
Aerospace 3D Printing
Description
Global Aerospace 3D Printing Market to Reach US$8.9 Billion by 2030
The global market for Aerospace 3D Printing estimated at US$3.2 Billion in the year 2024, is expected to reach US$8.9 Billion by 2030, growing at a CAGR of 18.5% over the analysis period 2024-2030. Aircraft End-Use, one of the segments analyzed in the report, is expected to record a 19.3% CAGR and reach US$5.5 Billion by the end of the analysis period. Growth in the Unmanned Aerial Vehicles (UAVs) End-Use segment is estimated at 17.6% CAGR over the analysis period.
The U.S. Market is Estimated at US$1.3 Billion While China is Forecast to Grow at 20.2% CAGR
The Aerospace 3D Printing market in the U.S. is estimated at US$1.3 Billion in the year 2024. China, the world`s second largest economy, is forecast to reach a projected market size of US$1.2 Billion by the year 2030 trailing a CAGR of 20.2% over the analysis period 2024-2030. Among the other noteworthy geographic markets are Japan and Canada, each forecast to grow at a CAGR of 17.2% and 18.1% respectively over the analysis period. Within Europe, Germany is forecast to grow at approximately 17.2% CAGR.
Global Aerospace 3D Printing Market - Key Trends & Drivers Summarized
Why Is 3D Printing Revolutionizing The Aerospace Industry?
3D printing, also known as additive manufacturing, is transforming the aerospace industry by introducing unprecedented flexibility and efficiency in the production of components and systems. The ability to create complex geometries with reduced material waste is a game-changer for an industry focused on weight reduction and cost management. Lightweight components manufactured through 3D printing significantly enhance fuel efficiency, making them critical for both commercial and military aerospace applications. This technology enables rapid prototyping, allowing designers to iterate and test new concepts in record time, thus accelerating innovation cycles. Moreover, aerospace companies are leveraging 3D printing to produce parts with improved performance characteristics, such as increased strength-to-weight ratios and enhanced heat resistance. These qualities are especially critical in applications involving engines, turbines, and other high-stress components.
Aerospace 3D printing is also redefining supply chain dynamics by enabling localized and on-demand production. This approach reduces lead times and inventory costs while improving overall supply chain resilience. From satellite components to aircraft interiors, the range of applications for 3D printing continues to expand, driving its adoption across both established players and emerging space exploration startups. As the aerospace sector grapples with increasing demands for sustainability, 3D printing aligns perfectly with this goal by minimizing material waste and enabling the use of eco-friendly materials. These benefits collectively highlight why 3D printing is emerging as a cornerstone of the aerospace industry`s future.
What Role Do Material Innovations Play In 3D Printing’s Aerospace Growth?
Material innovations are at the heart of 3D printing’s transformative impact on the aerospace industry. High-performance materials such as titanium alloys, high-temperature polymers, and composites are now routinely used in additive manufacturing to create components that meet the rigorous demands of aerospace applications. Titanium’s exceptional strength-to-weight ratio and corrosion resistance make it ideal for structural components, while high-temperature polymers such as PEEK are increasingly used in non-metallic applications requiring thermal stability and chemical resistance. Composite materials, on the other hand, enable the creation of lightweight yet durable parts that can withstand significant stress, making them indispensable in aircraft and spacecraft construction.
The development of new metal powders and filament technologies has expanded the range of printable materials, opening up possibilities for producing components previously deemed unfeasible through traditional manufacturing. The integration of gradient materials within a single component is another breakthrough facilitated by 3D printing, enabling engineers to design parts with optimized properties tailored to specific functional requirements. Additionally, sustainability is driving material innovations, with a focus on recyclable and bio-based materials to reduce the environmental footprint of production processes. Advanced material certifications are now ensuring that 3D-printed aerospace components meet stringent safety and performance standards, further encouraging adoption. These advancements in materials are a pivotal factor behind the growing reliance on 3D printing for aerospace applications.
How Are Market Dynamics Shaped By Advancements In 3D Printing Technologies?
The rapid evolution of 3D printing technologies is significantly shaping market dynamics in the aerospace industry. Technologies such as Selective Laser Sintering (SLS), Electron Beam Melting (EBM), and Direct Metal Laser Sintering (DMLS) are enabling the production of highly precise and robust components. These methods provide manufacturers with unparalleled control over the production process, ensuring consistency and quality. Hybrid manufacturing, which combines traditional subtractive processes with additive techniques, is also gaining traction for its ability to leverage the strengths of both approaches in producing complex aerospace components.
Another major development is the rise of large-format 3D printers, capable of manufacturing entire aircraft sections in a single build. This innovation drastically reduces assembly times and eliminates the need for multiple joints, enhancing structural integrity. The integration of artificial intelligence and machine learning into 3D printing workflows has further streamlined the design and production process. AI-driven optimization tools can now automatically adjust printing parameters to improve component performance and minimize defects.
The space exploration sector has emerged as a particularly dynamic area for aerospace 3D printing. With companies like SpaceX and Blue Origin utilizing 3D-printed parts for engines, spacecraft, and even habitats, the market is seeing a surge in demand for innovative printing solutions. Additionally, the ability to manufacture parts in microgravity environments is opening up new frontiers, enabling on-demand production of components aboard space stations and future lunar bases. These technological advancements are reshaping how the aerospace industry approaches design, manufacturing, and sustainability.
What Drives The Growth Of The Aerospace 3D Printing Market?
The growth in the aerospace 3D printing market is driven by several factors, each reflecting the industry’s evolving priorities and challenges. One of the primary drivers is the increasing demand for lightweight components, which directly contribute to fuel efficiency and lower carbon emissions in both commercial and military aircraft. The ability of 3D printing to create highly customized parts is another key factor, addressing the growing need for bespoke solutions in satellite systems, UAVs, and spacecraft. As the aerospace sector shifts towards electrification, 3D printing plays a critical role in developing lightweight battery casings and advanced cooling systems to enhance energy efficiency.
End-use trends also play a significant role, with airlines and defense organizations seeking cost-effective maintenance, repair, and overhaul (MRO) solutions. The ability to produce replacement parts on-demand reduces downtime and eliminates the need for extensive inventories, revolutionizing MRO practices. Consumer behavior, particularly the increasing preference for greener and more sustainable travel options, is pushing aerospace companies to adopt 3D printing for its eco-friendly production processes and material usage.
Technological advancements in additive manufacturing systems have further fueled market growth. Improved speed, precision, and scalability of modern 3D printers enable manufacturers to meet the high production standards of aerospace applications. Collaborative efforts between aerospace firms and 3D printing companies are fostering innovation, leading to faster adoption of new technologies. Additionally, government investments and initiatives, such as NASA’s use of 3D printing in its Artemis program, highlight the strategic importance of this technology for space exploration and national defense. These factors collectively underscore the robust growth trajectory of the aerospace 3D printing market, driven by innovation, sustainability, and the industry’s ever-expanding horizons.
SCOPE OF STUDY:The report analyzes the Aerospace 3D Printing market in terms of units by the following Segments, and Geographic Regions/Countries:
Segments:
Offering (Aerospace 3D Printers, Aerospace 3D Printing Materials, Aerospace 3D Printing Services, Aerospace 3D Printing Software); End-Use (Aircraft End-Use, Unmanned Aerial Vehicles (UAVs) End-Use, Spacecraft End-Use)
Geographic Regions/Countries:
World; USA; Canada; Japan; China; Europe; France; Germany; Italy; UK; Rest of Europe; Asia-Pacific; Rest of World.
Select Competitors (Total 50 Featured) -
- Stratasys Ltd.
- 3D Systems Corporation
- Colibrium Additive
- EOS GmbH
- Materialise NV
- Renishaw plc
- TRUMPF Inc.
- Norsk Titanium AS
- OC Oerlikon Management AG
- Ultimaker BV
- Höganäs AB
- Markforged
- Nikon SLM Solutions AG
- voxeljet AG
- Prodways
- Nano Dimension
We`re transforming market and competitive intelligence with validated expert content and AI tools.
Instead of following the general norm of querying LLMs and Industry-specific SLMs, we built repositories of content curated from domain experts worldwide including video transcripts, blogs, search engines research, and massive amounts of enterprise, product/service, and market data.
TARIFF IMPACT FACTOR
Our new release incorporates impact of tariffs on geographical markets as we predict a shift in competitiveness of companies based on HQ country, manufacturing base, exports and imports (finished goods and OEM). This intricate and multifaceted market reality will impact competitors by increasing the Cost of Goods Sold (COGS), reducing profitability, reconfiguring supply chains, amongst other micro and macro market dynamics.
Please note: Reports are sold as single-site single-user licenses. Electronic versions require 24-48 hours as each copy is customized to the client with digital controls and custom watermarks. The Publisher uses digital controls protecting against copying and printing is restricted to one full copy to be used at the same location.
The latest version of Adobe Acrobat Reader is required to view the report. Upon ordering an electronic version, the Publisher will provide a link to download the purchased report.
Prior to fulfillment of an order, the client will be required to sign a document detailing the purchase terms for a publication from this publisher.
Table of Contents
- I. METHODOLOGY
- II. EXECUTIVE SUMMARY
- 1. MARKET OVERVIEW
- Tariff Impact on Global Supply Chain Patterns
- The 3D Printing Revolution is Here!
- Economic Frontiers: Trends, Trials & Transformations
- In a World Torn by Geopolitical Instability & War, Steadfastness of Global GDP Becomes Increasingly Unpredictable Given the Many Direct and Indirect Economic Repercussions: World Economic Growth Projections (Real Gross Domestic Product (GDP), Annual % Change) for the Years 2022 Through 2025
- All Eyes on Global Inflation, the Main Risk Factor in Global Markets: Global Headline Inflation Rates (In %) for the Years 2019 through 2025
- With Oil Prices Influencing the Rate of inflation, it Remains the Most Watched Commodity in Global Markets: Global Average Annual Brent Crude Oil Price (In US$ Per Barrel) for Years 2019 through 2025
- Competition
- Aerospace 3D Printing – Global Key Competitors Percentage Market Share in 2025 (E)
- Competitive Market Presence - Strong/Active/Niche/Trivial for Players Worldwide in 2025 (E)
- Influencer/Product/Technology Insights
- Recent Market Activity
- 2. FOCUS ON SELECT PLAYERS
- 3. MARKET TRENDS & DRIVERS
- Recovery in Commercial Aerospace Provides a Fertile Environment for the Proliferation of 3D Printing Technology
- As Passenger Traffic Keeps Aircraft Production Activity Well Oiled & Ready to Absorb New Technologies like 3D Printing: Global Air Passenger Growth (In Trillion Revenue Passenger Kilometers (RPK)) for the Years 2024, 2026, 2028 and 2030
- As the World Steps Up Military Spending Amid Rising Global Political Conflicts, It is Uninterrupted Growth for 3D Printing in Military And Defense Component Manufacturing
- As Defense Budgets Grow More Generous Thanks to Rising Political Unrest in Europe, Asia & Middle East, 3D Printing Emerges as a Strategic Pillar of Efficiency Gains in Defense Manufacturing: Global Military Budget (In US$ Million) for the Year 2024 by Country
- AI Emerges to Transform 3D Printing. Here’s the Story
- Push for Innovative Aircraft Interiors Drives Interest in 3D Printing & Its Promised Possibilities
- A Growing Market for Aircraft Interiors Helps Expand Use Case Scenarios for 3D Printing: Global Aircraft Cabin Interior Market (In US$ Billion) for Years 2025, 2027, 2029, 2031 and 2033
- Aircraft MRO Service Providers Step Up Adoption of 3D Printing
- A Growing Market for MRO Expands the Addressable Market Opportunity for 3D Printing: Global Aircraft MRO Market (In US$ Billion) for Years 2025, 2027, 2029, 2031 and 2033
- Need for Parts Consolidation in Aircraft Design Strengthens Demand for 3D Printing Capabilities
- Advanced Material Innovations Strengthen Adoption & Feasibility of 3D Printing
- Exponential Growth of the Global Space Economy to Drive Demand for 3D Printing in Spacecraft & Rocket Production
- New Opportunities Emerge for 3D Printing in the Trillion Dollar & Growing Space Economy: Global Space Industry (In US$ Billion) for Years 2025, 2027, 2029, 2031, 2033 and 2035
- Focus on Supply Chain Optimization Drives Adoption of 3D Printing
- Focus on Lightweighting Drives Popularity Of 3D Printing In Aerospace Manufacturing
- On-Demand Manufacturing in the Aerospace Industry Strengthens the Business Case For 3D Printing
- Focus on Manufacturing Waste Reduction Drives Adoption Of 3D Printing
- 4. GLOBAL MARKET PERSPECTIVE
- TABLE 1: World Recent Past, Current & Future Analysis for Aerospace 3D Printers by Geographic Region - USA, Canada, Japan, China, Europe, Asia-Pacific and Rest of World Markets - Independent Analysis of Annual Revenues in US$ Thousand for Years 2024 through 2030 and % CAGR
- TABLE 2: World Historic Review for Aerospace 3D Printers by Geographic Region - USA, Canada, Japan, China, Europe, Asia-Pacific and Rest of World Markets - Independent Analysis of Annual Revenues in US$ Thousand for Years 2018 through 2023 and % CAGR
- TABLE 3: World 12-Year Perspective for Aerospace 3D Printers by Geographic Region - Percentage Breakdown of Value Revenues for USA, Canada, Japan, China, Europe, Asia-Pacific and Rest of World for Years 2018, 2025 & 2030
- TABLE 4: World Recent Past, Current & Future Analysis for Aerospace 3D Printing Materials by Geographic Region - USA, Canada, Japan, China, Europe, Asia-Pacific and Rest of World Markets - Independent Analysis of Annual Revenues in US$ Thousand for Years 2024 through 2030 and % CAGR
- TABLE 5: World Historic Review for Aerospace 3D Printing Materials by Geographic Region - USA, Canada, Japan, China, Europe, Asia-Pacific and Rest of World Markets - Independent Analysis of Annual Revenues in US$ Thousand for Years 2018 through 2023 and % CAGR
- TABLE 6: World 12-Year Perspective for Aerospace 3D Printing Materials by Geographic Region - Percentage Breakdown of Value Revenues for USA, Canada, Japan, China, Europe, Asia-Pacific and Rest of World for Years 2018, 2025 & 2030
- TABLE 7: World Recent Past, Current & Future Analysis for Aerospace 3D Printing Services by Geographic Region - USA, Canada, Japan, China, Europe, Asia-Pacific and Rest of World Markets - Independent Analysis of Annual Revenues in US$ Thousand for Years 2024 through 2030 and % CAGR
- TABLE 8: World Historic Review for Aerospace 3D Printing Services by Geographic Region - USA, Canada, Japan, China, Europe, Asia-Pacific and Rest of World Markets - Independent Analysis of Annual Revenues in US$ Thousand for Years 2018 through 2023 and % CAGR
- TABLE 9: World 12-Year Perspective for Aerospace 3D Printing Services by Geographic Region - Percentage Breakdown of Value Revenues for USA, Canada, Japan, China, Europe, Asia-Pacific and Rest of World for Years 2018, 2025 & 2030
- TABLE 10: World Recent Past, Current & Future Analysis for Aerospace 3D Printing Software by Geographic Region - USA, Canada, Japan, China, Europe, Asia-Pacific and Rest of World Markets - Independent Analysis of Annual Revenues in US$ Thousand for Years 2024 through 2030 and % CAGR
- TABLE 11: World Historic Review for Aerospace 3D Printing Software by Geographic Region - USA, Canada, Japan, China, Europe, Asia-Pacific and Rest of World Markets - Independent Analysis of Annual Revenues in US$ Thousand for Years 2018 through 2023 and % CAGR
- TABLE 12: World 12-Year Perspective for Aerospace 3D Printing Software by Geographic Region - Percentage Breakdown of Value Revenues for USA, Canada, Japan, China, Europe, Asia-Pacific and Rest of World for Years 2018, 2025 & 2030
- TABLE 13: World Recent Past, Current & Future Analysis for Aircraft End-Use by Geographic Region - USA, Canada, Japan, China, Europe, Asia-Pacific and Rest of World Markets - Independent Analysis of Annual Revenues in US$ Thousand for Years 2024 through 2030 and % CAGR
- TABLE 14: World Historic Review for Aircraft End-Use by Geographic Region - USA, Canada, Japan, China, Europe, Asia-Pacific and Rest of World Markets - Independent Analysis of Annual Revenues in US$ Thousand for Years 2018 through 2023 and % CAGR
- TABLE 15: World 12-Year Perspective for Aircraft End-Use by Geographic Region - Percentage Breakdown of Value Revenues for USA, Canada, Japan, China, Europe, Asia-Pacific and Rest of World for Years 2018, 2025 & 2030
- TABLE 16: World Recent Past, Current & Future Analysis for Unmanned Aerial Vehicles (UAVs) End-Use by Geographic Region - USA, Canada, Japan, China, Europe, Asia-Pacific and Rest of World Markets - Independent Analysis of Annual Revenues in US$ Thousand for Years 2024 through 2030 and % CAGR
- TABLE 17: World Historic Review for Unmanned Aerial Vehicles (UAVs) End-Use by Geographic Region - USA, Canada, Japan, China, Europe, Asia-Pacific and Rest of World Markets - Independent Analysis of Annual Revenues in US$ Thousand for Years 2018 through 2023 and % CAGR
- TABLE 18: World 12-Year Perspective for Unmanned Aerial Vehicles (UAVs) End-Use by Geographic Region - Percentage Breakdown of Value Revenues for USA, Canada, Japan, China, Europe, Asia-Pacific and Rest of World for Years 2018, 2025 & 2030
- TABLE 19: World Recent Past, Current & Future Analysis for Spacecraft End-Use by Geographic Region - USA, Canada, Japan, China, Europe, Asia-Pacific and Rest of World Markets - Independent Analysis of Annual Revenues in US$ Thousand for Years 2024 through 2030 and % CAGR
- TABLE 20: World Historic Review for Spacecraft End-Use by Geographic Region - USA, Canada, Japan, China, Europe, Asia-Pacific and Rest of World Markets - Independent Analysis of Annual Revenues in US$ Thousand for Years 2018 through 2023 and % CAGR
- TABLE 21: World 12-Year Perspective for Spacecraft End-Use by Geographic Region - Percentage Breakdown of Value Revenues for USA, Canada, Japan, China, Europe, Asia-Pacific and Rest of World for Years 2018, 2025 & 2030
- TABLE 22: World Aerospace 3D Printing Market Analysis of Annual Sales in US$ Thousand for Years 2018 through 2030
- TABLE 23: World Recent Past, Current & Future Analysis for Aerospace 3D Printing by Geographic Region - USA, Canada, Japan, China, Europe, Asia-Pacific and Rest of World Markets - Independent Analysis of Annual Revenues in US$ Thousand for Years 2024 through 2030 and % CAGR
- TABLE 24: World Historic Review for Aerospace 3D Printing by Geographic Region - USA, Canada, Japan, China, Europe, Asia-Pacific and Rest of World Markets - Independent Analysis of Annual Revenues in US$ Thousand for Years 2018 through 2023 and % CAGR
- TABLE 25: World 12-Year Perspective for Aerospace 3D Printing by Geographic Region - Percentage Breakdown of Value Revenues for USA, Canada, Japan, China, Europe, Asia-Pacific and Rest of World Markets for Years 2018, 2025 & 2030
- III. MARKET ANALYSIS
- UNITED STATES
- TABLE 26: USA Recent Past, Current & Future Analysis for Aerospace 3D Printing by Offering - Aerospace 3D Printers, Aerospace 3D Printing Materials, Aerospace 3D Printing Services and Aerospace 3D Printing Software - Independent Analysis of Annual Revenues in US$ Thousand for the Years 2024 through 2030 and % CAGR
- TABLE 27: USA Historic Review for Aerospace 3D Printing by Offering - Aerospace 3D Printers, Aerospace 3D Printing Materials, Aerospace 3D Printing Services and Aerospace 3D Printing Software Markets - Independent Analysis of Annual Revenues in US$ Thousand for Years 2018 through 2023 and % CAGR
- TABLE 28: USA 12-Year Perspective for Aerospace 3D Printing by Offering - Percentage Breakdown of Value Revenues for Aerospace 3D Printers, Aerospace 3D Printing Materials, Aerospace 3D Printing Services and Aerospace 3D Printing Software for the Years 2018, 2025 & 2030
- TABLE 29: USA Recent Past, Current & Future Analysis for Aerospace 3D Printing by End-Use - Aircraft End-Use, Unmanned Aerial Vehicles (UAVs) End-Use and Spacecraft End-Use - Independent Analysis of Annual Revenues in US$ Thousand for the Years 2024 through 2030 and % CAGR
- TABLE 30: USA Historic Review for Aerospace 3D Printing by End-Use - Aircraft End-Use, Unmanned Aerial Vehicles (UAVs) End-Use and Spacecraft End-Use Markets - Independent Analysis of Annual Revenues in US$ Thousand for Years 2018 through 2023 and % CAGR
- TABLE 31: USA 12-Year Perspective for Aerospace 3D Printing by End-Use - Percentage Breakdown of Value Revenues for Aircraft End-Use, Unmanned Aerial Vehicles (UAVs) End-Use and Spacecraft End-Use for the Years 2018, 2025 & 2030
- CANADA
- TABLE 32: Canada Recent Past, Current & Future Analysis for Aerospace 3D Printing by Offering - Aerospace 3D Printers, Aerospace 3D Printing Materials, Aerospace 3D Printing Services and Aerospace 3D Printing Software - Independent Analysis of Annual Revenues in US$ Thousand for the Years 2024 through 2030 and % CAGR
- TABLE 33: Canada Historic Review for Aerospace 3D Printing by Offering - Aerospace 3D Printers, Aerospace 3D Printing Materials, Aerospace 3D Printing Services and Aerospace 3D Printing Software Markets - Independent Analysis of Annual Revenues in US$ Thousand for Years 2018 through 2023 and % CAGR
- TABLE 34: Canada 12-Year Perspective for Aerospace 3D Printing by Offering - Percentage Breakdown of Value Revenues for Aerospace 3D Printers, Aerospace 3D Printing Materials, Aerospace 3D Printing Services and Aerospace 3D Printing Software for the Years 2018, 2025 & 2030
- TABLE 35: Canada Recent Past, Current & Future Analysis for Aerospace 3D Printing by End-Use - Aircraft End-Use, Unmanned Aerial Vehicles (UAVs) End-Use and Spacecraft End-Use - Independent Analysis of Annual Revenues in US$ Thousand for the Years 2024 through 2030 and % CAGR
- TABLE 36: Canada Historic Review for Aerospace 3D Printing by End-Use - Aircraft End-Use, Unmanned Aerial Vehicles (UAVs) End-Use and Spacecraft End-Use Markets - Independent Analysis of Annual Revenues in US$ Thousand for Years 2018 through 2023 and % CAGR
- TABLE 37: Canada 12-Year Perspective for Aerospace 3D Printing by End-Use - Percentage Breakdown of Value Revenues for Aircraft End-Use, Unmanned Aerial Vehicles (UAVs) End-Use and Spacecraft End-Use for the Years 2018, 2025 & 2030
- JAPAN
- TABLE 38: Japan Recent Past, Current & Future Analysis for Aerospace 3D Printing by Offering - Aerospace 3D Printers, Aerospace 3D Printing Materials, Aerospace 3D Printing Services and Aerospace 3D Printing Software - Independent Analysis of Annual Revenues in US$ Thousand for the Years 2024 through 2030 and % CAGR
- TABLE 39: Japan Historic Review for Aerospace 3D Printing by Offering - Aerospace 3D Printers, Aerospace 3D Printing Materials, Aerospace 3D Printing Services and Aerospace 3D Printing Software Markets - Independent Analysis of Annual Revenues in US$ Thousand for Years 2018 through 2023 and % CAGR
- TABLE 40: Japan 12-Year Perspective for Aerospace 3D Printing by Offering - Percentage Breakdown of Value Revenues for Aerospace 3D Printers, Aerospace 3D Printing Materials, Aerospace 3D Printing Services and Aerospace 3D Printing Software for the Years 2018, 2025 & 2030
- TABLE 41: Japan Recent Past, Current & Future Analysis for Aerospace 3D Printing by End-Use - Aircraft End-Use, Unmanned Aerial Vehicles (UAVs) End-Use and Spacecraft End-Use - Independent Analysis of Annual Revenues in US$ Thousand for the Years 2024 through 2030 and % CAGR
- TABLE 42: Japan Historic Review for Aerospace 3D Printing by End-Use - Aircraft End-Use, Unmanned Aerial Vehicles (UAVs) End-Use and Spacecraft End-Use Markets - Independent Analysis of Annual Revenues in US$ Thousand for Years 2018 through 2023 and % CAGR
- TABLE 43: Japan 12-Year Perspective for Aerospace 3D Printing by End-Use - Percentage Breakdown of Value Revenues for Aircraft End-Use, Unmanned Aerial Vehicles (UAVs) End-Use and Spacecraft End-Use for the Years 2018, 2025 & 2030
- CHINA
- TABLE 44: China Recent Past, Current & Future Analysis for Aerospace 3D Printing by Offering - Aerospace 3D Printers, Aerospace 3D Printing Materials, Aerospace 3D Printing Services and Aerospace 3D Printing Software - Independent Analysis of Annual Revenues in US$ Thousand for the Years 2024 through 2030 and % CAGR
- TABLE 45: China Historic Review for Aerospace 3D Printing by Offering - Aerospace 3D Printers, Aerospace 3D Printing Materials, Aerospace 3D Printing Services and Aerospace 3D Printing Software Markets - Independent Analysis of Annual Revenues in US$ Thousand for Years 2018 through 2023 and % CAGR
- TABLE 46: China 12-Year Perspective for Aerospace 3D Printing by Offering - Percentage Breakdown of Value Revenues for Aerospace 3D Printers, Aerospace 3D Printing Materials, Aerospace 3D Printing Services and Aerospace 3D Printing Software for the Years 2018, 2025 & 2030
- TABLE 47: China Recent Past, Current & Future Analysis for Aerospace 3D Printing by End-Use - Aircraft End-Use, Unmanned Aerial Vehicles (UAVs) End-Use and Spacecraft End-Use - Independent Analysis of Annual Revenues in US$ Thousand for the Years 2024 through 2030 and % CAGR
- TABLE 48: China Historic Review for Aerospace 3D Printing by End-Use - Aircraft End-Use, Unmanned Aerial Vehicles (UAVs) End-Use and Spacecraft End-Use Markets - Independent Analysis of Annual Revenues in US$ Thousand for Years 2018 through 2023 and % CAGR
- TABLE 49: China 12-Year Perspective for Aerospace 3D Printing by End-Use - Percentage Breakdown of Value Revenues for Aircraft End-Use, Unmanned Aerial Vehicles (UAVs) End-Use and Spacecraft End-Use for the Years 2018, 2025 & 2030
- EUROPE
- TABLE 50: Europe Recent Past, Current & Future Analysis for Aerospace 3D Printing by Offering - Aerospace 3D Printers, Aerospace 3D Printing Materials, Aerospace 3D Printing Services and Aerospace 3D Printing Software - Independent Analysis of Annual Revenues in US$ Thousand for the Years 2024 through 2030 and % CAGR
- TABLE 51: Europe Historic Review for Aerospace 3D Printing by Offering - Aerospace 3D Printers, Aerospace 3D Printing Materials, Aerospace 3D Printing Services and Aerospace 3D Printing Software Markets - Independent Analysis of Annual Revenues in US$ Thousand for Years 2018 through 2023 and % CAGR
- TABLE 52: Europe 12-Year Perspective for Aerospace 3D Printing by Offering - Percentage Breakdown of Value Revenues for Aerospace 3D Printers, Aerospace 3D Printing Materials, Aerospace 3D Printing Services and Aerospace 3D Printing Software for the Years 2018, 2025 & 2030
- TABLE 53: Europe Recent Past, Current & Future Analysis for Aerospace 3D Printing by End-Use - Aircraft End-Use, Unmanned Aerial Vehicles (UAVs) End-Use and Spacecraft End-Use - Independent Analysis of Annual Revenues in US$ Thousand for the Years 2024 through 2030 and % CAGR
- TABLE 54: Europe Historic Review for Aerospace 3D Printing by End-Use - Aircraft End-Use, Unmanned Aerial Vehicles (UAVs) End-Use and Spacecraft End-Use Markets - Independent Analysis of Annual Revenues in US$ Thousand for Years 2018 through 2023 and % CAGR
- TABLE 55: Europe 12-Year Perspective for Aerospace 3D Printing by End-Use - Percentage Breakdown of Value Revenues for Aircraft End-Use, Unmanned Aerial Vehicles (UAVs) End-Use and Spacecraft End-Use for the Years 2018, 2025 & 2030
- TABLE 56: Europe Recent Past, Current & Future Analysis for Aerospace 3D Printing by Geographic Region - France, Germany, Italy, UK and Rest of Europe Markets - Independent Analysis of Annual Revenues in US$ Thousand for Years 2024 through 2030 and % CAGR
- TABLE 57: Europe Historic Review for Aerospace 3D Printing by Geographic Region - France, Germany, Italy, UK and Rest of Europe Markets - Independent Analysis of Annual Revenues in US$ Thousand for Years 2018 through 2023 and % CAGR
- TABLE 58: Europe 12-Year Perspective for Aerospace 3D Printing by Geographic Region - Percentage Breakdown of Value Revenues for France, Germany, Italy, UK and Rest of Europe Markets for Years 2018, 2025 & 2030
- FRANCE
- TABLE 59: France Recent Past, Current & Future Analysis for Aerospace 3D Printing by Offering - Aerospace 3D Printers, Aerospace 3D Printing Materials, Aerospace 3D Printing Services and Aerospace 3D Printing Software - Independent Analysis of Annual Revenues in US$ Thousand for the Years 2024 through 2030 and % CAGR
- TABLE 60: France Historic Review for Aerospace 3D Printing by Offering - Aerospace 3D Printers, Aerospace 3D Printing Materials, Aerospace 3D Printing Services and Aerospace 3D Printing Software Markets - Independent Analysis of Annual Revenues in US$ Thousand for Years 2018 through 2023 and % CAGR
- TABLE 61: France 12-Year Perspective for Aerospace 3D Printing by Offering - Percentage Breakdown of Value Revenues for Aerospace 3D Printers, Aerospace 3D Printing Materials, Aerospace 3D Printing Services and Aerospace 3D Printing Software for the Years 2018, 2025 & 2030
- TABLE 62: France Recent Past, Current & Future Analysis for Aerospace 3D Printing by End-Use - Aircraft End-Use, Unmanned Aerial Vehicles (UAVs) End-Use and Spacecraft End-Use - Independent Analysis of Annual Revenues in US$ Thousand for the Years 2024 through 2030 and % CAGR
- TABLE 63: France Historic Review for Aerospace 3D Printing by End-Use - Aircraft End-Use, Unmanned Aerial Vehicles (UAVs) End-Use and Spacecraft End-Use Markets - Independent Analysis of Annual Revenues in US$ Thousand for Years 2018 through 2023 and % CAGR
- TABLE 64: France 12-Year Perspective for Aerospace 3D Printing by End-Use - Percentage Breakdown of Value Revenues for Aircraft End-Use, Unmanned Aerial Vehicles (UAVs) End-Use and Spacecraft End-Use for the Years 2018, 2025 & 2030
- GERMANY
- TABLE 65: Germany Recent Past, Current & Future Analysis for Aerospace 3D Printing by Offering - Aerospace 3D Printers, Aerospace 3D Printing Materials, Aerospace 3D Printing Services and Aerospace 3D Printing Software - Independent Analysis of Annual Revenues in US$ Thousand for the Years 2024 through 2030 and % CAGR
- TABLE 66: Germany Historic Review for Aerospace 3D Printing by Offering - Aerospace 3D Printers, Aerospace 3D Printing Materials, Aerospace 3D Printing Services and Aerospace 3D Printing Software Markets - Independent Analysis of Annual Revenues in US$ Thousand for Years 2018 through 2023 and % CAGR
- TABLE 67: Germany 12-Year Perspective for Aerospace 3D Printing by Offering - Percentage Breakdown of Value Revenues for Aerospace 3D Printers, Aerospace 3D Printing Materials, Aerospace 3D Printing Services and Aerospace 3D Printing Software for the Years 2018, 2025 & 2030
- TABLE 68: Germany Recent Past, Current & Future Analysis for Aerospace 3D Printing by End-Use - Aircraft End-Use, Unmanned Aerial Vehicles (UAVs) End-Use and Spacecraft End-Use - Independent Analysis of Annual Revenues in US$ Thousand for the Years 2024 through 2030 and % CAGR
- TABLE 69: Germany Historic Review for Aerospace 3D Printing by End-Use - Aircraft End-Use, Unmanned Aerial Vehicles (UAVs) End-Use and Spacecraft End-Use Markets - Independent Analysis of Annual Revenues in US$ Thousand for Years 2018 through 2023 and % CAGR
- TABLE 70: Germany 12-Year Perspective for Aerospace 3D Printing by End-Use - Percentage Breakdown of Value Revenues for Aircraft End-Use, Unmanned Aerial Vehicles (UAVs) End-Use and Spacecraft End-Use for the Years 2018, 2025 & 2030
- ITALY
- TABLE 71: Italy Recent Past, Current & Future Analysis for Aerospace 3D Printing by Offering - Aerospace 3D Printers, Aerospace 3D Printing Materials, Aerospace 3D Printing Services and Aerospace 3D Printing Software - Independent Analysis of Annual Revenues in US$ Thousand for the Years 2024 through 2030 and % CAGR
- TABLE 72: Italy Historic Review for Aerospace 3D Printing by Offering - Aerospace 3D Printers, Aerospace 3D Printing Materials, Aerospace 3D Printing Services and Aerospace 3D Printing Software Markets - Independent Analysis of Annual Revenues in US$ Thousand for Years 2018 through 2023 and % CAGR
- TABLE 73: Italy 12-Year Perspective for Aerospace 3D Printing by Offering - Percentage Breakdown of Value Revenues for Aerospace 3D Printers, Aerospace 3D Printing Materials, Aerospace 3D Printing Services and Aerospace 3D Printing Software for the Years 2018, 2025 & 2030
- TABLE 74: Italy Recent Past, Current & Future Analysis for Aerospace 3D Printing by End-Use - Aircraft End-Use, Unmanned Aerial Vehicles (UAVs) End-Use and Spacecraft End-Use - Independent Analysis of Annual Revenues in US$ Thousand for the Years 2024 through 2030 and % CAGR
- TABLE 75: Italy Historic Review for Aerospace 3D Printing by End-Use - Aircraft End-Use, Unmanned Aerial Vehicles (UAVs) End-Use and Spacecraft End-Use Markets - Independent Analysis of Annual Revenues in US$ Thousand for Years 2018 through 2023 and % CAGR
- TABLE 76: Italy 12-Year Perspective for Aerospace 3D Printing by End-Use - Percentage Breakdown of Value Revenues for Aircraft End-Use, Unmanned Aerial Vehicles (UAVs) End-Use and Spacecraft End-Use for the Years 2018, 2025 & 2030
- UNITED KINGDOM
- TABLE 77: UK Recent Past, Current & Future Analysis for Aerospace 3D Printing by Offering - Aerospace 3D Printers, Aerospace 3D Printing Materials, Aerospace 3D Printing Services and Aerospace 3D Printing Software - Independent Analysis of Annual Revenues in US$ Thousand for the Years 2024 through 2030 and % CAGR
- TABLE 78: UK Historic Review for Aerospace 3D Printing by Offering - Aerospace 3D Printers, Aerospace 3D Printing Materials, Aerospace 3D Printing Services and Aerospace 3D Printing Software Markets - Independent Analysis of Annual Revenues in US$ Thousand for Years 2018 through 2023 and % CAGR
- TABLE 79: UK 12-Year Perspective for Aerospace 3D Printing by Offering - Percentage Breakdown of Value Revenues for Aerospace 3D Printers, Aerospace 3D Printing Materials, Aerospace 3D Printing Services and Aerospace 3D Printing Software for the Years 2018, 2025 & 2030
- TABLE 80: UK Recent Past, Current & Future Analysis for Aerospace 3D Printing by End-Use - Aircraft End-Use, Unmanned Aerial Vehicles (UAVs) End-Use and Spacecraft End-Use - Independent Analysis of Annual Revenues in US$ Thousand for the Years 2024 through 2030 and % CAGR
- TABLE 81: UK Historic Review for Aerospace 3D Printing by End-Use - Aircraft End-Use, Unmanned Aerial Vehicles (UAVs) End-Use and Spacecraft End-Use Markets - Independent Analysis of Annual Revenues in US$ Thousand for Years 2018 through 2023 and % CAGR
- TABLE 82: UK 12-Year Perspective for Aerospace 3D Printing by End-Use - Percentage Breakdown of Value Revenues for Aircraft End-Use, Unmanned Aerial Vehicles (UAVs) End-Use and Spacecraft End-Use for the Years 2018, 2025 & 2030
- REST OF EUROPE
- TABLE 83: Rest of Europe Recent Past, Current & Future Analysis for Aerospace 3D Printing by Offering - Aerospace 3D Printers, Aerospace 3D Printing Materials, Aerospace 3D Printing Services and Aerospace 3D Printing Software - Independent Analysis of Annual Revenues in US$ Thousand for the Years 2024 through 2030 and % CAGR
- TABLE 84: Rest of Europe Historic Review for Aerospace 3D Printing by Offering - Aerospace 3D Printers, Aerospace 3D Printing Materials, Aerospace 3D Printing Services and Aerospace 3D Printing Software Markets - Independent Analysis of Annual Revenues in US$ Thousand for Years 2018 through 2023 and % CAGR
- TABLE 85: Rest of Europe 12-Year Perspective for Aerospace 3D Printing by Offering - Percentage Breakdown of Value Revenues for Aerospace 3D Printers, Aerospace 3D Printing Materials, Aerospace 3D Printing Services and Aerospace 3D Printing Software for the Years 2018, 2025 & 2030
- TABLE 86: Rest of Europe Recent Past, Current & Future Analysis for Aerospace 3D Printing by End-Use - Aircraft End-Use, Unmanned Aerial Vehicles (UAVs) End-Use and Spacecraft End-Use - Independent Analysis of Annual Revenues in US$ Thousand for the Years 2024 through 2030 and % CAGR
- TABLE 87: Rest of Europe Historic Review for Aerospace 3D Printing by End-Use - Aircraft End-Use, Unmanned Aerial Vehicles (UAVs) End-Use and Spacecraft End-Use Markets - Independent Analysis of Annual Revenues in US$ Thousand for Years 2018 through 2023 and % CAGR
- TABLE 88: Rest of Europe 12-Year Perspective for Aerospace 3D Printing by End-Use - Percentage Breakdown of Value Revenues for Aircraft End-Use, Unmanned Aerial Vehicles (UAVs) End-Use and Spacecraft End-Use for the Years 2018, 2025 & 2030
- ASIA-PACIFIC
- TABLE 89: Asia-Pacific Recent Past, Current & Future Analysis for Aerospace 3D Printing by Offering - Aerospace 3D Printers, Aerospace 3D Printing Materials, Aerospace 3D Printing Services and Aerospace 3D Printing Software - Independent Analysis of Annual Revenues in US$ Thousand for the Years 2024 through 2030 and % CAGR
- TABLE 90: Asia-Pacific Historic Review for Aerospace 3D Printing by Offering - Aerospace 3D Printers, Aerospace 3D Printing Materials, Aerospace 3D Printing Services and Aerospace 3D Printing Software Markets - Independent Analysis of Annual Revenues in US$ Thousand for Years 2018 through 2023 and % CAGR
- TABLE 91: Asia-Pacific 12-Year Perspective for Aerospace 3D Printing by Offering - Percentage Breakdown of Value Revenues for Aerospace 3D Printers, Aerospace 3D Printing Materials, Aerospace 3D Printing Services and Aerospace 3D Printing Software for the Years 2018, 2025 & 2030
- TABLE 92: Asia-Pacific Recent Past, Current & Future Analysis for Aerospace 3D Printing by End-Use - Aircraft End-Use, Unmanned Aerial Vehicles (UAVs) End-Use and Spacecraft End-Use - Independent Analysis of Annual Revenues in US$ Thousand for the Years 2024 through 2030 and % CAGR
- TABLE 93: Asia-Pacific Historic Review for Aerospace 3D Printing by End-Use - Aircraft End-Use, Unmanned Aerial Vehicles (UAVs) End-Use and Spacecraft End-Use Markets - Independent Analysis of Annual Revenues in US$ Thousand for Years 2018 through 2023 and % CAGR
- TABLE 94: Asia-Pacific 12-Year Perspective for Aerospace 3D Printing by End-Use - Percentage Breakdown of Value Revenues for Aircraft End-Use, Unmanned Aerial Vehicles (UAVs) End-Use and Spacecraft End-Use for the Years 2018, 2025 & 2030
- REST OF WORLD
- TABLE 95: Rest of World Recent Past, Current & Future Analysis for Aerospace 3D Printing by Offering - Aerospace 3D Printers, Aerospace 3D Printing Materials, Aerospace 3D Printing Services and Aerospace 3D Printing Software - Independent Analysis of Annual Revenues in US$ Thousand for the Years 2024 through 2030 and % CAGR
- TABLE 96: Rest of World Historic Review for Aerospace 3D Printing by Offering - Aerospace 3D Printers, Aerospace 3D Printing Materials, Aerospace 3D Printing Services and Aerospace 3D Printing Software Markets - Independent Analysis of Annual Revenues in US$ Thousand for Years 2018 through 2023 and % CAGR
- TABLE 97: Rest of World 12-Year Perspective for Aerospace 3D Printing by Offering - Percentage Breakdown of Value Revenues for Aerospace 3D Printers, Aerospace 3D Printing Materials, Aerospace 3D Printing Services and Aerospace 3D Printing Software for the Years 2018, 2025 & 2030
- TABLE 98: Rest of World Recent Past, Current & Future Analysis for Aerospace 3D Printing by End-Use - Aircraft End-Use, Unmanned Aerial Vehicles (UAVs) End-Use and Spacecraft End-Use - Independent Analysis of Annual Revenues in US$ Thousand for the Years 2024 through 2030 and % CAGR
- TABLE 99: Rest of World Historic Review for Aerospace 3D Printing by End-Use - Aircraft End-Use, Unmanned Aerial Vehicles (UAVs) End-Use and Spacecraft End-Use Markets - Independent Analysis of Annual Revenues in US$ Thousand for Years 2018 through 2023 and % CAGR
- TABLE 100: Rest of World 12-Year Perspective for Aerospace 3D Printing by End-Use - Percentage Breakdown of Value Revenues for Aircraft End-Use, Unmanned Aerial Vehicles (UAVs) End-Use and Spacecraft End-Use for the Years 2018, 2025 & 2030
- IV. COMPETITION
Pricing
Currency Rates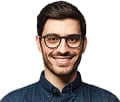