
United Kingdom Automotive Metals Market Overview, 2030
Description
The UK automotive metals sphere, a crucible of engineered resilience, hums with the legacy of Birmingham's industrial heart, a narrative forged in the soot and steel of yesteryear. It's a theatre where wrought alloys and precision-cast components dance a delicate ballet, driven by the rhythmic pulse of production lines. Here, the raw heft of high-tensile steel, the featherweight agility of aluminium, and the esoteric contributions of rare-earth metals converge, shaping the skeletal framework and kinetic heart of British motoring. This isn't merely a market; it's a living ecosystem where the metallic sinews of vehicles, from the chassis' sturdy backbone to the intricate gears of the drivetrain, are meticulously crafted. The clang of presses, the hiss of robotic welders, and the subtle shimmer of anodized surfaces paint a vivid portrait of a sector perpetually striving for lighter, stronger, and more sustainable solutions. The very air is thick with the scent of machining oils and the faint metallic tang of freshly formed components, a testament to the relentless pursuit of automotive excellence. This realm, marked by the constant evolution of material science, is where the past's robust legacy meets the future's demand for efficiency and innovation, all within the uniquely British context of automotive engineering. The UK automotive metals regulatory landscape, a tapestry woven with threads of EU harmonization and post-Brexit recalibration, reflects a historical trajectory marked by stringent environmental mandates and evolving safety protocols. From the early days of leaded steel phase-outs to the modern era of stringent carbon emission targets, policy has consistently shaped the composition and application of automotive metals. The specter of REACH compliance, now nuanced by UK-specific chemical regulations, looms large, demanding meticulous material traceability and lifecycle assessments. The echoes of the ""end-of-life vehicle"" directive, reverberating through recycling infrastructure, underscore the commitment to circular economy principles. Furthermore, the push for lightweighting, fueled by CO2 reduction targets, has triggered a shift towards advanced alloys and composites, necessitating a constant reevaluation of material standards and testing protocols. The government's active engagement in fostering domestic metal production and recycling, through targeted investments and strategic partnerships, underscores the strategic importance of this sector to the UK's industrial future.
According to the research report, “UK Automotive metals Market Overview, 2030,"" published by Bonafide Research, the UK Automotive metals market is anticipated to add to more than USD 750 Million by 2025–30. The UK automotive metals market, a dynamic arena of evolving demands, is currently navigating a complex interplay of forces. The electric vehicle (EV) revolution, a potent market driver, is reshaping metal selection, favouring lightweight aluminium and rare-earth magnets for electric powertrains. The drive for sustainability, coupled with stringent emission regulations, fuels demand for high-strength steel and recycled metals. Trade programs, such as the UK's participation in bilateral trade agreements and the pursuit of domestic supply chain resilience, are crucial in securing access to critical raw materials and fostering export opportunities. The fluctuating global commodity prices, coupled with supply chain disruptions, have introduced volatility, necessitating strategic sourcing and inventory management. The automotive industry's push for advanced manufacturing techniques, such as additive manufacturing and high-pressure die casting, is driving demand for specialized alloys and precision-engineered metal components. Moreover, the UK's focus on advanced research and development in materials science, supported by government initiatives and industry collaborations, is fostering innovation and competitiveness in the global market. The market, further influenced by consumer preferences for safety and performance, is witnessing a surge in demand for advanced high-strength steels and aluminium alloys designed for enhanced crashworthiness and lightweighting.
The UK automotive metals product type segment is a nuanced ecosystem where steel, aluminium, and other specialized metals vie for dominance, each with its distinct application. Steel, the stalwart of automotive manufacturing, continues to be the backbone of chassis construction and body panels, particularly in heavy commercial vehicles and traditional passenger cars. Advanced high-strength steels, engineered for superior crash performance and lightweighting, are increasingly favored. Aluminium, prized for its lightweight properties, is gaining prominence in electric vehicle platforms, body structures, and powertrain components, contributing to improved energy efficiency. The UK's advanced aluminium casting and extrusion capabilities support the production of intricate components for chassis, suspension, and electric vehicle battery housings. ""Others"" encompasses a diverse array of specialized metals, including magnesium alloys for lightweight interior components, titanium for high-performance applications, and rare-earth metals for electric motors and magnets. The UK's expertise in specialized metal processing and fabrication enables the production of high-quality components for niche applications and advanced vehicle technologies. The increasing demand for lightweighting and electrification is driving innovation in alloy development and manufacturing processes, ensuring the UK's continued competitiveness in the global market.
The UK automotive metals application segment is a complex interplay of material properties and engineering requirements, where body structure, powertrain, suspension, and other applications demand tailored metallic solutions. Body structure, the foundation of vehicle integrity, relies heavily on high-strength steel and aluminium alloys for crashworthiness and lightweighting. The powertrain, the heart of the vehicle, utilizes a range of metals, including steel for engine blocks and crankshafts, aluminium for cylinder heads and housings, and rare-earth metals for electric motors. Suspension systems, designed for optimal handling and ride comfort, employ steel for springs and control arms, and aluminium for lightweight components like suspension knuckles and subframes. ""Others"" encompasses a wide range of applications, including interior trim, braking systems, and electrical components. The UK's expertise in advanced manufacturing techniques, such as high-pressure die casting and additive manufacturing, enables the production of intricate and high-performance components for these diverse applications. The increasing demand for electric vehicles and lightweighting is driving innovation in material selection and component design, ensuring the UK's continued leadership in automotive engineering.
The UK automotive metals end-user segment is a multifaceted landscape, catering to a diverse range of vehicle types, from two-wheelers to heavy commercial vehicles. Two-wheelers, encompassing motorcycles and scooters, utilize lightweight aluminium alloys for frames and components, prioritizing agility and performance. Passenger vehicles, the largest segment, demand a wide range of metals, from high-strength steel for chassis and body panels to aluminium for lightweighting and electric vehicle applications. Light commercial vehicles, including vans and small trucks, rely on robust steel construction for durability and load-carrying capacity, with increasing adoption of aluminium for weight reduction. Heavy commercial vehicles, such as trucks and buses, demand high-strength steel for heavy-duty applications, ensuring structural integrity and longevity. The UK's robust manufacturing infrastructure and skilled workforce support the production of high-quality components for these diverse end-user segments. The increasing demand for electric vehicles and sustainable transportation solutions is driving a shift towards lightweight materials and advanced manufacturing techniques, ensuring the UK's continued competitiveness in the global automotive market.
Considered in this report
• Historic Year: 2019
• Base year: 2024
• Estimated year: 2025
• Forecast year: 2030
Aspects covered in this report
• Automotive Metal Market with its value and forecast along with its segments
• Various drivers and challenges
• On-going trends and developments
• Top profiled companies
• Strategic recommendation
By Product
• Steel
• Aluminum
• Others
By Application
• Body structure
• Power train
• Suspension
• Others
By End-Use
• Two Wheelers
• Passenger Vehicle
• Light Commercial Vehicles
• Heavy Commercial Vehicles
The approach of the report:
This report consists of a combined approach of primary as well as secondary research. Initially, secondary research was used to get an understanding of the market and listing out the companies that are present in the market. The secondary research consists of third-party sources such as press releases, annual report of companies, analyzing the government generated reports and databases. After gathering the data from secondary sources primary research was conducted by making telephonic interviews with the leading players about how the market is functioning and then conducted trade calls with dealers and distributors of the market. Post this we have started doing primary calls to consumers by equally segmenting consumers in regional aspects, tier aspects, age group, and gender. Once we have primary data with us we have started verifying the details obtained from secondary sources.
Intended audience
This report can be useful to industry consultants, manufacturers, suppliers, associations & organizations related to agriculture industry, government bodies and other stakeholders to align their market-centric strategies. In addition to marketing & presentations, it will also increase competitive knowledge about the industry.
According to the research report, “UK Automotive metals Market Overview, 2030,"" published by Bonafide Research, the UK Automotive metals market is anticipated to add to more than USD 750 Million by 2025–30. The UK automotive metals market, a dynamic arena of evolving demands, is currently navigating a complex interplay of forces. The electric vehicle (EV) revolution, a potent market driver, is reshaping metal selection, favouring lightweight aluminium and rare-earth magnets for electric powertrains. The drive for sustainability, coupled with stringent emission regulations, fuels demand for high-strength steel and recycled metals. Trade programs, such as the UK's participation in bilateral trade agreements and the pursuit of domestic supply chain resilience, are crucial in securing access to critical raw materials and fostering export opportunities. The fluctuating global commodity prices, coupled with supply chain disruptions, have introduced volatility, necessitating strategic sourcing and inventory management. The automotive industry's push for advanced manufacturing techniques, such as additive manufacturing and high-pressure die casting, is driving demand for specialized alloys and precision-engineered metal components. Moreover, the UK's focus on advanced research and development in materials science, supported by government initiatives and industry collaborations, is fostering innovation and competitiveness in the global market. The market, further influenced by consumer preferences for safety and performance, is witnessing a surge in demand for advanced high-strength steels and aluminium alloys designed for enhanced crashworthiness and lightweighting.
The UK automotive metals product type segment is a nuanced ecosystem where steel, aluminium, and other specialized metals vie for dominance, each with its distinct application. Steel, the stalwart of automotive manufacturing, continues to be the backbone of chassis construction and body panels, particularly in heavy commercial vehicles and traditional passenger cars. Advanced high-strength steels, engineered for superior crash performance and lightweighting, are increasingly favored. Aluminium, prized for its lightweight properties, is gaining prominence in electric vehicle platforms, body structures, and powertrain components, contributing to improved energy efficiency. The UK's advanced aluminium casting and extrusion capabilities support the production of intricate components for chassis, suspension, and electric vehicle battery housings. ""Others"" encompasses a diverse array of specialized metals, including magnesium alloys for lightweight interior components, titanium for high-performance applications, and rare-earth metals for electric motors and magnets. The UK's expertise in specialized metal processing and fabrication enables the production of high-quality components for niche applications and advanced vehicle technologies. The increasing demand for lightweighting and electrification is driving innovation in alloy development and manufacturing processes, ensuring the UK's continued competitiveness in the global market.
The UK automotive metals application segment is a complex interplay of material properties and engineering requirements, where body structure, powertrain, suspension, and other applications demand tailored metallic solutions. Body structure, the foundation of vehicle integrity, relies heavily on high-strength steel and aluminium alloys for crashworthiness and lightweighting. The powertrain, the heart of the vehicle, utilizes a range of metals, including steel for engine blocks and crankshafts, aluminium for cylinder heads and housings, and rare-earth metals for electric motors. Suspension systems, designed for optimal handling and ride comfort, employ steel for springs and control arms, and aluminium for lightweight components like suspension knuckles and subframes. ""Others"" encompasses a wide range of applications, including interior trim, braking systems, and electrical components. The UK's expertise in advanced manufacturing techniques, such as high-pressure die casting and additive manufacturing, enables the production of intricate and high-performance components for these diverse applications. The increasing demand for electric vehicles and lightweighting is driving innovation in material selection and component design, ensuring the UK's continued leadership in automotive engineering.
The UK automotive metals end-user segment is a multifaceted landscape, catering to a diverse range of vehicle types, from two-wheelers to heavy commercial vehicles. Two-wheelers, encompassing motorcycles and scooters, utilize lightweight aluminium alloys for frames and components, prioritizing agility and performance. Passenger vehicles, the largest segment, demand a wide range of metals, from high-strength steel for chassis and body panels to aluminium for lightweighting and electric vehicle applications. Light commercial vehicles, including vans and small trucks, rely on robust steel construction for durability and load-carrying capacity, with increasing adoption of aluminium for weight reduction. Heavy commercial vehicles, such as trucks and buses, demand high-strength steel for heavy-duty applications, ensuring structural integrity and longevity. The UK's robust manufacturing infrastructure and skilled workforce support the production of high-quality components for these diverse end-user segments. The increasing demand for electric vehicles and sustainable transportation solutions is driving a shift towards lightweight materials and advanced manufacturing techniques, ensuring the UK's continued competitiveness in the global automotive market.
Considered in this report
• Historic Year: 2019
• Base year: 2024
• Estimated year: 2025
• Forecast year: 2030
Aspects covered in this report
• Automotive Metal Market with its value and forecast along with its segments
• Various drivers and challenges
• On-going trends and developments
• Top profiled companies
• Strategic recommendation
By Product
• Steel
• Aluminum
• Others
By Application
• Body structure
• Power train
• Suspension
• Others
By End-Use
• Two Wheelers
• Passenger Vehicle
• Light Commercial Vehicles
• Heavy Commercial Vehicles
The approach of the report:
This report consists of a combined approach of primary as well as secondary research. Initially, secondary research was used to get an understanding of the market and listing out the companies that are present in the market. The secondary research consists of third-party sources such as press releases, annual report of companies, analyzing the government generated reports and databases. After gathering the data from secondary sources primary research was conducted by making telephonic interviews with the leading players about how the market is functioning and then conducted trade calls with dealers and distributors of the market. Post this we have started doing primary calls to consumers by equally segmenting consumers in regional aspects, tier aspects, age group, and gender. Once we have primary data with us we have started verifying the details obtained from secondary sources.
Intended audience
This report can be useful to industry consultants, manufacturers, suppliers, associations & organizations related to agriculture industry, government bodies and other stakeholders to align their market-centric strategies. In addition to marketing & presentations, it will also increase competitive knowledge about the industry.
Table of Contents
75 Pages
- 1. Executive Summary
- 2. Market Structure
- 2.1. Market Considerate
- 2.2. Assumptions
- 2.3. Limitations
- 2.4. Abbreviations
- 2.5. Sources
- 2.6. Definitions
- 3. Research Methodology
- 3.1. Secondary Research
- 3.2. Primary Data Collection
- 3.3. Market Formation & Validation
- 3.4. Report Writing, Quality Check & Delivery
- 4. United Kingdom Geography
- 4.1. Population Distribution Table
- 4.2. United Kingdom Macro Economic Indicators
- 5. Market Dynamics
- 5.1. Key Insights
- 5.2. Recent Developments
- 5.3. Market Drivers & Opportunities
- 5.4. Market Restraints & Challenges
- 5.5. Market Trends
- 5.5.1. XXXX
- 5.5.2. XXXX
- 5.5.3. XXXX
- 5.5.4. XXXX
- 5.5.5. XXXX
- 5.6. Supply chain Analysis
- 5.7. Policy & Regulatory Framework
- 5.8. Industry Experts Views
- 6. United Kingdom Automotive Metals Market Overview
- 6.1. Market Size By Value
- 6.2. Market Size and Forecast, By Product
- 6.3. Market Size and Forecast, By Application
- 6.4. Market Size and Forecast, By End-Use
- 6.5. Market Size and Forecast, By Region
- 7. United Kingdom Automotive Metals Market Segmentations
- 7.1. United Kingdom Automotive Metals Market, By Product
- 7.1.1. United Kingdom Automotive Metals Market Size, By Steel, 2019-2030
- 7.1.2. United Kingdom Automotive Metals Market Size, By Aluminum, 2019-2030
- 7.1.3. United Kingdom Automotive Metals Market Size, By Others, 2019-2030
- 7.2. United Kingdom Automotive Metals Market, By Application
- 7.2.1. United Kingdom Automotive Metals Market Size, By Body structure, 2019-2030
- 7.2.2. United Kingdom Automotive Metals Market Size, By Power train, 2019-2030
- 7.2.3. United Kingdom Automotive Metals Market Size, By Suspension, 2019-2030
- 7.2.4. United Kingdom Automotive Metals Market Size, By Others, 2019-2030
- 7.3. United Kingdom Automotive Metals Market, By End-Use
- 7.3.1. United Kingdom Automotive Metals Market Size, By Two Wheelers, 2019-2030
- 7.3.2. United Kingdom Automotive Metals Market Size, By Passenger Vehicle, 2019-2030
- 7.3.3. United Kingdom Automotive Metals Market Size, By Light Commercial Vehicles, 2019-2030
- 7.3.4. United Kingdom Automotive Metals Market Size, By Heavy Commercial Vehicles, 2019-2030
- 7.4. United Kingdom Automotive Metals Market, By Region
- 7.4.1. United Kingdom Automotive Metals Market Size, By North, 2019-2030
- 7.4.2. United Kingdom Automotive Metals Market Size, By East, 2019-2030
- 7.4.3. United Kingdom Automotive Metals Market Size, By West, 2019-2030
- 7.4.4. United Kingdom Automotive Metals Market Size, By South, 2019-2030
- 8. United Kingdom Automotive Metals Market Opportunity Assessment
- 8.1. By Product, 2025 to 2030
- 8.2. By Application, 2025 to 2030
- 8.3. By End-Use, 2025 to 2030
- 8.4. By Region, 2025 to 2030
- 9. Competitive Landscape
- 9.1. Porter's Five Forces
- 9.2. Company Profile
- 9.2.1. Company 1
- 9.2.1.1. Company Snapshot
- 9.2.1.2. Company Overview
- 9.2.1.3. Financial Highlights
- 9.2.1.4. Geographic Insights
- 9.2.1.5. Business Segment & Performance
- 9.2.1.6. Product Portfolio
- 9.2.1.7. Key Executives
- 9.2.1.8. Strategic Moves & Developments
- 9.2.2. Company 2
- 9.2.3. Company 3
- 9.2.4. Company 4
- 9.2.5. Company 5
- 9.2.6. Company 6
- 9.2.7. Company 7
- 9.2.8. Company 8
- 10. Strategic Recommendations
- 11. Disclaimer
- List of Figures
- Figure 1: United Kingdom Automotive Metals Market Size By Value (2019, 2024 & 2030F) (in USD Million)
- Figure 2: Market Attractiveness Index, By Product
- Figure 3: Market Attractiveness Index, By Application
- Figure 4: Market Attractiveness Index, By End-Use
- Figure 5: Market Attractiveness Index, By Region
- Figure 6: Porter's Five Forces of United Kingdom Automotive Metals Market
- List of Tables
- Table 1: Influencing Factors for Automotive Metals Market, 2024
- Table 2: United Kingdom Automotive Metals Market Size and Forecast, By By Product (2019 to 2030F) (In USD Million)
- Table 3: United Kingdom Automotive Metals Market Size and Forecast, By By Application (2019 to 2030F) (In USD Million)
- Table 4: United Kingdom Automotive Metals Market Size and Forecast, By By End-Use (2019 to 2030F) (In USD Million)
- Table 5: United Kingdom Automotive Metals Market Size and Forecast, By Region (2019 to 2030F) (In USD Million)
- Table 6: United Kingdom Automotive Metals Market Size of Steel (2019 to 2030) in USD Million
- Table 7: United Kingdom Automotive Metals Market Size of Aluminum (2019 to 2030) in USD Million
- Table 8: United Kingdom Automotive Metals Market Size of Others (2019 to 2030) in USD Million
- Table 9: United Kingdom Automotive Metals Market Size of Body structure (2019 to 2030) in USD Million
- Table 10: United Kingdom Automotive Metals Market Size of Power train (2019 to 2030) in USD Million
- Table 11: United Kingdom Automotive Metals Market Size of Suspension (2019 to 2030) in USD Million
- Table 12: United Kingdom Automotive Metals Market Size of Others (2019 to 2030) in USD Million
- Table 13: United Kingdom Automotive Metals Market Size of Two Wheelers (2019 to 2030) in USD Million
- Table 14: United Kingdom Automotive Metals Market Size of Passenger Vehicle (2019 to 2030) in USD Million
- Table 15: United Kingdom Automotive Metals Market Size of Light Commercial Vehicles (2019 to 2030) in USD Million
- Table 16: United Kingdom Automotive Metals Market Size of Heavy Commercial Vehicles (2019 to 2030) in USD Million
- Table 17: United Kingdom Automotive Metals Market Size of North (2019 to 2030) in USD Million
- Table 18: United Kingdom Automotive Metals Market Size of East (2019 to 2030) in USD Million
- Table 19: United Kingdom Automotive Metals Market Size of West (2019 to 2030) in USD Million
- Table 20: United Kingdom Automotive Metals Market Size of South (2019 to 2030) in USD Million
Pricing
Currency Rates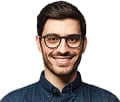
Questions or Comments?
Our team has the ability to search within reports to verify it suits your needs. We can also help maximize your budget by finding sections of reports you can purchase.