
France Predictive Maintenance Market Overview, 2030
Description
France’s predictive maintenance market is experiencing significant growth, driven by the country’s commitment to industrial innovation, digital transformation, and smart manufacturing. As one of Europe’s largest economies, France is rapidly adopting advanced technologies such as artificial intelligence (AI), the Internet of Things (IoT), big data analytics, and cloud computing to optimize asset performance, reduce downtime, and improve operational efficiency. Predictive maintenance is becoming an essential tool for industries such as manufacturing, aerospace, energy, transportation, and healthcare, enabling businesses to transition from traditional reactive and preventive maintenance strategies to a more data-driven, condition-based approach. By leveraging real-time sensor data and machine learning algorithms, predictive maintenance allows companies to detect early signs of equipment failure, implement timely interventions, and extend the lifespan of critical assets. The French government’s focus on Industry 4.0, digital innovation, and sustainability has further accelerated the adoption of predictive maintenance solutions, as businesses seek to improve energy efficiency, reduce emissions, and minimize waste. France’s strict regulatory requirements for workplace safety and equipment reliability are encouraging organizations to integrate predictive maintenance systems that ensure compliance while optimizing asset performance. The increasing availability of cloud-based solutions, edge computing, and AI-powered analytics is further enhancing predictive maintenance capabilities, making it more accessible and efficient for businesses across various sectors.
According to the research report ""France Predictive Maintenance Market Overview, 2030,"" published by Bonafide Research, the France Predictive Maintenance market is anticipated to grow at more than 27.87% CAGR from 2025 to 2030. France's predictive maintenance market is witnessing strong adoption across multiple industrial sectors, each leveraging the technology to optimize operations, improve efficiency, and reduce maintenance costs. The manufacturing sector, which is a key pillar of the French economy, is at the forefront of predictive maintenance adoption, with companies using AI-driven analytics and IoT-enabled sensors to monitor production lines, detect early signs of mechanical wear, and minimize unplanned downtime. Leading French automotive manufacturers such as Renault, Peugeot, and Citroën are integrating predictive maintenance solutions to enhance supply chain reliability, improve production efficiency, and ensure the longevity of critical components. The aerospace sector, a major contributor to France’s industrial landscape, is also investing heavily in predictive maintenance, with companies such as Airbus using advanced analytics to monitor aircraft engines, optimize maintenance schedules, and enhance flight safety. In the energy and utilities sector, predictive maintenance is playing a vital role in improving the efficiency of power plants, renewable energy infrastructure, and electrical grids. Wind farms, hydroelectric plants, and nuclear power stations are utilizing predictive analytics to monitor equipment performance, detect potential faults, and maximize energy output while minimizing maintenance costs. Similarly, the transportation and logistics industry is adopting predictive maintenance to improve railway infrastructure reliability, enhance fleet management, and reduce delays in public transportation networks. The healthcare sector is also leveraging predictive maintenance to ensure the continuous operation of critical medical equipment such as MRI machines, ventilators, and diagnostic systems, improving patient care and reducing maintenance-related disruptions.
France’s predictive maintenance market is shaped by various advanced techniques aimed at reducing operational disruptions, extending the lifespan of machinery, and optimizing maintenance costs across multiple industries. Among the widely used techniques, vibration monitoring plays a crucial role, particularly in sectors reliant on rotating equipment such as manufacturing, power plants, and heavy industrial machinery. Sensors continuously assess vibration patterns, identifying irregularities that could signal potential equipment failures. This technique helps in early detection of mechanical wear, misalignment, and imbalance, allowing businesses to schedule repairs before catastrophic breakdowns occur. Infrared thermography is another essential approach, leveraging thermal imaging to detect abnormal heat levels that may indicate issues such as excessive friction, electrical faults, or insufficient lubrication. It is widely used in electrical infrastructure, industrial motors, and process heating systems, ensuring that excessive heat buildup does not compromise equipment performance. Temperature monitoring is particularly beneficial for industries where overheating poses significant risks, including HVAC systems, power distribution networks, and heavy machinery operations. By tracking temperature fluctuations, companies can mitigate the risk of sudden failures due to thermal stress. Fluid analysis provides critical insights into the health of engines and hydraulic systems by evaluating lubricants, fuels, and coolants for contamination, degradation, or early signs of mechanical wear. This technique is essential for sectors such as transportation, aerospace, and automotive manufacturing, where engine efficiency and lubrication quality directly impact performance and longevity. Circuit monitoring analysis is widely adopted in electrical grids and industrial automation, assessing power circuits to detect abnormalities such as overloads, short circuits, or inefficiencies that could compromise system integrity. Power system assessments further enhance energy efficiency by evaluating the health of power generation and distribution systems, ensuring that infrastructure operates optimally while minimizing the risk of electrical failures.
The predictive maintenance market in France is structured around a combination of solutions and services that enable businesses to proactively manage their assets and equipment health. Software platforms play a central role in this landscape, with integrated solutions being widely implemented across large enterprises as part of broader enterprise asset management systems. These platforms leverage artificial intelligence, machine learning, and IoT-enabled sensors to continuously analyze real-time data, providing actionable insights that help businesses reduce unplanned downtime and optimize maintenance schedules. Standalone solutions, on the other hand, cater to companies seeking specialized predictive maintenance capabilities without the need for full-scale enterprise integration. These independent platforms provide flexibility, particularly for mid-sized industrial firms that require tailored predictive analytics for specific types of machinery or infrastructure. Beyond software-based solutions, services such as installation, support, maintenance, and consulting play an equally vital role in helping businesses effectively implement and utilize predictive maintenance technologies. Installation services ensure that sensors, monitoring equipment, and software platforms are correctly deployed and configured to capture accurate data. Ongoing support and maintenance services help companies address software updates, troubleshoot technical issues, and continuously optimize system performance. Consulting and training services provide organizations with strategic guidance on how to implement predictive maintenance frameworks effectively, helping employees understand data-driven decision-making and maximize the benefits of predictive technologies. These services are particularly valuable for businesses transitioning from reactive or preventive maintenance strategies to fully predictive maintenance models, ensuring a smoother adoption process and better long-term results. The combination of sophisticated software solutions and expert-driven services enhances operational efficiency across a range of industries, from manufacturing and energy to transportation and healthcare.
Deployment models for predictive maintenance solutions in France vary based on industry requirements, security considerations, and cost constraints, leading to a steady balance between on-premises and cloud-based implementations. On-premises predictive maintenance solutions are particularly favored by industries that prioritize data security, regulatory compliance, and high levels of system control. Large manufacturing plants, energy providers, and critical infrastructure operators often opt for on-premises deployments to ensure that sensitive operational data remains within their internal IT infrastructure. This model provides greater control over data access, customization, and integration with existing enterprise systems, though it requires significant initial investment in hardware, software licensing, and IT personnel for ongoing management. While on-premises solutions offer enhanced security and reliability, they also demand higher maintenance efforts and infrastructure costs, making them more suitable for enterprises with the necessary resources to sustain them. On the other hand, cloud-based predictive maintenance solutions are gaining widespread adoption due to their scalability, cost-effectiveness, and ability to facilitate remote monitoring. Hosted on cloud platforms, these solutions allow businesses to collect, analyze, and manage equipment data in real time without requiring extensive in-house IT infrastructure. Cloud-based deployment is particularly appealing to small and medium-sized enterprises looking for affordable, subscription-based models that provide access to advanced analytics without heavy upfront costs. The ability to access predictive maintenance insights from any location enhances operational flexibility, making cloud solutions ideal for industries with distributed assets, such as logistics, transportation, and utilities. Additionally, cloud-based predictive maintenance platforms benefit from continuous software updates, integration with other digital tools, and AI-driven improvements that enhance accuracy and predictive capabilities over time. The increasing adoption of IoT sensors, wireless connectivity, and edge computing further supports the shift toward cloud-based predictive maintenance, enabling real-time data analysis at scale. As organizations continue to modernize their maintenance strategies, the demand for hybrid approaches that combine both on-premises control and cloud-driven analytics is also emerging, allowing businesses to leverage the best of both models while optimizing costs and efficiency.
Considered in this report
• Historic Year: 2019
• Base year: 2024
• Estimated year: 2025
• Forecast year: 2030
Aspects covered in this report
• Predictive Maintenance Market with its value and forecast along with its segments
• Various drivers and challenges
• On-going trends and developments
• Top profiled companies
• Strategic recommendation
By Technique
• Vibration Monitoring
• Infrared Thermography
• Temperature Monitoring
• Fluid Analysis
• Circuit Monitor Analysis
• Power System Assessments
By Component
• Solutions (integrated or standalone)
• Services (installation, support & maintenance, consulting/training)
By Deployment Mode
• On-Premises
• Cloud-Based
The approach of the report:
This report consists of a combined approach of primary as well as secondary research. Initially, secondary research was used to get an understanding of the market and listing out the companies that are present in the market. The secondary research consists of third-party sources such as press releases, annual report of companies, analyzing the government generated reports and databases. After gathering the data from secondary sources primary research was conducted by making telephonic interviews with the leading players about how the market is functioning and then conducted trade calls with dealers and distributors of the market. Post this we have started doing primary calls to consumers by equally segmenting consumers in regional aspects, tier aspects, age group, and gender. Once we have primary data with us we have started verifying the details obtained from secondary sources.
Intended audience
This report can be useful to industry consultants, manufacturers, suppliers, associations & organizations related to agriculture industry, government bodies and other stakeholders to align their market-centric strategies. In addition to marketing & presentations, it will also increase competitive knowledge about the industry.
According to the research report ""France Predictive Maintenance Market Overview, 2030,"" published by Bonafide Research, the France Predictive Maintenance market is anticipated to grow at more than 27.87% CAGR from 2025 to 2030. France's predictive maintenance market is witnessing strong adoption across multiple industrial sectors, each leveraging the technology to optimize operations, improve efficiency, and reduce maintenance costs. The manufacturing sector, which is a key pillar of the French economy, is at the forefront of predictive maintenance adoption, with companies using AI-driven analytics and IoT-enabled sensors to monitor production lines, detect early signs of mechanical wear, and minimize unplanned downtime. Leading French automotive manufacturers such as Renault, Peugeot, and Citroën are integrating predictive maintenance solutions to enhance supply chain reliability, improve production efficiency, and ensure the longevity of critical components. The aerospace sector, a major contributor to France’s industrial landscape, is also investing heavily in predictive maintenance, with companies such as Airbus using advanced analytics to monitor aircraft engines, optimize maintenance schedules, and enhance flight safety. In the energy and utilities sector, predictive maintenance is playing a vital role in improving the efficiency of power plants, renewable energy infrastructure, and electrical grids. Wind farms, hydroelectric plants, and nuclear power stations are utilizing predictive analytics to monitor equipment performance, detect potential faults, and maximize energy output while minimizing maintenance costs. Similarly, the transportation and logistics industry is adopting predictive maintenance to improve railway infrastructure reliability, enhance fleet management, and reduce delays in public transportation networks. The healthcare sector is also leveraging predictive maintenance to ensure the continuous operation of critical medical equipment such as MRI machines, ventilators, and diagnostic systems, improving patient care and reducing maintenance-related disruptions.
France’s predictive maintenance market is shaped by various advanced techniques aimed at reducing operational disruptions, extending the lifespan of machinery, and optimizing maintenance costs across multiple industries. Among the widely used techniques, vibration monitoring plays a crucial role, particularly in sectors reliant on rotating equipment such as manufacturing, power plants, and heavy industrial machinery. Sensors continuously assess vibration patterns, identifying irregularities that could signal potential equipment failures. This technique helps in early detection of mechanical wear, misalignment, and imbalance, allowing businesses to schedule repairs before catastrophic breakdowns occur. Infrared thermography is another essential approach, leveraging thermal imaging to detect abnormal heat levels that may indicate issues such as excessive friction, electrical faults, or insufficient lubrication. It is widely used in electrical infrastructure, industrial motors, and process heating systems, ensuring that excessive heat buildup does not compromise equipment performance. Temperature monitoring is particularly beneficial for industries where overheating poses significant risks, including HVAC systems, power distribution networks, and heavy machinery operations. By tracking temperature fluctuations, companies can mitigate the risk of sudden failures due to thermal stress. Fluid analysis provides critical insights into the health of engines and hydraulic systems by evaluating lubricants, fuels, and coolants for contamination, degradation, or early signs of mechanical wear. This technique is essential for sectors such as transportation, aerospace, and automotive manufacturing, where engine efficiency and lubrication quality directly impact performance and longevity. Circuit monitoring analysis is widely adopted in electrical grids and industrial automation, assessing power circuits to detect abnormalities such as overloads, short circuits, or inefficiencies that could compromise system integrity. Power system assessments further enhance energy efficiency by evaluating the health of power generation and distribution systems, ensuring that infrastructure operates optimally while minimizing the risk of electrical failures.
The predictive maintenance market in France is structured around a combination of solutions and services that enable businesses to proactively manage their assets and equipment health. Software platforms play a central role in this landscape, with integrated solutions being widely implemented across large enterprises as part of broader enterprise asset management systems. These platforms leverage artificial intelligence, machine learning, and IoT-enabled sensors to continuously analyze real-time data, providing actionable insights that help businesses reduce unplanned downtime and optimize maintenance schedules. Standalone solutions, on the other hand, cater to companies seeking specialized predictive maintenance capabilities without the need for full-scale enterprise integration. These independent platforms provide flexibility, particularly for mid-sized industrial firms that require tailored predictive analytics for specific types of machinery or infrastructure. Beyond software-based solutions, services such as installation, support, maintenance, and consulting play an equally vital role in helping businesses effectively implement and utilize predictive maintenance technologies. Installation services ensure that sensors, monitoring equipment, and software platforms are correctly deployed and configured to capture accurate data. Ongoing support and maintenance services help companies address software updates, troubleshoot technical issues, and continuously optimize system performance. Consulting and training services provide organizations with strategic guidance on how to implement predictive maintenance frameworks effectively, helping employees understand data-driven decision-making and maximize the benefits of predictive technologies. These services are particularly valuable for businesses transitioning from reactive or preventive maintenance strategies to fully predictive maintenance models, ensuring a smoother adoption process and better long-term results. The combination of sophisticated software solutions and expert-driven services enhances operational efficiency across a range of industries, from manufacturing and energy to transportation and healthcare.
Deployment models for predictive maintenance solutions in France vary based on industry requirements, security considerations, and cost constraints, leading to a steady balance between on-premises and cloud-based implementations. On-premises predictive maintenance solutions are particularly favored by industries that prioritize data security, regulatory compliance, and high levels of system control. Large manufacturing plants, energy providers, and critical infrastructure operators often opt for on-premises deployments to ensure that sensitive operational data remains within their internal IT infrastructure. This model provides greater control over data access, customization, and integration with existing enterprise systems, though it requires significant initial investment in hardware, software licensing, and IT personnel for ongoing management. While on-premises solutions offer enhanced security and reliability, they also demand higher maintenance efforts and infrastructure costs, making them more suitable for enterprises with the necessary resources to sustain them. On the other hand, cloud-based predictive maintenance solutions are gaining widespread adoption due to their scalability, cost-effectiveness, and ability to facilitate remote monitoring. Hosted on cloud platforms, these solutions allow businesses to collect, analyze, and manage equipment data in real time without requiring extensive in-house IT infrastructure. Cloud-based deployment is particularly appealing to small and medium-sized enterprises looking for affordable, subscription-based models that provide access to advanced analytics without heavy upfront costs. The ability to access predictive maintenance insights from any location enhances operational flexibility, making cloud solutions ideal for industries with distributed assets, such as logistics, transportation, and utilities. Additionally, cloud-based predictive maintenance platforms benefit from continuous software updates, integration with other digital tools, and AI-driven improvements that enhance accuracy and predictive capabilities over time. The increasing adoption of IoT sensors, wireless connectivity, and edge computing further supports the shift toward cloud-based predictive maintenance, enabling real-time data analysis at scale. As organizations continue to modernize their maintenance strategies, the demand for hybrid approaches that combine both on-premises control and cloud-driven analytics is also emerging, allowing businesses to leverage the best of both models while optimizing costs and efficiency.
Considered in this report
• Historic Year: 2019
• Base year: 2024
• Estimated year: 2025
• Forecast year: 2030
Aspects covered in this report
• Predictive Maintenance Market with its value and forecast along with its segments
• Various drivers and challenges
• On-going trends and developments
• Top profiled companies
• Strategic recommendation
By Technique
• Vibration Monitoring
• Infrared Thermography
• Temperature Monitoring
• Fluid Analysis
• Circuit Monitor Analysis
• Power System Assessments
By Component
• Solutions (integrated or standalone)
• Services (installation, support & maintenance, consulting/training)
By Deployment Mode
• On-Premises
• Cloud-Based
The approach of the report:
This report consists of a combined approach of primary as well as secondary research. Initially, secondary research was used to get an understanding of the market and listing out the companies that are present in the market. The secondary research consists of third-party sources such as press releases, annual report of companies, analyzing the government generated reports and databases. After gathering the data from secondary sources primary research was conducted by making telephonic interviews with the leading players about how the market is functioning and then conducted trade calls with dealers and distributors of the market. Post this we have started doing primary calls to consumers by equally segmenting consumers in regional aspects, tier aspects, age group, and gender. Once we have primary data with us we have started verifying the details obtained from secondary sources.
Intended audience
This report can be useful to industry consultants, manufacturers, suppliers, associations & organizations related to agriculture industry, government bodies and other stakeholders to align their market-centric strategies. In addition to marketing & presentations, it will also increase competitive knowledge about the industry.
Table of Contents
75 Pages
- 1. Executive Summary
- 2. Market Structure
- 2.1. Market Considerate
- 2.2. Assumptions
- 2.3. Limitations
- 2.4. Abbreviations
- 2.5. Sources
- 2.6. Definitions
- 3. Research Methodology
- 3.1. Secondary Research
- 3.2. Primary Data Collection
- 3.3. Market Formation & Validation
- 3.4. Report Writing, Quality Check & Delivery
- 4. France Geography
- 4.1. Population Distribution Table
- 4.2. France Macro Economic Indicators
- 5. Market Dynamics
- 5.1. Key Insights
- 5.2. Recent Developments
- 5.3. Market Drivers & Opportunities
- 5.4. Market Restraints & Challenges
- 5.5. Market Trends
- 5.5.1. XXXX
- 5.5.2. XXXX
- 5.5.3. XXXX
- 5.5.4. XXXX
- 5.5.5. XXXX
- 5.6. Supply chain Analysis
- 5.7. Policy & Regulatory Framework
- 5.8. Industry Experts Views
- 6. France Predictive Maintenance Market Overview
- 6.1. Market Size By Value
- 6.2. Market Size and Forecast, By Technique
- 6.3. Market Size and Forecast, By Component
- 6.4. Market Size and Forecast, By Deployment Mode
- 6.5. Market Size and Forecast, By Region
- 7. France Predictive Maintenance Market Segmentations
- 7.1. France Predictive Maintenance Market, By Technique
- 7.1.1. France Predictive Maintenance Market Size, By Vibration Monitoring, 2019-2030
- 7.1.2. France Predictive Maintenance Market Size, By Infrared Thermography, 2019-2030
- 7.1.3. France Predictive Maintenance Market Size, By Temperature Monitoring, 2019-2030
- 7.1.4. France Predictive Maintenance Market Size, By Fluid Analysis, 2019-2030
- 7.1.5. France Predictive Maintenance Market Size, By Circuit Monitor Analysis, 2019-2030
- 7.1.6. France Predictive Maintenance Market Size, By Power System Assessments, 2019-2030
- 7.2. France Predictive Maintenance Market, By Component
- 7.2.1. France Predictive Maintenance Market Size, By Solutions (integrated or standalone), 2019-2030
- 7.2.2. France Predictive Maintenance Market Size, By Services (installation, support & maintenance, consulting/training), 2019-2030
- 7.3. France Predictive Maintenance Market, By Deployment Mode
- 7.3.1. France Predictive Maintenance Market Size, By On-Premises, 2019-2030
- 7.3.2. France Predictive Maintenance Market Size, By Cloud-Based, 2019-2030
- 7.4. France Predictive Maintenance Market, By Region
- 7.4.1. France Predictive Maintenance Market Size, By North, 2019-2030
- 7.4.2. France Predictive Maintenance Market Size, By East, 2019-2030
- 7.4.3. France Predictive Maintenance Market Size, By West, 2019-2030
- 7.4.4. France Predictive Maintenance Market Size, By South, 2019-2030
- 8. France Predictive Maintenance Market Opportunity Assessment
- 8.1. By Technique, 2025 to 2030
- 8.2. By Component, 2025 to 2030
- 8.3. By Deployment Mode, 2025 to 2030
- 8.4. By Region, 2025 to 2030
- 9. Competitive Landscape
- 9.1. Porter's Five Forces
- 9.2. Company Profile
- 9.2.1. Company 1
- 9.2.1.1. Company Snapshot
- 9.2.1.2. Company Overview
- 9.2.1.3. Financial Highlights
- 9.2.1.4. Geographic Insights
- 9.2.1.5. Business Segment & Performance
- 9.2.1.6. Product Portfolio
- 9.2.1.7. Key Executives
- 9.2.1.8. Strategic Moves & Developments
- 9.2.2. Company 2
- 9.2.3. Company 3
- 9.2.4. Company 4
- 9.2.5. Company 5
- 9.2.6. Company 6
- 9.2.7. Company 7
- 9.2.8. Company 8
- 10. Strategic Recommendations
- 11. Disclaimer
- List of Figures
- Figure 1: France Predictive Maintenance Market Size By Value (2019, 2024 & 2030F) (in USD Million)
- Figure 2: Market Attractiveness Index, By Technique
- Figure 3: Market Attractiveness Index, By Component
- Figure 4: Market Attractiveness Index, By Deployment Mode
- Figure 5: Market Attractiveness Index, By Region
- Figure 6: Porter's Five Forces of France Predictive Maintenance Market
- List of Tables
- Table 1: Influencing Factors for Predictive Maintenance Market, 2024
- Table 2: France Predictive Maintenance Market Size and Forecast, By Technique (2019 to 2030F) (In USD Million)
- Table 3: France Predictive Maintenance Market Size and Forecast, By Component (2019 to 2030F) (In USD Million)
- Table 4: France Predictive Maintenance Market Size and Forecast, By Deployment Mode (2019 to 2030F) (In USD Million)
- Table 5: France Predictive Maintenance Market Size and Forecast, By Region (2019 to 2030F) (In USD Million)
- Table 6: France Predictive Maintenance Market Size of Vibration Monitoring (2019 to 2030) in USD Million
- Table 7: France Predictive Maintenance Market Size of Infrared Thermography (2019 to 2030) in USD Million
- Table 8: France Predictive Maintenance Market Size of Temperature Monitoring (2019 to 2030) in USD Million
- Table 9: France Predictive Maintenance Market Size of Fluid Analysis (2019 to 2030) in USD Million
- Table 10: France Predictive Maintenance Market Size of Circuit Monitor Analysis (2019 to 2030) in USD Million
- Table 11: France Predictive Maintenance Market Size of Power System Assessments (2019 to 2030) in USD Million
- Table 12: France Predictive Maintenance Market Size of Solutions (integrated or standalone) (2019 to 2030) in USD Million
- Table 13: France Predictive Maintenance Market Size of Services (installation, support & maintenance, consulting/training) (2019 to 2030) in USD Million
- Table 14: France Predictive Maintenance Market Size of On-Premises (2019 to 2030) in USD Million
- Table 15: France Predictive Maintenance Market Size of Cloud-Based (2019 to 2030) in USD Million
- Table 16: France Predictive Maintenance Market Size of North (2019 to 2030) in USD Million
- Table 17: France Predictive Maintenance Market Size of East (2019 to 2030) in USD Million
- Table 18: France Predictive Maintenance Market Size of West (2019 to 2030) in USD Million
- Table 19: France Predictive Maintenance Market Size of South (2019 to 2030) in USD Million
Pricing
Currency Rates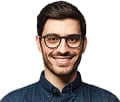
Questions or Comments?
Our team has the ability to search within reports to verify it suits your needs. We can also help maximize your budget by finding sections of reports you can purchase.