
Australia Industrial Evaporators Market Overview, 2030
Description
In Australia, industrial evaporators are used primarily for concentrating liquid mixtures, removing excess water, and recovering valuable components from industrial effluents or process streams. Given the country’s focus on resource conservation and environmental compliance, evaporators play a pivotal role in sectors such as mining, agriculture, food processing, and wastewater management. Evaporation involves applying heat to a liquid to convert it into vapor, separating the solvent (often water) from solutes. In Australia, where many applications involve thermally sensitive materials, evaporators are designed to perform under controlled temperatures to maintain product integrity and reduce thermal degradation. Australian evaporator systems typically operate under reduced pressures (vacuum) to lower boiling points and conserve energy. The equipment is engineered to provide high surface area exposure using advanced geometries like plate or spiral configurations, enabling efficient heat exchange even at lower temperatures, a key requirement in food and pharmaceutical sectors. Air-cooled and water-cooled condensers are integrated based on climate and water availability. In arid regions, dry cooling systems are favored to avoid water consumption. These condensers aid in reclaiming clean water from vapor, a critical advantage in industries like wine production or desalination, where every drop counts. Due to Australia’s emphasis on remote and autonomous operations, especially in the mining sector, pumps and recirculation units are designed to be robust, self-priming, and compatible with solar-powered or off-grid systems. These support consistent circulation, ensuring uniform evaporation and preventing sedimentation in concentrated streams. Australian industries widely adopt multiple-effect evaporation (MEE) and thermal vapor recompression (TVR) to drive down energy consumption. Many installations also use waste heat recovery from boilers or cogeneration units, aligning with national efforts to decarbonize industrial energy use.
According to the research report Australia Industrial Evaporator Market Overview, 2030, published by Bonafide Research, the Australia Industrial Evaporator market is anticipated to grow at more than 7.14% CAGR from 2025 to 2030. In Australia, industrial evaporators are designed to handle diverse flow rates, from low-capacity units in artisanal food processing to high-capacity systems in mining and chemical operations. Many evaporators operate under moderate vacuum conditions to facilitate low-temperature evaporation, preserving product integrity in sectors like dairy and wine. Given Australia's harsh water conditions in regions like Western Australia, manufacturers prioritize robust fouling resistance, often using internally polished surfaces and anti-fouling coatings. Evaporators in Australia are widely used for recovering water and solvents in agriculture, environmental services, and oil refining. High-efficiency condensers and multi-effect configurations are common to reduce both waste and input costs. With many Australian industries located in remote areas or modular facilities like mobile mining units or temporary processing plants, space-efficient designs are essential. Compact falling film and agitated thin film evaporators are favored for ease of transport and setup, particularly when infrastructure is minimal. Common issues in Australia’s high mineral content water particularly in arid regions include lime scaling and silica fouling. This is addressed through pre-heating, acid dosing, and the use of scale inhibitors. Evaporators used in seawater desalination and mine water treatment are specially constructed with non-stick surfaces and tube bundles optimized for turbulent flow to minimize scaling.
Shell and tube evaporators are extensively used in Australia’s heavy industries, particularly in mining and minerals processing, where their rugged construction and capacity to withstand high-pressure, high-temperature operations make them ideal for handling abrasive slurries and corrosive fluids such as those encountered in lithium extraction and rare earth processing. Their resistance to thermal and mechanical stress ensures operational reliability in remote, harsh environments like Western Australia’s Pilbara region, minimizing downtime and supporting the continuous, large-scale processing demands of the sector. These evaporators are engineered with thick-walled tubing and flexible design features that accommodate high turbulence and reduce fouling, thereby improving heat transfer efficiency and longevity. Meanwhile, plate evaporators are increasingly favored in Australia’s dairy, beverage, and wastewater treatment industries due to their compact footprint, ease of cleaning, and superior heat transfer performance. In regions like Victoria and Tasmania, where dairy production is a major economic activity, plate evaporators are used to concentrate milk and whey efficiently while maintaining product integrity through low-temperature processing. Their modular design allows small and medium enterprises to expand capacity easily without significant infrastructure investment, offering flexibility in response to fluctuating demand. Additionally, the sanitary design of plate evaporators aligns with strict hygiene requirements in food and beverage sectors, while their fast heat exchange capability supports energy efficiency and faster processing times.
Falling Film evaporators are widely adopted in the dairy and beverage sectors across regions like Victoria and New South Wales, where they enable efficient concentration of heat-sensitive liquids such as milk and fruit juices. These systems are favored for their low residence time and gentle handling, helping preserve flavor and nutritional content while reducing energy consumption. Rising Film evaporators, though less common, find their niche in agro-processing and sugar industries, where the fluid properties support effective vertical flow and vapor lift mechanisms. Their ability to function without pumps in some cases offers operational simplicity, which is attractive for medium-scale operations in rural Australia. Forced Circulation Evaporators are essential in the mining and chemical industries, particularly in Western Australia, where fluids with high solid content or crystallization tendencies must be handled. These evaporators maintain turbulent flow to prevent scaling and are crucial in brine concentration, acid recovery, and waste minimization in mineral processing. Agitated Thin Film Evaporators are utilized in the pharmaceutical and fine chemicals sectors, where viscous or thermally sensitive compounds are processed. Their design allows for rapid evaporation with minimal degradation, supporting the country’s growing biopharma and nutraceutical industries which demand precise and clean processing methods. Mechanical Vapor Recompression (MVR) systems are gaining momentum in wastewater treatment and zero-liquid discharge (ZLD) applications, especially in industrial hubs near Melbourne and Perth. These evaporators recycle vapor energy, significantly reducing power consumption aligning with Australia’s sustainability drive and high industrial energy costs.
In the Food & Beverage industry, industrial evaporators are essential for concentrating liquids, such as juices, milk, and soups, by removing water content. This process enhances flavor, extends shelf life, and reduces packaging volume. The demand for evaporators is growing due to the expanding food processing sector and the need for efficient preservation methods in the industry. The Pharmaceutical industry also relies heavily on evaporators, particularly in the production of active pharmaceutical ingredients (APIs) and drug formulations. Here, evaporators are used to remove solvents from liquid formulations, ensuring product purity and meeting stringent regulatory standards. With the increasing demand for biopharmaceuticals and vaccines in Australia, evaporators are critical for the concentration and purification of high-value, sensitive compounds. In the Chemical & Petrochemical industry, evaporators play a pivotal role in the separation and concentration of chemicals and petrochemical products. They are used for refining and purifying a wide range of substances, including fuels, solvents, and specialty chemicals. The growing emphasis on sustainability and the development of greener processes in this sector has further driven the need for energy-efficient evaporator systems. For Water & Wastewater Treatment, industrial evaporators are used to treat and concentrate wastewater, reducing its volume and making it easier to manage. These systems help in the recycling of water and removal of hazardous contaminants. Given the increasing focus on water conservation and environmental regulations in Australia, this segment is expanding as industries and municipalities seek more sustainable wastewater management solutions. The others segment encompasses various industries where evaporators are used for niche applications, such as mining, paper and pulp, and textiles.
Considered in this report
• Historic Year: 2019
• Base year: 2024
• Estimated year: 2025
• Forecast year: 2030
Aspects covered in this report
• Industrial Evaporators Market with its value and forecast along with its segments
• Various drivers and challenges
• On-going trends and developments
• Top profiled companies
• Strategic recommendation
By Construction Type
• Shell & Tube
• Plate
By Functionality Type
• Falling Film
• Rising Film
• Forced Circulation Evaporators
• Agitated Thin Film Evaporators
• Mechanical Vapor Recompression
• Others
By End-use Industry Type
• Food & Beverage
• Pharmaceutical
• Chemical & Petrochemical
• Water & Wastewater Treatment
• Others
The approach of the report:
This report consists of a combined approach of primary as well as secondary research. Initially, secondary research was used to get an understanding of the market and listing out the companies that are present in the market. The secondary research consists of third-party sources such as press releases, annual report of companies, analyzing the government generated reports and databases. After gathering the data from secondary sources primary research was conducted by making telephonic interviews with the leading players about how the market is functioning and then conducted trade calls with dealers and distributors of the market. Post this we have started doing primary calls to consumers by equally segmenting consumers in regional aspects, tier aspects, age group, and gender. Once we have primary data with us we have started verifying the details obtained from secondary sources.
Intended audience
This report can be useful to industry consultants, manufacturers, suppliers, associations & organizations related to agriculture industry, government bodies and other stakeholders to align their market-centric strategies. In addition to marketing & presentations, it will also increase competitive knowledge about the industry.
According to the research report Australia Industrial Evaporator Market Overview, 2030, published by Bonafide Research, the Australia Industrial Evaporator market is anticipated to grow at more than 7.14% CAGR from 2025 to 2030. In Australia, industrial evaporators are designed to handle diverse flow rates, from low-capacity units in artisanal food processing to high-capacity systems in mining and chemical operations. Many evaporators operate under moderate vacuum conditions to facilitate low-temperature evaporation, preserving product integrity in sectors like dairy and wine. Given Australia's harsh water conditions in regions like Western Australia, manufacturers prioritize robust fouling resistance, often using internally polished surfaces and anti-fouling coatings. Evaporators in Australia are widely used for recovering water and solvents in agriculture, environmental services, and oil refining. High-efficiency condensers and multi-effect configurations are common to reduce both waste and input costs. With many Australian industries located in remote areas or modular facilities like mobile mining units or temporary processing plants, space-efficient designs are essential. Compact falling film and agitated thin film evaporators are favored for ease of transport and setup, particularly when infrastructure is minimal. Common issues in Australia’s high mineral content water particularly in arid regions include lime scaling and silica fouling. This is addressed through pre-heating, acid dosing, and the use of scale inhibitors. Evaporators used in seawater desalination and mine water treatment are specially constructed with non-stick surfaces and tube bundles optimized for turbulent flow to minimize scaling.
Shell and tube evaporators are extensively used in Australia’s heavy industries, particularly in mining and minerals processing, where their rugged construction and capacity to withstand high-pressure, high-temperature operations make them ideal for handling abrasive slurries and corrosive fluids such as those encountered in lithium extraction and rare earth processing. Their resistance to thermal and mechanical stress ensures operational reliability in remote, harsh environments like Western Australia’s Pilbara region, minimizing downtime and supporting the continuous, large-scale processing demands of the sector. These evaporators are engineered with thick-walled tubing and flexible design features that accommodate high turbulence and reduce fouling, thereby improving heat transfer efficiency and longevity. Meanwhile, plate evaporators are increasingly favored in Australia’s dairy, beverage, and wastewater treatment industries due to their compact footprint, ease of cleaning, and superior heat transfer performance. In regions like Victoria and Tasmania, where dairy production is a major economic activity, plate evaporators are used to concentrate milk and whey efficiently while maintaining product integrity through low-temperature processing. Their modular design allows small and medium enterprises to expand capacity easily without significant infrastructure investment, offering flexibility in response to fluctuating demand. Additionally, the sanitary design of plate evaporators aligns with strict hygiene requirements in food and beverage sectors, while their fast heat exchange capability supports energy efficiency and faster processing times.
Falling Film evaporators are widely adopted in the dairy and beverage sectors across regions like Victoria and New South Wales, where they enable efficient concentration of heat-sensitive liquids such as milk and fruit juices. These systems are favored for their low residence time and gentle handling, helping preserve flavor and nutritional content while reducing energy consumption. Rising Film evaporators, though less common, find their niche in agro-processing and sugar industries, where the fluid properties support effective vertical flow and vapor lift mechanisms. Their ability to function without pumps in some cases offers operational simplicity, which is attractive for medium-scale operations in rural Australia. Forced Circulation Evaporators are essential in the mining and chemical industries, particularly in Western Australia, where fluids with high solid content or crystallization tendencies must be handled. These evaporators maintain turbulent flow to prevent scaling and are crucial in brine concentration, acid recovery, and waste minimization in mineral processing. Agitated Thin Film Evaporators are utilized in the pharmaceutical and fine chemicals sectors, where viscous or thermally sensitive compounds are processed. Their design allows for rapid evaporation with minimal degradation, supporting the country’s growing biopharma and nutraceutical industries which demand precise and clean processing methods. Mechanical Vapor Recompression (MVR) systems are gaining momentum in wastewater treatment and zero-liquid discharge (ZLD) applications, especially in industrial hubs near Melbourne and Perth. These evaporators recycle vapor energy, significantly reducing power consumption aligning with Australia’s sustainability drive and high industrial energy costs.
In the Food & Beverage industry, industrial evaporators are essential for concentrating liquids, such as juices, milk, and soups, by removing water content. This process enhances flavor, extends shelf life, and reduces packaging volume. The demand for evaporators is growing due to the expanding food processing sector and the need for efficient preservation methods in the industry. The Pharmaceutical industry also relies heavily on evaporators, particularly in the production of active pharmaceutical ingredients (APIs) and drug formulations. Here, evaporators are used to remove solvents from liquid formulations, ensuring product purity and meeting stringent regulatory standards. With the increasing demand for biopharmaceuticals and vaccines in Australia, evaporators are critical for the concentration and purification of high-value, sensitive compounds. In the Chemical & Petrochemical industry, evaporators play a pivotal role in the separation and concentration of chemicals and petrochemical products. They are used for refining and purifying a wide range of substances, including fuels, solvents, and specialty chemicals. The growing emphasis on sustainability and the development of greener processes in this sector has further driven the need for energy-efficient evaporator systems. For Water & Wastewater Treatment, industrial evaporators are used to treat and concentrate wastewater, reducing its volume and making it easier to manage. These systems help in the recycling of water and removal of hazardous contaminants. Given the increasing focus on water conservation and environmental regulations in Australia, this segment is expanding as industries and municipalities seek more sustainable wastewater management solutions. The others segment encompasses various industries where evaporators are used for niche applications, such as mining, paper and pulp, and textiles.
Considered in this report
• Historic Year: 2019
• Base year: 2024
• Estimated year: 2025
• Forecast year: 2030
Aspects covered in this report
• Industrial Evaporators Market with its value and forecast along with its segments
• Various drivers and challenges
• On-going trends and developments
• Top profiled companies
• Strategic recommendation
By Construction Type
• Shell & Tube
• Plate
By Functionality Type
• Falling Film
• Rising Film
• Forced Circulation Evaporators
• Agitated Thin Film Evaporators
• Mechanical Vapor Recompression
• Others
By End-use Industry Type
• Food & Beverage
• Pharmaceutical
• Chemical & Petrochemical
• Water & Wastewater Treatment
• Others
The approach of the report:
This report consists of a combined approach of primary as well as secondary research. Initially, secondary research was used to get an understanding of the market and listing out the companies that are present in the market. The secondary research consists of third-party sources such as press releases, annual report of companies, analyzing the government generated reports and databases. After gathering the data from secondary sources primary research was conducted by making telephonic interviews with the leading players about how the market is functioning and then conducted trade calls with dealers and distributors of the market. Post this we have started doing primary calls to consumers by equally segmenting consumers in regional aspects, tier aspects, age group, and gender. Once we have primary data with us we have started verifying the details obtained from secondary sources.
Intended audience
This report can be useful to industry consultants, manufacturers, suppliers, associations & organizations related to agriculture industry, government bodies and other stakeholders to align their market-centric strategies. In addition to marketing & presentations, it will also increase competitive knowledge about the industry.
Table of Contents
77 Pages
- 1. Executive Summary
- 2. Market Structure
- 2.1. Market Considerate
- 2.2. Assumptions
- 2.3. Limitations
- 2.4. Abbreviations
- 2.5. Sources
- 2.6. Definitions
- 3. Research Methodology
- 3.1. Secondary Research
- 3.2. Primary Data Collection
- 3.3. Market Formation & Validation
- 3.4. Report Writing, Quality Check & Delivery
- 4. Australia Geography
- 4.1. Population Distribution Table
- 4.2. Australia Macro Economic Indicators
- 5. Market Dynamics
- 5.1. Key Insights
- 5.2. Recent Developments
- 5.3. Market Drivers & Opportunities
- 5.4. Market Restraints & Challenges
- 5.5. Market Trends
- 5.5.1. XXXX
- 5.5.2. XXXX
- 5.5.3. XXXX
- 5.5.4. XXXX
- 5.5.5. XXXX
- 5.6. Supply chain Analysis
- 5.7. Policy & Regulatory Framework
- 5.8. Industry Experts Views
- 6. Australia Industrial Evaporators Market Overview
- 6.1. Market Size By Value
- 6.2. Market Size and Forecast, By Construction Type
- 6.3. Market Size and Forecast, By Functionality Type
- 6.4. Market Size and Forecast, By End-use Industry Type
- 6.5. Market Size and Forecast, By Region
- 7. Australia Industrial Evaporators Market Segmentations
- 7.1. Australia Industrial Evaporators Market, By Construction Type
- 7.1.1. Australia Industrial Evaporators Market Size, By Shell & Tube, 2019-2030
- 7.1.2. Australia Industrial Evaporators Market Size, By Plate, 2019-2030
- 7.2. Australia Industrial Evaporators Market, By Functionality Type
- 7.2.1. Australia Industrial Evaporators Market Size, By Falling Film, 2019-2030
- 7.2.2. Australia Industrial Evaporators Market Size, By Rising Film, 2019-2030
- 7.2.3. Australia Industrial Evaporators Market Size, By Forced Circulation Evaporators, 2019-2030
- 7.2.4. Australia Industrial Evaporators Market Size, By Agitated Thin Film Evaporators, 2019-2030
- 7.2.5. Australia Industrial Evaporators Market Size, By Mechanical Vapor Recompression, 2019-2030
- 7.2.6. Australia Industrial Evaporators Market Size, By Others, 2019-2030
- 7.3. Australia Industrial Evaporators Market, By End-use Industry Type
- 7.3.1. Australia Industrial Evaporators Market Size, By Food & Beverage, 2019-2030
- 7.3.2. Australia Industrial Evaporators Market Size, By Pharmaceutical, 2019-2030
- 7.3.3. Australia Industrial Evaporators Market Size, By Chemical & Petrochemical, 2019-2030
- 7.3.4. Australia Industrial Evaporators Market Size, By Water & Wastewater Treatment , 2019-2030
- 7.3.5. Australia Industrial Evaporators Market Size, By Others, 2019-2030
- 7.4. Australia Industrial Evaporators Market, By Region
- 7.4.1. Australia Industrial Evaporators Market Size, By North, 2019-2030
- 7.4.2. Australia Industrial Evaporators Market Size, By East, 2019-2030
- 7.4.3. Australia Industrial Evaporators Market Size, By West, 2019-2030
- 7.4.4. Australia Industrial Evaporators Market Size, By South, 2019-2030
- 8. Australia Industrial Evaporators Market Opportunity Assessment
- 8.1. By Construction Type, 2025 to 2030
- 8.2. By Functionality Type, 2025 to 2030
- 8.3. By End-use Industry Type, 2025 to 2030
- 8.4. By Region, 2025 to 2030
- 9. Competitive Landscape
- 9.1. Porter's Five Forces
- 9.2. Company Profile
- 9.2.1. Company 1
- 9.2.1.1. Company Snapshot
- 9.2.1.2. Company Overview
- 9.2.1.3. Financial Highlights
- 9.2.1.4. Geographic Insights
- 9.2.1.5. Business Segment & Performance
- 9.2.1.6. Product Portfolio
- 9.2.1.7. Key Executives
- 9.2.1.8. Strategic Moves & Developments
- 9.2.2. Company 2
- 9.2.3. Company 3
- 9.2.4. Company 4
- 9.2.5. Company 5
- 9.2.6. Company 6
- 9.2.7. Company 7
- 9.2.8. Company 8
- 10. Strategic Recommendations
- 11. Disclaimer
- List of Figures
- Figure 1: Australia Industrial Evaporators Market Size By Value (2019, 2024 & 2030F) (in USD Million)
- Figure 2: Market Attractiveness Index, By Construction Type
- Figure 3: Market Attractiveness Index, By Functionality Type
- Figure 4: Market Attractiveness Index, By End-use Industry Type
- Figure 5: Market Attractiveness Index, By Region
- Figure 6: Porter's Five Forces of Australia Industrial Evaporators Market
- List of Tables
- Table 1: Influencing Factors for Industrial Evaporators Market, 2024
- Table 2: Australia Industrial Evaporators Market Size and Forecast, By Construction Type (2019 to 2030F) (In USD Million)
- Table 3: Australia Industrial Evaporators Market Size and Forecast, By Functionality Type (2019 to 2030F) (In USD Million)
- Table 4: Australia Industrial Evaporators Market Size and Forecast, By End-use Industry Type (2019 to 2030F) (In USD Million)
- Table 5: Australia Industrial Evaporators Market Size and Forecast, By Region (2019 to 2030F) (In USD Million)
- Table 6: Australia Industrial Evaporators Market Size of Shell & Tube (2019 to 2030) in USD Million
- Table 7: Australia Industrial Evaporators Market Size of Plate (2019 to 2030) in USD Million
- Table 8: Australia Industrial Evaporators Market Size of Falling Film (2019 to 2030) in USD Million
- Table 9: Australia Industrial Evaporators Market Size of Rising Film (2019 to 2030) in USD Million
- Table 10: Australia Industrial Evaporators Market Size of Forced Circulation Evaporators (2019 to 2030) in USD Million
- Table 11: Australia Industrial Evaporators Market Size of Agitated Thin Film Evaporators (2019 to 2030) in USD Million
- Table 12: Australia Industrial Evaporators Market Size of Mechanical Vapor Recompression (2019 to 2030) in USD Million
- Table 13: Australia Industrial Evaporators Market Size of Others (2019 to 2030) in USD Million
- Table 14: Australia Industrial Evaporators Market Size of Food & Beverage (2019 to 2030) in USD Million
- Table 15: Australia Industrial Evaporators Market Size of Pharmaceutical (2019 to 2030) in USD Million
- Table 16: Australia Industrial Evaporators Market Size of Chemical & Petrochemical (2019 to 2030) in USD Million
- Table 17: Australia Industrial Evaporators Market Size of Water & Wastewater Treatment (2019 to 2030) in USD Million
- Table 18: Australia Industrial Evaporators Market Size of Others (2019 to 2030) in USD Million
- Table 19: Australia Industrial Evaporators Market Size of North (2019 to 2030) in USD Million
- Table 20: Australia Industrial Evaporators Market Size of East (2019 to 2030) in USD Million
- Table 21: Australia Industrial Evaporators Market Size of West (2019 to 2030) in USD Million
- Table 22: Australia Industrial Evaporators Market Size of South (2019 to 2030) in USD Million
Pricing
Currency Rates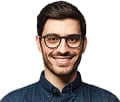
Questions or Comments?
Our team has the ability to search within reports to verify it suits your needs. We can also help maximize your budget by finding sections of reports you can purchase.