
United Kingdom Industrial Evaporators Market Overview, 2030
Description
The industrial evaporators market in the United Kingdom is poised for strong and steady growth as it aligns with the broader national priorities of energy efficiency, decarbonization, and circular economy development. These devices, which operate by using thermal energy to concentrate solutions or separate volatile components from liquids, have become increasingly indispensable across a wide range of industrial applications. As the UK transitions into a low-carbon, high-efficiency industrial future, evaporator systems are taking center stage in industrial infrastructure due to their ability to reduce waste, reclaim usable materials, and minimize the consumption of energy and water. The country’s aggressive regulatory stance on greenhouse gas emissions, water discharge limits, and waste management has put additional pressure on industries to upgrade or replace legacy systems with modern alternatives. In response, industrial plants across the UK are now integrating advanced evaporation technologies not only for compliance but for economic reasons, such as long-term cost savings and improved process efficiency. Government-backed schemes such as carbon reduction incentives, green industrial grants, and innovation funding further encourage investment in clean technology. The increasing complexity of industrial processes particularly in sectors such as chemicals, pharmaceuticals, and food processing demands more customized and intelligent solutions, making traditional evaporator models insufficient. In this evolving landscape, manufacturers, OEMs, and integrators are racing to provide smart, compact, and modular evaporator systems capable of delivering optimal performance while complying with stringent British and EU-derived environmental standards still enforced through UK domestic law.
According to the research report, United Kingdom Industrial Evaporators Market Overview, 2030, published by Bonafide Research, the United Kingdom Industrial Evaporators Market is anticipated to add to more than USD 150 Million by 2025–30. The UK industrial evaporators market is not only expanding in scale but also evolving in sophistication, reflecting the country's advanced technological landscape and the growing demand for process-specific thermal separation solutions. Industry 4.0 has begun to transform how evaporators are manufactured, deployed, and managed. Today's leading systems are equipped with digital monitoring tools, data analytics capabilities, and AI-driven optimization features that enable real-time performance tracking and predictive maintenance. These features are increasingly being adopted by UK industries aiming to improve operational uptime, reduce unexpected downtimes, and maintain high product quality while minimizing energy costs. The incorporation of IoT and SCADA systems allows for seamless integration with plant-wide control systems, thereby providing operators with a high degree of process visibility and responsiveness. The United Kingdom's robust R&D ecosystem, powered by universities, technology hubs, and private innovation centers, is fostering the continuous development of evaporators with advanced heat transfer materials, corrosion-resistant coatings, and modular configurations. These advances are enabling broader customization and making it easier to retrofit existing systems, an attractive proposition for industries facing tight budget constraints but requiring high-efficiency equipment. Additionally, sustainability concerns have led to a surge in hybrid systems that blend mechanical and thermal evaporation or integrate waste heat recovery. This ability to adapt and reconfigure based on evolving industrial needs is making modern evaporator systems highly attractive to UK-based firms seeking long-term technological and environmental resilience.
Shell and tube evaporators have long been favored in heavy-duty applications due to their ability to handle high volumes, extreme temperatures, and pressures. Their construction allows for extended continuous operation, making them well-suited for chemical and petrochemical plants, where 24/7 operation and minimal maintenance downtime are often required. These evaporators are also designed to accommodate high thermal and mechanical stresses, ensuring reliable performance over long lifespans. They are often constructed from materials such as stainless steel or high-grade alloys that offer resistance to corrosion and scaling, both critical in high-acidity or high-salinity environments. Conversely, plate evaporators are gaining strong traction in industries where space constraints, energy efficiency, and frequent product changeovers are more relevant. These systems are especially prominent in the UK’s robust food and beverage sector, as well as in pharmaceuticals, where their compact footprint, ease of cleaning, and high heat transfer efficiency provide a clear operational advantage. Plate evaporators are modular by nature, allowing for scalability and rapid adaptation to changing production needs, which is particularly useful for small and medium enterprises seeking flexibility. Furthermore, their reduced surface area and optimized thermal design contribute to lower energy consumption and faster processing cycles. In the UK, there is a growing interest in hybrid systems that combine the robustness of shell and tube with the efficiency and modularity of plate technologies, aimed at maximizing operational flexibility without compromising on durability.
Falling film evaporators dominate in industries where gentle handling of heat-sensitive materials is necessary, making them the go-to choice for the food and beverage sector as well as for pharmaceutical processes involving sensitive active ingredients. These systems allow liquids to form a thin film over heated surfaces, ensuring rapid evaporation with minimal thermal stress. Rising film evaporators, though based on similar principles, are less energy-efficient and are therefore gradually being phased out or used in basic applications such as water treatment or simple chemical processes. Forced circulation evaporators serve more demanding applications where scaling, crystallization, or high-viscosity fluids are involved. Their use of high-capacity pumps to ensure turbulence and uniform heat distribution makes them invaluable in chemical, petrochemical, and certain wastewater operations where solids buildup could otherwise cripple production. Agitated thin film evaporators cater to niche yet increasingly relevant applications, particularly in sectors such as waste recovery, bio-refining, and cosmetics, where thick, sticky, or thermally unstable substances require controlled and efficient evaporation. Mechanical vapor recompression systems are rapidly becoming a cornerstone of sustainability efforts, offering substantial energy savings by recycling vapor from the evaporation process. These systems are particularly relevant in regions of the UK where energy costs are high and regulatory incentives for carbon reduction are available. Furthermore, emerging multifunctional evaporator systems that integrate several functionalities within one unit are beginning to gain traction, especially in R&D labs and pilot plants. These newer systems appeal to firms seeking multi-stage processing in a compact form factor.
The food and beverage industry is a major consumer of evaporator systems, using them for applications such as milk concentration, fruit juice production, flavor extraction, and brewery operations. With consumer demand shifting towards organic and preservative-free products, manufacturers are adopting evaporators that can preserve natural qualities while improving yield and reducing energy costs. Similarly, the pharmaceutical industry in the UK, bolstered by a strong domestic research base and stringent regulatory oversight, relies heavily on evaporators for solvent recovery, purification of active ingredients, and formulation concentration. Systems in this sector must meet exacting standards of contamination control, documentation, and cleaning validation, which has led to the widespread adoption of fully automated, clean-in-place evaporator systems with real-time monitoring. The chemical and petrochemical industries, on the other hand, utilize heavy-duty evaporators capable of handling corrosive and hazardous fluids under high pressure and temperature. These systems often form the backbone of process loops where purity, separation, and crystallization are essential outcomes. The water and wastewater treatment sector has seen rising evaporator adoption, particularly in zero-liquid-discharge projects, effluent concentration, and sludge reduction. With local authorities and environmental agencies enforcing strict wastewater discharge regulations, evaporators are becoming essential tools in helping industries comply while reclaiming usable water. Other sectors, such as electronics, cosmetics, textiles, and even construction materials, are also exploring the potential of evaporation systems for recovering materials, concentrating slurries, or enhancing recycling operations.
Considered in this report
• Historic Year: 2019
• Base year: 2024
• Estimated year: 2025
• Forecast year: 2030
Aspects covered in this report
• Industrial Evaporators Market with its value and forecast along with its segments
• Various drivers and challenges
• On-going trends and developments
• Top profiled companies
• Strategic recommendation
By Construction Type
• Shell & Tube
• Plate
By Functionality Type
• Falling Film
• Rising Film
• Forced Circulation Evaporators
• Agitated Thin Film Evaporators
• Mechanical Vapor Recompression
• Others
By End-use Industry Type
• Food & Beverage
• Pharmaceutical
• Chemical & Petrochemical
• Water & Wastewater Treatment
• Others
The approach of the report:
This report consists of a combined approach of primary as well as secondary research. Initially, secondary research was used to get an understanding of the market and listing out the companies that are present in the market. The secondary research consists of third-party sources such as press releases, annual report of companies, analyzing the government generated reports and databases. After gathering the data from secondary sources primary research was conducted by making telephonic interviews with the leading players about how the market is functioning and then conducted trade calls with dealers and distributors of the market. Post this we have started doing primary calls to consumers by equally segmenting consumers in regional aspects, tier aspects, age group, and gender. Once we have primary data with us we have started verifying the details obtained from secondary sources.
Intended audience
This report can be useful to industry consultants, manufacturers, suppliers, associations & organizations related to agriculture industry, government bodies and other stakeholders to align their market-centric strategies. In addition to marketing & presentations, it will also increase competitive knowledge about the industry.
According to the research report, United Kingdom Industrial Evaporators Market Overview, 2030, published by Bonafide Research, the United Kingdom Industrial Evaporators Market is anticipated to add to more than USD 150 Million by 2025–30. The UK industrial evaporators market is not only expanding in scale but also evolving in sophistication, reflecting the country's advanced technological landscape and the growing demand for process-specific thermal separation solutions. Industry 4.0 has begun to transform how evaporators are manufactured, deployed, and managed. Today's leading systems are equipped with digital monitoring tools, data analytics capabilities, and AI-driven optimization features that enable real-time performance tracking and predictive maintenance. These features are increasingly being adopted by UK industries aiming to improve operational uptime, reduce unexpected downtimes, and maintain high product quality while minimizing energy costs. The incorporation of IoT and SCADA systems allows for seamless integration with plant-wide control systems, thereby providing operators with a high degree of process visibility and responsiveness. The United Kingdom's robust R&D ecosystem, powered by universities, technology hubs, and private innovation centers, is fostering the continuous development of evaporators with advanced heat transfer materials, corrosion-resistant coatings, and modular configurations. These advances are enabling broader customization and making it easier to retrofit existing systems, an attractive proposition for industries facing tight budget constraints but requiring high-efficiency equipment. Additionally, sustainability concerns have led to a surge in hybrid systems that blend mechanical and thermal evaporation or integrate waste heat recovery. This ability to adapt and reconfigure based on evolving industrial needs is making modern evaporator systems highly attractive to UK-based firms seeking long-term technological and environmental resilience.
Shell and tube evaporators have long been favored in heavy-duty applications due to their ability to handle high volumes, extreme temperatures, and pressures. Their construction allows for extended continuous operation, making them well-suited for chemical and petrochemical plants, where 24/7 operation and minimal maintenance downtime are often required. These evaporators are also designed to accommodate high thermal and mechanical stresses, ensuring reliable performance over long lifespans. They are often constructed from materials such as stainless steel or high-grade alloys that offer resistance to corrosion and scaling, both critical in high-acidity or high-salinity environments. Conversely, plate evaporators are gaining strong traction in industries where space constraints, energy efficiency, and frequent product changeovers are more relevant. These systems are especially prominent in the UK’s robust food and beverage sector, as well as in pharmaceuticals, where their compact footprint, ease of cleaning, and high heat transfer efficiency provide a clear operational advantage. Plate evaporators are modular by nature, allowing for scalability and rapid adaptation to changing production needs, which is particularly useful for small and medium enterprises seeking flexibility. Furthermore, their reduced surface area and optimized thermal design contribute to lower energy consumption and faster processing cycles. In the UK, there is a growing interest in hybrid systems that combine the robustness of shell and tube with the efficiency and modularity of plate technologies, aimed at maximizing operational flexibility without compromising on durability.
Falling film evaporators dominate in industries where gentle handling of heat-sensitive materials is necessary, making them the go-to choice for the food and beverage sector as well as for pharmaceutical processes involving sensitive active ingredients. These systems allow liquids to form a thin film over heated surfaces, ensuring rapid evaporation with minimal thermal stress. Rising film evaporators, though based on similar principles, are less energy-efficient and are therefore gradually being phased out or used in basic applications such as water treatment or simple chemical processes. Forced circulation evaporators serve more demanding applications where scaling, crystallization, or high-viscosity fluids are involved. Their use of high-capacity pumps to ensure turbulence and uniform heat distribution makes them invaluable in chemical, petrochemical, and certain wastewater operations where solids buildup could otherwise cripple production. Agitated thin film evaporators cater to niche yet increasingly relevant applications, particularly in sectors such as waste recovery, bio-refining, and cosmetics, where thick, sticky, or thermally unstable substances require controlled and efficient evaporation. Mechanical vapor recompression systems are rapidly becoming a cornerstone of sustainability efforts, offering substantial energy savings by recycling vapor from the evaporation process. These systems are particularly relevant in regions of the UK where energy costs are high and regulatory incentives for carbon reduction are available. Furthermore, emerging multifunctional evaporator systems that integrate several functionalities within one unit are beginning to gain traction, especially in R&D labs and pilot plants. These newer systems appeal to firms seeking multi-stage processing in a compact form factor.
The food and beverage industry is a major consumer of evaporator systems, using them for applications such as milk concentration, fruit juice production, flavor extraction, and brewery operations. With consumer demand shifting towards organic and preservative-free products, manufacturers are adopting evaporators that can preserve natural qualities while improving yield and reducing energy costs. Similarly, the pharmaceutical industry in the UK, bolstered by a strong domestic research base and stringent regulatory oversight, relies heavily on evaporators for solvent recovery, purification of active ingredients, and formulation concentration. Systems in this sector must meet exacting standards of contamination control, documentation, and cleaning validation, which has led to the widespread adoption of fully automated, clean-in-place evaporator systems with real-time monitoring. The chemical and petrochemical industries, on the other hand, utilize heavy-duty evaporators capable of handling corrosive and hazardous fluids under high pressure and temperature. These systems often form the backbone of process loops where purity, separation, and crystallization are essential outcomes. The water and wastewater treatment sector has seen rising evaporator adoption, particularly in zero-liquid-discharge projects, effluent concentration, and sludge reduction. With local authorities and environmental agencies enforcing strict wastewater discharge regulations, evaporators are becoming essential tools in helping industries comply while reclaiming usable water. Other sectors, such as electronics, cosmetics, textiles, and even construction materials, are also exploring the potential of evaporation systems for recovering materials, concentrating slurries, or enhancing recycling operations.
Considered in this report
• Historic Year: 2019
• Base year: 2024
• Estimated year: 2025
• Forecast year: 2030
Aspects covered in this report
• Industrial Evaporators Market with its value and forecast along with its segments
• Various drivers and challenges
• On-going trends and developments
• Top profiled companies
• Strategic recommendation
By Construction Type
• Shell & Tube
• Plate
By Functionality Type
• Falling Film
• Rising Film
• Forced Circulation Evaporators
• Agitated Thin Film Evaporators
• Mechanical Vapor Recompression
• Others
By End-use Industry Type
• Food & Beverage
• Pharmaceutical
• Chemical & Petrochemical
• Water & Wastewater Treatment
• Others
The approach of the report:
This report consists of a combined approach of primary as well as secondary research. Initially, secondary research was used to get an understanding of the market and listing out the companies that are present in the market. The secondary research consists of third-party sources such as press releases, annual report of companies, analyzing the government generated reports and databases. After gathering the data from secondary sources primary research was conducted by making telephonic interviews with the leading players about how the market is functioning and then conducted trade calls with dealers and distributors of the market. Post this we have started doing primary calls to consumers by equally segmenting consumers in regional aspects, tier aspects, age group, and gender. Once we have primary data with us we have started verifying the details obtained from secondary sources.
Intended audience
This report can be useful to industry consultants, manufacturers, suppliers, associations & organizations related to agriculture industry, government bodies and other stakeholders to align their market-centric strategies. In addition to marketing & presentations, it will also increase competitive knowledge about the industry.
Table of Contents
77 Pages
- 1. Executive Summary
- 2. Market Structure
- 2.1. Market Considerate
- 2.2. Assumptions
- 2.3. Limitations
- 2.4. Abbreviations
- 2.5. Sources
- 2.6. Definitions
- 3. Research Methodology
- 3.1. Secondary Research
- 3.2. Primary Data Collection
- 3.3. Market Formation & Validation
- 3.4. Report Writing, Quality Check & Delivery
- 4. United Kingdom Geography
- 4.1. Population Distribution Table
- 4.2. United Kingdom Macro Economic Indicators
- 5. Market Dynamics
- 5.1. Key Insights
- 5.2. Recent Developments
- 5.3. Market Drivers & Opportunities
- 5.4. Market Restraints & Challenges
- 5.5. Market Trends
- 5.5.1. XXXX
- 5.5.2. XXXX
- 5.5.3. XXXX
- 5.5.4. XXXX
- 5.5.5. XXXX
- 5.6. Supply chain Analysis
- 5.7. Policy & Regulatory Framework
- 5.8. Industry Experts Views
- 6. United Kingdom Industrial Evaporators Market Overview
- 6.1. Market Size By Value
- 6.2. Market Size and Forecast, By Construction Type
- 6.3. Market Size and Forecast, By Functionality Type
- 6.4. Market Size and Forecast, By End-use Industry Type
- 6.5. Market Size and Forecast, By Region
- 7. United Kingdom Industrial Evaporators Market Segmentations
- 7.1. United Kingdom Industrial Evaporators Market, By Construction Type
- 7.1.1. United Kingdom Industrial Evaporators Market Size, By Shell & Tube, 2019-2030
- 7.1.2. United Kingdom Industrial Evaporators Market Size, By Plate, 2019-2030
- 7.2. United Kingdom Industrial Evaporators Market, By Functionality Type
- 7.2.1. United Kingdom Industrial Evaporators Market Size, By Falling Film, 2019-2030
- 7.2.2. United Kingdom Industrial Evaporators Market Size, By Rising Film, 2019-2030
- 7.2.3. United Kingdom Industrial Evaporators Market Size, By Forced Circulation Evaporators, 2019-2030
- 7.2.4. United Kingdom Industrial Evaporators Market Size, By Agitated Thin Film Evaporators, 2019-2030
- 7.2.5. United Kingdom Industrial Evaporators Market Size, By Mechanical Vapor Recompression, 2019-2030
- 7.2.6. United Kingdom Industrial Evaporators Market Size, By Others, 2019-2030
- 7.3. United Kingdom Industrial Evaporators Market, By End-use Industry Type
- 7.3.1. United Kingdom Industrial Evaporators Market Size, By Food & Beverage, 2019-2030
- 7.3.2. United Kingdom Industrial Evaporators Market Size, By Pharmaceutical, 2019-2030
- 7.3.3. United Kingdom Industrial Evaporators Market Size, By Chemical & Petrochemical, 2019-2030
- 7.3.4. United Kingdom Industrial Evaporators Market Size, By Water & Wastewater Treatment , 2019-2030
- 7.3.5. United Kingdom Industrial Evaporators Market Size, By Others, 2019-2030
- 7.4. United Kingdom Industrial Evaporators Market, By Region
- 7.4.1. United Kingdom Industrial Evaporators Market Size, By North, 2019-2030
- 7.4.2. United Kingdom Industrial Evaporators Market Size, By East, 2019-2030
- 7.4.3. United Kingdom Industrial Evaporators Market Size, By West, 2019-2030
- 7.4.4. United Kingdom Industrial Evaporators Market Size, By South, 2019-2030
- 8. United Kingdom Industrial Evaporators Market Opportunity Assessment
- 8.1. By Construction Type, 2025 to 2030
- 8.2. By Functionality Type, 2025 to 2030
- 8.3. By End-use Industry Type, 2025 to 2030
- 8.4. By Region, 2025 to 2030
- 9. Competitive Landscape
- 9.1. Porter's Five Forces
- 9.2. Company Profile
- 9.2.1. Company 1
- 9.2.1.1. Company Snapshot
- 9.2.1.2. Company Overview
- 9.2.1.3. Financial Highlights
- 9.2.1.4. Geographic Insights
- 9.2.1.5. Business Segment & Performance
- 9.2.1.6. Product Portfolio
- 9.2.1.7. Key Executives
- 9.2.1.8. Strategic Moves & Developments
- 9.2.2. Company 2
- 9.2.3. Company 3
- 9.2.4. Company 4
- 9.2.5. Company 5
- 9.2.6. Company 6
- 9.2.7. Company 7
- 9.2.8. Company 8
- 10. Strategic Recommendations
- 11. Disclaimer
- List of Figures
- Figure 1: United Kingdom Industrial Evaporators Market Size By Value (2019, 2024 & 2030F) (in USD Million)
- Figure 2: Market Attractiveness Index, By Construction Type
- Figure 3: Market Attractiveness Index, By Functionality Type
- Figure 4: Market Attractiveness Index, By End-use Industry Type
- Figure 5: Market Attractiveness Index, By Region
- Figure 6: Porter's Five Forces of United Kingdom Industrial Evaporators Market
- List of Tables
- Table 1: Influencing Factors for Industrial Evaporators Market, 2024
- Table 2: United Kingdom Industrial Evaporators Market Size and Forecast, By Construction Type (2019 to 2030F) (In USD Million)
- Table 3: United Kingdom Industrial Evaporators Market Size and Forecast, By Functionality Type (2019 to 2030F) (In USD Million)
- Table 4: United Kingdom Industrial Evaporators Market Size and Forecast, By End-use Industry Type (2019 to 2030F) (In USD Million)
- Table 5: United Kingdom Industrial Evaporators Market Size and Forecast, By Region (2019 to 2030F) (In USD Million)
- Table 6: United Kingdom Industrial Evaporators Market Size of Shell & Tube (2019 to 2030) in USD Million
- Table 7: United Kingdom Industrial Evaporators Market Size of Plate (2019 to 2030) in USD Million
- Table 8: United Kingdom Industrial Evaporators Market Size of Falling Film (2019 to 2030) in USD Million
- Table 9: United Kingdom Industrial Evaporators Market Size of Rising Film (2019 to 2030) in USD Million
- Table 10: United Kingdom Industrial Evaporators Market Size of Forced Circulation Evaporators (2019 to 2030) in USD Million
- Table 11: United Kingdom Industrial Evaporators Market Size of Agitated Thin Film Evaporators (2019 to 2030) in USD Million
- Table 12: United Kingdom Industrial Evaporators Market Size of Mechanical Vapor Recompression (2019 to 2030) in USD Million
- Table 13: United Kingdom Industrial Evaporators Market Size of Others (2019 to 2030) in USD Million
- Table 14: United Kingdom Industrial Evaporators Market Size of Food & Beverage (2019 to 2030) in USD Million
- Table 15: United Kingdom Industrial Evaporators Market Size of Pharmaceutical (2019 to 2030) in USD Million
- Table 16: United Kingdom Industrial Evaporators Market Size of Chemical & Petrochemical (2019 to 2030) in USD Million
- Table 17: United Kingdom Industrial Evaporators Market Size of Water & Wastewater Treatment (2019 to 2030) in USD Million
- Table 18: United Kingdom Industrial Evaporators Market Size of Others (2019 to 2030) in USD Million
- Table 19: United Kingdom Industrial Evaporators Market Size of North (2019 to 2030) in USD Million
- Table 20: United Kingdom Industrial Evaporators Market Size of East (2019 to 2030) in USD Million
- Table 21: United Kingdom Industrial Evaporators Market Size of West (2019 to 2030) in USD Million
- Table 22: United Kingdom Industrial Evaporators Market Size of South (2019 to 2030) in USD Million
Pricing
Currency Rates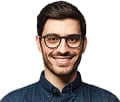
Questions or Comments?
Our team has the ability to search within reports to verify it suits your needs. We can also help maximize your budget by finding sections of reports you can purchase.