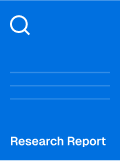
Automotive Engine Management System Market Size, Share & Trends Analysis Report By Component (Electronic Control Unit, Sensors), By Engine Type (Gasoline, Diesel, Hybrid, Electric), By Vehicle Type, By Region, And Segment Forecasts, 2025 - 2030
Description
Automotive Engine Management System Market Summary
The global automotive engine management system market size was estimated at USD 65.54 billion in 2024 and is projected to reach USD 80.25 billion by 2030, growing at a CAGR of 3.6% from 2025 to 2030. Modern engine management systems are increasingly designed to accommodate renewable and alternative fuels, a shift driven by the need to reduce greenhouse gas emissions and dependence on fossil fuels, which boosts the market growth.
The U.S. Department of Energy emphasizes that internal combustion engines (ICEs) can operate on fuels such as natural gas, propane, biodiesel, and ethanol without significant modifications to existing infrastructure.
For instance, hydrogen combustion engines represent a pivotal innovation, with Sandia National Laboratories demonstrating that hydrogen-powered ICEs achieve 50% fuel-to-electricity efficiency while producing near-zero nitrogen oxide (NOx) emissions. This capability positions hydrogen as a viable transitional fuel for hybrid vehicles and stationary power applications. The adaptability of EMS to diverse fuel chemistries is critical for enabling a carbon-neutral future. Research under the Advanced Combustion Engines subprogram focuses on co-optimizing engine designs with fuel properties, ensuring optimal combustion dynamics for both conventional and alternative fuels. For example, ethanol’s high octane rating allows for higher compression ratios in spark-ignition engines, improving thermal efficiency by 10-15% compared to gasoline. Such advancements underscore the EMS’s role in bridging the gap between existing ICE architectures and future renewable fuel ecosystems.
The integration of hybrid electric powertrains with advanced EMS has emerged as a cornerstone strategy for improving fuel economy and reducing emissions. DOE studies reveal that combining internal combustion engines with hybrid electric systems can enhance fuel efficiency by 25-50%, depending on vehicle class and driving conditions. A notable instance is the Plug-in Hybrid Electric Vehicle (PHEV) initiative, where Oak Ridge National Laboratory developed engine control strategies to minimize cold-start emissions, a persistent challenge in hybrid systems.
By decoupling engine operation from immediate driver demand, series hybrid configurations enable optimized warm-up cycles, reducing hydrocarbon emissions by 45% during cold starts. Furthermore, the application of synergistic technologies, such as engine downsizing and turbocharging, allows manufacturers to maintain performance while reducing displacement. Ricardo’s roadmap for gasoline engine efficiency highlights that downsizing a 2.0L engine to 1.4L, coupled with direct injection and variable valve timing, can improve fuel economy by 20% without sacrificing power output. These advancements rely on EMS algorithms that dynamically adjust air-fuel ratios, ignition timing, and boost pressure to balance efficiency and drivability.
The pursuit of higher engine efficiencies propelled the market growth, which necessitates materials capable of withstanding extreme temperatures and pressures. DOE’s Vehicle Technologies Office (VTO) identifies lightweight alloys and advanced ceramics as critical enablers for next-generation engines, with the potential to save 5 billion gallons of fuel annually by 2030 if deployed across 25% of the U.S. fleet. For instance, silicon carbide (SiC) coatings on piston crowns and cylinder liners reduce heat loss, enabling combustion temperatures exceeding 1,500°C, a 15% improvement in thermal efficiency over conventional aluminum components. Heavy-duty engines benefit similarly from iron-based cast alloys with enhanced fatigue resistance, allowing higher peak cylinder pressures in diesel engines. The Materials Genome Initiative has accelerated the development of these materials through computational modeling, reducing prototyping cycles by 40%. Such innovations are integral to achieving the DOE’s target of 55% brake thermal efficiency for heavy-duty engines by 2030, up from the current 45% baseline.
The DOE’s co-optimization initiative represents a paradigm shift in EMS design, where fuel formulations and engine architectures are developed in tandem. This approach leverages the interplay between fuel chemistry and combustion dynamics to maximize efficiency. For example, gasoline compression ignition (GCI) engines, a focus of Argonne National Laboratory, utilize low-octane fuels to enable lean-burn combustion, achieving 35% higher fuel economy compared to conventional spark-ignition engines.
Similarly, the Combustion Research Facility at Sandia National Laboratories has demonstrated that tailored fuel blends, such as di-methyl ether (DME) mixed with diesel, reduce soot formation by 90% while maintaining ignition stability. These breakthroughs rely on EMS capabilities to adjust injection timing and pressure in real-time, ensuring optimal combustion phasing across diverse fuel mixtures. The DOE estimates that co-optimization could yield a 10% efficiency gain in light-duty vehicles by 2030, complementing the 25% improvement expected from advanced engine research alone.
Global Automotive Engine Management System Market Report Segmentation
This report forecasts revenue growth at the global, regional, and country levels and provides an analysis of the latest industry trends in each of the sub-segments from 2018 to 2030. For this study, Grand View Research has segmented the global automotive engine management system market report based on component, engine type, vehicle type, and region:
The global automotive engine management system market size was estimated at USD 65.54 billion in 2024 and is projected to reach USD 80.25 billion by 2030, growing at a CAGR of 3.6% from 2025 to 2030. Modern engine management systems are increasingly designed to accommodate renewable and alternative fuels, a shift driven by the need to reduce greenhouse gas emissions and dependence on fossil fuels, which boosts the market growth.
The U.S. Department of Energy emphasizes that internal combustion engines (ICEs) can operate on fuels such as natural gas, propane, biodiesel, and ethanol without significant modifications to existing infrastructure.
For instance, hydrogen combustion engines represent a pivotal innovation, with Sandia National Laboratories demonstrating that hydrogen-powered ICEs achieve 50% fuel-to-electricity efficiency while producing near-zero nitrogen oxide (NOx) emissions. This capability positions hydrogen as a viable transitional fuel for hybrid vehicles and stationary power applications. The adaptability of EMS to diverse fuel chemistries is critical for enabling a carbon-neutral future. Research under the Advanced Combustion Engines subprogram focuses on co-optimizing engine designs with fuel properties, ensuring optimal combustion dynamics for both conventional and alternative fuels. For example, ethanol’s high octane rating allows for higher compression ratios in spark-ignition engines, improving thermal efficiency by 10-15% compared to gasoline. Such advancements underscore the EMS’s role in bridging the gap between existing ICE architectures and future renewable fuel ecosystems.
The integration of hybrid electric powertrains with advanced EMS has emerged as a cornerstone strategy for improving fuel economy and reducing emissions. DOE studies reveal that combining internal combustion engines with hybrid electric systems can enhance fuel efficiency by 25-50%, depending on vehicle class and driving conditions. A notable instance is the Plug-in Hybrid Electric Vehicle (PHEV) initiative, where Oak Ridge National Laboratory developed engine control strategies to minimize cold-start emissions, a persistent challenge in hybrid systems.
By decoupling engine operation from immediate driver demand, series hybrid configurations enable optimized warm-up cycles, reducing hydrocarbon emissions by 45% during cold starts. Furthermore, the application of synergistic technologies, such as engine downsizing and turbocharging, allows manufacturers to maintain performance while reducing displacement. Ricardo’s roadmap for gasoline engine efficiency highlights that downsizing a 2.0L engine to 1.4L, coupled with direct injection and variable valve timing, can improve fuel economy by 20% without sacrificing power output. These advancements rely on EMS algorithms that dynamically adjust air-fuel ratios, ignition timing, and boost pressure to balance efficiency and drivability.
The pursuit of higher engine efficiencies propelled the market growth, which necessitates materials capable of withstanding extreme temperatures and pressures. DOE’s Vehicle Technologies Office (VTO) identifies lightweight alloys and advanced ceramics as critical enablers for next-generation engines, with the potential to save 5 billion gallons of fuel annually by 2030 if deployed across 25% of the U.S. fleet. For instance, silicon carbide (SiC) coatings on piston crowns and cylinder liners reduce heat loss, enabling combustion temperatures exceeding 1,500°C, a 15% improvement in thermal efficiency over conventional aluminum components. Heavy-duty engines benefit similarly from iron-based cast alloys with enhanced fatigue resistance, allowing higher peak cylinder pressures in diesel engines. The Materials Genome Initiative has accelerated the development of these materials through computational modeling, reducing prototyping cycles by 40%. Such innovations are integral to achieving the DOE’s target of 55% brake thermal efficiency for heavy-duty engines by 2030, up from the current 45% baseline.
The DOE’s co-optimization initiative represents a paradigm shift in EMS design, where fuel formulations and engine architectures are developed in tandem. This approach leverages the interplay between fuel chemistry and combustion dynamics to maximize efficiency. For example, gasoline compression ignition (GCI) engines, a focus of Argonne National Laboratory, utilize low-octane fuels to enable lean-burn combustion, achieving 35% higher fuel economy compared to conventional spark-ignition engines.
Similarly, the Combustion Research Facility at Sandia National Laboratories has demonstrated that tailored fuel blends, such as di-methyl ether (DME) mixed with diesel, reduce soot formation by 90% while maintaining ignition stability. These breakthroughs rely on EMS capabilities to adjust injection timing and pressure in real-time, ensuring optimal combustion phasing across diverse fuel mixtures. The DOE estimates that co-optimization could yield a 10% efficiency gain in light-duty vehicles by 2030, complementing the 25% improvement expected from advanced engine research alone.
Global Automotive Engine Management System Market Report Segmentation
This report forecasts revenue growth at the global, regional, and country levels and provides an analysis of the latest industry trends in each of the sub-segments from 2018 to 2030. For this study, Grand View Research has segmented the global automotive engine management system market report based on component, engine type, vehicle type, and region:
- Component Outlook (Revenue, USD Million, 2018 - 2030)
- Electronic Control Unit (ECU)
- Sensors
- Fuel Pump
- Actuators
- Others
- Engine Type Outlook (Revenue, USD Million, 2018 - 2030)
- Gasoline Engines
- Diesel Engines
- Hybrid Engines
- Electric Engines
- Vehicle Type Outlook (Revenue, USD Million, 2018 - 2030)
- Passenger Cars
- Light Commercial Vehicles (LCVs)
- Heavy Commercial Vehicles (HCVs)
- Two-Wheelers
- Regional Outlook (Revenue, USD Million, 2018 - 2030)
- North America
- U.S.
- Canada
- Mexico
- Europe
- Germany
- UK
- France
- Asia Pacific
- China
- Japan
- India
- South Korea
- Australia
- Latin America
- Brazil
- Middle East and Africa (MEA)
- KSA
- UAE
- South Africa
Table of Contents
130 Pages
- Chapter 1. Methodology and Scope
- 1.1. Market Segmentation and Scope
- 1.2. Research Methodology
- 1.2.1. Information Procurement
- 1.3. Information or Data Analysis
- 1.4. Methodology
- 1.5. Research Scope and Assumptions
- 1.6. Market Formulation & Validation
- 1.7. Country Based Segment Share Calculation
- 1.8. List of Data Sources
- Chapter 2. Executive Summary
- 2.1. Market Outlook
- 2.2. Segment Outlook
- 2.3. Competitive Insights
- Chapter 3. Automotive Engine Management System Market Variables, Trends, & Scope
- 3.1. Market Lineage Outlook
- 3.2. Market Dynamics
- 3.2.1. Market Driver Analysis
- 3.2.2. Market Restraint Analysis
- 3.2.3. Industry Challenge
- 3.3. Automotive Engine Management System Market Analysis Tools
- 3.3.1. Industry Analysis – Porter’s
- 3.3.1.1. Bargaining power of the suppliers
- 3.3.1.2. Bargaining power of the buyers
- 3.3.1.3. Threats of substitution
- 3.3.1.4. Threats from new entrants
- 3.3.1.5. Competitive rivalry
- 3.3.2. PESTEL Analysis
- 3.3.2.1. Political landscape
- 3.3.2.2. Economic landscape
- 3.3.2.3. Social landscape
- 3.3.2.4. Technological landscape
- 3.3.2.5. Environmental landscape
- 3.3.2.6. Legal landscape
- Chapter 4. Automotive Engine Management System Market: Component Estimates & Trend Analysis
- 4.1. Segment Dashboard
- 4.2. Automotive Engine Management System Market: Component Movement Analysis, 2024 & 2030 (USD Million)
- 4.3. Electronic Control Unit (ECU)
- 4.3.1. Electronic Control Unit (ECU) Market Revenue Estimates and Forecasts, 2018 - 2030 (USD Million)
- 4.4. Sensors
- 4.4.1. Sensors Market Revenue Estimates and Forecasts, 2018 - 2030 (USD Million)
- 4.5. Fuel Pump
- 4.5.1. Fuel Pump Market Revenue Estimates and Forecasts, 2018 - 2030 (USD Million)
- 4.6. Actuators
- 4.6.1. Actuators Market Revenue Estimates and Forecasts, 2018 - 2030 (USD Million)
- 4.7. Others
- 4.7.1. Others Market Revenue Estimates and Forecasts, 2018 - 2030 (USD Million)
- Chapter 5. Automotive Engine Management System Market: Engine Type Estimates & Trend Analysis
- 5.1. Segment Dashboard
- 5.2. Automotive Engine Management System Market: Engine Type Movement Analysis, 2024 & 2030 (USD Million)
- 5.3. Gasoline Engines
- 5.3.1. Gasoline Engines Market Revenue Estimates and Forecasts, 2018 - 2030 (USD Million)
- 5.4. Diesel Engines
- 5.4.1. Diesel Engines Market Revenue Estimates and Forecasts, 2018 - 2030 (USD Million)
- 5.5. Hybrid Engines
- 5.5.1. Hybrid Engines Market Revenue Estimates and Forecasts, 2018 - 2030 (USD Million)
- 5.6. Electric Engines
- 5.6.1. Electric Engines Market Revenue Estimates and Forecasts, 2018 - 2030 (USD Million)
- Chapter 6. Automotive Engine Management System Market: Vehicle Type Estimates & Trend Analysis
- 6.1. Segment Dashboard
- 6.2. Automotive Engine Management System Market: Vehicle Type Movement Analysis, 2024 & 2030 (USD Million)
- 6.3. Passenger Cars
- 6.3.1. Passenger Cars Market Revenue Estimates and Forecasts, 2018 - 2030 (USD Million)
- 6.4. Light Commercial Vehicles (LCVs)
- 6.4.1. Light Commercial Vehicles (LCVs) Market Revenue Estimates and Forecasts, 2018 - 2030 (USD Million)
- 6.5. Heavy Commercial Vehicles (HCVs)
- 6.5.1. Heavy Commercial Vehicles (HCVs) Market Revenue Estimates and Forecasts, 2018 - 2030 (USD Million)
- 6.6. Two-Wheelers
- 6.6.1. Two-Wheelers Market Revenue Estimates and Forecasts, 2018 - 2030 (USD Million)
- Chapter 7. Automotive Engine Management System Market: Regional Estimates & Trend Analysis
- 7.1. Automotive Engine Management System Market Share, By Region, 2024 & 2030, USD Million
- 7.2. North America
- 7.2.1. North America Automotive Engine Management System Market Estimates and Forecasts, 2018 - 2030 (USD Million)
- 7.2.2. U.S.
- 7.2.2.1. U.S. Automotive Engine Management System Market Estimates and Forecasts, 2018 - 2030 (USD Million)
- 7.2.3. Canada
- 7.2.3.1. Canada Automotive Engine Management System Market Estimates and Forecasts, 2018 - 2030 (USD Million)
- 7.2.4. Mexico
- 7.2.4.1. Mexico Automotive Engine Management System Market Estimates and Forecasts, 2018 - 2030 (USD Million)
- 7.3. Europe
- 7.3.1. Europe Automotive Engine Management System Market Estimates and Forecasts, 2018 - 2030 (USD Million)
- 7.3.2. UK
- 7.3.2.1. UK Automotive Engine Management System Market Estimates and Forecasts, 2018 - 2030 (USD Million)
- 7.3.3. Germany
- 7.3.3.1. Germany Automotive Engine Management System Market Estimates and Forecasts, 2018 - 2030 (USD Million)
- 7.3.4. France
- 7.3.4.1. France Automotive Engine Management System Market Estimates and Forecasts, 2018 - 2030 (USD Million)
- 7.4. Asia Pacific
- 7.4.1. Asia Pacific Automotive Engine Management System Market Estimates and Forecasts, 2018 - 2030 (USD Million)
- 7.4.2. China
- 7.4.2.1. China Automotive Engine Management System Market Estimates and Forecasts, 2018 - 2030 (USD Million)
- 7.4.3. Japan
- 7.4.3.1. Japan Automotive Engine Management System Market Estimates and Forecasts, 2018 - 2030 (USD Million)
- 7.4.4. India
- 7.4.4.1. India Automotive Engine Management System Market Estimates and Forecasts, 2018 - 2030 (USD Million)
- 7.4.5. South Korea
- 7.4.5.1. South Korea Automotive Engine Management System Market Estimates and Forecasts, 2018 - 2030 (USD Million)
- 7.4.6. Australia
- 7.4.6.1. Australia Automotive Engine Management System Market Estimates and Forecasts, 2018 - 2030 (USD Million)
- 7.5. Latin America
- 7.5.1. Latin America Automotive Engine Management System Market Estimates and Forecasts, 2018 - 2030 (USD Million)
- 7.5.2. Brazil
- 7.5.2.1. Brazil Automotive Engine Management System Market Estimates and Forecasts, 2018 - 2030 (USD Million)
- 7.6. Middle East and Africa
- 7.6.1. Middle East and Africa Automotive Engine Management System Market Estimates and Forecasts, 2018 - 2030 (USD Million)
- 7.6.2. UAE
- 7.6.2.1. UAE Automotive Engine Management System Market Estimates and Forecasts, 2018 - 2030 (USD Million)
- 7.6.3. KSA
- 7.6.3.1. KSA Automotive Engine Management System Market Estimates and Forecasts, 2018 - 2030 (USD Million)
- 7.6.4. South Africa
- 7.6.4.1. South Africa Automotive Engine Management System Market Estimates and Forecasts, 2018 - 2030 (USD Million)
- Chapter 8. Competitive Landscape
- 8.1. Company Categorization
- 8.2. Company Market Positioning
- 8.3. Company Heat Map Analysis
- 8.4. Company Profiles/Listing
- 8.4.1. Robert Bosch GmbH
- 8.4.1.1. Participant’s Overview
- 8.4.1.2. Financial Performance
- 8.4.1.3. Product Benchmarking
- 8.4.1.4. Strategic Initiatives
- 8.4.2. Continental AG
- 8.4.2.1. Participant’s Overview
- 8.4.2.2. Financial Performance
- 8.4.2.3. Product Benchmarking
- 8.4.2.4. Strategic Initiatives
- 8.4.3. Denso Corporation
- 8.4.3.1. Participant’s Overview
- 8.4.3.2. Financial Performance
- 8.4.3.3. Product Benchmarking
- 8.4.3.4. Strategic Initiatives
- 8.4.4. BorgWarner Inc.
- 8.4.4.1. Participant’s Overview
- 8.4.4.2. Financial Performance
- 8.4.4.3. Product Benchmarking
- 8.4.4.4. Strategic Initiatives
- 8.4.5. Hitachi Astemo, Ltd.
- 8.4.5.1. Participant’s Overview
- 8.4.5.2. Financial Performance
- 8.4.5.3. Product Benchmarking
- 8.4.5.4. Strategic Initiatives
- 8.4.6. Valeo
- 8.4.6.1. Participant’s Overview
- 8.4.6.2. Financial Performance
- 8.4.6.3. Product Benchmarking
- 8.4.6.4. Strategic Initiatives
- 8.4.7. Infineon Technologies AG
- 8.4.7.1. Participant’s Overview
- 8.4.7.2. Financial Performance
- 8.4.7.3. Product Benchmarking
- 8.4.7.4. Strategic Initiatives
- 8.4.8. Sensata Technologies, Inc.
- 8.4.8.1. Participant’s Overview
- 8.4.8.2. Financial Performance
- 8.4.8.3. Product Benchmarking
- 8.4.8.4. Strategic Initiatives
- 8.4.9. Niterra Co., Ltd.
- 8.4.9.1. Participant’s Overview
- 8.4.9.2. Financial Performance
- 8.4.9.3. Product Benchmarking
- 8.4.9.4. Strategic Initiatives
- 8.4.10. Mitsubishi Heavy Industries Ltd.
- 8.4.10.1. Participant’s Overview
- 8.4.10.2. Financial Performance
- 8.4.10.3. Product Benchmarking
- 8.4.10.4. Strategic Initiatives
Pricing
Currency Rates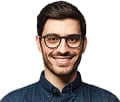
Questions or Comments?
Our team has the ability to search within reports to verify it suits your needs. We can also help maximize your budget by finding sections of reports you can purchase.