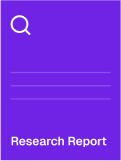
Heat Shrink Tubing and Sleeves Market- Growth, Share, Opportunities & Competitive Analysis, 2024 – 2032
Description
Market Overview:
The Heat Shrink Tubing and Sleeves Market is projected to expand from USD 4,450.00 million in 2024 to USD 6,280.06 million by 2032, registering a compound annual growth rate (CAGR) of 4.4% over the forecast period.
The market’s growth is primarily driven by rising demand for reliable electrical insulation and component protection across critical industries such as automotive, aerospace, telecommunications, and construction. As these sectors adopt increasingly complex and high-performance electronic systems, the need for safer, more durable, and thermally stable insulation solutions becomes essential. Technological advancements in extrusion and laser-etching processes are enhancing the performance, precision, and durability of heat shrink tubing and sleeves. Additionally, the push for stricter compliance with global safety regulations and growing emphasis on dependable electrical connectivity is accelerating the widespread application of heat shrink solutions across multiple industrial domains.
Market Drivers:
Expansion in Automotive and Electronics Industries:
The automotive sector, particularly with the rapid growth of electric vehicles (EVs), is a major growth engine for the heat shrink tubing and sleeves market. EVs require significantly more wiring than traditional vehicles—averaging up to 3,000 meters of wire harness protection per unit. These systems must endure temperatures reaching 150°C and remain resistant to automotive fluids and environmental stress. Notably, demand for specialized tubing solutions with enhanced thermal aging resistance (up to 3,000 hours) has increased by 70%. With over 1,500 connectors and harnesses per EV, the need for robust, high-performance insulation continues to intensify, reinforcing demand for advanced tubing technologies.
Market Challenges:
Raw Material Price Instability:
One of the critical challenges facing the market is the volatility in raw material prices. The Federal Trade Commission (FTC) notes that polymer material prices have shown fluctuations of up to 25% annually, directly affecting manufacturing consistency and overall cost-efficiency. For instance, the price of polyolefin—a key raw material in heat shrink tubing—has seen increases of up to 25%, leading to a 15–20% surge in production expenses. This disproportionately affects small and medium-sized manufacturers, limiting their competitiveness and potentially impacting supply chain continuity. Such instability necessitates the exploration of alternative materials and cost optimization strategies to maintain profitability and supply reliability.
Market Segmentation:
By Material Type:
Polyolefin (POE)
Ethylene Vinyl Acetate (EVA)
Polytetrafluoroethylene (PTFE)
By Length:
Spool
Standard (1.2 Meter)
By Product Type:
Tubes
Sleeves
By Sales Channel:
Original Equipment Manufacturer (OEM)
Aftermarket
By Applications:
Automotive
Aerospace
Railways
By Region:
North America:
U.S., Canada, Mexico
Europe:
Germany, France, U.K., Italy, Spain, Rest of Europe
Asia Pacific:
China, Japan, India, South Korea, Southeast Asia, Rest of Asia Pacific
Latin America:
Brazil, Argentina, Rest of Latin America
Middle East & Africa:
GCC Countries, South Africa, Rest of Middle East & Africa
Key Player Analysis:
TE Connectivity
3M Company
Raychem (part of TE Connectivity)
Amphenol Corporation
Sumitomo Electric Industries
HellermannTyton
Delphi Technologies
Molex
Standard Electric
The Innovation Company
The Heat Shrink Tubing and Sleeves Market is projected to expand from USD 4,450.00 million in 2024 to USD 6,280.06 million by 2032, registering a compound annual growth rate (CAGR) of 4.4% over the forecast period.
The market’s growth is primarily driven by rising demand for reliable electrical insulation and component protection across critical industries such as automotive, aerospace, telecommunications, and construction. As these sectors adopt increasingly complex and high-performance electronic systems, the need for safer, more durable, and thermally stable insulation solutions becomes essential. Technological advancements in extrusion and laser-etching processes are enhancing the performance, precision, and durability of heat shrink tubing and sleeves. Additionally, the push for stricter compliance with global safety regulations and growing emphasis on dependable electrical connectivity is accelerating the widespread application of heat shrink solutions across multiple industrial domains.
Market Drivers:
Expansion in Automotive and Electronics Industries:
The automotive sector, particularly with the rapid growth of electric vehicles (EVs), is a major growth engine for the heat shrink tubing and sleeves market. EVs require significantly more wiring than traditional vehicles—averaging up to 3,000 meters of wire harness protection per unit. These systems must endure temperatures reaching 150°C and remain resistant to automotive fluids and environmental stress. Notably, demand for specialized tubing solutions with enhanced thermal aging resistance (up to 3,000 hours) has increased by 70%. With over 1,500 connectors and harnesses per EV, the need for robust, high-performance insulation continues to intensify, reinforcing demand for advanced tubing technologies.
Market Challenges:
Raw Material Price Instability:
One of the critical challenges facing the market is the volatility in raw material prices. The Federal Trade Commission (FTC) notes that polymer material prices have shown fluctuations of up to 25% annually, directly affecting manufacturing consistency and overall cost-efficiency. For instance, the price of polyolefin—a key raw material in heat shrink tubing—has seen increases of up to 25%, leading to a 15–20% surge in production expenses. This disproportionately affects small and medium-sized manufacturers, limiting their competitiveness and potentially impacting supply chain continuity. Such instability necessitates the exploration of alternative materials and cost optimization strategies to maintain profitability and supply reliability.
Market Segmentation:
By Material Type:
Polyolefin (POE)
Ethylene Vinyl Acetate (EVA)
Polytetrafluoroethylene (PTFE)
By Length:
Spool
Standard (1.2 Meter)
By Product Type:
Tubes
Sleeves
By Sales Channel:
Original Equipment Manufacturer (OEM)
Aftermarket
By Applications:
Automotive
Aerospace
Railways
By Region:
North America:
U.S., Canada, Mexico
Europe:
Germany, France, U.K., Italy, Spain, Rest of Europe
Asia Pacific:
China, Japan, India, South Korea, Southeast Asia, Rest of Asia Pacific
Latin America:
Brazil, Argentina, Rest of Latin America
Middle East & Africa:
GCC Countries, South Africa, Rest of Middle East & Africa
Key Player Analysis:
TE Connectivity
3M Company
Raychem (part of TE Connectivity)
Amphenol Corporation
Sumitomo Electric Industries
HellermannTyton
Delphi Technologies
Molex
Standard Electric
The Innovation Company
Table of Contents
190 Pages
- CHAPTER NO. 1 : INTRODUCTION
- 1.1.1. Report Description
- Purpose of the Report
- USP & Key Offerings
- 1.1.2. Key Benefits for Stakeholders
- 1.1.3. Target Audience
- 1.1.4. Report Scope
- CHAPTER NO. 2 : EXECUTIVE SUMMARY
- 2.1. Heat Shrink Tubing and Sleeves Market Snapshot
- 2.1.1. Heat Shrink Tubing and Sleeves Market, 2018 - 2032 (USD Million)
- CHAPTER NO. 3 : Heat Shrink Tubing and Sleeves Market – INDUSTRY ANALYSIS
- 3.1. Introduction
- 3.2. Market Drivers
- 3.3. Market Restraints
- 3.4. Market Opportunities
- 3.5. Porter’s Five Forces Analysis
- CHAPTER NO. 4 : ANALYSIS COMPETITIVE LANDSCAPE
- 4.1. Company Market Share Analysis – 2023
- 4.2. Heat Shrink Tubing and Sleeves Market Company Revenue Market Share, 2023
- 4.3. Company Assessment Metrics, 2023
- 4.4. Start-ups /SMEs Assessment Metrics, 2023
- 4.5. Strategic Developments
- 4.6. Key Players Product Matrix
- CHAPTER NO. 5 : PESTEL & ADJACENT MARKET ANALYSIS
- CHAPTER NO. 6 : Heat Shrink Tubing and Sleeves Market – By Material Type: ANALYSIS
- CHAPTER NO. 7 : Heat Shrink Tubing and Sleeves Market – By Length: ANALYSIS
- CHAPTER NO. 8 : Heat Shrink Tubing and Sleeves Market – By Product Type: ANALYSIS
- CHAPTER NO. 9 : Heat Shrink Tubing and Sleeves Market – By Sales Channel: ANALYSIS
- CHAPTER NO. 10 : Heat Shrink Tubing and Sleeves Market – By Applications: ANALYSIS
- CHAPTER NO. 11 : Heat Shrink Tubing and Sleeves Market – By Region: ANALYSIS
- CHAPTER NO. 12 : COMPANY PROFILES
- 12.1. TE Connectivity
- 12.1.1. Company Overview
- 12.1.2. Product Portfolio
- 12.1.3. SWOT Analysis
- 12.1.4. Business Strategy
- 12.1.5. Financial Overview
- 12.2. 3M Company
- 12.3. Raychem (part of TE Connectivity)
- 12.4. Amphenol Corporation
- 12.5. Sumitomo Electric Industries
- 12.6. HellermannTyton
- 12.7. Delphi Technologies
- 12.8. Molex
- 12.9. Standard Electric
- 12.10. The Innovation Company
Pricing
Currency Rates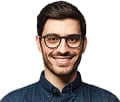
Questions or Comments?
Our team has the ability to search within reports to verify it suits your needs. We can also help maximize your budget by finding sections of reports you can purchase.