
India Industrial Evaporators Market Overview, 2030
Description
Industrial evaporators in India are essential thermal separation systems used across various sectors to remove water or other solvents from industrial fluids. These systems are designed to handle large-scale processing where concentration of liquids, recovery of solutes, or reduction of waste volume is critical. In the Indian context, industrial evaporators are widely used to concentrate dilute solutions, such as sugar juice in food processing or saline waste streams in textile and chemical industries. They also recover valuable byproducts like caustic soda or fertilizers and eliminate excess water, especially from effluents in compliance with strict pollution control regulations. Evaporators are critical to maintaining product quality, resource efficiency, and compliance with industrial standards in India. in pharmaceutical manufacturing, achieving precise concentrations of active ingredients is essential. Evaporation involves heating a liquid until its solvent most often water transforms into vapor, leaving behind a more concentrated solution. Indian manufacturers often adapt this principle by optimizing thermal input based on local energy sources like coal, biomass, or solar thermal systems to reduce dependence on expensive electricity or imported fuels. In India, where industrial processes often face varying energy availability and quality of inputs, evaporators are fine-tuned to work efficiently under controlled temperature and pressure conditions. Some setups operate under vacuum to lower the boiling point and reduce energy demand. Given the wide variation in feedstock and wastewater compositions, Indian evaporators are usually constructed using SS-316, duplex steel, or specialty alloys to handle corrosive environments like in acid recovery or tannery operations. The emphasis is on low maintenance and long operational life, particularly in rural or semi-urban industrial zones where repair infrastructure is limited. As industries in India face mounting energy and water costs, evaporators offer a practical solution by enabling zero liquid discharge (ZLD) systems.
According to the research report India Industrial Evaporator Market Overview, 2030, published by Bonafide Research, the India Industrial Evaporator market is anticipated to grow at more than 8.05% CAGR from 2025 to 2030. Indian evaporator systems are designed with flexible capacities, ranging from a few hundred liters per hour in small-scale food units to several hundred cubic meters per day in large chemical plants. Temperature and pressure ranges are often adapted to suit regional climatic conditions and input material, for instance, low-pressure operations are favored in heat-sensitive industries like dairy or herbal extraction. Indian conditions especially hard water and complex effluents make fouling resistance a critical design aspect, with manufacturers incorporating anti-scaling surfaces or coatings to ensure uninterrupted performance. Due to fluctuating input quality and inconsistent utilities in many Indian industrial zones, ease of maintenance is prioritized. Evaporators are often built with Clean-in-Place systems or easy-access ports to reduce downtime. Companies also prefer self-draining designs and automated flushing features, particularly in industries with batch processes like pharmaceuticals, where frequent cleaning is non-negotiable for GMP compliance. In sectors such as agrochemicals and fine chemicals, where solvent recovery is essential, Indian evaporators are tailored for precise control of evaporation rates to maximize recovery. Advanced models incorporate vapor condensation management, ensuring that solvents like ethanol or methanol are not just removed efficiently but also recovered and reused, significantly cutting down operational costs.
These systems are especially popular in heavy-duty applications like chemical manufacturing, petrochemicals, and distilleries, where thermal loads and volumes are high. Indian manufacturers favor this design for its high tolerance to fouling, which is crucial in handling complex effluents and high TDS (Total Dissolved Solids) feed streams typical in local operations. The long lifecycle and mechanical strength of shell & tube systems make them a preferred choice for plants operating in aggressive environments, such as coastal areas or industrial zones with corrosive airborne chemicals. Moreover, Indian engineers often retrofit these systems with multi-effect and vapor recompression features to tackle energy costs without sacrificing performance. Plate-type evaporators are gaining traction in India, particularly in space-constrained and hygiene-critical sectors like dairy, food processing, and pharmaceuticals. Their compact footprint and easy disassembly for cleaning align well with Indian SMEs and mid-sized enterprises looking to optimize both cost and space. These systems are ideal for low to moderate viscosity fluids, which is common in sectors such as fruit pulp concentration, milk pasteurization, and liquid APIs (Active Pharmaceutical Ingredients). Indian manufacturers are increasingly customizing plate configurations to handle localized input variations like seasonal sugarcane juice quality or region-specific herbal extracts. Although more sensitive to fouling than shell & tube systems, Indian suppliers mitigate this by integrating CIP (Clean-In-Place) systems and anti-scaling coatings to support uninterrupted operations and meet regulatory requirements.
Falling film evaporators are increasingly favored in India’s dairy, beverage, and pharma sectors due to their high thermal efficiency and gentle heat treatment, which is vital for heat-sensitive products like milk, fruit juice, or herbal extracts. Their suitability for continuous operations, especially in automated dairy plants of Gujarat and Maharashtra, has driven widespread adoption. Although less common than falling film systems, rising film evaporators still find use in legacy food processing units and sugar mills across India. They are particularly valued for handling low-viscosity fluids with good heat transfer properties. Their limited scalability and fouling sensitivity have led Indian manufacturers to transition toward more modern systems for newer plants, especially in high-capacity applications. These evaporators are heavily used in India’s chemical, textile, and zero liquid discharge (ZLD) applications, especially in Tamil Nadu and industrial belts of Gujarat. Their ability to handle highly viscous, scaling-prone, or crystallizing fluids makes them ideal for effluent treatment and brine concentration. Indian industries struggling with water pollution mandates increasingly opt for this design, supported by government incentives for effluent recycling and pollution control. In India, ATFEs are primarily applied in pharmaceutical, specialty chemical, and nutraceutical segments, especially in areas like Hyderabad and Baddi. Their design enables the evaporation of heat-sensitive, viscous, and high-solids content materials. Indian companies are leveraging this technology for solvent recovery and API concentration, where product degradation is a risk. MVR is gaining traction in India’s energy-conscious industries, especially among multinational food, dairy, and biotech manufacturers operating in regions with high power tariffs like Maharashtra and Karnataka.
In India, the food and beverage industry is a major driver of evaporator demand, particularly in dairy, fruit pulp, and juice processing segments. States like Gujarat, Punjab, and Maharashtra have high evaporator usage for milk concentration, tomato paste, mango pulp, and sugar syrup processing. Government schemes like PMFME (Pradhan Mantri Formalisation of Micro Food Processing Enterprises) have indirectly encouraged modernization of food processing infrastructure, where energy-efficient evaporators play a key role in product consistency and shelf-life enhancement. India’s status as the “pharmacy of the world” has propelled the need for evaporators in API concentration, solvent recovery, and crystallization processes. Pharma hubs such as Hyderabad, Baddi, and Ahmedabad demand precision evaporator systems like agitated thin film and falling film evaporators. These systems are essential for maintaining product purity and thermal stability. This segment represents one of the most versatile and demanding use cases for evaporators in India. Used for brine concentration, acid recovery, and solvent recycling, evaporators in this sector must withstand corrosive environments and high operational loads. Industrial clusters in Gujarat are significant adopters, often requiring forced circulation and multi-effect designs. Driven by tightening pollution norms from the Central Pollution Control Board (CPCB) and state agencies, this sector is witnessing rapid adoption of evaporators in ZLD systems, especially in textile, dye, and tannery industries in Tamil Nadu and Rajasthan. These units are used for reject water concentration post reverse osmosis (RO), ensuring minimal discharge.
Considered in this report
• Historic Year: 2019
• Base year: 2024
• Estimated year: 2025
• Forecast year: 2030
Aspects covered in this report
• Industrial Evaporators Market with its value and forecast along with its segments
• Various drivers and challenges
• On-going trends and developments
• Top profiled companies
• Strategic recommendation
By Construction Type
• Shell & Tube
• Plate
By Functionality Type
• Falling Film
• Rising Film
• Forced Circulation Evaporators
• Agitated Thin Film Evaporators
• Mechanical Vapor Recompression
• Others
By End-use Industry Type
• Food & Beverage
• Pharmaceutical
• Chemical & Petrochemical
• Water & Wastewater Treatment
• Others
The approach of the report:
This report consists of a combined approach of primary as well as secondary research. Initially, secondary research was used to get an understanding of the market and listing out the companies that are present in the market. The secondary research consists of third-party sources such as press releases, annual report of companies, analyzing the government generated reports and databases. After gathering the data from secondary sources primary research was conducted by making telephonic interviews with the leading players about how the market is functioning and then conducted trade calls with dealers and distributors of the market. Post this we have started doing primary calls to consumers by equally segmenting consumers in regional aspects, tier aspects, age group, and gender. Once we have primary data with us we have started verifying the details obtained from secondary sources.
Intended audience
This report can be useful to industry consultants, manufacturers, suppliers, associations & organizations related to agriculture industry, government bodies and other stakeholders to align their market-centric strategies. In addition to marketing & presentations, it will also increase competitive knowledge about the industry.
According to the research report India Industrial Evaporator Market Overview, 2030, published by Bonafide Research, the India Industrial Evaporator market is anticipated to grow at more than 8.05% CAGR from 2025 to 2030. Indian evaporator systems are designed with flexible capacities, ranging from a few hundred liters per hour in small-scale food units to several hundred cubic meters per day in large chemical plants. Temperature and pressure ranges are often adapted to suit regional climatic conditions and input material, for instance, low-pressure operations are favored in heat-sensitive industries like dairy or herbal extraction. Indian conditions especially hard water and complex effluents make fouling resistance a critical design aspect, with manufacturers incorporating anti-scaling surfaces or coatings to ensure uninterrupted performance. Due to fluctuating input quality and inconsistent utilities in many Indian industrial zones, ease of maintenance is prioritized. Evaporators are often built with Clean-in-Place systems or easy-access ports to reduce downtime. Companies also prefer self-draining designs and automated flushing features, particularly in industries with batch processes like pharmaceuticals, where frequent cleaning is non-negotiable for GMP compliance. In sectors such as agrochemicals and fine chemicals, where solvent recovery is essential, Indian evaporators are tailored for precise control of evaporation rates to maximize recovery. Advanced models incorporate vapor condensation management, ensuring that solvents like ethanol or methanol are not just removed efficiently but also recovered and reused, significantly cutting down operational costs.
These systems are especially popular in heavy-duty applications like chemical manufacturing, petrochemicals, and distilleries, where thermal loads and volumes are high. Indian manufacturers favor this design for its high tolerance to fouling, which is crucial in handling complex effluents and high TDS (Total Dissolved Solids) feed streams typical in local operations. The long lifecycle and mechanical strength of shell & tube systems make them a preferred choice for plants operating in aggressive environments, such as coastal areas or industrial zones with corrosive airborne chemicals. Moreover, Indian engineers often retrofit these systems with multi-effect and vapor recompression features to tackle energy costs without sacrificing performance. Plate-type evaporators are gaining traction in India, particularly in space-constrained and hygiene-critical sectors like dairy, food processing, and pharmaceuticals. Their compact footprint and easy disassembly for cleaning align well with Indian SMEs and mid-sized enterprises looking to optimize both cost and space. These systems are ideal for low to moderate viscosity fluids, which is common in sectors such as fruit pulp concentration, milk pasteurization, and liquid APIs (Active Pharmaceutical Ingredients). Indian manufacturers are increasingly customizing plate configurations to handle localized input variations like seasonal sugarcane juice quality or region-specific herbal extracts. Although more sensitive to fouling than shell & tube systems, Indian suppliers mitigate this by integrating CIP (Clean-In-Place) systems and anti-scaling coatings to support uninterrupted operations and meet regulatory requirements.
Falling film evaporators are increasingly favored in India’s dairy, beverage, and pharma sectors due to their high thermal efficiency and gentle heat treatment, which is vital for heat-sensitive products like milk, fruit juice, or herbal extracts. Their suitability for continuous operations, especially in automated dairy plants of Gujarat and Maharashtra, has driven widespread adoption. Although less common than falling film systems, rising film evaporators still find use in legacy food processing units and sugar mills across India. They are particularly valued for handling low-viscosity fluids with good heat transfer properties. Their limited scalability and fouling sensitivity have led Indian manufacturers to transition toward more modern systems for newer plants, especially in high-capacity applications. These evaporators are heavily used in India’s chemical, textile, and zero liquid discharge (ZLD) applications, especially in Tamil Nadu and industrial belts of Gujarat. Their ability to handle highly viscous, scaling-prone, or crystallizing fluids makes them ideal for effluent treatment and brine concentration. Indian industries struggling with water pollution mandates increasingly opt for this design, supported by government incentives for effluent recycling and pollution control. In India, ATFEs are primarily applied in pharmaceutical, specialty chemical, and nutraceutical segments, especially in areas like Hyderabad and Baddi. Their design enables the evaporation of heat-sensitive, viscous, and high-solids content materials. Indian companies are leveraging this technology for solvent recovery and API concentration, where product degradation is a risk. MVR is gaining traction in India’s energy-conscious industries, especially among multinational food, dairy, and biotech manufacturers operating in regions with high power tariffs like Maharashtra and Karnataka.
In India, the food and beverage industry is a major driver of evaporator demand, particularly in dairy, fruit pulp, and juice processing segments. States like Gujarat, Punjab, and Maharashtra have high evaporator usage for milk concentration, tomato paste, mango pulp, and sugar syrup processing. Government schemes like PMFME (Pradhan Mantri Formalisation of Micro Food Processing Enterprises) have indirectly encouraged modernization of food processing infrastructure, where energy-efficient evaporators play a key role in product consistency and shelf-life enhancement. India’s status as the “pharmacy of the world” has propelled the need for evaporators in API concentration, solvent recovery, and crystallization processes. Pharma hubs such as Hyderabad, Baddi, and Ahmedabad demand precision evaporator systems like agitated thin film and falling film evaporators. These systems are essential for maintaining product purity and thermal stability. This segment represents one of the most versatile and demanding use cases for evaporators in India. Used for brine concentration, acid recovery, and solvent recycling, evaporators in this sector must withstand corrosive environments and high operational loads. Industrial clusters in Gujarat are significant adopters, often requiring forced circulation and multi-effect designs. Driven by tightening pollution norms from the Central Pollution Control Board (CPCB) and state agencies, this sector is witnessing rapid adoption of evaporators in ZLD systems, especially in textile, dye, and tannery industries in Tamil Nadu and Rajasthan. These units are used for reject water concentration post reverse osmosis (RO), ensuring minimal discharge.
Considered in this report
• Historic Year: 2019
• Base year: 2024
• Estimated year: 2025
• Forecast year: 2030
Aspects covered in this report
• Industrial Evaporators Market with its value and forecast along with its segments
• Various drivers and challenges
• On-going trends and developments
• Top profiled companies
• Strategic recommendation
By Construction Type
• Shell & Tube
• Plate
By Functionality Type
• Falling Film
• Rising Film
• Forced Circulation Evaporators
• Agitated Thin Film Evaporators
• Mechanical Vapor Recompression
• Others
By End-use Industry Type
• Food & Beverage
• Pharmaceutical
• Chemical & Petrochemical
• Water & Wastewater Treatment
• Others
The approach of the report:
This report consists of a combined approach of primary as well as secondary research. Initially, secondary research was used to get an understanding of the market and listing out the companies that are present in the market. The secondary research consists of third-party sources such as press releases, annual report of companies, analyzing the government generated reports and databases. After gathering the data from secondary sources primary research was conducted by making telephonic interviews with the leading players about how the market is functioning and then conducted trade calls with dealers and distributors of the market. Post this we have started doing primary calls to consumers by equally segmenting consumers in regional aspects, tier aspects, age group, and gender. Once we have primary data with us we have started verifying the details obtained from secondary sources.
Intended audience
This report can be useful to industry consultants, manufacturers, suppliers, associations & organizations related to agriculture industry, government bodies and other stakeholders to align their market-centric strategies. In addition to marketing & presentations, it will also increase competitive knowledge about the industry.
Table of Contents
77 Pages
- 1. Executive Summary
- 2. Market Structure
- 2.1. Market Considerate
- 2.2. Assumptions
- 2.3. Limitations
- 2.4. Abbreviations
- 2.5. Sources
- 2.6. Definitions
- 3. Research Methodology
- 3.1. Secondary Research
- 3.2. Primary Data Collection
- 3.3. Market Formation & Validation
- 3.4. Report Writing, Quality Check & Delivery
- 4. India Geography
- 4.1. Population Distribution Table
- 4.2. India Macro Economic Indicators
- 5. Market Dynamics
- 5.1. Key Insights
- 5.2. Recent Developments
- 5.3. Market Drivers & Opportunities
- 5.4. Market Restraints & Challenges
- 5.5. Market Trends
- 5.5.1. XXXX
- 5.5.2. XXXX
- 5.5.3. XXXX
- 5.5.4. XXXX
- 5.5.5. XXXX
- 5.6. Supply chain Analysis
- 5.7. Policy & Regulatory Framework
- 5.8. Industry Experts Views
- 6. India Industrial Evaporators Market Overview
- 6.1. Market Size By Value
- 6.2. Market Size and Forecast, By Construction Type
- 6.3. Market Size and Forecast, By Functionality Type
- 6.4. Market Size and Forecast, By End-use Industry Type
- 6.5. Market Size and Forecast, By Region
- 7. India Industrial Evaporators Market Segmentations
- 7.1. India Industrial Evaporators Market, By Construction Type
- 7.1.1. India Industrial Evaporators Market Size, By Shell & Tube, 2019-2030
- 7.1.2. India Industrial Evaporators Market Size, By Plate, 2019-2030
- 7.2. India Industrial Evaporators Market, By Functionality Type
- 7.2.1. India Industrial Evaporators Market Size, By Falling Film, 2019-2030
- 7.2.2. India Industrial Evaporators Market Size, By Rising Film, 2019-2030
- 7.2.3. India Industrial Evaporators Market Size, By Forced Circulation Evaporators, 2019-2030
- 7.2.4. India Industrial Evaporators Market Size, By Agitated Thin Film Evaporators, 2019-2030
- 7.2.5. India Industrial Evaporators Market Size, By Mechanical Vapor Recompression, 2019-2030
- 7.2.6. India Industrial Evaporators Market Size, By Others, 2019-2030
- 7.3. India Industrial Evaporators Market, By End-use Industry Type
- 7.3.1. India Industrial Evaporators Market Size, By Food & Beverage, 2019-2030
- 7.3.2. India Industrial Evaporators Market Size, By Pharmaceutical, 2019-2030
- 7.3.3. India Industrial Evaporators Market Size, By Chemical & Petrochemical, 2019-2030
- 7.3.4. India Industrial Evaporators Market Size, By Water & Wastewater Treatment , 2019-2030
- 7.3.5. India Industrial Evaporators Market Size, By Others, 2019-2030
- 7.4. India Industrial Evaporators Market, By Region
- 7.4.1. India Industrial Evaporators Market Size, By North, 2019-2030
- 7.4.2. India Industrial Evaporators Market Size, By East, 2019-2030
- 7.4.3. India Industrial Evaporators Market Size, By West, 2019-2030
- 7.4.4. India Industrial Evaporators Market Size, By South, 2019-2030
- 8. India Industrial Evaporators Market Opportunity Assessment
- 8.1. By Construction Type, 2025 to 2030
- 8.2. By Functionality Type, 2025 to 2030
- 8.3. By End-use Industry Type, 2025 to 2030
- 8.4. By Region, 2025 to 2030
- 9. Competitive Landscape
- 9.1. Porter's Five Forces
- 9.2. Company Profile
- 9.2.1. Company 1
- 9.2.1.1. Company Snapshot
- 9.2.1.2. Company Overview
- 9.2.1.3. Financial Highlights
- 9.2.1.4. Geographic Insights
- 9.2.1.5. Business Segment & Performance
- 9.2.1.6. Product Portfolio
- 9.2.1.7. Key Executives
- 9.2.1.8. Strategic Moves & Developments
- 9.2.2. Company 2
- 9.2.3. Company 3
- 9.2.4. Company 4
- 9.2.5. Company 5
- 9.2.6. Company 6
- 9.2.7. Company 7
- 9.2.8. Company 8
- 10. Strategic Recommendations
- 11. Disclaimer
- List of Figures
- Figure 1: India Industrial Evaporators Market Size By Value (2019, 2024 & 2030F) (in USD Million)
- Figure 2: Market Attractiveness Index, By Construction Type
- Figure 3: Market Attractiveness Index, By Functionality Type
- Figure 4: Market Attractiveness Index, By End-use Industry Type
- Figure 5: Market Attractiveness Index, By Region
- Figure 6: Porter's Five Forces of India Industrial Evaporators Market
- List of Tables
- Table 1: Influencing Factors for Industrial Evaporators Market, 2024
- Table 2: India Industrial Evaporators Market Size and Forecast, By Construction Type (2019 to 2030F) (In USD Million)
- Table 3: India Industrial Evaporators Market Size and Forecast, By Functionality Type (2019 to 2030F) (In USD Million)
- Table 4: India Industrial Evaporators Market Size and Forecast, By End-use Industry Type (2019 to 2030F) (In USD Million)
- Table 5: India Industrial Evaporators Market Size and Forecast, By Region (2019 to 2030F) (In USD Million)
- Table 6: India Industrial Evaporators Market Size of Shell & Tube (2019 to 2030) in USD Million
- Table 7: India Industrial Evaporators Market Size of Plate (2019 to 2030) in USD Million
- Table 8: India Industrial Evaporators Market Size of Falling Film (2019 to 2030) in USD Million
- Table 9: India Industrial Evaporators Market Size of Rising Film (2019 to 2030) in USD Million
- Table 10: India Industrial Evaporators Market Size of Forced Circulation Evaporators (2019 to 2030) in USD Million
- Table 11: India Industrial Evaporators Market Size of Agitated Thin Film Evaporators (2019 to 2030) in USD Million
- Table 12: India Industrial Evaporators Market Size of Mechanical Vapor Recompression (2019 to 2030) in USD Million
- Table 13: India Industrial Evaporators Market Size of Others (2019 to 2030) in USD Million
- Table 14: India Industrial Evaporators Market Size of Food & Beverage (2019 to 2030) in USD Million
- Table 15: India Industrial Evaporators Market Size of Pharmaceutical (2019 to 2030) in USD Million
- Table 16: India Industrial Evaporators Market Size of Chemical & Petrochemical (2019 to 2030) in USD Million
- Table 17: India Industrial Evaporators Market Size of Water & Wastewater Treatment (2019 to 2030) in USD Million
- Table 18: India Industrial Evaporators Market Size of Others (2019 to 2030) in USD Million
- Table 19: India Industrial Evaporators Market Size of North (2019 to 2030) in USD Million
- Table 20: India Industrial Evaporators Market Size of East (2019 to 2030) in USD Million
- Table 21: India Industrial Evaporators Market Size of West (2019 to 2030) in USD Million
- Table 22: India Industrial Evaporators Market Size of South (2019 to 2030) in USD Million
Pricing
Currency Rates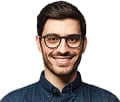
Questions or Comments?
Our team has the ability to search within reports to verify it suits your needs. We can also help maximize your budget by finding sections of reports you can purchase.