
Japan Air Quality Control Systems Market Overview, 2030
Description
Japan's air quality control systems market is evolving into one of the most technologically advanced and policy-driven sectors within the broader environmental engineering landscape. As an industrialized nation with a long history of grappling with pollution-related challenges, Japan has consistently prioritized air quality improvement through a combination of stringent environmental regulations, robust public policy, and a culture of technological innovation. The country's dense urbanization and concentration of industrial activities necessitate precise, high-efficiency systems capable of addressing a wide array of air pollutants, from fine particulates to hazardous chemical compounds. Government institutions such as the Ministry of the Environment and local prefectural agencies continue to impose and update air quality standards in alignment with international protocols and domestic public health goals. Consequently, both private enterprises and public utilities are compelled to adopt increasingly sophisticated emission control technologies. Japan’s emphasis on sustainability and decarbonization further reinforces the integration of air quality control systems into broader environmental management frameworks, particularly within sectors undergoing transitions toward green energy and low-emission manufacturing. Investments in smart city initiatives and digital environmental monitoring are also boosting the demand for advanced air quality control infrastructure, underpinned by artificial intelligence, real-time analytics, and IoT-enabled devices.
According to the research report Japan Air Quality Control Systems Market Overview, 2030, published by Bonafide Research, the Japan Air Quality Control Systems Market is expected to reach a market size of more than USD 5.49 Billion by 2030. The growing emphasis on decarbonization, circular economy principles, and ESG-compliant industrial operations is reshaping the demand for air quality control systems across Japan’s core industrial and energy sectors. As industries face mounting pressure to align operations with carbon neutrality and pollution abatement objectives, the role of air quality technologies is becoming both regulatory and strategic. Japan’s manufacturing sector, which spans automotive, chemicals, metallurgy, and cement, continues to deploy air pollution control systems not only for compliance but also to enhance operational efficiency and social license to operate. There is an increasing tendency to integrate air quality systems with broader environmental automation setups, ensuring seamless coordination between emission monitoring, filtration, and waste management. In power generation, especially within fossil-fuel reliant and biomass plants, sophisticated AQCS setups are being installed to meet both particulate and gaseous emission limits. These include multi-stage filtration systems, real-time gas analyzers, and hybrid scrubbing units designed for adaptability and redundancy. In urban centers and industrial belts, localized pollution monitoring and response mechanisms are also gaining traction, supported by national efforts to decentralize environmental governance. Japan’s unique geography, characterized by mountainous regions and coastal plains, also affects the dispersion and concentration of pollutants, leading to region-specific demand for both indoor and ambient air control systems. The resurgence of energy security concerns, driven by geopolitical uncertainties and fossil fuel dependency, is driving innovation in cleaner thermal generation methods that inherently depend on high-performance air quality systems. Public-private partnerships, green bonds, and government subsidies are increasingly leveraged to finance next-generation AQCS deployment, making Japan a frontrunner in the global air quality management landscape.
Electrostatic precipitators remain integral to power plants, cement kilns, and steel production units due to their remarkable efficiency in removing fine particulates from flue gas. Their adaptability to handle large volumes of gas with minimal pressure drop and maintenance needs makes them particularly valuable in legacy facilities undergoing technological upgrades. Flue gas desulfurization systems, especially wet variants using lime-based reagents, are widely employed to curb sulfur dioxide emissions, reflecting Japan’s adherence to transboundary air pollution agreements and acid rain mitigation efforts. Scrubber systems, both wet and dry, are used extensively in sectors ranging from municipal waste incineration to chemical manufacturing, offering flexible pollutant removal across acidic gases, VOCs, and dust. Selective catalytic reduction systems are prominently installed in both stationary sources like power plants and mobile applications such as marine vessels and heavy-duty transport vehicles. Their ability to reduce nitrogen oxides aligns with Japan’s broader goals of smog reduction and ozone layer protection. Fabric filters or baghouses serve as essential components in dust-intensive operations, notably in cement manufacturing and biomass energy conversion, providing extremely high efficiency in particulate matter control. Catalytic converters, once confined to automotive exhaust systems, are now increasingly deployed in industrial engines and backup generators to manage localized emissions. Thermal oxidizers find application in solvent-heavy industries such as pharmaceutical and electronics production, where they ensure safe disposal of hazardous organic compounds. Additionally, niche technologies like activated carbon injection for mercury control and hybrid systems combining filtration and catalytic processes are gaining ground in response to ultra-low emission targets and site-specific challenges.
The power generation sector, especially thermal and waste-to-energy plants, continues to be a primary driver of demand for large-scale AQCS technologies. These facilities are major contributors of SO₂, NOx, and heavy metals, necessitating complex configurations involving ESPs, FGD units, and SCR systems to meet strict discharge limits. In the cement industry, where kilns emit substantial quantities of dust, acidic gases, and NOx, the integration of fabric filters and low-NOx combustion systems is standard practice. Automotive applications, both in vehicle exhaust treatment and production facility emissions, are heavily influenced by government mandates on fuel efficiency and air quality. Catalytic converters dominate vehicle installations, while scrubbers and oxidizers manage emissions from paint shops and engine testing facilities. The chemical and petrochemical industries, with their complex VOC and HAP emissions, rely on thermal oxidizers and wet scrubbers customized for varying gas loads and toxicity levels. In metal processing and mining, operations that generate airborne heavy metals and sulfur compounds employ a mix of baghouses, ESPs, and dry scrubbers to prevent contamination of nearby communities and natural ecosystems. Pharmaceutical production, while not a high-volume emitter, requires precise control over VOCs and indoor air purity, often achieved through carbon filters and HEPA-grade filtration systems. Other sectors such as food processing and pulp and paper contribute to localized air quality concerns through odor and particulate emissions, prompting the use of biofilters, wet scrubbers, and compact filtration units.
Indoor systems are increasingly in demand in industries where product sensitivity or human health is at risk from airborne contaminants. These include pharmaceuticals, semiconductors, food processing, and clean manufacturing zones, where the control of particulate matter, microbes, and VOCs is mission-critical. Technologies such as HEPA filtration, activated carbon filters, catalytic oxidizers, and ducted scrubber systems are often integrated into HVAC units to maintain optimal indoor air conditions. These systems are engineered for precision and modularity, allowing for retrofitting into existing production lines or cleanrooms without compromising throughput. Ambient air quality systems, on the other hand, are geared toward large-scale pollutant capture prior to environmental release, focusing on compliance with outdoor emission standards. These systems are commonly seen in heavy industries and power plants, utilizing ESPs, tall-stack FGD units, and SCR modules to ensure that emissions meet environmental discharge norms. Unlike indoor systems, ambient units must endure variable weather conditions, large volumetric flows, and fluctuating pollutant loads, requiring robust design and automated performance monitoring. As the national discourse shifts toward sustainable industrialization and low-carbon transitions, both indoor and ambient AQCS are being augmented with digital enhancements like IoT sensors, AI-based diagnostics, and predictive maintenance tools. These innovations are helping Japanese industries maintain air quality standards with greater accuracy and lower operational costs, reflecting a holistic approach that treats air quality not just as a compliance metric, but as an integral part of overall process excellence and social responsibility.
Considered in this report
• Historic Year: 2019
• Base year: 2024
• Estimated year: 2025
• Forecast year: 2030
Aspects covered in this report
• Air Quality Control System Market with its value and forecast along with its segments
• Various drivers and challenges
• On-going trends and developments
• Top profiled companies
• Strategic recommendation
By Technology
• Electrostatic Precipitators (ESP)
• Flue Gas Desulfurization (FGD)
• Scrubbers (Wet & Dry)
• Selective Catalytic Reduction (SCR)
• Fabric Filters (Baghouses)
• Catalytic Converters
• Thermal Oxidizers
• Others (Mercury Control Systems, Hybrid Systems)
By Application
• Power Generation
• Cement Industry
• Automotive
• Chemical & Petrochemical
• Metal Processing & Mining
• Pharmaceuticals
• Others (Food processing, Pulp & Paper)
By Product type
• Indoor
• Ambient
The approach of the report:
This report consists of a combined approach of primary as well as secondary research. Initially, secondary research was used to get an understanding of the market and listing out the companies that are present in the market. The secondary research consists of third-party sources such as press releases, annual report of companies, analyzing the government generated reports and databases. After gathering the data from secondary sources primary research was conducted by making telephonic interviews with the leading players about how the market is functioning and then conducted trade calls with dealers and distributors of the market. Post this we have started doing primary calls to consumers by equally segmenting consumers in regional aspects, tier aspects, age group, and gender. Once we have primary data with us we have started verifying the details obtained from secondary sources.
Intended audience
This report can be useful to industry consultants, manufacturers, suppliers, associations & organizations related to agriculture industry, government bodies and other stakeholders to align their market-centric strategies. In addition to marketing & presentations, it will also increase competitive knowledge about the industry.
According to the research report Japan Air Quality Control Systems Market Overview, 2030, published by Bonafide Research, the Japan Air Quality Control Systems Market is expected to reach a market size of more than USD 5.49 Billion by 2030. The growing emphasis on decarbonization, circular economy principles, and ESG-compliant industrial operations is reshaping the demand for air quality control systems across Japan’s core industrial and energy sectors. As industries face mounting pressure to align operations with carbon neutrality and pollution abatement objectives, the role of air quality technologies is becoming both regulatory and strategic. Japan’s manufacturing sector, which spans automotive, chemicals, metallurgy, and cement, continues to deploy air pollution control systems not only for compliance but also to enhance operational efficiency and social license to operate. There is an increasing tendency to integrate air quality systems with broader environmental automation setups, ensuring seamless coordination between emission monitoring, filtration, and waste management. In power generation, especially within fossil-fuel reliant and biomass plants, sophisticated AQCS setups are being installed to meet both particulate and gaseous emission limits. These include multi-stage filtration systems, real-time gas analyzers, and hybrid scrubbing units designed for adaptability and redundancy. In urban centers and industrial belts, localized pollution monitoring and response mechanisms are also gaining traction, supported by national efforts to decentralize environmental governance. Japan’s unique geography, characterized by mountainous regions and coastal plains, also affects the dispersion and concentration of pollutants, leading to region-specific demand for both indoor and ambient air control systems. The resurgence of energy security concerns, driven by geopolitical uncertainties and fossil fuel dependency, is driving innovation in cleaner thermal generation methods that inherently depend on high-performance air quality systems. Public-private partnerships, green bonds, and government subsidies are increasingly leveraged to finance next-generation AQCS deployment, making Japan a frontrunner in the global air quality management landscape.
Electrostatic precipitators remain integral to power plants, cement kilns, and steel production units due to their remarkable efficiency in removing fine particulates from flue gas. Their adaptability to handle large volumes of gas with minimal pressure drop and maintenance needs makes them particularly valuable in legacy facilities undergoing technological upgrades. Flue gas desulfurization systems, especially wet variants using lime-based reagents, are widely employed to curb sulfur dioxide emissions, reflecting Japan’s adherence to transboundary air pollution agreements and acid rain mitigation efforts. Scrubber systems, both wet and dry, are used extensively in sectors ranging from municipal waste incineration to chemical manufacturing, offering flexible pollutant removal across acidic gases, VOCs, and dust. Selective catalytic reduction systems are prominently installed in both stationary sources like power plants and mobile applications such as marine vessels and heavy-duty transport vehicles. Their ability to reduce nitrogen oxides aligns with Japan’s broader goals of smog reduction and ozone layer protection. Fabric filters or baghouses serve as essential components in dust-intensive operations, notably in cement manufacturing and biomass energy conversion, providing extremely high efficiency in particulate matter control. Catalytic converters, once confined to automotive exhaust systems, are now increasingly deployed in industrial engines and backup generators to manage localized emissions. Thermal oxidizers find application in solvent-heavy industries such as pharmaceutical and electronics production, where they ensure safe disposal of hazardous organic compounds. Additionally, niche technologies like activated carbon injection for mercury control and hybrid systems combining filtration and catalytic processes are gaining ground in response to ultra-low emission targets and site-specific challenges.
The power generation sector, especially thermal and waste-to-energy plants, continues to be a primary driver of demand for large-scale AQCS technologies. These facilities are major contributors of SO₂, NOx, and heavy metals, necessitating complex configurations involving ESPs, FGD units, and SCR systems to meet strict discharge limits. In the cement industry, where kilns emit substantial quantities of dust, acidic gases, and NOx, the integration of fabric filters and low-NOx combustion systems is standard practice. Automotive applications, both in vehicle exhaust treatment and production facility emissions, are heavily influenced by government mandates on fuel efficiency and air quality. Catalytic converters dominate vehicle installations, while scrubbers and oxidizers manage emissions from paint shops and engine testing facilities. The chemical and petrochemical industries, with their complex VOC and HAP emissions, rely on thermal oxidizers and wet scrubbers customized for varying gas loads and toxicity levels. In metal processing and mining, operations that generate airborne heavy metals and sulfur compounds employ a mix of baghouses, ESPs, and dry scrubbers to prevent contamination of nearby communities and natural ecosystems. Pharmaceutical production, while not a high-volume emitter, requires precise control over VOCs and indoor air purity, often achieved through carbon filters and HEPA-grade filtration systems. Other sectors such as food processing and pulp and paper contribute to localized air quality concerns through odor and particulate emissions, prompting the use of biofilters, wet scrubbers, and compact filtration units.
Indoor systems are increasingly in demand in industries where product sensitivity or human health is at risk from airborne contaminants. These include pharmaceuticals, semiconductors, food processing, and clean manufacturing zones, where the control of particulate matter, microbes, and VOCs is mission-critical. Technologies such as HEPA filtration, activated carbon filters, catalytic oxidizers, and ducted scrubber systems are often integrated into HVAC units to maintain optimal indoor air conditions. These systems are engineered for precision and modularity, allowing for retrofitting into existing production lines or cleanrooms without compromising throughput. Ambient air quality systems, on the other hand, are geared toward large-scale pollutant capture prior to environmental release, focusing on compliance with outdoor emission standards. These systems are commonly seen in heavy industries and power plants, utilizing ESPs, tall-stack FGD units, and SCR modules to ensure that emissions meet environmental discharge norms. Unlike indoor systems, ambient units must endure variable weather conditions, large volumetric flows, and fluctuating pollutant loads, requiring robust design and automated performance monitoring. As the national discourse shifts toward sustainable industrialization and low-carbon transitions, both indoor and ambient AQCS are being augmented with digital enhancements like IoT sensors, AI-based diagnostics, and predictive maintenance tools. These innovations are helping Japanese industries maintain air quality standards with greater accuracy and lower operational costs, reflecting a holistic approach that treats air quality not just as a compliance metric, but as an integral part of overall process excellence and social responsibility.
Considered in this report
• Historic Year: 2019
• Base year: 2024
• Estimated year: 2025
• Forecast year: 2030
Aspects covered in this report
• Air Quality Control System Market with its value and forecast along with its segments
• Various drivers and challenges
• On-going trends and developments
• Top profiled companies
• Strategic recommendation
By Technology
• Electrostatic Precipitators (ESP)
• Flue Gas Desulfurization (FGD)
• Scrubbers (Wet & Dry)
• Selective Catalytic Reduction (SCR)
• Fabric Filters (Baghouses)
• Catalytic Converters
• Thermal Oxidizers
• Others (Mercury Control Systems, Hybrid Systems)
By Application
• Power Generation
• Cement Industry
• Automotive
• Chemical & Petrochemical
• Metal Processing & Mining
• Pharmaceuticals
• Others (Food processing, Pulp & Paper)
By Product type
• Indoor
• Ambient
The approach of the report:
This report consists of a combined approach of primary as well as secondary research. Initially, secondary research was used to get an understanding of the market and listing out the companies that are present in the market. The secondary research consists of third-party sources such as press releases, annual report of companies, analyzing the government generated reports and databases. After gathering the data from secondary sources primary research was conducted by making telephonic interviews with the leading players about how the market is functioning and then conducted trade calls with dealers and distributors of the market. Post this we have started doing primary calls to consumers by equally segmenting consumers in regional aspects, tier aspects, age group, and gender. Once we have primary data with us we have started verifying the details obtained from secondary sources.
Intended audience
This report can be useful to industry consultants, manufacturers, suppliers, associations & organizations related to agriculture industry, government bodies and other stakeholders to align their market-centric strategies. In addition to marketing & presentations, it will also increase competitive knowledge about the industry.
Table of Contents
78 Pages
- 1. Executive Summary
- 2. Market Structure
- 2.1. Market Considerate
- 2.2. Assumptions
- 2.3. Limitations
- 2.4. Abbreviations
- 2.5. Sources
- 2.6. Definitions
- 3. Research Methodology
- 3.1. Secondary Research
- 3.2. Primary Data Collection
- 3.3. Market Formation & Validation
- 3.4. Report Writing, Quality Check & Delivery
- 4. Japan Geography
- 4.1. Population Distribution Table
- 4.2. Japan Macro Economic Indicators
- 5. Market Dynamics
- 5.1. Key Insights
- 5.2. Recent Developments
- 5.3. Market Drivers & Opportunities
- 5.4. Market Restraints & Challenges
- 5.5. Market Trends
- 5.5.1. XXXX
- 5.5.2. XXXX
- 5.5.3. XXXX
- 5.5.4. XXXX
- 5.5.5. XXXX
- 5.6. Supply chain Analysis
- 5.7. Policy & Regulatory Framework
- 5.8. Industry Experts Views
- 6. Japan Air Quality Control System Market Overview
- 6.1. Market Size By Value
- 6.2. Market Size and Forecast, By Technology
- 6.3. Market Size and Forecast, By Application
- 6.4. Market Size and Forecast, By Product type
- 6.5. Market Size and Forecast, By Region
- 7. Japan Air Quality Control System Market Segmentations
- 7.1. Japan Air Quality Control System Market, By Technology
- 7.1.1. Japan Air Quality Control System Market Size, By Electrostatic Precipitators (ESP), 2019-2030
- 7.1.2. Japan Air Quality Control System Market Size, By Flue Gas Desulfurization (FGD), 2019-2030
- 7.1.3. Japan Air Quality Control System Market Size, By Scrubbers (Wet & Dry), 2019-2030
- 7.1.4. Japan Air Quality Control System Market Size, By Selective Catalytic Reduction (SCR), 2019-2030
- 7.1.5. Japan Air Quality Control System Market Size, By Fabric Filters (Baghouses), 2019-2030
- 7.1.6. Japan Air Quality Control System Market Size, By Catalytic Converters, 2019-2030
- 7.1.7. Japan Air Quality Control System Market Size, By Thermal Oxidizers, 2019-2030
- 7.1.8. Japan Air Quality Control System Market Size, By Others (Mercury Control Systems, Hybrid Systems), 2019-2030
- 7.2. Japan Air Quality Control System Market, By Application
- 7.2.1. Japan Air Quality Control System Market Size, By Power Generation, 2019-2030
- 7.2.2. Japan Air Quality Control System Market Size, By Cement Industry, 2019-2030
- 7.2.3. Japan Air Quality Control System Market Size, By Automotive, 2019-2030
- 7.2.4. Japan Air Quality Control System Market Size, By Chemical & Petrochemical, 2019-2030
- 7.2.5. Japan Air Quality Control System Market Size, By Metal Processing & Mining, 2019-2030
- 7.2.6. Japan Air Quality Control System Market Size, By Pharmaceuticals, 2019-2030
- 7.3. Japan Air Quality Control System Market, By Product type
- 7.3.1. Japan Air Quality Control System Market Size, By Indoor, 2019-2030
- 7.3.2. Japan Air Quality Control System Market Size, By Ambient, 2019-2030
- 7.4. Japan Air Quality Control System Market, By Region
- 7.4.1. Japan Air Quality Control System Market Size, By North, 2019-2030
- 7.4.2. Japan Air Quality Control System Market Size, By East, 2019-2030
- 7.4.3. Japan Air Quality Control System Market Size, By West, 2019-2030
- 7.4.4. Japan Air Quality Control System Market Size, By South, 2019-2030
- 8. Japan Air Quality Control System Market Opportunity Assessment
- 8.1. By Technology, 2025 to 2030
- 8.2. By Application, 2025 to 2030
- 8.3. By Product type, 2025 to 2030
- 8.4. By Region, 2025 to 2030
- 9. Competitive Landscape
- 9.1. Porter's Five Forces
- 9.2. Company Profile
- 9.2.1. Company 1
- 9.2.1.1. Company Snapshot
- 9.2.1.2. Company Overview
- 9.2.1.3. Financial Highlights
- 9.2.1.4. Geographic Insights
- 9.2.1.5. Business Segment & Performance
- 9.2.1.6. Product Portfolio
- 9.2.1.7. Key Executives
- 9.2.1.8. Strategic Moves & Developments
- 9.2.2. Company 2
- 9.2.3. Company 3
- 9.2.4. Company 4
- 9.2.5. Company 5
- 9.2.6. Company 6
- 9.2.7. Company 7
- 9.2.8. Company 8
- 10. Strategic Recommendations
- 11. Disclaimer
- List of Figures
- Figure 1: Japan Air Quality Control System Market Size By Value (2019, 2024 & 2030F) (in USD Million)
- Figure 2: Market Attractiveness Index, By Technology
- Figure 3: Market Attractiveness Index, By Application
- Figure 4: Market Attractiveness Index, By Product type
- Figure 5: Market Attractiveness Index, By Region
- Figure 6: Porter's Five Forces of Japan Air Quality Control System Market
- List of Tables
- Table 1: Influencing Factors for Air Quality Control System Market, 2024
- Table 2: Japan Air Quality Control System Market Size and Forecast, By Technology (2019 to 2030F) (In USD Million)
- Table 3: Japan Air Quality Control System Market Size and Forecast, By Application (2019 to 2030F) (In USD Million)
- Table 4: Japan Air Quality Control System Market Size and Forecast, By Product type (2019 to 2030F) (In USD Million)
- Table 5: Japan Air Quality Control System Market Size and Forecast, By Region (2019 to 2030F) (In USD Million)
- Table 6: Japan Air Quality Control System Market Size of Electrostatic Precipitators (ESP) (2019 to 2030) in USD Million
- Table 7: Japan Air Quality Control System Market Size of Flue Gas Desulfurization (FGD) (2019 to 2030) in USD Million
- Table 8: Japan Air Quality Control System Market Size of Scrubbers (Wet & Dry) (2019 to 2030) in USD Million
- Table 9: Japan Air Quality Control System Market Size of Selective Catalytic Reduction (SCR) (2019 to 2030) in USD Million
- Table 10: Japan Air Quality Control System Market Size of Fabric Filters (Baghouses) (2019 to 2030) in USD Million
- Table 11: Japan Air Quality Control System Market Size of Catalytic Converters (2019 to 2030) in USD Million
- Table 12: Japan Air Quality Control System Market Size of Thermal Oxidizers (2019 to 2030) in USD Million
- Table 13: Japan Air Quality Control System Market Size of Others (Mercury Control Systems, Hybrid Systems) (2019 to 2030) in USD Million
- Table 14: Japan Air Quality Control System Market Size of Power Generation (2019 to 2030) in USD Million
- Table 15: Japan Air Quality Control System Market Size of Cement Industry (2019 to 2030) in USD Million
- Table 16: Japan Air Quality Control System Market Size of Automotive (2019 to 2030) in USD Million
- Table 17: Japan Air Quality Control System Market Size of Chemical & Petrochemical (2019 to 2030) in USD Million
- Table 18: Japan Air Quality Control System Market Size of Metal Processing & Mining (2019 to 2030) in USD Million
- Table 19: Japan Air Quality Control System Market Size of Pharmaceuticals (2019 to 2030) in USD Million
- Table 20: Japan Air Quality Control System Market Size of Indoor (2019 to 2030) in USD Million
- Table 21: Japan Air Quality Control System Market Size of Ambient (2019 to 2030) in USD Million
- Table 22: Japan Air Quality Control System Market Size of North (2019 to 2030) in USD Million
- Table 23: Japan Air Quality Control System Market Size of East (2019 to 2030) in USD Million
- Table 24: Japan Air Quality Control System Market Size of West (2019 to 2030) in USD Million
- Table 25: Japan Air Quality Control System Market Size of South (2019 to 2030) in USD Million
Pricing
Currency Rates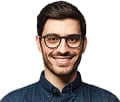
Questions or Comments?
Our team has the ability to search within reports to verify it suits your needs. We can also help maximize your budget by finding sections of reports you can purchase.