
Germany Industrial Evaporators Market Overview, 2030
Description
The industrial evaporators market in Germany is set to experience a significant transformation by 2030, driven by a confluence of advanced process engineering, evolving environmental standards, and increasing demands across high-growth sectors. Germany, as the backbone of Europe’s manufacturing and processing industries, represents a fertile ground for the expansion and diversification of industrial evaporator applications. This equipment, designed to remove excess water or other solvents through thermal methods, plays a critical role in enabling operational efficiency, reducing waste, and concentrating valuable substances in various industrial workflows. The German market is increasingly defined by its transition towards sustainable and energy-efficient solutions, with evaporator systems becoming central to industries looking to reduce operational costs while complying with stringent environmental directives such as the EU’s Industrial Emissions Directive and national decarbonization commitments. This market landscape is shaped by strong investments in clean technology and energy optimization, particularly in sectors such as food and beverage, pharmaceuticals, chemicals, and wastewater treatment. Government incentives and R&D initiatives have further fueled interest in next-generation evaporators that offer enhanced automation, reduced energy consumption, and longer operational life. The increasing need to recover valuable resources from effluents and byproducts is creating additional traction for high-efficiency evaporator models. German companies, known for their engineering precision and process integration expertise, are also leading innovation in modular and compact systems tailored for smaller-scale or decentralized industrial setups, reflecting broader trends in industrial agility and digital transformation. The rising influence of Industry 4.0 is also pushing demand for systems embedded with real-time monitoring and smart diagnostics, enabling proactive maintenance and continuous process optimization.
According to the research report Germany Industrial Evaporators Market Overview,2030 published by Bonafide Research, the Germany Industrial Evaporators Market is anticipated to grow at more than 2.97% CAGR from 2025 to 2030. One of the defining features of Germany’s industrial evaporators market is its commitment to integrating cutting-edge engineering solutions into legacy production systems across sectors. This is largely driven by Germany’s mature and diversified industrial base, where companies continuously seek to modernize processes without compromising productivity or environmental performance. Evaporator systems are being adopted not only for their role in water and solvent removal but also for their ability to recover valuable materials, including heat, solvents, and high-purity process outputs. These systems are increasingly engineered to function efficiently within closed-loop production systems, aligning with circular economy principles that Germany strongly advocates for. Furthermore, Germany’s reputation as a global export powerhouse influences the domestic market dynamics, as manufacturers in the country often develop technologies suited for both domestic use and international deployment. The interplay of high regulatory standards and export-driven innovation ensures that industrial evaporators designed in Germany are often at the forefront of technological capability. The growing need to reduce greenhouse gas emissions and improve waste management efficiency is also pushing operators across various sectors to replace outdated evaporation technologies with systems capable of achieving higher concentration ratios using less energy. These demands are further amplified by the need for operational flexibility, as many German manufacturers cater to diversified production runs and require evaporator systems that can seamlessly adapt to different materials, batch sizes, and process parameters. In this context, the market is seeing heightened investment in custom-engineered systems with a strong emphasis on ease of maintenance, heat recovery, and automation capabilities.
Shell and tube evaporators remain the more traditional and widely used format, particularly in large-scale industrial settings due to their robust design, high capacity handling, and ease of cleaning, which is vital in sectors like chemical processing and wastewater treatment. These systems are especially favored in continuous operations where thermal efficiency and durability are paramount. On the other hand, plate evaporators, with their compact design and higher heat transfer efficiency, are gaining ground in industries where space optimization and lower operational loads are key considerations. Their modular design enables more flexible configurations, which is increasingly important in food and beverage as well as pharmaceutical manufacturing environments that often operate under stringent hygiene regulations and require frequent equipment sanitization. Furthermore, technological advancements in plate material and sealing techniques are addressing long-standing concerns related to pressure tolerance and corrosion resistance, expanding their applicability in more demanding process environments. Manufacturers in Germany are investing in dual-format or hybrid constructions that merge the advantages of both shell and tube and plate designs, catering to niche process requirements such as those involving volatile organic compounds or high-viscosity substances. The growing prevalence of multi-effect evaporator systems, often employing a mix of construction types within a single setup, further illustrates the trend toward integrated, performance-optimized solutions.
Falling film evaporators dominate in sectors where delicate heat-sensitive products must be concentrated without thermal degradation, such as dairy processing and pharmaceutical manufacturing. Their high energy efficiency and short residence time make them suitable for continuous processes requiring precise control over product quality. In contrast, rising film evaporators, although less commonly deployed, are leveraged where fluid characteristics favor upward film motion due to natural convection or vapor lift effects. Forced circulation evaporators have found a solid foothold in chemical and petrochemical industries, where the presence of fouling fluids and high viscosities demand rigorous mixing and circulation. These systems are designed to withstand aggressive solvents and corrosive compounds, making them ideal for high-solids concentration and crystal-forming applications. Agitated thin film evaporators, characterized by their mechanical wiping action and minimal thermal stress, are indispensable for processing slurries, suspensions, or shear-sensitive fluids frequently seen in cosmetic, nutraceutical, and specialty chemical operations. Mechanical vapor recompression systems, which recycle energy from vapor to reduce steam usage, are becoming increasingly vital in sectors under pressure to minimize carbon footprints and energy costs. This energy recovery model is particularly attractive in water-scarce or energy-intensive applications such as industrial effluent treatment and large-scale food manufacturing.
The food and beverage industry remains one of the leading adopters, especially in applications involving juice concentration, milk processing, and brewing, where product quality, hygiene, and thermal efficiency are of paramount concern. The pharmaceutical sector follows closely, driven by the need for ultra-pure process environments, compliance with GMP standards, and the growing production of biological drugs that require gentle but effective moisture removal systems. Chemical and petrochemical companies employ evaporators to handle a broad spectrum of solvents, acids, and byproducts, where system resilience, corrosion resistance, and energy efficiency are non-negotiable features. Water and wastewater treatment facilities, both municipal and industrial, represent a growing end-use category, particularly in the context of Germany’s increased focus on water conservation, pollutant recovery, and zero liquid discharge initiatives. Here, evaporators are integrated into advanced effluent management systems to reduce waste volume and recover reusable components. Other emerging application domains include sectors such as renewable energy, where evaporators play a role in processing biofuels and managing condensates in power generation. The automotive and electronics sectors are also beginning to utilize advanced evaporator systems for chemical recovery and waste minimization during component manufacturing. This broadening of the end-user base is reflective of Germany’s overarching industrial shift toward sustainability, automation, and lean production.
Considered in this report
• Historic Year: 2019
• Base year: 2024
• Estimated year: 2025
• Forecast year: 2030
Aspects covered in this report
• Industrial Evaporators Market with its value and forecast along with its segments
• Various drivers and challenges
• On-going trends and developments
• Top profiled companies
• Strategic recommendation
By Construction Type
• Shell & Tube
• Plate
By Functionality Type
• Falling Film
• Rising Film
• Forced Circulation Evaporators
• Agitated Thin Film Evaporators
• Mechanical Vapor Recompression
• Others
By End-use Industry Type
• Food & Beverage
• Pharmaceutical
• Chemical & Petrochemical
• Water & Wastewater Treatment
• Others
The approach of the report:
This report consists of a combined approach of primary as well as secondary research. Initially, secondary research was used to get an understanding of the market and listing out the companies that are present in the market. The secondary research consists of third-party sources such as press releases, annual report of companies, analyzing the government generated reports and databases. After gathering the data from secondary sources primary research was conducted by making telephonic interviews with the leading players about how the market is functioning and then conducted trade calls with dealers and distributors of the market. Post this we have started doing primary calls to consumers by equally segmenting consumers in regional aspects, tier aspects, age group, and gender. Once we have primary data with us we have started verifying the details obtained from secondary sources.
Intended audience
This report can be useful to industry consultants, manufacturers, suppliers, associations & organizations related to agriculture industry, government bodies and other stakeholders to align their market-centric strategies. In addition to marketing & presentations, it will also increase competitive knowledge about the industry.
According to the research report Germany Industrial Evaporators Market Overview,2030 published by Bonafide Research, the Germany Industrial Evaporators Market is anticipated to grow at more than 2.97% CAGR from 2025 to 2030. One of the defining features of Germany’s industrial evaporators market is its commitment to integrating cutting-edge engineering solutions into legacy production systems across sectors. This is largely driven by Germany’s mature and diversified industrial base, where companies continuously seek to modernize processes without compromising productivity or environmental performance. Evaporator systems are being adopted not only for their role in water and solvent removal but also for their ability to recover valuable materials, including heat, solvents, and high-purity process outputs. These systems are increasingly engineered to function efficiently within closed-loop production systems, aligning with circular economy principles that Germany strongly advocates for. Furthermore, Germany’s reputation as a global export powerhouse influences the domestic market dynamics, as manufacturers in the country often develop technologies suited for both domestic use and international deployment. The interplay of high regulatory standards and export-driven innovation ensures that industrial evaporators designed in Germany are often at the forefront of technological capability. The growing need to reduce greenhouse gas emissions and improve waste management efficiency is also pushing operators across various sectors to replace outdated evaporation technologies with systems capable of achieving higher concentration ratios using less energy. These demands are further amplified by the need for operational flexibility, as many German manufacturers cater to diversified production runs and require evaporator systems that can seamlessly adapt to different materials, batch sizes, and process parameters. In this context, the market is seeing heightened investment in custom-engineered systems with a strong emphasis on ease of maintenance, heat recovery, and automation capabilities.
Shell and tube evaporators remain the more traditional and widely used format, particularly in large-scale industrial settings due to their robust design, high capacity handling, and ease of cleaning, which is vital in sectors like chemical processing and wastewater treatment. These systems are especially favored in continuous operations where thermal efficiency and durability are paramount. On the other hand, plate evaporators, with their compact design and higher heat transfer efficiency, are gaining ground in industries where space optimization and lower operational loads are key considerations. Their modular design enables more flexible configurations, which is increasingly important in food and beverage as well as pharmaceutical manufacturing environments that often operate under stringent hygiene regulations and require frequent equipment sanitization. Furthermore, technological advancements in plate material and sealing techniques are addressing long-standing concerns related to pressure tolerance and corrosion resistance, expanding their applicability in more demanding process environments. Manufacturers in Germany are investing in dual-format or hybrid constructions that merge the advantages of both shell and tube and plate designs, catering to niche process requirements such as those involving volatile organic compounds or high-viscosity substances. The growing prevalence of multi-effect evaporator systems, often employing a mix of construction types within a single setup, further illustrates the trend toward integrated, performance-optimized solutions.
Falling film evaporators dominate in sectors where delicate heat-sensitive products must be concentrated without thermal degradation, such as dairy processing and pharmaceutical manufacturing. Their high energy efficiency and short residence time make them suitable for continuous processes requiring precise control over product quality. In contrast, rising film evaporators, although less commonly deployed, are leveraged where fluid characteristics favor upward film motion due to natural convection or vapor lift effects. Forced circulation evaporators have found a solid foothold in chemical and petrochemical industries, where the presence of fouling fluids and high viscosities demand rigorous mixing and circulation. These systems are designed to withstand aggressive solvents and corrosive compounds, making them ideal for high-solids concentration and crystal-forming applications. Agitated thin film evaporators, characterized by their mechanical wiping action and minimal thermal stress, are indispensable for processing slurries, suspensions, or shear-sensitive fluids frequently seen in cosmetic, nutraceutical, and specialty chemical operations. Mechanical vapor recompression systems, which recycle energy from vapor to reduce steam usage, are becoming increasingly vital in sectors under pressure to minimize carbon footprints and energy costs. This energy recovery model is particularly attractive in water-scarce or energy-intensive applications such as industrial effluent treatment and large-scale food manufacturing.
The food and beverage industry remains one of the leading adopters, especially in applications involving juice concentration, milk processing, and brewing, where product quality, hygiene, and thermal efficiency are of paramount concern. The pharmaceutical sector follows closely, driven by the need for ultra-pure process environments, compliance with GMP standards, and the growing production of biological drugs that require gentle but effective moisture removal systems. Chemical and petrochemical companies employ evaporators to handle a broad spectrum of solvents, acids, and byproducts, where system resilience, corrosion resistance, and energy efficiency are non-negotiable features. Water and wastewater treatment facilities, both municipal and industrial, represent a growing end-use category, particularly in the context of Germany’s increased focus on water conservation, pollutant recovery, and zero liquid discharge initiatives. Here, evaporators are integrated into advanced effluent management systems to reduce waste volume and recover reusable components. Other emerging application domains include sectors such as renewable energy, where evaporators play a role in processing biofuels and managing condensates in power generation. The automotive and electronics sectors are also beginning to utilize advanced evaporator systems for chemical recovery and waste minimization during component manufacturing. This broadening of the end-user base is reflective of Germany’s overarching industrial shift toward sustainability, automation, and lean production.
Considered in this report
• Historic Year: 2019
• Base year: 2024
• Estimated year: 2025
• Forecast year: 2030
Aspects covered in this report
• Industrial Evaporators Market with its value and forecast along with its segments
• Various drivers and challenges
• On-going trends and developments
• Top profiled companies
• Strategic recommendation
By Construction Type
• Shell & Tube
• Plate
By Functionality Type
• Falling Film
• Rising Film
• Forced Circulation Evaporators
• Agitated Thin Film Evaporators
• Mechanical Vapor Recompression
• Others
By End-use Industry Type
• Food & Beverage
• Pharmaceutical
• Chemical & Petrochemical
• Water & Wastewater Treatment
• Others
The approach of the report:
This report consists of a combined approach of primary as well as secondary research. Initially, secondary research was used to get an understanding of the market and listing out the companies that are present in the market. The secondary research consists of third-party sources such as press releases, annual report of companies, analyzing the government generated reports and databases. After gathering the data from secondary sources primary research was conducted by making telephonic interviews with the leading players about how the market is functioning and then conducted trade calls with dealers and distributors of the market. Post this we have started doing primary calls to consumers by equally segmenting consumers in regional aspects, tier aspects, age group, and gender. Once we have primary data with us we have started verifying the details obtained from secondary sources.
Intended audience
This report can be useful to industry consultants, manufacturers, suppliers, associations & organizations related to agriculture industry, government bodies and other stakeholders to align their market-centric strategies. In addition to marketing & presentations, it will also increase competitive knowledge about the industry.
Table of Contents
77 Pages
- 1. Executive Summary
- 2. Market Structure
- 2.1. Market Considerate
- 2.2. Assumptions
- 2.3. Limitations
- 2.4. Abbreviations
- 2.5. Sources
- 2.6. Definitions
- 3. Research Methodology
- 3.1. Secondary Research
- 3.2. Primary Data Collection
- 3.3. Market Formation & Validation
- 3.4. Report Writing, Quality Check & Delivery
- 4. Germany Geography
- 4.1. Population Distribution Table
- 4.2. Germany Macro Economic Indicators
- 5. Market Dynamics
- 5.1. Key Insights
- 5.2. Recent Developments
- 5.3. Market Drivers & Opportunities
- 5.4. Market Restraints & Challenges
- 5.5. Market Trends
- 5.5.1. XXXX
- 5.5.2. XXXX
- 5.5.3. XXXX
- 5.5.4. XXXX
- 5.5.5. XXXX
- 5.6. Supply chain Analysis
- 5.7. Policy & Regulatory Framework
- 5.8. Industry Experts Views
- 6. Germany Industrial Evaporators Market Overview
- 6.1. Market Size By Value
- 6.2. Market Size and Forecast, By Construction Type
- 6.3. Market Size and Forecast, By Functionality Type
- 6.4. Market Size and Forecast, By End-use Industry Type
- 6.5. Market Size and Forecast, By Region
- 7. Germany Industrial Evaporators Market Segmentations
- 7.1. Germany Industrial Evaporators Market, By Construction Type
- 7.1.1. Germany Industrial Evaporators Market Size, By Shell & Tube, 2019-2030
- 7.1.2. Germany Industrial Evaporators Market Size, By Plate, 2019-2030
- 7.2. Germany Industrial Evaporators Market, By Functionality Type
- 7.2.1. Germany Industrial Evaporators Market Size, By Falling Film, 2019-2030
- 7.2.2. Germany Industrial Evaporators Market Size, By Rising Film, 2019-2030
- 7.2.3. Germany Industrial Evaporators Market Size, By Forced Circulation Evaporators, 2019-2030
- 7.2.4. Germany Industrial Evaporators Market Size, By Agitated Thin Film Evaporators, 2019-2030
- 7.2.5. Germany Industrial Evaporators Market Size, By Mechanical Vapor Recompression, 2019-2030
- 7.2.6. Germany Industrial Evaporators Market Size, By Others, 2019-2030
- 7.3. Germany Industrial Evaporators Market, By End-use Industry Type
- 7.3.1. Germany Industrial Evaporators Market Size, By Food & Beverage, 2019-2030
- 7.3.2. Germany Industrial Evaporators Market Size, By Pharmaceutical, 2019-2030
- 7.3.3. Germany Industrial Evaporators Market Size, By Chemical & Petrochemical, 2019-2030
- 7.3.4. Germany Industrial Evaporators Market Size, By Water & Wastewater Treatment , 2019-2030
- 7.3.5. Germany Industrial Evaporators Market Size, By Others, 2019-2030
- 7.4. Germany Industrial Evaporators Market, By Region
- 7.4.1. Germany Industrial Evaporators Market Size, By North, 2019-2030
- 7.4.2. Germany Industrial Evaporators Market Size, By East, 2019-2030
- 7.4.3. Germany Industrial Evaporators Market Size, By West, 2019-2030
- 7.4.4. Germany Industrial Evaporators Market Size, By South, 2019-2030
- 8. Germany Industrial Evaporators Market Opportunity Assessment
- 8.1. By Construction Type, 2025 to 2030
- 8.2. By Functionality Type, 2025 to 2030
- 8.3. By End-use Industry Type, 2025 to 2030
- 8.4. By Region, 2025 to 2030
- 9. Competitive Landscape
- 9.1. Porter's Five Forces
- 9.2. Company Profile
- 9.2.1. Company 1
- 9.2.1.1. Company Snapshot
- 9.2.1.2. Company Overview
- 9.2.1.3. Financial Highlights
- 9.2.1.4. Geographic Insights
- 9.2.1.5. Business Segment & Performance
- 9.2.1.6. Product Portfolio
- 9.2.1.7. Key Executives
- 9.2.1.8. Strategic Moves & Developments
- 9.2.2. Company 2
- 9.2.3. Company 3
- 9.2.4. Company 4
- 9.2.5. Company 5
- 9.2.6. Company 6
- 9.2.7. Company 7
- 9.2.8. Company 8
- 10. Strategic Recommendations
- 11. Disclaimer
- List of Figures
- Figure 1: Germany Industrial Evaporators Market Size By Value (2019, 2024 & 2030F) (in USD Million)
- Figure 2: Market Attractiveness Index, By Construction Type
- Figure 3: Market Attractiveness Index, By Functionality Type
- Figure 4: Market Attractiveness Index, By End-use Industry Type
- Figure 5: Market Attractiveness Index, By Region
- Figure 6: Porter's Five Forces of Germany Industrial Evaporators Market
- List of Tables
- Table 1: Influencing Factors for Industrial Evaporators Market, 2024
- Table 2: Germany Industrial Evaporators Market Size and Forecast, By Construction Type (2019 to 2030F) (In USD Million)
- Table 3: Germany Industrial Evaporators Market Size and Forecast, By Functionality Type (2019 to 2030F) (In USD Million)
- Table 4: Germany Industrial Evaporators Market Size and Forecast, By End-use Industry Type (2019 to 2030F) (In USD Million)
- Table 5: Germany Industrial Evaporators Market Size and Forecast, By Region (2019 to 2030F) (In USD Million)
- Table 6: Germany Industrial Evaporators Market Size of Shell & Tube (2019 to 2030) in USD Million
- Table 7: Germany Industrial Evaporators Market Size of Plate (2019 to 2030) in USD Million
- Table 8: Germany Industrial Evaporators Market Size of Falling Film (2019 to 2030) in USD Million
- Table 9: Germany Industrial Evaporators Market Size of Rising Film (2019 to 2030) in USD Million
- Table 10: Germany Industrial Evaporators Market Size of Forced Circulation Evaporators (2019 to 2030) in USD Million
- Table 11: Germany Industrial Evaporators Market Size of Agitated Thin Film Evaporators (2019 to 2030) in USD Million
- Table 12: Germany Industrial Evaporators Market Size of Mechanical Vapor Recompression (2019 to 2030) in USD Million
- Table 13: Germany Industrial Evaporators Market Size of Others (2019 to 2030) in USD Million
- Table 14: Germany Industrial Evaporators Market Size of Food & Beverage (2019 to 2030) in USD Million
- Table 15: Germany Industrial Evaporators Market Size of Pharmaceutical (2019 to 2030) in USD Million
- Table 16: Germany Industrial Evaporators Market Size of Chemical & Petrochemical (2019 to 2030) in USD Million
- Table 17: Germany Industrial Evaporators Market Size of Water & Wastewater Treatment (2019 to 2030) in USD Million
- Table 18: Germany Industrial Evaporators Market Size of Others (2019 to 2030) in USD Million
- Table 19: Germany Industrial Evaporators Market Size of North (2019 to 2030) in USD Million
- Table 20: Germany Industrial Evaporators Market Size of East (2019 to 2030) in USD Million
- Table 21: Germany Industrial Evaporators Market Size of West (2019 to 2030) in USD Million
- Table 22: Germany Industrial Evaporators Market Size of South (2019 to 2030) in USD Million
Pricing
Currency Rates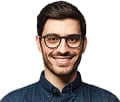
Questions or Comments?
Our team has the ability to search within reports to verify it suits your needs. We can also help maximize your budget by finding sections of reports you can purchase.