
United States Automotive Carbon Fiber Market Overview, 2030
Description
The U.S. automotive carbon fiber market is a high-performance symphony of innovation, where lightweight strength meets futuristic design, redefining speed, efficiency, and sustainability on American roads. Born from aerospace and motorsport excellence where materials like carbon fiber reinforced polymers (CFRP) first proved their worth in Formula 1 and military aircraft this advanced composite has now infiltrated mainstream automotive manufacturing, driven by stringent Corporate Average Fuel Economy (CAFE) standards and the accelerating electric vehicle (EV) revolution. The U.S. leads global adoption, with automotive giants like Ford, General Motors, and Tesla integrating carbon fiber into high-performance models such as the Corvette Z06 and Ford GT, as well as critical EV components like battery enclosures and structural reinforcements. Regulatory policies, including the Environmental Protection Agency’s (EPA) tightening emissions mandates and the Biden administration’s Infrastructure Investment and Jobs Act, actively incentivize the use of lightweight materials to enhance energy efficiency and reduce carbon footprints. Additionally, Department of Energy (DOE) grants and initiatives, such as the Lightweight Materials Program, are accelerating domestic carbon fiber production, reducing reliance on foreign suppliers like Japan’s Toray and Germany’s SGL Group. The market thrives on a legacy of innovation pioneered by aerospace titans Boeing and Lockheed Martin now transitioning into hypercars luxury sedans, and even rugged pickup trucks. Beyond performance vehicles, carbon fiber is increasingly used in mass-market EVs to offset heavy battery weights, proving it is no longer confined to elite supercars but has become a cornerstone of next-generation mobility. Startups like Czinger Vehicles are pushing boundaries with 3D-printed carbon fiber structures, while legacy automakers invest in scalable manufacturing techniques to lower costs. With advancements in recycled carbon fiber and bio-based precursors, the U.S. market is not just chasing performance but also sustainability, ensuring carbon fiber remains at the forefront of automotive innovation for decades to come.
According to the research report USA Automotive carbon fiber Market Overview, 2030, published by Bonafide Research, the USA Automotive carbon fiber Market is anticipated to grow at more than 8.91% CAGR from 2025 to 2030. The U.S. automotive carbon fiber market is experiencing unprecedented growth, fueled by an industry-wide obsession with weight reduction, the urgent demands of EV battery efficiency, and consumers' growing appetite for premium performance aesthetics. This revolution is being driven by several transformative trends, most notably the dramatic shift from exclusive supercar applications to mainstream electric vehicles, where carbon fiber-reinforced polymers (CFRP) are proving critical for extending battery range through radical weight savings. The federal government is playing a pivotal role through initiatives like the DOE's Lightweight Materials Program and Advanced Manufacturing Office, which provide substantial R&D subsidies to accelerate technological breakthroughs. Trade policies such as the USMCA are simultaneously strengthening North American supply chains, helping domestic manufacturers compete against Asian giants like Toray and Teijin. Automakers are capitalizing on multiple advantages - from federal tax credits for EVs incorporating lightweight composites to innovative partnerships like GM's groundbreaking work with Carbon Fiber Recycling to develop closed-loop production systems. The market is further energized by emerging technologies like hydrogen fuel cell vehicles (exemplified by the Toyota Mirai), where carbon fiber's unique properties make it indispensable for high-pressure hydrogen storage tanks. Yet significant challenges remain, particularly the high production costs and complex recycling processes that have historically limited widespread adoption. These hurdles are sparking remarkable innovations, including next-generation low-cost PAN-based fibers, automated layup technologies that slash production time, and novel resin systems that improve manufacturability.
The U.S. automotive carbon fiber market is witnessing an intense materials evolution, with Polyacrylonitrile (PAN)-based fibers currently commanding the lion's share due to their exceptional tensile strength (500-700 GPa) and remarkable versatility across critical automotive applications. American manufacturers like Hexcel and Solvay have made significant strides in optimizing PAN-based carbon fibers specifically for automotive applications, achieving the delicate balance between performance characteristics and cost efficiency that is absolutely vital for electric vehicles, where every pound of weight reduction translates directly into extended battery range and improved efficiency. These advanced PAN fibers have become the material of choice for structural components including chassis systems, body panels, and crash structures, offering an unmatched combination of strength-to-weight ratio and design flexibility that enables engineers to push the boundaries of vehicle performance. On the other end of the spectrum, Pitch-based carbon fiber - derived from petroleum or coal tar precursors - occupies a more specialized niche in the market, prized for its extraordinary stiffness and exceptional thermal conductivity properties that make it particularly suitable for high-temperature applications such as brake discs, thermal management systems, and electromagnetic shielding components. However, Pitch fiber's inherent brittleness, coupled with significantly higher production costs and more complex manufacturing processes, has restricted its adoption primarily to high-performance motorsports and limited aerospace applications. Recognizing these material limitations, the Department of Energy has been actively funding research into next-generation PAN alternatives, including promising bio-based solutions like lignin-derived carbon fibers that could dramatically reduce both production costs and environmental impact. Innovative startups such as Carbon Nexus are pioneering breakthrough production technologies like plasma oxidation that promise to slash processing times and energy consumption. Geographically, PAN production has concentrated in Southern states like Tennessee and Alabama, where access to affordable energy and established manufacturing infrastructure provides competitive advantages, while Pitch production remains minimal and highly specialized.
In structural applications, carbon fiber reinforced polymers (CFRP) have become indispensable for their unparalleled strength-to-weight ratio, with flagship implementations like the Corvette's CFRP torque tube and Tesla's Cybertruck exoskeleton demonstrating revolutionary load-bearing capabilities while dramatically reducing vehicle mass. The electric vehicle revolution has particularly benefited from these advancements, where CFRP battery enclosures provide dual benefits of exceptional EMI shielding and weight reduction - critical factors for maximizing range and safety in EVs like the Lucid Air and upcoming electric Silverado. Powertrain applications present another frontier of innovation, where carbon fiber's unique properties enable rotating mass reduction in high-performance driveshafts (Ford Shelby GT500) and provide essential containment solutions for hydrogen fuel cell vehicles through advanced tank linings. The interior/exterior segment has seen particularly rapid adoption, transitioning from exotic supercars to premium production vehicles, with BMW's i3 CFRP roof panels reducing center of gravity and Lucid's woven carbon fiber trim establishing new benchmarks for automotive luxury. America's rich motorsport heritage continues to drive innovation, with NASCAR and IndyCar teams developing rapid-cure prepreg technologies that eventually trickle down to consumer vehicles, accelerating production cycles. However, challenges remain in areas like repairability protocols and crash energy management, where traditional steel structures still hold advantages. The industry is responding with groundbreaking solutions like Local Motors' 3D-printed carbon fiber components and SABIC's thermoplastic CFRP systems that promise easier repairability and recyclability. These innovations are supported by a robust ecosystem of domestic material suppliers and manufacturing specialists working to overcome historical barriers to widespread adoption.
On the OEM front, major automakers are increasingly integrating carbon fiber into production vehicles at scale, from halo cars like the Acura NSX and Chevrolet Corvette to volume EVs such as the Rivian R1T. These manufacturers are developing deep strategic partnerships with material science leaders like Toray (through its Cyptus joint venture with BMW) to optimize fiber formulations specifically for automotive applications, while government initiatives like the DOE-supported Institute for Advanced Composites Manufacturing Innovation (IACMI) are accelerating industry-wide collaboration on manufacturing breakthroughs. OEMs are also pioneering sustainability efforts through programs like BMW's iCycle closed-loop recycling system, which recovers production waste for reuse. Meanwhile, the aftermarket carbon fiber ecosystem thrives on customization and performance enhancement, with legendary tuners like Singer Vehicle Design and Hennessey Performance Engineering crafting bespoke CFRP body panels and aerodynamic components for discerning enthusiasts. A growing network of e-commerce platforms and specialty retailers has emerged to serve the DIY market, though the premium pricing of quality carbon fiber parts continues to limit mainstream penetration. The distinction between OEM and aftermarket channels is becoming increasingly blurred as automakers introduce factory-approved carbon fiber accessory programs and modular component kits for popular models like the Jeep Wrangler.
Considered in this report
• Historic Year: 2019
• Base year: 2024
• Estimated year: 2025
• Forecast year: 2030
Aspects covered in this report
• Automotive Carbon Fiber Market with its value and forecast along with its segments
• Various drivers and challenges
• On-going trends and developments
• Top profiled companies
• Strategic recommendation
By Material
• Polyacrylonitrile (PAN)
• Pitch
By Application
• Structural Assembly
• Powertrain Components
• Interior and Exterior
By Sales Channel
• OEM
• Aftermarket
The approach of the report:
This report consists of a combined approach of primary as well as secondary research. Initially, secondary research was used to get an understanding of the market and listing out the companies that are present in the market. The secondary research consists of third-party sources such as press releases, annual report of companies, analyzing the government generated reports and databases. After gathering the data from secondary sources primary research was conducted by making telephonic interviews with the leading players about how the market is functioning and then conducted trade calls with dealers and distributors of the market. Post this we have started doing primary calls to consumers by equally segmenting consumers in regional aspects, tier aspects, age group, and gender. Once we have primary data with us we have started verifying the details obtained from secondary sources.
Intended audience
This report can be useful to industry consultants, manufacturers, suppliers, associations & organizations related to agriculture industry, government bodies and other stakeholders to align their market-centric strategies. In addition to marketing & presentations, it will also increase competitive knowledge about the industry.
According to the research report USA Automotive carbon fiber Market Overview, 2030, published by Bonafide Research, the USA Automotive carbon fiber Market is anticipated to grow at more than 8.91% CAGR from 2025 to 2030. The U.S. automotive carbon fiber market is experiencing unprecedented growth, fueled by an industry-wide obsession with weight reduction, the urgent demands of EV battery efficiency, and consumers' growing appetite for premium performance aesthetics. This revolution is being driven by several transformative trends, most notably the dramatic shift from exclusive supercar applications to mainstream electric vehicles, where carbon fiber-reinforced polymers (CFRP) are proving critical for extending battery range through radical weight savings. The federal government is playing a pivotal role through initiatives like the DOE's Lightweight Materials Program and Advanced Manufacturing Office, which provide substantial R&D subsidies to accelerate technological breakthroughs. Trade policies such as the USMCA are simultaneously strengthening North American supply chains, helping domestic manufacturers compete against Asian giants like Toray and Teijin. Automakers are capitalizing on multiple advantages - from federal tax credits for EVs incorporating lightweight composites to innovative partnerships like GM's groundbreaking work with Carbon Fiber Recycling to develop closed-loop production systems. The market is further energized by emerging technologies like hydrogen fuel cell vehicles (exemplified by the Toyota Mirai), where carbon fiber's unique properties make it indispensable for high-pressure hydrogen storage tanks. Yet significant challenges remain, particularly the high production costs and complex recycling processes that have historically limited widespread adoption. These hurdles are sparking remarkable innovations, including next-generation low-cost PAN-based fibers, automated layup technologies that slash production time, and novel resin systems that improve manufacturability.
The U.S. automotive carbon fiber market is witnessing an intense materials evolution, with Polyacrylonitrile (PAN)-based fibers currently commanding the lion's share due to their exceptional tensile strength (500-700 GPa) and remarkable versatility across critical automotive applications. American manufacturers like Hexcel and Solvay have made significant strides in optimizing PAN-based carbon fibers specifically for automotive applications, achieving the delicate balance between performance characteristics and cost efficiency that is absolutely vital for electric vehicles, where every pound of weight reduction translates directly into extended battery range and improved efficiency. These advanced PAN fibers have become the material of choice for structural components including chassis systems, body panels, and crash structures, offering an unmatched combination of strength-to-weight ratio and design flexibility that enables engineers to push the boundaries of vehicle performance. On the other end of the spectrum, Pitch-based carbon fiber - derived from petroleum or coal tar precursors - occupies a more specialized niche in the market, prized for its extraordinary stiffness and exceptional thermal conductivity properties that make it particularly suitable for high-temperature applications such as brake discs, thermal management systems, and electromagnetic shielding components. However, Pitch fiber's inherent brittleness, coupled with significantly higher production costs and more complex manufacturing processes, has restricted its adoption primarily to high-performance motorsports and limited aerospace applications. Recognizing these material limitations, the Department of Energy has been actively funding research into next-generation PAN alternatives, including promising bio-based solutions like lignin-derived carbon fibers that could dramatically reduce both production costs and environmental impact. Innovative startups such as Carbon Nexus are pioneering breakthrough production technologies like plasma oxidation that promise to slash processing times and energy consumption. Geographically, PAN production has concentrated in Southern states like Tennessee and Alabama, where access to affordable energy and established manufacturing infrastructure provides competitive advantages, while Pitch production remains minimal and highly specialized.
In structural applications, carbon fiber reinforced polymers (CFRP) have become indispensable for their unparalleled strength-to-weight ratio, with flagship implementations like the Corvette's CFRP torque tube and Tesla's Cybertruck exoskeleton demonstrating revolutionary load-bearing capabilities while dramatically reducing vehicle mass. The electric vehicle revolution has particularly benefited from these advancements, where CFRP battery enclosures provide dual benefits of exceptional EMI shielding and weight reduction - critical factors for maximizing range and safety in EVs like the Lucid Air and upcoming electric Silverado. Powertrain applications present another frontier of innovation, where carbon fiber's unique properties enable rotating mass reduction in high-performance driveshafts (Ford Shelby GT500) and provide essential containment solutions for hydrogen fuel cell vehicles through advanced tank linings. The interior/exterior segment has seen particularly rapid adoption, transitioning from exotic supercars to premium production vehicles, with BMW's i3 CFRP roof panels reducing center of gravity and Lucid's woven carbon fiber trim establishing new benchmarks for automotive luxury. America's rich motorsport heritage continues to drive innovation, with NASCAR and IndyCar teams developing rapid-cure prepreg technologies that eventually trickle down to consumer vehicles, accelerating production cycles. However, challenges remain in areas like repairability protocols and crash energy management, where traditional steel structures still hold advantages. The industry is responding with groundbreaking solutions like Local Motors' 3D-printed carbon fiber components and SABIC's thermoplastic CFRP systems that promise easier repairability and recyclability. These innovations are supported by a robust ecosystem of domestic material suppliers and manufacturing specialists working to overcome historical barriers to widespread adoption.
On the OEM front, major automakers are increasingly integrating carbon fiber into production vehicles at scale, from halo cars like the Acura NSX and Chevrolet Corvette to volume EVs such as the Rivian R1T. These manufacturers are developing deep strategic partnerships with material science leaders like Toray (through its Cyptus joint venture with BMW) to optimize fiber formulations specifically for automotive applications, while government initiatives like the DOE-supported Institute for Advanced Composites Manufacturing Innovation (IACMI) are accelerating industry-wide collaboration on manufacturing breakthroughs. OEMs are also pioneering sustainability efforts through programs like BMW's iCycle closed-loop recycling system, which recovers production waste for reuse. Meanwhile, the aftermarket carbon fiber ecosystem thrives on customization and performance enhancement, with legendary tuners like Singer Vehicle Design and Hennessey Performance Engineering crafting bespoke CFRP body panels and aerodynamic components for discerning enthusiasts. A growing network of e-commerce platforms and specialty retailers has emerged to serve the DIY market, though the premium pricing of quality carbon fiber parts continues to limit mainstream penetration. The distinction between OEM and aftermarket channels is becoming increasingly blurred as automakers introduce factory-approved carbon fiber accessory programs and modular component kits for popular models like the Jeep Wrangler.
Considered in this report
• Historic Year: 2019
• Base year: 2024
• Estimated year: 2025
• Forecast year: 2030
Aspects covered in this report
• Automotive Carbon Fiber Market with its value and forecast along with its segments
• Various drivers and challenges
• On-going trends and developments
• Top profiled companies
• Strategic recommendation
By Material
• Polyacrylonitrile (PAN)
• Pitch
By Application
• Structural Assembly
• Powertrain Components
• Interior and Exterior
By Sales Channel
• OEM
• Aftermarket
The approach of the report:
This report consists of a combined approach of primary as well as secondary research. Initially, secondary research was used to get an understanding of the market and listing out the companies that are present in the market. The secondary research consists of third-party sources such as press releases, annual report of companies, analyzing the government generated reports and databases. After gathering the data from secondary sources primary research was conducted by making telephonic interviews with the leading players about how the market is functioning and then conducted trade calls with dealers and distributors of the market. Post this we have started doing primary calls to consumers by equally segmenting consumers in regional aspects, tier aspects, age group, and gender. Once we have primary data with us we have started verifying the details obtained from secondary sources.
Intended audience
This report can be useful to industry consultants, manufacturers, suppliers, associations & organizations related to agriculture industry, government bodies and other stakeholders to align their market-centric strategies. In addition to marketing & presentations, it will also increase competitive knowledge about the industry.
Table of Contents
74 Pages
- 1. Executive Summary
- 2. Market Structure
- 2.1. Market Considerate
- 2.2. Assumptions
- 2.3. Limitations
- 2.4. Abbreviations
- 2.5. Sources
- 2.6. Definitions
- 3. Research Methodology
- 3.1. Secondary Research
- 3.2. Primary Data Collection
- 3.3. Market Formation & Validation
- 3.4. Report Writing, Quality Check & Delivery
- 4. United States Geography
- 4.1. Population Distribution Table
- 4.2. United States Macro Economic Indicators
- 5. Market Dynamics
- 5.1. Key Insights
- 5.2. Recent Developments
- 5.3. Market Drivers & Opportunities
- 5.4. Market Restraints & Challenges
- 5.5. Market Trends
- 5.5.1. XXXX
- 5.5.2. XXXX
- 5.5.3. XXXX
- 5.5.4. XXXX
- 5.5.5. XXXX
- 5.6. Supply chain Analysis
- 5.7. Policy & Regulatory Framework
- 5.8. Industry Experts Views
- 6. United States Automotive carbon fiber Market Overview
- 6.1. Market Size By Value
- 6.2. Market Size and Forecast, By Material
- 6.3. Market Size and Forecast, By Application
- 6.4. Market Size and Forecast, By Sales Channel
- 6.5. Market Size and Forecast, By Region
- 7. United States Automotive carbon fiber Market Segmentations
- 7.1. United States Automotive carbon fiber Market, By Material
- 7.1.1. United States Automotive carbon fiber Market Size, By Polyacrylonitrile (PAN), 2019-2030
- 7.1.2. United States Automotive carbon fiber Market Size, By Pitch, 2019-2030
- 7.2. United States Automotive carbon fiber Market, By Application
- 7.2.1. United States Automotive carbon fiber Market Size, By Structural Assembly, 2019-2030
- 7.2.2. United States Automotive carbon fiber Market Size, By Powertrain Components, 2019-2030
- 7.2.3. United States Automotive carbon fiber Market Size, By Interior and Exterior, 2019-2030
- 7.3. United States Automotive carbon fiber Market, By Sales Channel
- 7.3.1. United States Automotive carbon fiber Market Size, By OEM, 2019-2030
- 7.3.2. United States Automotive carbon fiber Market Size, By Aftermarket, 2019-2030
- 7.4. United States Automotive carbon fiber Market, By Region
- 7.4.1. United States Automotive carbon fiber Market Size, By North, 2019-2030
- 7.4.2. United States Automotive carbon fiber Market Size, By East, 2019-2030
- 7.4.3. United States Automotive carbon fiber Market Size, By West, 2019-2030
- 7.4.4. United States Automotive carbon fiber Market Size, By South, 2019-2030
- 8. United States Automotive carbon fiber Market Opportunity Assessment
- 8.1. By Material, 2025 to 2030
- 8.2. By Application, 2025 to 2030
- 8.3. By Sales Channel, 2025 to 2030
- 8.4. By Region, 2025 to 2030
- 9. Competitive Landscape
- 9.1. Porter's Five Forces
- 9.2. Company Profile
- 9.2.1. Company 1
- 9.2.1.1. Company Snapshot
- 9.2.1.2. Company Overview
- 9.2.1.3. Financial Highlights
- 9.2.1.4. Geographic Insights
- 9.2.1.5. Business Segment & Performance
- 9.2.1.6. Product Portfolio
- 9.2.1.7. Key Executives
- 9.2.1.8. Strategic Moves & Developments
- 9.2.2. Company 2
- 9.2.3. Company 3
- 9.2.4. Company 4
- 9.2.5. Company 5
- 9.2.6. Company 6
- 9.2.7. Company 7
- 9.2.8. Company 8
- 10. Strategic Recommendations
- 11. Disclaimer
- List of Figures
- Figure 1: United States Automotive carbon fiber Market Size By Value (2019, 2024 & 2030F) (in USD Million)
- Figure 2: Market Attractiveness Index, By Material
- Figure 3: Market Attractiveness Index, By Application
- Figure 4: Market Attractiveness Index, By Sales Channel
- Figure 5: Market Attractiveness Index, By Region
- Figure 6: Porter's Five Forces of United States Automotive carbon fiber Market
- List of Tables
- Table 1: Influencing Factors for Automotive carbon fiber Market, 2024
- Table 2: United States Automotive carbon fiber Market Size and Forecast, By Material (2019 to 2030F) (In USD Million)
- Table 3: United States Automotive carbon fiber Market Size and Forecast, By Application (2019 to 2030F) (In USD Million)
- Table 4: United States Automotive carbon fiber Market Size and Forecast, By Sales Channel (2019 to 2030F) (In USD Million)
- Table 5: United States Automotive carbon fiber Market Size and Forecast, By Region (2019 to 2030F) (In USD Million)
- Table 6: United States Automotive carbon fiber Market Size of Polyacrylonitrile (PAN) (2019 to 2030) in USD Million
- Table 7: United States Automotive carbon fiber Market Size of Pitch (2019 to 2030) in USD Million
- Table 8: United States Automotive carbon fiber Market Size of Structural Assembly (2019 to 2030) in USD Million
- Table 9: United States Automotive carbon fiber Market Size of Powertrain Components (2019 to 2030) in USD Million
- Table 10: United States Automotive carbon fiber Market Size of Interior and Exterior (2019 to 2030) in USD Million
- Table 11: United States Automotive carbon fiber Market Size of OEM (2019 to 2030) in USD Million
- Table 12: United States Automotive carbon fiber Market Size of Aftermarket (2019 to 2030) in USD Million
- Table 13: United States Automotive carbon fiber Market Size of North (2019 to 2030) in USD Million
- Table 14: United States Automotive carbon fiber Market Size of East (2019 to 2030) in USD Million
- Table 15: United States Automotive carbon fiber Market Size of West (2019 to 2030) in USD Million
- Table 16: United States Automotive carbon fiber Market Size of South (2019 to 2030) in USD Million
Pricing
Currency Rates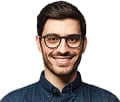
Questions or Comments?
Our team has the ability to search within reports to verify it suits your needs. We can also help maximize your budget by finding sections of reports you can purchase.