
United States Industrial Evaporators Market Overview, 2030
Description
Industrial evaporators are essential devices used in various industries to remove solvents, typically water, from liquids through the process of evaporation. This process involves heating a liquid to turn it into vapor, thereby concentrating the remaining material. The most notable innovations are the development of energy-efficient models, particularly those that utilize Mechanical Vapor Recompression (MVR) technology. MVR systems recover waste heat from the evaporated vapor and redirect it to power the evaporation process, which significantly reduces energy consumption. This is particularly important for industries like food processing and chemical manufacturing, where the evaporation process can be highly energy-intensive. By lowering energy usage, MVR technology helps U.S. manufacturers reduce operational costs and meet environmental regulations that are increasingly demanding energy-efficient solutions. The U.S. industrial evaporator market is also adopting more compact and modular evaporator designs. These systems are smaller, more flexible, and easier to install than their traditional counterparts, making them ideal for industries that need to conserve space and quickly scale production. Modular designs allow for easier upgrades and expansions, giving U.S. manufacturers greater flexibility to meet changing market demands. In the pharmaceutical and chemical sectors, customized evaporators are critical for achieving high levels of purity. Pharmaceutical companies often need evaporators made from specialized materials that prevent contamination during the evaporation process. These evaporators are also designed to meet strict industry regulations that govern the production of medicines, ensuring that the final product is safe and effective. Advanced insulation and heat exchanger designs are being incorporated into newer evaporators to prevent heat loss, ensuring that energy is used more efficiently throughout the process.
According to the research report US Industrial Evaporators Market Overview, 2030, published by Bonafide Research, the US Industrial Evaporators market is anticipated to grow at more than 3.68% CAGR from 2025 to 2030. Desalination is a critical process in arid regions of the U.S., relies on evaporators to separate salt and impurities from seawater, making it potable. The process typically involves heating seawater to evaporate the water vapor, which is then condensed into fresh water, leaving salt and other contaminants behind. Evaporative desalination systems, such as multi-effect distillation (MED) and multi-stage flash (MSF) evaporators, are increasingly being used in the U.S. to meet growing water demands, particularly in coastal areas like California and Florida, where freshwater sources are limited. Evaporators also play a key role in wastewater treatment, where they help reduce the volume of wastewater by evaporating water and leaving behind concentrated waste materials that can then be safely disposed of or further treated. In purification systems, evaporators are used to concentrate valuable materials or remove impurities from water sources, improving water quality for industrial use or even for potable water production. In refrigeration, evaporators are responsible for absorbing heat from the surrounding environment and transferring it to a refrigerant, which then circulates through the system to cool the space. As the demand for more durable and long-lasting evaporators grows, manufacturers are increasingly using corrosion-resistant materials like titanium, stainless steel, and specialized coatings. These materials help extend the lifespan of evaporators by protecting them from the corrosive effects of harsh chemicals, saltwater, and other corrosive substances that are often encountered in industries such as chemicals, pharmaceuticals, and food processing.
Shell & Tube evaporators are one of the most common types in the U.S. market, particularly for large-scale industrial applications. This design consists of a series of tubes housed within a cylindrical shell, where the liquid to be evaporated flows through the tubes, while a heating or cooling fluid circulates around the tubes within the shell. Shell & Tube evaporators are typically employed in industries such as chemical processing, food and beverage, and pharmaceuticals, where the need for efficient heat transfer and large-scale evaporation is critical. These evaporators are highly favored in water desalination plants and wastewater treatment facilities in the U.S. due to their robustness and ability to handle high pressures and temperatures. Plate evaporators are increasingly gaining traction in the U.S. market, particularly in industries where space is limited or the volume of fluid to be processed is relatively smaller. A plate evaporator consists of multiple thin, corrugated plates that are stacked together, with alternate plates forming channels for the fluids to flow through. This design allows for high heat transfer efficiency in a compact and space-saving unit, which makes it particularly useful in food processing, pharmaceuticals, and HVAC systems in the U.S. Plate evaporators are especially popular in juice concentration and dairy processing, where the need for precise temperature control and gentle evaporation is critical to preserving product quality. In the U.S. food industry, plate evaporators are widely used to concentrate milk, fruit juices, and syrups, as they ensure consistent heat application without compromising the flavor, color, or texture of the product.
Falling Film evaporators are widely used in the U.S. food and beverage industry, particularly for concentrating juices, dairy products, and syrups. In this design, the liquid being processed flows down the vertical tubes as a thin film while heat is applied to the outside of the tubes. In contrast to falling film systems, Rising Film evaporators are used primarily in chemical and petrochemical industries in the U.S., where the process involves liquids that need to be evaporated at higher temperatures. In a rising film evaporator, the liquid is fed at the bottom of vertical tubes, and as it is heated, it rises due to the vapor formation inside the tubes. The rising flow helps prevent the formation of hot spots, which is particularly important when working with sensitive or highly viscous liquids. In the U.S. pharmaceutical and chemical sectors, forced circulation evaporators are often employed to concentrate slurries or other materials that are prone to forming deposits, like pharmaceutical concentrates or biochemical solutions. The agitated thin film evaporator is increasingly used in the U.S. food industry, particularly in the concentration of edible oils and high-fructose corn syrup, where maintaining a delicate balance between temperature control and product quality is critical. In the U.S. food industry, MVR systems are increasingly used for juice concentration, milk processing, and syrup production due to their ability to significantly reduce energy consumption. MVR evaporators are also employed in chemical manufacturing and pharmaceutical production, where continuous evaporation processes are necessary for large-scale operations.
In the U.S. food and beverage industry, evaporators are vital for concentrating liquids such as fruit juices, dairy products, syrups, and sauces, while maintaining their taste, texture, and nutritional value. Falling Film evaporators are particularly popular in this sector for their ability to process large volumes of liquid efficiently without compromising the product's quality. The U.S. beverage industry also uses evaporators to concentrate ingredients in soft drinks and to remove excess water from flavor extracts. As energy efficiency becomes a growing concern, manufacturers in the U.S. food sector are increasingly adopting Mechanical Vapor Recompression (MVR) systems in their evaporators to reduce energy consumption. In pharmaceutical manufacturing, the purity of the final product is paramount, and evaporators help to remove solvents or concentrate key ingredients without compromising efficacy. Evaporators are particularly crucial in the manufacturing of injectable drugs, where precise concentration and the removal of water or other solvents are essential for ensuring the stability and safety of the final product. Rising Film evaporators are particularly favored in this sector, as they are effective for high-temperature processes, which are common in petrochemical refining. For instance, evaporators are employed to concentrate chemical solutions like polymer solutions, acidic compounds, and oil refining by-products, facilitating the extraction of useful materials and reducing waste. Multi-effect evaporators (MED) and Multi-stage flash (MSF) evaporators are commonly used for desalination plants along coastal areas like California and Florida, where they help convert seawater into potable water. In wastewater treatment, evaporators are employed to remove excess water from sewage sludge or industrial effluents, reducing the volume of waste that needs to be processed or disposed of. This includes sectors like energy production, where evaporators are used in geothermal energy and biomass operations for concentrating and recovering heat from industrial by-products.
Considered in this report
• Historic Year: 2019
• Base year: 2024
• Estimated year: 2025
• Forecast year: 2030
Aspects covered in this report
• Industrial Evaporators Market with its value and forecast along with its segments
• Various drivers and challenges
• On-going trends and developments
• Top profiled companies
• Strategic recommendation
By Construction Type
• Shell & Tube
• Plate
By Functionality Type
• Falling Film
• Rising Film
• Forced Circulation Evaporators
• Agitated Thin Film Evaporators
• Mechanical Vapor Recompression
• Others
By End-use Industry Type
• Food & Beverage
• Pharmaceutical
• Chemical & Petrochemical
• Water & Wastewater Treatment
• Others
The approach of the report:
This report consists of a combined approach of primary as well as secondary research. Initially, secondary research was used to get an understanding of the market and listing out the companies that are present in the market. The secondary research consists of third-party sources such as press releases, annual report of companies, analyzing the government generated reports and databases. After gathering the data from secondary sources primary research was conducted by making telephonic interviews with the leading players about how the market is functioning and then conducted trade calls with dealers and distributors of the market. Post this we have started doing primary calls to consumers by equally segmenting consumers in regional aspects, tier aspects, age group, and gender. Once we have primary data with us we have started verifying the details obtained from secondary sources.
Intended audience
This report can be useful to industry consultants, manufacturers, suppliers, associations & organizations related to agriculture industry, government bodies and other stakeholders to align their market-centric strategies. In addition to marketing & presentations, it will also increase competitive knowledge about the industry.
According to the research report US Industrial Evaporators Market Overview, 2030, published by Bonafide Research, the US Industrial Evaporators market is anticipated to grow at more than 3.68% CAGR from 2025 to 2030. Desalination is a critical process in arid regions of the U.S., relies on evaporators to separate salt and impurities from seawater, making it potable. The process typically involves heating seawater to evaporate the water vapor, which is then condensed into fresh water, leaving salt and other contaminants behind. Evaporative desalination systems, such as multi-effect distillation (MED) and multi-stage flash (MSF) evaporators, are increasingly being used in the U.S. to meet growing water demands, particularly in coastal areas like California and Florida, where freshwater sources are limited. Evaporators also play a key role in wastewater treatment, where they help reduce the volume of wastewater by evaporating water and leaving behind concentrated waste materials that can then be safely disposed of or further treated. In purification systems, evaporators are used to concentrate valuable materials or remove impurities from water sources, improving water quality for industrial use or even for potable water production. In refrigeration, evaporators are responsible for absorbing heat from the surrounding environment and transferring it to a refrigerant, which then circulates through the system to cool the space. As the demand for more durable and long-lasting evaporators grows, manufacturers are increasingly using corrosion-resistant materials like titanium, stainless steel, and specialized coatings. These materials help extend the lifespan of evaporators by protecting them from the corrosive effects of harsh chemicals, saltwater, and other corrosive substances that are often encountered in industries such as chemicals, pharmaceuticals, and food processing.
Shell & Tube evaporators are one of the most common types in the U.S. market, particularly for large-scale industrial applications. This design consists of a series of tubes housed within a cylindrical shell, where the liquid to be evaporated flows through the tubes, while a heating or cooling fluid circulates around the tubes within the shell. Shell & Tube evaporators are typically employed in industries such as chemical processing, food and beverage, and pharmaceuticals, where the need for efficient heat transfer and large-scale evaporation is critical. These evaporators are highly favored in water desalination plants and wastewater treatment facilities in the U.S. due to their robustness and ability to handle high pressures and temperatures. Plate evaporators are increasingly gaining traction in the U.S. market, particularly in industries where space is limited or the volume of fluid to be processed is relatively smaller. A plate evaporator consists of multiple thin, corrugated plates that are stacked together, with alternate plates forming channels for the fluids to flow through. This design allows for high heat transfer efficiency in a compact and space-saving unit, which makes it particularly useful in food processing, pharmaceuticals, and HVAC systems in the U.S. Plate evaporators are especially popular in juice concentration and dairy processing, where the need for precise temperature control and gentle evaporation is critical to preserving product quality. In the U.S. food industry, plate evaporators are widely used to concentrate milk, fruit juices, and syrups, as they ensure consistent heat application without compromising the flavor, color, or texture of the product.
Falling Film evaporators are widely used in the U.S. food and beverage industry, particularly for concentrating juices, dairy products, and syrups. In this design, the liquid being processed flows down the vertical tubes as a thin film while heat is applied to the outside of the tubes. In contrast to falling film systems, Rising Film evaporators are used primarily in chemical and petrochemical industries in the U.S., where the process involves liquids that need to be evaporated at higher temperatures. In a rising film evaporator, the liquid is fed at the bottom of vertical tubes, and as it is heated, it rises due to the vapor formation inside the tubes. The rising flow helps prevent the formation of hot spots, which is particularly important when working with sensitive or highly viscous liquids. In the U.S. pharmaceutical and chemical sectors, forced circulation evaporators are often employed to concentrate slurries or other materials that are prone to forming deposits, like pharmaceutical concentrates or biochemical solutions. The agitated thin film evaporator is increasingly used in the U.S. food industry, particularly in the concentration of edible oils and high-fructose corn syrup, where maintaining a delicate balance between temperature control and product quality is critical. In the U.S. food industry, MVR systems are increasingly used for juice concentration, milk processing, and syrup production due to their ability to significantly reduce energy consumption. MVR evaporators are also employed in chemical manufacturing and pharmaceutical production, where continuous evaporation processes are necessary for large-scale operations.
In the U.S. food and beverage industry, evaporators are vital for concentrating liquids such as fruit juices, dairy products, syrups, and sauces, while maintaining their taste, texture, and nutritional value. Falling Film evaporators are particularly popular in this sector for their ability to process large volumes of liquid efficiently without compromising the product's quality. The U.S. beverage industry also uses evaporators to concentrate ingredients in soft drinks and to remove excess water from flavor extracts. As energy efficiency becomes a growing concern, manufacturers in the U.S. food sector are increasingly adopting Mechanical Vapor Recompression (MVR) systems in their evaporators to reduce energy consumption. In pharmaceutical manufacturing, the purity of the final product is paramount, and evaporators help to remove solvents or concentrate key ingredients without compromising efficacy. Evaporators are particularly crucial in the manufacturing of injectable drugs, where precise concentration and the removal of water or other solvents are essential for ensuring the stability and safety of the final product. Rising Film evaporators are particularly favored in this sector, as they are effective for high-temperature processes, which are common in petrochemical refining. For instance, evaporators are employed to concentrate chemical solutions like polymer solutions, acidic compounds, and oil refining by-products, facilitating the extraction of useful materials and reducing waste. Multi-effect evaporators (MED) and Multi-stage flash (MSF) evaporators are commonly used for desalination plants along coastal areas like California and Florida, where they help convert seawater into potable water. In wastewater treatment, evaporators are employed to remove excess water from sewage sludge or industrial effluents, reducing the volume of waste that needs to be processed or disposed of. This includes sectors like energy production, where evaporators are used in geothermal energy and biomass operations for concentrating and recovering heat from industrial by-products.
Considered in this report
• Historic Year: 2019
• Base year: 2024
• Estimated year: 2025
• Forecast year: 2030
Aspects covered in this report
• Industrial Evaporators Market with its value and forecast along with its segments
• Various drivers and challenges
• On-going trends and developments
• Top profiled companies
• Strategic recommendation
By Construction Type
• Shell & Tube
• Plate
By Functionality Type
• Falling Film
• Rising Film
• Forced Circulation Evaporators
• Agitated Thin Film Evaporators
• Mechanical Vapor Recompression
• Others
By End-use Industry Type
• Food & Beverage
• Pharmaceutical
• Chemical & Petrochemical
• Water & Wastewater Treatment
• Others
The approach of the report:
This report consists of a combined approach of primary as well as secondary research. Initially, secondary research was used to get an understanding of the market and listing out the companies that are present in the market. The secondary research consists of third-party sources such as press releases, annual report of companies, analyzing the government generated reports and databases. After gathering the data from secondary sources primary research was conducted by making telephonic interviews with the leading players about how the market is functioning and then conducted trade calls with dealers and distributors of the market. Post this we have started doing primary calls to consumers by equally segmenting consumers in regional aspects, tier aspects, age group, and gender. Once we have primary data with us we have started verifying the details obtained from secondary sources.
Intended audience
This report can be useful to industry consultants, manufacturers, suppliers, associations & organizations related to agriculture industry, government bodies and other stakeholders to align their market-centric strategies. In addition to marketing & presentations, it will also increase competitive knowledge about the industry.
Table of Contents
77 Pages
- 1. Executive Summary
- 2. Market Structure
- 2.1. Market Considerate
- 2.2. Assumptions
- 2.3. Limitations
- 2.4. Abbreviations
- 2.5. Sources
- 2.6. Definitions
- 3. Research Methodology
- 3.1. Secondary Research
- 3.2. Primary Data Collection
- 3.3. Market Formation & Validation
- 3.4. Report Writing, Quality Check & Delivery
- 4. United States Geography
- 4.1. Population Distribution Table
- 4.2. United States Macro Economic Indicators
- 5. Market Dynamics
- 5.1. Key Insights
- 5.2. Recent Developments
- 5.3. Market Drivers & Opportunities
- 5.4. Market Restraints & Challenges
- 5.5. Market Trends
- 5.5.1. XXXX
- 5.5.2. XXXX
- 5.5.3. XXXX
- 5.5.4. XXXX
- 5.5.5. XXXX
- 5.6. Supply chain Analysis
- 5.7. Policy & Regulatory Framework
- 5.8. Industry Experts Views
- 6. United States Industrial Evaporators Market Overview
- 6.1. Market Size By Value
- 6.2. Market Size and Forecast, By Construction Type
- 6.3. Market Size and Forecast, By Functionality Type
- 6.4. Market Size and Forecast, By End-use Industry Type
- 6.5. Market Size and Forecast, By Region
- 7. United States Industrial Evaporators Market Segmentations
- 7.1. United States Industrial Evaporators Market, By Construction Type
- 7.1.1. United States Industrial Evaporators Market Size, By Shell & Tube, 2019-2030
- 7.1.2. United States Industrial Evaporators Market Size, By Plate, 2019-2030
- 7.2. United States Industrial Evaporators Market, By Functionality Type
- 7.2.1. United States Industrial Evaporators Market Size, By Falling Film, 2019-2030
- 7.2.2. United States Industrial Evaporators Market Size, By Rising Film, 2019-2030
- 7.2.3. United States Industrial Evaporators Market Size, By Forced Circulation Evaporators, 2019-2030
- 7.2.4. United States Industrial Evaporators Market Size, By Agitated Thin Film Evaporators, 2019-2030
- 7.2.5. United States Industrial Evaporators Market Size, By Mechanical Vapor Recompression, 2019-2030
- 7.2.6. United States Industrial Evaporators Market Size, By Others, 2019-2030
- 7.3. United States Industrial Evaporators Market, By End-use Industry Type
- 7.3.1. United States Industrial Evaporators Market Size, By Food & Beverage, 2019-2030
- 7.3.2. United States Industrial Evaporators Market Size, By Pharmaceutical, 2019-2030
- 7.3.3. United States Industrial Evaporators Market Size, By Chemical & Petrochemical, 2019-2030
- 7.3.4. United States Industrial Evaporators Market Size, By Water & Wastewater Treatment , 2019-2030
- 7.3.5. United States Industrial Evaporators Market Size, By Others, 2019-2030
- 7.4. United States Industrial Evaporators Market, By Region
- 7.4.1. United States Industrial Evaporators Market Size, By North, 2019-2030
- 7.4.2. United States Industrial Evaporators Market Size, By East, 2019-2030
- 7.4.3. United States Industrial Evaporators Market Size, By West, 2019-2030
- 7.4.4. United States Industrial Evaporators Market Size, By South, 2019-2030
- 8. United States Industrial Evaporators Market Opportunity Assessment
- 8.1. By Construction Type, 2025 to 2030
- 8.2. By Functionality Type, 2025 to 2030
- 8.3. By End-use Industry Type, 2025 to 2030
- 8.4. By Region, 2025 to 2030
- 9. Competitive Landscape
- 9.1. Porter's Five Forces
- 9.2. Company Profile
- 9.2.1. Company 1
- 9.2.1.1. Company Snapshot
- 9.2.1.2. Company Overview
- 9.2.1.3. Financial Highlights
- 9.2.1.4. Geographic Insights
- 9.2.1.5. Business Segment & Performance
- 9.2.1.6. Product Portfolio
- 9.2.1.7. Key Executives
- 9.2.1.8. Strategic Moves & Developments
- 9.2.2. Company 2
- 9.2.3. Company 3
- 9.2.4. Company 4
- 9.2.5. Company 5
- 9.2.6. Company 6
- 9.2.7. Company 7
- 9.2.8. Company 8
- 10. Strategic Recommendations
- 11. Disclaimer
- List of Figures
- Figure 1: United States Industrial Evaporators Market Size By Value (2019, 2024 & 2030F) (in USD Million)
- Figure 2: Market Attractiveness Index, By Construction Type
- Figure 3: Market Attractiveness Index, By Functionality Type
- Figure 4: Market Attractiveness Index, By End-use Industry Type
- Figure 5: Market Attractiveness Index, By Region
- Figure 6: Porter's Five Forces of United States Industrial Evaporators Market
- List of Tables
- Table 1: Influencing Factors for Industrial Evaporators Market, 2024
- Table 2: United States Industrial Evaporators Market Size and Forecast, By Construction Type (2019 to 2030F) (In USD Million)
- Table 3: United States Industrial Evaporators Market Size and Forecast, By Functionality Type (2019 to 2030F) (In USD Million)
- Table 4: United States Industrial Evaporators Market Size and Forecast, By End-use Industry Type (2019 to 2030F) (In USD Million)
- Table 5: United States Industrial Evaporators Market Size and Forecast, By Region (2019 to 2030F) (In USD Million)
- Table 6: United States Industrial Evaporators Market Size of Shell & Tube (2019 to 2030) in USD Million
- Table 7: United States Industrial Evaporators Market Size of Plate (2019 to 2030) in USD Million
- Table 8: United States Industrial Evaporators Market Size of Falling Film (2019 to 2030) in USD Million
- Table 9: United States Industrial Evaporators Market Size of Rising Film (2019 to 2030) in USD Million
- Table 10: United States Industrial Evaporators Market Size of Forced Circulation Evaporators (2019 to 2030) in USD Million
- Table 11: United States Industrial Evaporators Market Size of Agitated Thin Film Evaporators (2019 to 2030) in USD Million
- Table 12: United States Industrial Evaporators Market Size of Mechanical Vapor Recompression (2019 to 2030) in USD Million
- Table 13: United States Industrial Evaporators Market Size of Others (2019 to 2030) in USD Million
- Table 14: United States Industrial Evaporators Market Size of Food & Beverage (2019 to 2030) in USD Million
- Table 15: United States Industrial Evaporators Market Size of Pharmaceutical (2019 to 2030) in USD Million
- Table 16: United States Industrial Evaporators Market Size of Chemical & Petrochemical (2019 to 2030) in USD Million
- Table 17: United States Industrial Evaporators Market Size of Water & Wastewater Treatment (2019 to 2030) in USD Million
- Table 18: United States Industrial Evaporators Market Size of Others (2019 to 2030) in USD Million
- Table 19: United States Industrial Evaporators Market Size of North (2019 to 2030) in USD Million
- Table 20: United States Industrial Evaporators Market Size of East (2019 to 2030) in USD Million
- Table 21: United States Industrial Evaporators Market Size of West (2019 to 2030) in USD Million
- Table 22: United States Industrial Evaporators Market Size of South (2019 to 2030) in USD Million
Pricing
Currency Rates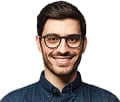
Questions or Comments?
Our team has the ability to search within reports to verify it suits your needs. We can also help maximize your budget by finding sections of reports you can purchase.