
Germany Automotive Carbon Fiber Market Overview, 2030
Description
Germany’s carbon fiber market has established itself as a cornerstone of the nation’s high-performance engineering landscape, particularly within the automotive sector. As global focus shifts towards sustainability, lightweight construction, and energy efficiency, carbon fiber has emerged as a strategic material due to its exceptional strength-to-weight ratio, corrosion resistance, and durability. In Germany, where precision engineering and innovation are deeply embedded in the industrial culture, carbon fiber is not only being adopted but also being refined and repurposed to suit evolving automotive demands. Automakers are increasingly leveraging this material to reduce overall vehicle weight, thereby achieving better fuel economy and compliance with tightening emissions regulations. Additionally, the growing interest in electric vehicles has further fueled demand, as reducing battery load and extending range are directly supported by lighter vehicle structures. German automotive giants are pioneering composite material integration, supported by a strong network of material scientists, researchers, and manufacturing specialists who are continually improving production efficiency and material properties. This collaboration fosters a competitive and technologically advanced ecosystem, reinforcing Germany’s status as a global leader in automotive innovation and material science.
According to the research report Germany Automotive Carbon Fiber Market Overview, 2030, published by Bonafide Research, the Germany Automotive Carbon Fiber Market is expected to reach a market size of more than USD 5.36 Billion by 2030. The evolution of Germany’s carbon fiber market is being significantly shaped by the rise of electric mobility, advancements in manufacturing technology, and increased governmental emphasis on sustainable industrial development. In the last decade, German manufacturers have invested heavily in localizing production, scaling up operations, and enhancing supply chain capabilities to meet growing demand from the automotive and aerospace sectors. These developments are also driven by European climate mandates and Germany’s national targets for carbon neutrality, encouraging the use of advanced materials in transportation infrastructure. Companies are increasingly adopting automation in carbon fiber production through techniques such as resin transfer molding and automated fiber placement, which significantly reduce labor costs and production time. Moreover, a shift towards circular economy principles is prompting research into carbon fiber recycling and second-life applications, ensuring long-term resource efficiency and sustainability. Germany’s emphasis on quality and precision has further accelerated the development of advanced testing facilities and pilot projects, allowing new applications to be prototyped and commercialized more rapidly. The presence of globally recognized research institutions and technical universities also plays a vital role in fostering innovation and creating a skilled workforce to support the carbon fiber industry. With this strong foundation and forward-looking approach, Germany is poised to drive the next phase of global carbon fiber adoption.
In the context of materials, polyacrylonitrile (PAN) continues to be the most prevalent raw material used for carbon fiber production in Germany’s automotive landscape. PAN-based carbon fiber is renowned for its excellent balance of tensile strength, flexibility, and lightweight properties, making it the material of choice for structural and performance-focused vehicle components. Its adaptability across various parts, from structural frames to aesthetic elements, allows manufacturers to optimize production without significantly altering their existing processes. This compatibility with conventional composite fabrication methods like filament winding and pultrusion makes PAN fibers a practical and cost-effective solution for large-scale production. Furthermore, its chemical stability and resistance to environmental stress enhance its appeal for automotive applications that demand durability under high-stress conditions. While pitch-based carbon fiber offers a significantly higher modulus of elasticity, making it suitable for applications requiring extreme stiffness, its high production costs and limited processing scalability have hindered broader adoption. Pitch fibers are primarily used in niche segments such as luxury sports cars and aerospace-grade components, where performance takes precedence over cost. In Germany, the conservative approach to cost management in automotive production restricts pitch fiber to select high-end applications. However, ongoing R&D efforts are aiming to reduce pitch fiber production complexities, potentially opening new pathways for its integration into future mobility solutions.
Carbon fiber's versatility is reflected in its wide array of applications within the German automotive sector, particularly in structural assemblies. These applications capitalize on the material’s high tensile strength, stiffness, and light weight, allowing engineers to design more agile and fuel-efficient vehicles without compromising on safety or performance. Structural carbon fiber components are commonly used in underbodies, subframes, and crash zones, where their ability to absorb energy while maintaining form is critical. This is particularly valuable in electric vehicles, which require strong yet lightweight frames to offset the added mass of battery systems. In powertrain components, carbon fiber plays a crucial role in enhancing thermal resistance, strength, and rotational performance. Drive shafts made from carbon fiber can reduce rotational mass significantly, leading to faster acceleration and improved handling. Battery enclosures crafted from carbon composites also offer superior fire resistance and energy absorption properties, critical for electric mobility. Beyond mechanical and functional uses, carbon fiber is increasingly featured in interior and exterior elements. German automakers employ carbon fiber in dashboards, center consoles, spoilers, and body trims to create sleek, high-end aesthetics that align with their brand image. The material’s tactile and visual appeal, combined with its performance benefits, make it an attractive choice for luxury and performance vehicle lines. These broad applications underscore carbon fiber’s role as both a functional and design-oriented material in Germany’s advanced automotive production landscape.
The German carbon fiber market’s distribution network is defined by two primary sales channels that cater to distinct consumer bases and industrial needs. The first is the original equipment manufacturer (OEM) channel, where carbon fiber components are integrated directly into new vehicle designs during the manufacturing process. This channel involves long-term contracts and partnerships between carbon fiber producers and automakers, often with co-development of proprietary components that meet exacting design and performance standards. OEMs in Germany prioritize consistency, quality assurance, and scalability, prompting suppliers to develop advanced logistics systems and production technologies that ensure timely and reliable delivery. As a result, carbon fiber becomes an integral part of a vehicle’s structure, from initial design to final assembly, contributing to overall vehicle efficiency and market competitiveness. On the other hand, the aftermarket channel is driven by individual consumers and specialty shops focused on customization, performance tuning, and motorsports. Carbon fiber parts such as hoods, spoilers, interior trims, and exhaust housings are highly sought after by enthusiasts who value both aesthetics and performance enhancements. Germany’s deep-rooted car culture, combined with a strong presence of automotive clubs and racing circuits, provides a thriving aftermarket environment for carbon fiber upgrades. This parallel demand ensures steady market growth and diversification, as both large-scale manufacturers and niche consumers continue to seek out carbon fiber solutions tailored to their specific needs.
Considered in this report
• Historic Year: 2019
• Base year: 2024
• Estimated year: 2025
• Forecast year: 2030
Aspects covered in this report
• Automotive Carbon Fiber Market with its value and forecast along with its segments
• Various drivers and challenges
• On-going trends and developments
• Top profiled companies
• Strategic recommendation
By Material
• Polyacrylonitrile (PAN)
• Pitch
By Application
• Structural Assembly
• Powertrain Components
• Interior and Exterior
By Sales Channel
• OEM
• Aftermarket
The approach of the report:
This report consists of a combined approach of primary as well as secondary research. Initially, secondary research was used to get an understanding of the market and listing out the companies that are present in the market. The secondary research consists of third-party sources such as press releases, annual report of companies, analyzing the government generated reports and databases. After gathering the data from secondary sources primary research was conducted by making telephonic interviews with the leading players about how the market is functioning and then conducted trade calls with dealers and distributors of the market. Post this we have started doing primary calls to consumers by equally segmenting consumers in regional aspects, tier aspects, age group, and gender. Once we have primary data with us we have started verifying the details obtained from secondary sources.
Intended audience
This report can be useful to industry consultants, manufacturers, suppliers, associations & organizations related to agriculture industry, government bodies and other stakeholders to align their market-centric strategies. In addition to marketing & presentations, it will also increase competitive knowledge about the industry.
According to the research report Germany Automotive Carbon Fiber Market Overview, 2030, published by Bonafide Research, the Germany Automotive Carbon Fiber Market is expected to reach a market size of more than USD 5.36 Billion by 2030. The evolution of Germany’s carbon fiber market is being significantly shaped by the rise of electric mobility, advancements in manufacturing technology, and increased governmental emphasis on sustainable industrial development. In the last decade, German manufacturers have invested heavily in localizing production, scaling up operations, and enhancing supply chain capabilities to meet growing demand from the automotive and aerospace sectors. These developments are also driven by European climate mandates and Germany’s national targets for carbon neutrality, encouraging the use of advanced materials in transportation infrastructure. Companies are increasingly adopting automation in carbon fiber production through techniques such as resin transfer molding and automated fiber placement, which significantly reduce labor costs and production time. Moreover, a shift towards circular economy principles is prompting research into carbon fiber recycling and second-life applications, ensuring long-term resource efficiency and sustainability. Germany’s emphasis on quality and precision has further accelerated the development of advanced testing facilities and pilot projects, allowing new applications to be prototyped and commercialized more rapidly. The presence of globally recognized research institutions and technical universities also plays a vital role in fostering innovation and creating a skilled workforce to support the carbon fiber industry. With this strong foundation and forward-looking approach, Germany is poised to drive the next phase of global carbon fiber adoption.
In the context of materials, polyacrylonitrile (PAN) continues to be the most prevalent raw material used for carbon fiber production in Germany’s automotive landscape. PAN-based carbon fiber is renowned for its excellent balance of tensile strength, flexibility, and lightweight properties, making it the material of choice for structural and performance-focused vehicle components. Its adaptability across various parts, from structural frames to aesthetic elements, allows manufacturers to optimize production without significantly altering their existing processes. This compatibility with conventional composite fabrication methods like filament winding and pultrusion makes PAN fibers a practical and cost-effective solution for large-scale production. Furthermore, its chemical stability and resistance to environmental stress enhance its appeal for automotive applications that demand durability under high-stress conditions. While pitch-based carbon fiber offers a significantly higher modulus of elasticity, making it suitable for applications requiring extreme stiffness, its high production costs and limited processing scalability have hindered broader adoption. Pitch fibers are primarily used in niche segments such as luxury sports cars and aerospace-grade components, where performance takes precedence over cost. In Germany, the conservative approach to cost management in automotive production restricts pitch fiber to select high-end applications. However, ongoing R&D efforts are aiming to reduce pitch fiber production complexities, potentially opening new pathways for its integration into future mobility solutions.
Carbon fiber's versatility is reflected in its wide array of applications within the German automotive sector, particularly in structural assemblies. These applications capitalize on the material’s high tensile strength, stiffness, and light weight, allowing engineers to design more agile and fuel-efficient vehicles without compromising on safety or performance. Structural carbon fiber components are commonly used in underbodies, subframes, and crash zones, where their ability to absorb energy while maintaining form is critical. This is particularly valuable in electric vehicles, which require strong yet lightweight frames to offset the added mass of battery systems. In powertrain components, carbon fiber plays a crucial role in enhancing thermal resistance, strength, and rotational performance. Drive shafts made from carbon fiber can reduce rotational mass significantly, leading to faster acceleration and improved handling. Battery enclosures crafted from carbon composites also offer superior fire resistance and energy absorption properties, critical for electric mobility. Beyond mechanical and functional uses, carbon fiber is increasingly featured in interior and exterior elements. German automakers employ carbon fiber in dashboards, center consoles, spoilers, and body trims to create sleek, high-end aesthetics that align with their brand image. The material’s tactile and visual appeal, combined with its performance benefits, make it an attractive choice for luxury and performance vehicle lines. These broad applications underscore carbon fiber’s role as both a functional and design-oriented material in Germany’s advanced automotive production landscape.
The German carbon fiber market’s distribution network is defined by two primary sales channels that cater to distinct consumer bases and industrial needs. The first is the original equipment manufacturer (OEM) channel, where carbon fiber components are integrated directly into new vehicle designs during the manufacturing process. This channel involves long-term contracts and partnerships between carbon fiber producers and automakers, often with co-development of proprietary components that meet exacting design and performance standards. OEMs in Germany prioritize consistency, quality assurance, and scalability, prompting suppliers to develop advanced logistics systems and production technologies that ensure timely and reliable delivery. As a result, carbon fiber becomes an integral part of a vehicle’s structure, from initial design to final assembly, contributing to overall vehicle efficiency and market competitiveness. On the other hand, the aftermarket channel is driven by individual consumers and specialty shops focused on customization, performance tuning, and motorsports. Carbon fiber parts such as hoods, spoilers, interior trims, and exhaust housings are highly sought after by enthusiasts who value both aesthetics and performance enhancements. Germany’s deep-rooted car culture, combined with a strong presence of automotive clubs and racing circuits, provides a thriving aftermarket environment for carbon fiber upgrades. This parallel demand ensures steady market growth and diversification, as both large-scale manufacturers and niche consumers continue to seek out carbon fiber solutions tailored to their specific needs.
Considered in this report
• Historic Year: 2019
• Base year: 2024
• Estimated year: 2025
• Forecast year: 2030
Aspects covered in this report
• Automotive Carbon Fiber Market with its value and forecast along with its segments
• Various drivers and challenges
• On-going trends and developments
• Top profiled companies
• Strategic recommendation
By Material
• Polyacrylonitrile (PAN)
• Pitch
By Application
• Structural Assembly
• Powertrain Components
• Interior and Exterior
By Sales Channel
• OEM
• Aftermarket
The approach of the report:
This report consists of a combined approach of primary as well as secondary research. Initially, secondary research was used to get an understanding of the market and listing out the companies that are present in the market. The secondary research consists of third-party sources such as press releases, annual report of companies, analyzing the government generated reports and databases. After gathering the data from secondary sources primary research was conducted by making telephonic interviews with the leading players about how the market is functioning and then conducted trade calls with dealers and distributors of the market. Post this we have started doing primary calls to consumers by equally segmenting consumers in regional aspects, tier aspects, age group, and gender. Once we have primary data with us we have started verifying the details obtained from secondary sources.
Intended audience
This report can be useful to industry consultants, manufacturers, suppliers, associations & organizations related to agriculture industry, government bodies and other stakeholders to align their market-centric strategies. In addition to marketing & presentations, it will also increase competitive knowledge about the industry.
Table of Contents
74 Pages
- 1. Executive Summary
- 2. Market Structure
- 2.1. Market Considerate
- 2.2. Assumptions
- 2.3. Limitations
- 2.4. Abbreviations
- 2.5. Sources
- 2.6. Definitions
- 3. Research Methodology
- 3.1. Secondary Research
- 3.2. Primary Data Collection
- 3.3. Market Formation & Validation
- 3.4. Report Writing, Quality Check & Delivery
- 4. Germany Geography
- 4.1. Population Distribution Table
- 4.2. Germany Macro Economic Indicators
- 5. Market Dynamics
- 5.1. Key Insights
- 5.2. Recent Developments
- 5.3. Market Drivers & Opportunities
- 5.4. Market Restraints & Challenges
- 5.5. Market Trends
- 5.5.1. XXXX
- 5.5.2. XXXX
- 5.5.3. XXXX
- 5.5.4. XXXX
- 5.5.5. XXXX
- 5.6. Supply chain Analysis
- 5.7. Policy & Regulatory Framework
- 5.8. Industry Experts Views
- 6. Germany Automotive carbon fiber Market Overview
- 6.1. Market Size By Value
- 6.2. Market Size and Forecast, By Material
- 6.3. Market Size and Forecast, By Application
- 6.4. Market Size and Forecast, By Sales Channel
- 6.5. Market Size and Forecast, By Region
- 7. Germany Automotive carbon fiber Market Segmentations
- 7.1. Germany Automotive carbon fiber Market, By Material
- 7.1.1. Germany Automotive carbon fiber Market Size, By Polyacrylonitrile (PAN), 2019-2030
- 7.1.2. Germany Automotive carbon fiber Market Size, By Pitch, 2019-2030
- 7.2. Germany Automotive carbon fiber Market, By Application
- 7.2.1. Germany Automotive carbon fiber Market Size, By Structural Assembly, 2019-2030
- 7.2.2. Germany Automotive carbon fiber Market Size, By Powertrain Components, 2019-2030
- 7.2.3. Germany Automotive carbon fiber Market Size, By Interior and Exterior, 2019-2030
- 7.3. Germany Automotive carbon fiber Market, By Sales Channel
- 7.3.1. Germany Automotive carbon fiber Market Size, By OEM, 2019-2030
- 7.3.2. Germany Automotive carbon fiber Market Size, By Aftermarket, 2019-2030
- 7.4. Germany Automotive carbon fiber Market, By Region
- 7.4.1. Germany Automotive carbon fiber Market Size, By North, 2019-2030
- 7.4.2. Germany Automotive carbon fiber Market Size, By East, 2019-2030
- 7.4.3. Germany Automotive carbon fiber Market Size, By West, 2019-2030
- 7.4.4. Germany Automotive carbon fiber Market Size, By South, 2019-2030
- 8. Germany Automotive carbon fiber Market Opportunity Assessment
- 8.1. By Material, 2025 to 2030
- 8.2. By Application, 2025 to 2030
- 8.3. By Sales Channel, 2025 to 2030
- 8.4. By Region, 2025 to 2030
- 9. Competitive Landscape
- 9.1. Porter's Five Forces
- 9.2. Company Profile
- 9.2.1. Company 1
- 9.2.1.1. Company Snapshot
- 9.2.1.2. Company Overview
- 9.2.1.3. Financial Highlights
- 9.2.1.4. Geographic Insights
- 9.2.1.5. Business Segment & Performance
- 9.2.1.6. Product Portfolio
- 9.2.1.7. Key Executives
- 9.2.1.8. Strategic Moves & Developments
- 9.2.2. Company 2
- 9.2.3. Company 3
- 9.2.4. Company 4
- 9.2.5. Company 5
- 9.2.6. Company 6
- 9.2.7. Company 7
- 9.2.8. Company 8
- 10. Strategic Recommendations
- 11. Disclaimer
- List of Figures
- Figure 1: Germany Automotive carbon fiber Market Size By Value (2019, 2024 & 2030F) (in USD Million)
- Figure 2: Market Attractiveness Index, By Material
- Figure 3: Market Attractiveness Index, By Application
- Figure 4: Market Attractiveness Index, By Sales Channel
- Figure 5: Market Attractiveness Index, By Region
- Figure 6: Porter's Five Forces of Germany Automotive carbon fiber Market
- List of Tables
- Table 1: Influencing Factors for Automotive carbon fiber Market, 2024
- Table 2: Germany Automotive carbon fiber Market Size and Forecast, By Material (2019 to 2030F) (In USD Million)
- Table 3: Germany Automotive carbon fiber Market Size and Forecast, By Application (2019 to 2030F) (In USD Million)
- Table 4: Germany Automotive carbon fiber Market Size and Forecast, By Sales Channel (2019 to 2030F) (In USD Million)
- Table 5: Germany Automotive carbon fiber Market Size and Forecast, By Region (2019 to 2030F) (In USD Million)
- Table 6: Germany Automotive carbon fiber Market Size of Polyacrylonitrile (PAN) (2019 to 2030) in USD Million
- Table 7: Germany Automotive carbon fiber Market Size of Pitch (2019 to 2030) in USD Million
- Table 8: Germany Automotive carbon fiber Market Size of Structural Assembly (2019 to 2030) in USD Million
- Table 9: Germany Automotive carbon fiber Market Size of Powertrain Components (2019 to 2030) in USD Million
- Table 10: Germany Automotive carbon fiber Market Size of Interior and Exterior (2019 to 2030) in USD Million
- Table 11: Germany Automotive carbon fiber Market Size of OEM (2019 to 2030) in USD Million
- Table 12: Germany Automotive carbon fiber Market Size of Aftermarket (2019 to 2030) in USD Million
- Table 13: Germany Automotive carbon fiber Market Size of North (2019 to 2030) in USD Million
- Table 14: Germany Automotive carbon fiber Market Size of East (2019 to 2030) in USD Million
- Table 15: Germany Automotive carbon fiber Market Size of West (2019 to 2030) in USD Million
- Table 16: Germany Automotive carbon fiber Market Size of South (2019 to 2030) in USD Million
Pricing
Currency Rates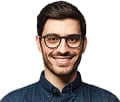
Questions or Comments?
Our team has the ability to search within reports to verify it suits your needs. We can also help maximize your budget by finding sections of reports you can purchase.