pacific (Australia; India; South Korea; and Rest of Asia-Pacific); Latin America (Argentina; Brazil; Mexico; and Rest of Latin America); Middle East (Iran; Israel; Saudi Arabia; United Arab Emirates; and Rest of Middle East); and Africa.
Select Competitors (Total 42 Featured) -
- ABB Ltd
- Aspen Technology, Inc.
- Dassault Systèmes SE
- Emerson Electric Co.
- FANUC Corporation
- General Electric Company
- Honeywell International Inc.
- IBM Corporation
- Mitsubishi Electric Corporation
- National Instruments Corporation
- Oracle Corporation
- Panasonic Corporation
- PTC Inc.
- Rockwell Automation, Inc.
- SAP SE
- Schneider Electric SE
- Siemens AG
- Software AG
- Toshiba Corporation
- Zebra Technologies Corporation
We`re transforming market and competitive intelligence with validated expert content and AI tools.
Instead of following the general norm of querying LLMs and Industry-specific SLMs, we built repositories of content curated from domain experts worldwide including video transcripts, blogs, search engines research, and massive amounts of enterprise, product/service, and market data.
TARIFF IMPACT FACTOR
Our new release incorporates impact of tariffs on geographical markets as we predict a shift in competitiveness of companies based on HQ country, manufacturing base, exports and imports (finished goods and OEM). This intricate and multifaceted market reality will impact competitors by increasing the Cost of Goods Sold (COGS), reducing profitability, reconfiguring supply chains, amongst other micro and macro market dynamics.
Please note: Reports are sold as single-site single-user licenses. Electronic versions require 24-48 hours as each copy is customized to the client with digital controls and custom watermarks. The Publisher uses digital controls protecting against copying and printing is restricted to one full copy to be used at the same location.
The latest version of Adobe Acrobat Reader is required to view the report. Upon ordering an electronic version, the Publisher will provide a link to download the purchased report.
Prior to fulfillment of an order, the client will be required to sign a document detailing the purchase terms for a publication from this publisher.
Table of Contents
- I. METHODOLOGY
- II. EXECUTIVE SUMMARY
- 1. MARKET OVERVIEW
- Influencer Market Insights
- World Market Trajectories
- Tariff Impact on Global Supply Chain Patterns
- Computer Integrated Manufacturing – Global Key Competitors Percentage Market Share in 2025 (E)
- Competitive Market Presence - Strong/Active/Niche/Trivial for Players Worldwide in 2025 (E)
- 2. FOCUS ON SELECT PLAYERS
- 3. MARKET TRENDS & DRIVERS
- Rising Demand for End-to-End Automation in Manufacturing Throws the Spotlight on Computer Integrated Manufacturing (CIM)
- Industry 4.0 Transformation Accelerates Adoption of Digitally Connected, AI-Enabled Manufacturing Workflows
- OEM Focus on Reducing Lead Times and Downtime Strengthens Business Case for CIM in High-Volume Production Environments
- Integration of CAD/CAM/CAE Platforms Enables Seamless Transition from Product Design to Real-Time Production
- Growth in Smart Factory Initiatives Drives Investment in CIM for Synchronized Machine, Material, and Workflow Management
- Surge in Demand for Mass Customization Supports Flexible, Software-Driven Manufacturing Configurations
- Rising Adoption of Industrial IoT and Cyber-Physical Systems Enhances Real-Time Monitoring and Control Capabilities
- CIM-Focused Robotics and PLC Integration Streamline Repetitive and Precision-Based Production Tasks
- OEM Innovations in Simulation, Virtual Commissioning, and Digital Twin Technology Support Predictive Manufacturing Operations
- Increasing Pressure for Quality Control and Traceability Drives Use of Integrated CIM Systems with QA Modules
- Expansion of Additive Manufacturing Supports CIM Integration for Hybrid Production Environments
- 4. GLOBAL MARKET PERSPECTIVE
- TABLE 1: World Computer Integrated Manufacturing Market Analysis of Annual Sales in US$ Million for Years 2014 through 2030
- TABLE 2: World Recent Past, Current & Future Analysis for Computer Integrated Manufacturing by Geographic Region - USA, Canada, Japan, China, Europe, Asia-Pacific, Latin America, Middle East and Africa Markets - Independent Analysis of Annual Sales in US$ Million for Years 2024 through 2030 and % CAGR
- TABLE 3: World Historic Review for Computer Integrated Manufacturing by Geographic Region - USA, Canada, Japan, China, Europe, Asia-Pacific, Latin America, Middle East and Africa Markets - Independent Analysis of Annual Sales in US$ Million for Years 2014 through 2023 and % CAGR
- TABLE 4: World 16-Year Perspective for Computer Integrated Manufacturing by Geographic Region - Percentage Breakdown of Value Sales for USA, Canada, Japan, China, Europe, Asia-Pacific, Latin America, Middle East and Africa Markets for Years 2014, 2025 & 2030
- TABLE 5: World Recent Past, Current & Future Analysis for Computer-Aided Design Manufacturing by Geographic Region - USA, Canada, Japan, China, Europe, Asia-Pacific, Latin America, Middle East and Africa Markets - Independent Analysis of Annual Sales in US$ Million for Years 2024 through 2030 and % CAGR
- TABLE 6: World Historic Review for Computer-Aided Design Manufacturing by Geographic Region - USA, Canada, Japan, China, Europe, Asia-Pacific, Latin America, Middle East and Africa Markets - Independent Analysis of Annual Sales in US$ Million for Years 2014 through 2023 and % CAGR
- TABLE 7: World 16-Year Perspective for Computer-Aided Design Manufacturing by Geographic Region - Percentage Breakdown of Value Sales for USA, Canada, Japan, China, Europe, Asia-Pacific, Latin America, Middle East and Africa for Years 2014, 2025 & 2030
- TABLE 8: World Recent Past, Current & Future Analysis for Computer-Aided Manufacturing by Geographic Region - USA, Canada, Japan, China, Europe, Asia-Pacific, Latin America, Middle East and Africa Markets - Independent Analysis of Annual Sales in US$ Million for Years 2024 through 2030 and % CAGR
- TABLE 9: World Historic Review for Computer-Aided Manufacturing by Geographic Region - USA, Canada, Japan, China, Europe, Asia-Pacific, Latin America, Middle East and Africa Markets - Independent Analysis of Annual Sales in US$ Million for Years 2014 through 2023 and % CAGR
- TABLE 10: World 16-Year Perspective for Computer-Aided Manufacturing by Geographic Region - Percentage Breakdown of Value Sales for USA, Canada, Japan, China, Europe, Asia-Pacific, Latin America, Middle East and Africa for Years 2014, 2025 & 2030
- TABLE 11: World Recent Past, Current & Future Analysis for Digital Manufacturing by Geographic Region - USA, Canada, Japan, China, Europe, Asia-Pacific, Latin America, Middle East and Africa Markets - Independent Analysis of Annual Sales in US$ Million for Years 2024 through 2030 and % CAGR
- TABLE 12: World Historic Review for Digital Manufacturing by Geographic Region - USA, Canada, Japan, China, Europe, Asia-Pacific, Latin America, Middle East and Africa Markets - Independent Analysis of Annual Sales in US$ Million for Years 2014 through 2023 and % CAGR
- TABLE 13: World 16-Year Perspective for Digital Manufacturing by Geographic Region - Percentage Breakdown of Value Sales for USA, Canada, Japan, China, Europe, Asia-Pacific, Latin America, Middle East and Africa for Years 2014, 2025 & 2030
- TABLE 14: World Recent Past, Current & Future Analysis for Large Enterprises by Geographic Region - USA, Canada, Japan, China, Europe, Asia-Pacific, Latin America, Middle East and Africa Markets - Independent Analysis of Annual Sales in US$ Million for Years 2024 through 2030 and % CAGR
- TABLE 15: World Historic Review for Large Enterprises by Geographic Region - USA, Canada, Japan, China, Europe, Asia-Pacific, Latin America, Middle East and Africa Markets - Independent Analysis of Annual Sales in US$ Million for Years 2014 through 2023 and % CAGR
- TABLE 16: World 16-Year Perspective for Large Enterprises by Geographic Region - Percentage Breakdown of Value Sales for USA, Canada, Japan, China, Europe, Asia-Pacific, Latin America, Middle East and Africa for Years 2014, 2025 & 2030
- TABLE 17: World Recent Past, Current & Future Analysis for SMEs by Geographic Region - USA, Canada, Japan, China, Europe, Asia-Pacific, Latin America, Middle East and Africa Markets - Independent Analysis of Annual Sales in US$ Million for Years 2024 through 2030 and % CAGR
- TABLE 18: World Historic Review for SMEs by Geographic Region - USA, Canada, Japan, China, Europe, Asia-Pacific, Latin America, Middle East and Africa Markets - Independent Analysis of Annual Sales in US$ Million for Years 2014 through 2023 and % CAGR
- TABLE 19: World 16-Year Perspective for SMEs by Geographic Region - Percentage Breakdown of Value Sales for USA, Canada, Japan, China, Europe, Asia-Pacific, Latin America, Middle East and Africa for Years 2014, 2025 & 2030
- III. MARKET ANALYSIS
- UNITED STATES
- Computer Integrated Manufacturing Market Presence - Strong/Active/Niche/Trivial - Key Competitors in the United States for 2025 (E)
- TABLE 20: USA Recent Past, Current & Future Analysis for Computer Integrated Manufacturing by Manufacturing Type - Computer-Aided Design Manufacturing, Computer-Aided Manufacturing and Digital Manufacturing - Independent Analysis of Annual Sales in US$ Million for the Years 2024 through 2030 and % CAGR
- TABLE 21: USA Historic Review for Computer Integrated Manufacturing by Manufacturing Type - Computer-Aided Design Manufacturing, Computer-Aided Manufacturing and Digital Manufacturing Markets - Independent Analysis of Annual Sales in US$ Million for Years 2014 through 2023 and % CAGR
- TABLE 22: USA 16-Year Perspective for Computer Integrated Manufacturing by Manufacturing Type - Percentage Breakdown of Value Sales for Computer-Aided Design Manufacturing, Computer-Aided Manufacturing and Digital Manufacturing for the Years 2014, 2025 & 2030
- TABLE 23: USA Recent Past, Current & Future Analysis for Computer Integrated Manufacturing by Organization Size - Large Enterprises and SMEs - Independent Analysis of Annual Sales in US$ Million for the Years 2024 through 2030 and % CAGR
- TABLE 24: USA Historic Review for Computer Integrated Manufacturing by Organization Size - Large Enterprises and SMEs Markets - Independent Analysis of Annual Sales in US$ Million for Years 2014 through 2023 and % CAGR
- TABLE 25: USA 16-Year Perspective for Computer Integrated Manufacturing by Organization Size - Percentage Breakdown of Value Sales for Large Enterprises and SMEs for the Years 2014, 2025 & 2030
- CANADA
- TABLE 26: Canada Recent Past, Current & Future Analysis for Computer Integrated Manufacturing by Manufacturing Type - Computer-Aided Design Manufacturing, Computer-Aided Manufacturing and Digital Manufacturing - Independent Analysis of Annual Sales in US$ Million for the Years 2024 through 2030 and % CAGR
- TABLE 27: Canada Historic Review for Computer Integrated Manufacturing by Manufacturing Type - Computer-Aided Design Manufacturing, Computer-Aided Manufacturing and Digital Manufacturing Markets - Independent Analysis of Annual Sales in US$ Million for Years 2014 through 2023 and % CAGR
- TABLE 28: Canada 16-Year Perspective for Computer Integrated Manufacturing by Manufacturing Type - Percentage Breakdown of Value Sales for Computer-Aided Design Manufacturing, Computer-Aided Manufacturing and Digital Manufacturing for the Years 2014, 2025 & 2030
- TABLE 29: Canada Recent Past, Current & Future Analysis for Computer Integrated Manufacturing by Organization Size - Large Enterprises and SMEs - Independent Analysis of Annual Sales in US$ Million for the Years 2024 through 2030 and % CAGR
- TABLE 30: Canada Historic Review for Computer Integrated Manufacturing by Organization Size - Large Enterprises and SMEs Markets - Independent Analysis of Annual Sales in US$ Million for Years 2014 through 2023 and % CAGR
- TABLE 31: Canada 16-Year Perspective for Computer Integrated Manufacturing by Organization Size - Percentage Breakdown of Value Sales for Large Enterprises and SMEs for the Years 2014, 2025 & 2030
- JAPAN
- Computer Integrated Manufacturing Market Presence - Strong/Active/Niche/Trivial - Key Competitors in Japan for 2025 (E)
- TABLE 32: Japan Recent Past, Current & Future Analysis for Computer Integrated Manufacturing by Manufacturing Type - Computer-Aided Design Manufacturing, Computer-Aided Manufacturing and Digital Manufacturing - Independent Analysis of Annual Sales in US$ Million for the Years 2024 through 2030 and % CAGR
- TABLE 33: Japan Historic Review for Computer Integrated Manufacturing by Manufacturing Type - Computer-Aided Design Manufacturing, Computer-Aided Manufacturing and Digital Manufacturing Markets - Independent Analysis of Annual Sales in US$ Million for Years 2014 through 2023 and % CAGR
- TABLE 34: Japan 16-Year Perspective for Computer Integrated Manufacturing by Manufacturing Type - Percentage Breakdown of Value Sales for Computer-Aided Design Manufacturing, Computer-Aided Manufacturing and Digital Manufacturing for the Years 2014, 2025 & 2030
- TABLE 35: Japan Recent Past, Current & Future Analysis for Computer Integrated Manufacturing by Organization Size - Large Enterprises and SMEs - Independent Analysis of Annual Sales in US$ Million for the Years 2024 through 2030 and % CAGR
- TABLE 36: Japan Historic Review for Computer Integrated Manufacturing by Organization Size - Large Enterprises and SMEs Markets - Independent Analysis of Annual Sales in US$ Million for Years 2014 through 2023 and % CAGR
- TABLE 37: Japan 16-Year Perspective for Computer Integrated Manufacturing by Organization Size - Percentage Breakdown of Value Sales for Large Enterprises and SMEs for the Years 2014, 2025 & 2030
- CHINA
- Computer Integrated Manufacturing Market Presence - Strong/Active/Niche/Trivial - Key Competitors in China for 2025 (E)
- TABLE 38: China Recent Past, Current & Future Analysis for Computer Integrated Manufacturing by Manufacturing Type - Computer-Aided Design Manufacturing, Computer-Aided Manufacturing and Digital Manufacturing - Independent Analysis of Annual Sales in US$ Million for the Years 2024 through 2030 and % CAGR
- TABLE 39: China Historic Review for Computer Integrated Manufacturing by Manufacturing Type - Computer-Aided Design Manufacturing, Computer-Aided Manufacturing and Digital Manufacturing Markets - Independent Analysis of Annual Sales in US$ Million for Years 2014 through 2023 and % CAGR
- TABLE 40: China 16-Year Perspective for Computer Integrated Manufacturing by Manufacturing Type - Percentage Breakdown of Value Sales for Computer-Aided Design Manufacturing, Computer-Aided Manufacturing and Digital Manufacturing for the Years 2014, 2025 & 2030
- TABLE 41: China Recent Past, Current & Future Analysis for Computer Integrated Manufacturing by Organization Size - Large Enterprises and SMEs - Independent Analysis of Annual Sales in US$ Million for the Years 2024 through 2030 and % CAGR
- TABLE 42: China Historic Review for Computer Integrated Manufacturing by Organization Size - Large Enterprises and SMEs Markets - Independent Analysis of Annual Sales in US$ Million for Years 2014 through 2023 and % CAGR
- TABLE 43: China 16-Year Perspective for Computer Integrated Manufacturing by Organization Size - Percentage Breakdown of Value Sales for Large Enterprises and SMEs for the Years 2014, 2025 & 2030
- EUROPE
- Computer Integrated Manufacturing Market Presence - Strong/Active/Niche/Trivial - Key Competitors in Europe for 2025 (E)
- TABLE 44: Europe Recent Past, Current & Future Analysis for Computer Integrated Manufacturing by Geographic Region - France, Germany, Italy, UK, Spain, Russia and Rest of Europe Markets - Independent Analysis of Annual Sales in US$ Million for Years 2024 through 2030 and % CAGR
- TABLE 45: Europe Historic Review for Computer Integrated Manufacturing by Geographic Region - France, Germany, Italy, UK, Spain, Russia and Rest of Europe Markets - Independent Analysis of Annual Sales in US$ Million for Years 2014 through 2023 and % CAGR
- TABLE 46: Europe 16-Year Perspective for Computer Integrated Manufacturing by Geographic Region - Percentage Breakdown of Value Sales for France, Germany, Italy, UK, Spain, Russia and Rest of Europe Markets for Years 2014, 2025 & 2030
- TABLE 47: Europe Recent Past, Current & Future Analysis for Computer Integrated Manufacturing by Manufacturing Type - Computer-Aided Design Manufacturing, Computer-Aided Manufacturing and Digital Manufacturing - Independent Analysis of Annual Sales in US$ Million for the Years 2024 through 2030 and % CAGR
- TABLE 48: Europe Historic Review for Computer Integrated Manufacturing by Manufacturing Type - Computer-Aided Design Manufacturing, Computer-Aided Manufacturing and Digital Manufacturing Markets - Independent Analysis of Annual Sales in US$ Million for Years 2014 through 2023 and % CAGR
- TABLE 49: Europe 16-Year Perspective for Computer Integrated Manufacturing by Manufacturing Type - Percentage Breakdown of Value Sales for Computer-Aided Design Manufacturing, Computer-Aided Manufacturing and Digital Manufacturing for the Years 2014, 2025 & 2030
- TABLE 50: Europe Recent Past, Current & Future Analysis for Computer Integrated Manufacturing by Organization Size - Large Enterprises and SMEs - Independent Analysis of Annual Sales in US$ Million for the Years 2024 through 2030 and % CAGR
- TABLE 51: Europe Historic Review for Computer Integrated Manufacturing by Organization Size - Large Enterprises and SMEs Markets - Independent Analysis of Annual Sales in US$ Million for Years 2014 through 2023 and % CAGR
- TABLE 52: Europe 16-Year Perspective for Computer Integrated Manufacturing by Organization Size - Percentage Breakdown of Value Sales for Large Enterprises and SMEs for the Years 2014, 2025 & 2030
- FRANCE
- Computer Integrated Manufacturing Market Presence - Strong/Active/Niche/Trivial - Key Competitors in France for 2025 (E)
- TABLE 53: France Recent Past, Current & Future Analysis for Computer Integrated Manufacturing by Manufacturing Type - Computer-Aided Design Manufacturing, Computer-Aided Manufacturing and Digital Manufacturing - Independent Analysis of Annual Sales in US$ Million for the Years 2024 through 2030 and % CAGR
- TABLE 54: France Historic Review for Computer Integrated Manufacturing by Manufacturing Type - Computer-Aided Design Manufacturing, Computer-Aided Manufacturing and Digital Manufacturing Markets - Independent Analysis of Annual Sales in US$ Million for Years 2014 through 2023 and % CAGR
- TABLE 55: France 16-Year Perspective for Computer Integrated Manufacturing by Manufacturing Type - Percentage Breakdown of Value Sales for Computer-Aided Design Manufacturing, Computer-Aided Manufacturing and Digital Manufacturing for the Years 2014, 2025 & 2030
- TABLE 56: France Recent Past, Current & Future Analysis for Computer Integrated Manufacturing by Organization Size - Large Enterprises and SMEs - Independent Analysis of Annual Sales in US$ Million for the Years 2024 through 2030 and % CAGR
- TABLE 57: France Historic Review for Computer Integrated Manufacturing by Organization Size - Large Enterprises and SMEs Markets - Independent Analysis of Annual Sales in US$ Million for Years 2014 through 2023 and % CAGR
- TABLE 58: France 16-Year Perspective for Computer Integrated Manufacturing by Organization Size - Percentage Breakdown of Value Sales for Large Enterprises and SMEs for the Years 2014, 2025 & 2030
- GERMANY
- Computer Integrated Manufacturing Market Presence - Strong/Active/Niche/Trivial - Key Competitors in Germany for 2025 (E)
- TABLE 59: Germany Recent Past, Current & Future Analysis for Computer Integrated Manufacturing by Manufacturing Type - Computer-Aided Design Manufacturing, Computer-Aided Manufacturing and Digital Manufacturing - Independent Analysis of Annual Sales in US$ Million for the Years 2024 through 2030 and % CAGR
- TABLE 60: Germany Historic Review for Computer Integrated Manufacturing by Manufacturing Type - Computer-Aided Design Manufacturing, Computer-Aided Manufacturing and Digital Manufacturing Markets - Independent Analysis of Annual Sales in US$ Million for Years 2014 through 2023 and % CAGR
- TABLE 61: Germany 16-Year Perspective for Computer Integrated Manufacturing by Manufacturing Type - Percentage Breakdown of Value Sales for Computer-Aided Design Manufacturing, Computer-Aided Manufacturing and Digital Manufacturing for the Years 2014, 2025 & 2030
- TABLE 62: Germany Recent Past, Current & Future Analysis for Computer Integrated Manufacturing by Organization Size - Large Enterprises and SMEs - Independent Analysis of Annual Sales in US$ Million for the Years 2024 through 2030 and % CAGR
- TABLE 63: Germany Historic Review for Computer Integrated Manufacturing by Organization Size - Large Enterprises and SMEs Markets - Independent Analysis of Annual Sales in US$ Million for Years 2014 through 2023 and % CAGR
- TABLE 64: Germany 16-Year Perspective for Computer Integrated Manufacturing by Organization Size - Percentage Breakdown of Value Sales for Large Enterprises and SMEs for the Years 2014, 2025 & 2030
- ITALY
- TABLE 65: Italy Recent Past, Current & Future Analysis for Computer Integrated Manufacturing by Manufacturing Type - Computer-Aided Design Manufacturing, Computer-Aided Manufacturing and Digital Manufacturing - Independent Analysis of Annual Sales in US$ Million for the Years 2024 through 2030 and % CAGR
- TABLE 66: Italy Historic Review for Computer Integrated Manufacturing by Manufacturing Type - Computer-Aided Design Manufacturing, Computer-Aided Manufacturing and Digital Manufacturing Markets - Independent Analysis of Annual Sales in US$ Million for Years 2014 through 2023 and % CAGR
- TABLE 67: Italy 16-Year Perspective for Computer Integrated Manufacturing by Manufacturing Type - Percentage Breakdown of Value Sales for Computer-Aided Design Manufacturing, Computer-Aided Manufacturing and Digital Manufacturing for the Years 2014, 2025 & 2030
- TABLE 68: Italy Recent Past, Current & Future Analysis for Computer Integrated Manufacturing by Organization Size - Large Enterprises and SMEs - Independent Analysis of Annual Sales in US$ Million for the Years 2024 through 2030 and % CAGR
- TABLE 69: Italy Historic Review for Computer Integrated Manufacturing by Organization Size - Large Enterprises and SMEs Markets - Independent Analysis of Annual Sales in US$ Million for Years 2014 through 2023 and % CAGR
- TABLE 70: Italy 16-Year Perspective for Computer Integrated Manufacturing by Organization Size - Percentage Breakdown of Value Sales for Large Enterprises and SMEs for the Years 2014, 2025 & 2030
- UNITED KINGDOM
- Computer Integrated Manufacturing Market Presence - Strong/Active/Niche/Trivial - Key Competitors in the United Kingdom for 2025 (E)
- TABLE 71: UK Recent Past, Current & Future Analysis for Computer Integrated Manufacturing by Manufacturing Type - Computer-Aided Design Manufacturing, Computer-Aided Manufacturing and Digital Manufacturing - Independent Analysis of Annual Sales in US$ Million for the Years 2024 through 2030 and % CAGR
- TABLE 72: UK Historic Review for Computer Integrated Manufacturing by Manufacturing Type - Computer-Aided Design Manufacturing, Computer-Aided Manufacturing and Digital Manufacturing Markets - Independent Analysis of Annual Sales in US$ Million for Years 2014 through 2023 and % CAGR
- TABLE 73: UK 16-Year Perspective for Computer Integrated Manufacturing by Manufacturing Type - Percentage Breakdown of Value Sales for Computer-Aided Design Manufacturing, Computer-Aided Manufacturing and Digital Manufacturing for the Years 2014, 2025 & 2030
- TABLE 74: UK Recent Past, Current & Future Analysis for Computer Integrated Manufacturing by Organization Size - Large Enterprises and SMEs - Independent Analysis of Annual Sales in US$ Million for the Years 2024 through 2030 and % CAGR
- TABLE 75: UK Historic Review for Computer Integrated Manufacturing by Organization Size - Large Enterprises and SMEs Markets - Independent Analysis of Annual Sales in US$ Million for Years 2014 through 2023 and % CAGR
- TABLE 76: UK 16-Year Perspective for Computer Integrated Manufacturing by Organization Size - Percentage Breakdown of Value Sales for Large Enterprises and SMEs for the Years 2014, 2025 & 2030
- SPAIN
- TABLE 77: Spain Recent Past, Current & Future Analysis for Computer Integrated Manufacturing by Manufacturing Type - Computer-Aided Design Manufacturing, Computer-Aided Manufacturing and Digital Manufacturing - Independent Analysis of Annual Sales in US$ Million for the Years 2024 through 2030 and % CAGR
- TABLE 78: Spain Historic Review for Computer Integrated Manufacturing by Manufacturing Type - Computer-Aided Design Manufacturing, Computer-Aided Manufacturing and Digital Manufacturing Markets - Independent Analysis of Annual Sales in US$ Million for Years 2014 through 2023 and % CAGR
- TABLE 79: Spain 16-Year Perspective for Computer Integrated Manufacturing by Manufacturing Type - Percentage Breakdown of Value Sales for Computer-Aided Design Manufacturing, Computer-Aided Manufacturing and Digital Manufacturing for the Years 2014, 2025 & 2030
- TABLE 80: Spain Recent Past, Current & Future Analysis for Computer Integrated Manufacturing by Organization Size - Large Enterprises and SMEs - Independent Analysis of Annual Sales in US$ Million for the Years 2024 through 2030 and % CAGR
- TABLE 81: Spain Historic Review for Computer Integrated Manufacturing by Organization Size - Large Enterprises and SMEs Markets - Independent Analysis of Annual Sales in US$ Million for Years 2014 through 2023 and % CAGR
- TABLE 82: Spain 16-Year Perspective for Computer Integrated Manufacturing by Organization Size - Percentage Breakdown of Value Sales for Large Enterprises and SMEs for the Years 2014, 2025 & 2030
- RUSSIA
- TABLE 83: Russia Recent Past, Current & Future Analysis for Computer Integrated Manufacturing by Manufacturing Type - Computer-Aided Design Manufacturing, Computer-Aided Manufacturing and Digital Manufacturing - Independent Analysis of Annual Sales in US$ Million for the Years 2024 through 2030 and % CAGR
- TABLE 84: Russia Historic Review for Computer Integrated Manufacturing by Manufacturing Type - Computer-Aided Design Manufacturing, Computer-Aided Manufacturing and Digital Manufacturing Markets - Independent Analysis of Annual Sales in US$ Million for Years 2014 through 2023 and % CAGR
- TABLE 85: Russia 16-Year Perspective for Computer Integrated Manufacturing by Manufacturing Type - Percentage Breakdown of Value Sales for Computer-Aided Design Manufacturing, Computer-Aided Manufacturing and Digital Manufacturing for the Years 2014, 2025 & 2030
- TABLE 86: Russia Recent Past, Current & Future Analysis for Computer Integrated Manufacturing by Organization Size - Large Enterprises and SMEs - Independent Analysis of Annual Sales in US$ Million for the Years 2024 through 2030 and % CAGR
- TABLE 87: Russia Historic Review for Computer Integrated Manufacturing by Organization Size - Large Enterprises and SMEs Markets - Independent Analysis of Annual Sales in US$ Million for Years 2014 through 2023 and % CAGR
- TABLE 88: Russia 16-Year Perspective for Computer Integrated Manufacturing by Organization Size - Percentage Breakdown of Value Sales for Large Enterprises and SMEs for the Years 2014, 2025 & 2030
- REST OF EUROPE
- TABLE 89: Rest of Europe Recent Past, Current & Future Analysis for Computer Integrated Manufacturing by Manufacturing Type - Computer-Aided Design Manufacturing, Computer-Aided Manufacturing and Digital Manufacturing - Independent Analysis of Annual Sales in US$ Million for the Years 2024 through 2030 and % CAGR
- TABLE 90: Rest of Europe Historic Review for Computer Integrated Manufacturing by Manufacturing Type - Computer-Aided Design Manufacturing, Computer-Aided Manufacturing and Digital Manufacturing Markets - Independent Analysis of Annual Sales in US$ Million for Years 2014 through 2023 and % CAGR
- TABLE 91: Rest of Europe 16-Year Perspective for Computer Integrated Manufacturing by Manufacturing Type - Percentage Breakdown of Value Sales for Computer-Aided Design Manufacturing, Computer-Aided Manufacturing and Digital Manufacturing for the Years 2014, 2025 & 2030
- TABLE 92: Rest of Europe Recent Past, Current & Future Analysis for Computer Integrated Manufacturing by Organization Size - Large Enterprises and SMEs - Independent Analysis of Annual Sales in US$ Million for the Years 2024 through 2030 and % CAGR
- TABLE 93: Rest of Europe Historic Review for Computer Integrated Manufacturing by Organization Size - Large Enterprises and SMEs Markets - Independent Analysis of Annual Sales in US$ Million for Years 2014 through 2023 and % CAGR
- TABLE 94: Rest of Europe 16-Year Perspective for Computer Integrated Manufacturing by Organization Size - Percentage Breakdown of Value Sales for Large Enterprises and SMEs for the Years 2014, 2025 & 2030
- ASIA-PACIFIC
- Computer Integrated Manufacturing Market Presence - Strong/Active/Niche/Trivial - Key Competitors in Asia-Pacific for 2025 (E)
- TABLE 95: Asia-Pacific Recent Past, Current & Future Analysis for Computer Integrated Manufacturing by Geographic Region - Australia, India, South Korea and Rest of Asia-Pacific Markets - Independent Analysis of Annual Sales in US$ Million for Years 2024 through 2030 and % CAGR
- TABLE 96: Asia-Pacific Historic Review for Computer Integrated Manufacturing by Geographic Region - Australia, India, South Korea and Rest of Asia-Pacific Markets - Independent Analysis of Annual Sales in US$ Million for Years 2014 through 2023 and % CAGR
- TABLE 97: Asia-Pacific 16-Year Perspective for Computer Integrated Manufacturing by Geographic Region - Percentage Breakdown of Value Sales for Australia, India, South Korea and Rest of Asia-Pacific Markets for Years 2014, 2025 & 2030
- TABLE 98: Asia-Pacific Recent Past, Current & Future Analysis for Computer Integrated Manufacturing by Manufacturing Type - Computer-Aided Design Manufacturing, Computer-Aided Manufacturing and Digital Manufacturing - Independent Analysis of Annual Sales in US$ Million for the Years 2024 through 2030 and % CAGR
- TABLE 99: Asia-Pacific Historic Review for Computer Integrated Manufacturing by Manufacturing Type - Computer-Aided Design Manufacturing, Computer-Aided Manufacturing and Digital Manufacturing Markets - Independent Analysis of Annual Sales in US$ Million for Years 2014 through 2023 and % CAGR
- TABLE 100: Asia-Pacific 16-Year Perspective for Computer Integrated Manufacturing by Manufacturing Type - Percentage Breakdown of Value Sales for Computer-Aided Design Manufacturing, Computer-Aided Manufacturing and Digital Manufacturing for the Years 2014, 2025 & 2030
- TABLE 101: Asia-Pacific Recent Past, Current & Future Analysis for Computer Integrated Manufacturing by Organization Size - Large Enterprises and SMEs - Independent Analysis of Annual Sales in US$ Million for the Years 2024 through 2030 and % CAGR
- TABLE 102: Asia-Pacific Historic Review for Computer Integrated Manufacturing by Organization Size - Large Enterprises and SMEs Markets - Independent Analysis of Annual Sales in US$ Million for Years 2014 through 2023 and % CAGR
- TABLE 103: Asia-Pacific 16-Year Perspective for Computer Integrated Manufacturing by Organization Size - Percentage Breakdown of Value Sales for Large Enterprises and SMEs for the Years 2014, 2025 & 2030
- AUSTRALIA
- Computer Integrated Manufacturing Market Presence - Strong/Active/Niche/Trivial - Key Competitors in Australia for 2025 (E)
- TABLE 104: Australia Recent Past, Current & Future Analysis for Computer Integrated Manufacturing by Manufacturing Type - Computer-Aided Design Manufacturing, Computer-Aided Manufacturing and Digital Manufacturing - Independent Analysis of Annual Sales in US$ Million for the Years 2024 through 2030 and % CAGR
- TABLE 105: Australia Historic Review for Computer Integrated Manufacturing by Manufacturing Type - Computer-Aided Design Manufacturing, Computer-Aided Manufacturing and Digital Manufacturing Markets - Independent Analysis of Annual Sales in US$ Million for Years 2014 through 2023 and % CAGR
- TABLE 106: Australia 16-Year Perspective for Computer Integrated Manufacturing by Manufacturing Type - Percentage Breakdown of Value Sales for Computer-Aided Design Manufacturing, Computer-Aided Manufacturing and Digital Manufacturing for the Years 2014, 2025 & 2030
- TABLE 107: Australia Recent Past, Current & Future Analysis for Computer Integrated Manufacturing by Organization Size - Large Enterprises and SMEs - Independent Analysis of Annual Sales in US$ Million for the Years 2024 through 2030 and % CAGR
- TABLE 108: Australia Historic Review for Computer Integrated Manufacturing by Organization Size - Large Enterprises and SMEs Markets - Independent Analysis of Annual Sales in US$ Million for Years 2014 through 2023 and % CAGR
- TABLE 109: Australia 16-Year Perspective for Computer Integrated Manufacturing by Organization Size - Percentage Breakdown of Value Sales for Large Enterprises and SMEs for the Years 2014, 2025 & 2030
- INDIA
- Computer Integrated Manufacturing Market Presence - Strong/Active/Niche/Trivial - Key Competitors in India for 2025 (E)
- TABLE 110: India Recent Past, Current & Future Analysis for Computer Integrated Manufacturing by Manufacturing Type - Computer-Aided Design Manufacturing, Computer-Aided Manufacturing and Digital Manufacturing - Independent Analysis of Annual Sales in US$ Million for the Years 2024 through 2030 and % CAGR
- TABLE 111: India Historic Review for Computer Integrated Manufacturing by Manufacturing Type - Computer-Aided Design Manufacturing, Computer-Aided Manufacturing and Digital Manufacturing Markets - Independent Analysis of Annual Sales in US$ Million for Years 2014 through 2023 and % CAGR
- TABLE 112: India 16-Year Perspective for Computer Integrated Manufacturing by Manufacturing Type - Percentage Breakdown of Value Sales for Computer-Aided Design Manufacturing, Computer-Aided Manufacturing and Digital Manufacturing for the Years 2014, 2025 & 2030
- TABLE 113: India Recent Past, Current & Future Analysis for Computer Integrated Manufacturing by Organization Size - Large Enterprises and SMEs - Independent Analysis of Annual Sales in US$ Million for the Years 2024 through 2030 and % CAGR
- TABLE 114: India Historic Review for Computer Integrated Manufacturing by Organization Size - Large Enterprises and SMEs Markets - Independent Analysis of Annual Sales in US$ Million for Years 2014 through 2023 and % CAGR
- TABLE 115: India 16-Year Perspective for Computer Integrated Manufacturing by Organization Size - Percentage Breakdown of Value Sales for Large Enterprises and SMEs for the Years 2014, 2025 & 2030
- SOUTH KOREA
- TABLE 116: South Korea Recent Past, Current & Future Analysis for Computer Integrated Manufacturing by Manufacturing Type - Computer-Aided Design Manufacturing, Computer-Aided Manufacturing and Digital Manufacturing - Independent Analysis of Annual Sales in US$ Million for the Years 2024 through 2030 and % CAGR
- TABLE 117: South Korea Historic Review for Computer Integrated Manufacturing by Manufacturing Type - Computer-Aided Design Manufacturing, Computer-Aided Manufacturing and Digital Manufacturing Markets - Independent Analysis of Annual Sales in US$ Million for Years 2014 through 2023 and % CAGR
- TABLE 118: South Korea 16-Year Perspective for Computer Integrated Manufacturing by Manufacturing Type - Percentage Breakdown of Value Sales for Computer-Aided Design Manufacturing, Computer-Aided Manufacturing and Digital Manufacturing for the Years 2014, 2025 & 2030
- TABLE 119: South Korea Recent Past, Current & Future Analysis for Computer Integrated Manufacturing by Organization Size - Large Enterprises and SMEs - Independent Analysis of Annual Sales in US$ Million for the Years 2024 through 2030 and % CAGR
- TABLE 120: South Korea Historic Review for Computer Integrated Manufacturing by Organization Size - Large Enterprises and SMEs Markets - Independent Analysis of Annual Sales in US$ Million for Years 2014 through 2023 and % CAGR
- TABLE 121: South Korea 16-Year Perspective for Computer Integrated Manufacturing by Organization Size - Percentage Breakdown of Value Sales for Large Enterprises and SMEs for the Years 2014, 2025 & 2030
- REST OF ASIA-PACIFIC
- TABLE 122: Rest of Asia-Pacific Recent Past, Current & Future Analysis for Computer Integrated Manufacturing by Manufacturing Type - Computer-Aided Design Manufacturing, Computer-Aided Manufacturing and Digital Manufacturing - Independent Analysis of Annual Sales in US$ Million for the Years 2024 through 2030 and % CAGR
- TABLE 123: Rest of Asia-Pacific Historic Review for Computer Integrated Manufacturing by Manufacturing Type - Computer-Aided Design Manufacturing, Computer-Aided Manufacturing and Digital Manufacturing Markets - Independent Analysis of Annual Sales in US$ Million for Years 2014 through 2023 and % CAGR
- TABLE 124: Rest of Asia-Pacific 16-Year Perspective for Computer Integrated Manufacturing by Manufacturing Type - Percentage Breakdown of Value Sales for Computer-Aided Design Manufacturing, Computer-Aided Manufacturing and Digital Manufacturing for the Years 2014, 2025 & 2030
- TABLE 125: Rest of Asia-Pacific Recent Past, Current & Future Analysis for Computer Integrated Manufacturing by Organization Size - Large Enterprises and SMEs - Independent Analysis of Annual Sales in US$ Million for the Years 2024 through 2030 and % CAGR
- TABLE 126: Rest of Asia-Pacific Historic Review for Computer Integrated Manufacturing by Organization Size - Large Enterprises and SMEs Markets - Independent Analysis of Annual Sales in US$ Million for Years 2014 through 2023 and % CAGR
- TABLE 127: Rest of Asia-Pacific 16-Year Perspective for Computer Integrated Manufacturing by Organization Size - Percentage Breakdown of Value Sales for Large Enterprises and SMEs for the Years 2014, 2025 & 2030
- LATIN AMERICA
- Computer Integrated Manufacturing Market Presence - Strong/Active/Niche/Trivial - Key Competitors in Latin America for 2025 (E)
- TABLE 128: Latin America Recent Past, Current & Future Analysis for Computer Integrated Manufacturing by Geographic Region - Argentina, Brazil, Mexico and Rest of Latin America Markets - Independent Analysis of Annual Sales in US$ Million for Years 2024 through 2030 and % CAGR
- TABLE 129: Latin America Historic Review for Computer Integrated Manufacturing by Geographic Region - Argentina, Brazil, Mexico and Rest of Latin America Markets - Independent Analysis of Annual Sales in US$ Million for Years 2014 through 2023 and % CAGR
- TABLE 130: Latin America 16-Year Perspective for Computer Integrated Manufacturing by Geographic Region - Percentage Breakdown of Value Sales for Argentina, Brazil, Mexico and Rest of Latin America Markets for Years 2014, 2025 & 2030
- TABLE 131: Latin America Recent Past, Current & Future Analysis for Computer Integrated Manufacturing by Manufacturing Type - Computer-Aided Design Manufacturing, Computer-Aided Manufacturing and Digital Manufacturing - Independent Analysis of Annual Sales in US$ Million for the Years 2024 through 2030 and % CAGR
- TABLE 132: Latin America Historic Review for Computer Integrated Manufacturing by Manufacturing Type - Computer-Aided Design Manufacturing, Computer-Aided Manufacturing and Digital Manufacturing Markets - Independent Analysis of Annual Sales in US$ Million for Years 2014 through 2023 and % CAGR
- TABLE 133: Latin America 16-Year Perspective for Computer Integrated Manufacturing by Manufacturing Type - Percentage Breakdown of Value Sales for Computer-Aided Design Manufacturing, Computer-Aided Manufacturing and Digital Manufacturing for the Years 2014, 2025 & 2030
- TABLE 134: Latin America Recent Past, Current & Future Analysis for Computer Integrated Manufacturing by Organization Size - Large Enterprises and SMEs - Independent Analysis of Annual Sales in US$ Million for the Years 2024 through 2030 and % CAGR
- TABLE 135: Latin America Historic Review for Computer Integrated Manufacturing by Organization Size - Large Enterprises and SMEs Markets - Independent Analysis of Annual Sales in US$ Million for Years 2014 through 2023 and % CAGR
- TABLE 136: Latin America 16-Year Perspective for Computer Integrated Manufacturing by Organization Size - Percentage Breakdown of Value Sales for Large Enterprises and SMEs for the Years 2014, 2025 & 2030
- ARGENTINA
- TABLE 137: Argentina Recent Past, Current & Future Analysis for Computer Integrated Manufacturing by Manufacturing Type - Computer-Aided Design Manufacturing, Computer-Aided Manufacturing and Digital Manufacturing - Independent Analysis of Annual Sales in US$ Million for the Years 2024 through 2030 and % CAGR
- TABLE 138: Argentina Historic Review for Computer Integrated Manufacturing by Manufacturing Type - Computer-Aided Design Manufacturing, Computer-Aided Manufacturing and Digital Manufacturing Markets - Independent Analysis of Annual Sales in US$ Million for Years 2014 through 2023 and % CAGR
- TABLE 139: Argentina 16-Year Perspective for Computer Integrated Manufacturing by Manufacturing Type - Percentage Breakdown of Value Sales for Computer-Aided Design Manufacturing, Computer-Aided Manufacturing and Digital Manufacturing for the Years 2014, 2025 & 2030
- TABLE 140: Argentina Recent Past, Current & Future Analysis for Computer Integrated Manufacturing by Organization Size - Large Enterprises and SMEs - Independent Analysis of Annual Sales in US$ Million for the Years 2024 through 2030 and % CAGR
- TABLE 141: Argentina Historic Review for Computer Integrated Manufacturing by Organization Size - Large Enterprises and SMEs Markets - Independent Analysis of Annual Sales in US$ Million for Years 2014 through 2023 and % CAGR
- TABLE 142: Argentina 16-Year Perspective for Computer Integrated Manufacturing by Organization Size - Percentage Breakdown of Value Sales for Large Enterprises and SMEs for the Years 2014, 2025 & 2030
- BRAZIL
- TABLE 143: Brazil Recent Past, Current & Future Analysis for Computer Integrated Manufacturing by Manufacturing Type - Computer-Aided Design Manufacturing, Computer-Aided Manufacturing and Digital Manufacturing - Independent Analysis of Annual Sales in US$ Million for the Years 2024 through 2030 and % CAGR
- TABLE 144: Brazil Historic Review for Computer Integrated Manufacturing by Manufacturing Type - Computer-Aided Design Manufacturing, Computer-Aided Manufacturing and Digital Manufacturing Markets - Independent Analysis of Annual Sales in US$ Million for Years 2014 through 2023 and % CAGR
- TABLE 145: Brazil 16-Year Perspective for Computer Integrated Manufacturing by Manufacturing Type - Percentage Breakdown of Value Sales for Computer-Aided Design Manufacturing, Computer-Aided Manufacturing and Digital Manufacturing for the Years 2014, 2025 & 2030
- TABLE 146: Brazil Recent Past, Current & Future Analysis for Computer Integrated Manufacturing by Organization Size - Large Enterprises and SMEs - Independent Analysis of Annual Sales in US$ Million for the Years 2024 through 2030 and % CAGR
- TABLE 147: Brazil Historic Review for Computer Integrated Manufacturing by Organization Size - Large Enterprises and SMEs Markets - Independent Analysis of Annual Sales in US$ Million for Years 2014 through 2023 and % CAGR
- TABLE 148: Brazil 16-Year Perspective for Computer Integrated Manufacturing by Organization Size - Percentage Breakdown of Value Sales for Large Enterprises and SMEs for the Years 2014, 2025 & 2030
- MEXICO
- TABLE 149: Mexico Recent Past, Current & Future Analysis for Computer Integrated Manufacturing by Manufacturing Type - Computer-Aided Design Manufacturing, Computer-Aided Manufacturing and Digital Manufacturing - Independent Analysis of Annual Sales in US$ Million for the Years 2024 through 2030 and % CAGR
- TABLE 150: Mexico Historic Review for Computer Integrated Manufacturing by Manufacturing Type - Computer-Aided Design Manufacturing, Computer-Aided Manufacturing and Digital Manufacturing Markets - Independent Analysis of Annual Sales in US$ Million for Years 2014 through 2023 and % CAGR
- TABLE 151: Mexico 16-Year Perspective for Computer Integrated Manufacturing by Manufacturing Type - Percentage Breakdown of Value Sales for Computer-Aided Design Manufacturing, Computer-Aided Manufacturing and Digital Manufacturing for the Years 2014, 2025 & 2030
- TABLE 152: Mexico Recent Past, Current & Future Analysis for Computer Integrated Manufacturing by Organization Size - Large Enterprises and SMEs - Independent Analysis of Annual Sales in US$ Million for the Years 2024 through 2030 and % CAGR
- TABLE 153: Mexico Historic Review for Computer Integrated Manufacturing by Organization Size - Large Enterprises and SMEs Markets - Independent Analysis of Annual Sales in US$ Million for Years 2014 through 2023 and % CAGR
- TABLE 154: Mexico 16-Year Perspective for Computer Integrated Manufacturing by Organization Size - Percentage Breakdown of Value Sales for Large Enterprises and SMEs for the Years 2014, 2025 & 2030
- REST OF LATIN AMERICA
- TABLE 155: Rest of Latin America Recent Past, Current & Future Analysis for Computer Integrated Manufacturing by Manufacturing Type - Computer-Aided Design Manufacturing, Computer-Aided Manufacturing and Digital Manufacturing - Independent Analysis of Annual Sales in US$ Million for the Years 2024 through 2030 and % CAGR
- TABLE 156: Rest of Latin America Historic Review for Computer Integrated Manufacturing by Manufacturing Type - Computer-Aided Design Manufacturing, Computer-Aided Manufacturing and Digital Manufacturing Markets - Independent Analysis of Annual Sales in US$ Million for Years 2014 through 2023 and % CAGR
- TABLE 157: Rest of Latin America 16-Year Perspective for Computer Integrated Manufacturing by Manufacturing Type - Percentage Breakdown of Value Sales for Computer-Aided Design Manufacturing, Computer-Aided Manufacturing and Digital Manufacturing for the Years 2014, 2025 & 2030
- TABLE 158: Rest of Latin America Recent Past, Current & Future Analysis for Computer Integrated Manufacturing by Organization Size - Large Enterprises and SMEs - Independent Analysis of Annual Sales in US$ Million for the Years 2024 through 2030 and % CAGR
- TABLE 159: Rest of Latin America Historic Review for Computer Integrated Manufacturing by Organization Size - Large Enterprises and SMEs Markets - Independent Analysis of Annual Sales in US$ Million for Years 2014 through 2023 and % CAGR
- TABLE 160: Rest of Latin America 16-Year Perspective for Computer Integrated Manufacturing by Organization Size - Percentage Breakdown of Value Sales for Large Enterprises and SMEs for the Years 2014, 2025 & 2030
- MIDDLE EAST
- Computer Integrated Manufacturing Market Presence - Strong/Active/Niche/Trivial - Key Competitors in Middle East for 2025 (E)
- TABLE 161: Middle East Recent Past, Current & Future Analysis for Computer Integrated Manufacturing by Geographic Region - Iran, Israel, Saudi Arabia, UAE and Rest of Middle East Markets - Independent Analysis of Annual Sales in US$ Million for Years 2024 through 2030 and % CAGR
- TABLE 162: Middle East Historic Review for Computer Integrated Manufacturing by Geographic Region - Iran, Israel, Saudi Arabia, UAE and Rest of Middle East Markets - Independent Analysis of Annual Sales in US$ Million for Years 2014 through 2023 and % CAGR
- TABLE 163: Middle East 16-Year Perspective for Computer Integrated Manufacturing by Geographic Region - Percentage Breakdown of Value Sales for Iran, Israel, Saudi Arabia, UAE and Rest of Middle East Markets for Years 2014, 2025 & 2030
- TABLE 164: Middle East Recent Past, Current & Future Analysis for Computer Integrated Manufacturing by Manufacturing Type - Computer-Aided Design Manufacturing, Computer-Aided Manufacturing and Digital Manufacturing - Independent Analysis of Annual Sales in US$ Million for the Years 2024 through 2030 and % CAGR
- TABLE 165: Middle East Historic Review for Computer Integrated Manufacturing by Manufacturing Type - Computer-Aided Design Manufacturing, Computer-Aided Manufacturing and Digital Manufacturing Markets - Independent Analysis of Annual Sales in US$ Million for Years 2014 through 2023 and % CAGR
- TABLE 166: Middle East 16-Year Perspective for Computer Integrated Manufacturing by Manufacturing Type - Percentage Breakdown of Value Sales for Computer-Aided Design Manufacturing, Computer-Aided Manufacturing and Digital Manufacturing for the Years 2014, 2025 & 2030
- TABLE 167: Middle East Recent Past, Current & Future Analysis for Computer Integrated Manufacturing by Organization Size - Large Enterprises and SMEs - Independent Analysis of Annual Sales in US$ Million for the Years 2024 through 2030 and % CAGR
- TABLE 168: Middle East Historic Review for Computer Integrated Manufacturing by Organization Size - Large Enterprises and SMEs Markets - Independent Analysis of Annual Sales in US$ Million for Years 2014 through 2023 and % CAGR
- TABLE 169: Middle East 16-Year Perspective for Computer Integrated Manufacturing by Organization Size - Percentage Breakdown of Value Sales for Large Enterprises and SMEs for the Years 2014, 2025 & 2030
- IRAN
- TABLE 170: Iran Recent Past, Current & Future Analysis for Computer Integrated Manufacturing by Manufacturing Type - Computer-Aided Design Manufacturing, Computer-Aided Manufacturing and Digital Manufacturing - Independent Analysis of Annual Sales in US$ Million for the Years 2024 through 2030 and % CAGR
- TABLE 171: Iran Historic Review for Computer Integrated Manufacturing by Manufacturing Type - Computer-Aided Design Manufacturing, Computer-Aided Manufacturing and Digital Manufacturing Markets - Independent Analysis of Annual Sales in US$ Million for Years 2014 through 2023 and % CAGR
- TABLE 172: Iran 16-Year Perspective for Computer Integrated Manufacturing by Manufacturing Type - Percentage Breakdown of Value Sales for Computer-Aided Design Manufacturing, Computer-Aided Manufacturing and Digital Manufacturing for the Years 2014, 2025 & 2030
- TABLE 173: Iran Recent Past, Current & Future Analysis for Computer Integrated Manufacturing by Organization Size - Large Enterprises and SMEs - Independent Analysis of Annual Sales in US$ Million for the Years 2024 through 2030 and % CAGR
- TABLE 174: Iran Historic Review for Computer Integrated Manufacturing by Organization Size - Large Enterprises and SMEs Markets - Independent Analysis of Annual Sales in US$ Million for Years 2014 through 2023 and % CAGR
- TABLE 175: Iran 16-Year Perspective for Computer Integrated Manufacturing by Organization Size - Percentage Breakdown of Value Sales for Large Enterprises and SMEs for the Years 2014, 2025 & 2030
- ISRAEL
- TABLE 176: Israel Recent Past, Current & Future Analysis for Computer Integrated Manufacturing by Manufacturing Type - Computer-Aided Design Manufacturing, Computer-Aided Manufacturing and Digital Manufacturing - Independent Analysis of Annual Sales in US$ Million for the Years 2024 through 2030 and % CAGR
- TABLE 177: Israel Historic Review for Computer Integrated Manufacturing by Manufacturing Type - Computer-Aided Design Manufacturing, Computer-Aided Manufacturing and Digital Manufacturing Markets - Independent Analysis of Annual Sales in US$ Million for Years 2014 through 2023 and % CAGR
- TABLE 178: Israel 16-Year Perspective for Computer Integrated Manufacturing by Manufacturing Type - Percentage Breakdown of Value Sales for Computer-Aided Design Manufacturing, Computer-Aided Manufacturing and Digital Manufacturing for the Years 2014, 2025 & 2030
- TABLE 179: Israel Recent Past, Current & Future Analysis for Computer Integrated Manufacturing by Organization Size - Large Enterprises and SMEs - Independent Analysis of Annual Sales in US$ Million for the Years 2024 through 2030 and % CAGR
- TABLE 180: Israel Historic Review for Computer Integrated Manufacturing by Organization Size - Large Enterprises and SMEs Markets - Independent Analysis of Annual Sales in US$ Million for Years 2014 through 2023 and % CAGR
- TABLE 181: Israel 16-Year Perspective for Computer Integrated Manufacturing by Organization Size - Percentage Breakdown of Value Sales for Large Enterprises and SMEs for the Years 2014, 2025 & 2030
- SAUDI ARABIA
- TABLE 182: Saudi Arabia Recent Past, Current & Future Analysis for Computer Integrated Manufacturing by Manufacturing Type - Computer-Aided Design Manufacturing, Computer-Aided Manufacturing and Digital Manufacturing - Independent Analysis of Annual Sales in US$ Million for the Years 2024 through 2030 and % CAGR
- TABLE 183: Saudi Arabia Historic Review for Computer Integrated Manufacturing by Manufacturing Type - Computer-Aided Design Manufacturing, Computer-Aided Manufacturing and Digital Manufacturing Markets - Independent Analysis of Annual Sales in US$ Million for Years 2014 through 2023 and % CAGR
- TABLE 184: Saudi Arabia 16-Year Perspective for Computer Integrated Manufacturing by Manufacturing Type - Percentage Breakdown of Value Sales for Computer-Aided Design Manufacturing, Computer-Aided Manufacturing and Digital Manufacturing for the Years 2014, 2025 & 2030
- TABLE 185: Saudi Arabia Recent Past, Current & Future Analysis for Computer Integrated Manufacturing by Organization Size - Large Enterprises and SMEs - Independent Analysis of Annual Sales in US$ Million for the Years 2024 through 2030 and % CAGR
- TABLE 186: Saudi Arabia Historic Review for Computer Integrated Manufacturing by Organization Size - Large Enterprises and SMEs Markets - Independent Analysis of Annual Sales in US$ Million for Years 2014 through 2023 and % CAGR
- TABLE 187: Saudi Arabia 16-Year Perspective for Computer Integrated Manufacturing by Organization Size - Percentage Breakdown of Value Sales for Large Enterprises and SMEs for the Years 2014, 2025 & 2030
- UNITED ARAB EMIRATES
- TABLE 188: UAE Recent Past, Current & Future Analysis for Computer Integrated Manufacturing by Manufacturing Type - Computer-Aided Design Manufacturing, Computer-Aided Manufacturing and Digital Manufacturing - Independent Analysis of Annual Sales in US$ Million for the Years 2024 through 2030 and % CAGR
- TABLE 189: UAE Historic Review for Computer Integrated Manufacturing by Manufacturing Type - Computer-Aided Design Manufacturing, Computer-Aided Manufacturing and Digital Manufacturing Markets - Independent Analysis of Annual Sales in US$ Million for Years 2014 through 2023 and % CAGR
- TABLE 190: UAE 16-Year Perspective for Computer Integrated Manufacturing by Manufacturing Type - Percentage Breakdown of Value Sales for Computer-Aided Design Manufacturing, Computer-Aided Manufacturing and Digital Manufacturing for the Years 2014, 2025 & 2030
- TABLE 191: UAE Recent Past, Current & Future Analysis for Computer Integrated Manufacturing by Organization Size - Large Enterprises and SMEs - Independent Analysis of Annual Sales in US$ Million for the Years 2024 through 2030 and % CAGR
- TABLE 192: UAE Historic Review for Computer Integrated Manufacturing by Organization Size - Large Enterprises and SMEs Markets - Independent Analysis of Annual Sales in US$ Million for Years 2014 through 2023 and % CAGR
- TABLE 193: UAE 16-Year Perspective for Computer Integrated Manufacturing by Organization Size - Percentage Breakdown of Value Sales for Large Enterprises and SMEs for the Years 2014, 2025 & 2030
- REST OF MIDDLE EAST
- TABLE 194: Rest of Middle East Recent Past, Current & Future Analysis for Computer Integrated Manufacturing by Manufacturing Type - Computer-Aided Design Manufacturing, Computer-Aided Manufacturing and Digital Manufacturing - Independent Analysis of Annual Sales in US$ Million for the Years 2024 through 2030 and % CAGR
- TABLE 195: Rest of Middle East Historic Review for Computer Integrated Manufacturing by Manufacturing Type - Computer-Aided Design Manufacturing, Computer-Aided Manufacturing and Digital Manufacturing Markets - Independent Analysis of Annual Sales in US$ Million for Years 2014 through 2023 and % CAGR
- TABLE 196: Rest of Middle East 16-Year Perspective for Computer Integrated Manufacturing by Manufacturing Type - Percentage Breakdown of Value Sales for Computer-Aided Design Manufacturing, Computer-Aided Manufacturing and Digital Manufacturing for the Years 2014, 2025 & 2030
- TABLE 197: Rest of Middle East Recent Past, Current & Future Analysis for Computer Integrated Manufacturing by Organization Size - Large Enterprises and SMEs - Independent Analysis of Annual Sales in US$ Million for the Years 2024 through 2030 and % CAGR
- TABLE 198: Rest of Middle East Historic Review for Computer Integrated Manufacturing by Organization Size - Large Enterprises and SMEs Markets - Independent Analysis of Annual Sales in US$ Million for Years 2014 through 2023 and % CAGR
- TABLE 199: Rest of Middle East 16-Year Perspective for Computer Integrated Manufacturing by Organization Size - Percentage Breakdown of Value Sales for Large Enterprises and SMEs for the Years 2014, 2025 & 2030
- AFRICA
- Computer Integrated Manufacturing Market Presence - Strong/Active/Niche/Trivial - Key Competitors in Africa for 2025 (E)
- TABLE 200: Africa Recent Past, Current & Future Analysis for Computer Integrated Manufacturing by Manufacturing Type - Computer-Aided Design Manufacturing, Computer-Aided Manufacturing and Digital Manufacturing - Independent Analysis of Annual Sales in US$ Million for the Years 2024 through 2030 and % CAGR
- TABLE 201: Africa Historic Review for Computer Integrated Manufacturing by Manufacturing Type - Computer-Aided Design Manufacturing, Computer-Aided Manufacturing and Digital Manufacturing Markets - Independent Analysis of Annual Sales in US$ Million for Years 2014 through 2023 and % CAGR
- TABLE 202: Africa 16-Year Perspective for Computer Integrated Manufacturing by Manufacturing Type - Percentage Breakdown of Value Sales for Computer-Aided Design Manufacturing, Computer-Aided Manufacturing and Digital Manufacturing for the Years 2014, 2025 & 2030
- TABLE 203: Africa Recent Past, Current & Future Analysis for Computer Integrated Manufacturing by Organization Size - Large Enterprises and SMEs - Independent Analysis of Annual Sales in US$ Million for the Years 2024 through 2030 and % CAGR
- TABLE 204: Africa Historic Review for Computer Integrated Manufacturing by Organization Size - Large Enterprises and SMEs Markets - Independent Analysis of Annual Sales in US$ Million for Years 2014 through 2023 and % CAGR
- TABLE 205: Africa 16-Year Perspective for Computer Integrated Manufacturing by Organization Size - Percentage Breakdown of Value Sales for Large Enterprises and SMEs for the Years 2014, 2025 & 2030
- IV. COMPETITION
Pricing
Currency Rates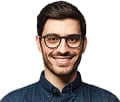