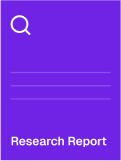
Automated Bending Machine Market- Growth, Share, Opportunities & Competitive Analysis, 2024 – 2032
Description
Market Overview
The Automated Bending Machine Market is expected to grow from USD 2.385 billion in 2024 to USD 3.470 billion by 2032, with a compound annual growth rate (CAGR) of 4.8%.
The market growth is driven by the increasing demand for precision manufacturing, the need to reduce labor costs, and the desire to improve production efficiency across industries such as automotive, aerospace, and construction. Technological advancements, including the integration of artificial intelligence and Industry 4.0, are enhancing the capabilities of these machines, enabling more flexible, precise, and automated bending operations. The ongoing shift toward automation in manufacturing processes—prompted by the need for faster turnaround times and higher quality standards—further accelerates market expansion. The growth of smart factories and the growing emphasis on operational cost reduction contribute to the increasing adoption of automated bending machines. Additionally, the expansion of industries such as metalworking and sheet metal fabrication is expected to further drive demand for these machines, indicating positive market growth as companies seek innovative, efficient production solutions.
Market Drivers
Cost Efficiency and Labor Reduction
Automated bending machines help reduce labor costs by minimizing the need for manual intervention, which is especially beneficial in industries experiencing labor shortages or rising wage costs. For example, AMADA’s automated bending processes reduce reliance on skilled labor, streamlining operations and enhancing productivity. As manufacturers look for cost-effective solutions to increase output and profitability, the efficiency provided by automation makes these machines a preferred option for optimizing operations across various industries.
Market Challenges Analysis
High Initial Investment and Maintenance Costs
A significant challenge in the Automated Bending Machine Market is the high initial investment required for acquiring and deploying these advanced machines. The cost of automated bending machines can be substantial due to their complex design, integration of advanced technologies, and high precision capabilities. This financial burden is particularly challenging for small and medium-sized enterprises (SMEs), who may struggle to justify such large capital expenditures, especially when compared to traditional manual bending methods that incur lower initial costs. Additionally, the maintenance and servicing of these machines can be costly, as specialized technicians, spare parts, and regular upkeep are necessary to ensure optimal performance. For manufacturers with tight budgets, these ongoing costs may discourage the adoption of the technology, limiting broader market penetration. The high upfront costs may deter potential buyers, especially in regions where budget constraints and cost-benefit considerations are key factors.
Segmentation
By Type:
Automatic
Semiautomatic
By Technology:
Electric
Hydraulic
Pneumatic
Induction
By Application:
Tube/Pipe
Metal Sheet
Bar
By Industry:
Automotive
Shipbuilding
Aerospace
Construction & Mining
Others (Heavy Machine Engineering and Machine Manufacturing)
By Geography:
North America
U.S.
Canada
Mexico
Europe
Germany
France
U.K.
Italy
Spain
Rest of Europe
Asia Pacific
China
Japan
India
South Korea
Southeast Asia
Rest of Asia Pacific
Latin America
Brazil
Argentina
Rest of Latin America
Middle East & Africa
GCC Countries
South Africa
Rest of the Middle East and Africa
Key Player Analysis:
Baileigh Industries, Inc.
SOCO Machinery Co., Ltd
Haco NV
Prima Industrie S.p.A.
WAFIOS AG
Pines Engineering & H&H Tooling
Horn Machines Tools, Inc.
Transfluid Maschinenbau GmbH
Shuz Tung Machinery Industrial Co., Ltd
PEDAX GmbH
The Automated Bending Machine Market is expected to grow from USD 2.385 billion in 2024 to USD 3.470 billion by 2032, with a compound annual growth rate (CAGR) of 4.8%.
The market growth is driven by the increasing demand for precision manufacturing, the need to reduce labor costs, and the desire to improve production efficiency across industries such as automotive, aerospace, and construction. Technological advancements, including the integration of artificial intelligence and Industry 4.0, are enhancing the capabilities of these machines, enabling more flexible, precise, and automated bending operations. The ongoing shift toward automation in manufacturing processes—prompted by the need for faster turnaround times and higher quality standards—further accelerates market expansion. The growth of smart factories and the growing emphasis on operational cost reduction contribute to the increasing adoption of automated bending machines. Additionally, the expansion of industries such as metalworking and sheet metal fabrication is expected to further drive demand for these machines, indicating positive market growth as companies seek innovative, efficient production solutions.
Market Drivers
Cost Efficiency and Labor Reduction
Automated bending machines help reduce labor costs by minimizing the need for manual intervention, which is especially beneficial in industries experiencing labor shortages or rising wage costs. For example, AMADA’s automated bending processes reduce reliance on skilled labor, streamlining operations and enhancing productivity. As manufacturers look for cost-effective solutions to increase output and profitability, the efficiency provided by automation makes these machines a preferred option for optimizing operations across various industries.
Market Challenges Analysis
High Initial Investment and Maintenance Costs
A significant challenge in the Automated Bending Machine Market is the high initial investment required for acquiring and deploying these advanced machines. The cost of automated bending machines can be substantial due to their complex design, integration of advanced technologies, and high precision capabilities. This financial burden is particularly challenging for small and medium-sized enterprises (SMEs), who may struggle to justify such large capital expenditures, especially when compared to traditional manual bending methods that incur lower initial costs. Additionally, the maintenance and servicing of these machines can be costly, as specialized technicians, spare parts, and regular upkeep are necessary to ensure optimal performance. For manufacturers with tight budgets, these ongoing costs may discourage the adoption of the technology, limiting broader market penetration. The high upfront costs may deter potential buyers, especially in regions where budget constraints and cost-benefit considerations are key factors.
Segmentation
By Type:
Automatic
Semiautomatic
By Technology:
Electric
Hydraulic
Pneumatic
Induction
By Application:
Tube/Pipe
Metal Sheet
Bar
By Industry:
Automotive
Shipbuilding
Aerospace
Construction & Mining
Others (Heavy Machine Engineering and Machine Manufacturing)
By Geography:
North America
U.S.
Canada
Mexico
Europe
Germany
France
U.K.
Italy
Spain
Rest of Europe
Asia Pacific
China
Japan
India
South Korea
Southeast Asia
Rest of Asia Pacific
Latin America
Brazil
Argentina
Rest of Latin America
Middle East & Africa
GCC Countries
South Africa
Rest of the Middle East and Africa
Key Player Analysis:
Baileigh Industries, Inc.
SOCO Machinery Co., Ltd
Haco NV
Prima Industrie S.p.A.
WAFIOS AG
Pines Engineering & H&H Tooling
Horn Machines Tools, Inc.
Transfluid Maschinenbau GmbH
Shuz Tung Machinery Industrial Co., Ltd
PEDAX GmbH
Table of Contents
199 Pages
- CHAPTER NO. 1 : INTRODUCTION
- 1.1.1. Report Description
- Purpose of the Report
- USP & Key Offerings
- 1.1.2. Key Benefits for Stakeholders
- 1.1.3. Target Audience
- 1.1.4. Report Scope
- CHAPTER NO. 2 : EXECUTIVE SUMMARY
- 2.1. Automated Bending Machine Market Snapshot
- 2.1.1. Automated Bending Machine Market, 2018 - 2032 (USD Million)
- CHAPTER NO. 3 : Automated Bending Machine Market – INDUSTRY ANALYSIS
- 3.1. Introduction
- 3.2. Market Drivers
- 3.3. Market Restraints
- 3.4. Market Opportunities
- 3.5. Porter’s Five Forces Analysis
- CHAPTER NO. 4 : ANALYSIS COMPETITIVE LANDSCAPE
- 4.1. Company Market Share Analysis – 2023
- 4.2. Automated Bending Machine Market Company Revenue Market Share, 2023
- 4.3. Company Assessment Metrics, 2023
- 4.4. Start-ups /SMEs Assessment Metrics, 2023
- 4.5. Strategic Developments
- 4.6. Key Players Product Matrix
- CHAPTER NO. 5 : PESTEL & ADJACENT MARKET ANALYSIS
- CHAPTER NO. 6 : Automated Bending Machine Market – BY BASED ON TYPE ANALYSIS
- CHAPTER NO. 7 : Automated Bending Machine Market – BY BASED ON TECHNOLOGY ANALYSIS
- CHAPTER NO. 8 : Automated Bending Machine Market – BY BASED ON APPLICATION ANALYSIS
- CHAPTER NO. 9 : Automated Bending Machine Market – BY BASED ON INDUSTRY ANALYSIS
- CHAPTER NO. 10 : Automated Bending Machine Market – BY BASED ON GEOGRAPHY ANALYSIS
- CHAPTER NO. 11 : COMPANY PROFILES
- 9.1. Baileigh Industries, Inc.
- 9.1.1. Company Overview
- 9.1.2. Product Portfolio
- 9.1.3. SWOT Analysis
- 9.1.4. Business Strategy
- 9.1.5. Financial Overview
- 9.2. SOCO Machinery Co., Ltd
- 9.3. Haco NV.
- 9.4. Prima Industrie S.p.A.
- 9.5. WAFIOS AG
- 9.6. Pines Engineering & H&H Tooling
- 9.7. Horn Machines Tools, Inc.
- 9.8. Transfluid Maschinenbau GmbH
- 9.9. Shuz Tung Machinery Industrial Co., Ltd
- 9.10. PEDAX GmbH
Pricing
Currency Rates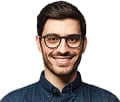
Questions or Comments?
Our team has the ability to search within reports to verify it suits your needs. We can also help maximize your budget by finding sections of reports you can purchase.